I received an interesting phone call a few weeks ago regarding an RV-6A that was in the process of being towed to our shop. It had recently been purchased in California and flown back to Falcon Field a day earlier. It was here for a final training flight for the new owner, who was going to fly home to Auburn, Alabama, once the lesson was completed. Obviously, a long cross-country trip doesn’t allow many opportunities for air work, such as stalls and engine-out maneuvers, so this was the opportunity to complete the training.
During the flight from California, the pilots had noticed engine vibrations at varying rpm, usually most noticeable at startup and shutdown, but they seemed to smooth out at 2400 rpm. During the training flight, the vibrations got noticeably worse, and the decision was made to return to the airport ASAP. That was an excellent decision, as upon landing the propeller departed the aircraft!
I had left for the day, but my son, Nick, was still there. He remarked that he heard it making awful noises on final approach, sounds that he had never heard from an airplane. He lost sight of the aircraft behind some trees as it touched down, but another customer saw the propeller depart the aircraft. Luckily, the throttle was immediately reduced, and the aircraft landed without any further issues.
I couldn’t wait to get back to the shop in the morning to investigate, all the while thinking about how lucky they had been on the trip home. Surprisingly, the composite prop and spinner showed minor damage, and I was happy that the spinner was still attached as it meant the bolts should still be there.
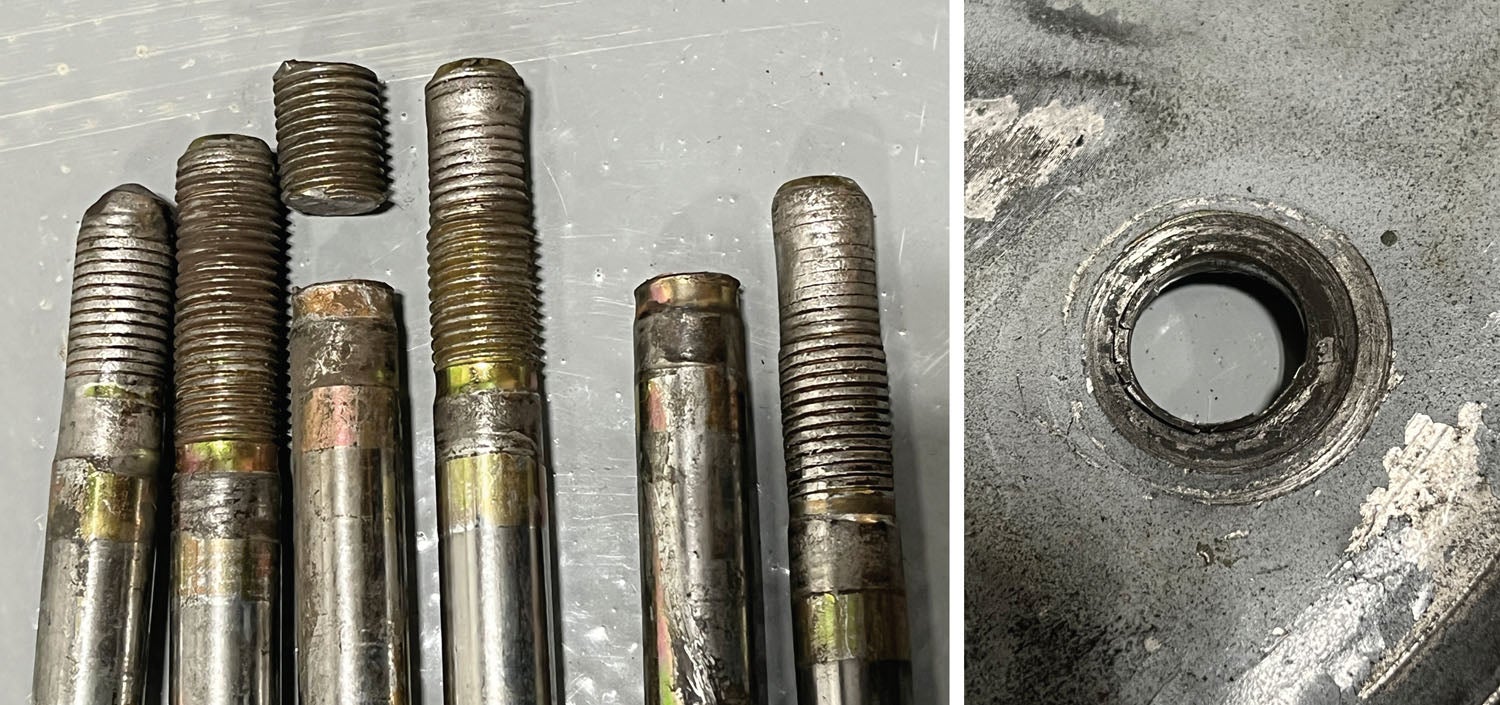
What Happened?
My initial thinking was that the prop bolts had not been properly torqued when it was installed. There is no logbook entry for the composite propeller installation. At some point we know there was a metal Sensenich propeller installed. Twenty hours prior to the sale, there is a logbook entry stating that a Sam James cowl was installed, along with a metal propeller crush plate “for W&B.” Allowing for the 10-hour flight since purchase, it had been flying for about 20 hours with the new prop prior to the sale. Every accident has a chain, and this one started here.
All the prop bolts were still inside the spinner. The safety wires had all been broken, and three of the bolts were sheared, with the remaining three all having been stripped of their threads. The aluminum spacer had severe fretting in multiple places, which is caused from the propeller being loose. The drive lugs on the spacer had “oblong” holes in the propeller. Clearly, this propeller had been loose for quite some time.
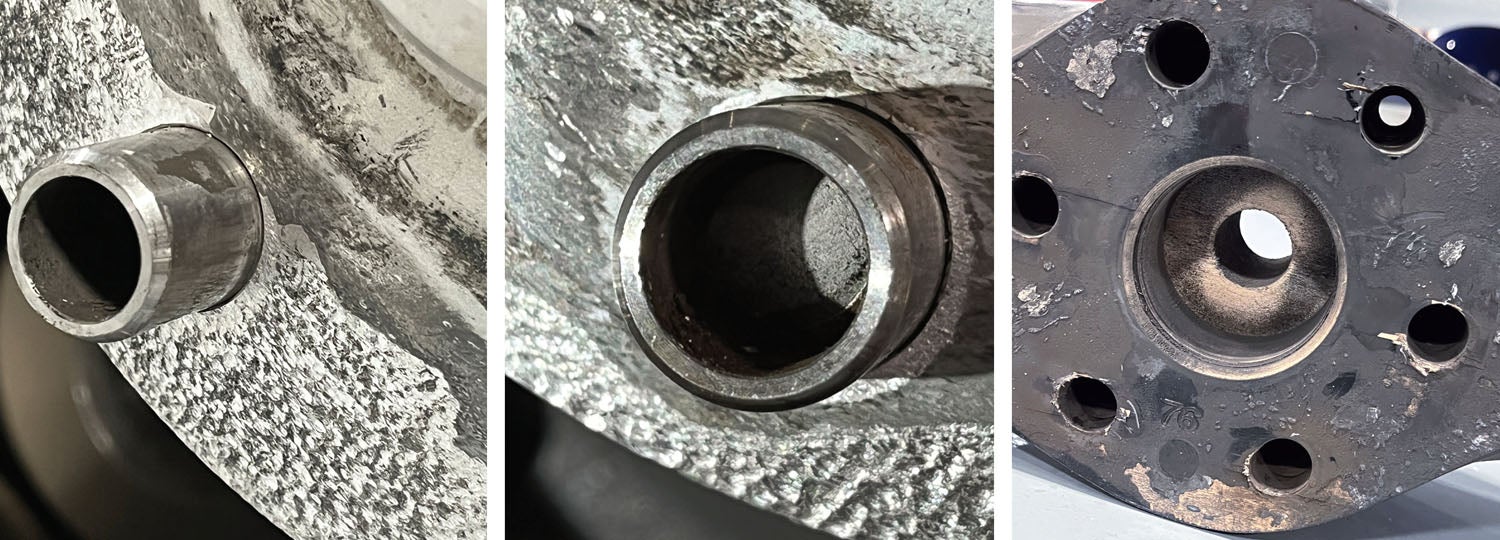
Careful inspection of the front of the propeller showed evidence of washer indentations into the propeller hub, indicating that the propeller had been installed at one time without a crush plate. Wooden and composite propellers require a crush plate! Keep in mind that a metal propeller had been removed, so there was no crush plate. I could also see that the forward spinner bulkhead was deformed from the bolts and washers, plus it was not an entirely flat bulkhead as is common on RVs. It had a little ridge on it, which I think came into play to set up the eventual failure.
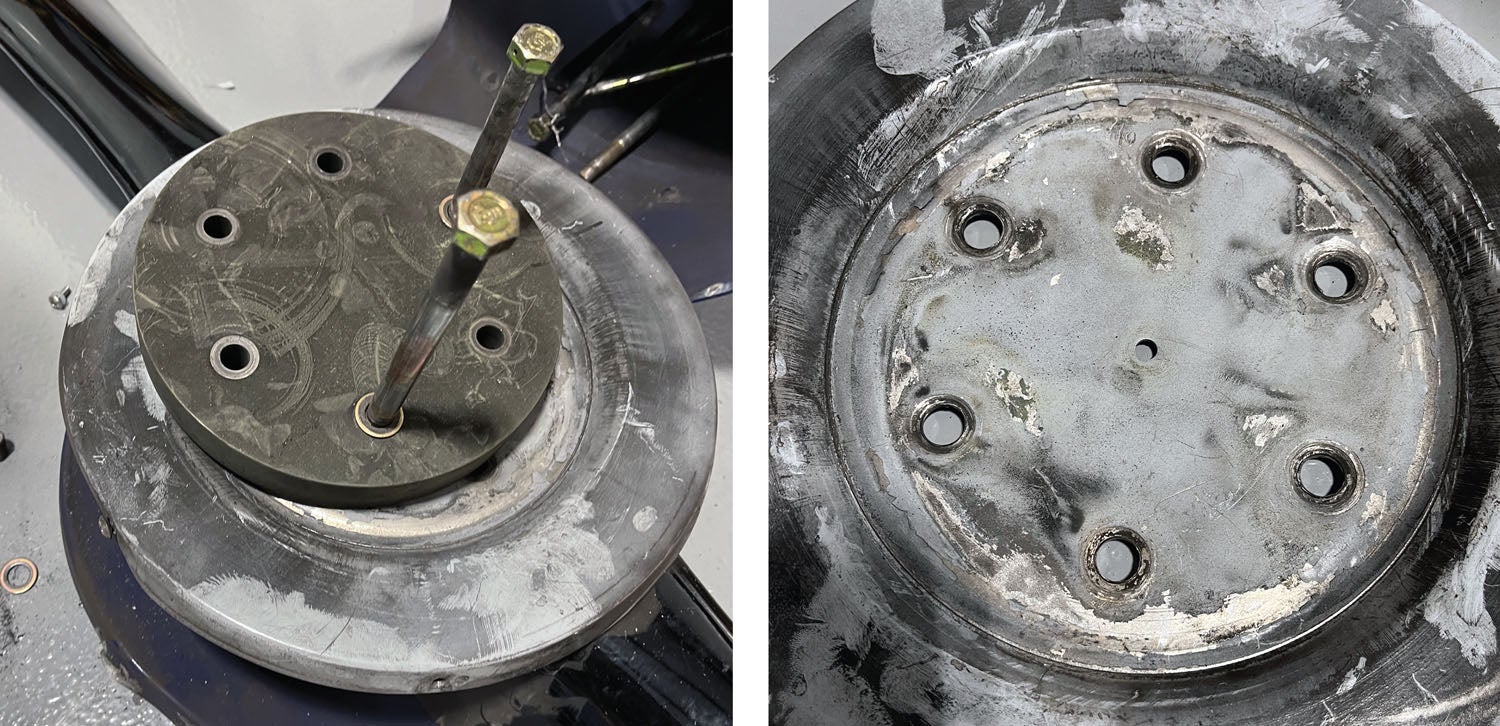
The installed crush plate for “W&B” was central to the failure. The problem here is that it was a 7-inch diameter crush plate, while the propeller needed a 6-inch crush plate. This 7-inch crush plate now sat on that ridgeline I mentioned, keeping it slightly above the propeller. Even with proper torque applied to the mounting bolts, there was no way this crush plate was going to fit tight against the propeller hub and properly secure the propeller to the flange. After 30 hours, it all finally let go.
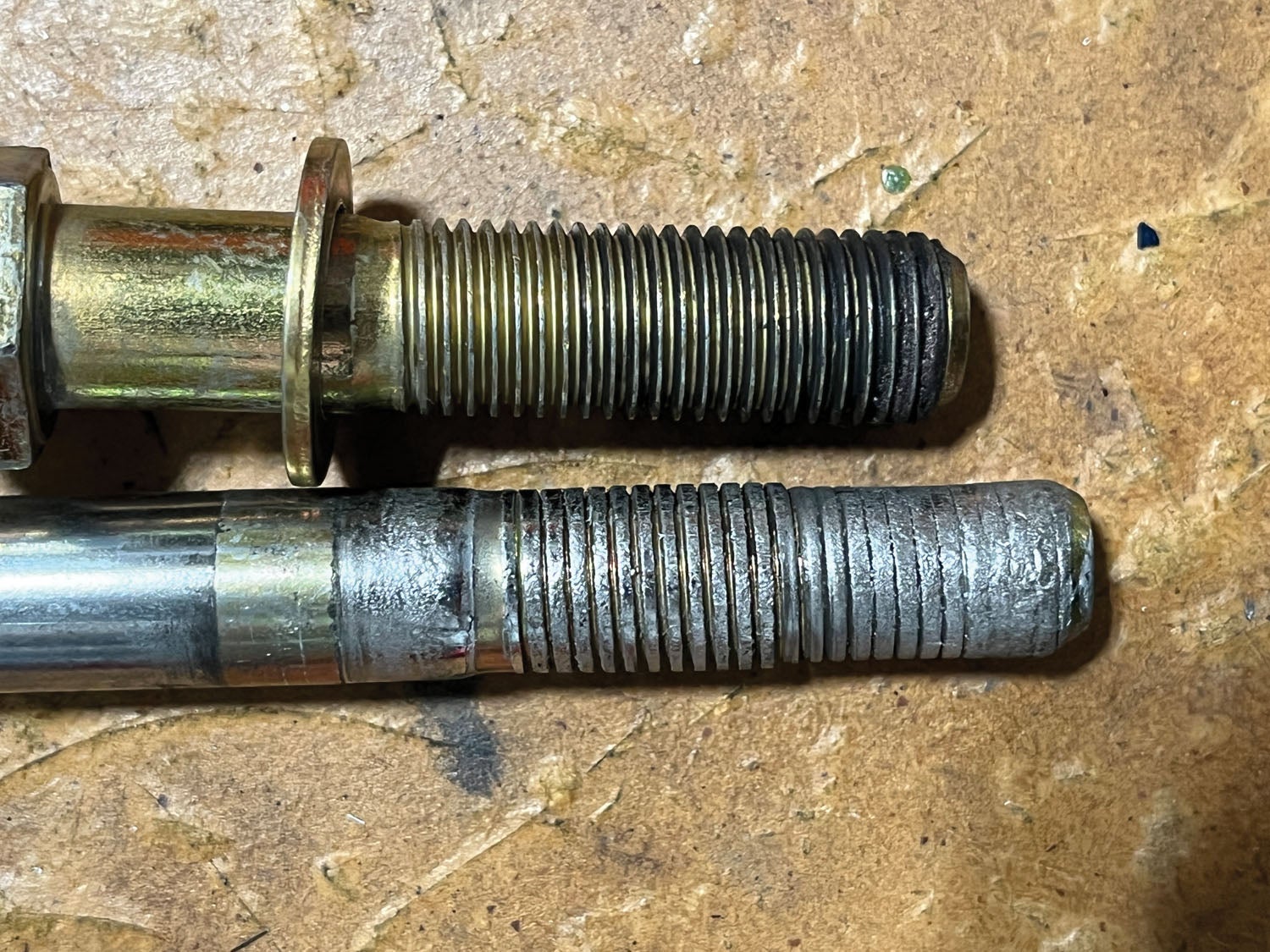
The Takeaway
There’s a big lesson here for new owners, whether you built the airplane or not. Yes, one of the attractions to amateur-built aviation is that we get to do our own maintenance and modifications without a lot of oversight. But we must remind ourselves that with that freedom also comes responsibility. Some changes and modifications have the potential to cause severe injury or death, and perhaps it’s wise to get some help or advice occasionally. Luckily, nobody got hurt here, but it is still going to be expensive as Lycoming has a mandatory engine teardown for propeller separation. The teardown and rebuild, along with labor to remove and install, will be close to $15,000.
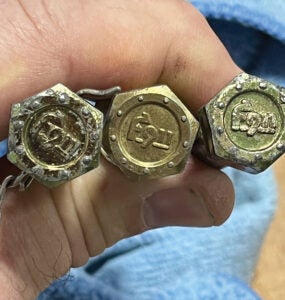
I also have some concerns with the bolts that were used. They are F911 bolts, such as are used in the auto racing circuits. The shorter bolts holding the spacer to the engine flange appear to be high-quality F911 bolts. The longer propeller bolts look to be cheap, even though they are stamped quite poorly with the F911 logo, and the plating is a different color and is flaking off. There is some noise out there that there are bogus F911 bolts being made in China. Propeller bolts usually have rolled threads, not cut threads. Rolled threads are much stronger, up to 35%. Look at the picture and judge for yourself.
I advocate that changing a propeller on an aircraft should be one of those times when having an A&P take a good close look at it would be a wise decision. In this case, a careful inspection of the parts that were removed would have indicated that they should not have been reused. If not an A&P, then at least find someone who has lots of experience. Single-engine aircraft have many components in them that are critical to the safe outcome of the flight.
This is one of those times that enlisting the services of an experienced person would have kept the fun factor alive much longer. Luckily, the pilots didn’t suffer any injuries.
Excellent points. Ignorance can be very costly.
A friend noted a ‘rattle’ as he tapped the spinner, as he was pre-flighting his PA-28. He and an A&P removed the spinner and noted that the front spinner mounting plate had 3 large cracks, going through the prop bolt holes. They removed the prop bolts and noted that the cracked edges of the mounting plate had caused fretting corrosion of the prop face , deeper than the allowed limits.
The result was a red tagged prop and now , $5,000+ for a new prop and spinner mounting plates, and a couple of months waiting for the new prop to be delivered.
For composite or wood props, in addition to the required crush plate, I would recommend using Belleville washers under the prop bolts. That’s become SOP in the canard community after a prop departed a Cozy at altitude, resulting in a successful engine-out landing at a desert airport. Some engineer-pilots have worked out the exact part numbers and torque schedule.
A pre flight shake of the prop would not have been a benefit?
You know where I live can you get the airplane to me ?
If before you
Chinese counterfeit parts are at epidemic portions. They will counterfeit anything.