I am happy to report that many of the things that were in the “holding pattern” from the last installment now seem to be rolling again. The backordered 29-inch tundra tires should be here in a few weeks, more brake and axle parts are on their way and the new front suspension strut prototype should be ready to mock up soon as well. There will be a lot more focus on all these things coming soon. Progress always feels good.
For now, with the seat frames basically complete and the door frames and windows in the works, I have also been spending some time getting the correct position for the instrument panel. Since I have the Garmin G3X Touch display in hand, it is finally time to put some of my ideas for this unique instrument pod/panel to the test.
I have been staring at cardboard mockups for months, considering exactly how I wanted it. The instrument panel is one area where the builder’s creativity and uniqueness shines. You can walk by a whole line of kit airplanes and not see too many differences on the outside, besides paint, of course. But when you look at their instrument panels, it is usually difficult to find two that are similar. I really enjoyed building the super-clean and nearly switchless panel for my Super701 and I am now determined that all the cabin area inside this Zenith CH 750 SD will put even the Super701 to shame.
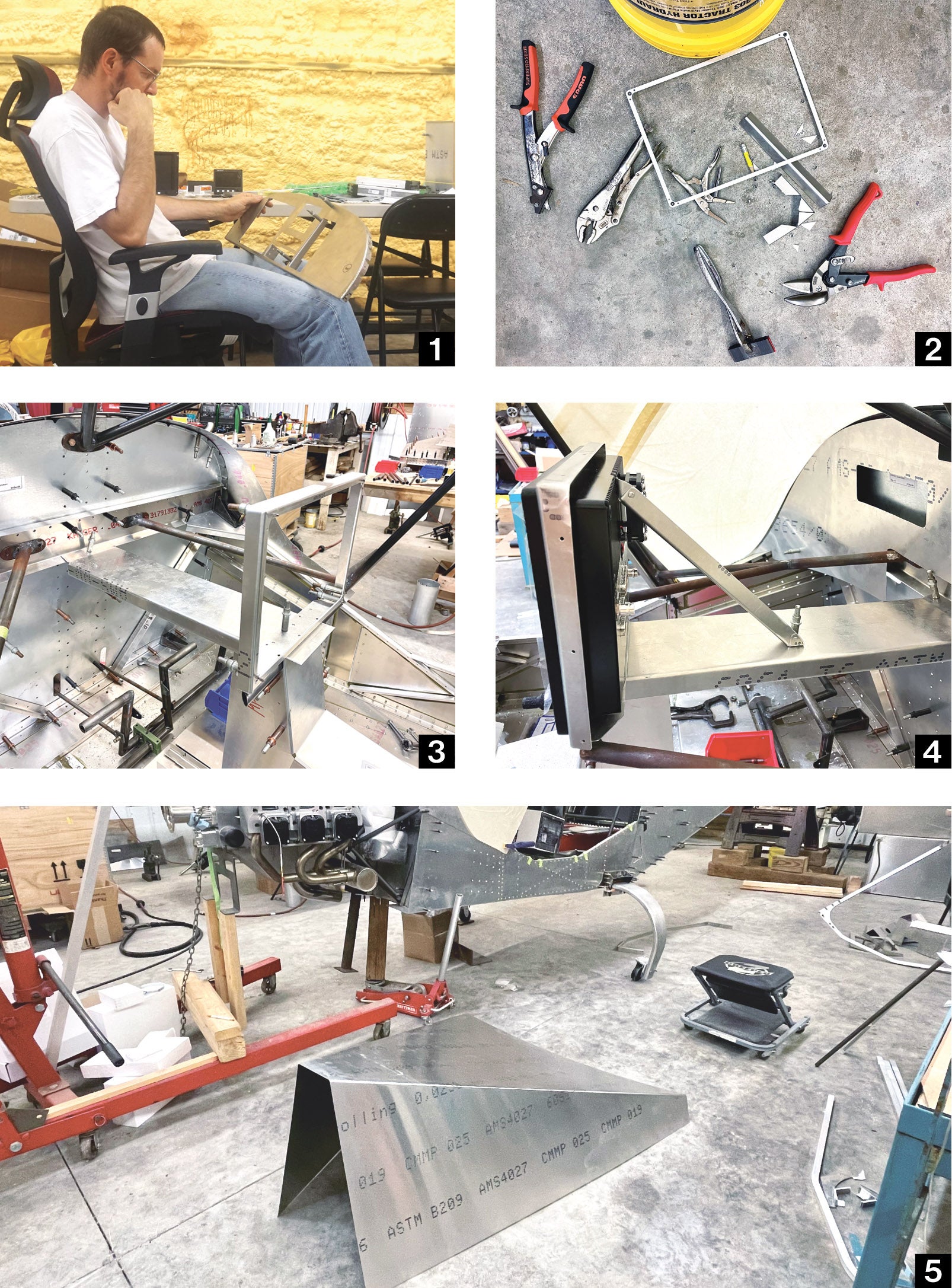
While most Zeniths are built using one of the available instrument panel blanks from the factory (Zenith also offers some precut packages), I have decided to do this one differently. The common instrument panel is formed with flanges around the sides for mounting into the plane and a large flat face that can be cut out for instruments of various sizes so the builder can install almost any combination of instruments they desire.
With my 750 SDX goals, I do not need all the extra real estate for instrumentation because I am going to depend on the single Garmin G3X for practically everything. So instead of having to fit all the instruments into the panel, I will be building a frame around the G3X.
Although these one-off pieces are very time-consuming to fabricate and build, they are still some of my favorite parts of constructing the 750 SDX. Starting with pieces of the standard L angles that come with the kit (I ordered several extra when I got the kit), I trimmed/crafted them into what is basically a small profile picture frame around the G3X, with a wider flange on the bottom for mounting and a special brace for the back to keep the G3X where it needs to be when the panel cover is removed.
The panel cover is just a flat piece of the same aluminum skin used by the factory that I carefully marked and bent to fit around the G3X frame. I have to admit that trimming the back of the panel cover to match the rounded firewall cover was incredibly time-consuming. It is now all mocked up and mostly trimmed to fit, but there is still a little tweaking left to do to make everything exactly how I want it, so I will show more of the pod/panel next time.
The Balancing Act
Let’s briefly consider the latest goals I have for this 750 SDX. I am so deep into this build with highly modified components at this point that I cannot just simply stop, back up and switch to the much easier path, which would have been to build an unmodified 750 SD “by the book.” My ultimate goal is to build the best CH 750 Super Duty in existence based on power-to-weight ratio and overall usable performance.
I have shaved many ounces from various parts to recover tiny bits of weight in hopes that those weight savings will all add up and allow a reasonable offset of several other things I need and want to install. I could have easily saved more than 40 pounds by going with the non-turbo version of this six-cylinder ULPower engine, but I did not want to build it with a less advantageous power-to-weight ratio than my Super701 has. The only option left requires me to carefully shave weight off everywhere possible without trimming so much that the plane loses structural integrity.
Example? Even the recently fabricated and installed chrome-moly throttle bracket has been shaved to a bare minimum. The throttle cable will be one of the very few exposed pieces required for engine control and I intend to keep that to a minimum as well. The actual bracket started as a flat chrome-moly plate. I bent a 90° angle onto the plate to help with structural rigidity, then carefully measured, positioned and drilled the half-inch hole for the throttle cable to pass through and be tightened down. With plenty of trimming and sanding, I “coped” and made the bracket fit nicely onto the side tube of the cabin frame. Finally, I eliminated all the extra material possible and then welded the bracket directly to the cabin frame.
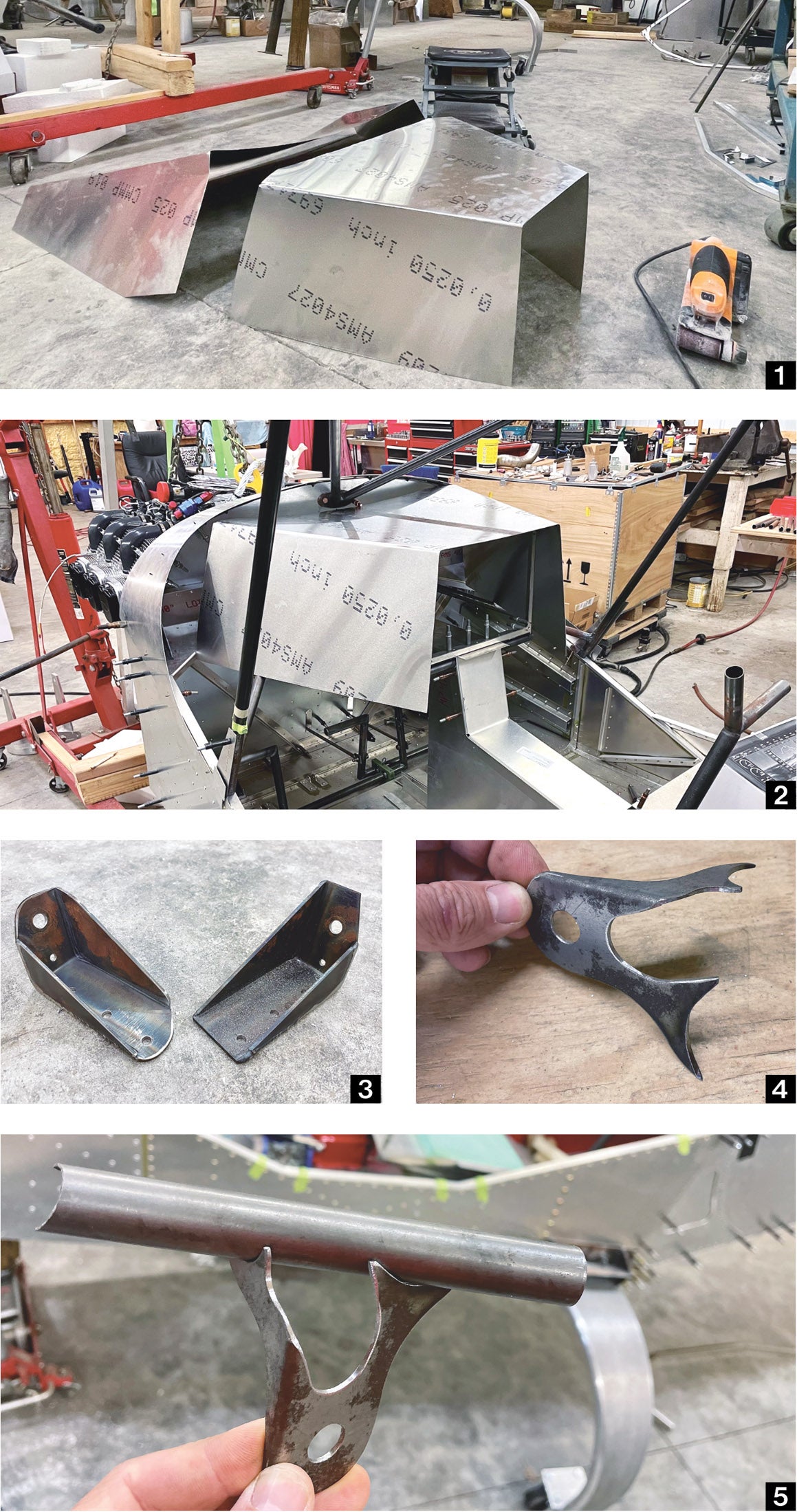
Titanium!
To trek even further into the never-ending pursuit of lightweight performance, it is now official that I am going to try out my abilities on fabricating and welding some titanium parts. I have been around titanium before, but I have never personally tried welding or fabricating this specialized metal. If my math is correct, with the small list of components that I intend to build and replace with titanium, the weight savings should easily add up to around 5 pounds. I know this really isn’t needed or necessary because the 750 SD already has a generous load capacity, but titanium is something that I have wanted to try my hand at for quite a few years.
Several titanium parts are currently on the way and I’ll keep you posted. Anyway, with these latest pieces being placed on a diet like all the previous pieces, I feel like I am slowly finding a nice balance between what is necessary and what is desired while still keeping performance at a maximum.
Cabin Ventilation
I have been working on several of the foam molds that will one day help construct some uniquely designed composite shrouds, plenums and ducting. Specifically, I have been figuring out the nicest way to get some extra fresh air into the cabin. The standard Zenith kits use a “snap” vent that is mounted in the bubble window of the doors. It is very simple and works great, but I personally always thought it was a bit distracting with the visibility and I have heard a few people say they had slight fitting and sealing issues with these vents. In the Super701, I adapted a twist-style vent that has proven robust and works well to bring in air. But it is still a bit distracting to me and just does not give the finished look I want.
In the Super701, I also incorporated two other simple and lightweight vents into the aluminum cabin side skins. When open, they create an exposed flap that catches a lot of air and when they are closed they seal well and go nearly completely unnoticed. I have been very happy with these and decided to also use them in this build (I already have the small rectangular holes cut into the side skins for the rear seating in the 750 SDX).
I am also swapping the door’s bubble windows that came with my kit for a set of windows that do not have the precut hole for the standard snap vents. This will allow the 750 SDX’s doors and windows to be free of any obstructions to visibility since there will be nothing but pure window.
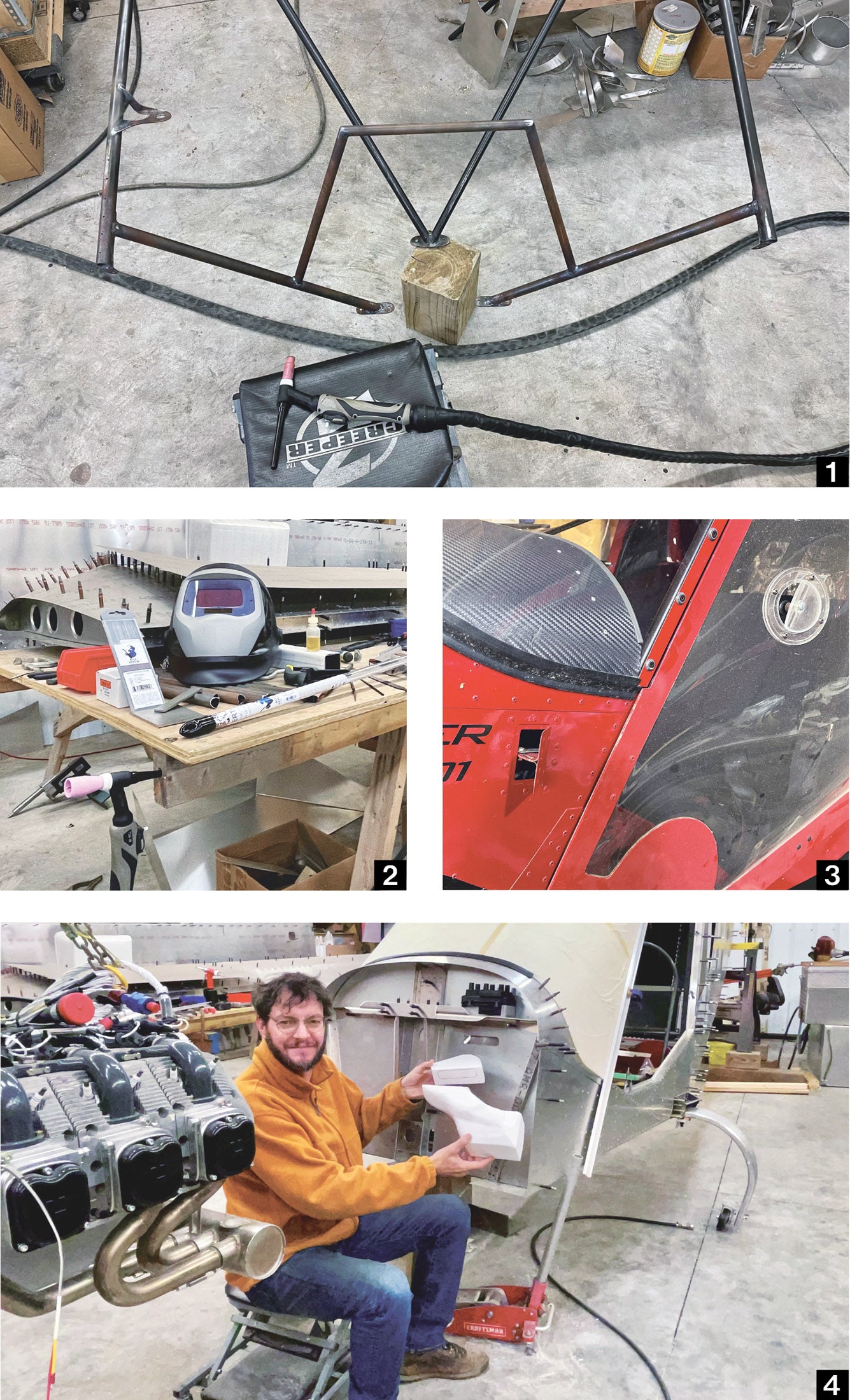
I have to bring air in somewhere, though, and the problem I’m running into is that there isn’t much cabin side skin high enough to bring fresh air in around the upper body. I definitely want to have some fresh air available to blow across my face for flying in the summer heat. I really have to do some creative thinking because I want to also bring fresh air into a set of eyeball vents installed into the center console just below the Garmin G3X.
While researching all kinds of intake systems, like NACA ducts, I have come to the conclusion that I do not have adequate space on the cabin side skins and I will have to bring this air in through the cowl and duct it through the firewall and into the cabin. This will still require some careful planning and also some good insulating to keep the engine heat from penetrating the ducting and ultimately into the cabin.
The next dilemma is that this ducting will have to pass through the firewall and I am definitely running out of firewall space for a pass-through area that will remain hidden inside the instrument panel cover. With the tight-fitting turbo at the right side of the firewall and the intercooler/intake system on the left side, I am very limited for duct space. You see how multiple modifications can bang into each other?
The only place left that is seemingly possible to duct fresh air through the firewall is just above the intercooler, and even that space is very limited and is not suitable for large enough round ducting to suit the airflow needs.
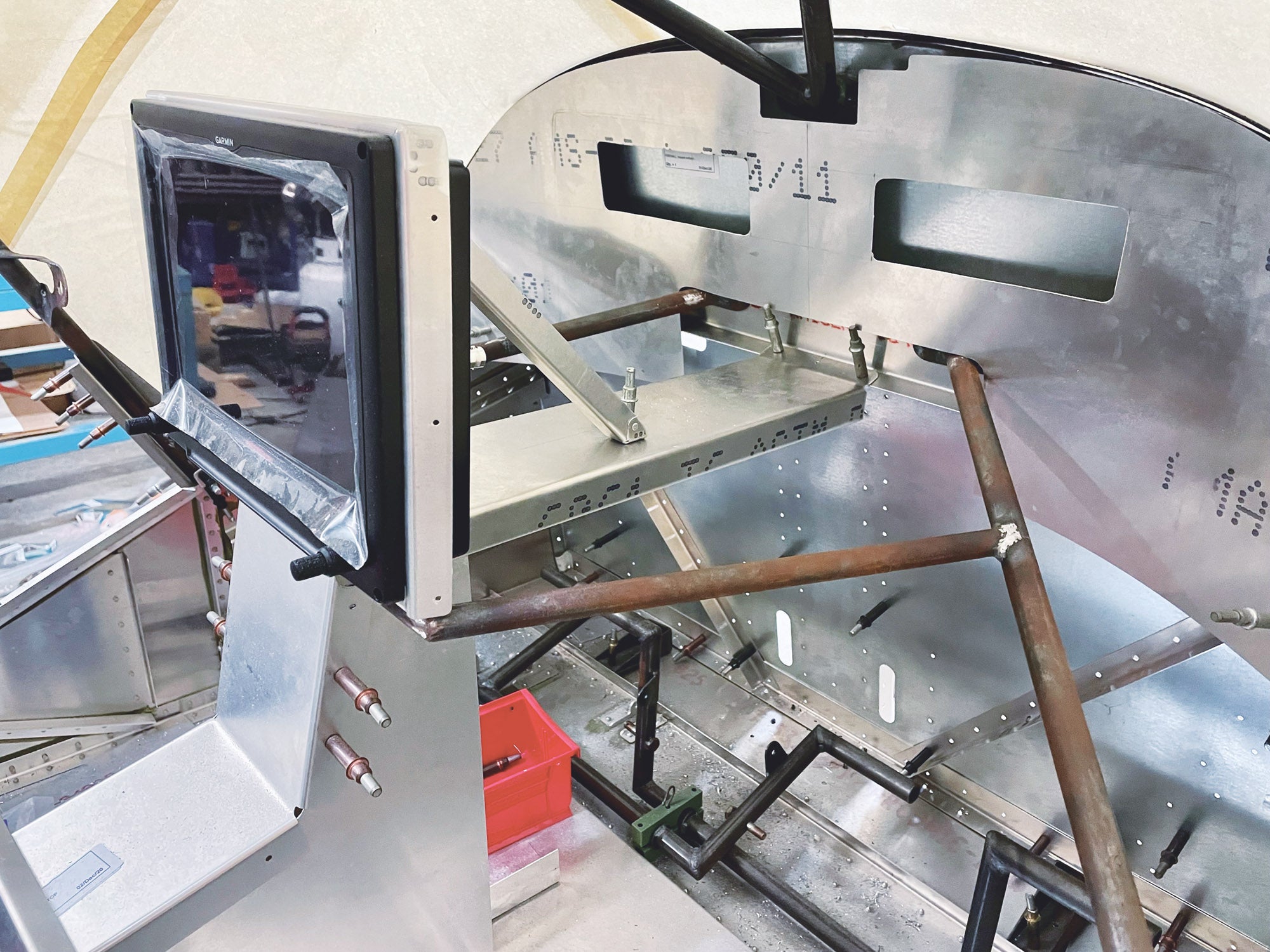
About Those Composite Forms
I have measured and studied and measured and studied and finally marked and cut out a rectangular slot into the firewall in the very tight area between some of the firewall bracing. To get air through this slot, I will have to build two custom shrouds. These will be attached to the firewall as a pass-through (one for the engine side and one for the cabin side) that will ultimately mate up and allow me to connect to the two eyeball vents with two SCAT tubes that will remain hidden behind the instrument panel.
It’s not an easy task. This area is getting “busy.” As am I. Shaping the foam molds is time-consuming because you don’t want to trim too much and restrict the duct volume. However, you also want the shape to be smooth and formed in such a way that it will flow nicely. The eyeball vents are ordered and I will continue this ducting process once I have figured out exactly how and where to install them in the center console. Finalizing the firewall-side mold and duct will probably be put on hold until the cowl is built so I can be sure it will tie into the cowl design properly.
Space Limitations
I knew things were going to get tight before I started, but I am now realizing just how insanely tight-fitting the area between the engine and the firewall is actually becoming. I have almost boxed myself into a corner with the custom-built short engine mount for my ULPower engine. The extra 6 inches of room offered by the factory-built engine mount would be really nice to have for installing all the required (and desired) accessories for this airplane. As I continue to look at all the pieces of the puzzle that have yet to be installed, I’m realizing that even more outside-the-box thinking is definitely going to be requi;red if I’m going to stick to my Xtreme goals of clean, light and comfortable.
This makes me think of a good parting quote: “The elevator to success is out of order. You’ll have to use the stairs…one step at a time.” Sometimes I feel like I am trying to walk up an escalator that is going down, but I am determined to succeed and will keep taking the steps until I do so.