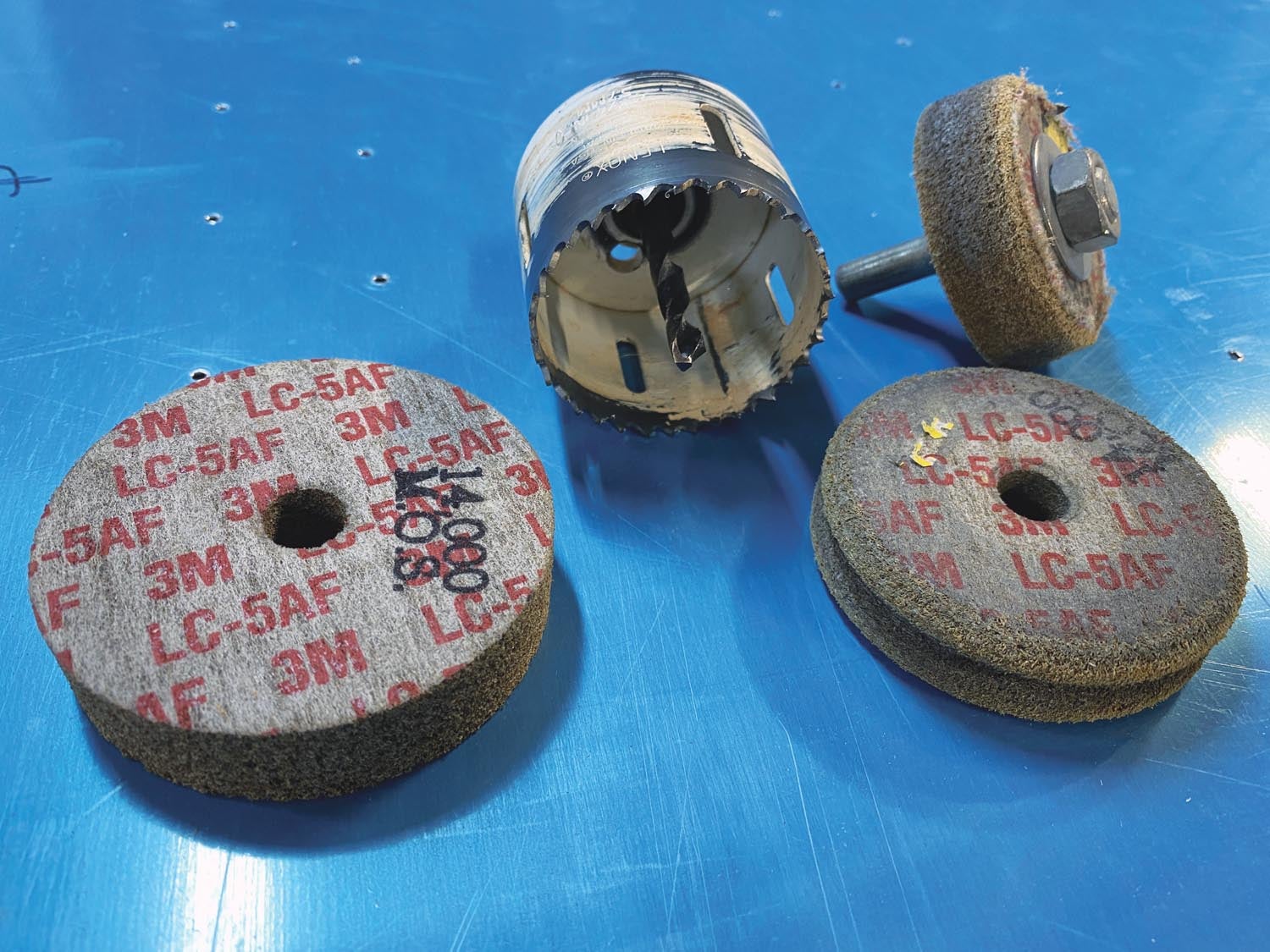
Making round holes with drills or Greenlee punches is fairly simple, but how do you keep it round when you have to “freehand” it? To make the fuel filler neck hole in the top skin of a GlaStar wing, the builder is instructed to drill a 2-1/4-inch hole with a hole saw and then enlarge it for a precise fit because the location obtained by measuring from the skin’s edge can be off by about 1/8 inch.
So, let’s say you need to move the hole to keep it centered on the fuel filler neck while making it larger at the same time. Drill the hole undersize, then find the exact location and mark the edge with a fine marker. Now you can use a half-round file and go slow or a round file in an air-powered grinder and gently creep up to the line. That will get you close, but chances are the hole will not be perfectly round or it may have some scalloping from filing.
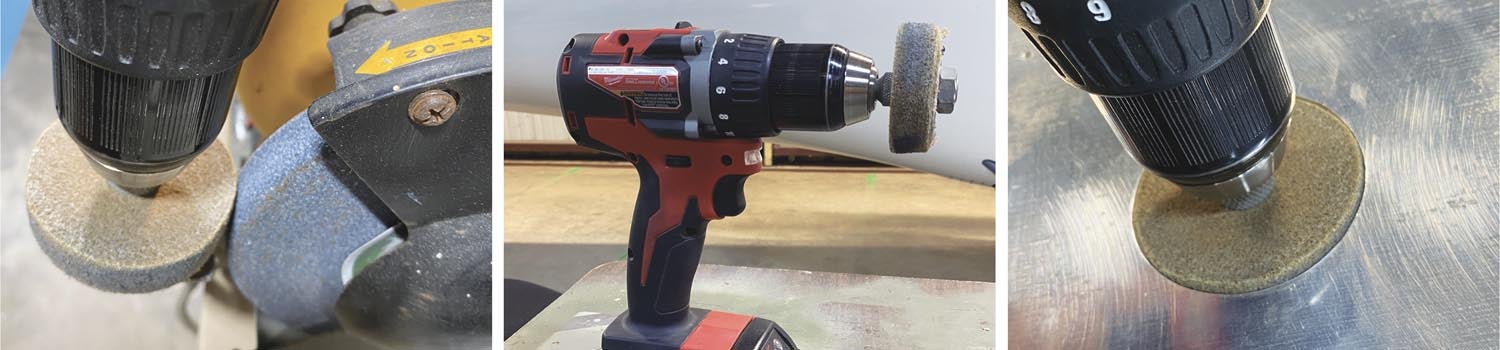
Instead, I had a used-up 3-inch Scotch-Brite Cut & Polish wheel in my toolbox that I would use in my drill press to deburr parts that couldn’t be easily maneuvered around the 6-inch bench grinder-mounted wheel. I chucked it in my cordless drill, I reduced the diameter of the small deburring wheel on the grinder and gave it a slightly conical shape. Now it was perfect for use on the large hole in the wing skin.
The skin is only 0.032 inches thick so the deburring wheel makes quick work of getting the size exactly to the line.
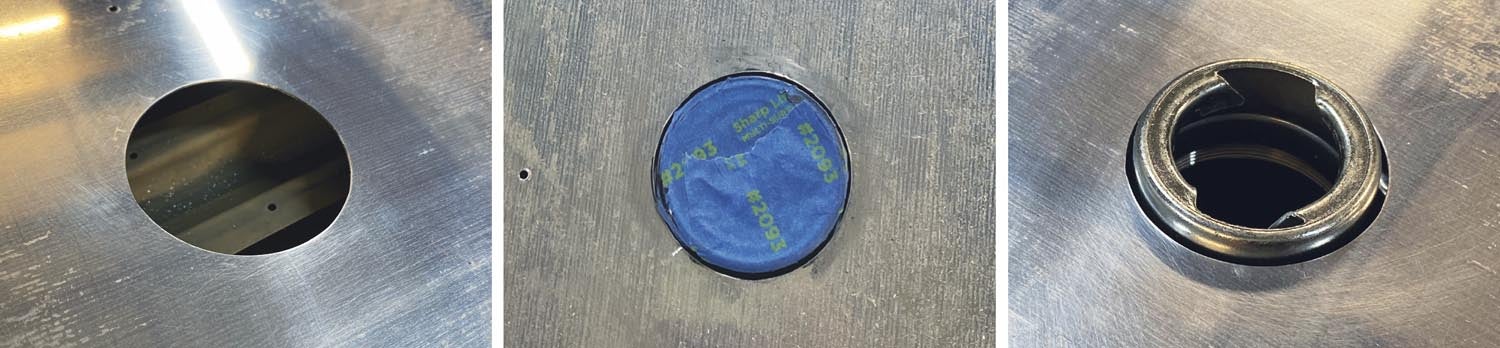
The same could be accomplished with a sanding drum of a diameter smaller than the hole—just keep moving it in a circular motion because dwelling in one spot will do the opposite of what you’re trying to do. No one likes egg-shaped holes.
Helpful tips, Omar!