What began, for one homebuilder, as a cross-country odyssey to AirVenture turned into an altogether different odyssey when his airplane’s voltmeter began an un-commanded descent to the left. Charging voltage became battery voltage. Battery voltage became too weak to maintain the ship’s systems. The pilot contacted ATC, which vectored him to a remote mining airstrip. After the pilot informed ATC that the field was in sight, the battery’s voltage became too weak to satisfy the transponder’s need, and the aircraft vanished from ATC’s radar. While a grateful pilot made a successful landing somewhere near Nowhere, Arizona, a panicked controller dispatched the state patrol.
By the time I spoke to the stranded airman, the state trooper had departed, having found the subject of his welfare check safe, but sweaty. Troubleshooting had already been performed, and the more important phone calls (to home and to a buddy with a possible spare) had been made. The call to me was to pick my brain for other diagnostic efforts he could make. His inspection didn’t reveal any poor electrical connections. Nothing smelled burnt or looked overheated. He said his three-year old battery suckled on a battery maintainer when the airplane wasn’t flying.
There was, however, history of a failed voltage regulator. My long-distance diagnoses agreed with his: Another failed voltage regulator. Recovery time? Two days staring at the desert, waiting for a replacement part to arrive. Postoperative instructions? The pilot’s next of kin ordered him home.
Had the OSH-bound aviator been carrying some basic spares he could have replaced the voltage regulator and continued his flight with a “there I was” story for his camping buddies. Instead, he spent two days, nowhere, waiting for the arrival of an inexpensive, lightweight, easily replaced part. And he missed an opportunity to fly his homebuilt to The Big One. Worse still are the long-term consequences. His spouse is (more) worried each time he flies because now she knows that “it” can happen.
An Appropriate Level of Preparedness
Packing for preparedness includes three distinct considerations: The nature of the flight, what parts to pack, and what tools to transport. On local flights within gliding or walking distance of your airport, evict the parts and tools from the baggage area so they can’t hit you in the head when a hammerhead goes bad. A sightseeing trip without a planned stop away from home may seem like another opportunity to evict the spares, but I’d disagree.
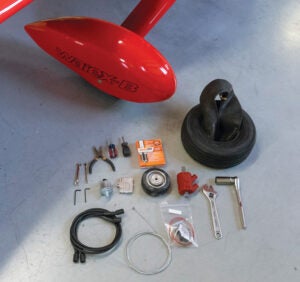
I was patrolling Lake Winnebago for submarines (there was never a reported sub-sighting when I patrolled it, a record I’m proud of) when Metal Illness gave me some little kicks in the butt. Not knowing if I was losing an engine, a prop, a cylinder, or the ignition, I climbed for altitude and pointed my Sonex’s polished spinner toward home, 20 miles away. I made it home without issue, but I was ready to divert to closer airports if necessary. My post-landing inspection revealed an intermittent ignition-coil failure. I had it replaced in a few minutes. Had I landed at another airport the repair would have been just as quick, as the part and tools were on board in a small ditty bag I carried.
Spare spark plugs (pre-gapped), distributor caps and rotors, and, ahem, voltage regulators are all small, light, and handy to have if you have to land somewhere other than home to diagnose an engine miss, as I almost did. Spark plug wires can fail, too, but never all of them at once. Carry only the two longest wires as they also fit where shorter wires are needed. On flights where you plan to land back home, carrying a spare tire and inner tube is unnecessary as there is no way to diagnose a flat tire in the air. But on a flight that includes a landing away from home a spare inner tube (or tube repair kit) can rescue you from an extended stay. A full deflation, however, can also destroy a tire. The decision to carry a spare tire rests on where you are flying to, where you may land, and how common your tire size is. Flying with a spare tube and tire pre-mounted on a wheel is not unheard of on a cross-country flight with many planned stops.
Tools, though small, are heavy, and should be given careful consideration. Don’t pack a full set of sockets and wrenches when only a few sizes are needed. Ditch the 9/16-inch combination wrench that doesn’t fit anything you’d repair in the field, but pack the 9/64-inch hex wrench that’s needed to swap an ignition coil. If your spark plugs require a unique socket, like an odd size or a thin-walled socket, pack that. A small adjustable wrench will fit nearly everything, including axle bolts. Pack fuses. Pack safety wire. Pack a small piece of emery cloth. Duct tape? Did you really ask that?
I carried parts that could fail and were relatively easy to replace, as well as any unique tools needed to do it. Parts earned priority-boarding status if they needed to come from a very specific source or could take days to order and arrive. Tools were chosen based on what can be easily bummed from any FBO or hangar owner, and what would be needed to install the spares I packed. No point in having a spare ignition coil along but not a 9/64-inch hex wrench to install it. A hammer can be found anywhere, sometimes disguised as a rock or a chock.
Airplanes are kept aloft by components that can fail. Prevention of a failure through routine maintenance and proactive replacement is the preferred approach to aircraft maintenance. Carrying spare parts and the tools to install them, however, is a safety net against failures that come out of nowhere and threaten to strand you there. Or very near there.