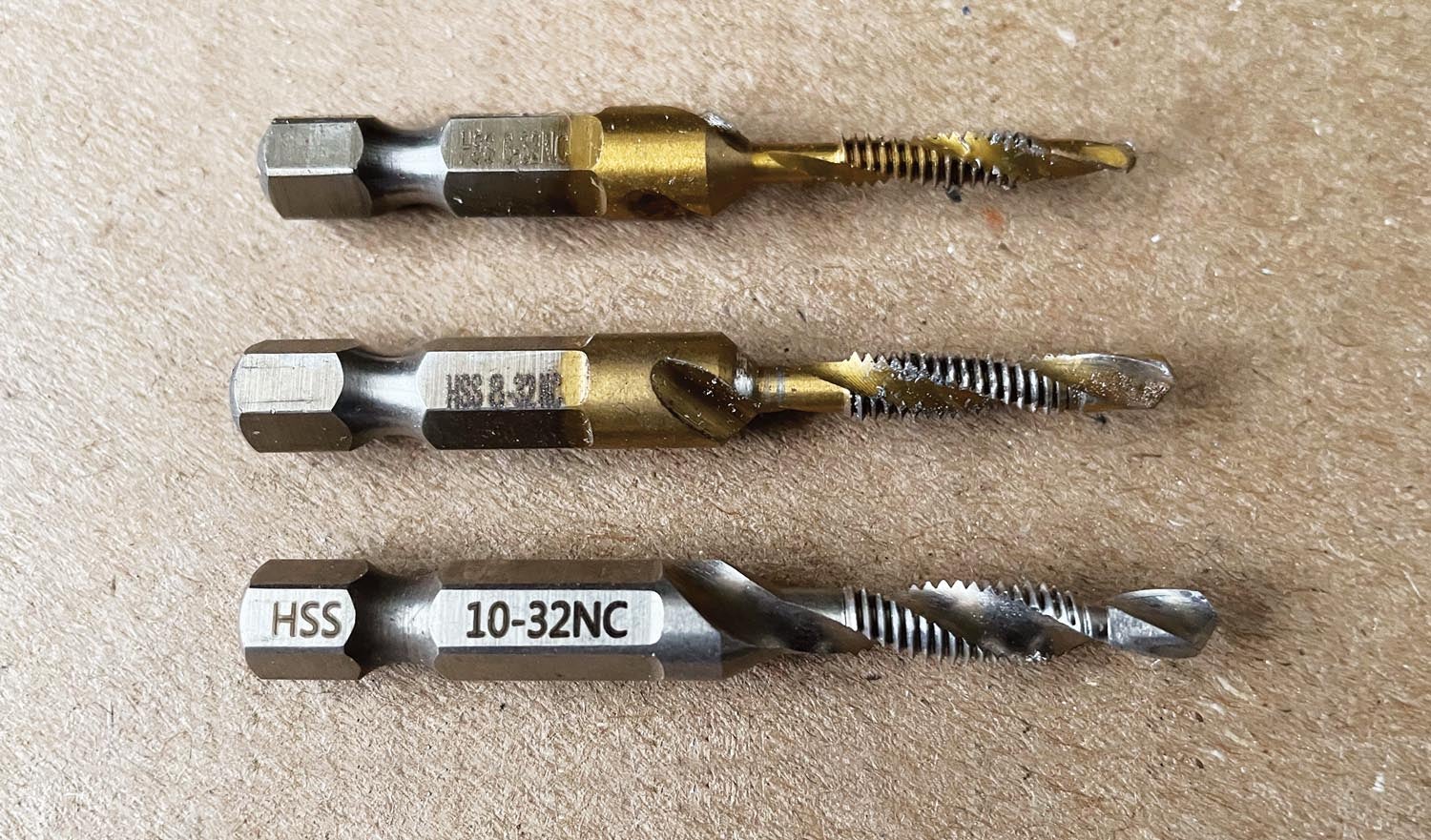
We use quite a few small machine screws in our homebuilt projects. These small screws might be found, for example, holding the instrument panel together with all its miscellaneous brackets and mounts. Other uses for these fasteners are quite numerous and varied including inspection cover panels, trim pieces, etc. Every screw requires a corresponding nut for attachment. This can come in the form of a nut, nut plate, nut clip, rivnut or simply a threaded hole.
The advantage of using a screw over a rivet as a fastener is the ability to easily remove it as desired. This allows us to inspect, repair or maintain an area of the aircraft without delay or challenge. In fact, someday you might wish you had not used rivets in some part of your aircraft for this very reason. There is an endless need to take things apart. More screws and less rivets if the structure allows!
Using nuts with machine screws is the common standard where it makes sense. Sometimes using nuts is not possible when access to them is not possible or not easy. The next set of choices include installing a nut plate or, if possible, tapping the material with appropriate threads to match the screw. This eliminates the nut or nut plate altogether. Often this tapping procedure is overlooked because of the complexity and time needed to implement. Who wants to drill and then carefully run a tap through dozens of holes? It also takes a long time to complete. We need a way to speed up the drill-tapping procedure so many holes can be completed in short order.
There is a unique drill bit that can both drill and tap holes simultaneously in very short order. How fast? The total time to complete a drilled and threaded hole is just moments longer than just drilling the hole!
A closer look at this type of bit—called a drill tap bit—reveals that a thread cutter is located just beyond the drilling portion of the bit. This means that the drilling procedure includes the tapping operation moments later. After the bit cuts the threads into the hole, you must stop and reverse the drill, backing the bit out of those new threads. The drilling and tapping are one continuous operation.
These drill tap bits require you to use a slow drill speed (about 300 rpm). It is good practice, but not required, to drill a pilot hole first. Each bit drills and taps for a specific screw size. I have been practicing with #6, #8 and #10 machine screws (32 threads per inch). As you might expect, tapping very thin sheet metal becomes problematic as there is not enough room for multiple threads. Aluminum sheet as thin as 0.063-inch thickness seems adequate for small screws.
This fast tapping doesn’t change existing engineering standards for the strength available when tapping thin materials. Looking carefully at these bits, you can also see that the last part of the cutting shank is designed to create a chamfer into the tapped hole. This is useful when using countersunk-head screws. So, there are really three distinct operations that can be performed before backing the bit out.
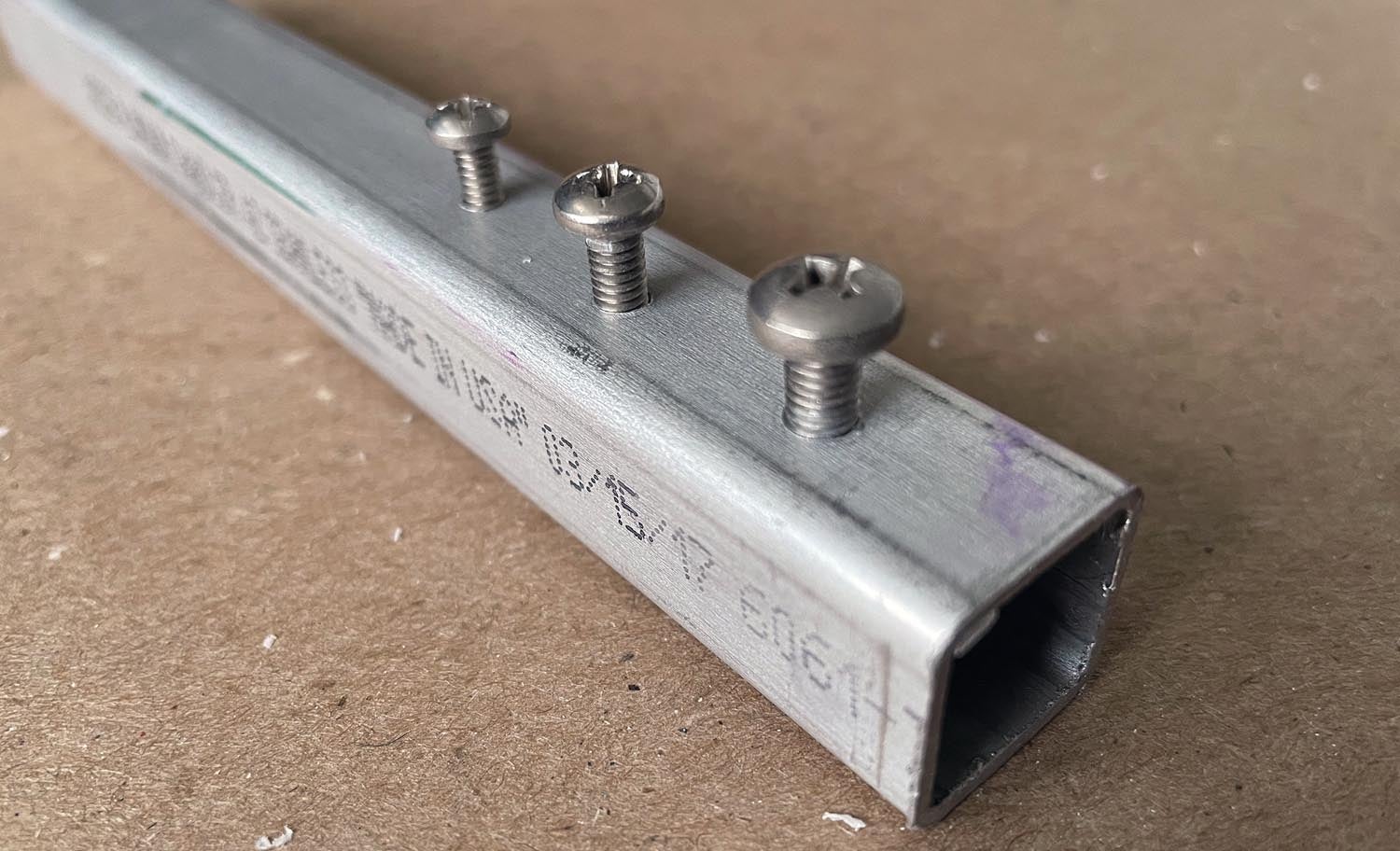
These bits are available from the likes of Amazon as well as any good tool supplier. They have been around for a long time. They are well suited for the aluminum we use when building our aircraft. I would not expect them to hold up well when tapping steel of any considerable thickness.
Remember that tapping using conventional tools into steel requires slow, careful rotation of the tap with repeated backing out to clear burrs. In contrast, drill tap bits go in fast and back out only once! So, limiting these bits to aluminum is our expectation. Once you try one of these and experience how easy and fast it is to tap, you will find yourself using machine screws more often. Leave the rivets for those aircraft areas that never come apart. Plane and simple!
Any quality brand names for these drill/taps please? Sick of buying worthless junk tools that don’t last, from dodgy vendors?