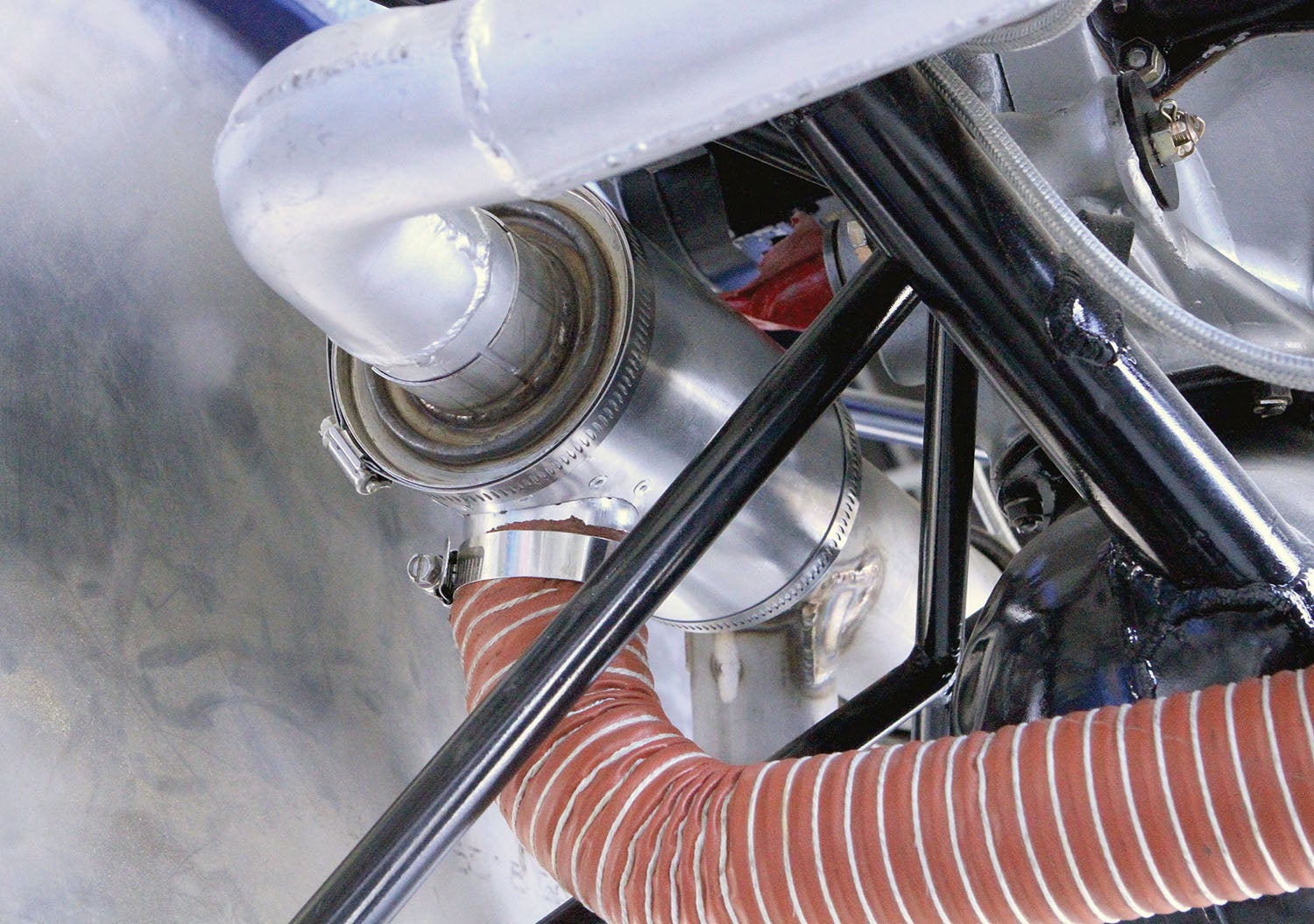
This month’s project is a follow-on to the Pietenpol muffler that was the subject of the Home Shop Machinist column in the May 2019 issue. That column showed how to make a J3 Cub-style muffler for a Continental A65 engine. If you remember, we ended up finding a new factory muffler. In addition to being lighter and more durable than our DIY muffler, it included flanges for carb heat and cabin heat cuffs.
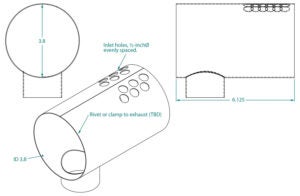
While there’s not much point to cabin heat on an open-cockpit tandem like the Pietenpol, a hot air/carb heat system is absolutely required on almost any engine with a carburetor.
The carb heat system on the A65 is as simple as it gets: A sheet metal cuff wraps around the flanges to form a heat chamber. Openings at one end allow air to be drawn in, and an outlet tube at the other end provides a way (usually via SCAT-type hose) for hot air to be ducted to the carb.
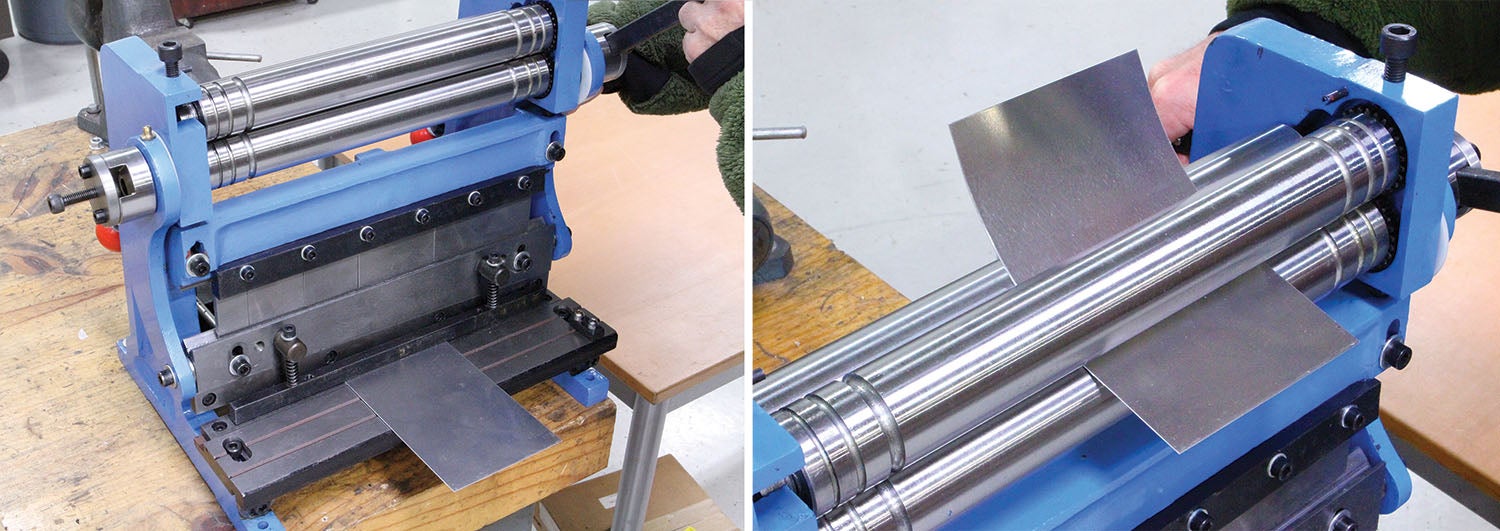
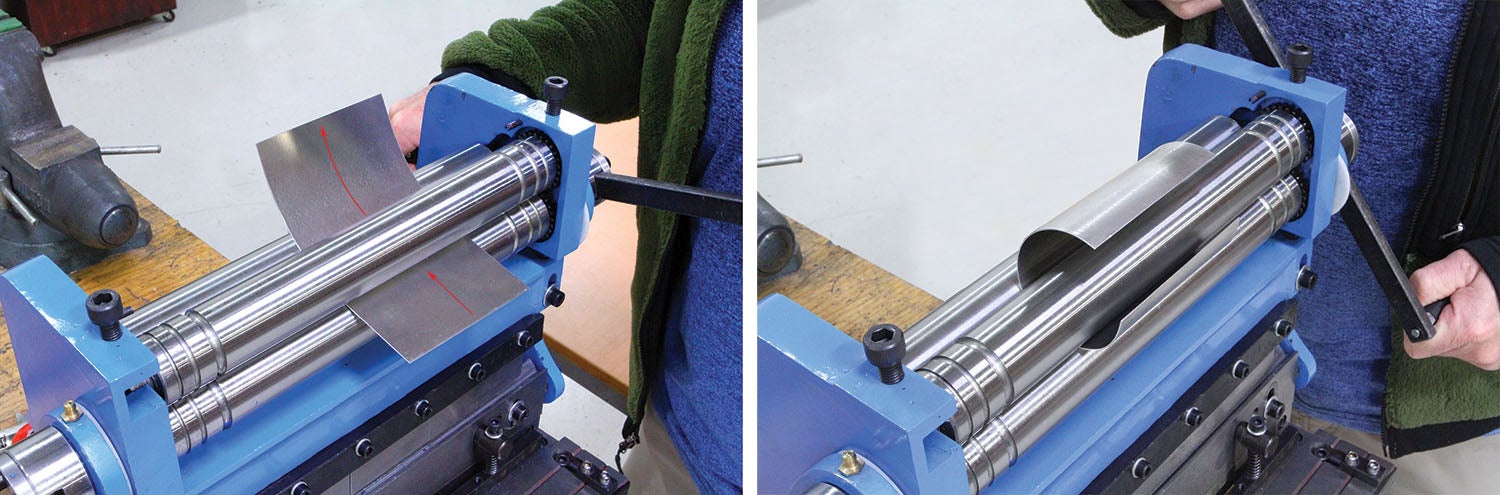
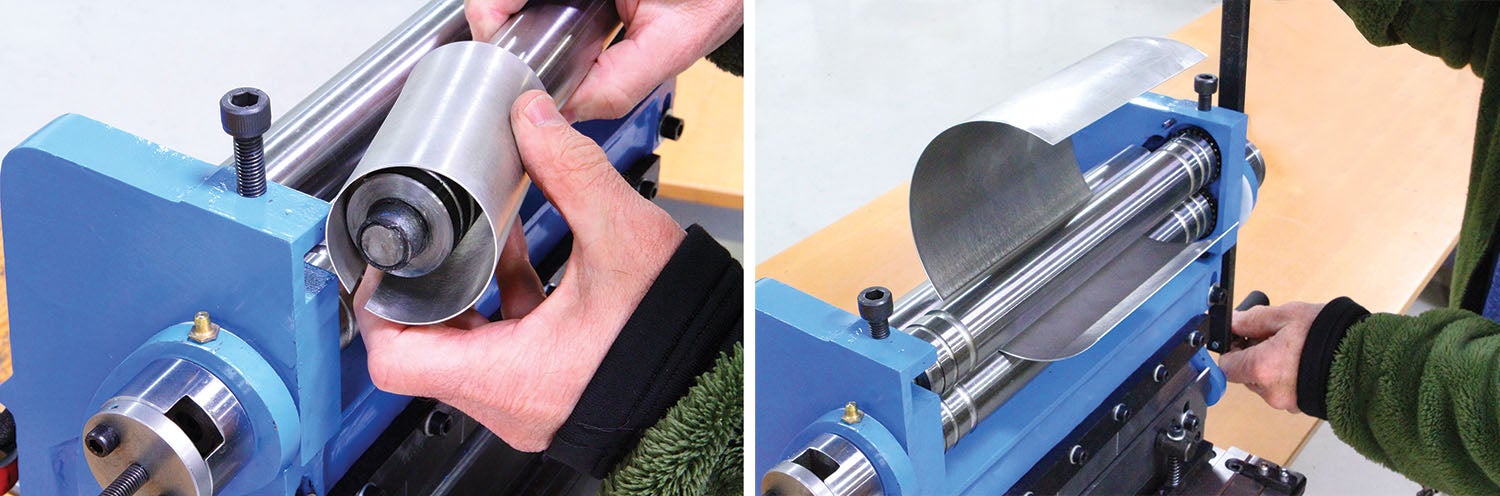
Both parts, the cuff and outlet, are cylindrical and constructed of thin (0.040-inch) 6061-0 aluminum sheet. If there was ever an ideal job for an all-in-one benchtop shear, press brake and slip roll machine, this has to be it!
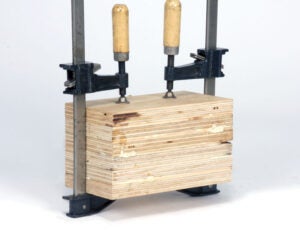
As the name implies, this tool combines the functions of three old-school sheet metal tools in one. The model used for this article was an inexpensive 12-inch capacity benchtop machine that I would classify as hobby grade. It was purchased on Amazon for $380. A 30-inch version sells for around $840.
There are a lot of ways to cut sheet metal, but few tools do a nicer job than a shear when it comes to making straight, distortion-free cuts. The same goes for making bends: There are other ways, but few work better than a press-type brake.
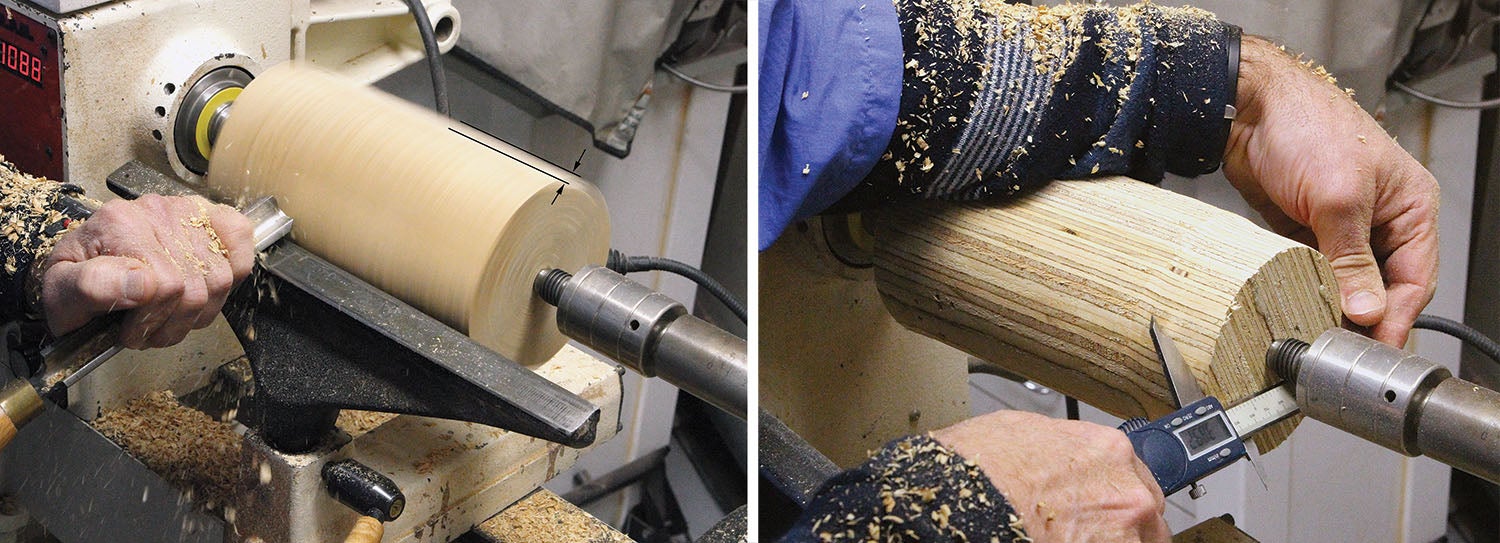
For forming sheet metal into cones and cylinders, the slip roll is pretty much the only option. Yes, it’s possible to get close by stretching sheet around a form, but there will always be some springback, whereas a cylinder (or cone) formed with a slip roll will retain its shape.
To make the carb heat cuff, I measured the diameter and the width between the muffler flanges. Adding the material thickness (0.040 inch x 2) and some basic math (C=πd) gave me the circumference and the length of the sheet needed for a perfect cylinder. The same simple math was used to size the sheet needed for the outlet connector to fit a 2-inch SCAT hose. About 1/2 inch was added to make an overlapping connection called a joggle. The joggle provided the necessary real estate to rivet the joint.

The outlet connector is attached to the cuff with rivets. TIG welding was initially considered to attach the outlet, but a few test welds on some scraps of 0.040-inch-thick aluminum by my ace welder Billy Griggs resulted in burn through. The problem was that our shop wasn’t set up to weld thin aluminum sheet. Billy suggested it might be possible with some practice, but he would probably need several sets of parts. Even then, Billy said there was only a slim chance that one might come out acceptable, so rivets were the fallback choice.
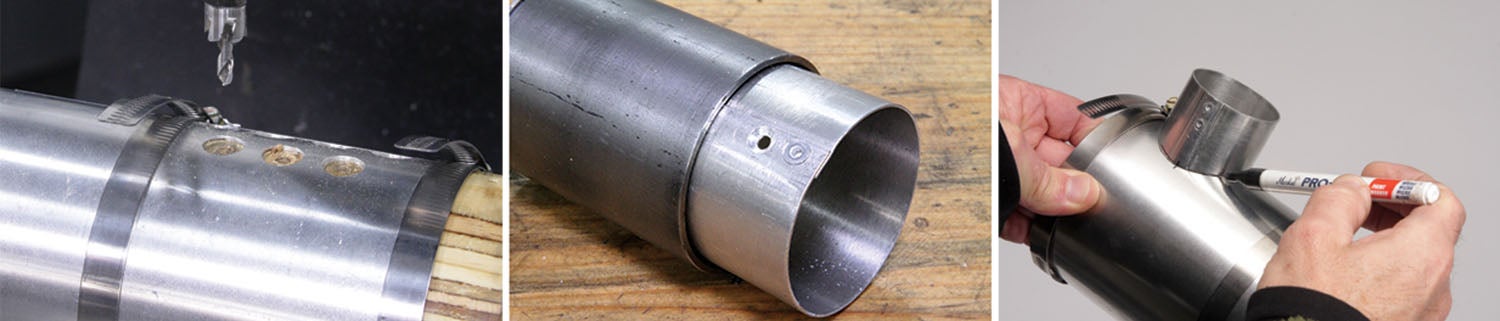
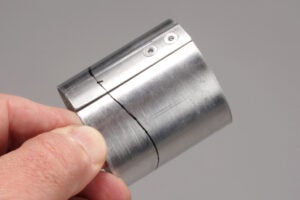
The 2-inch diameter hole in the cuff for the outlet connector was another challenge. Using a nibbler was considered, but it was decided the cleanest way to make the opening would be to fishmouth the opening with a hole saw after slip rolling the cuff to a cylinder.
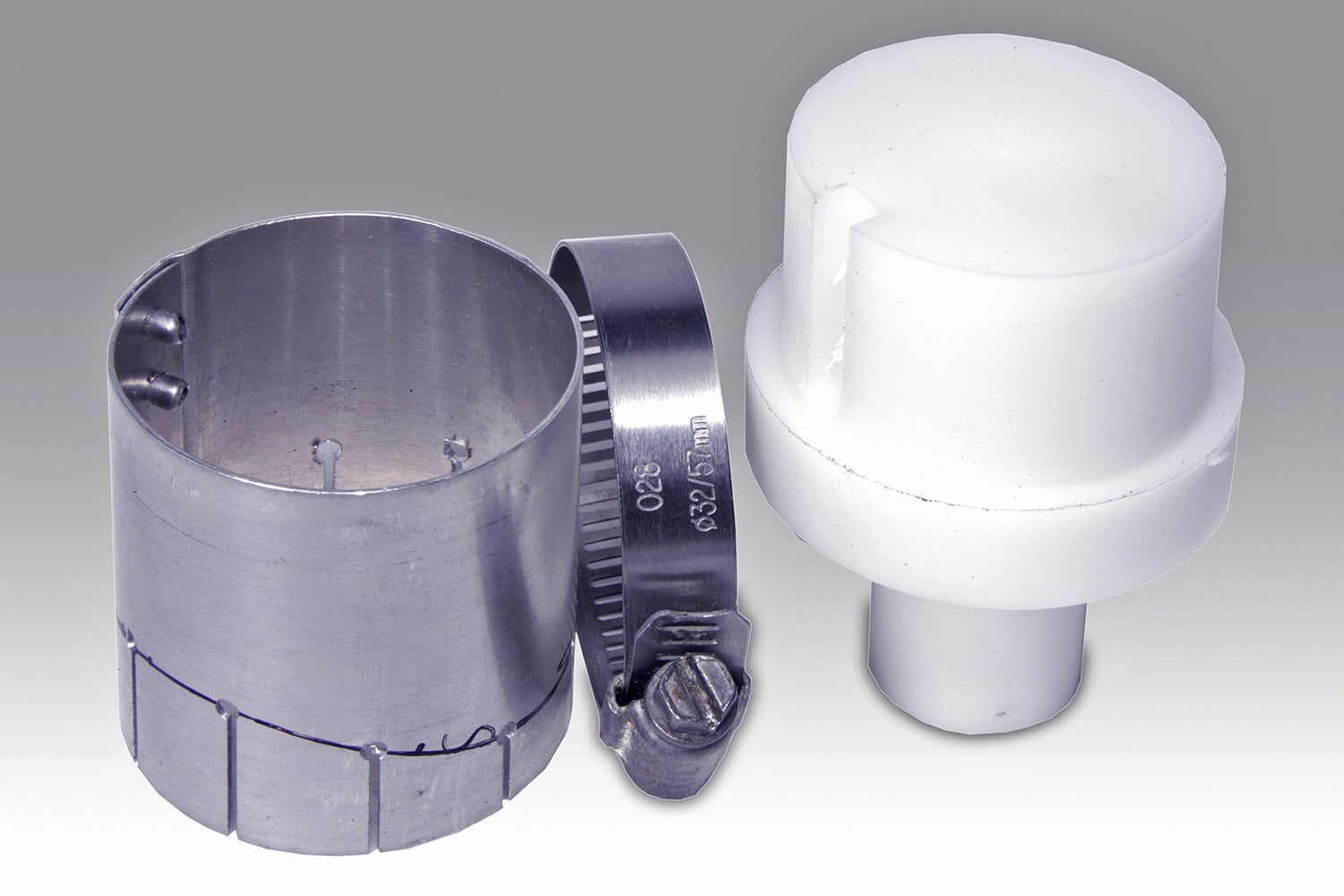
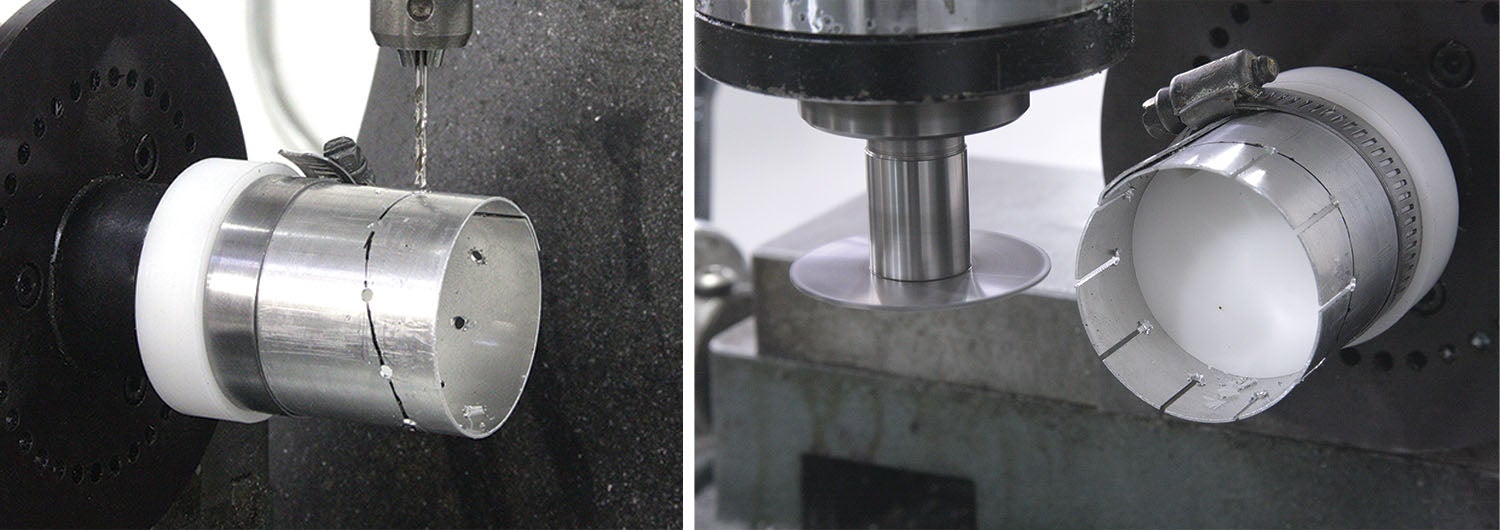
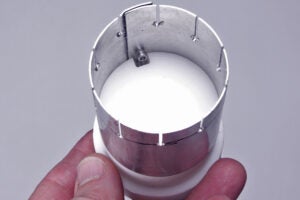
To prevent the cuff from collapsing and snagging on the hole saw, I made a large dowel to provide sacrificial support for drilling the cuff in the mill. I used a similar idea to hold the outlet tube in the indexer for drilling and slitting. But instead of wood and a wood lathe, I used my metal lathe and some 2-1/2-inch diameter Delrin rod.
It will probably be a few months before we can test the effectiveness of the cuff. As any pilot knows, for carb heat to be effective it must absorb enough heat from the exhaust system to raise the air temperature high enough to prevent ice from forming in the carburetor or melt any ice that does form.
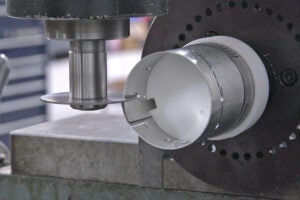
Confirmation will come during the initial run-up of the engine: With carb heat applied, we’ll watch the tach and listen for a rev drop (hot air is less dense than cold air, which results in less power for a given throttle setting). Hopefully the test will prove there are enough inlet holes for the engine to breathe and enough volume to provide sufficient heat. Only time will tell. In the meantime, get into the shop and make some chips!
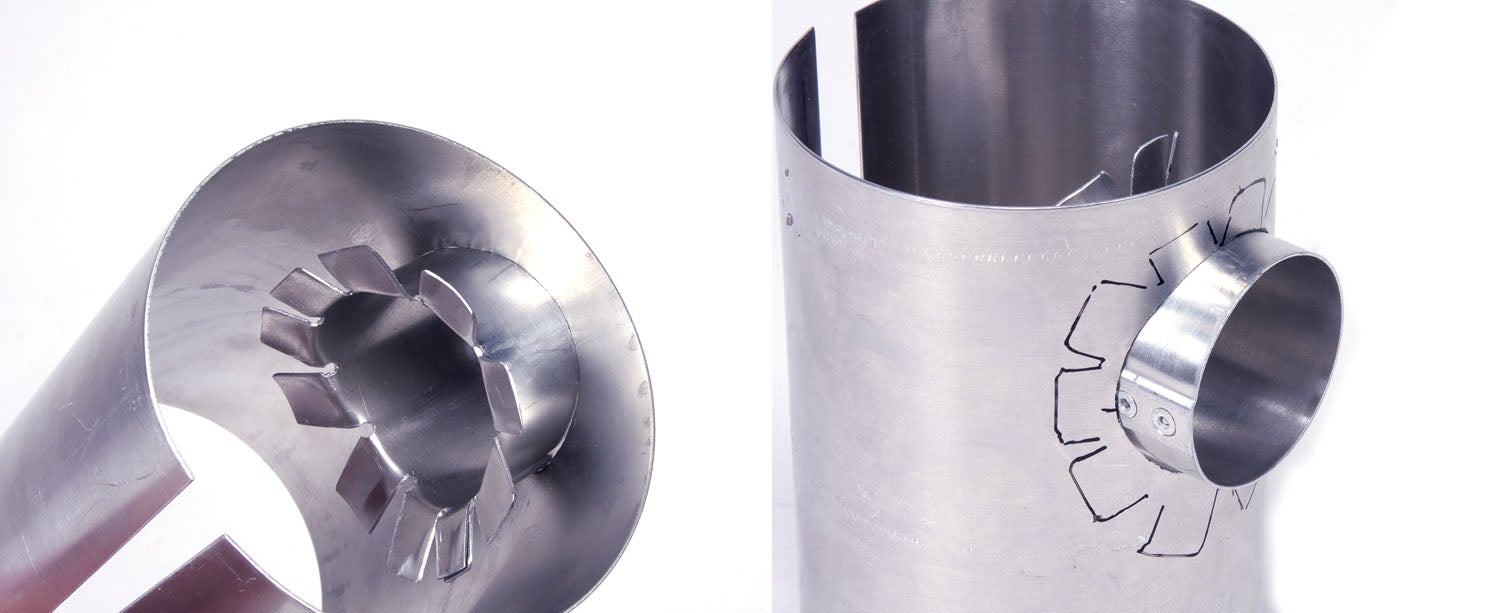
The title, “Ye Olde Slip Roll,” pays homage to the story of WW-II Captain Charlie Brown and his crew of the B-17 Ye Olde Pub as detailed in the book “A Higher Call” by Adam Makos.
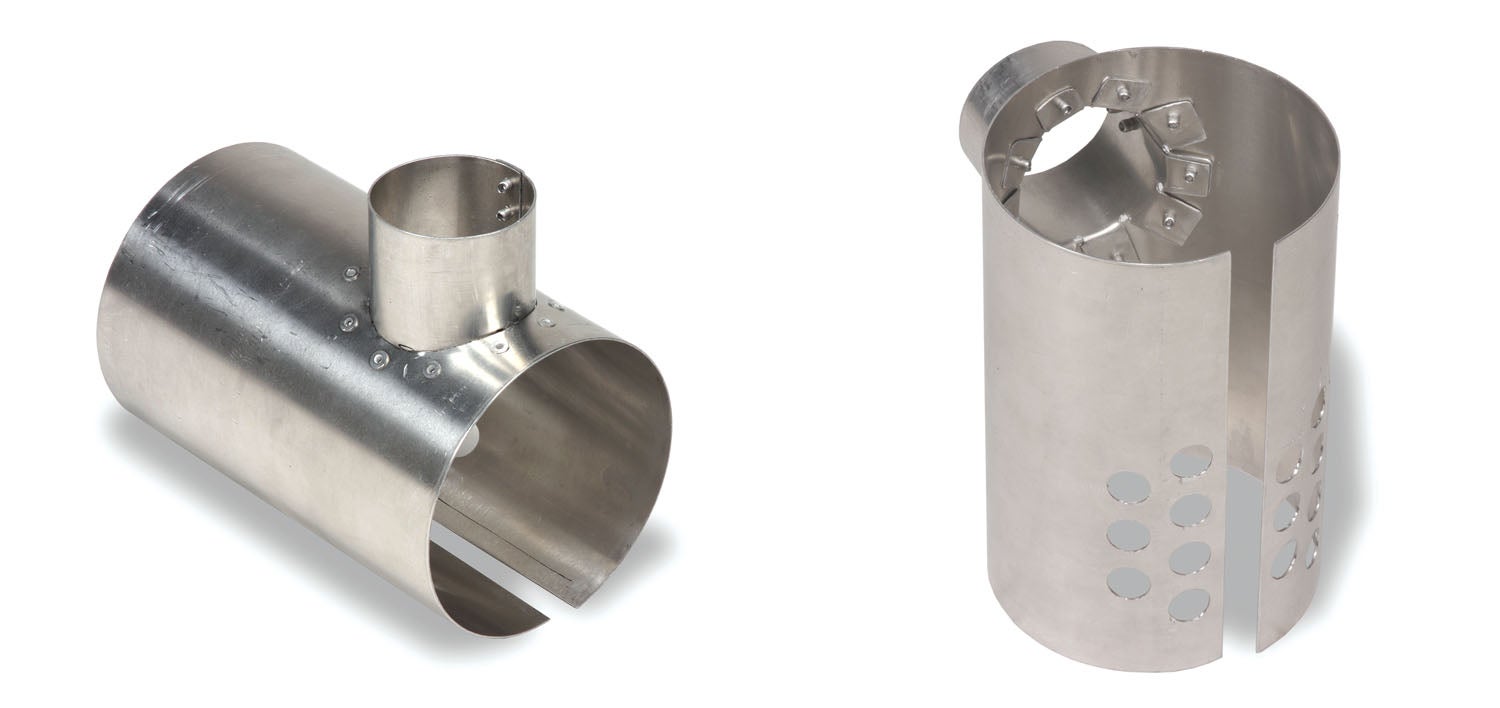