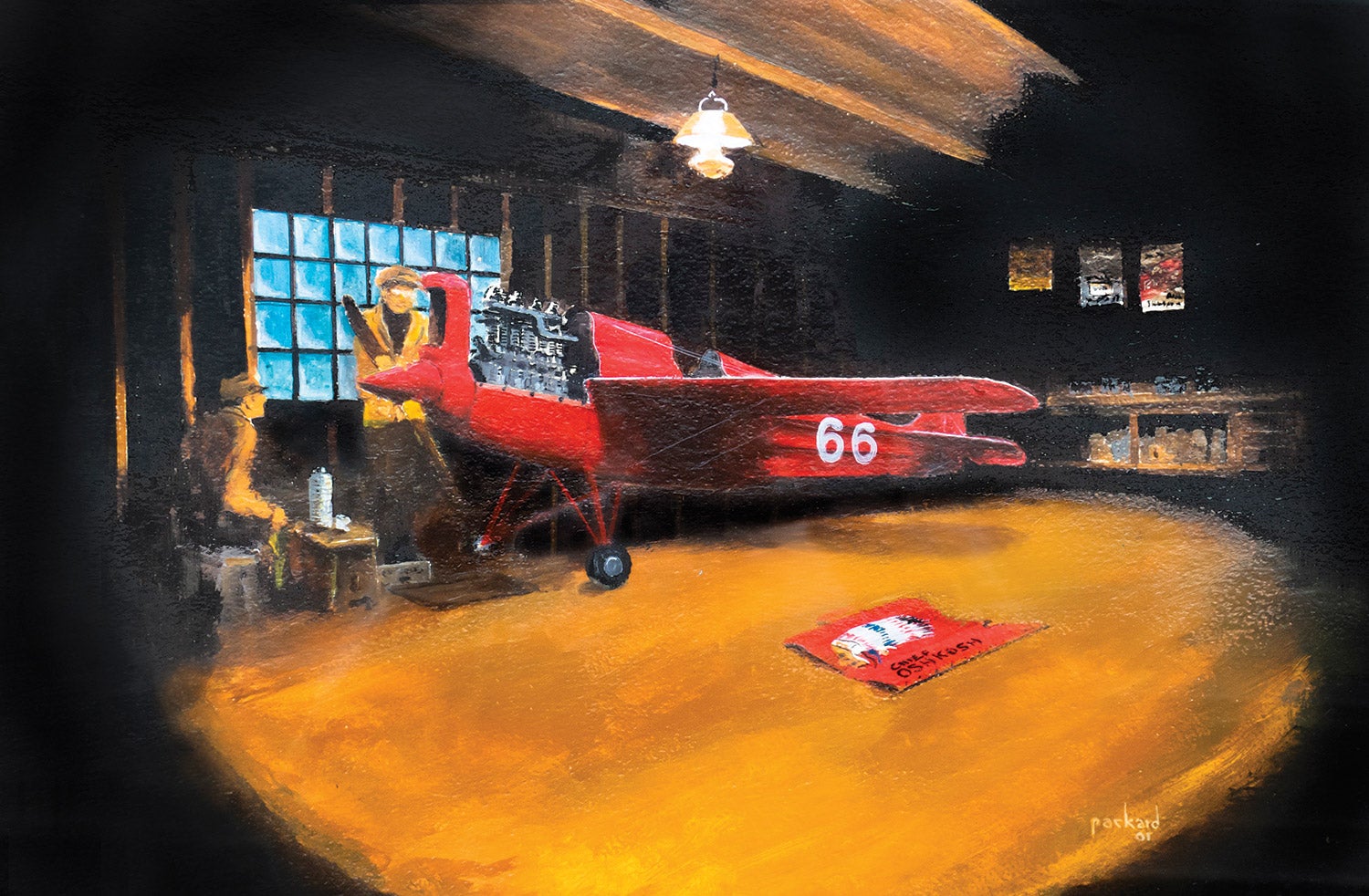
I’ve confessed to building Metal Illness in a space that many, or most, would rate less than ideal. In my defense, my brain’s right and left hemispheres have been locked in a battle for control of my actions since the Johnson administration. I’m equally equipped to plan so intensely that I’ll plan my way right out of a project or under-plan so severely that I’ll find myself tuck-pointing a chimney in Sunday-go-to-meetin’ clothes. The day I took delivery of 13 sheets of 4×12-foot aluminum for my Sonex, I didn’t know where I’d store them. And thank goodness! If I had thought about my workspace at all I may have never started a project that changed my life for the better in more ways than I can count.
Is It Uncomfortable in Here?
My project germinated in a garage whose walls were dull, earthy shades of light-absorbing green and brown. One small window on the north wall throttled the only natural light available. My family of five had haphazardly populated the garage with bikes, yard implements, sporting goods and a heavy workbench. I never considered moving everything to paint the walls white to brighten the space. That task would have halted the airplane project before it began. However, very few evening or closed-garage-door work sessions went by that I didn’t think, “I should hang another fluorescent fixture.” Yet I never did. It would have made my building sessions more comfortable. Perhaps what I mean is it would have made them less uncomfortable. There’s the crux. We notice when we are uncomfortable more so than when we are comfortable. Tune in to that. That discomfort signals a needed upgrade, the most common of which I’ll review here.
Lighting
If you haven’t shopped for shop lights lately, you are in for a treat. I hung an LED shop light in my current garage. It is a quantum improvement over the fluorescent fixtures of yore. It is instant-on in the coldest weather, it doesn’t hum or flicker, and the light temperature is in the daylight spectrum (5000K), which is beneficial when working with color-related tasks like wiring. It also helps stave off seasonal affective disorder. There was a warning on the box that discouraged looking directly at the light. Lawyers! (My retinas have healed.) Improving the light of almost any workspace is easy and inexpensive, and the benefits extend well beyond seeing the 64ths on a ruler so they can be transferred to aluminum with a fat Sharpie.
What’s Underfoot?
We’ve all drooled over someone’s glossy white epoxy shop floor. The owners don’t mind because drool, like all liquids, cleans up easily from epoxy-coated surfaces. But for my money, I’ll take a few rubber mats. A layer of rubber between my feet and the concrete eases the strain on my joints and insulates me from the cold concrete. The rubber mats also blunt the rebound of dropped tools, parts and hardware, making them easier to retrieve and less likely to get damaged. Many styles of mats are available, and any mat is better than none.
Climate Control
My brother thinks 30° below zero—on any scale: Fahrenheit, Celsius or Kelvin—is about ideal. I think 30° F above freezing is ideal. Regardless of your definition of comfortable, conditioning a workspace is relatively easy these days. Heating with an electric infrared heater is safe, practical and effective even in a poorly insulated space. Like the sun, infrared heat heats things, not air. You, your parts and your tools will be warm long before the airmass in the shop has warmed.
In hot, dry climates, a swamp cooler can keep you cool. In a humid environment, an air conditioner, fans and closing doors and windows to lock out humidity may be all you need to extend a work session and keep salty sweat off the airframe. Room air conditioners are no longer restricted to teetering in double-hung windows. Floor-standing units are available that can be positioned anywhere their air hoses can reach a door, window or dedicated vent.
Hearing Protection or Hearing Aids. Pick One
I’ve noticed when I hangar fly with other pilots, the conversation, among those who can hear to participate, is increasingly about the pros and cons of the hearing aids they have. (It wasn’t until the 1980s that scientists discovered aircraft engines create thrust and tinnitus.) At the risk of being scorned like Galileo, Copernicus and the person who first noted activities prefaced with “hold my beer, watch this” end poorly, I’ll state that screaming shop vacs, whining air drills, dull band saw blades friction-cutting through aluminum, grinders, air compressors and pounding rivet guns also damage hearing. Noise is also fatiguing. Fatigue can impact your workmanship. Any discomfort from wearing hearing protection some of the time is minimal compared to needing hearing aids all of the time.
Building to New Heights
Bending over a workbench for hours has put me on my back. Experts on the internet agree the ideal workbench height is 36 to 38 inches. Hogwash. The ideal height is the height that is comfortable for you and the task at hand. I still use the floor as a workbench too often. My left and right hemispheres are still slugging it out, leaving my knees bruised.
Do It for You and Your Project
The best workshop is always the space you have to get a project underway and keep it moving forward. Improvements can be made as needed. The key is to notice when you are uncomfortable and take action to eliminate the cause. (Which may also include changing the clothing you wear. If you find yourself being extra cautious mixing resin, it’s time to change out of the office khakis and white button-down.) Technology has made it easy and inexpensive to improve the conditions in any shop. Comfort translates into longer, more productive work sessions, better workmanship and more enjoyment of the project.
Good article, but as a professional engineer who’s designed lighting for thousands of facilities in my career I have one correction. The color of the light will not help with color critical tasks. What’s important is how complete the spectrum is. Light manufacturers list this in terms of the Color Rendering Index (CRI). A CRI of 100 is a complete spectrum only found in natural light and incandescent lights. For most general purpose applications, including my own shop, I recommend getting a CRI of at least 80 with a color temperature between 3,000K and 5,000K, with 4,000K being the most neutral white and most people’s preference. Specialty LED lights are available for art studios and galleries that have CRI as high as 96, but as you can imagine you pay a premium for that. Beware anything labeled “Full Spectrum”, it’s not an industry recognized term and is typically used to market cheap 5,000K or higher lamps that can have a CRI as low as 50. Similarly anything labeled as Shop or Kitchen lights are typically very cheap with a CRI around 30. And if they don’t list the CRI, you can be sure it’s not good. Hope this is helpful.