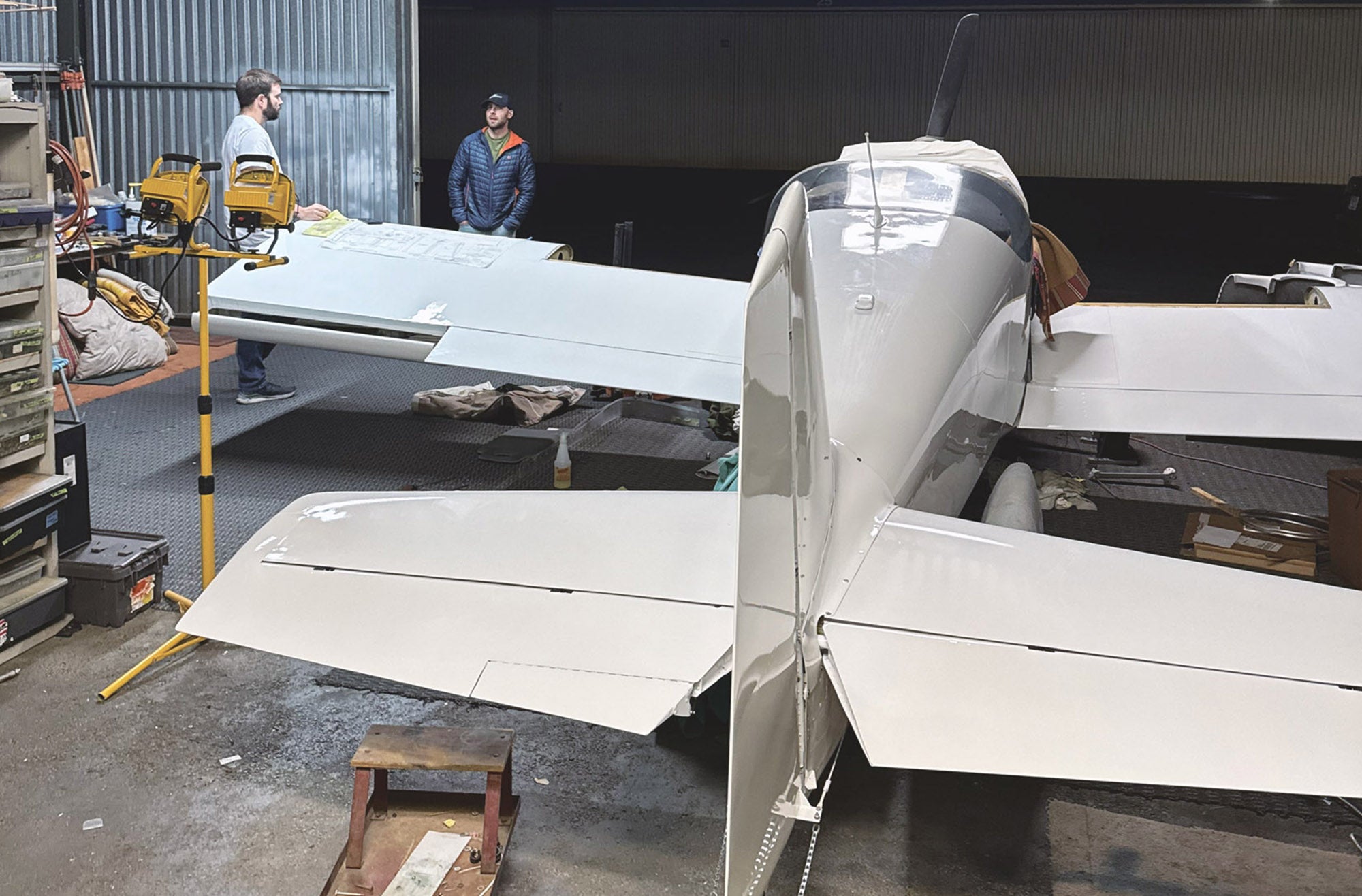
The ailerons on N2165U have been giving me a run for my money. Here’s why. On the Van’s RV-6, the ailerons have a bracket on each end. The outside bracket connects to a ball bearing, while the bracket closest to the fuselage connects to a pushrod. The pushrod then runs through the wing to a long rod that goes through the fuselage and connects to the other side.
Our challenge was that the ailerons did not clear the wing. Every time they would rotate into the “up” position, they would rub the bottom of the wing and not meet the stop. It looked like the previous owners had solved this problem by elongating the holes in the brackets.
The problem with elongating holes is that it can make areas more prone to stress if they aren’t designed for it. Therefore, my CFI and adopted grandfather, Stan Lawrence, purchased new brackets and we drilled new holes using the old brackets for reference. Unfortunately, because the holes are nearly impossible to line up, we ended up drilling them in the same place as the last ones. Because of that, we ended up elongating them slightly (just like they were before) to make them fit properly, making them pretty much identical to the old ones.
The Solution: Washers and Shims
Instead of once again buying new brackets, we decided to weld AN-970-3 washers to the existing brackets. This ended up being much more accurate, less expensive and easier to do, and it strengthened the brackets. My super-smart engineer friend, Kyle Rodrigues, took on the project and within a week they were ready to go. Stan painted them white, then I reattached them to the aileron using a ⅜-inch wrench and customized socket. In order to fit the socket onto the bolts to tighten, Kerry had to grind down a socket so the ends could be thin.
In addition to welding the washers, we added a shim between the brackets and the aileron itself. This created more clearance by moving the aileron slightly lower to the ground, away from the wing. Now, the aileron could travel farther and not rub.
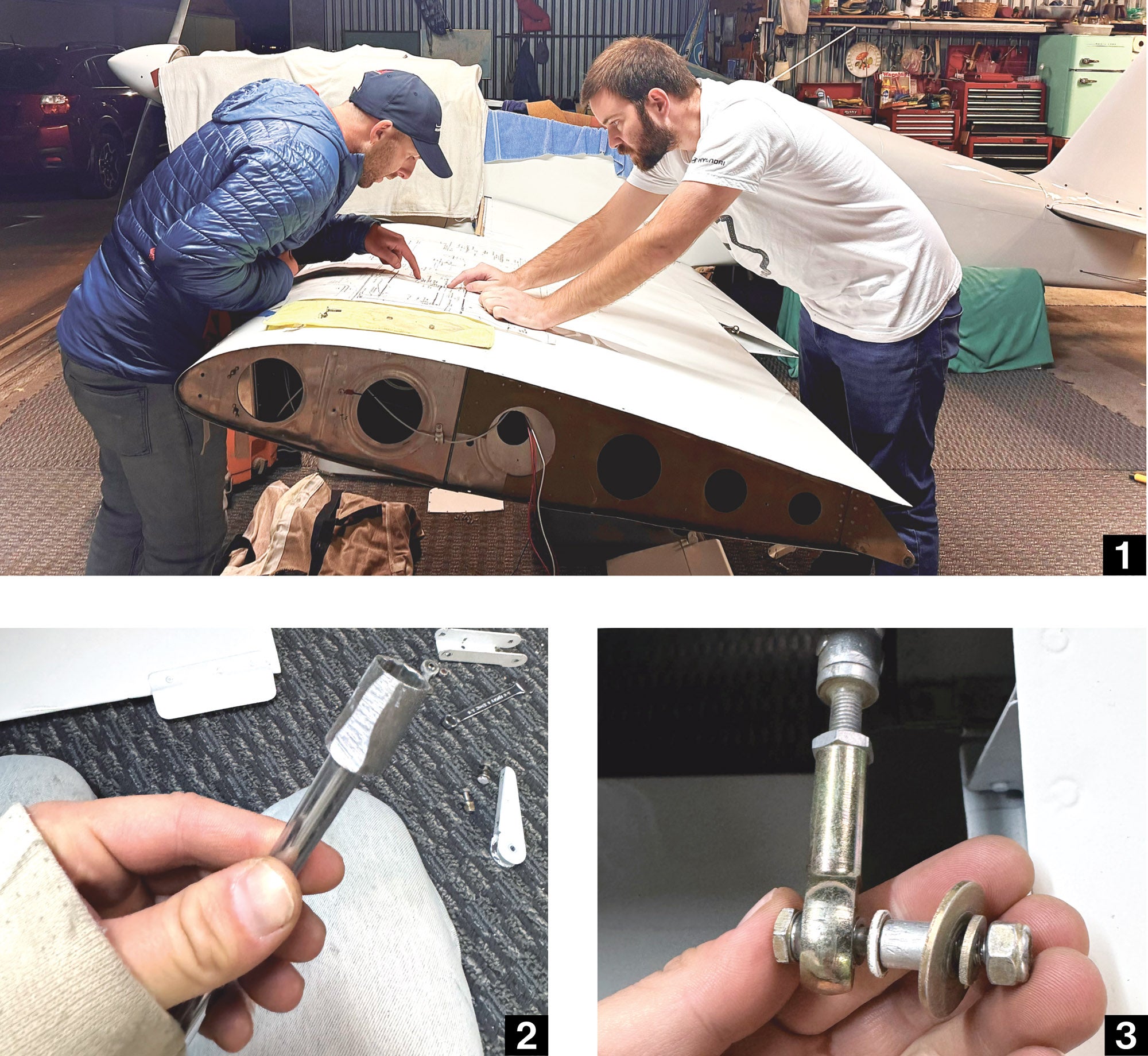
Testing the Solution: Attaching the Aileron
Kyle and my boyfriend, Zach Lauzon, spent an evening with me reattaching the aileron. After studying the airplane wing diagram, we managed to put the washers on in the correct order and almost correctly reattach it. Of course, almost. In the process, we found that because of the added washers to the brackets, we needed to adjust the spacer size. Kyle offered to help me make custom spacers out of bare aluminum. I got to go to his house and use the lathe! More on that journey later.
After successfully crafting the new spacers, we needed to test them. Zach and I went back the next day and he tirelessly worked to mount the aileron again. He had to shave down the custom spacers a little bit but managed to get both bolts through and put the washers in the correct order, all without scratching the paint. That’s a feat. Yay, Zach!
But it wasn’t over yet. When he attached the pushrod to the main bar using a bolt and tested the travel of the aileron, it got stuck! It turns out that the pushrod must go through a hole in the rear spar to get to the aileron. In the instructions, you can change the size of the hole as much as you need to for the pushrod to travel through freely without rubbing the sides. Unfortunately, somehow with our adjustments, the rod was rubbing on the hole, meaning we had to enlarge it or move a spacer and washer.
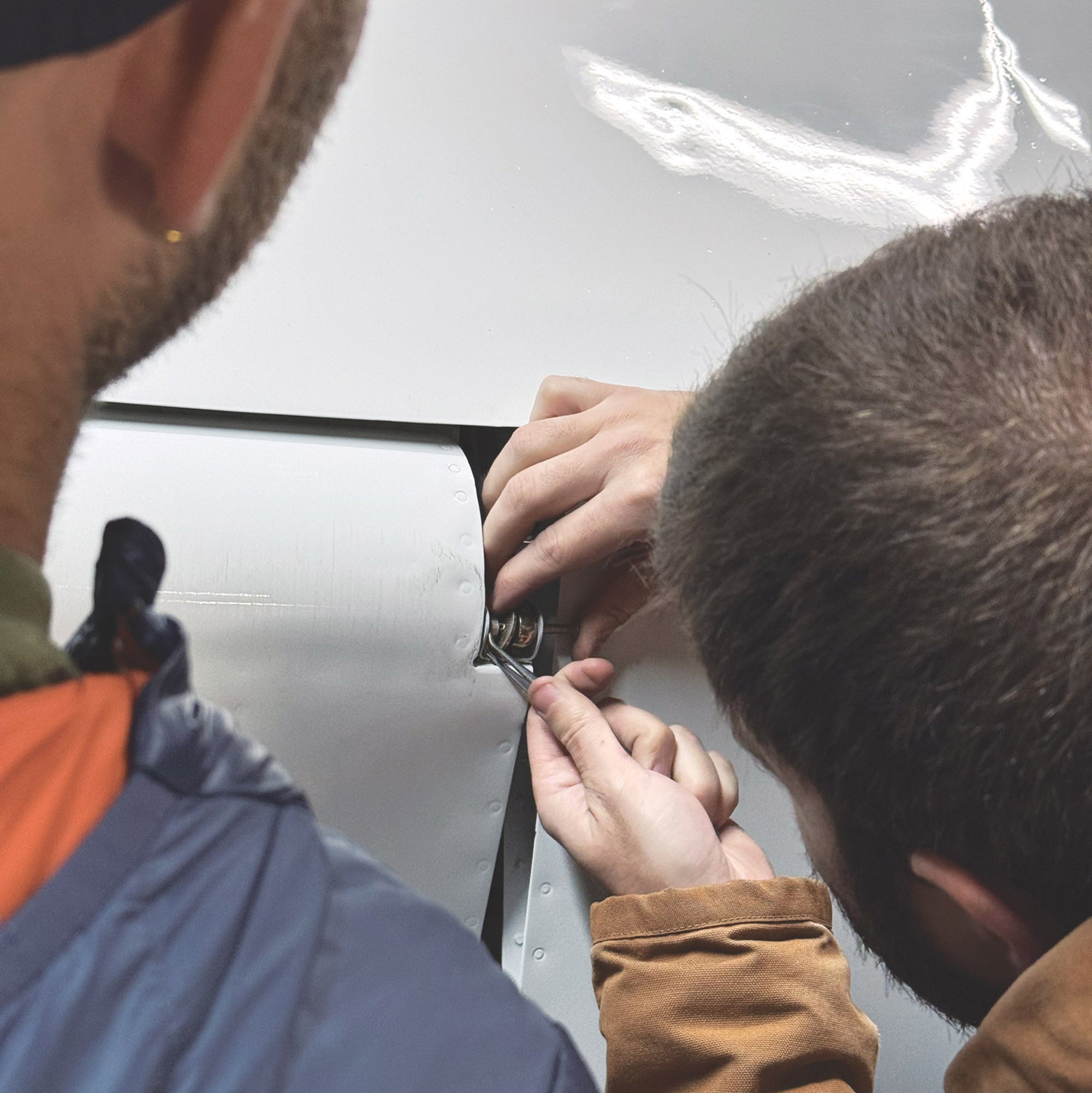
Stan and Kerry helped me assess what to do. When we looked at the size of the hole that the pushrod was going through, they were shocked. “That’s big enough for a cat to go in,” Kerry said. They advised swapping the location of the spacers and washers before trying to elongate the hole.
Kyle and Tyler took it upon themselves to try it out. They swapped the spacer and rod end in the aileron. However, that put the rod end at a steeper angle, which bound it against the big washer. Again, this limited full aileron movement. Therefore, we are continuing to troubleshoot the ailerons and are very close to completing them.
This experience points to one of the many lessons with this project. Earlier homebuilts are literally one-off examples, with so many seemingly minor variations from airplane to airplane. When trying to fit parts built for one RV-6 to another RV-6, some of this is to be expected. More modern kits, where there is intrinsically less guesswork for the builder, don’t experience this nearly as much.
Learning the Lathe
As mentioned above, we needed new spacers and Kyle’s house was the place to go. Walking into his garage is like walking into a machine-shop wonderland. He has a whole shelf of raw aluminum blocks just waiting to be made into something. Kyle’s philosophy is that instead of investing money into buying new parts, just invest in the machine to make them so you can make more if you need to. Because of this, he owns a manual lathe, CNC milling machine, multiple welders and even an industrial sewing machine.
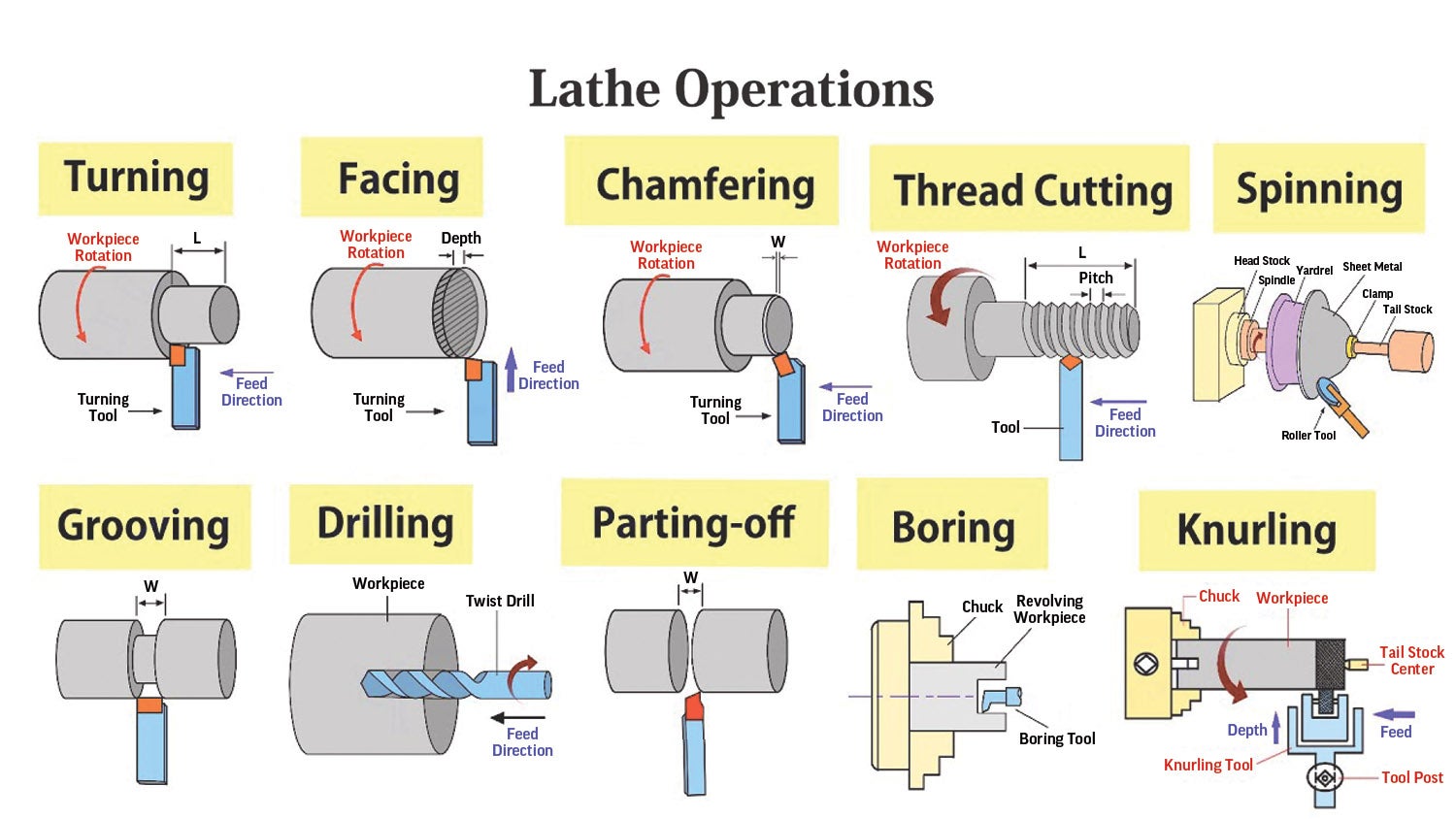
I had the great privilege of learning the lathe. We started by picking out an aluminum rod. Kyle had taken some measurements, so he knew the diameter, length and hole size we needed. We mounted the piece and then turned it down to the diameter we wanted. After that, we picked a starter drill bit and started a hole. Then, we took the correct sized drill and drilled a hole through the aluminum. After that, we measured the exact length of the spacer we needed and cut the aluminum accordingly. It left a little piece of metal sticking out when it broke off, so when the spacer fell, we grabbed it and put it back in the lathe, then carefully faced off the last bit of metal.
In a debrief with Kyle, he taught me more about the technical terms for lathe operations. “We did facing, turning, drilling, parting off and then facing the backside. In that order,” he said. He shared a photo with me to help describe it.
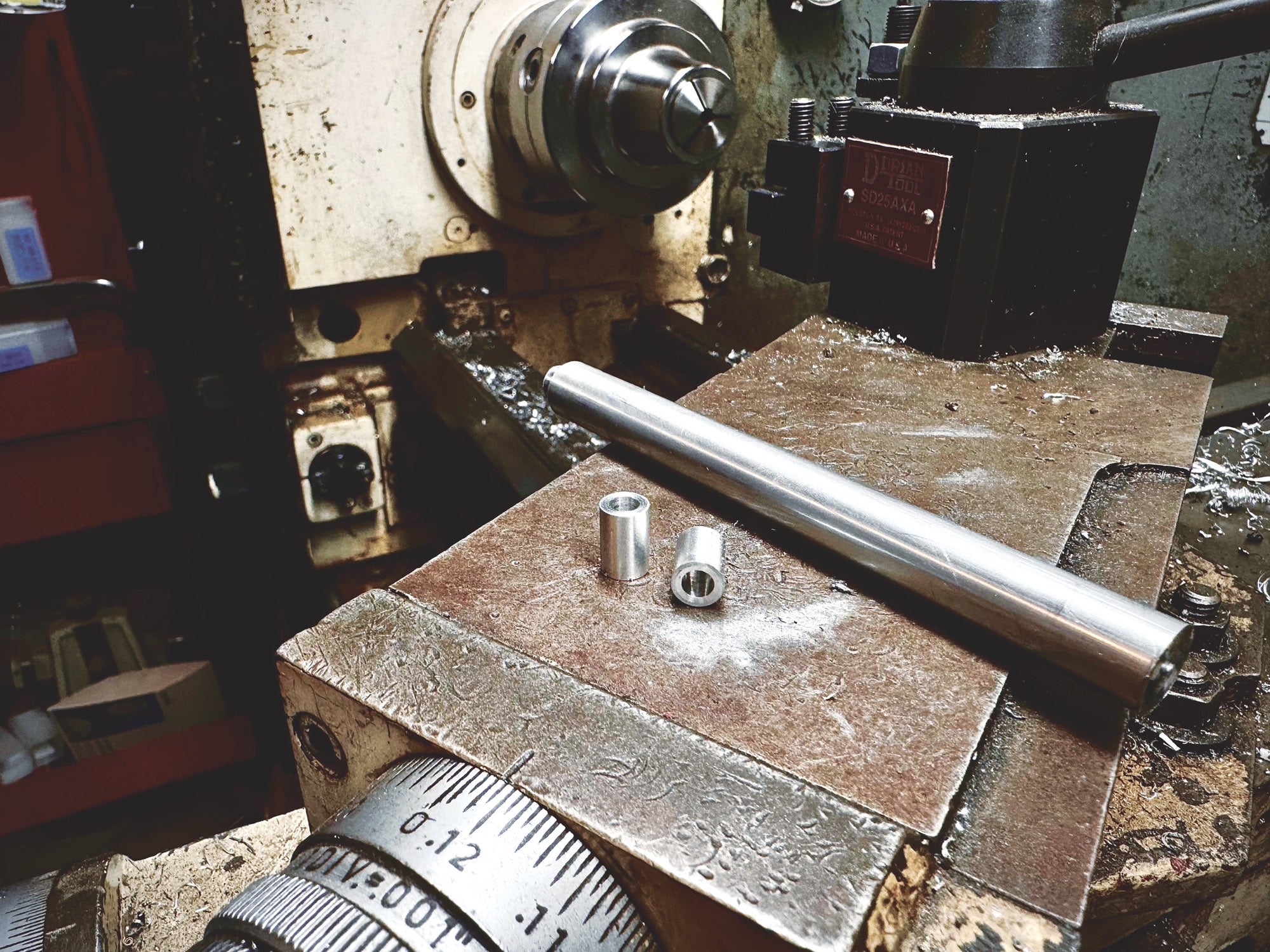
Working the Wiring
Like I’ve mentioned before, I don’t know the first thing about wiring. Fortunately, some of my friends do. Stan was out of town, so it was up to me, Kyle, Zach and my friends Tyler Pierson and Shawn Davison to figure it out. Essentially, the blind leading the blind. Fortunately, though, everyone comes with their strengths. Kyle actually does have some wiring knowledge. Zach studied the installation manual and is great at project management. Tyler and Shawn are both super smart and they always have good ideas.
The Advanced Flight Systems panel comes precut (I sent my old panel in and they custom cut it). As we’ve discussed before, we went through multiple layouts. Stan grouped the CHT/EGT harness and SV-Net harness for the EMS and sent it through the firewall, so now most everything we need to do is inside the cockpit.
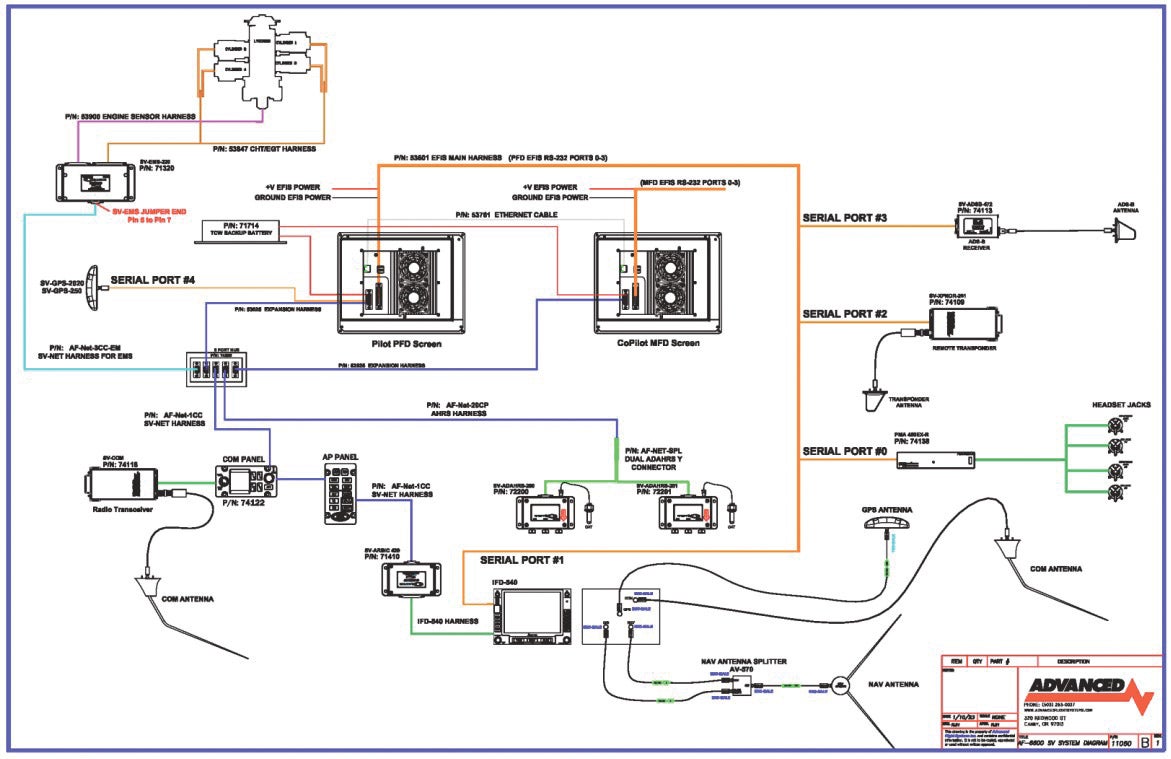
A “Big Picture Look” at the AFS Installation
Where to start? First, we need to understand what components I have to determine what needs to get done. It all starts with two harnesses, the engine sensor harness and CHT/EGT harness. They connect to the Engine Monitoring System (SV-EMS-220) to provide information about the engine. The EMS then connects to the Advanced Control Module (ACM).
Ah, The ACM. The center of it all. It’s Advanced Flight System’s genius idea to make it all a simple plug and play. A central place for everything to connect and talk to what it needs to talk to. The ACM has 20 different ports. Of the 20, we are only going to be using 17—and they connect to, among other things, the EFIS primary display, backup battery, transponder, audio panel, backup EFIS, com radio, autopilot servos, panel switches, pitch-trim motor and, of course, the rest of the SV-Network data/power cables.
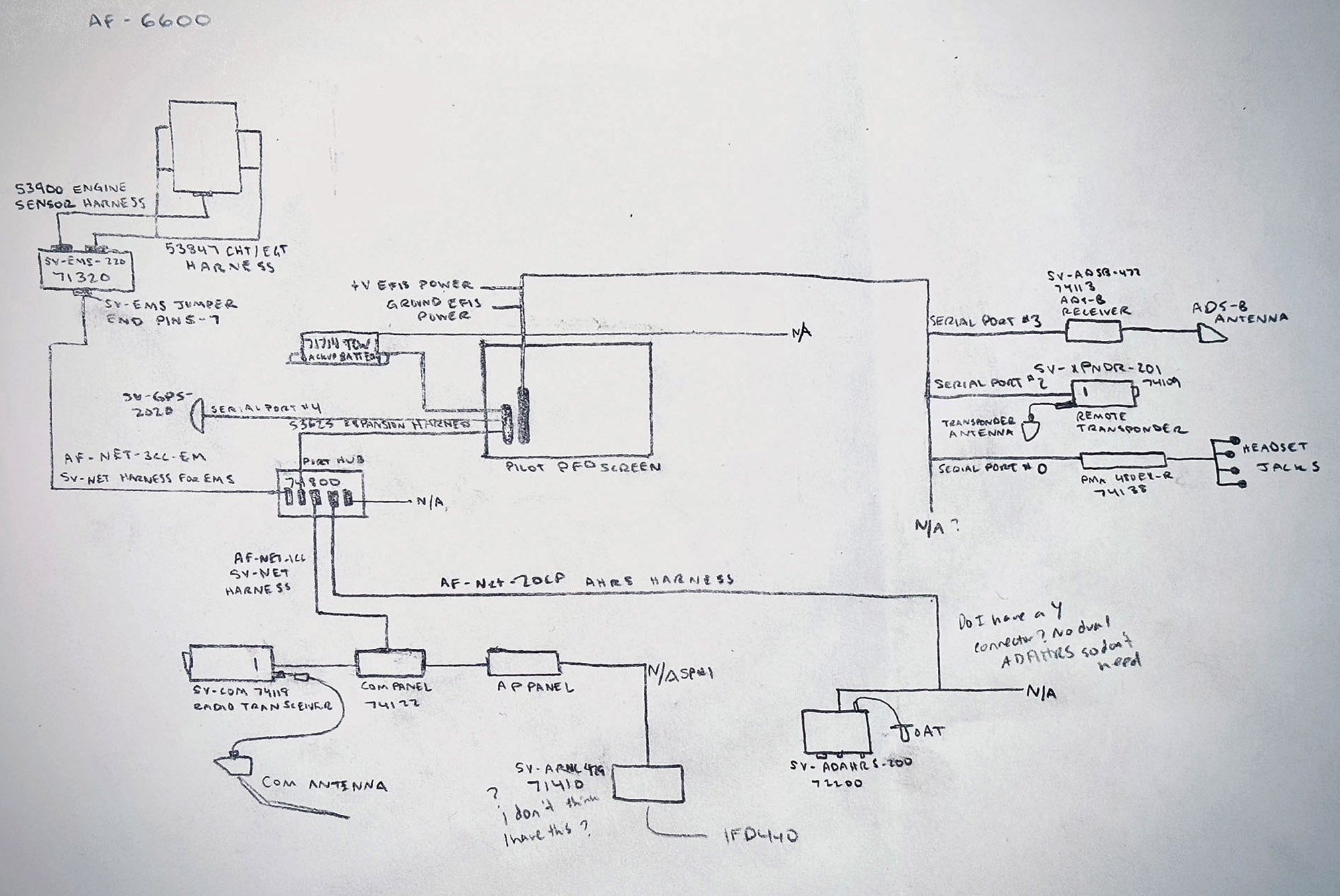
The ACM allows us to wire two to five avionics data buses. These include the Dynon Advanced SV-Network, RS-232 serial data, ARINC 429, ethernet and CAN bus. The SV-Network is the main one that I will need, because most of the Dynon components connect to it to talk to the EFIS screen. These include the SV-EMS-220, SV-ADAHRS-200, SV-COM, SV-AP-PANEL, ACM and AP Servos (pitch and roll). I also need the RS-232 serial for the backup EFIS (probably a Garmin G5), remote transponder, ADS-B receiver, audio panel, SV-GPS, ACM and radio transceiver. Right now, I don’t need the ARINC 429 (no certified GPS yet), the ethernet connector (I only have one EFIS screen because I’m broke) or the CAN bus (not a FADEC engine).
Shawn and Kyle and I hooked up SV-COM-PANEL and SV-AP-PANEL using 6/32 screws. Then we attached the switch panel and made the wires as neat as possible. We swapped some of the SV-Network harnesses around, as the one connecting the com panel to the ACM was too short. We need to get a new ribbon because one that connects the switches to the ACM isn’t long enough.
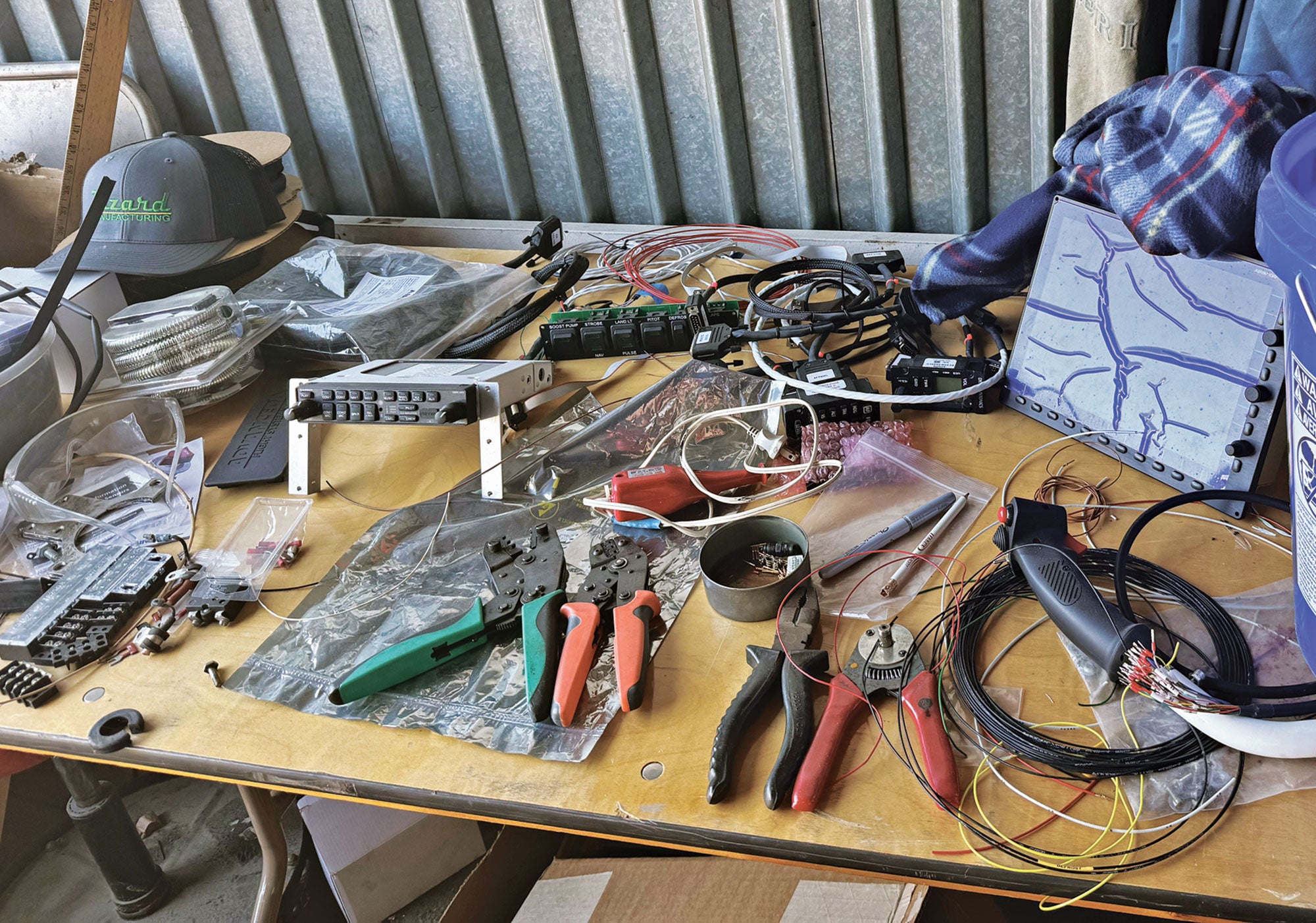
“Guys, I have a question,” I asked as we were plugging things in. “What the heck is a bus? I googled it everywhere and still don’t get it.” Shawn replied, “It’s a yellow vehicle that takes you to school.” Smart aleck. Kyle finally explained it in a way that made sense. “Imagine shouting information out to a room full of people and whoever needs the information will take it. Anyone who doesn’t will just ignore it. That’s a CAN bus. Now imagine talking on the phone and giving someone information directly. That’s a serial port.” Kyle said. Ah, the light bulb turned on.
There are a few more big wiring tasks to do. We need to terminate connectors to most of the wires that are left. These include the wires coming off the EMS and the tricky part will be measuring them, so they don’t end up too long or too short. We also need to hook up the GPS, wire the navigation lights and landing lights, install and wire the control sticks and finish installing and wiring the autopilot servos. Outside of wiring, we need to finish troubleshooting the aileron and flaps, complete the engine baffling, attach the fuel tanks and wingtips, reinstall the seats, complete the floorboard and attach the canopy and new struts. There’s light at the end of the tunnel and it’s getting brighter each day I spend at the hangar with my friends.