Yes, it’s an oxymoron—a factory head is made in a factory, and shop heads are made in the shop—but the truth is, sometimes you can “fake” a factory head in the shop, mostly for aesthetic reasons. All it takes is a flush rivet (an “oops” rivet will do), a round-head squeezer die, a flat die, and a rivet squeezer.
This is a floor panel for our F1 Rocket project. The hinge is for the bottom of the pilot’ seat back. The rivets you see all go into a stiffener that fits between the floor ribs. The two holes on either side (on the extension of the hinge material) will have screws that go into nut plates on the floor substructure. But when the floor panel is removed, those hinge extensions will be flopping around – I wanted them tacked down. But since they have to lay flush on the substructure, I needed a flush rivet head on the bottom.
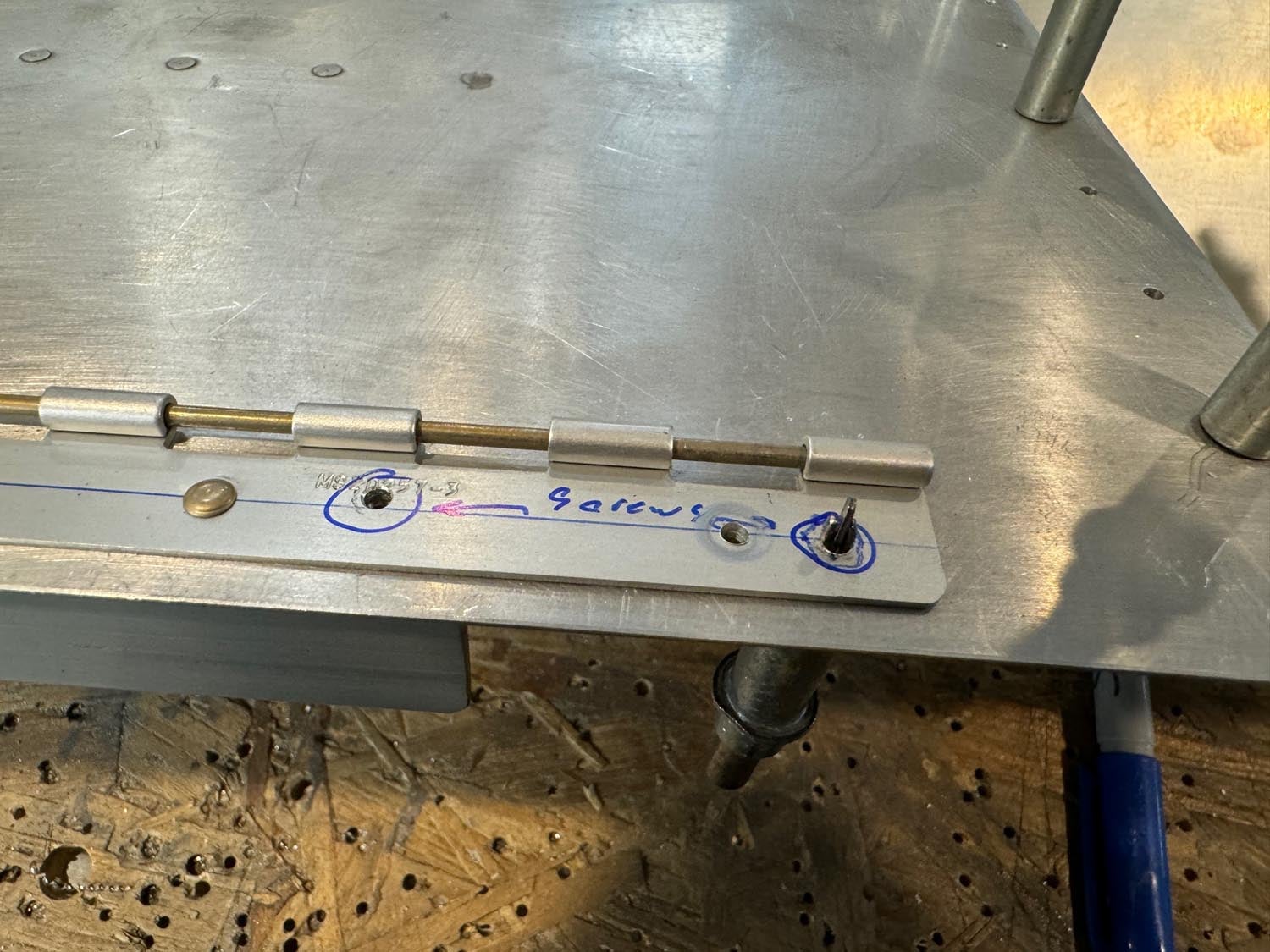
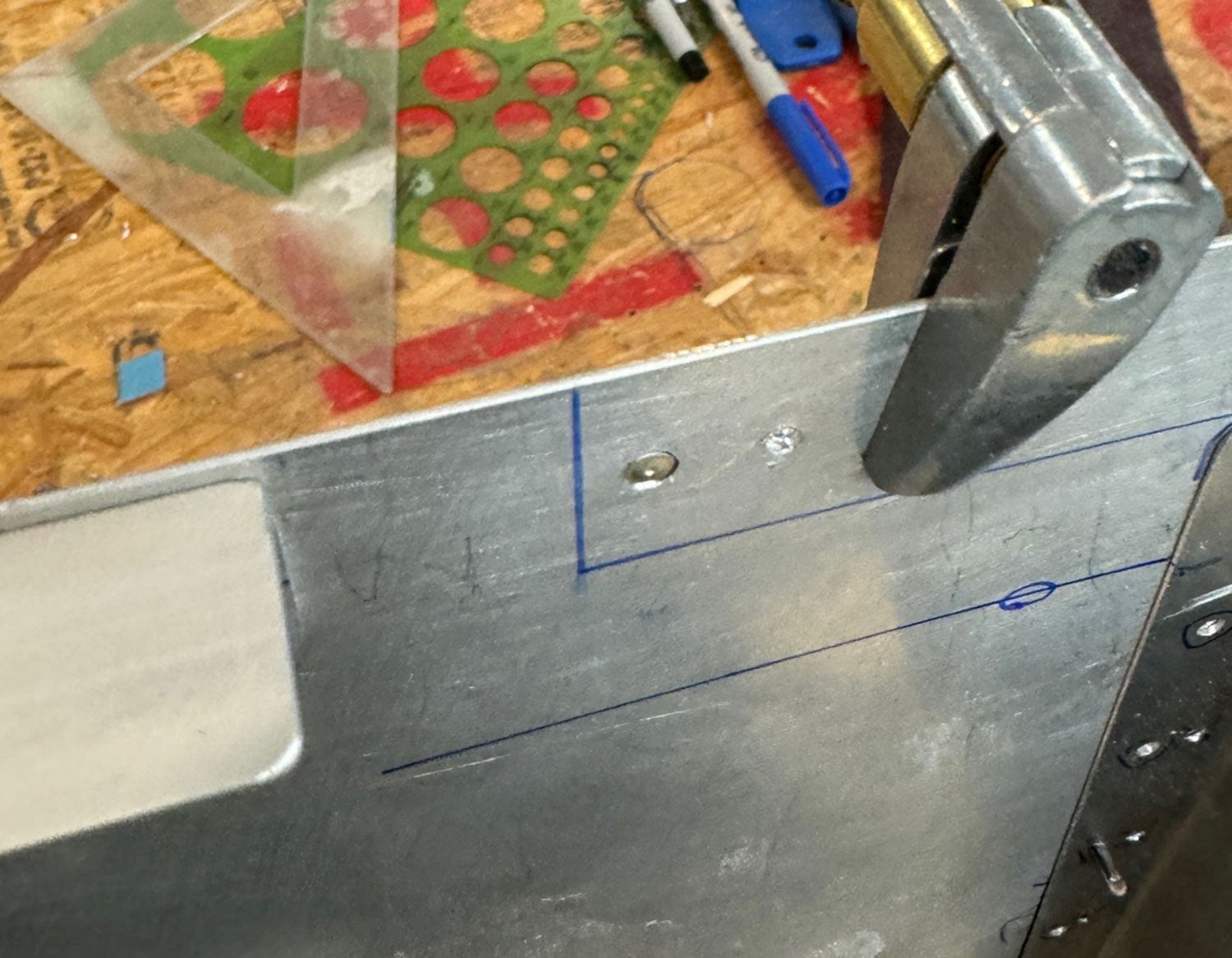
Here is the shank of the flush rivet stick up. Sure, I could just squeeze it and have a cylindrical factory head there, but it wouldn’t match the line of round-head rivets on the rest of the hinge material.
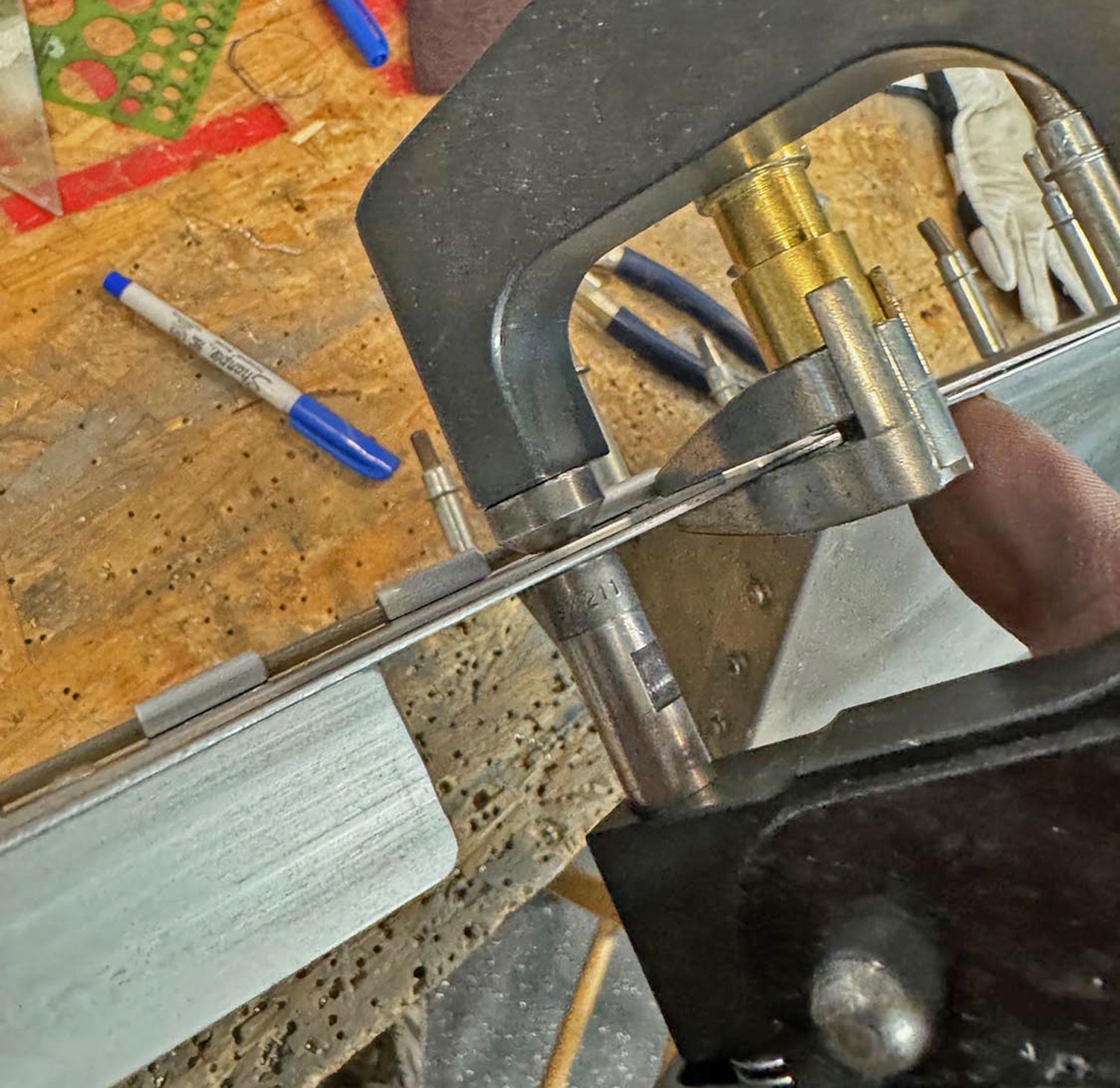
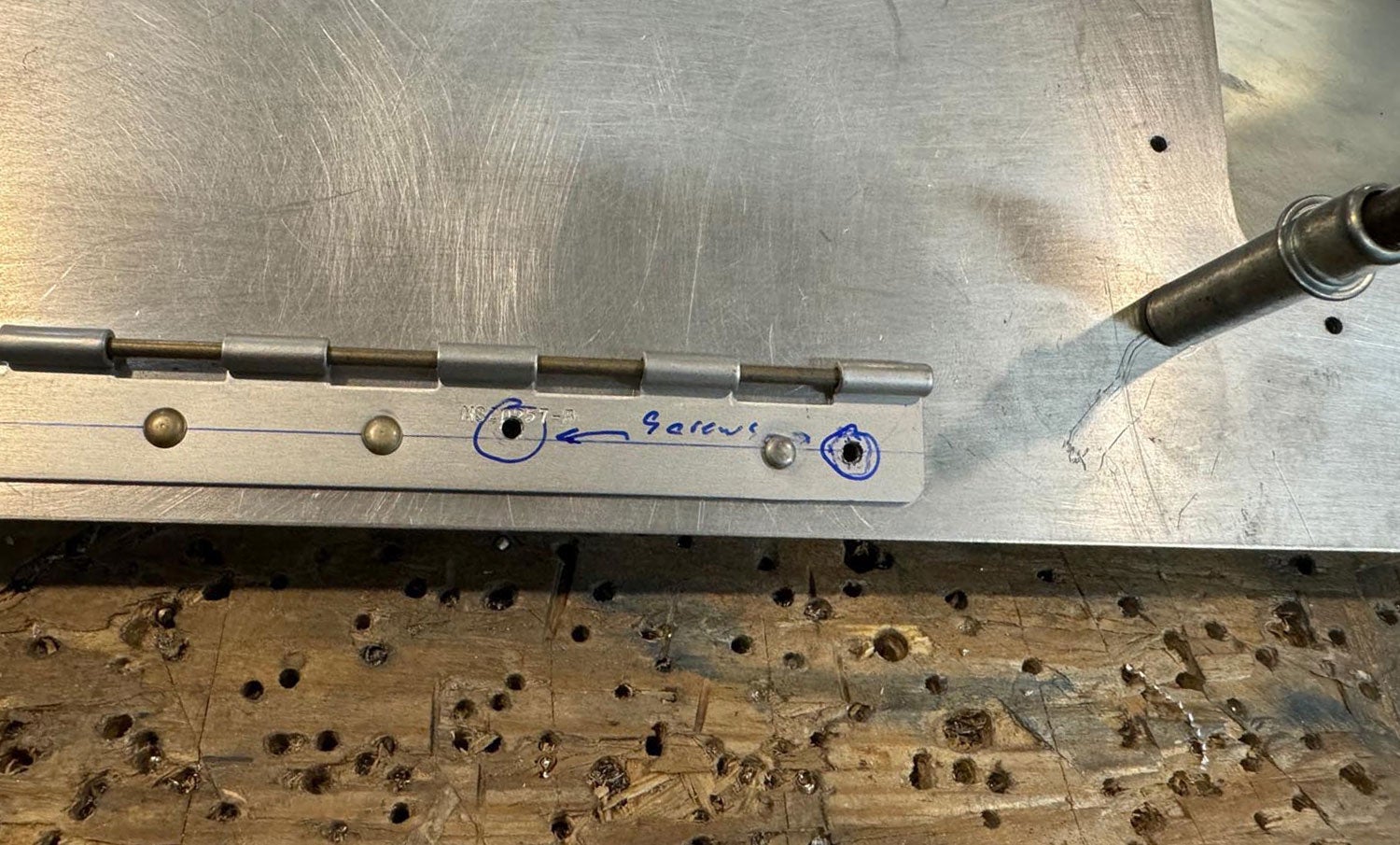
This could also have been a place to do a “double flush” rivet, where you countersink both sides and squeeze the tail flat into a countersink….but the material here was too thin to really make that work. And remember, in this case, it’s not engineering (there is no load on this)… it’s just art!
I like it!
I like that your tip has the “look and feel” of the real world — as do your videos. It takes a few months or even years to come to the realization that most of the YT videos and builder website pics rarely display the less than “perfect” project pieces logic would indicate certainly exist.