Florida in August-hot, steamy, with an atmosphere just waiting to add more humidity. Sitting in the hangar of Sport Performance Aviation with its principals, Dan and Rachel Weseman, we talked about the condition of the grass runway at their airpark near Jacksonville. It had rained on and off for a couple of days (typical of Florida in summer), but Dan was confident that the tires of their new single-seat LSA-capable airplane, the Panther, would not sink into the unmowed turf and underlying soil. As the sun broke out from behind the latest lone rain shower, we decided to give it a go-2700 feet should be more than enough to see the little plane airborne.
I had come to Florida to fly their new creation: a CAD-designed, low-wing taildragger that promises to be a fast build to an airplane that should be loads of fun. With a pop-riveted airframe, the prototype is powered by a 100-horsepower Corvair engine, modified for aviation use. The instrument panel spoke of the airplane’s simplicity -a single Grand Rapids Technologies Sport EFIS was joined by a small radio and five switches-all that was needed to play gleefully among the clouds.
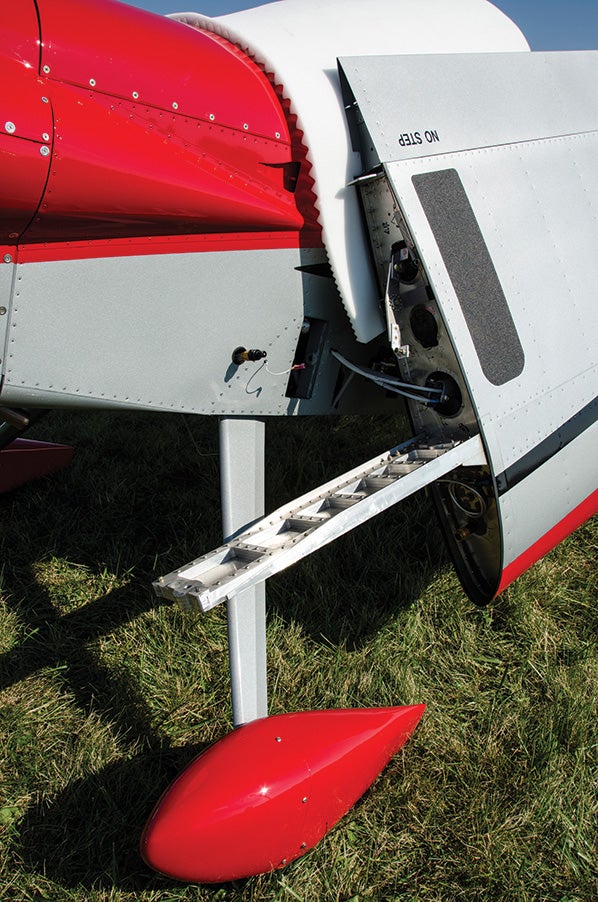
Having missed the sunrise starting time and endured the breakfast shower, I launched into a sky with scattered cumulus (some of which had ambitions of greatness) about 10 a.m. There was no real wind and no bumps; it was a perfect opportunity to see what the little Panther could do.
Engine start was simple-except for the unnerving feeling that something was wrong when I hit the starter button and the prop began to turn the wrong way! Oh, that’s right-it’s a Corvair, mounted tail forward-that’s just the way it turns. I made a note to self: left rudder on takeoff! After powering up the EFIS and letting it align, I added power to taxi across the wet grass of the Weseman’s taxiway and kept the power in to keep from settling into the swampland until I made it to the runway. It was hard to tell if the brakes were effective, for all I had to do was reduce power and Florida had me in her grasp. Steering, however, was excellent with the single-link tailwheel connection. Truthfully, who needs brakes in the grass? Dan had assured me that they were adequate, and in fact, they proved just fine on landing.
Run-up was, again, simple. Switch off each of the ignition systems in turn (to make sure they both work), wiggle the stick, check the carb heat and fuel valves -and we were off! Acceleration was about as expected for a 100 horsepower engine in long wet grass; while not exactly Lindbergh-like, it was not what a naval aviator would remember as a cat shot either. There was that odd tendency to wander toward the right side of the runway-ahh, the left-turning prop! All was comfortably controlled with rudder however, and we continued to accelerate. There was never any doubt that we would be airborne before running out of turf; the liftoff was smooth and establishing a climb still gave me excellent visibility over the nose.
The cockpit is surprisingly roomy for a single-seat airplane; most pilots will find the room to be more than adequate. The panel will allow customization and a simple EFIS will more than meet most builders’ needs for instrumentation and low cost.
Visibility, in fact, was wonderful in all directions. The airplane would best be described as a “fastback,” with enough of a bubble to provide a pilot’s view in all directions that anyone can comfortably achieve, unless they are an owl. The cockpit is roomy for a single seater, but even loosening up a harness strap and peeking over your shoulder gave not much more than sky. A quick rock of the wings confirmed good roll control-light, stable, and sure. Pitch was likewise comfortably controllable. A wag of the rudder provided the odd sensation of sliding back and forth across the cockpit-the parachute not having good purchase on the painted bare seatback. The fact that the slide was noticeable gives praise once again to the roominess of the cockpit-in most single seat airplanes, the pilot is fitted like a pea in a pod.
Climbing out of the airport area to a few thousand feet, the first thing on my list was to check the stability in all three axes. The airplane stayed where I put it in both pitch and roll, with no tendency towards divergence. Elevator trim was more than adequate and suitably quick to establish whatever speed condition I liked. The airplane liked to stay at whatever angle of bank I desired-little additional stick force was required to keep it in-or to keep it from steepening. Rudder stability was strong-a boot full gave a straight shot back, with little overshoot when released. The rudder was quite effective and light as well-pointing the nose well off axis was easy.
The seat can be adjusted before flight for distance to the rudder pedals and angle. Most pilots will find a way to make the cockpit fit comfortably.
Rolling into turns of various bank angles, I noticed that I had to actually move the stick back a little to maintain altitude. Many airplanes require a little back pressure, but the Panther wanted movement as well. For some reason, this was more noticeable at the onset of a turn than at steep bank angles. Not objectionable, but simply a bit different from other low-wing sport planes.
Satisfied that the airplane was nicely behaved under cruise conditions, I decided it was time to slow things down. Pulling back on the power and the trim knob (placed side by side), it was no trouble at all to bring the ASI down to 60 mph. Turning left and right, there was no tendency to bob or bobble. The airplane was smooth as silk in the slow-speed regime. When I leveled the wings and pulled back into a power-off stall, the buffet came about 2 mph before the break-which was straight ahead. The controls stayed effective throughout, and there was never a feeling that the airplane might depart controlled flight. The test pilot had told me that it took positive, pro-spin controls to keep the airplane in a spin, and I saw little to no tendency for the craft to surprise the pilot with a violent departure.
Putting the throttle back in and trimming for level fight, it was time to see what the little airplane would do flat out. Accelerating in the smooth air at 3000 feet, the ASI finally settled out at 162 mph. With a temperature of 75 F, that came out at 171 mph true-not bad on 100 hp. Cruise speed is a function of power setting, of course, and the Panther folks have not yet completed performance tables that would help one choose a speed, rpm, and fuel flow. But in the end, does it really matter? This is not a cross-country cruiser-it’s a fun plane! Knowing that it can make it quickly to that hundred-dollar hamburger is enough.
As a sport plane, the Panther was designed for aerobatics-not competition aerobatics, of course, but the kind you enjoy on a smooth morning flight-or when being bounced by an airpark neighbor. I started out with a couple of aileron rolls, followed by barrel rolls. Both left and right, all were fine and smooth. The controls were harmonious in pitch and roll, and full deflection gave a satisfying rate-not neck-snapping swift, but better than most production aircraft or aerobatic trainers. And it is hard to beat the view from the bubble in a 1 G barrel roll.
Wingovers gave me a chance to see just how well all three axes controlled with the speed changing down close to the stall-it felt natural, and the airplane was easy to point wherever I wanted-even at the slow end of the range. There was sufficient energy to roll at the top of the wingover and continue down the other side. A dive to 150 mph followed by a pull up to 60 and a half-roll with a half G pull over the top to the nose-low was a lovely float with the green of Florida spread out above my head. It’s hard to avoid the inevitable comparison to more familiar craft, so I’ll say that the Panther gave me aerobatic rates equal to those in my RV-8, with stick forces about those of an RV-4. Stick motions were larger to get the same rate than in the RVs, but then, they are faster, more powerful airplanes and the stick on the Panther was longer-requiring a little more movement to get to full deflection. All in all, this little sport plane will be more than adequate for the pilot who simple wants to turn upside down once in awhile without giving themselves a nose bleeding headache as they could with an Extra.
The canopy is attached with simple hinge pins and will self-jettison in flight if opened. Most pilots will probably fly without a parachute, but since it’s aerobatic, this gives an egress option if desired.
Air work done, it was time to head for the barn. I had scouted out the turf runway before departure, and determined that the soft spots were in the first couple of hundred feet after the threshold. Preferring not to make my first landing look like a carrier trap, I aimed a bit long with full flaps and holding about 75 mph over the fence. This gave a nice stable approach, but was probably about 5 mph fast-speed which was not easy to kill close to the runway. It didn’t so much float as it simply cruised along, decelerating slowly until the tendrils of the long grass grasped at the wheels. At this point, it was clear that we were going to stop…and how! Once again, I felt disappointed not to be able to check the brakes. The touchdown was a wheelie-a very comfortable one.
Taxiing back to the beginning of the soft turf, I decided I simply couldn’t quit without one more go, so I wheeled around, set the trim and poured on the coal-this time remembering the left rudder to keep her going straight. The takeoff was once again delayed due to the long grass, but I was expecting it, and had cranked on 10 degrees of flaps. Pattern altitude was easily achieved, and I set up for the second landing. This one came closer to a three point, but I started out high and had to kill off both speed and altitude. The touchdown was nice with no bad manners-a pleasant taildragger if I ever saw one.
Taxiing back to the Weseman’s hangar, I was sad that I didn’t have anything more on my test card. It would have been fun to stay in the air for a while, chasing clouds and looking for adversaries-but the airplane had already proven itself to be up to the task. It is an enjoyable craft, limited in horsepower, but not in spirit. Of the Light-Sport- eligible aircraft I have flown, this was probably the most pure fun-aerobatic capability is, after all, an indication of at least the ability to be free in all axes and to explore (and enjoy) the aerial experience to its fullest.
The prototype Panther is powered with a converted Corvair engine, which fits very nicely into the cowl and the aircraft’s performance envelope. Builders are free to choose their own powerplant.
The Plane
The first time I saw the Panther, it looked vaguely familiar. Single seat, low wing, cheek cowls bulging to cover the engine, and a large canopy for visibility. Oh yes, now I remember-it looks just like the sketches that I (and many other aspiring aeronautical engineers) covered their school notebooks with when we were students! It is, in fact, one of those iconic personal airplanes that those infected with the flying bug from an early age have always wanted. Wings, tail, engine, cockpit-what more do you need to slip the surly bonds? It looks much like those U-control or R/C models intended for sport aerobatics; all it lacks is the plastic pilot with the painted-on grin smiling from inside the canopy. Except that this one is full sized, and the cockpit is waiting for a real person.
The Panther is the first design of Dan Weseman, a long-time pilot and machinist who has developed parts for the popular Corvair engine conversion, owned a number of airplanes, and lives on a quirky airpark strip populated by some amazing aviation talent in Florida. Drawing on all of his resources, he has created a modern single-seater designed for fun-and the fact that it fits within LSA parameters is a definite plus. The fact that it can also accommodate more power and achieve faster speeds and climb is even better! The prototype is powered by a 100 hp Corvair engine that, if you took the cowl off without knowing what it was, you’d suspect to be a purpose-built aircraft engine. The all-metal, low-wing monoplane has a tip-over canopy and a large cockpit that will easily accommodate most pilots. Removable wings cap the design, making this airplane truly portable-and possibly affordable when you eliminate hangar expenses-for many. Sport Performance Aviation is committed to encouraging builders no matter what powerplant they choose, and while they might not be able to supply mass-produced parts for any engine under the sun, they will do their best to support a builder’s choice.
The Corvair conversion is mounted “backwards” compared to automotive use, with a fifth bearing, flywheel, and starter added to swing the prop.
The Panther is a new-generation kit featuring CAD-design parts that should fit together well for a reasonably quick build. Skins are all pre-punched to allow quick match-drilling to ribs, and since the design uses pulled rivets, structures can be finished in a snap. The fuselage consists of a steel-tube frame in the forward section that carries loads from engine to wing to cockpit, and a monocoque aft fuselage that supports the tail surfaces. The wings and tail are traditionally constructed of aluminum skin and ribs-nothing new and revolutionary here, which is fine for an airplane intended to be flown quickly. The wing’s aspect ratio is higher than many sport planes, providing good performance and a low stall to meet LSA requirements (and a short-winged “sport” version is available for those that might want a little higher roll rate at the expense of low-speed performance). The fastback design features a large tip-over canopy that affords the pilot excellent visibility everywhere but straight back-in my experience, better than most aircraft with raised turtledecks.
As mentioned, the roomy cockpit is designed for a wide variety of pilot sizes. The seat back is adjustable with pip pins before flight, and the rudder pedals can be moved for long- or short-legged pilots as required. The relatively long stick provides good throw for the controls, and the rudder throw reflects the same design ideas-fairly long throw to full deflection. The trim is a lever with a knob just outside the throttle quadrant and is easy to manipulate in the pattern, along with the power lever. The Corvair engine in the prototype operates just like a small Continental or Lycoming, with throttle, mixture, and carb heat controls falling right where your left hand wants to go. Carb heat, I was warned, is essential in the Corvair, so I resurrected my Cub instincts for the flight and pulled it on every time I throttled back. The placement in the cockpit made this easy.
Ribs and bulkheads are CNC cut, then hydro formed, so that the builder doesn’t have to create forms. Fluting is built-in to the hydro-formed blocks-this saves loads of building time.
The prototype’s instrument panel is simple: a master switch, an avionics switch (for the radio and EFIS), two switches for the ignition and fuel pumps, and a start button. The aircraft EFIS is a GRT Sport, and a small, 21/4-inch round radio provided communications. For a Day VFR airplane, there wasn’t much that was needed, except for the transponder.
Additional cockpit features include the highly visible wing attachment pins and safety clips. It is comforting for the pilot to be able to see that the wings have been attached properly before flight. The quick-disconnect bellcranks for the ailerons are also visible. A flap lever on the left side of the seat provides three locking positions: up, 10 degrees, and full down. The fuel selector is located comfortably in front of the pilot’s stick. The canopy latch is simple and reminiscent of other tip-overs on sport planes and gliders. When the lever is pulled back, it drives lock pins fore and aft-this is opposite of many airplanes where the “locked” position is forward, and Dan is considering changing this for standardization. There are, however, quite a few homebuilts flying with the same type of latch and the locked position aft, so what is “standard” is a matter for hangar debate. More importantly, Dan is considering a locking mechanism for the latch so that it can’t accidently be moved in flight. Canopy jettison capability is provided by using tear-away hinges on the right side-open the latch, pop the canopy a bit to catch the slipstream, and it will be gone in short order.
The first customer-built Panther is going together just down the runway from the Weseman’s and will sport an O-320 on the nose. So far, the builder reports that the structure goes together quickly.
Fuel is provided in two leading-edge wing tanks, plumbed to the fuel selector in front of the pilot, and then fed to the Corvair engine with two parallel fuel pumps. One pump is activated with each side of the dual ignition system. Both are used for takeoff, and it is then recommended to cruise on one or the other. Once the fuel line penetrates the firewall, the propulsion system is simple. Firewall forward, there is an engine mount, an engine, and a propeller-and little else.
The Corvair is a six-cylinder, horizontally-opposed, air-cooled engine that has been modified with a new crankshaft and an extra fifth main bearing at the propeller end. The engine is mounted “backwards” so that what was the transmission end in a car is now forward and supporting the prop. The extra bearing takes the loads of the propeller, turning this automotive powerplant into a fairly robust aircraft engine. The new “rear” of the engine mounts a small alternator (on the end of the driveshaft) and the traditional automotive distributor cap. An aircraft updraft carburetor hangs below the rear of the engine and feeds a custom-built intake manifold, which runs to the cylinder heads. The exhaust is likewise custom built and simple. There aren’t any more moving parts than necessary to make the airplane go.
Structural parts for the airframe will look familiar to anyone that has built a metal airplane; all ribs and bulkheads come stamped to shape using a hydro-press. The ribs are fluted in the pressing process, eliminating the somewhat tedious job of straightening them to get flat webs. Dan noted that the plans provide all of the necessary dimensions and templates for someone wanting to plans-build the airplane, but with the parts so nicely made at affordable prices, we suspect that most will skip this step. We looked at a wing being assembled by a beta-builder on the Weseman’s home field, and it looked to be going together quite easily. The skins being prepunched, all the builder needed to do was draw a centerline down each rib flange and scooch the rib around until the marks were visible through the line of holes in the skin, then drill and Cleco. This is not totally match-hole technology, and it still requires a wing jig for building, but it is pretty simple, just the same. Dan’s goal is to fully match-hole these components in the future, which will speed up production even more.
Rachel Weseman is an integral part of Sport Performance Aviation, here installing the cowling for another test flight.
Dan, an experienced machinist, is using a combination of in-house and outsourced manufacturing for parts and sub-assemblies for the kits. He has carefully selected those fabrication tasks that are best done by production facilities with advanced CAD/CAM capability to provide components that he can then perform final work on before sending them out in the kits. For example, Dan’s shop welds mounts for various engines out of tubing cut at another shop to exact dimensions. He simply needs to jig up the fish-mouthed tubes and do the critical welds. The Weseman’s have been providing Corvair crankshafts and fifth bearings under similar manufacturing concepts for some time, and the model works.
Traditional Revolution
Overall, the Panther can best be described as traditional-it is a traditional configuration, using traditional materials, constructed with traditional techniques. “Revolutionary” is a term often used to describe “better” but in aviation, a lot of things have already been figured out, and when they work, they should be reused. This is an airframe that should go together quickly and provide good, solid, dependable service when properly built.