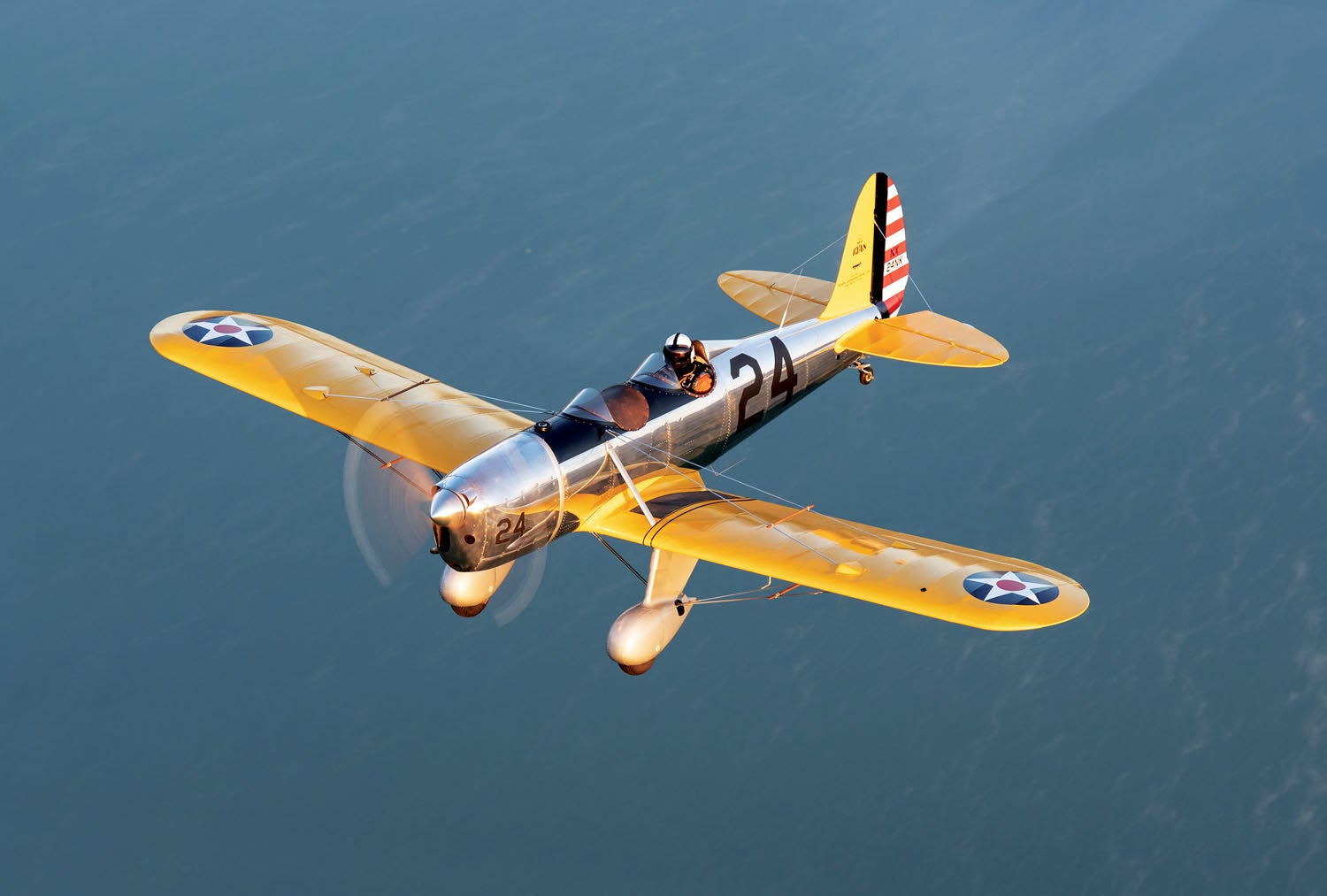
How often have you been at an airshow and seen a replica aircraft that just doesn’t look quite right? Something about the shape and proportions doesn’t seem to blend. Granted, it’s a tall order to re-create a highly recognizable airplane. But with the uncompromising goal of maintaining the form of the Ryan ST, Timber Tiger Aircraft’s replica, the ST-L, keeps the lines of the original and harmonizes its appearance wonderfully.
First flown in 1934, the Ryan ST (for Sport Trainer) was built by the Ryan Aeronautical Company of San Diego. Founded by T. Claude Ryan, the fledgling company was the descendent of Ryan Airlines, which created the Ryan NYP, famously known as the Spirit of St. Louis.
Initially powered by a 95-hp Menasco Pirate B-4 engine, the ST went on to further developments and variations, but its timeless allure remains in its graceful lines. The combination of a modern (for the time) semimonocoque fuselage with strut-braced wings, open cockpit and a graceful aesthetic appearance has drawn admirers since its debut. One fan is Nick Pfannenstiel, founder of Timber Tiger Aircraft. Thumbing through an AeroCrafter Homebuilt Aircraft Sourcebook, the ST was the one airplane that caught his eye and ignited a passion that forever changed his life.
Beginnings
Nick Pfannenstiel was 14 when he fell in love with aviation. How many of us have been there? For him, it wasn’t the flash and boom of military aviation, but rather the weird and wonderful world of unusual aircraft, especially vintage designs. He began studying everything he could about flying and aircraft and got his private pilot license at 18. A stint in college studying mechanical engineering led to the realization that while he liked some aspects of engineering, the hands-on approach was what he truly enjoyed. He left school and started his own business, a high-end custom automotive shop focused on creating hot rods with impeccable craftsmanship.
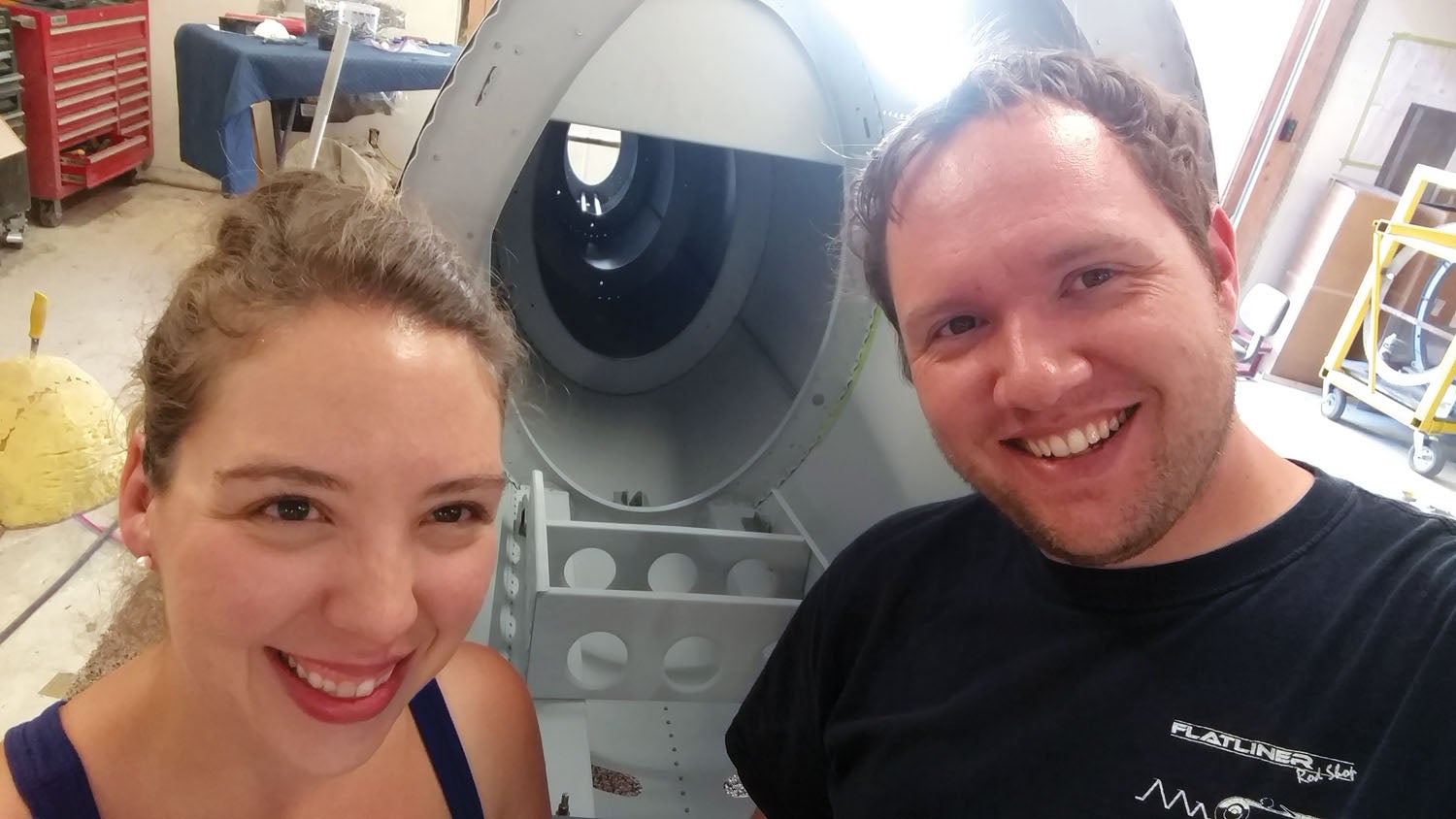
After 15 years of building cars but dreaming about planes, Nick was ready for a new challenge. With the encouragement of his then fiancée, now wife, Kayla, in February 2015, they decided to move forward with the Ryan project, a major life change. They closed the doors of their automotive business, opened Timber Tiger Aircraft (the name is a pun on chipmunks, which explains the company’s logo) and began working full time on this art-deco masterpiece. Throughout the entire project, Kayla has been a tremendous and unwavering support. “It wouldn’t have been possible without her,” says Nick. “She’s towed the project across the country twice and has managed all the logistics of setting everything up for our display at Oshkosh.”
Nick acquired a set of original blueprints for the ST and started working backwards from the drawings. His goal was to maintain the Ryan’s appearance while incorporating technical improvements.
Given the lack of readily available Menasco engines, it quickly became apparent that a full-scale replica wasn’t going to be feasible. Even other in-line engines, such as the LOM, didn’t lend themselves to the required engineering parameters, and the aircraft would have been woefully underpowered with many current engine choices. Trimming the aircraft’s size by just 5% provided the needed dimensions to work with numerous options and keep things manageable. The scaled-down Ryan ST was designated the ST-L.
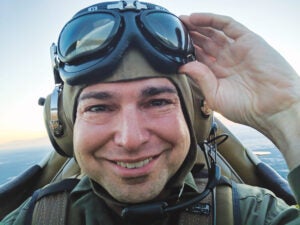
Eight minutes and 46 seconds after Nick went public with the project, posting on the Homebuilt Airplane Forum, he was contacted by Glenn Gordon, who just had to get involved. A talented mechanical design engineer, he became the self-appointed CAD consultant to the project and took the dream of the ST-L and made it manufacturable.
Glenn’s 3D CAD creations also made it possible to test ideas before committing them to metal or fiberglass. Throughout the process he kept a careful eye not only on creating parts, but also the downstream effects that would make the aircraft easy to build and maintain. Once his design work was complete, the next step was to use the CAD files to create the tooling to make precision parts on CNC machines.
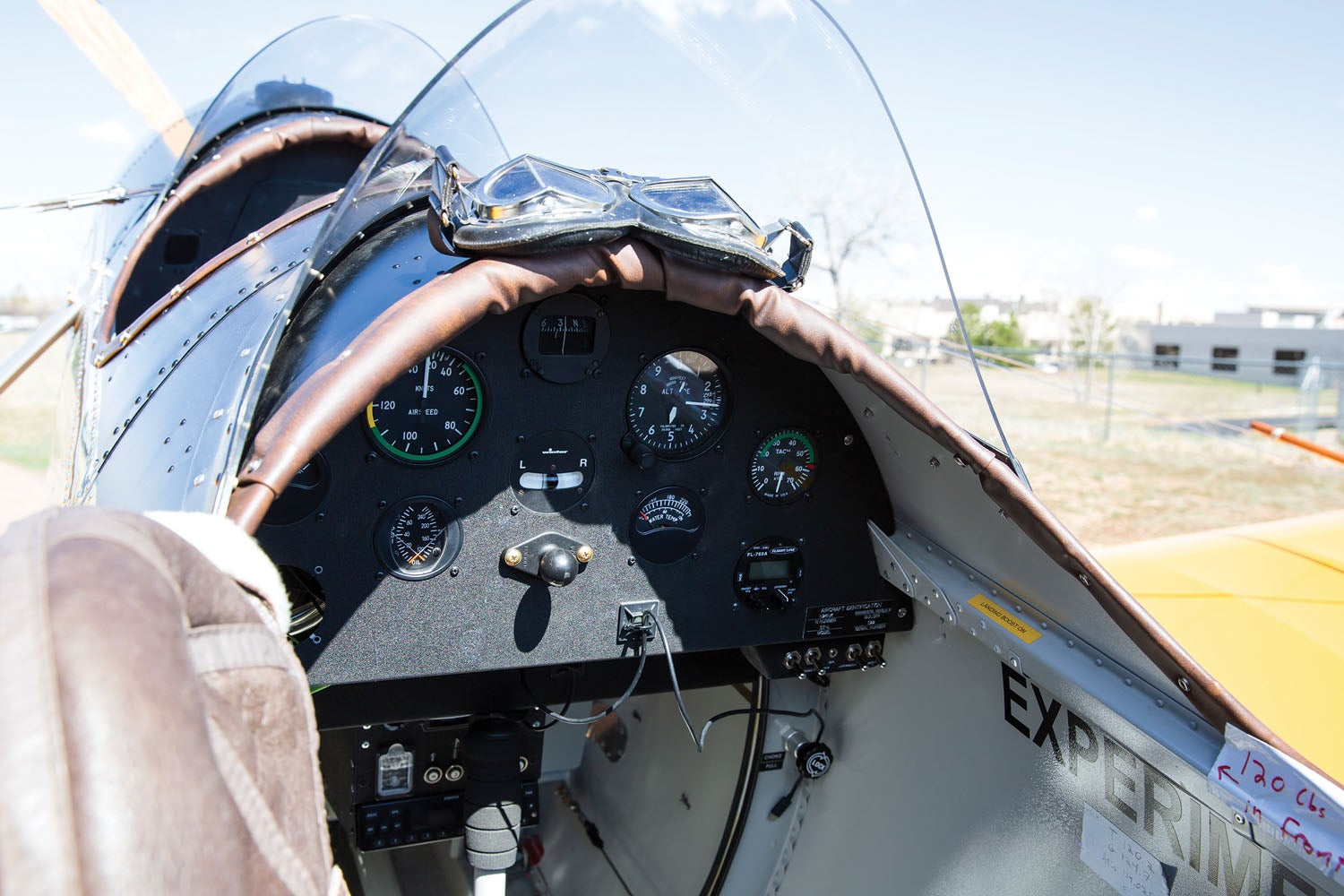
An ST for the 21st Century
While the ST-L utilizes a semimonocoque fuselage like the original, the internal structure was redesigned from the ground up. There is a central steel bulkhead, which acts as the keystone for all of the aerodynamic stresses. This is heat treated after welding for strength. Steel wing stubs and landing gear complete the central attachments. Otherwise, the fuselage is composed of aluminum bulkheads and longerons. In order to preserve the Ryan’s pleasing lines, all bulkheads are positioned in the same locations as the originals. Other aspects of the airframe, including the tail feathers, wings and landing gear, also flow together nicely and fit the 95% scale replica perfectly.
Although it is 5% smaller than the ST, the ST-L actually has more room in the cockpit. “To create more space, we moved the rudder pedals to either side of the front seat rather than keeping them behind the seat like the original,” explained Nick. “So far, people up to 6 feet 5 have fit comfortably.”
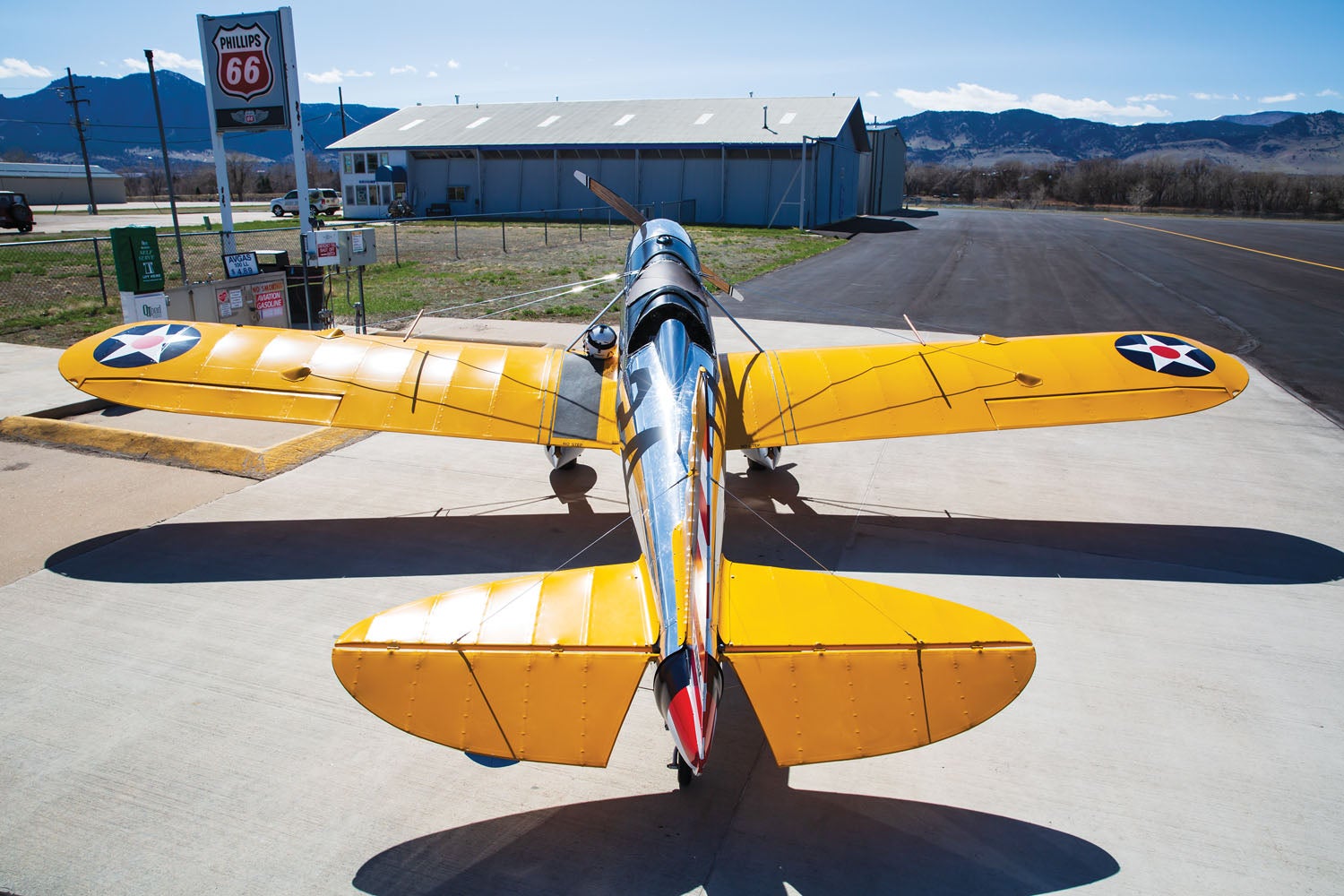
For the wings, an aluminum spar was used in place of the wood spar found on the ST. The airfoil was changed from the original NACA 2412 to a Riblett GA30U-612, like that of the Kitfox. The ribs are a bonded aluminum honeycomb, which provides added strength while saving weight, and they are coated with an epoxy primer for corrosion protection. The wings are covered with Superflite, and the paint is from Stewart Systems. For simplicity, the drag/anti-drag wires were switched to a drag truss, similar to what’s used on the Kitfox and Just Aircraft’s Highlander/SuperSTOL series.
The Ryan ST has a reputation for being squirrelly on landings, mostly because of the leading-link landing gear. This was replaced with a torque-link landing gear, making ground handling much easier. “If you can fly a Citabria, you can fly this replica,” is the opinion of both Nick and Brooks Mershon, who has been doing most of the test flying of the prototype.
Nick’s brother Jake did the welding of the prototype, and Nick says he would be remiss not to remind folks that such a project wouldn’t be possible without the involvement of numerous other people, including his parents and the rest of his family. “It’s easy to forget because their encouragement comes so naturally, but we wouldn’t be where we are today without their help and support.”
Because the ST-L was specifically designed to look as much like a real ST as possible, small details can make a big difference. Giving the illusion that a Menasco Pirate engine is lurking under the cowl is a four-pipe exhaust stack, although only two of the pipes actually do the job. Looking at the landing gear fairings, you can’t help but notice the mock rivets that help preserve the appearance of the original spats.
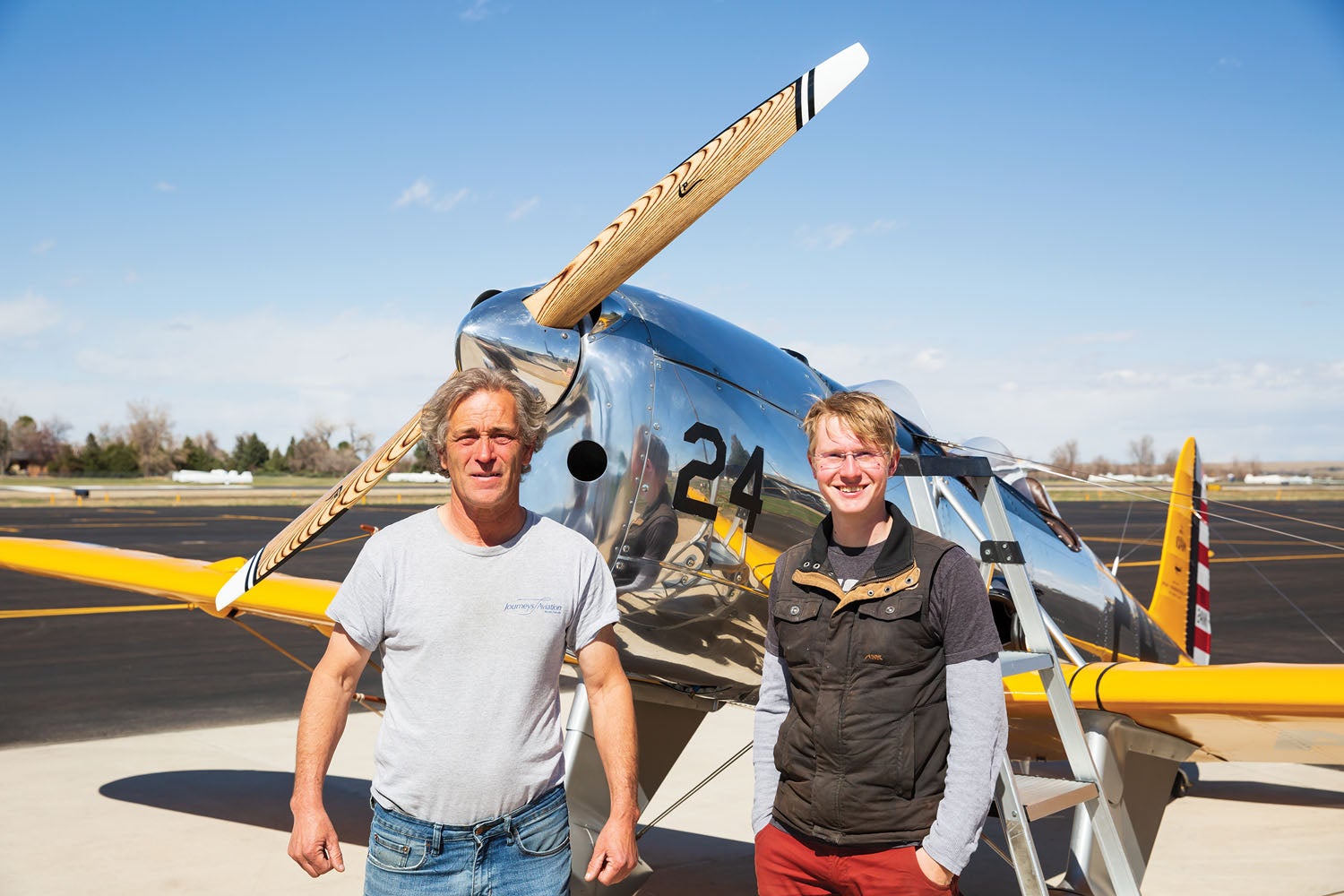
Equally impressive is the handcrafted cowl, formed by David and Maxwell Wenglarz at Wings Metal Work in San Pierre, Indiana. “They create works of art out of metal and have been just amazing to work with,” says Nick. “However, for those who want to make their own cowl, it can be deleted from the kit.”
Completing the appearance of a resurrected icon from the golden age of aviation is the polished aluminum finish. While it does require a certain amount of maintenance, for those interested in authenticity, it’s entirely worth the effort. (A big thanks to Steve Pomeroy of Journeys Aviation at Boulder Municipal Airport for polishing the ST-L for the photo shoot!)
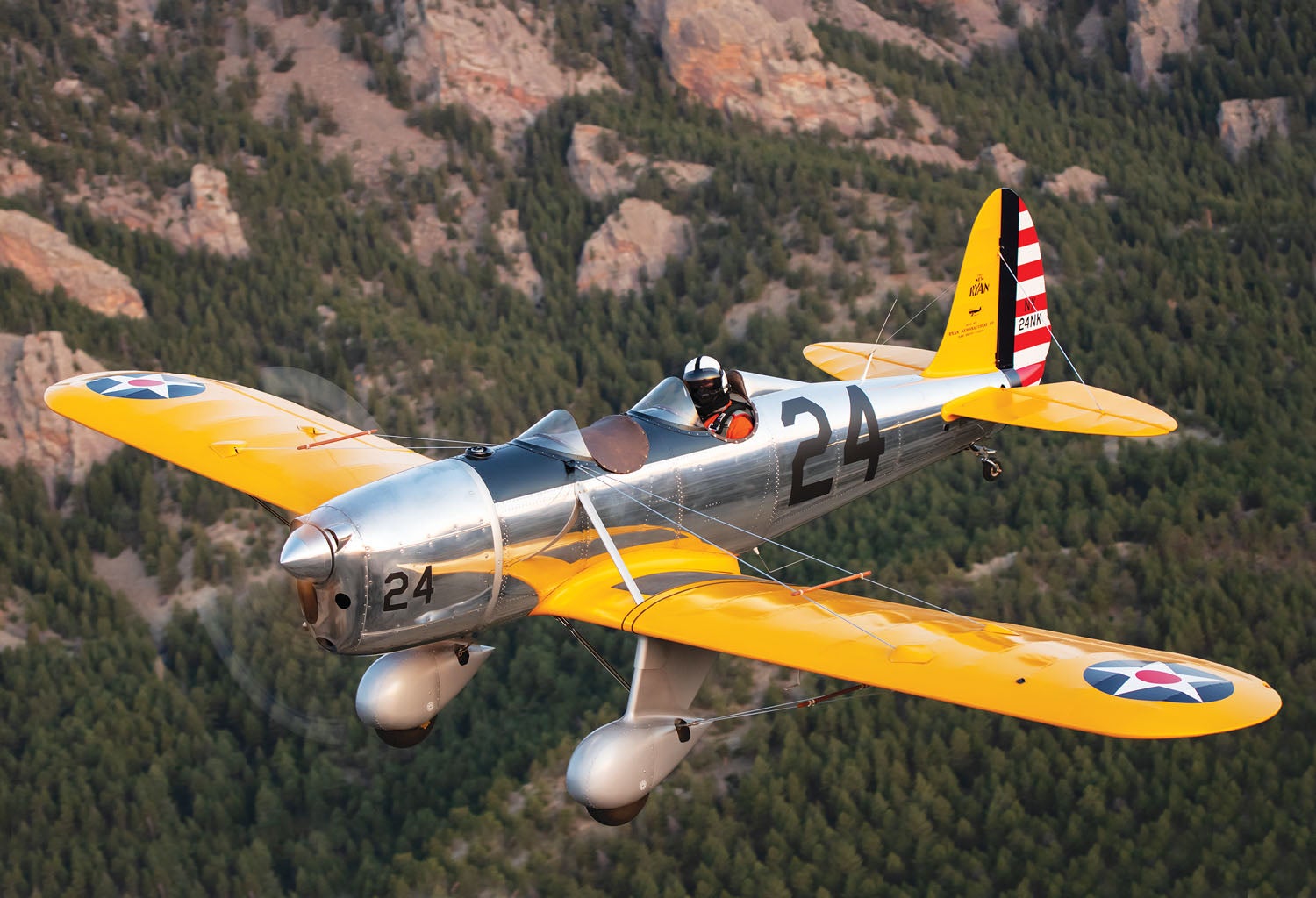
A Few Refinements
At the end of construction, the ST-L came in 200 pounds lighter than the original ST. For the most part, everything worked as expected, but there were a few tweaks along the way.
During the initial taxi test, Arlan Grover, the project’s original test pilot, found that the landing gear didn’t track as well as expected. To solve the problem, “We wound up going back to the drawing board and put together better geometry that has worked out quite well,” explained Nick.
When towing the prototype across the country to AirVenture, there was a mishap when the tailwheel wasn’t properly secured. While bouncing along, it eventually collapsed, damaging the rear bulkhead and requiring a redesign. After reviewing what happened and performing structural analysis, it was determined that the bulkhead took the equivalent of more than 36,000 landings before it deformed. The redesign should tolerate even more.
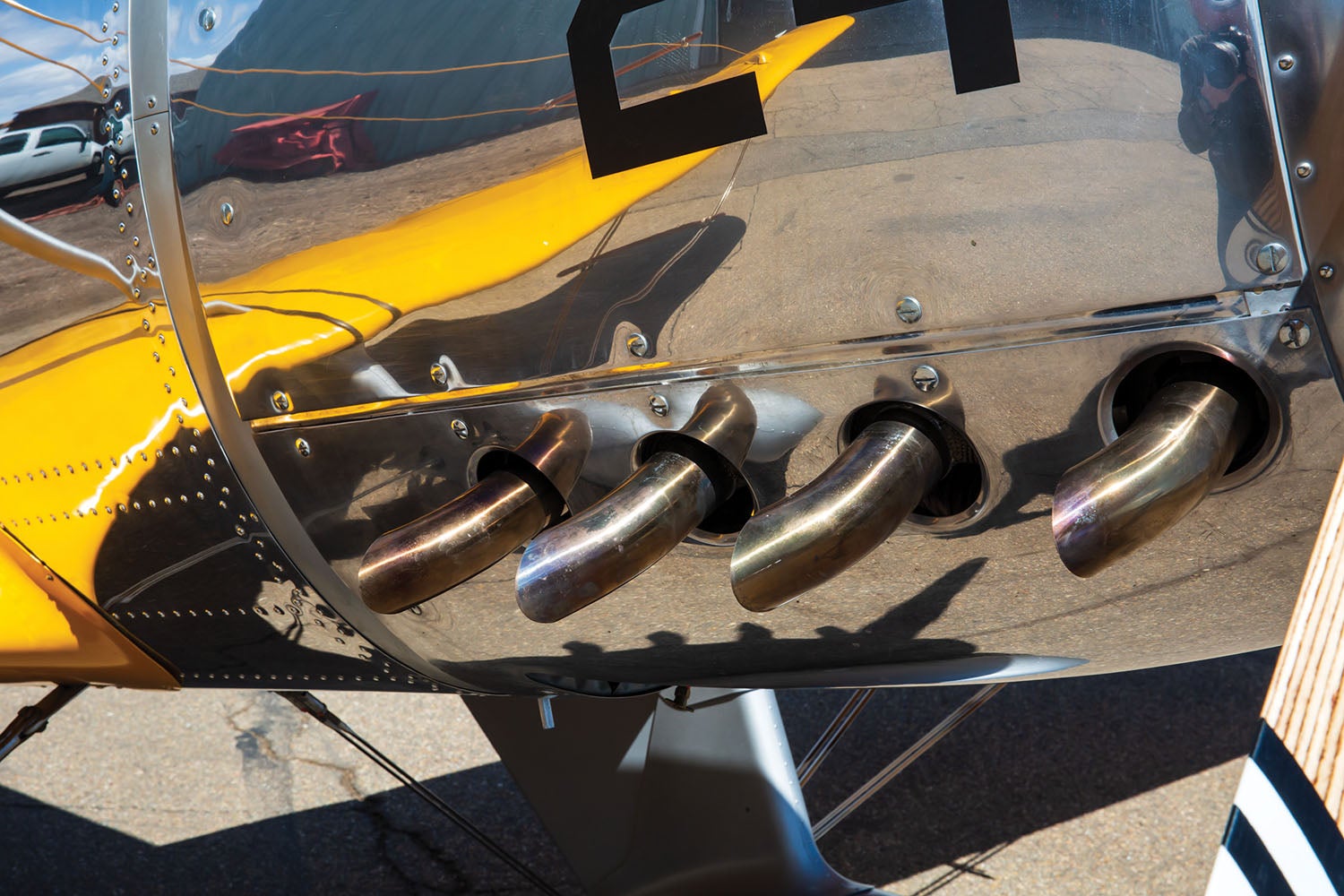
What About the Engine?
Given the shortage of Menascos, the decision was made to go with a 100-hp Rotax 912 ULS, which fit perfectly under the cowl and has performed wonderfully in the prototype. Also considered was the 121-hp D-Motor LF-39. A Continental O-200 could work but will require some reworking of the cowl.
Ideas for the future include the 100-hp AeroMomentum AM13, and the extra horsepower of a Rotax 915 is tempting, especially given that the prototype is based in Colorado and operating out of Boulder at 5288 feet msl before density altitude is ever considered.
“A few people are interested in putting a radial engine on the airframe, such as a Rotec or Verner,” says Nick. “We are working with one customer who wants to go that route.” While the ST and PT-22 have the same lineage, they are very different aircraft. The PT-22 is about 300 pounds heavier than the ST, so they fly and handle very differently.
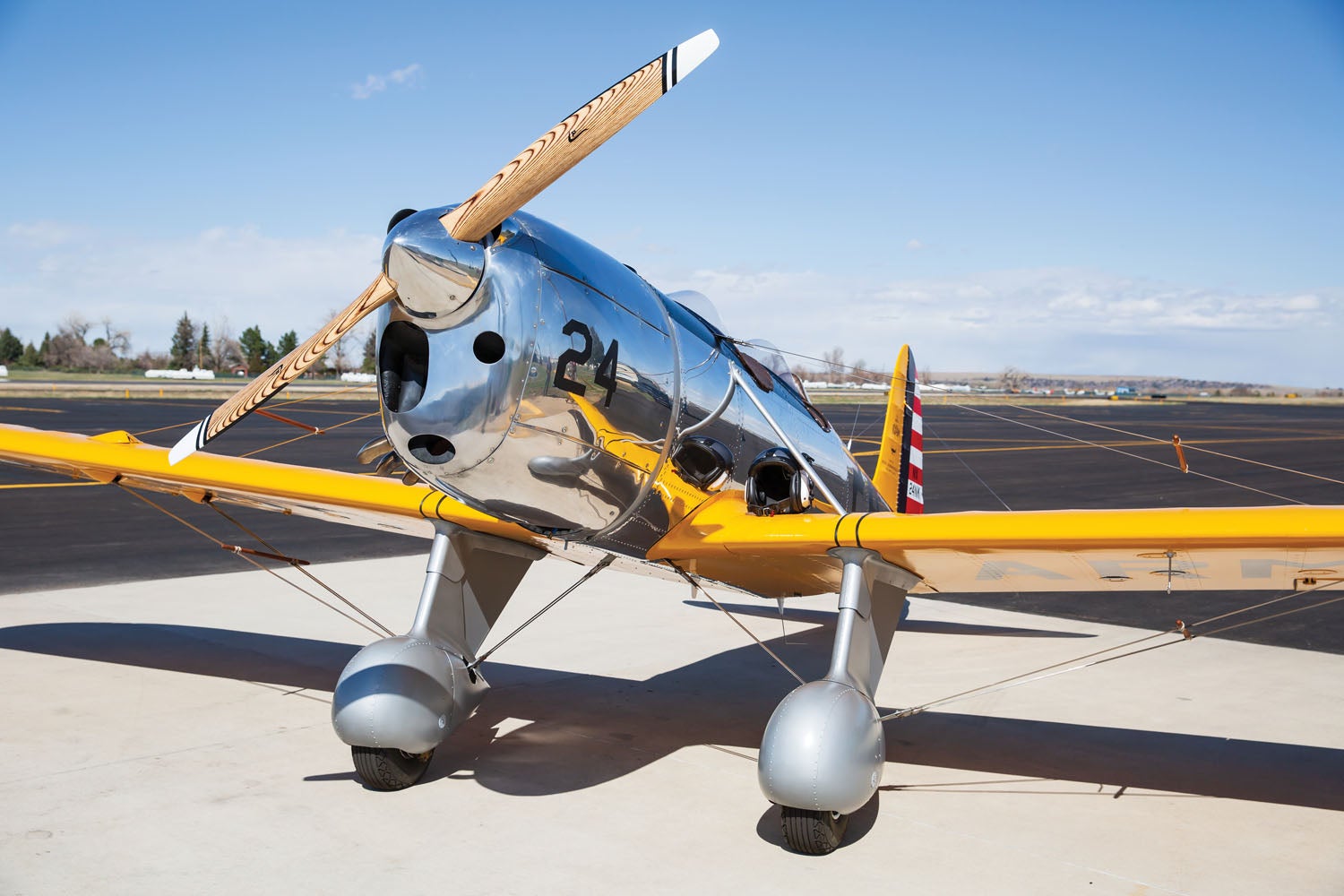
The lines of the PT-22 also call for a more rounded fuselage. According to Nick, “The ST-L doesn’t lend itself to the PT-22 easily, although it can be modified. It would be easier to replicate the radial-powered PT-20A, which was the predecessor to the PT-22 and has more in common with the original ST.”
There is a very interesting article by Norm Goyer entitled “The Beauty and the Beast” if you want to go down the rabbit hole of comparing how each plane handles and flies.
Putting Together the Kit
The ST-L kit is set up to create a natural progression where building one component naturally flows into the next. Starting with fuselage bulkhead Number 2, for example, the steel components are assembled first and everything else is added to this core. Structures and skins are predrilled where possible, but the tapered skins preclude predrilling all of the pieces. The builder will need to make a jig to build the fuselage. However, this is not required with the fully riveted quickbuild option.
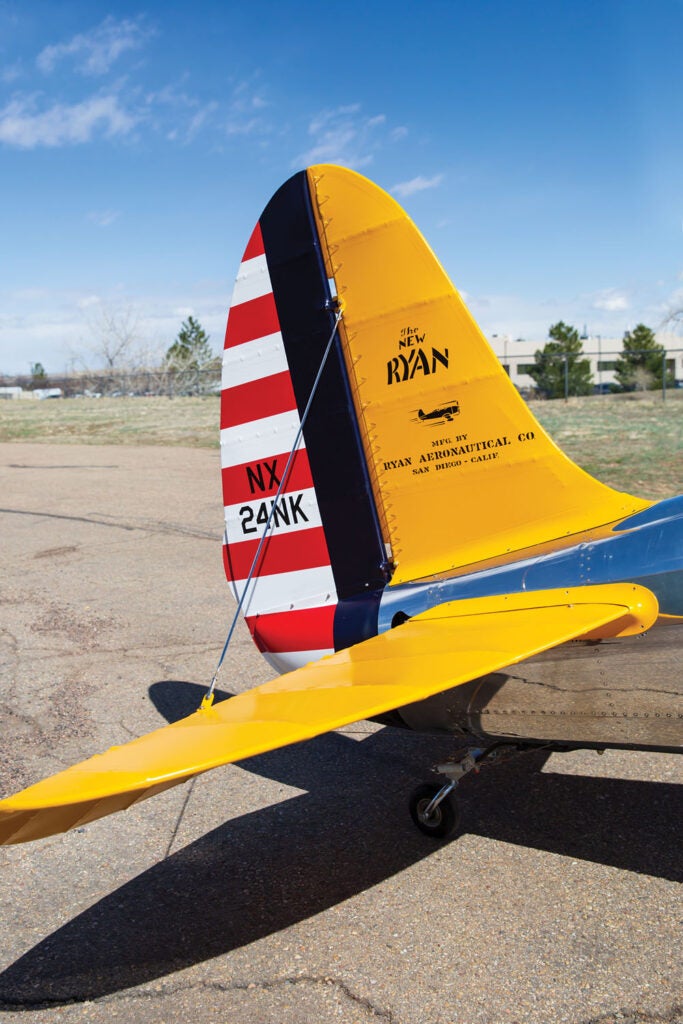
Aluminum components are riveted into place using either solid or pulled rivets. For aesthetic reasons solid rivets are encouraged. The tail is composed of ribs attached to tubing, just like the original ST.
The wings can be constructed on a flat table and act as their own jig. Control cables have been replaced by push-pull tubes, and changes to the ST-L structure make wing rigging significantly easier than it was with the original ST. Other wing modifications include the change in airfoil and landing gear geometry, the addition of hydraulic toe brakes, simplification of the landing gear shock absorbers and using wire attachment fittings at the lower landing gear.
The finishing kit includes the handcrafted metal cowl to maintain the lines of the ST, as well as the firewall ring. The wheel pants and fairings for the gear legs, wing roots, stabilizer, rudder, gas cap and windshield are all fiberglass but can be made of aluminum if desired.
Build time is estimated at around 1500 hours for the standard kit, with significant time savings if the quickbuild fuselage option is selected. As of 2021, the estimated average cost to build is $75,000 to $90,000, but the price will vary from plane to plane depending on the engine and other options.
Kit production started on March 1 of this year. Current lead time for partial kits (such as the fuselage, wings and tail) is approximately two months, with a four-month lead time for complete airframe kits. There has been significant interest in the ST-L, and some of the kindest praise was from Dick VanGrunsven who, after checking it out at AirVenture, commented, “Why hasn’t someone done this before?”
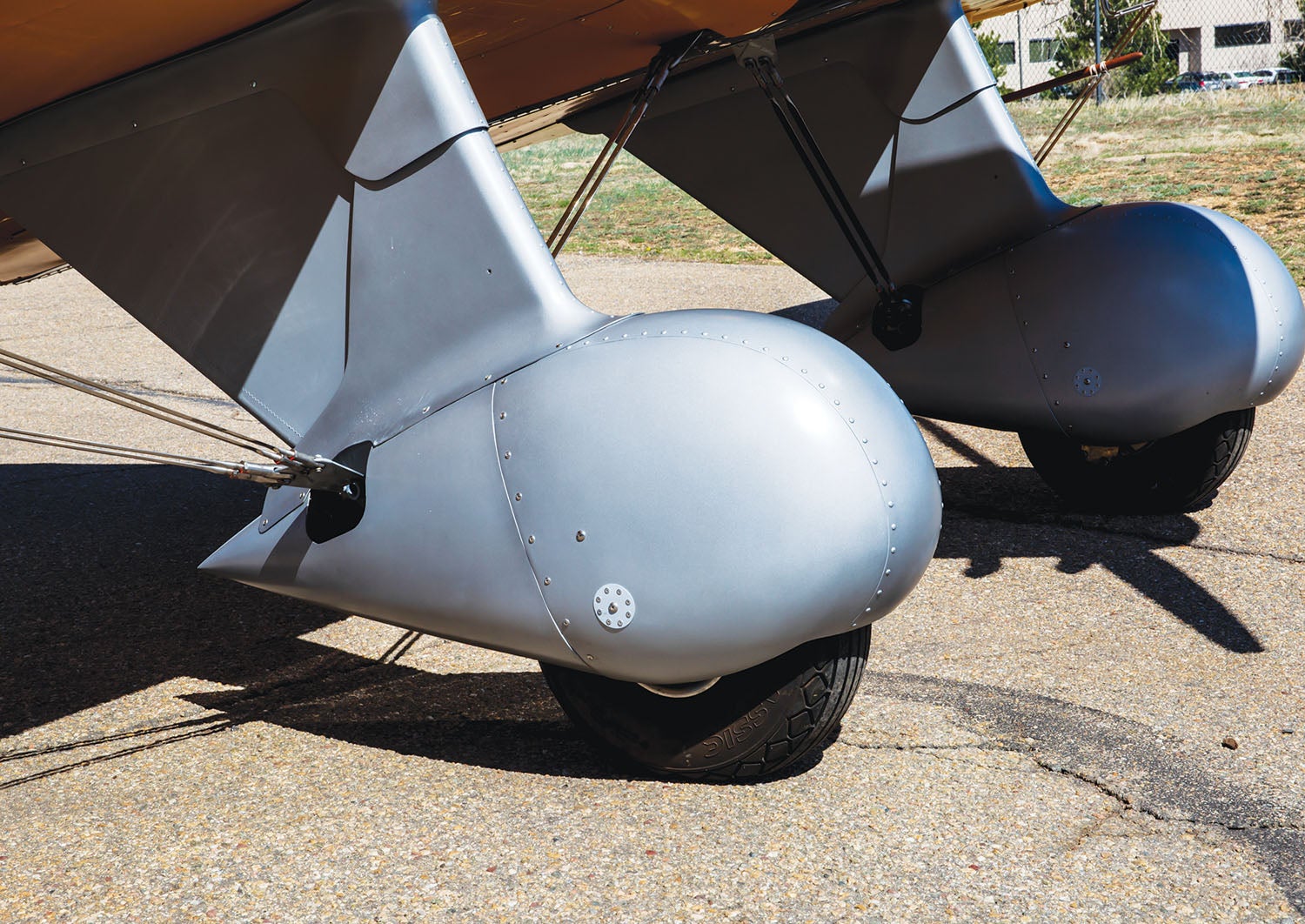
How Does It Fly?
We won’t go into great detail about the flight characteristics now, but you can expect a full flight review of the ST-L in a future article. Test pilot Brooks Mershon shares that “At the risk of sounding like a cliché, it flies like a Cub…or, if not a Cub, a Cessna 150. With its high-lift wing it’s very predictable and, well, easy to fly. Everything happens at a slow speed. But when you pull up to the fuel pumps, you feel like a hero. Everyone comes out of the woodwork to check it out. It feels like you just arrived in a classic convertible.”
By all reports, the ST-L has no vices. It cruises around 80 knots at 4800 rpm and up to 113 knots at higher power settings. It stalls around 40 knots, power off. Frank Johnson at Performance Propeller has been “incredibly generous” and provided the climb prop that is currently being utilized (and is a piece of art).
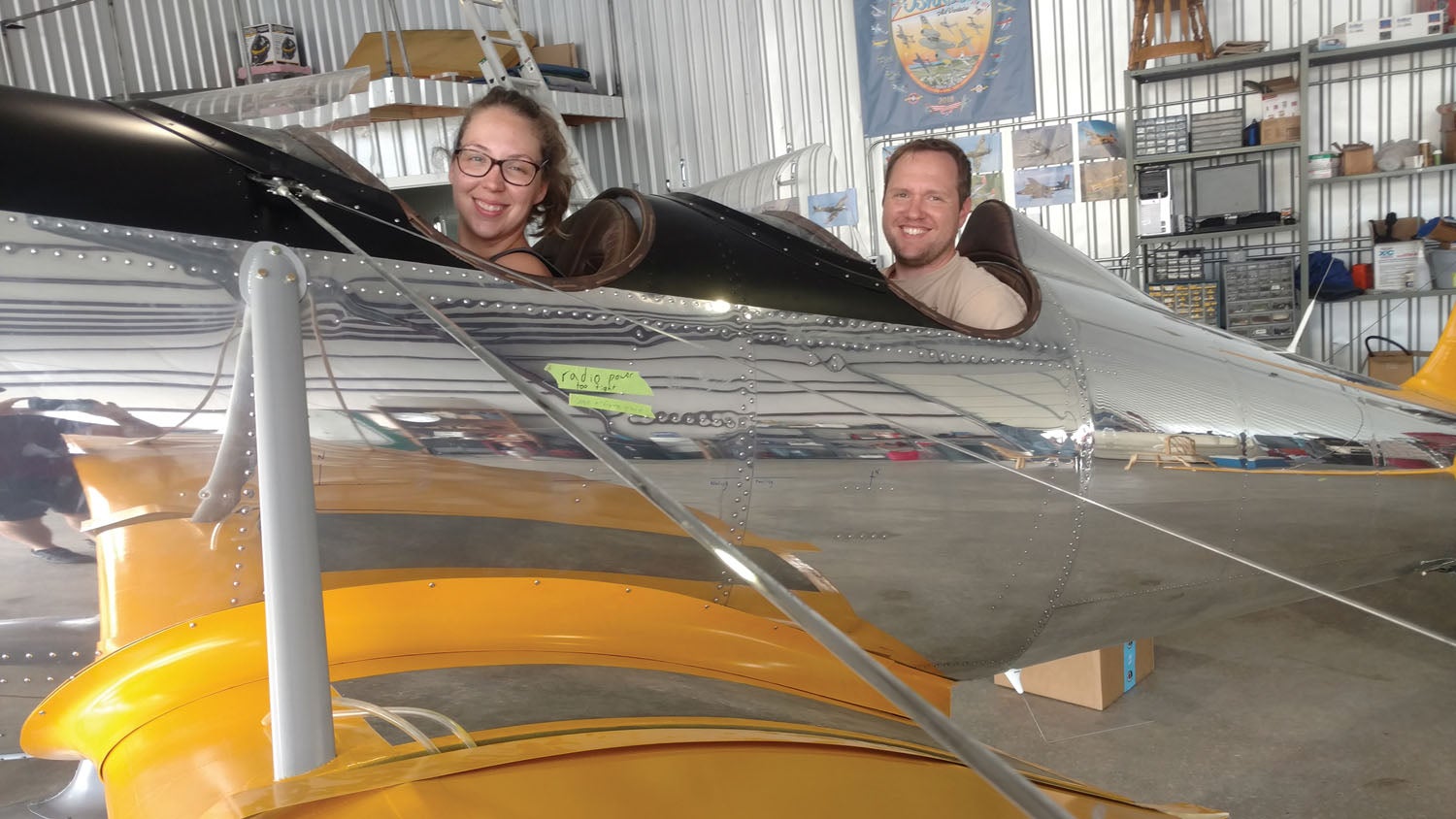
With 200 pounds in the front seat, Brooks has had the ST-L up to 14,000 feet without any dark corners showing up. It is slightly lighter in roll than pitch and rolls about 90° per second.
One consideration that keeps coming up during testing is that, like most Light Sport Aircraft, the ST-L has light wing loading. This has limited its crosswind component as they continue to expand the flight envelope.
Future exploration includes plans to clip the wings by a foot and a half on each side by removing the last rib bay and extending the ailerons inward the same distance. This will increase the airframe tolerances to +6/-3 G, allowing for increased aerobatic capabilities. After all, this airplane is clearly meant for more than just straight-and-level flying.
Design engineer Glenn Gordon is starting to build one of the first ST-L kits and plans to trim the wings as described and add a larger engine. It should be quite the performer! For more information visit www.timbertigeraircraft.com.
Photos: Julia Apfelbaum.