For the most part, we accept that the company providing our kit aircraft—or the people who penned the plans, should we be scratch-building—have done the hard work of inventing and then refining the design. Stuff they thought would work in the beginning, but didn’t, gets fixed as they go along so that the builder is, ideally, left with the mere task of putting the pieces together. In truth, the way early airplanes are designed and built is more the best guess of the designer, who is influenced by what he knows how to do, availability of parts for himself and the end builder—and cost. Everything is a compromise.
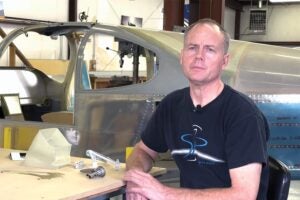
In today’s world of Experimentals, some builders move past “good enough” to the world of truly custom pretty quickly, while others are content to borrow bits and pieces from those Type-A personalities to make their own builds a little bit better. To a great degree, that’s where a company like Show Planes comes in. Based in Medford, Oregon, Show Planes was started by Bryan Milani as part of his builder-assist efforts.
“The beginning of our company goes back to 1984 when I helped my father build an RV-4. I went on to general aviation, working in an FBO and repair station, but I was really attracted to Experimental aviation,” says Milani. “I came back to it in the late 1990s and that’s when Show Planes started.” At that point, Milani had helped build a few airplanes that showed very well, making their owners happy and causing other builders to take notice of his approach and workmanship. “There was interest in some of the products I’d made for these aircraft,” he says, which led him to re-create these custom pieces for others.
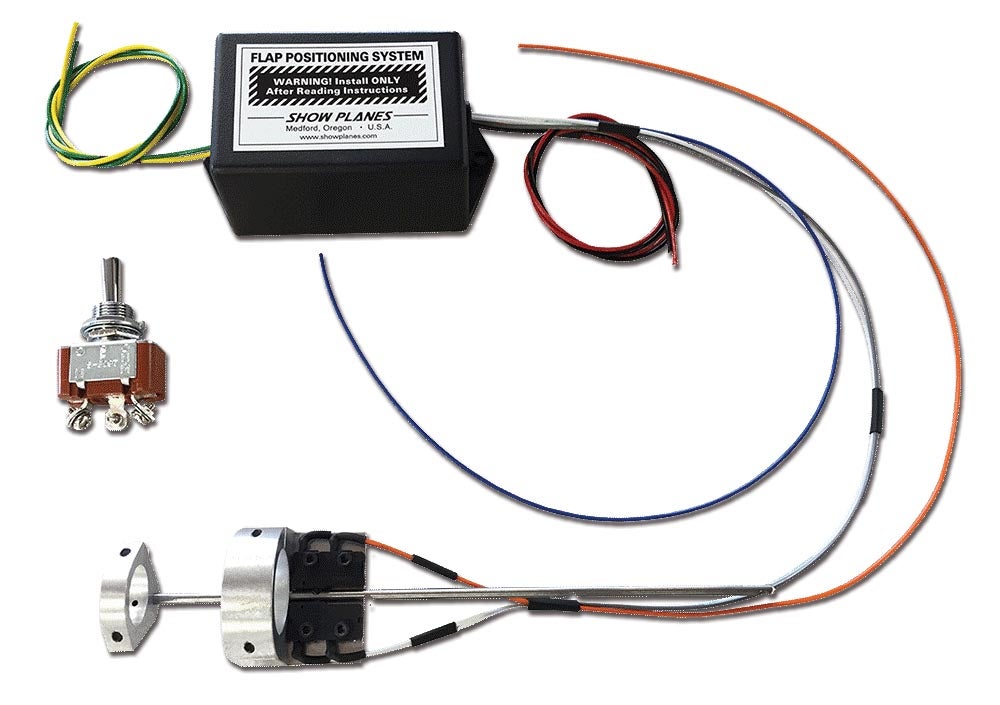
One of the first products Milani brought to market was a flap-positioning system for RVs—basically a control system for the electric flaps to provide preselected positions—that has been popular for almost two decades. It’s one of those clever, highly customizable accessories you wish you’d thought of first. But it was the fastback modification for the RV-8 that was a lot more visually obvious on the flight line. Replacing the upper rear deck and substituting a tip-over canopy for the standard slider on the RV-8 gave the airplane a new appearance and, according to Milani, was popular because it afforded better access to the cabin, especially for the rear seat. (A rollover structure between the seats takes the place of the windshield bow in the stock airplane.)
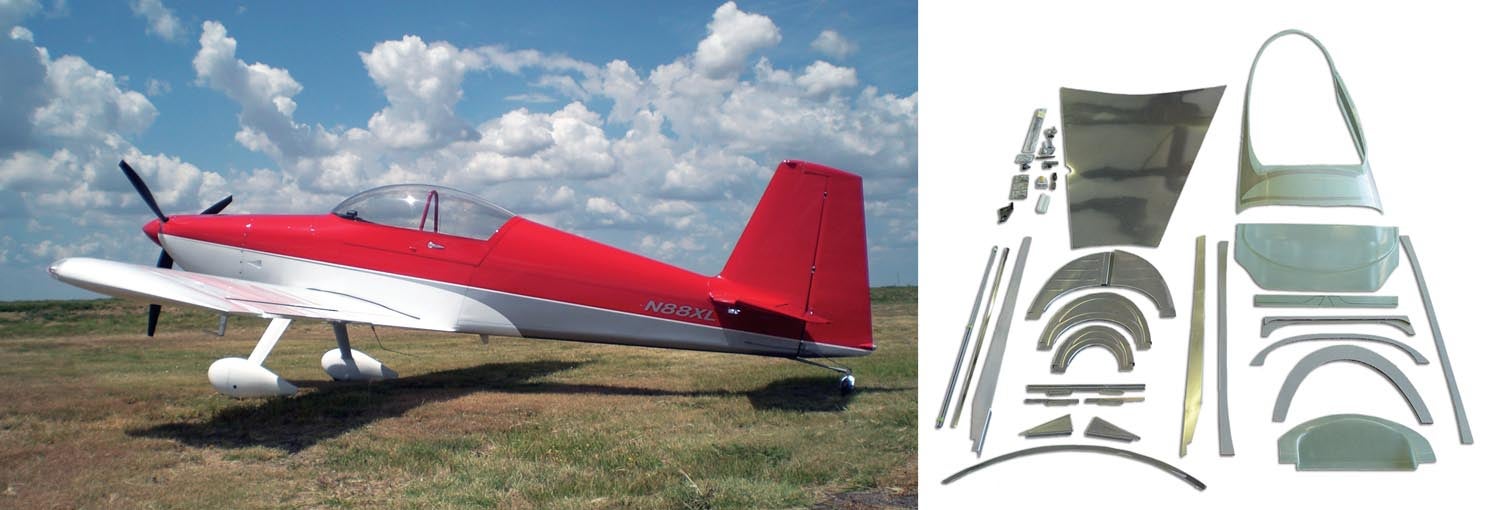
It’s less a knock on the stock RV-8 as it is a nod toward customization. As one veteran RV builder noted, “It’s P-51A or P-51D, which do you like better?” Milani notes that the composites are lightweight prepreg epoxy and the aluminum parts are precut and formed to simplify installation. The tilt-over canopy uses the standard Plexiglas from the RV-8 kit, though it’s obviously cut differently so this project, as a retrofit, will require a new bubble. The basic kit is $4100 currently.
Following much the same concept is Show Planes’ RV-10 composite tail cone skin. If you know your RV-10s, you know that the upper cabin is a fiberglass shell that tapers down to meet an aluminum upper deck that forms part of the tail cone. There is a noticeable kink as the cabin transitions to the tail cone.
With the Show Planes modification, the top of the airplane has a constant taper from cabin top to the base of the vertical stabilizer, all made in composite (for structural reasons there are aluminum reinforcements under the skin).
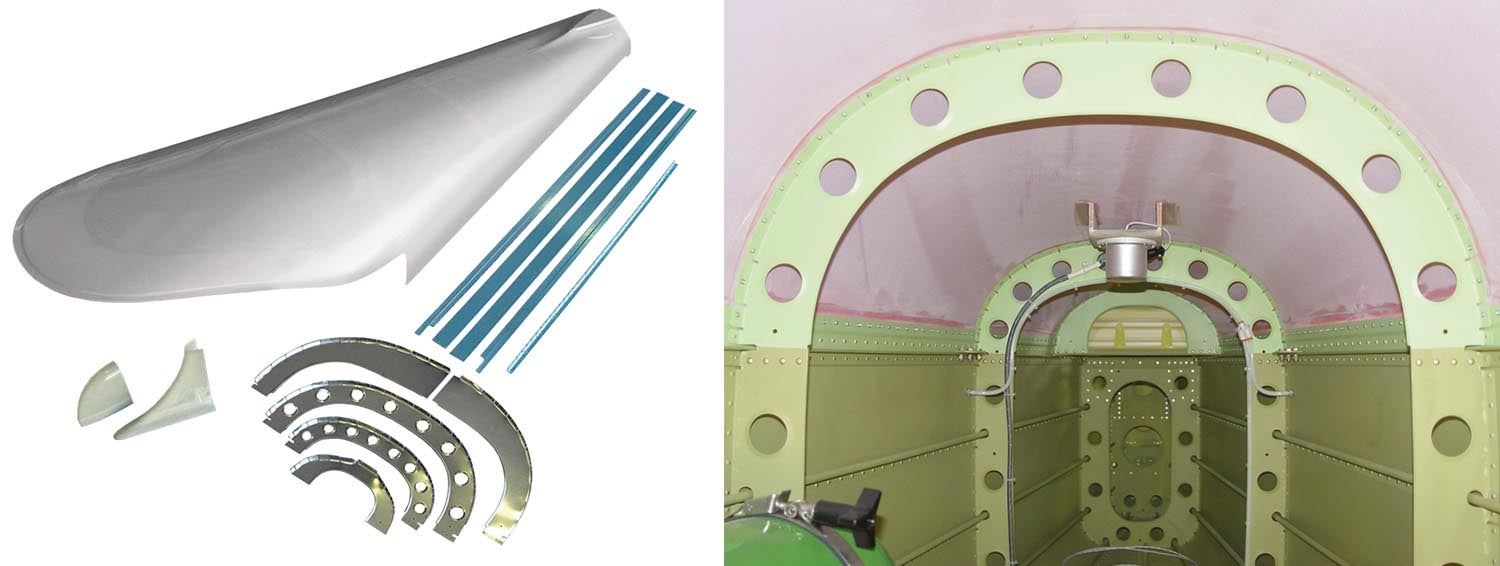
One advantage of the composite surface is that you can place sky-facing antennas farther back into the tail cone than you can on the standard RV-10. (Many RV-10 builders do place GPS antennas inside the cabin fiberglass, but this gives them more options.) But, truly, the biggest advantage is almost certainly cosmetic, which is enough for most builders. The kit costs just over $3000 currently.
At the other end of the RV-10, Show Planes came up with a new round-inlet cowling and a specialized induction to match. This was in part meant as a solution for forward-induction versions of the IO-540 that would not be compatible with the traditional inlet snout used by the vertical-induction models. “We did a lot of testing on this intake system,” Milani says, “and found it has very little restriction. I think we’ve duplicated the performance of having the scoop on the bottom of the RV-10 cowling” without actually having the snout. The cowling uses a 15-inch spinner to smooth airflow into the inlets and an expanded outlet section to help improve engine cooling. Induction air comes in through the main inlets through a pair of smile-shaped ducts that lead to reusable K&N filters. A similar cowling is available for the RV-8 and RV-8A. The RV-10 cowling is $2895 with the induction system an additional $895. The RV-8 cowling is $1985 currently.
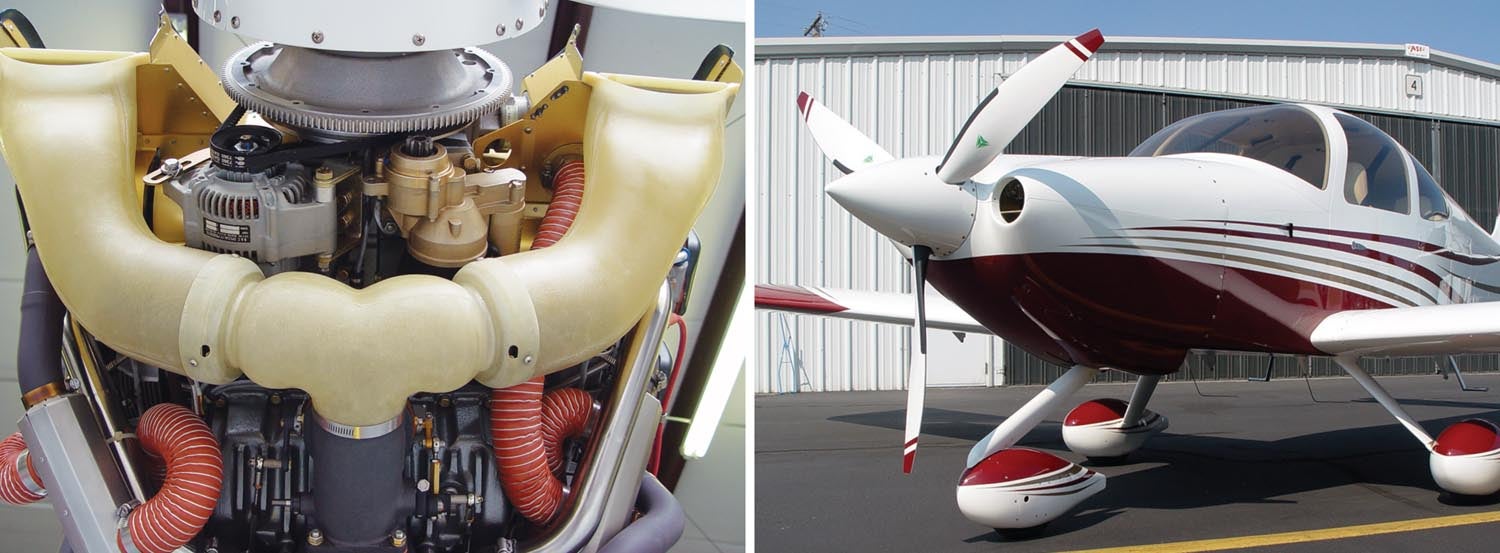
Small but Big Parts
Show Planes’ products represent quite a range but tend to focus on one of two aspects of building: finding solutions when a modification (or set of mods) “breaks” a factory procedure or creating a nicer, more elegant way to do something. I was aware of Show Planes from a few custom RV projects I’d seen but purchased my first SP product when I swapped engines in my GlaStar. I didn’t want to reproduce the Adel-clamp method of securing various sensors to the engine mount that was on my airplane originally. Nor did I want to move them to the central manifold since I already had the hoses.
So I found Show Planes’ transducer clamps, beautifully machined aluminum with an integral flare fitting and a 1/8-inch NPT. I used two of the $53 clamps—yes, that’s more than the Adel solution, but so much more elegant—for oil and fuel pressure. Later, when installing P-Mag electronic ignition, which needs a manifold-pressure source, I nabbed one of the $73 special transducer clamps that includes a barbed fitting for the MAP sense line. Sure, I could have cobbled together a bunch of AN fittings to do the same thing but, again, that’s not a slick solution. According to Milani, the clamp series came out of the desire to make “simple, all-in-one solutions” for what otherwise would be a stackup of fittings. “This reduces the chances for a leak,” he notes.
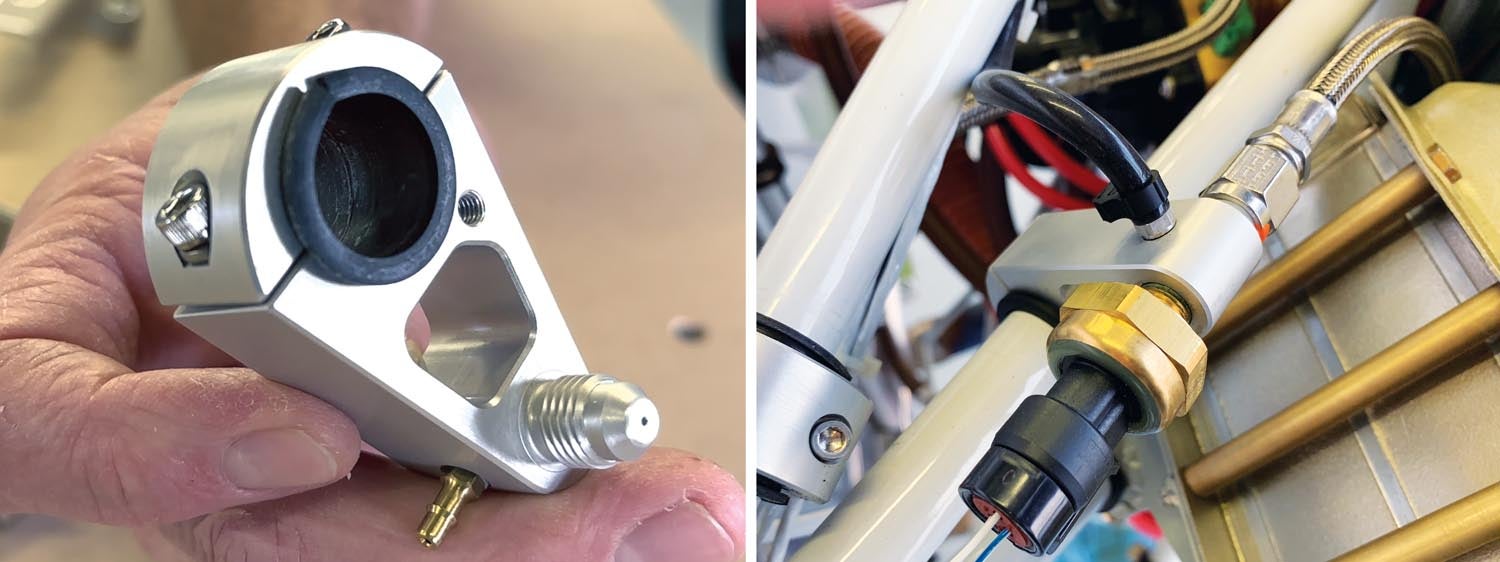
Another of Show Planes’ popular product lines involves oil cooler relocation. Many FWF schemes, in an attempt to keep things simple, mount conventional oil coolers to the vertical aft baffle. The thinking is basically sound in that you reduce the number of parts and can use shorter (and therefore lighter) hoses to and from the cooler. The problem is vibration, which can lead to cracking baffle pieces, even when heavily reinforced. What’s more, the oil cooler does not benefit from being attached to a 360-cubic-inch paint shaker. Finally, there is a practical limit to the size of cooler that can be mounted directly to the engine, with the common seven-row version often the largest.
Show Planes’ solution is a series of remote-mount schemes that combine a welded-steel support structure that allows the cooler to be carried by the engine mount plus a fiberglass baffle that ducts air from the common aft-baffle window to the face of the cooler. Obviously, a flexible seal connects the duct to the aft cooling baffle to accommodate engine movement. Because this system does not move the cooler very far from the original location, it may be possible to reuse existing hoses. The system is designed around the RV-7, RV-8 and RV-9 models to upgrade to a 10-row or 13-row cooler. Larger coolers are helpful either when the engine selected is a high-output angle-valve Lycoming (especially the IO-390, whose piston oil squirters really tax the cooling capacity of most installations) or the airplane is flown in persistently warm climates. “This has been a popular mod for airplanes already flying,” Milani points out.
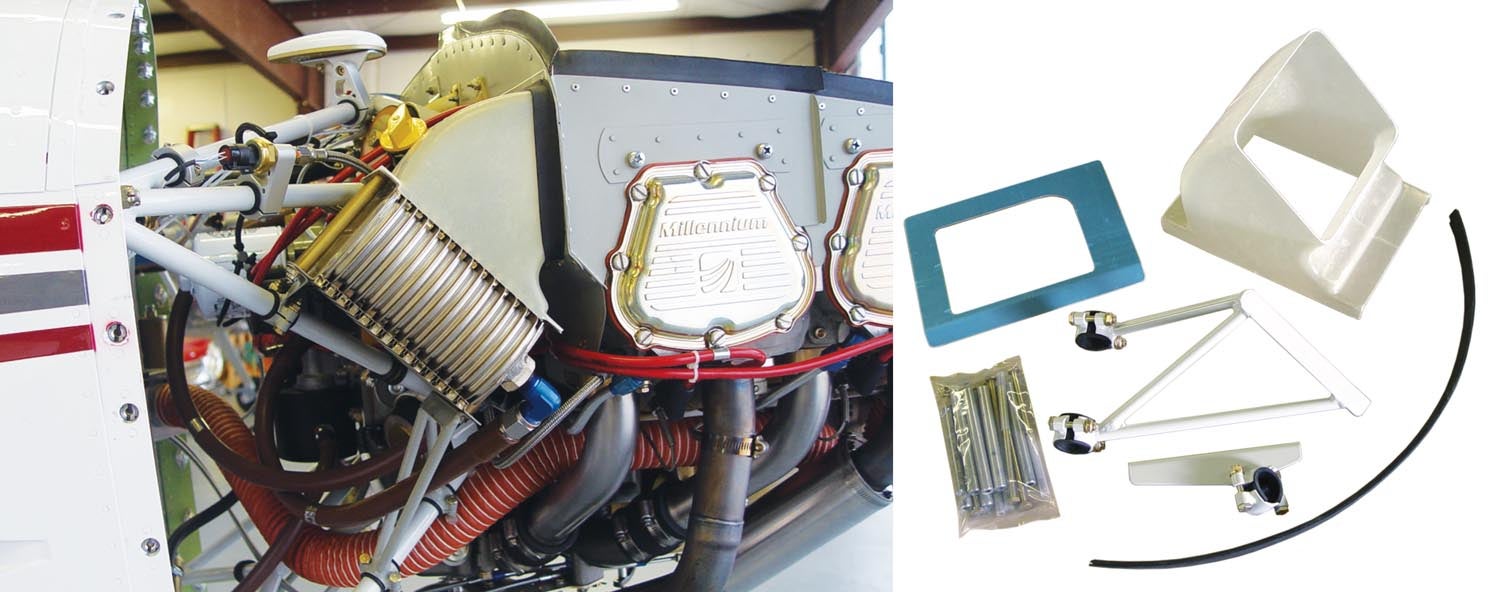
Of course, when you add cooling capacity sometimes it’s too much, typically in winter. Naturally, Show Planes has an air-control valve for its relocation kits. This simple rectangular butterfly valve can be ordered as the valve itself or as part of a kit with control cable and hardware. It mounts in the aft-baffle aperture upstream of the cooler. All oil-cooler relocation kits run $415 with the air-control valve kit another $215.
Following the theme of making simple solutions to vexing problems, Show Planes developed a handful of engine-control mounts for cold-air induction systems and prop governors. “These are things not already out there that could make their job easier. They wouldn’t have to create it.” If you’ve ever spent hours with a band saw and bending brake trying to make your own brackets—and, yes, I have—you’ll appreciate it when someone has done this work for you. Especially, as in the case of the throttle/mixture mounts, when there are multiple holes and mounting options to accommodate a wide range of systems and controls.

The Scale of Business
Milani runs Show Planes out of a large hangar on the Medford, Oregon, airport but his support structure is all over the state. The larger composite parts are crafted by local contractors with extensive experience in aviation. “The prepreg fiberglass with honeycomb cores we use requires large ovens under vacuum,” which is a capability he doesn’t have in-house. “We do try to use suppliers close to us, but when there’s only one or two guys in the industry who can do this type of product then we have to go wherever they are.” He has local companies do the laser-cut metal work as well as the CNC-machined components. Some of the smaller composite pieces are done in-house, and all pieces are brought to the home office for inspection and packaging. “We keep a really close eye on the products that come in and scrutinize them so we can catch any problems before the part gets to consumers.” And, of course, builder-assist projects take place there, too.
I asked Milani how he gets ideas for new products. “When we come up with a new product, some of it’s based on what people are talking about. We have the opportunity to build aircraft in-house here [as part of builder assist], which gives us an opportunity to fabricate and test. We can fly the product for many hours. We look at things that can make the build easier.” It’s also about differentiation and customization. “A lot of builders want something different and we try to cater to that, to give them a chance to stand out.”
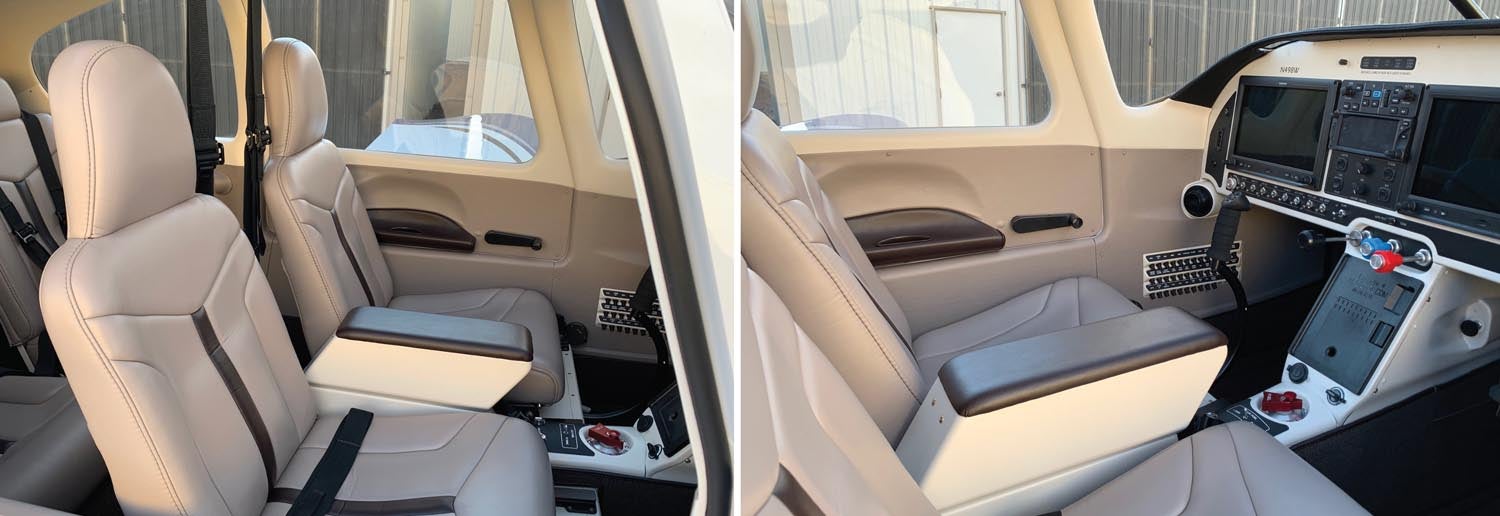
“Every time we go into the creation of a new product,” Milani says, “we’re thinking about how the builder is going to implement it,” meaning taking into consideration both new builders and retrofitters. And that drives some of the design choices because there have to be a few assumptions on what’s already in the airplane and how these pieces will fit. Obviously some, like the RV-8 canopy or the RV-10 composite tail cone, are better done during the initial build, but Milani says some have retrofitted even those projects. “We’ve had a few people do conversions on flying aircraft, where they had to repaint and things of that nature, but the desire was strong enough that it was worth the effort.”
“We’re always looking for new products. We probably have 10 to 12 products under development at a time. Some products are out for beta testing and feedback. That feedback really helps when we put together the instructions,” Milani says. Some of the changes from early design through beta and then to production spec focus on making the parts easier to fit and install. The ultimate goal is to provide solutions for builders who want to embrace customization. “Our business is really about enabling that customization. How can we just build upon such a great platform that Van’s has offered us?”
For more information, visit www.showplanes.com or call 541-773-3344.
Photos: Marc Cook and courtesy of Show Planes.