So about that lathe and how it begat the need to learn welding. A recent addition to our airpark neighborhood is KITPLANES Home Shop Machinist himself, Robert Hadley. Never one to pass up the chance to learn from someone “who knows,” we tackled several small projects in the fall. In the process, I stripped out some bolts on my Smithy’s tool post. That required welding up some new special bolts (sure, you can buy them, but…why?) and me learning the value of TIG welding! The lathe fixed, I set about making parts for several small projects, including a special tool for inserting the long hinge pins that holds the wingtips on the eXenos (more about that tool another time). We also needed bushings for an electric aircraft tug we’ve been building—more on that in a future issue of KITPLANES—and the lathe was just the thing!
More recently, I was working on another little task that required a very narrow-nosed socket wrench. In the past, I have butchered cheap sockets on a bench grinder, most notably to have a tool that fits Lycoming connecting rod big-end bolts. But now realized I could have a whole set of such custom sockets with the new lathe skills I’d been learning. Off to Harbor Freight for the sacrificial victims.
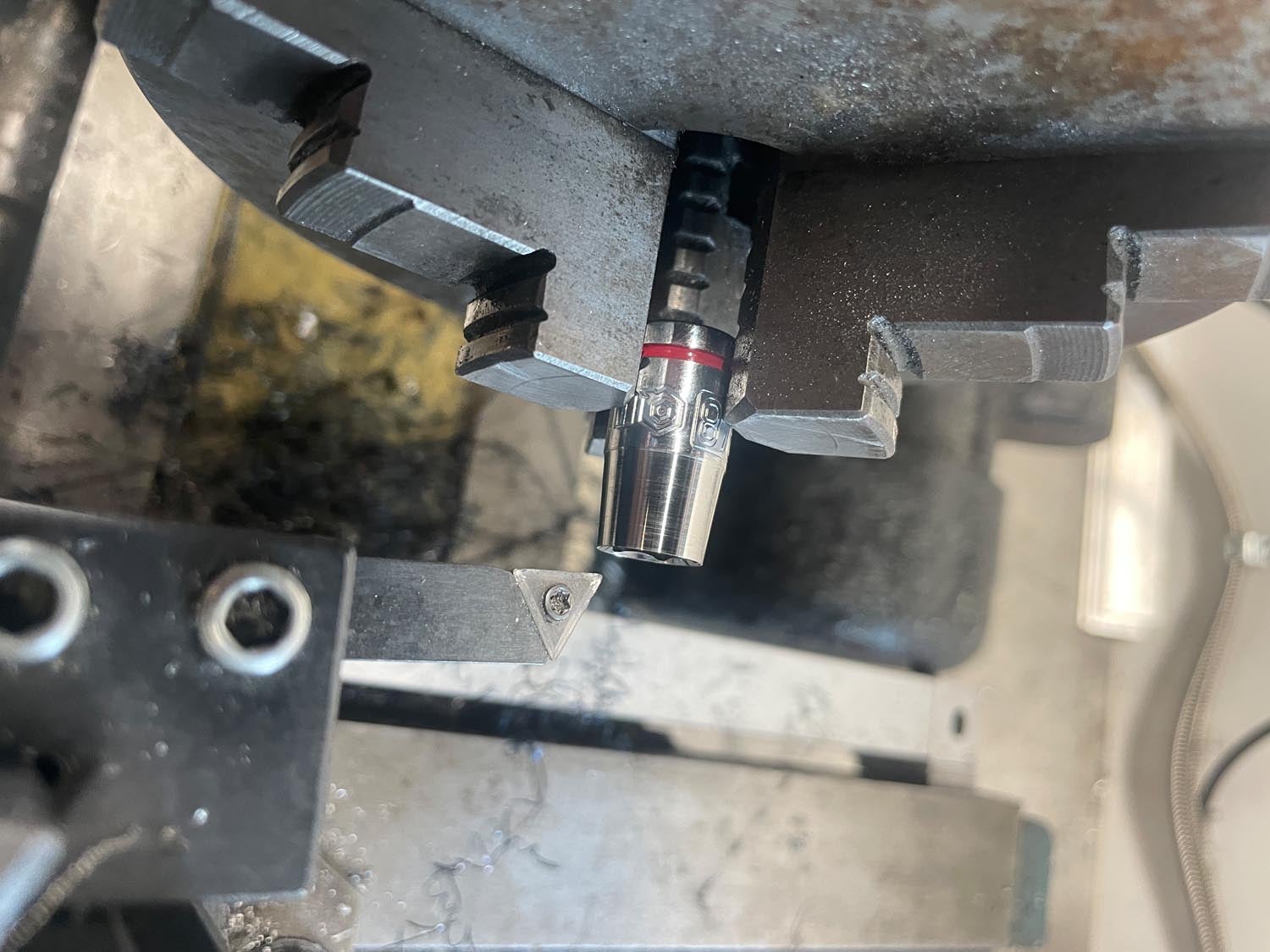
It’s a simple matter to set the lathe up to move the tool at a 5 degree taper angle, and I proceeded to turn down the entire set of sockets (one at a time) until they were tapered to a knife edge. Given that it is a set of small sockets and torques rarely get very high, they should do the job—whatever that might be—in the future. Since things were all set up, I did regular and deep sockets at the same time!
Hey, what’s all that racket on the internet? Oh dang, a new service bulletin just came out that affects all three of our RVs… get the tools out!