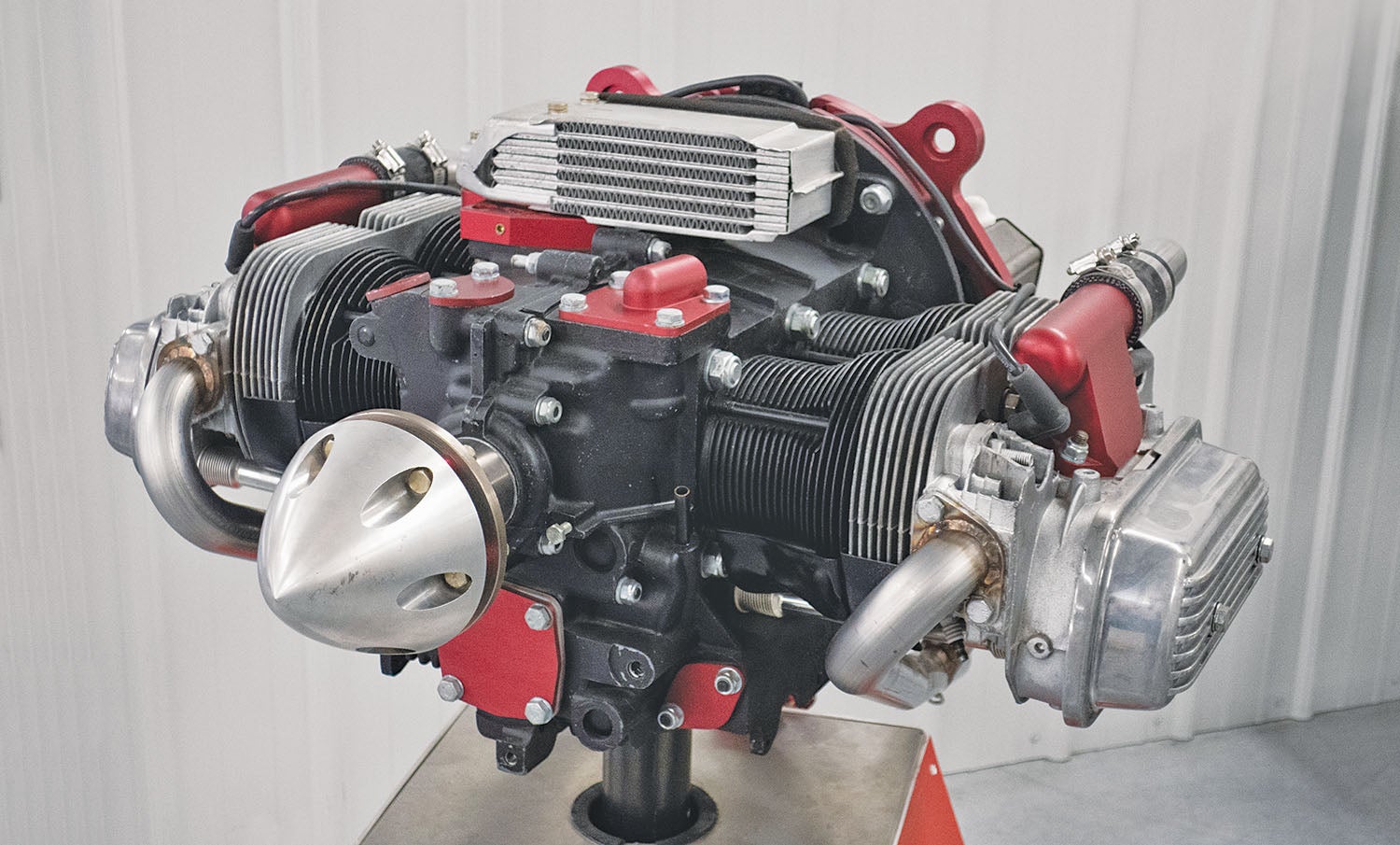
April 2022 marks the 20th anniversary of the first AeroConversions AeroVee 2180 engine kit delivery. Over those same 20 years, another generation of homebuilders has spawned into a hobby that continues to evolve and drift further from its roots as the realm of tight-budgeted do-it-yourselfers with a penchant for scrounging. Like steam gauges and fabric-covered wooden airframes, the AeroVee engine kit is a touchstone to those roots, sans scrounging. To properly mark this anniversary, however, we must first look back nearly 60 years. The AeroConversions AeroVee didn’t spring from nothing; it has a back story.
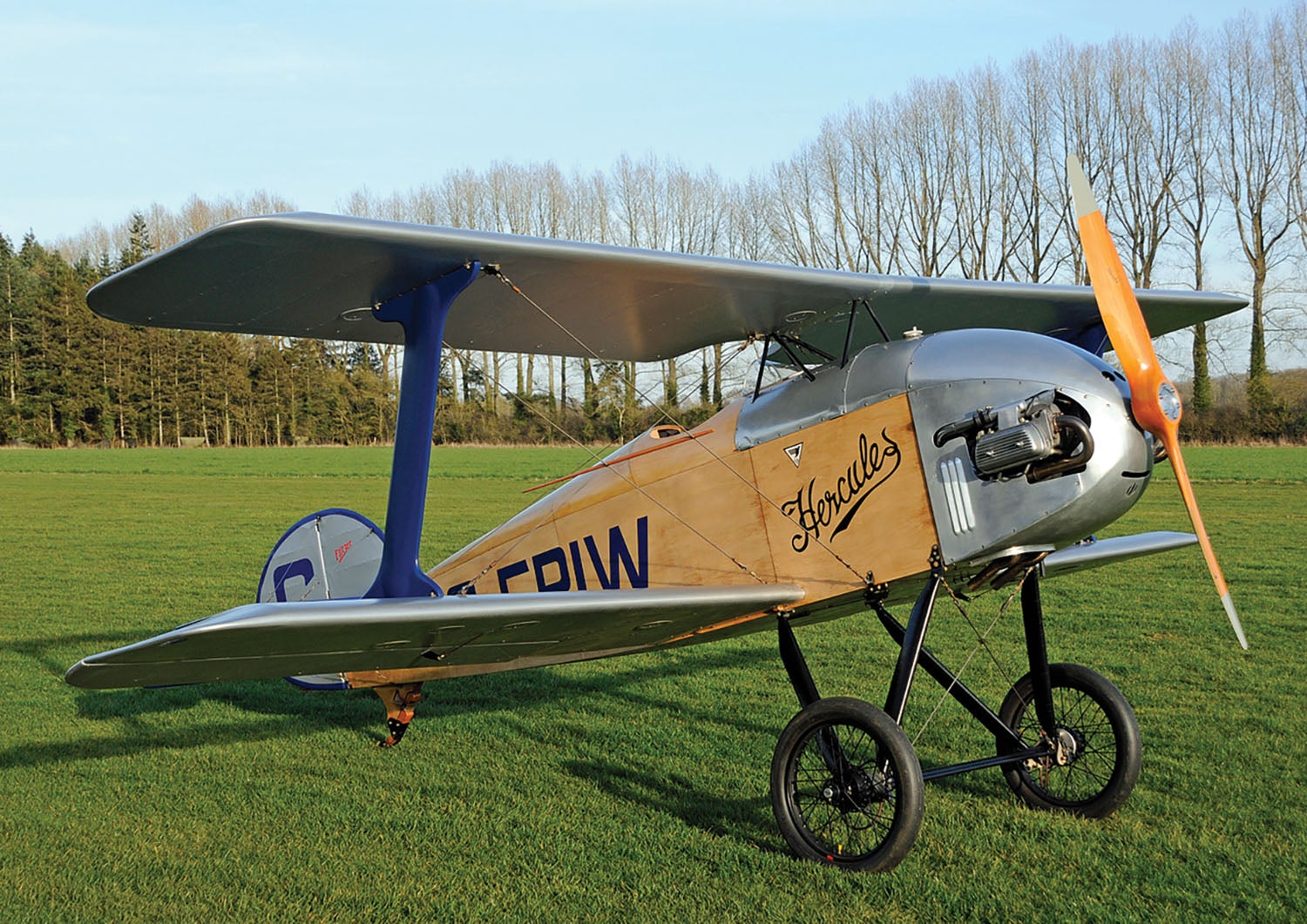
VW Conversions Emerge From Homebuilding’s Primordial Soup
AeroConversions founder John Monnett was an art teacher sculpting a Midget Mustang in the mid-60s when it became clear his teacher’s salary made no accommodation for a $10,000 airplane. He pivoted to the Jeannie’s Teenie, which was featured on the cover of the May 1968 issue of Popular Mechanics magazine with the heading, “Build a VW-Powered Plane for $600.” (Also on the cover, “Protecting Yourself from Highway Booby Traps.”) Though still in their infancy, VW-based aircraft engine conversions were gaining an ardent following. The Evans Volksplane, as its name implies, was designed in 1966 specifically for VW-based powerplants.
Monnett recalls the first conversion he saw, in 1966, was fitted to a Taylor Monoplane. Drawn, particularly, to the pioneering conversions of Robert Huggins, Monnett fitted his Jeannie’s Teenie with a junkyard-sourced engine (as was the norm in those days) converted to Huggins’ specifications. John and his Teenie attended the 1970 EAA convention. There, upon seeing Steve Wittman’s V-Witt Formula Vee racer and speaking with him in the shade of an oak tree about VW-based conversions, he decided to design a Formula Vee racer. That effort birthed the Sonerai.
Under the tight, self-imposed deadline to complete the aircraft in a year, John postponed his secondary goal of developing a VW Type 1 engine conversion to power his new racer. The Sonerai debuted at EAA’s 1971 convention powered by an engine from Ted Barker Experimental Engines. John describes that engine succinctly, “pathetic.” The Sonerai spent a great deal of the convention with its nose buried in Barker’s tent, getting engine issues sorted. The experience further fueled John’s desire to develop a VW-based conversion of his own, one he dubbed “AeroVee.” A wellspring of bolt-on AeroVee-branded components was designed and marketed through John’s newly minted Monnett Experimental Aircraft company. Budget-minded builders had yet another source of parts to make old Beetle engines fly.
With hindsight and characteristic bluntness, John calls that approach folly. Engines not suitable for ground transportation were recruited to fly. AeroVee-branded parts were bolted to engine cores of varying displacements and quality. Engine failures were attributed to AeroVee engines simply because AeroVee-scripted valve covers—sometimes the only AeroVee part on an engine—were bolted to their cylinder heads.

The AeroConversions AeroVee Emerges
The March 1996 issue of Sport Aviation magazine noted that Monnett, whose Monnett Experimental Aircraft-cum-INAV company closed in 1987, was developing a new aircraft. To power his new airframe, the Sonex, John fell back comfortably on the idea of a VW-based powerplant conversion, an updated version he would develop in tandem with the Sonex.
Monnett’s requirements for his new conversion were that it be lightweight, streamlined (you can’t go fast and have a sleek cowl if there is a distributor jutting up like a rhinoceros horn) and the core parts—the bits that make and transfer power—be unmodified, mass-produced parts that were readily available and inexpensive. For those parts, the thriving VW aftermarket community was tapped. For the conversion parts, modern materials and manufacturing techniques were employed.
History was repeated in 1998. Monnett’s new airframe broke ground powered by an understudy—a Jabiru 2200. His reimagined 2180cc, 80-hp VW conversion wasn’t baptized by flight until June 25, 2000. The next two years were spent testing, debugging and kitting the engine. Its availability as the AeroConversions AeroVee 2180 (a.k.a. AeroVee 2002) was announced in the spring of 2002. Twenty engines were delivered that year, many to quench the pent-up demand of Sonex builders.
The AeroVee 2180 continued the decades-old homebuilding tradition of employing the readily available VW Type 1 engine as a simple, affordable platform for an aircraft engine. Unlike VW conversions of the past, however, Monnett had no intention of selling individual AeroVee 2180 conversion parts or plans to builders who wished to convert a donor engine of questionable pedigree, nor would fully assembled engines be offered. Having learned from the lessons of the past, the AeroConversions AeroVee, marketed by Sonex LLC, is offered only as a kit, which includes all new parts, no scrounging or machining necessary. Each builder assembles their own engine or, hopefully, at least participates in the assembly of their engine if they hire the task out.
This approach serves a few purposes, none by accident. It keeps the engine price down, making aviation affordable to more people. It assures an AeroVee 2180 engine is assembled with known parts. And it acquaints each builder with the engine’s innards, instilling in them the knowledge and confidence to perform maintenance, troubleshooting and repairs as necessary. As Monnett points out to timid builders, if you can build an airplane, you can build a VW Type 1 engine. By extension, if you can build the engine, you can maintain and repair it. It’s a straightforward organism, familiar to at least two generations of professional and driveway mechanics.
The AeroVee’s DNA and Evolution
Power-producing core: Keeping the price low and serviceability high dictated the use of as many off-the-shelf parts as possible, particularly the parts that produce power and wear out in time. The steel pistons and cylinders (Nikasil cylinders were briefly offered but discontinued), cam, bearings, connecting rods, oil pump, rear seal (the AeroVee has no front seal, it uses the same oil slinger that proved effective in the Beetle), pushrods, lifters, gasket kit and oil screen are mass-produced parts employed without modification. The cylinder heads, also mass-produced, are tapped for a second set of spark plugs.
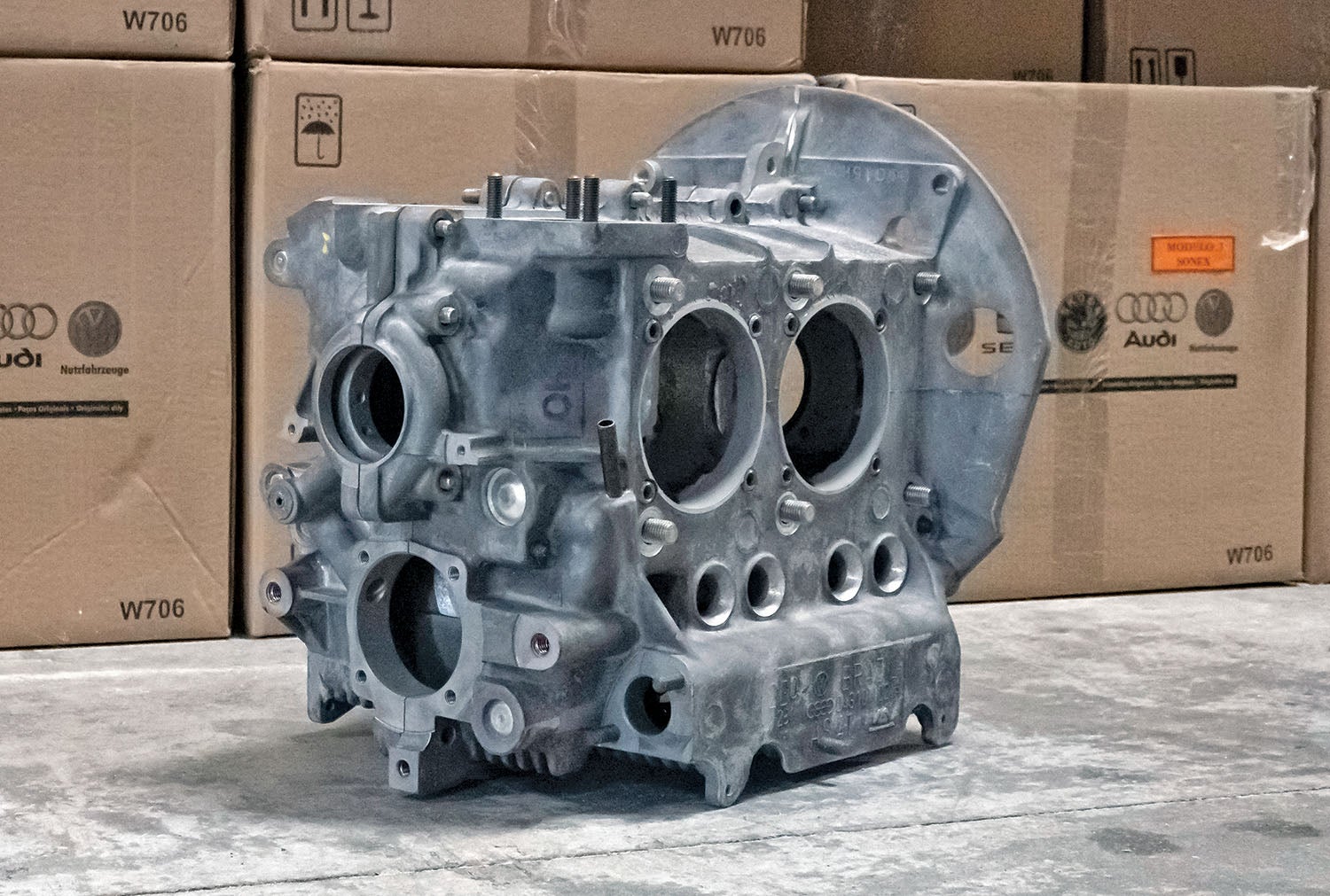
Engine case: The magnesium engine case, cast in Brazil, is one of the few VW-branded parts used. Case modifications for AeroVee-specific use are minimal. The front of the case (the rear, on a Beetle) is bored to accommodate the prop hub’s diameter, two areas of the unneeded transaxle flange are ground away to make space for the magnatron ignition coils, and a hole is drilled through the transaxle flange to accommodate the starter’s pinion gear.
Accessory plate: The heart of the conversion may be the accessory plate, which also bears the engine’s serial number. Machined from 6061-T6 aluminum and anodized red, it bolts to the engine case and provides the interface between the engine and an airframe. It also serves as a sturdy mount for the starter, alternator stator and the primary ignition components of both ignition systems.
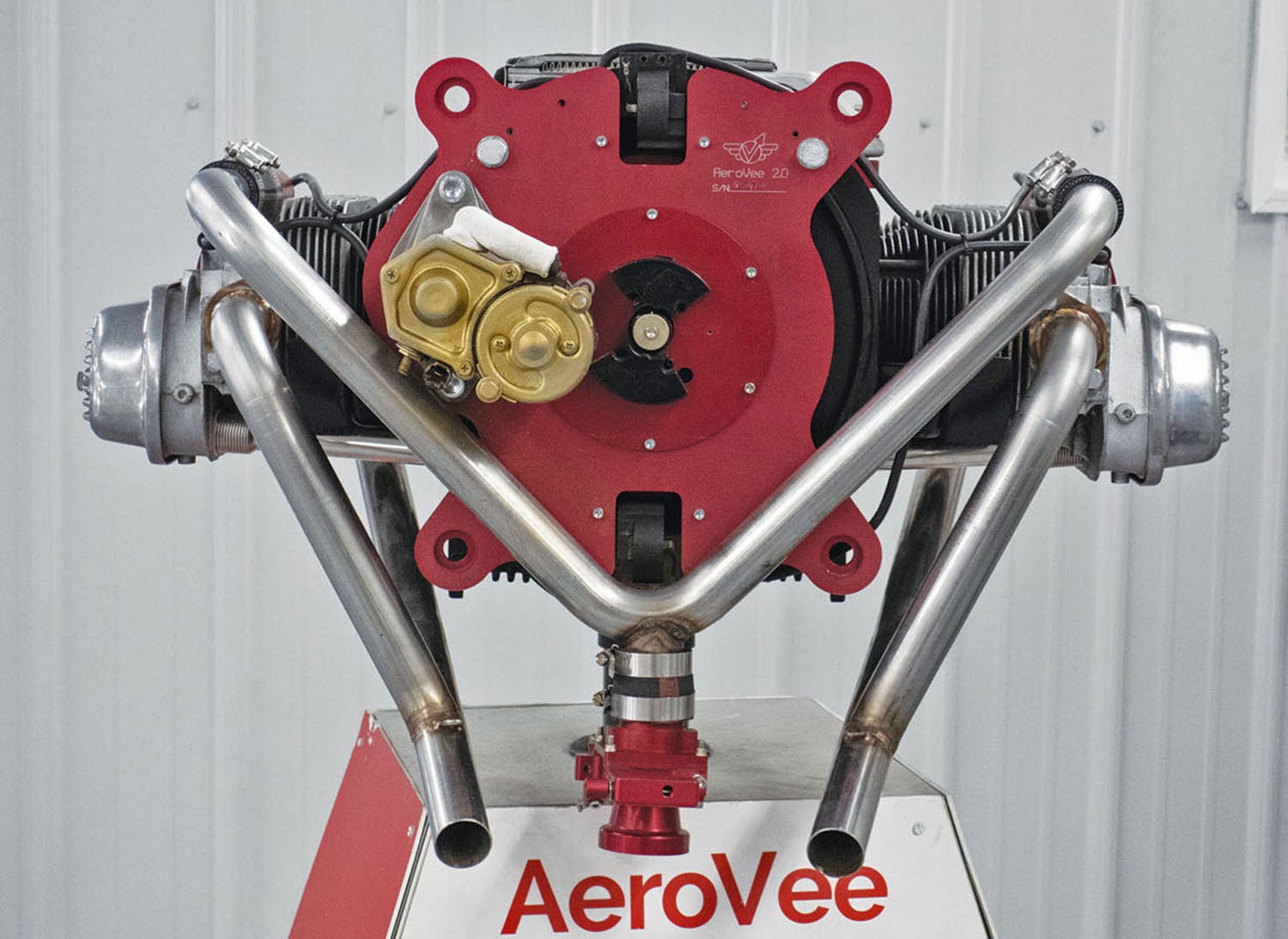
Flywheel: A lightweight CNC-machined aluminum flywheel incorporates the magnet ring for the engine’s stator alternator, a perimeter-mounted magnet to trigger the redundant garden-tractor ignition and a starter ring gear. It is driven by eight dowel pins in the end of the crankshaft.
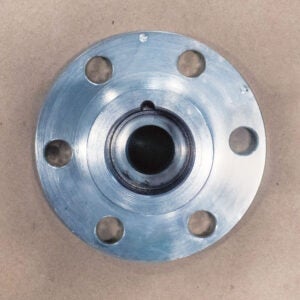
Crankshaft and prop hub: The crankshaft and prop hub are key to converting combustion into thrust. Here, too, Monnett employed lessons learned in the past. A shrink-fit prop hub allowed the use of an off-the-shelf crankshaft, but shrink-fit hubs of yore could crack and depart the crank, divorcing combustion from thrust with negative results. Monnett addressed this on the AeroVee 2180 by thickening the wall of the prop hub and keying it to the crank with a round, rather than square, key, thereby eliminating sharp corners in the hub’s keyway, which was the source of most prop hub failures.
Though the use of an off-the-shelf crank made sense economically, it necessitated using two vestigial Beetle parts: the distributor drive gear and racer spacer. Neither part was needed for the distributor-less AeroVee. Like the prop hub and cam timing gear, those parts had to be shrunk-fit to the crank. That proved problematic for some builders. AeroConversions announced a change in May 2008: “Thanks to burgeoning sales, the AeroVee 2.1 features a purpose-built custom crankshaft that has a larger diameter and longer prop hub interface. This new design also eliminates the distributor drive gear and the racer spacer, making for an easier assembly.” As noted in the press release, the new crankshaft/hub assembly ushered in a new engine designation, the AeroVee 2.1.
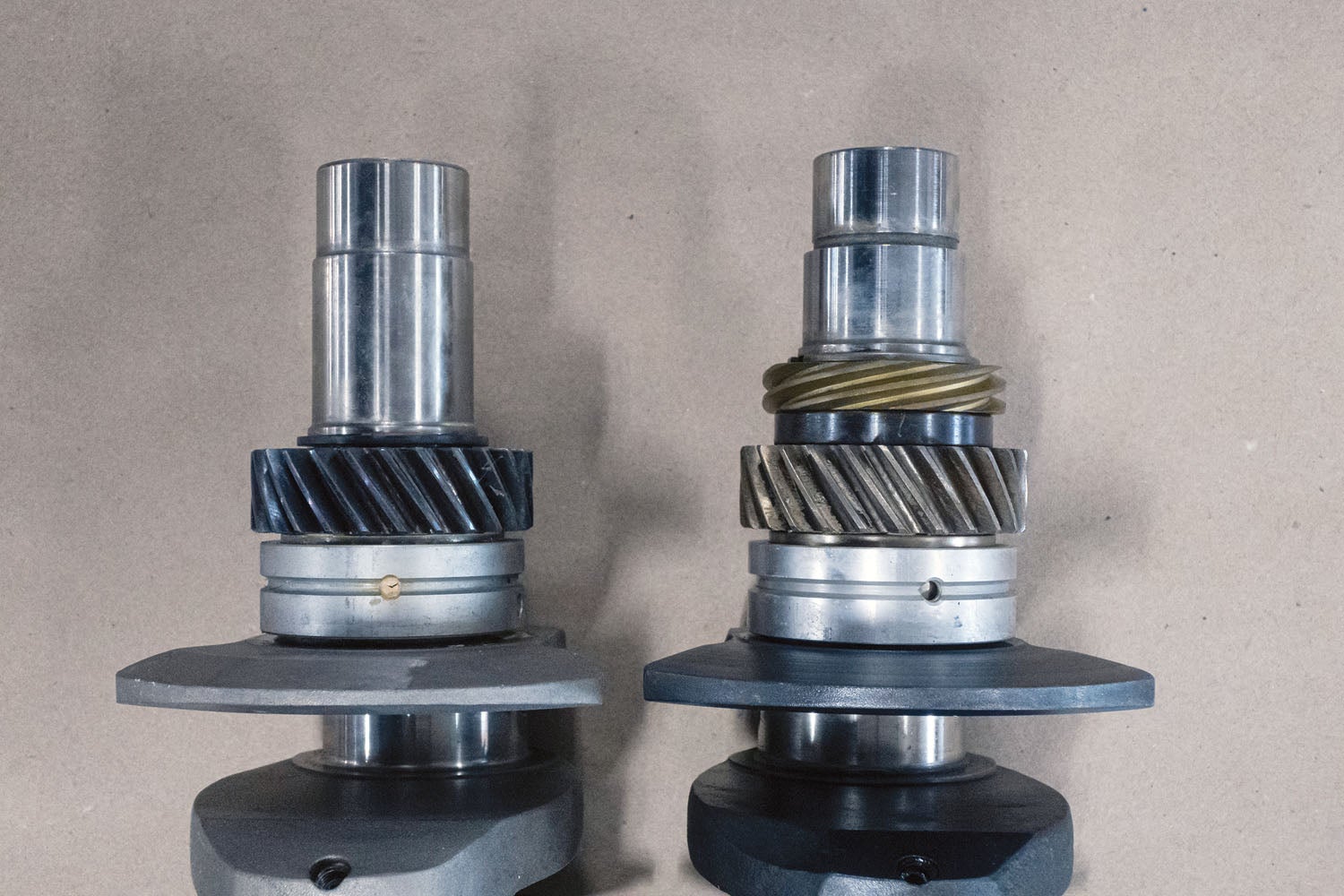
Ignition systems: The first 50-ish AeroVees were ignited by one spark plug per cylinder but two separate ignition coils. This provided a degree of redundancy; if one coil failed, the other continued to fire two opposing cylinders. The magnetically triggered coils (often referred to as magnatrons) are of the garden-tractor variety. They fire without a power source but require 300 rpm to do so. Hand-propping was out of the question. Soon, it became apparent a weak battery or cold weather could make starting an AeroVee difficult. That was remedied in 2003 with the addition of an electronic ignition system. This system also added the potential for hand-propping, but that was not its intent. The update required the off-the-shelf cylinder heads to be machined to accept a second set of spark plugs. It was a small price to pay for the added benefits.
Alternator: A magnet ring on the flywheel spins around a stator mounted on the accessory plate. Because the alternator is not geared, charging voltage cannot be expected until the engine breaches 1400 rpm or so, depending on the demand on the electrical system. The AeroVee was introduced with a 10-amp alternator as standard and a 20-amp option. The 20-amp option proved unpopular and was discontinued in January 2004. As things go, the discontinuation of the 20-amp option heightened demand for it. It became standard equipment in January 2007.
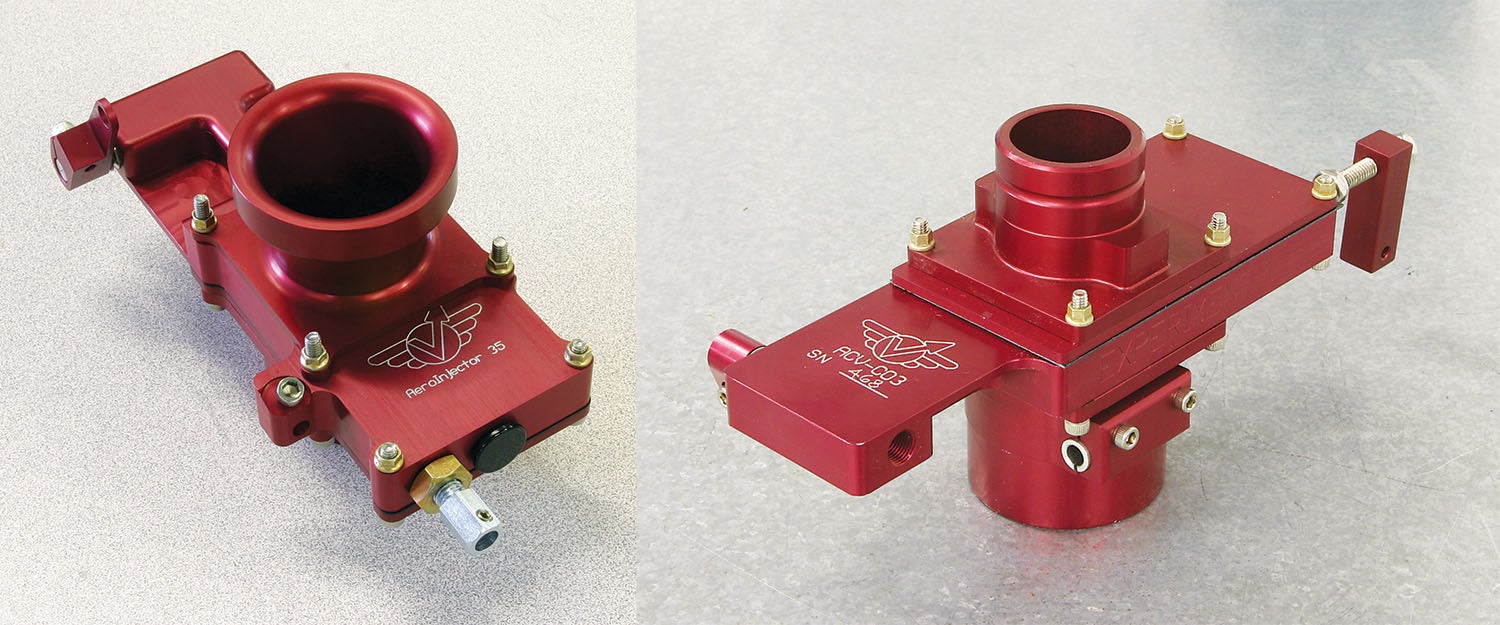
Intake and throttle-body fuel injection: Monnett had extensive experience with Posa slide-style throttle bodies and knew their strengths and weaknesses. Strengths included being dirt-simple machines that resisted carb icing. Weaknesses were limited tunability and no mixture control/fuel cutoff valve.
Thus, the AeroCarb was born. It retained the Posa’s simplicity while incorporating an infinitely adjustable mixture needle and a fuel shutoff valve that permits in-flight mixture adjustments. The AeroCarb is attached to a Y-shaped intake manifold that positions the AeroCarb below and behind the engine. The intake manifold attaches to billet intake elbows that—in keeping with the goal of developing a streamlined engine—hug the top of the engine.
In time, the AeroCarb gained the ability to utilize a reversing throttle quadrant, which eliminated binding many builders experienced if the pushrod-style throttle cable was not aligned properly with the throttle shaft. In early 2010, the AeroCarb was replaced by the AeroInjector, a smaller, lighter redesign of the AeroCarb that eliminated the option for using a pushrod-style throttle cable.
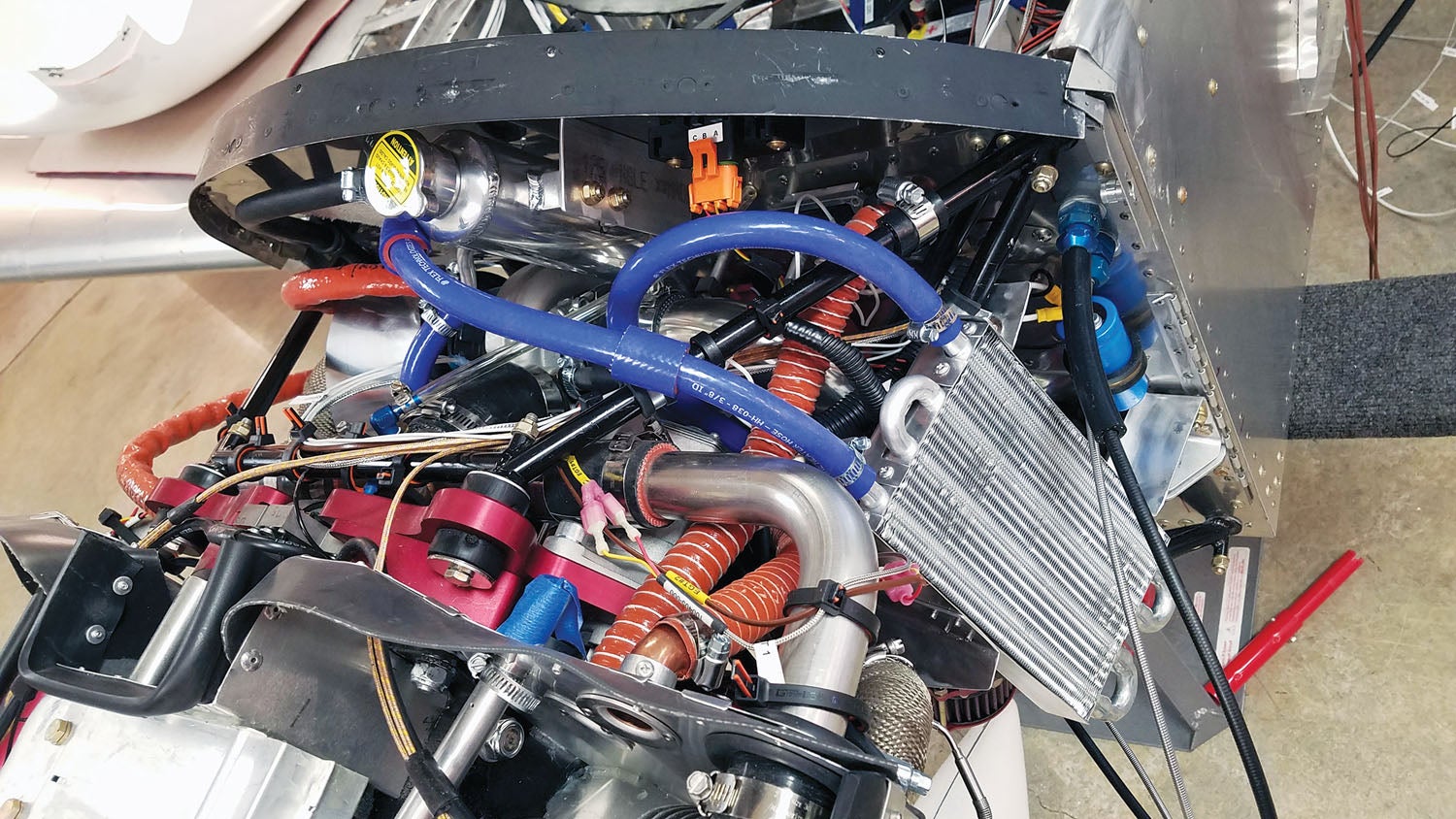
AeroVee turbo: The AeroVee turbo first flew on August 30, 2010, and was available by AirVenture 2014. Though the turbo increased power output to an estimated 100 hp, its stated purpose is to normalize the AeroVee for high-density-altitude operations. The turbo was designed to bolt onto existing AeroVee engines without the need to open the engine case or, in some instances, remove the engine from the airframe. To take advantage of the turbo, an existing AeroVee needs to be fitted with a 2.1 crank assembly, steel—not Nikasil—cylinders and, ideally, run a 7:1 compression ratio. The AeroVee does not support an in-flight-adjustable propeller; therefore, the pilot controls manifold pressure and rpm via the throttle. After initial teething problems related to overheated oil burning onto turbo bearings after shutdown, the upgrade has settled into its role boosting power for those pilots who want or need it. It can be argued that turbocharging an AeroVee disqualifies it as a low-cost, simple powerplant. It isn’t for everyone, but it is for some.
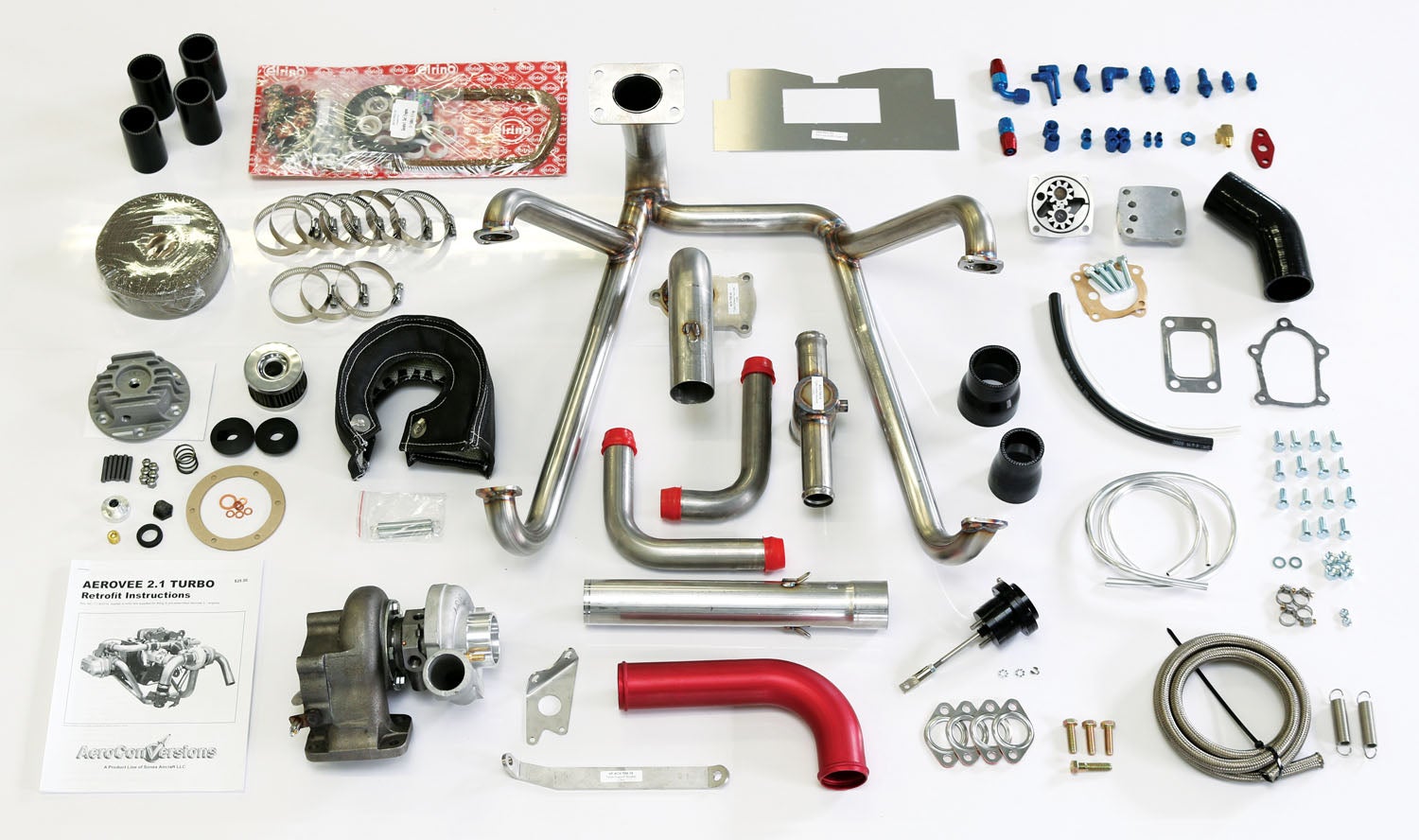
Assembly, Operation and Maintenance
The AeroVee kit includes the parts and hardware necessary to assemble the engine but excludes fluids and the need to scrounge. After inventorying the kit’s contents, attention should turn to the included 70-page assembly manual (which can be downloaded at AeroConversions.com). The manual breaks the project into approachable, step-by-step tasks. For instance, installation of the oil pump is guided by seven steps and five photos—many early VW engine conversions were documented entirely on one sheet of paper! An assembly DVD is available, but AeroConversions cautions it is for big-picture reference only. The manual, which is updated as necessary, overrides the information in the DVD.
Assembly requires few specialized tools or skills. However, the ability to use a digital caliper and feeler gauges is a must. They are needed to set the compression ratio and crankshaft end play. (The manual walks through the compression ratio calculation like a federal tax form.) A torque wrench capable of 227 foot-pounds, to secure the flywheel’s gland nut, can often be borrowed from a tool-collecting friend. A ring compressor will be needed.
If you opt for the pre-assembled crank, you buy your way out of the need for a pneumatic impact wrench and heat-proof gloves. If the project is approached as a learning experience and attention is given to cleaning the parts and following the manual, assembling your own engine can be extremely rewarding.
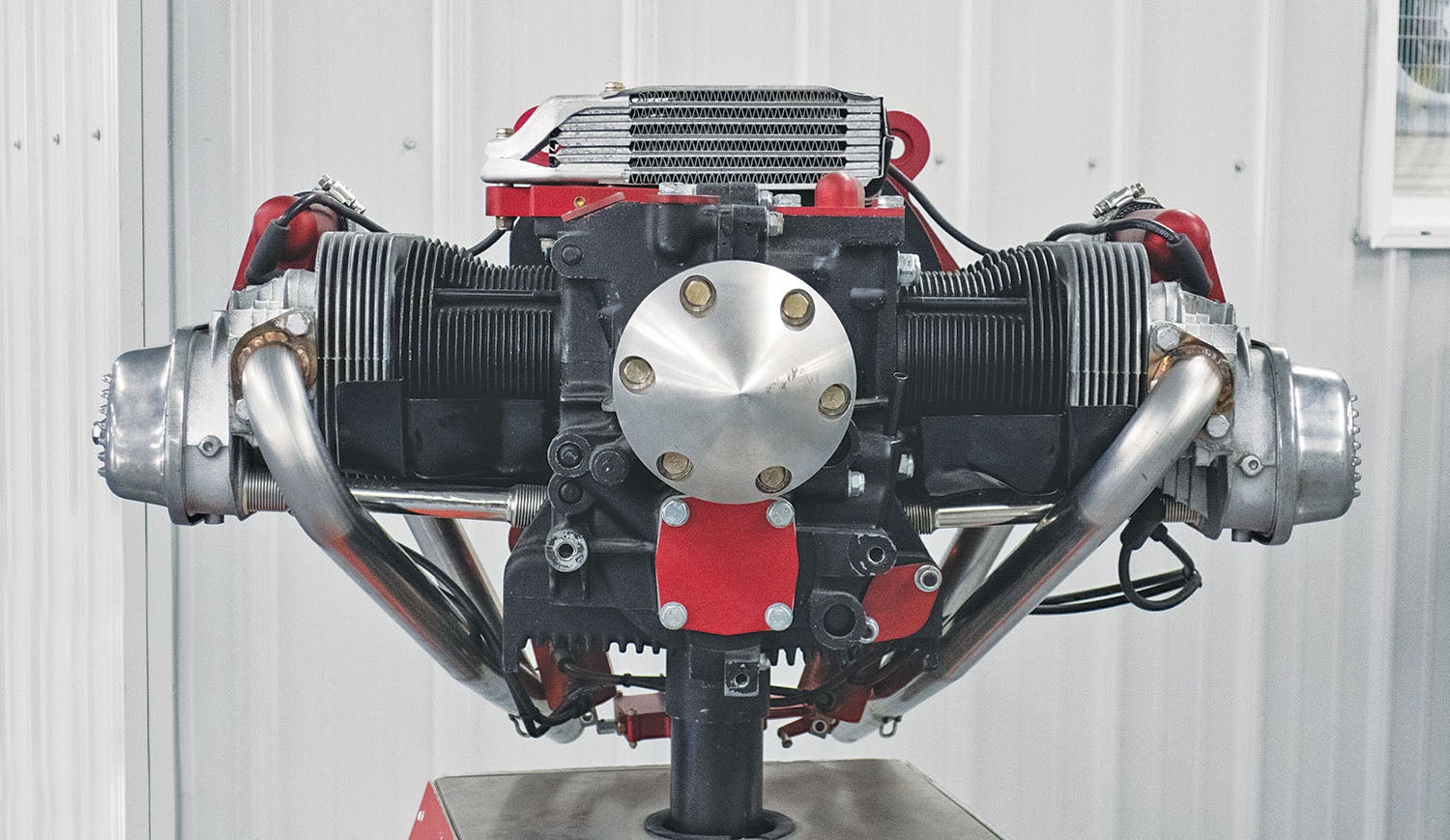
Engines are often only as good as their installation and operation, especially air-cooled engines. Installed in the butt of a Beetle, the engine was cooled by an engine-driven fan inside a shroud that towered above the engine and engulfed the cylinders. (The time-worn tale of VW engines running a hot Number 3 cylinder applies only to car-mounted engines, where the oil cooler sat above Number 3 cylinder, disrupting its airflow). Even at idle, the engine was being cooled. Air-cooled airplane engines enjoy little cooling during ground running; therefore, ground operations must be done in a manner that minimizes the risk of overheating the engine. This is particularly important when an engine is new and its tolerances are tight.
AeroConversions recommends initial ground running be limited to what’s necessary to tune the engine and assure it isn’t hemorrhaging oil, is developing power and responds well to throttle inputs. That should take less than an hour of Hobbs time, accumulated in 5-minute or smaller increments. Initial break-in is accomplished with a 1-hour flight at or near full throttle while keeping temperatures under control. Proper cooling, as with any air-cooled engine, is airframe-dependent. A slow airplane will need different baffling and cowl openings than a fast one.
When the time for repairs arises—and for the non-certified AeroVee that is predicated on need, not accumulated hours—the AeroVee keeps its promise as an affordable powerplant for budget-minded pilots. Browsing the AeroConversions web store in January 2022 revealed a full set of pistons, rings and cylinders are $680. Only need rings? Those are $40.50. A cylinder head is $556. Together, the main bearings, cam bearings and rod-end bearings totaled $123. An assembled crankshaft with prop hub is $1270. Your labor is free.
The AeroConversions AeroVee kit continues the decades-old VW engine conversion tradition of making available a low-cost, simple powerplant for low-cost, simple aircraft. Over 21 million VW Type 1-powered automobiles were manufactured and distributed worldwide. The Type 1 engine enjoys an almost cult-like following that all-but-guarantees core parts will remain available and affordable for another generation. It is the people’s engine—for people with light airplanes.
Photos: Kerry Fores and courtesy of Sonex LLC.
Upgrades, Service Bulletins and Alterations
In this chart, major AeroVee changes are keyed to delivery dates and engine serial numbers. It is not uncommon, however, for engines to ship slightly out of serial-number sequence, impacting a clean cutoff date or serial number range for changes. Most upgrades were made available to existing owners; therefore, no engine can be dated solely by its physical features. If one were inclined, the first AeroVee delivered could be updated to current specifications. Subtle changes have been implemented through the years that can’t be cataloged by engine version or serial number. Some were driven by ongoing improvements (for instance, changing from black-oxide-coated hardware to zinc-coated hardware) and others by supply changes or issues. As they say, “Subject to change without notice.”
Over the 20-year production run, some features have been discontinued and are no longer supported. AeroConversions no longer stocks 10-amp alternators, though the original single-phase 10-amp Jabiru alternator is a direct replacement. The original crankshaft and prop hub are also no longer sold. An engine equipped with an original crank and prop hub must be upgraded to the 2.1 crank if either the crank or hub are damaged. The upgrade is straightforward and requires no additional engine modifications. Finally, lightweight Nikasil cylinders were offered for a period, but their quality was inconsistent and they were discontinued.
AeroConversions maintain an online service bulletin database (AeroConversions.com). It is recommended that existing owners, or anyone contemplating the purchase of secondhand AeroVee, acquaint themselves with any applicable service bulletins.
There are AeroVee engines known to be altered. The E/A-B category allows this. It is from such experimenting that the use of VW engines in aircraft came to be. AeroConversions recommends all alterations and parts substitutions be noted in the engine’s logbook and assembly documentation for the benefit of future, or forgetful, owners. Certainly, any change to a system described in this article places an engine firmly in the one-of-a-kind category. AeroConversions support for AeroVee engines is limited to the parts provided in the AeroVee kit.
—K.F.
AeroVee 2002 | |
|
|
AeroVee 2.0 | |
|
|
AeroVee 2.1 | |
|
|
AeroVee Turbo | |
|
|
As AeroConversions note – TBO is “On Condition” and not a published number. I just gave a naturally aspirated 2.1 a top overhaul at 473 hours. A strict oil program every 25 hours gave a clue that iron was on the uptick. Borescope showed bores that had honing marks visible at 380 hours but now showed almost no honing marks – just polish at 473. Compressions were headed south. At 380 hours on freshly lapped valves I could still get 78/78/78/78. At 473 the compressions were all over with the worst at 62. Winter ops in negative density altitude were masking the reality of poorer compressions. It was time.
On tear down – camshaft looked like new and on the basis that there were no notable bearing metals in the oil program – did not split the case. Reused the cylinder heads with new valves. With new heavy duty cylinders and forged pistons, all new valves, fasteners and gaskets – the whole job was JUST under $1,000 in parts and about 12 hours labor. 2 for the tear down and 10 for the refurb and build up. Back on the oil program to determine the next overhaul!
As Kerry notes – if you mis-spent your youth tinkering with engines under the hood of your beater car – this engine will bring back memories and is not intimidating.
Enjoyed your article on the Aero Conversions VW conversions,. Myself and a friend built David here in Texas built a two cylinder VW engine (Half VW) andstuck a saab turbo charger on it. David was a jet engine mechanic and was good at what he does. It was mounted to a Spitfire ultralight aircraft and flew at Sun n Fun. The boost control was adjustable and we could get 7 lbs of boost into the engine. Once it achieved flight altitude the boost control could be adjusted back to two lbs. This gave a much better fuel control burn with only burning 1 and 1/2 gallons fuel hour. So a five gallon tank could fly you a great distance at 60 mph. This was flown under the company name “Sunrise Aircraft Manufacturing” and no publicity was written about our work. Howevver the Japenese di copy our work and the HKS engine later came out with the turbo charged model built exactly as we had flown. It was a great engine design and some rework had to be done to the engine to make this work. We tried to sell these engines to the public for 4500 dolars but had zero takers. Never the less, we flew the engine and plane all over east Texas and had a blast. Thanks for the article..