Since the beginning of aviation, various types of wires have been used for bracing aircraft structures. The earliest airplanes used solid piano wire, hay baling wire or whatever an amateur builder could scrounge, with varying results. But even early on, it was known that a streamlined (or airfoil) shape has significantly less drag than a round shape.
In 1909, Bruntons (now known as Bruntons Aero Products) in Scotland introduced the first streamline wire for aircraft use and since then, streamline wires have been the standard for wire-braced airplanes. In 1927, the U.S. National Advisory Committee for Aeronautics (NACA, the forerunner to NASA) tested the drag of several sizes of streamline and round wires and found that round wires have five to 10 times the drag of streamline wires of the same cross-sectional area. The numbers from the technical report are the basis of the analysis I’ll get into later.
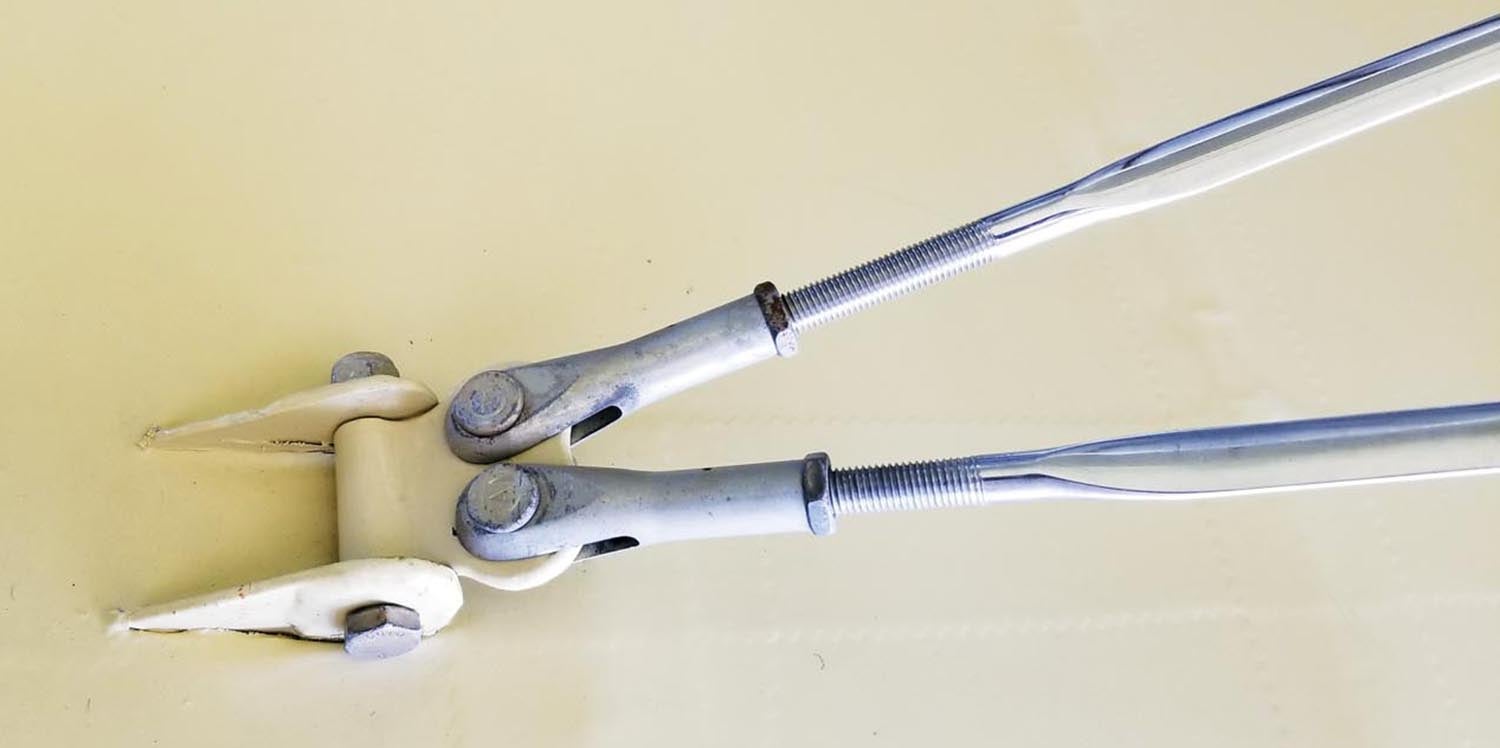
Back then, extensive external bracing was necessary due to the thin airfoil sections in use at the time. Most biplanes used wires, though many monoplanes and even a few biplanes used rigid struts. Improvements in aerodynamic science led to thicker and stronger wing sections, which required less bracing, and even fully cantilevered wings, the Fokker Dr.I and D.VIII being early examples. Today, wire-braced airplanes are all but obsolete, except for whatever it is that drives some of us to choose such an airplane. The lack of demand for streamline wires today has led to much higher prices, to the extent that a wire set is a significant portion of the cost to build a biplane.
It is likely that the cost of streamline wires was what led Gus Mihlebach, the builder of my Hatz biplane, to use cables (properly called “wire rope”) with swaged eyes and turnbuckles instead of streamline wires (which are properly termed “tie-rods”). Today’s turnbuckle prices might change the equation somewhat compared to 1987 when my plane was built and surplus hardware was more available, but still, cost-conscious builders are always looking for alternatives.
When I bought the plane a few years ago, people said the extra drag of round cables would cost me anywhere from 5 to 15 mph airspeed at any particular power setting, though nobody had any real data to back it up. I didn’t really care. Certainly my plane is no speed demon, but for a pilot whose goal is to go fast, a biplane probably isn’t the best choice anyway. When the question of cables versus streamline wires came up again recently on the Homebuilt Airplanes Forum, I was motivated to look into the details. The first thing to consider was the strength of the substituted wires. I had never done any analysis, trusting that Gus (who was an engineer like myself) had done the appropriate analysis when making the substitution, and the hundreds of hours of flight time the plane had accumulated tended to bear that out.
The Hatz drawings call for a mix of 5/16-, 1/4- and 3/16-inch streamline wires (AN675, AN674 and AN673, respectively). The original AN specification sheets have long been canceled, but Bruntons’ U.S. distributor, Steen Aero Lab, has a good summary chart on their website giving the basic dimensions and strengths for the various sizes.

Wire rope used for control runs around pulleys is usually flexible 7×7 or 7×19 cable meeting the MIL-DTL-84320 specification. For fixed bracing, non-flexible 1×19 per MIL-DTL-87161F not only has less stretch but is also slightly stronger and more abrasion resistant. Both are available in stainless or galvanized steel. The cables used on my plane, being 1/4-, 3/16- and 5/32-inch, are one size smaller than the streamline size specified in each case, but according to the specs they are comfortably stronger than the original streamline wires, so clearly Gus did his homework.
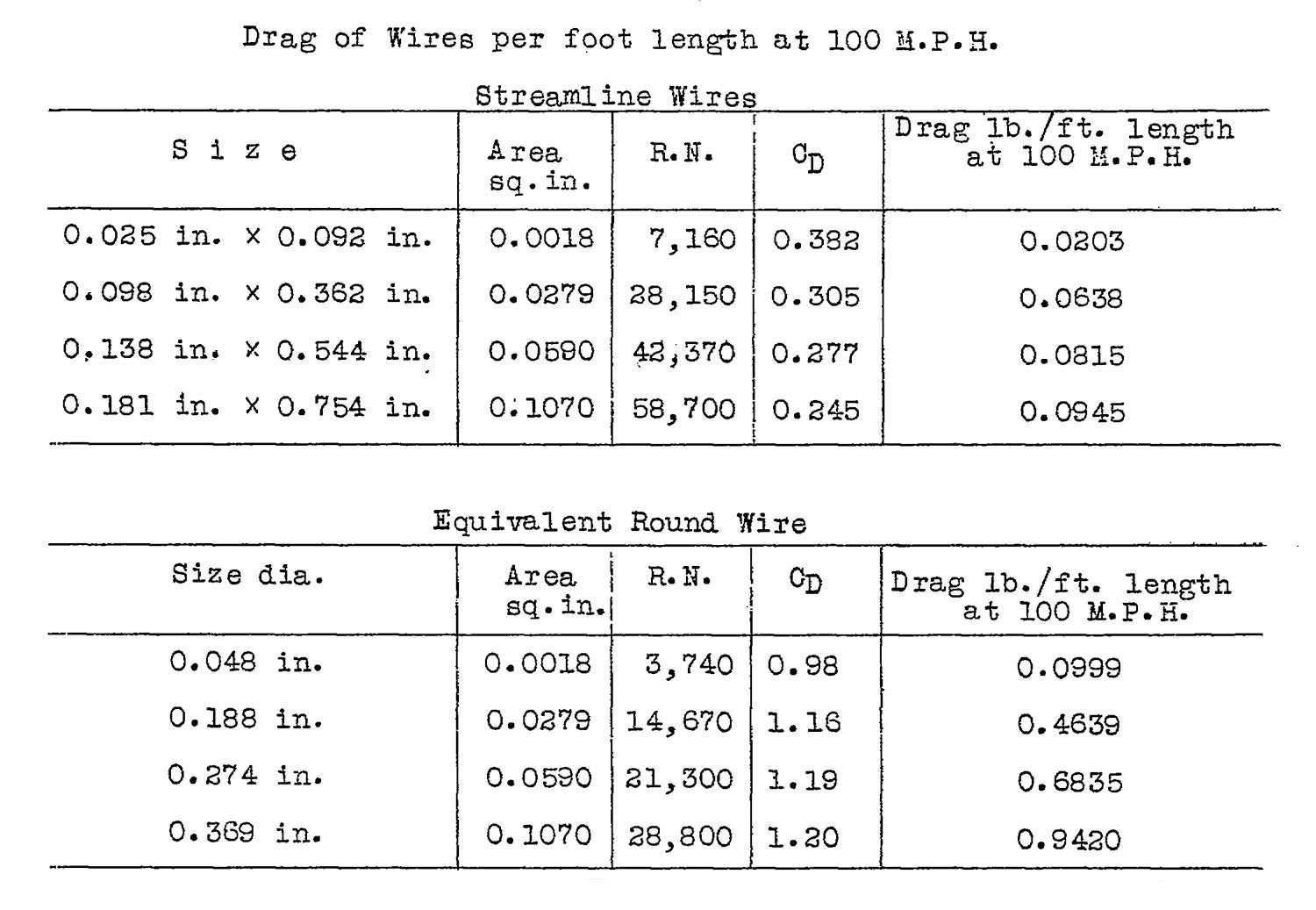
There is some question about the use of swaged (Nicopress) sleeves on 1×19 cable, and the MS51844 spec for the sleeves only mentions their use on the 84320 flexible cable. Some say to use two sleeves on 1×19 cable. In the old days Nicopress sleeves didn’t exist, and my 1940 book on aircraft maintenance details how to make eyes by wrapping with soft steel wire and soldering (flexible cables were normally terminated with a five-tuck woven splice covered with shellacked thread). On my plane, Gus used a single Nicopress sleeve on each cable end and followed them up with wire wrap and solder in the old way, so I’m not too concerned about the strength.
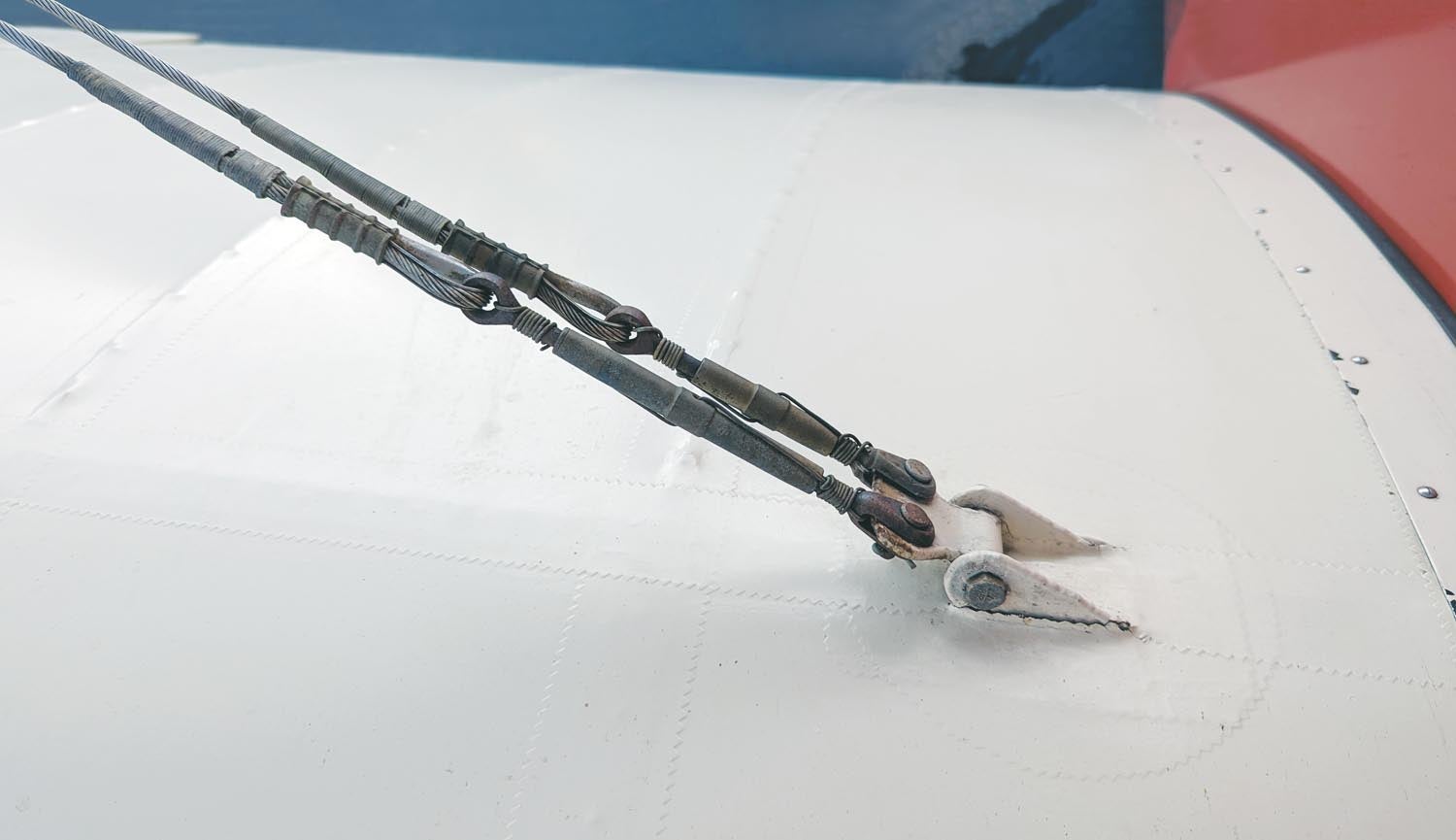
Performance Differences
Without testing both types of bracing on the same airplane, it’s hard to say for certain what the difference in performance will be, but with some assumptions we can get an idea. I started with NACA Technical Note #279 from 1927, and in particular the table on Page 49, which gives the actual drag in pounds per foot of wire length for each of the tested sizes at 100 mph. Since the tests didn’t include all the sizes used on my plane, I entered the data into a spreadsheet and interpolated to get the intermediate values. The surprisingly (for 1927 instrumentation) linear curves gave me confidence in the accuracy of my interpolated numbers.
With drag-per-foot values, I could add up the drag values of all of the wires on my plane. The difference is significant: 7.45 pounds for streamline wires versus 47.27 pounds for round wires, for a penalty of just under 40 pounds at 100 mph. Since drag is proportional to the square of airspeed, multiplying that penalty by 0.8 squared gives a difference of 25.48 pounds at my plane’s 80-mph cruise speed. Still, it’s a small part of the airplane’s total drag, but how small?
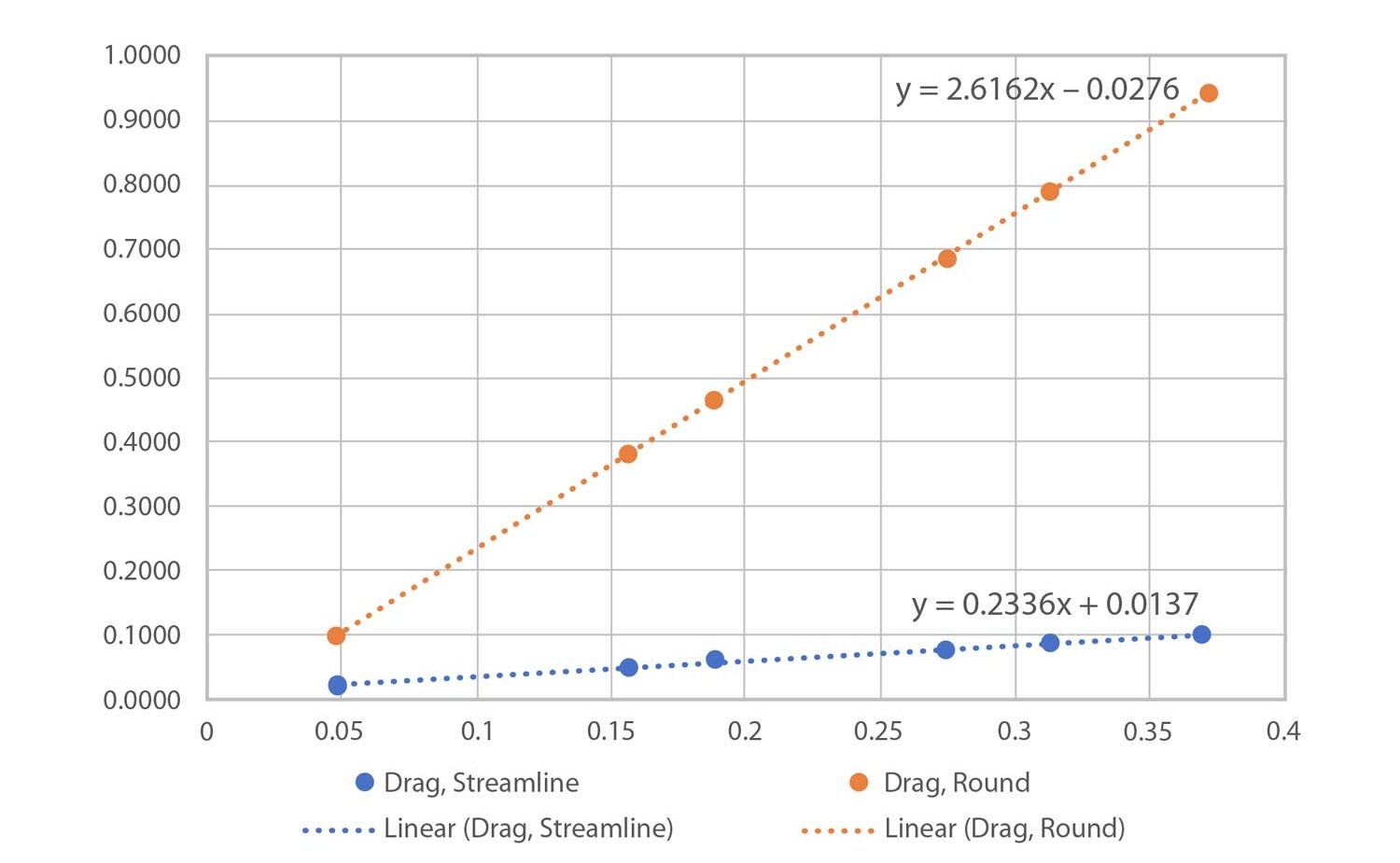
Absent design data or a detailed aerodynamic analysis of the entire airplane, by making some assumptions we can estimate the aircraft’s total drag from the observed performance. My plane cruises at 80 mph at 2250 rpm, which is 65% power according to the manual for its 125-hp Lycoming O-290-D, or 81.25 hp. Assuming a typical 80% propeller efficiency, that’s 65 thrust horsepower (thp). From this we can calculate (see sidebar) that the propeller is producing 304.7 pounds of thrust, so that’s what the aircraft’s total drag is at that speed.
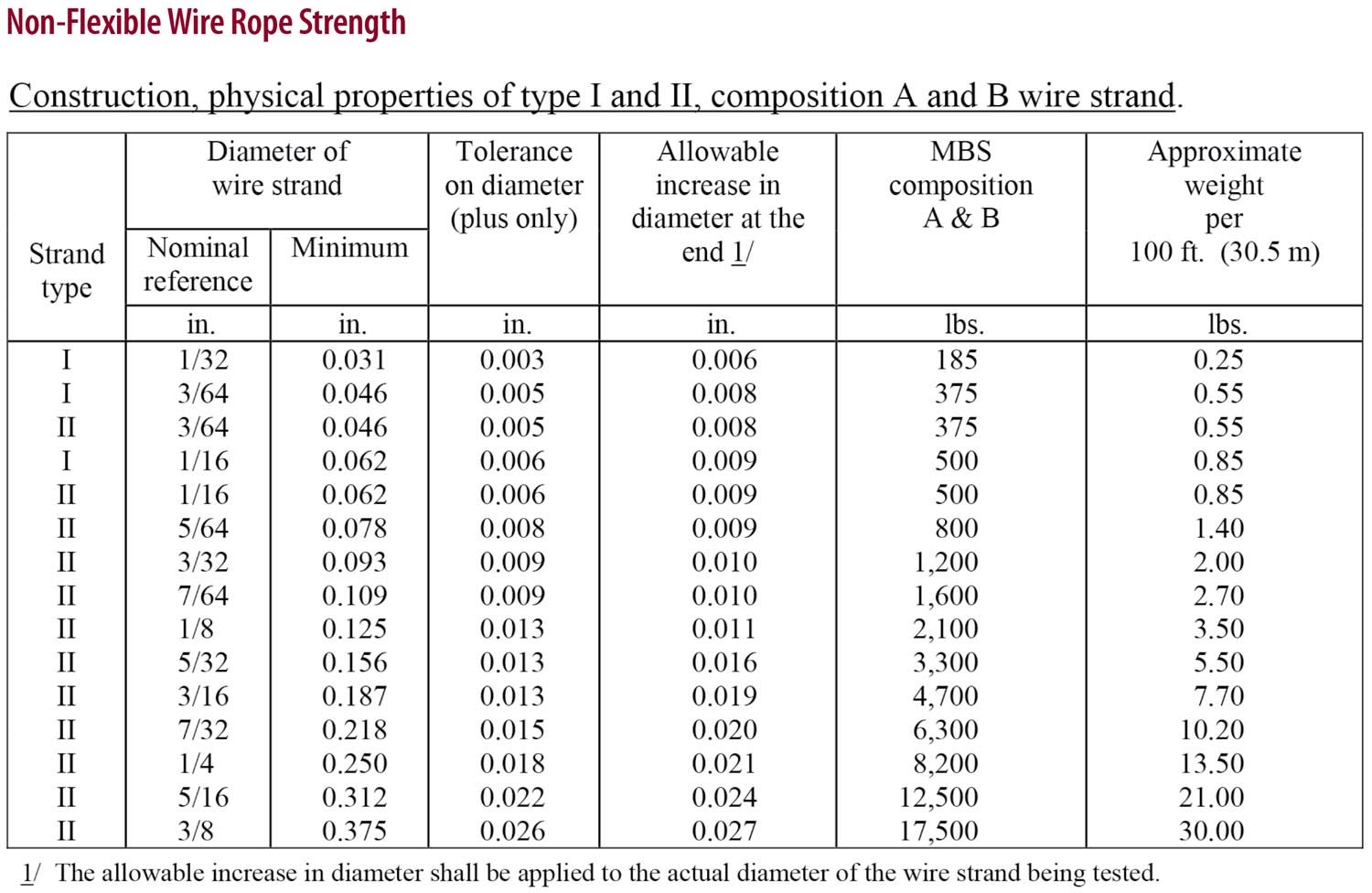
But wait: 65 thp produces 304.7 pounds of thrust only at exactly 80 mph. At higher speeds the thrust drops off if power is unchanged…but we don’t know how fast the plane would go with streamline wires; that’s what we’re trying to figure out.
The solution is to not use the drag values directly but to calculate the power cost of that drag. Applying the same relationships to the 25.48-pound drag difference, we find that 5.44 hp is being used to counter the additional drag of round versus streamline wires at 80 mph. Put another way, the same plane with streamline wires would require only 59.6 hp to fly at 80 mph, or with 65 hp it would go faster than 80 mph. Just how much faster is what we want to know.
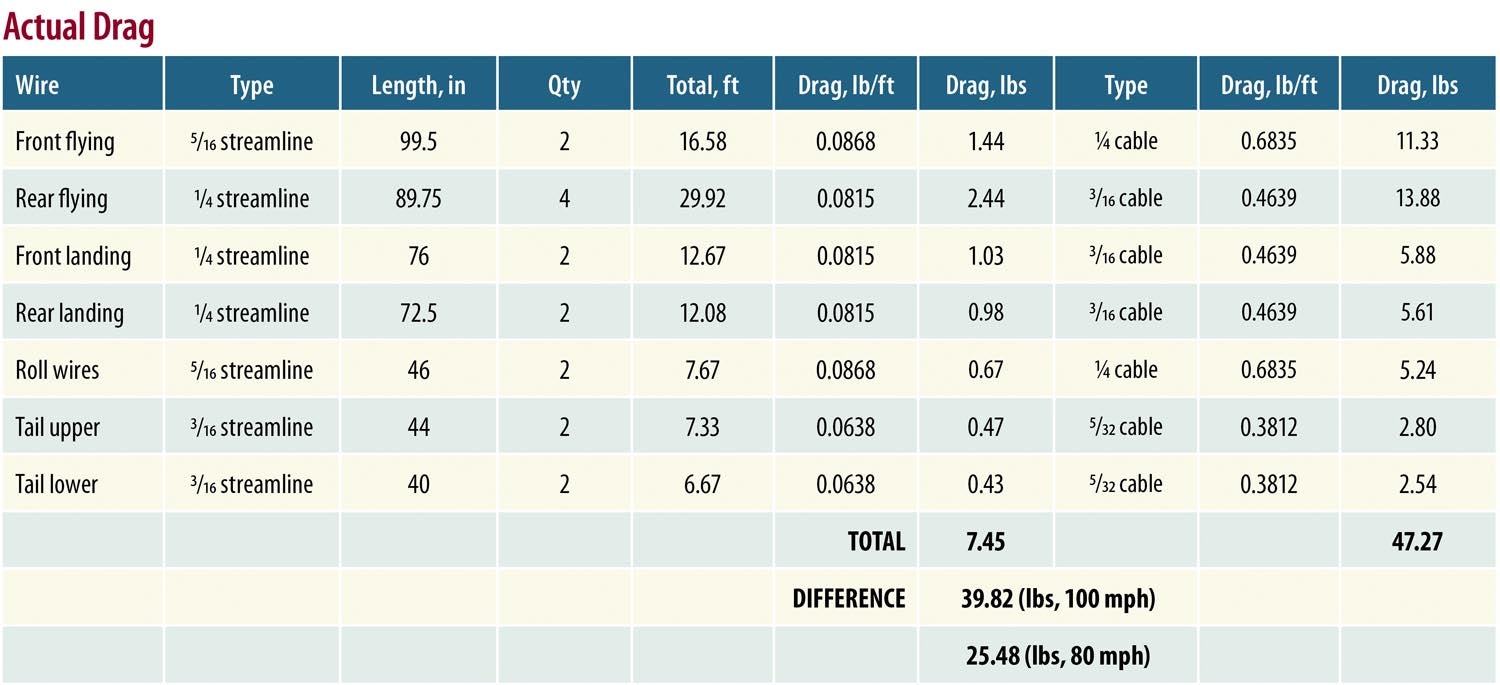
If we switch from round to streamline wires, it’s like getting that extra 5.44 hp out of the engine. So how fast would the plane fly on 70.44 hp? That part is easy! Since the power required to fly is proportional to the cube of airspeed as described in the sidebar, it’s a simple matter of taking the cube root of 70.44/65 and multiplying it by 80 mph for a new airspeed of 82.2 mph. That’s it—a $5000 wire set would give me a gain of just a little over 2 mph! I must say, I was surprised by this; I expected it to be a lot more. Of course, the faster you go, the more gain you get from reducing drag. A plane already flying at 100 mph would pick up just over 5 mph from the change, and at 120 mph the difference is around 10 mph.

More Considerations
Granted, the above analysis is fast and loose with a lot of rough assumptions. I assumed the propeller efficiency wouldn’t change with the airspeed change; it will but not by much over the narrow speed difference. I neglected the decrease in induced drag achieved by flying faster and thus a lower lift coefficient, but it’s only a 2.7-pound difference for a 5-mph speed increase (again making some rough assumptions), a small amount compared to the parasite drag. I also ignored any change in parasite drag with angle of attack. Again, it should be small over such a small AOA difference (about 0.5° for a 5-mph airspeed change).
I used the “pin-to-pin” dimension on the Hatz drawings, rather than the actual length of the streamlined portion, but that is offset to some extent by the additional drag of the eyes and turnbuckles on the cables compared to the single threaded terminal on a streamline wire. Finally, the NACA tests used smooth round rods, not stranded cable. I couldn’t find any data on drag of cables compared to smooth wires and it could go either way; the rough surface of the cable may increase drag, or it may actually decrease drag by delaying separation, like dimples on a golf ball or vortex generators on a wing.
Speed gains aside, another consideration is the effect of the reduced drag at the same speed. As noted above, it’s like getting an extra 5.44 hp, which improves climb. It works out to 128 fpm at the same 80-mph speed and power setting, though the improvement would be less at the normal (slower) climb speed. Or, the reduced power requirement for the same speed in level flight means reduced fuel consumption. Going back to the Lycoming manual, a 5.44-hp lower power setting means about a 1/2 gph reduction in fuel flow. There is also significantly less labor and room for error involved in installing solid tie-rods compared to cutting and swaging cables, installing and safetying turnbuckles, etc., which may be more important to an aircraft manufacturer than to a homebuilder.
So, are streamlined wires worth the price? For many people they will be. They look nice and have a significant effect at higher speeds, though the climb and/or fuel consumption improvements may be more important than any speed gains. Others, particularly builders of slower aircraft, may look at cables and say, “Good enough.”
Great article! Thanks so much for writing it. The sidebar on power, thrust, drag & performance is an excellent summary of the principles.
I like to also calculate what the drag is costing me per hour. The 5.4 hp is about 2.7 lb/hr in fuel or over $2/hr in avgas (if bought at $5/gal). For 40 hr/yr of flying, that’s $80 in fuel per year, plus increased wear and tear on the engine. I wonder what is the payback time for those nice Bruntons flying wires?
Good article, I have been carrying out electrical maintenance in the Bruntons factory around 20 years, I own & fly. CP301a Piel Emeraude, does not require wires but Bruntons have supplied other items, I always watch in interest every time I watch these wires being made, a lot of the equipment from early 1900’s. I have friends who I have assisted in the purchase of wires, Pits, S1 & 2 Booker Youngman, Isick Fury, Bruntons have also supplied the wires for the recently completed 1 1/2 Sopwith Strutter.
Nice article but streamlined flying wires have another plus – comfort. Try flying your Pitts Special at over 100 mph with cable rigging and the vibrations will make you want to leave the airplane.