It’s a common misconception that the only engine for Van’s RVs is a Lycoming—or a Lycoming clone. It’s true that’s the most common choice but not the only one. Van’s has, in fact, considered other engines—it flew the RV-10 behind a 210-hp Continental six-cylinder IO-360 but never offered the firewall-forward kit because builders indicated they wanted the most horsepower available. And then almost two decades ago, Van’s embraced the Rotax 912 for its then-new RV-12. In the intervening years, many LSA RVs have soldiered on with the dependable little powerplant—originally the carbureted 912 ULS and more recently the injected, computer-controlled 912 iS.
The engines have proven perfect for the job and many have wondered if that same technology couldn’t be used on larger (and faster) RVs. The problem was power. The 912-series engines topped out at 100 hp normally aspirated and just 115 hp with the turbocharged 914. Neither choice would give a two-place RV larger than the RV-12 the kind of performance Van’s builders expect. No one wants to build a doggy airplane, after all.
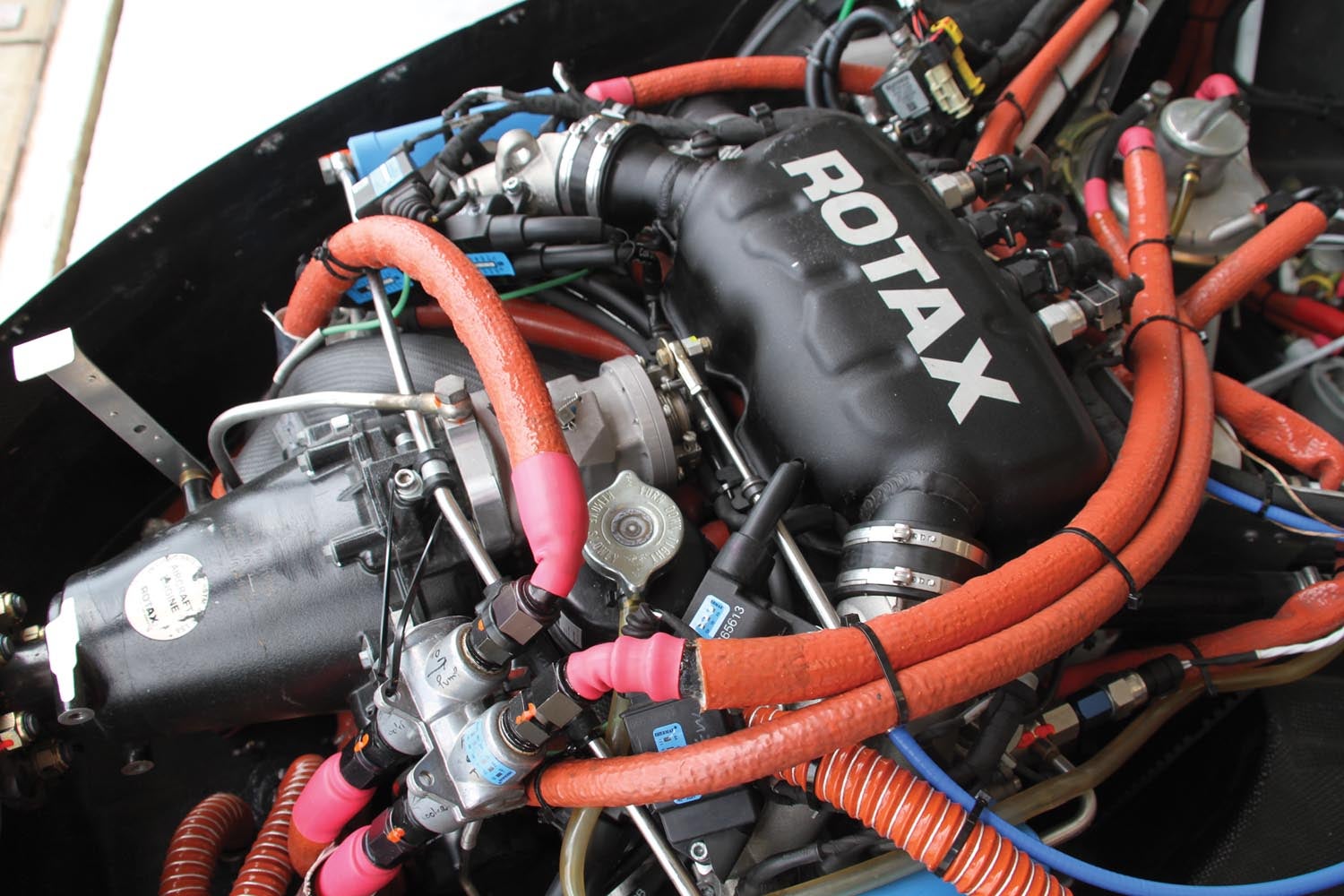
But in the intervening years since the RV-12’s debut, Rotax has been busy. The carbureted 914 was succeeded by the injected 915, which brought 141 peak horsepower (and 135 hp continuous), getting us much closer to the common 180-hp Lycoming engines found in the RV-6, RV-7 and RV-8. And even closer to the “ideal” engine for the big-wing RV-9, the Lycoming O-320. Then this year Rotax unleashed the 916 on the same platform, only with 160 hp for 5 minutes. That’s in the neighborhood with most Lycoming 320s. Now we’re talking.
Plus, of course, the Rotax is turbocharged, making it capable of producing max power up to 15,000 feet and maximum-continuous power (137 hp) to 23,000 feet. If the 916 leaves something on the table compared to the familiar 180-hp engines, it only does so briefly. By the time you’ve climbed through 3000 feet (or lined up for takeoff on a high-country strip), the blown Rotax is on par with or better than the non-turbo Lycoming. Even at the max-continuous power of 137 hp, the 916 pulls even with the much bigger Lycoming by around 7000 feet (density altitude) and pulls ahead as the airplane climbs and the Lyc starts to run out of breath. If your goal is power at altitude, such as for a long-distance cruiser, that Rotax—modern, electronically controlled and able to burn autogas—is mighty attractive if you’re trying to power a two-seat RV, especially one with a wing designed for high-altitude cruising, like the RV-9.
So what happens when you match an RV-9 with that engine? Up until now, it was mostly hand waving and paper design. But Phil Lockwood, owner of Lockwood Aviation, one of the largest Rotax service centers in the U.S., decided to take it a step further and make such an airplane a reality. After seeing the airplane under construction at Lockwood’s Sebring, Florida-based skunk works last spring and looking at it on static display at AirVenture, I finally got a chance to examine it up close and fly it late last year. I was not disappointed.
The Realities of an Engine Change
Throwing a different engine than the designer intended on an airframe is never as simple as it sounds. There are many things to think about, including system integration, weight and balance and stability and control considerations.
Systems integration is a matter of adapting the existing airframe systems to the new engine configuration. How the fuel system matches up is the first thing to think about. Then there are electrical things to consider—an electrically dependent engine (there are many of these in the Lycoming world too) requires bomb-proof electrical redundancy to keep the prop turning. These have to be carefully considered because you’re losing the experience gained with the rest of the fleet using the baseline, as originally designed configuration.
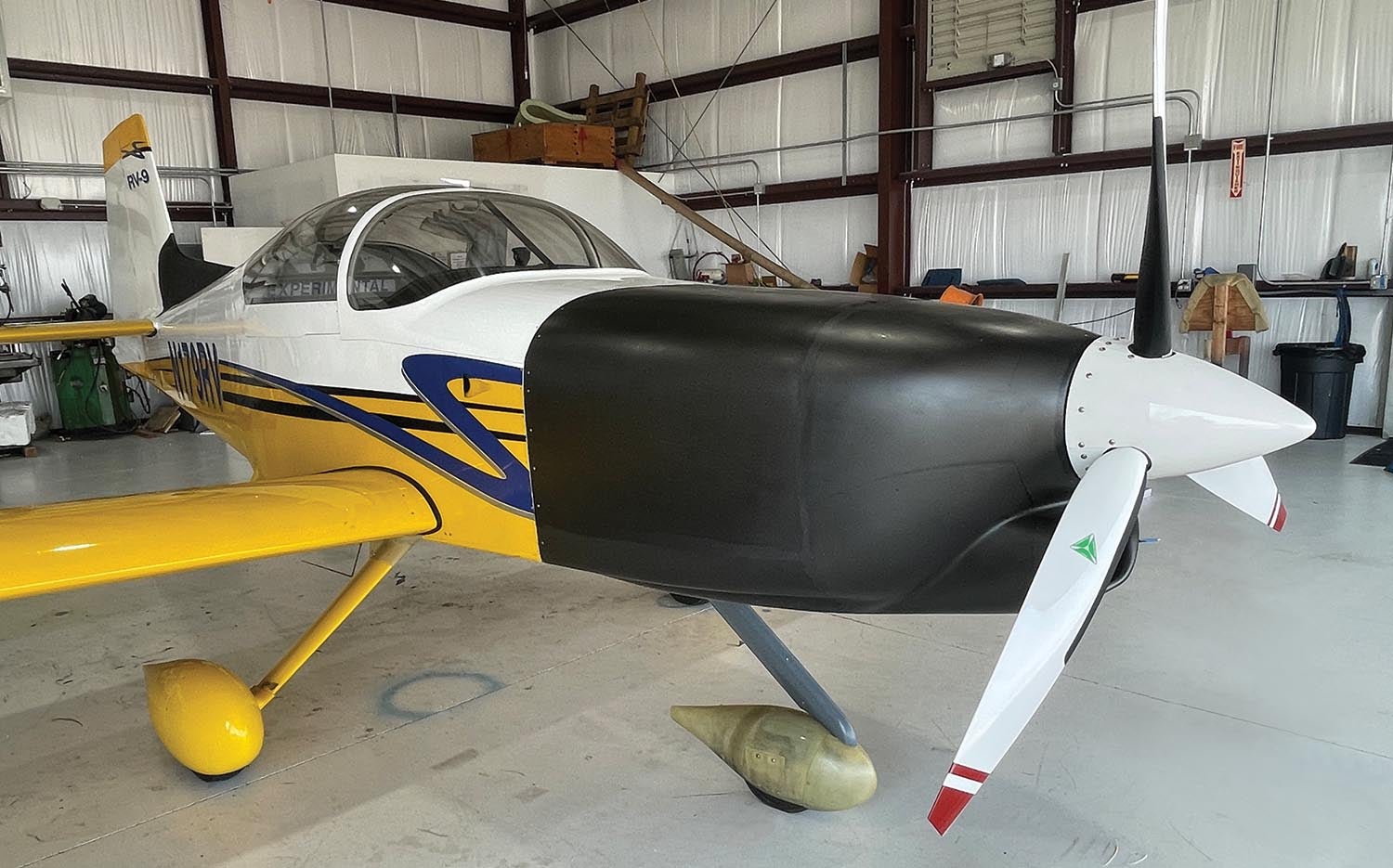
Obviously, there are thousands of Rotax-powered airplanes flying from which to draw inspiration—it pays for a builder (or designer) to borrow from those with a good track record. In the case of this RV-9, it is hard to beat Lockwood Aviation’s experience with a wide variety of Rotax-powered aircraft. While I was visiting their maintenance shop, I counted six different types of Rotax-powered machines, so they know what works and what doesn’t.
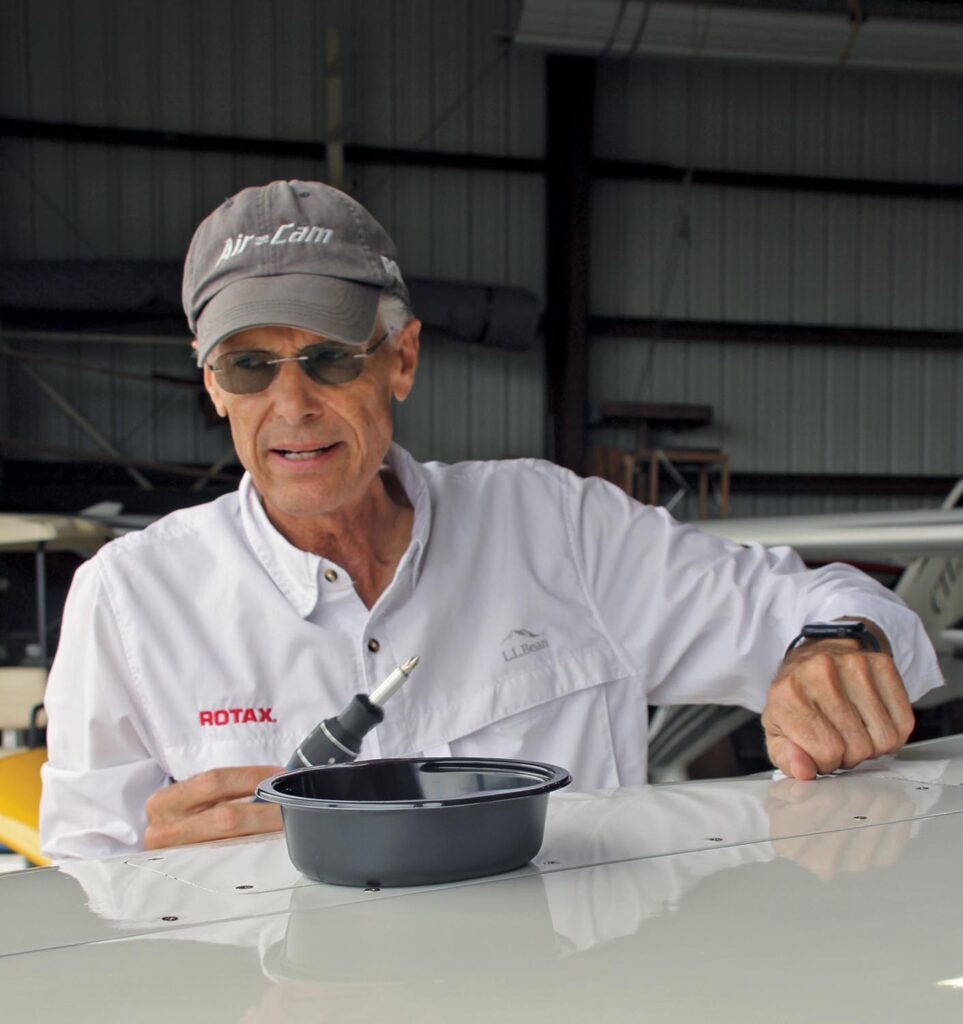
Once you have satisfied yourself that the systems can be made to work, you need to think about weight and balance. We all know that when it comes to aircraft, lighter is better and the Rotax four-banger is much lighter than a Lycoming. Start adding things like cooling systems and the gap becomes just a little narrower—but not a lot. So that means that you’re going to end up with a tail-heavy airplane if you just bolt the motor in the same place. That’s why most aircraft converted to a lighter powerplant have a longer nose. Ever looked at turboprop conversions of airplanes designed for pistons? They all share an exceptionally long nose.
Lengthening the nose is not simply a matter of building a new motor mount—you also have to modify cowlings and find places to hang radiators. Coming up with the proper inlets and outlets for cooling air (to feed the radiator as well as the oil cooler) is not always as simple as it seems. Proper engineering up front is your friend.
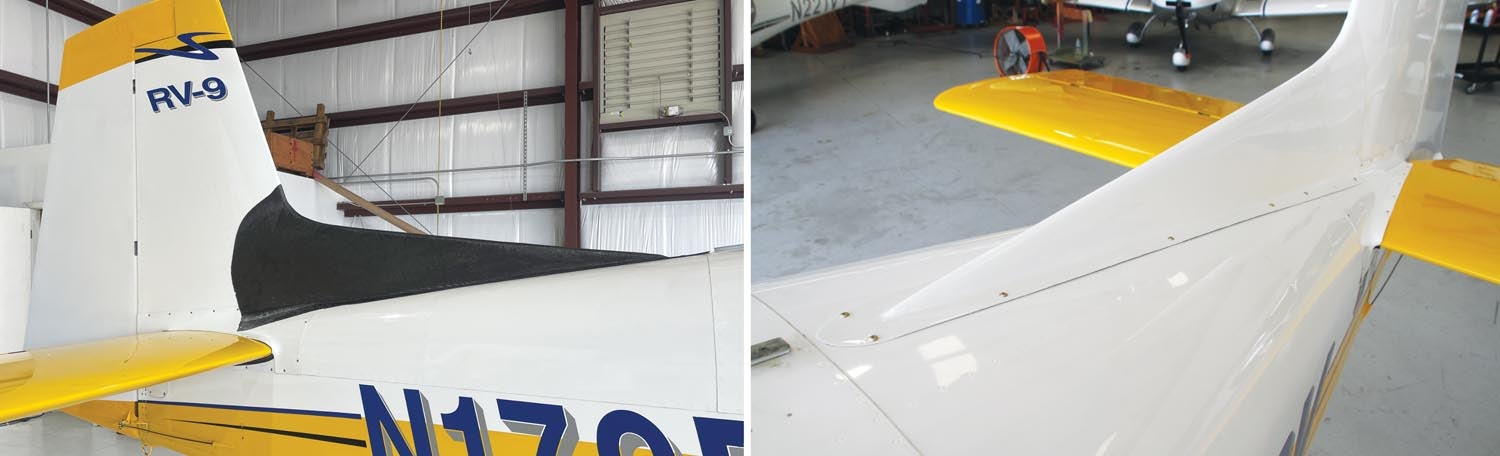
Finally, lengthening the nose adds “sail area” forward of the aircraft CG and this can degrade yaw stability. Most pilots and builders are unaware of their aircraft’s yaw stability and rudder power because airplanes are designed and tested to have it. Upset the balance and you can have an airplane that doesn’t want to stay straight or won’t return to straight-ahead flight after an upset. This is most easily figured out at the edges of the yaw envelope, such as in an extreme forward slip—an unstable airplane can decide to yaw farther when you have full rudder and opposite aileron to the stops—an unsettling feeling that can lead to spins.
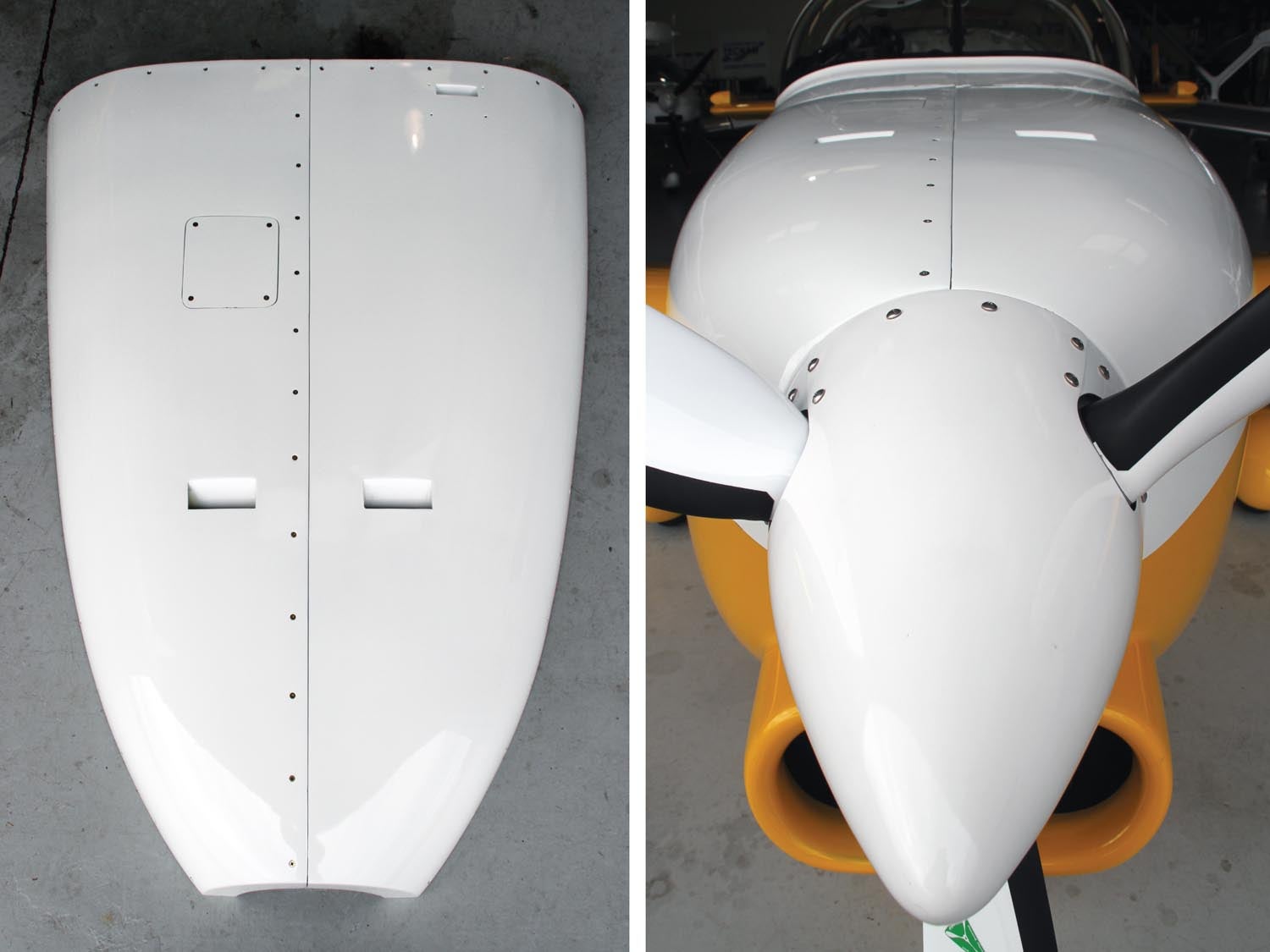
The Lockwood Project
Phil Lockwood has been using Rotax engines in designs for decades, making him a knowledge center on the type. Plus, Lockwood was part of the Aircraft Kit Industry Association (AKIA), so it wasn’t hard for him to collaborate with Van’s through chief engineer Rian Johnson. The result: A factory RV-9A appeared in Florida for modification. The airframe is still owned by Van’s but otherwise this is a Lockwood project.
When I visited Lockwood back in May 2023, the RV-9A had been flying for quite a while and was reaching its final configuration. I didn’t get to fly it because it was undergoing some modifications to improve on the baseline cowl and to add some yaw stability with a dorsal fin, but I learned a lot about the project that we can share. True to the norms of R&D, the airplane I saw was on its third engine mount—improvements along the way were to change engine position and mount components (such as radiators) in various positions and locations. They had also built several cowls, mostly to accommodate the different engine mounts, but also to provide incremental improvements in cooling airflow for the radiators. The cowling I saw was close to being modified once again, with tape lines indicating that they would drop the upper profile down maybe 6 inches at the front and add a bump to the top for the top of the spinner (similar to an RV-8 profile). The cowling then was larger than necessary, but it is the shape “the aero guy” specified. While there was intent to narrow it up a bit more, the cowling I flew was essentially what I saw in my spring visit—and it works quite well.
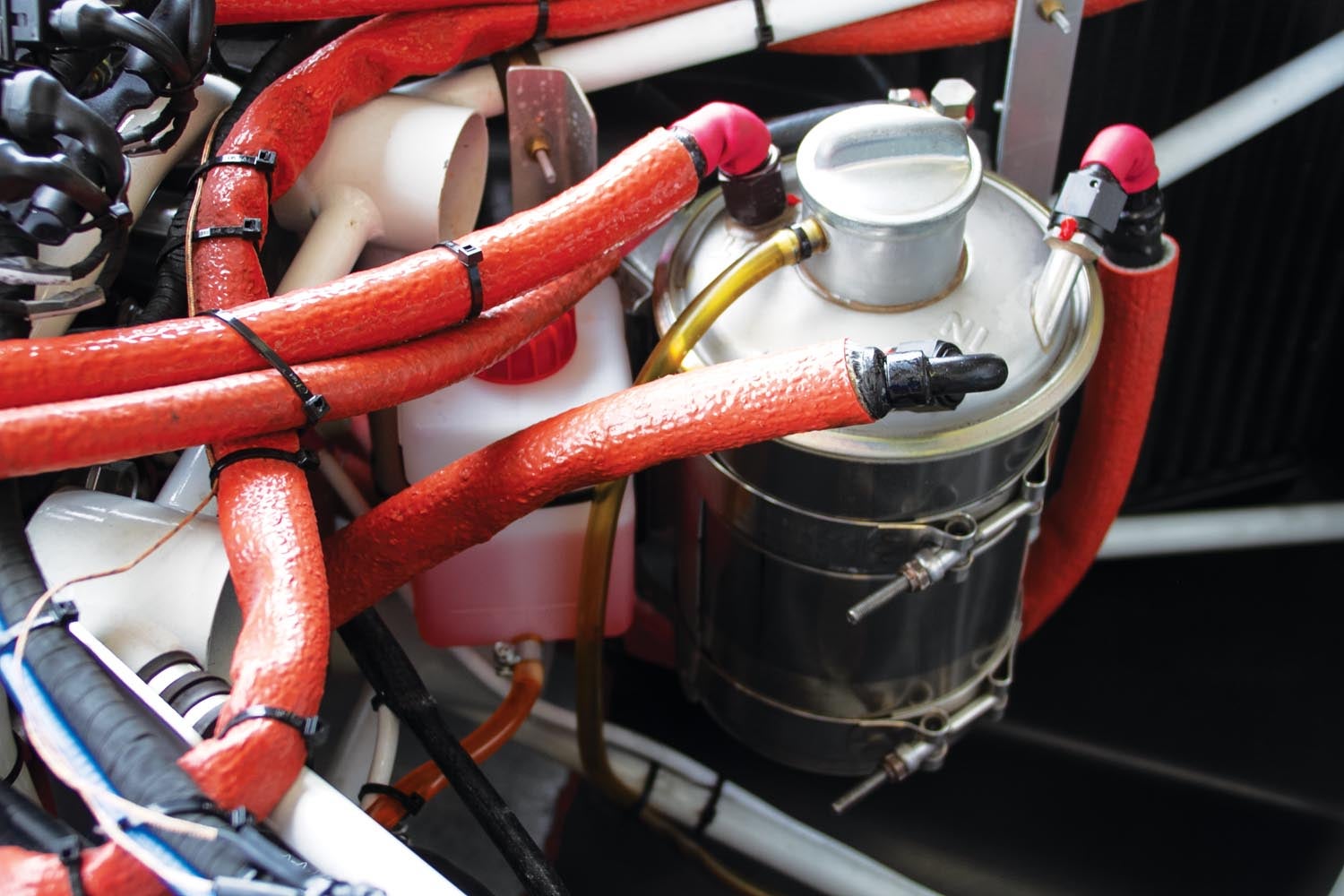
In May, the cooling was pretty well sorted out, with a single air intake underneath the prop to provide cooling air for the water and oil radiators, intercoolers and cylinders. This inlet also provides intake air. In my September visit, the engineers were looking toward a slightly different intercooler for the turbocharger—I saw no evidence that it was necessary, but engineers are always looking for “better.”
The engine is fairly far forward to make the CG come out right and this leads to the turboprop look. Lockwood mentioned that the CG of the -9A is fairly far aft with a Lycoming and since he was going to be able to define the CG position from the start, he didn’t want to be limited when it came to baggage, so he put the engine plenty forward. He added that there is probably room for a forward baggage compartment between the engine and avionics, but this isn’t currently in the plans.
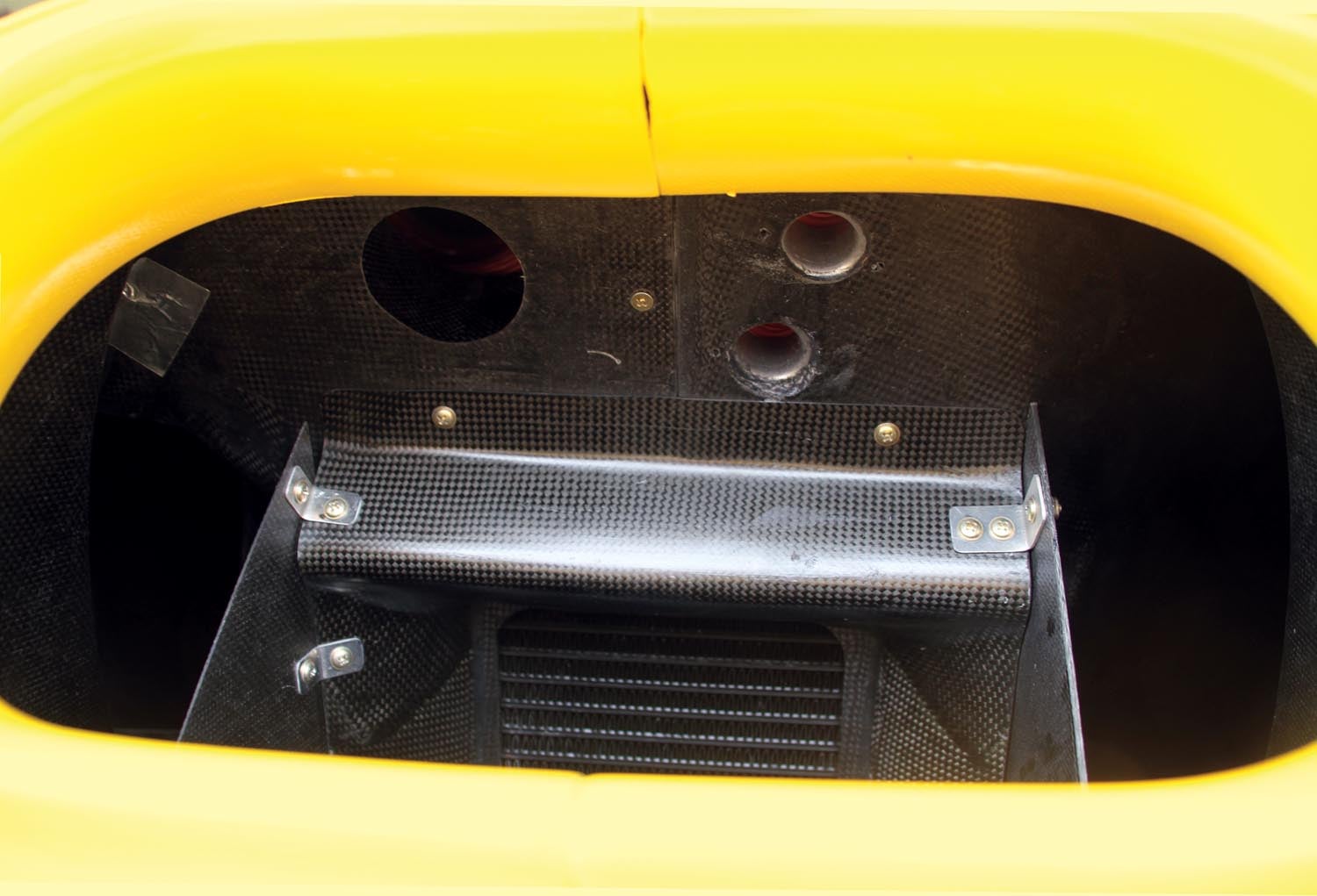
The propeller is an MT, hydraulically actuated constant-speed with three blades. While the engine has FADEC mixture control, this application still has manual prop and throttle, which Lockwood prefers. Having flown Rotax-powered aircraft with fully integrated, single-lever power controls, I think I agree with him because I am never quite certain what the prop is doing on those fully automated machines.
When Rian Johnson flew the Rotax-powered RV-9A in springtime, he found that with full rudder deflection, the yaw was divergent and he had to positively put in opposite rudder to bring the nose back in line. Lockwood has fixed this with a dorsal fin—they were on their second dorsal design when I was there since the first was bigger than needed. I watched them fit the second fin, beautifully made out of carbon fiber, and wished that I’d been able to stay a few more days to fly it.
A Taste of Performance
During that May visit, I talked performance numbers with Lockwood, as long as I understood they were preliminary. Because the Rotax 915 iS is turbocharged to give full horsepower almost to the flight levels, Lockwood was expecting 200 KTAS at 18,000 feet but hadn’t yet tested that high. He was very aware that max-allowable speed limits on the RV-9 airframe could limit performance potential. More on that issue later.
Lockwood said that the airplane with this engine is smoother than anything he has ever flown. My overall experience with the Rotaxes confirms that the combination of high engine speed and a well-balanced prop makes for an incredibly smooth power package. He also noted that the fuel burn is much less than the Lycoming but didn’t get it quantified. Again, my experience with Rotax-powered airplanes such as the Slings confirms that they are thrifty on fuel—and that they are happy with less-expensive automotive fuel.
Engineering Details
The airplane I flew in September was fully tested and very mature, but there are still a few items that Lockwood wants to tweak before coming up with a final kit for customers. Let’s take a look at a few things that set this engineered engine installation apart from someone simply guessing at what might work.
First, there is only one item behind the firewall that has been changed and that is the addition of a dorsal fin. Most airplanes have them; RVs generally do not. Many, many certified aircraft do. The idea behind a dorsal fin is to add yaw stability, though there is a compromise in yaw maneuverability.
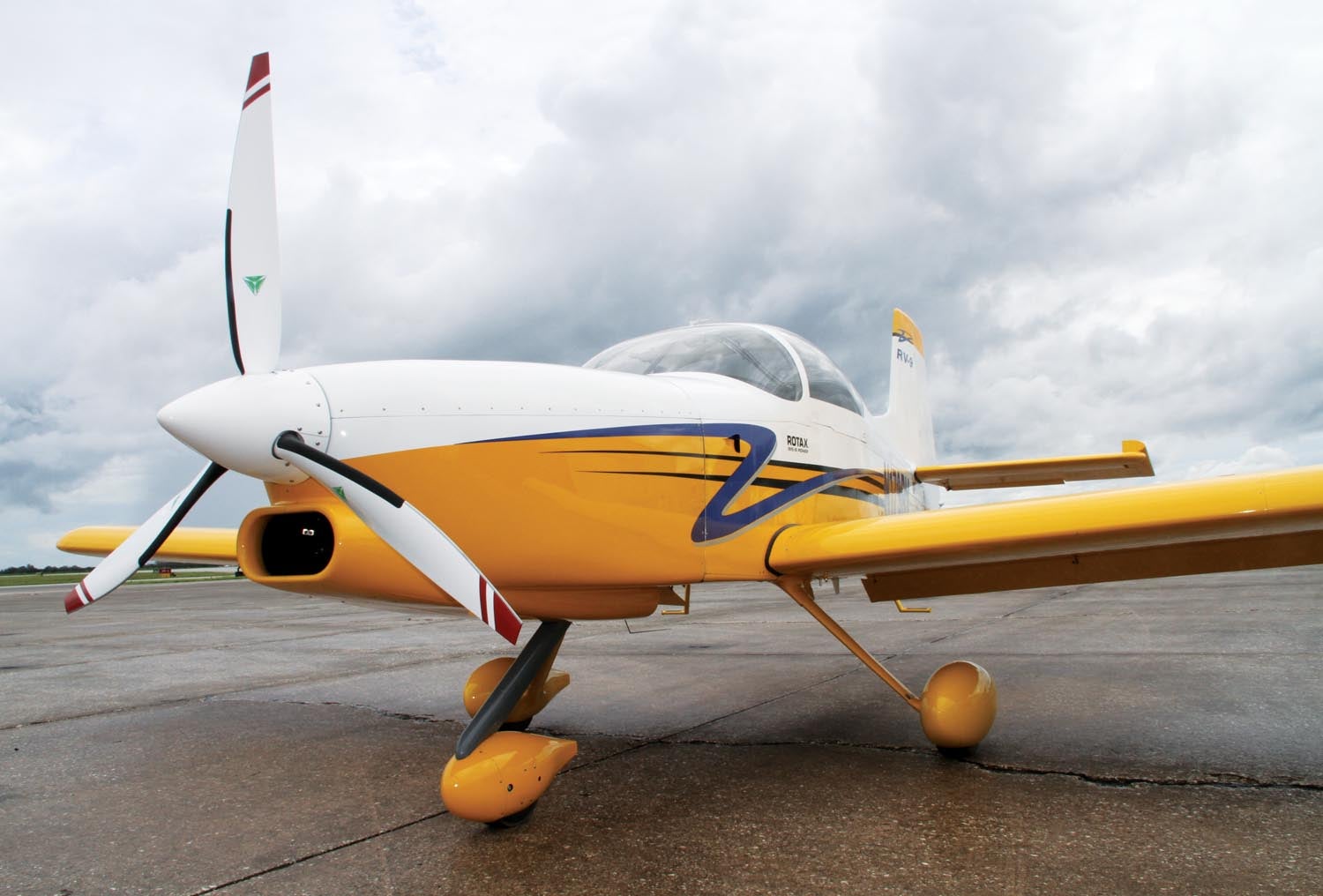
With the Lockwood project, the first fin was larger than needed—the one on the airplane now provides excellent stability without losing maneuverability. Lockwood noted that he wants to make another pass at the final design to make it attach with hidden fasteners. He also wants a better mold so that the finished parts come out perfect. But what’s there is close to perfect.
Now let’s go back up front. If you’re building a new RV-9A, just stop building when you get done with the firewall—everything in the kit will be replaced with parts from Lockwood. If you’re modifying an existing airplane, the same idea holds true with a notable exception. In June 2019, Van’s changed the RV-9A’s nose gear design to one similar to the RV-14’s, which has rubber isolators to absorb shocks. (The previous version was the more common steel strut.) But Lockwood’s engine mount is designed for the newer nose gear, making it incompatible for earlier RV-9As.
The engine mount is custom built in Lockwood’s welding shop and extends the engine well forward of the firewall. The truth is, any builder is going to look at all that empty space and think “baggage compartment” or maybe ‘“ballistic chute.” But Lockwood was determined to build an airplane much lighter than a Lycoming-powered ship and that meant not adding things. If you feel the additions are necessary, well—that’s up to you. The mount includes the attachments for the nosewheel, of course, as well as hard points for powerplant systems and components.
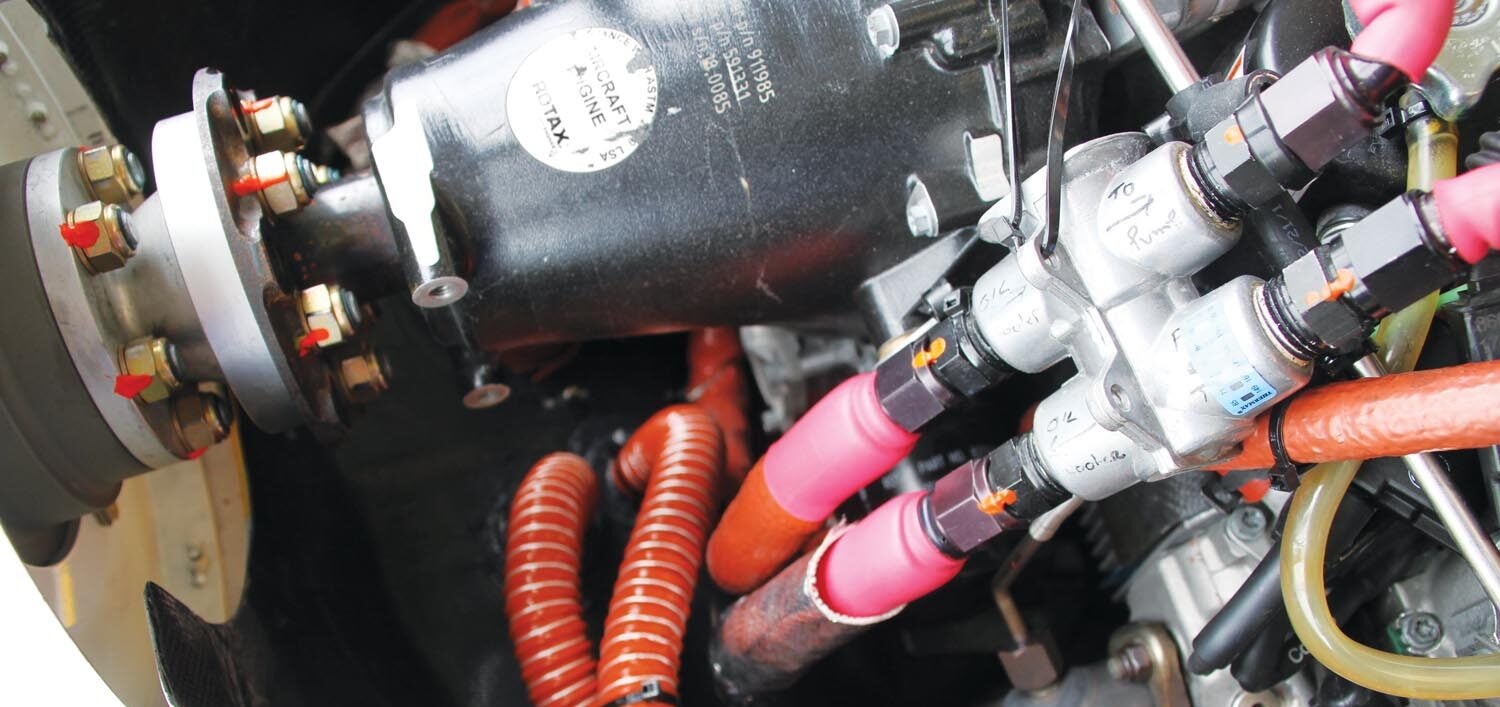
The Rotax 915 iS (or the 916 iS as both options should fit under the same cowl and to the same mounts) bolts on to the engine mount, of course, but many components (computer, ignition, etc.) will be mounted to the firewall or onto the engine mount itself. The installation features an oil cooler, water radiator, intercooler (for the turbocharger) and a hydraulic prop governor.
A few words about choosing the 915 or 916. As mentioned, the newer 916 has nearly 20 hp more for takeoff, but the maximum-continuous power is up only by 2 hp, from 135 to 137. It would be reasonable to expect the 916 to provide better runway performance and a stronger initial climb during the 5-minute limit for full power. Beyond that, the 915 and 916 are well matched. The newer 916 is, however, about $7000 more expensive.
Probably the largest part of Lockwood’s FWF kit is the cowling—and it is a beautiful (and complicated) piece of work. This is not just a shell to cover the engine. It includes ducting to move cooling air from the single inlet snout to where it needs to go to cool various components. If you look in the snout, you’ll see a large square heat exchanger in the middle—that is the oil cooler. On the starboard side of that cooler is a passage that carries air back to the intercooler and the engine-air inlet. On the port side, the duct feeds the water radiator. Above the oil cooler you’ll see a 2-inch SCAT tube adapter—this feeds air to the cylinder barrel cooling shrouds. (Like all 912-series engines, the Rotax 915 and 916 have liquid-cooled cylinder heads and air-cooled barrels.)
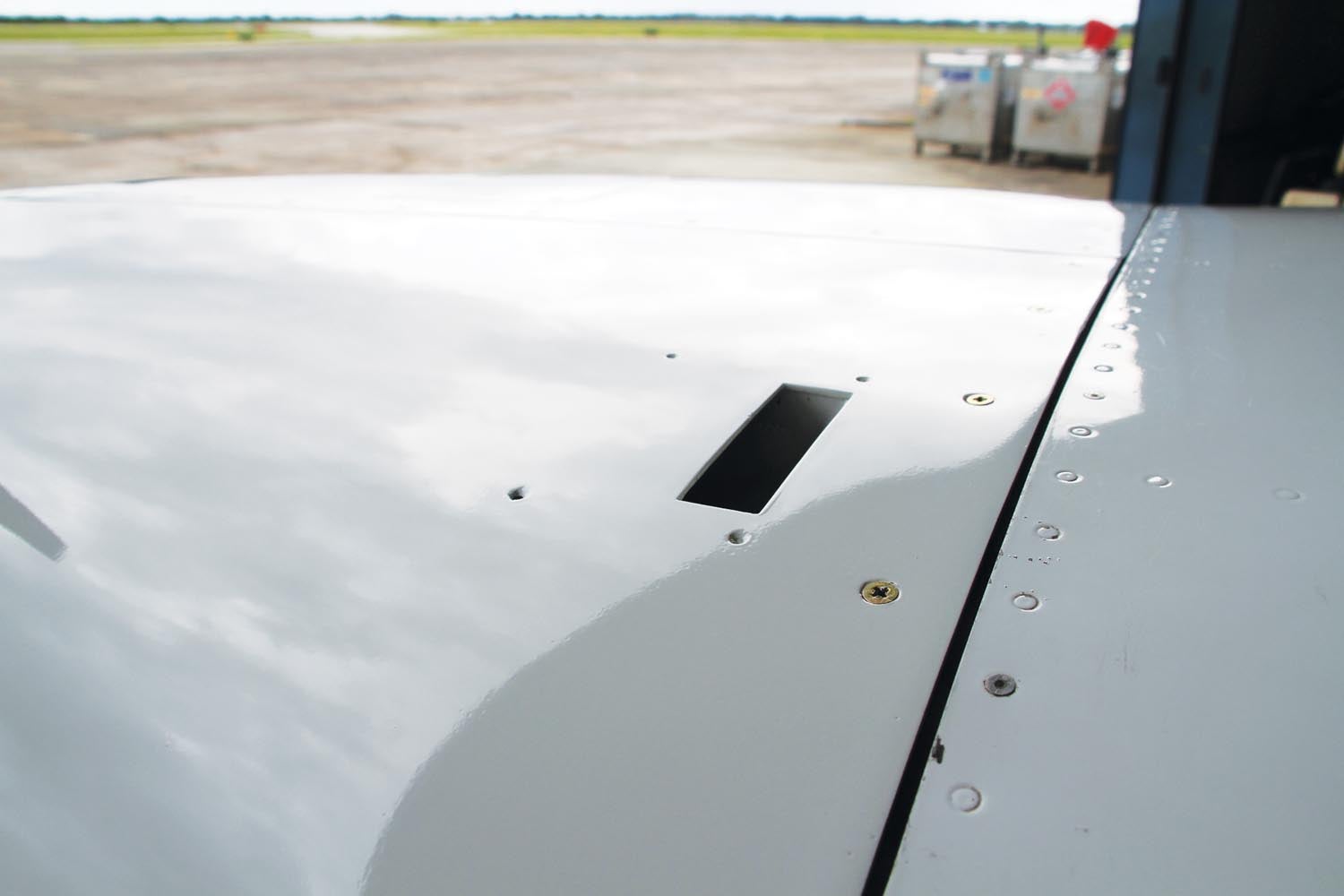
There are two smaller circular openings (also above the oil cooler) that feed air to the coil packs and voltage regulator. On top of the coil, you’ll see some small exit ports—these allow the coil pack and regulator air to escape. All the rest of the exhausted air goes out the bottom, along with the engine exhaust.
The cooling works exceptionally well. With a Lycoming in an RV, you’re often busy adjusting power, mixture and airspeed to cool the engine in climb. With the Rotax in the RV-9A, I just pushed the throttle in, set a nice climb power setting and forgot about things. I flew in late summer in Florida, yet the temperatures never got anywhere near any limits—the engine is well cooled and demands no attention from the pilot.
The cowling shape has evolved to the narrow, almost turbine-like profile that is now flying. This was mostly to reduce area exposed to the relative wind for both pitch and yaw—the initial cowling was more squared off. I found the change to be very effective and pitch stability was quite good. The same thing is true in yaw—the narrower cowl reduced sail area—but the dorsal fin was what got the airplane back to where it should be in yaw stability.
Overall, this is a very well thought-out and thoroughly engineered installation and the parts quality is superb. From the engine mount to the cowling, the parts built by Lockwood will stack up against anyone’s quality and if I were displaying this at Oshkosh, I’d take the top cowl off for the judges to look at. Even for a prototype, it is award-winning.
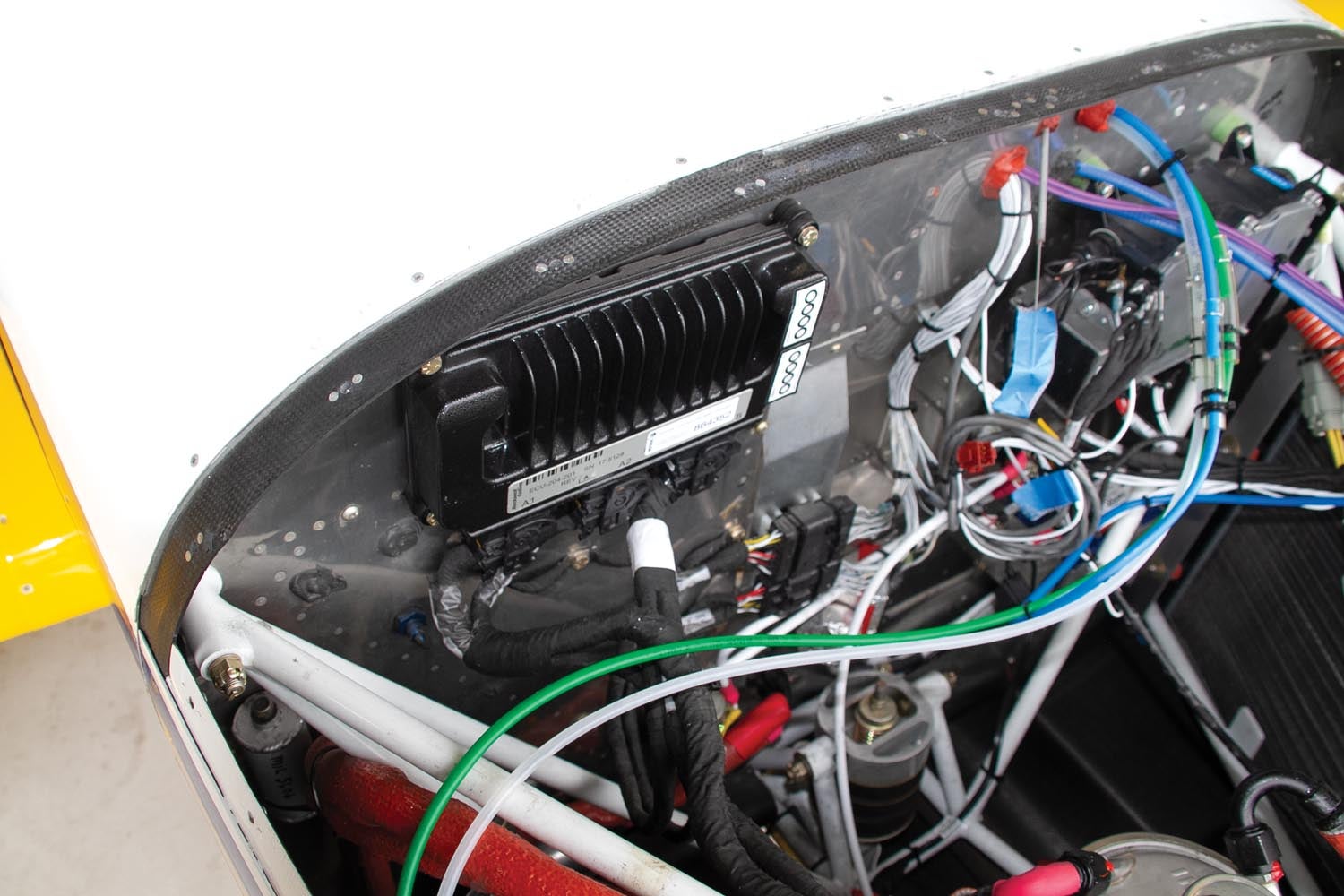
Our Turn to Fly!
I showed up at Lockwood’s hangar in Sebring in late September, planning on flying a photo mission first, then an evaluation flight after the time-limited photo pilot left for his day job. Florida being Florida, the weather was low and gray at 0800. Canceling the photo pilot, Lockwood and I talked about the project for a few hours until we noticed that the ceilings were up around 10,000 feet and there were breaks in the overcast! That meant it was time to launch.
I strapped into the familiar left seat of a Van’s two-seat side-by-side RV—so far, nothing unusual. The simple panel featured a single Dynon SkyView display but also a screen unfamiliar to me that turned out to be an engine monitor. It also had an engine/ignition panel betraying what was under the cowl—anytime you see switches for Lane A and Lane B, you pretty much know there is a Rotax under the hood.
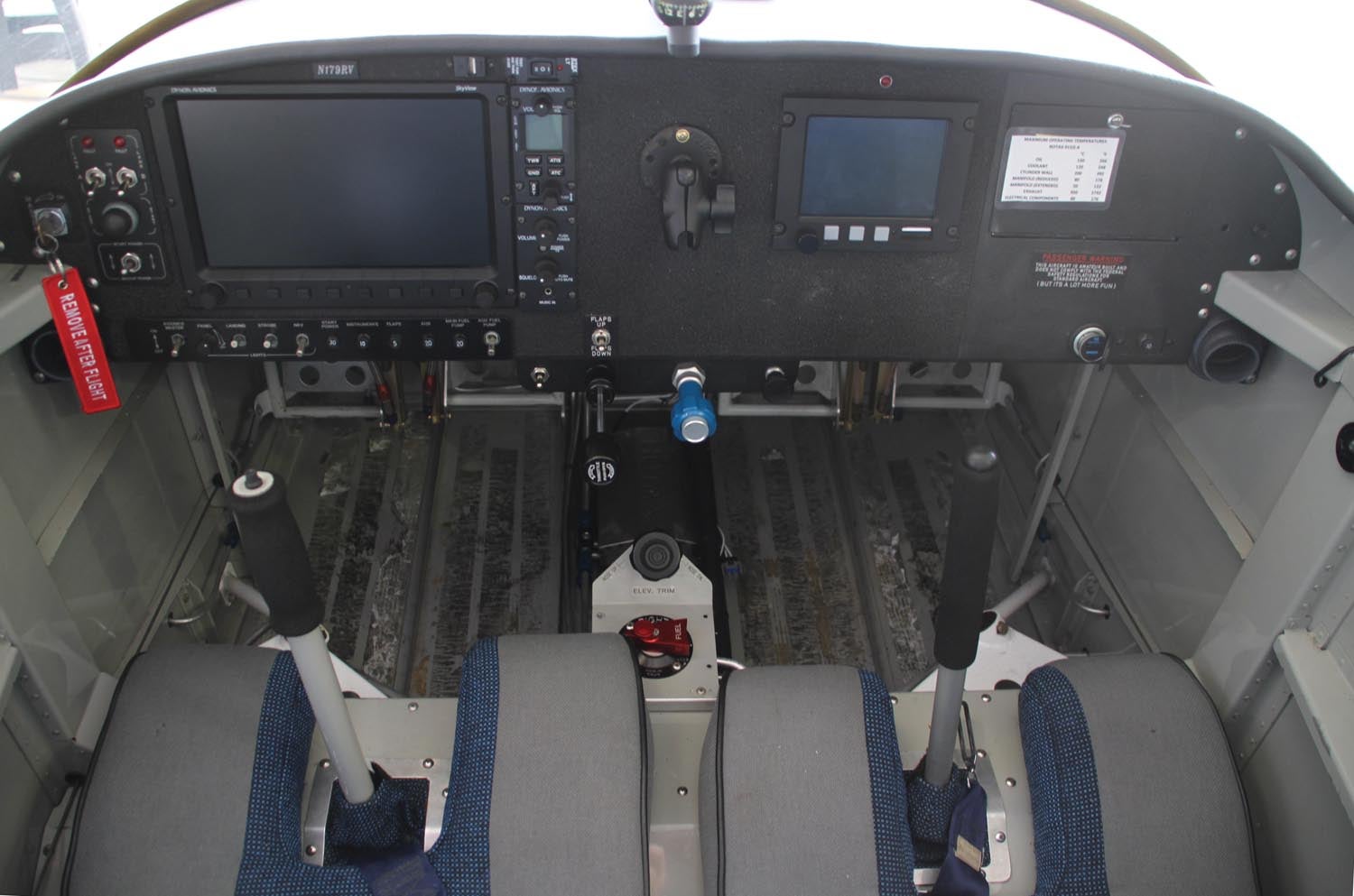
Looking at the weight-and-balance data before startup, it became apparent what a 100-pound-lighter empty weight can buy you. This airplane can be loaded with two 200-plus-pound people, full fuel (36 gallons) and 100 pounds of baggage—and still have more room in the weight-and-balance envelope. The CG was near the middle of the range with just the two of us in the seats and no luggage—and well under gross. This promised to be fun.
Engine start was typical Rotax—turn on the master, both ignition/injection lanes and a fuel pump and hit the start button—it fired right up. Advance the throttle to about 2700 rpm to bring the alternators online, then throttle back to idle for warmup. This being Florida in the late summer, warmup was not something we had to wait for—but warmth was also not an issue. I’ll just say up front that cooling was never an issue on the flight, even though I climbed steeply and continuously to 15,000 feet with no allowances required for oil or water temps.
I wondered if I’d notice the long nose while taxiing and the answer was: not really. In fact, the nose steered normally with differential braking and there was virtually no “head bobbing,” even when crossing expansion cracks. Run-up was also typical Rotax—make sure you’re up to temperature, check each lane, cycle the constant-speed prop and then do the airframe stuff—controls, fuel selector, canopy latch and lights.
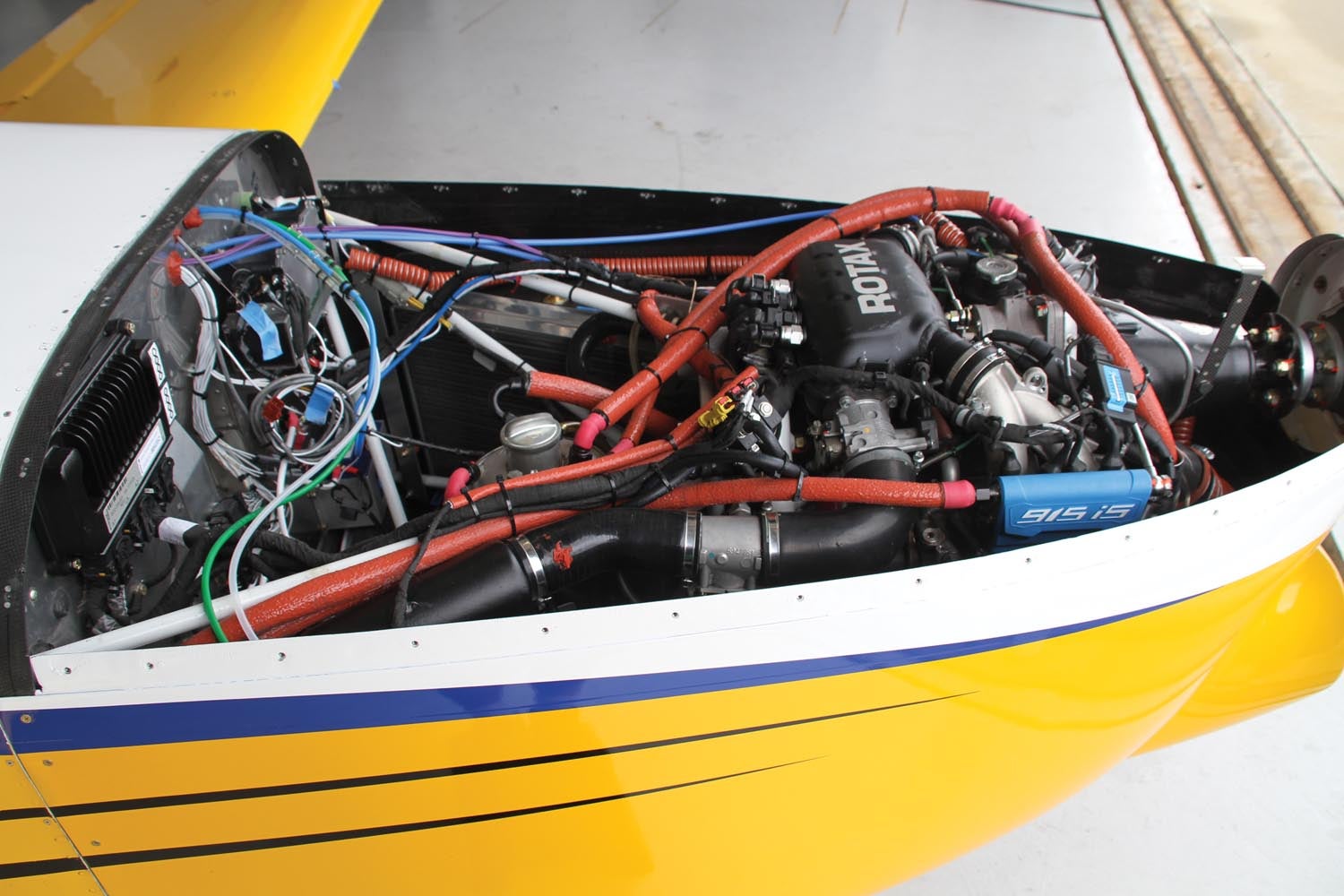
A quick call on CTAF that we were departing and I asked Phil if there were any engine limitations I should watch on takeoff or climb and he said, “Nope—just fly!” So a smooth application of power led to a comfortably quick acceleration, rotation and establishment of a normal climb. I noted 1300–1400 fpm, not spectacular for an RV at sea level but, hey, it’s 141 hp. At the 5-minute point, we were 5000 feet up (I relaxed back pressure a bit to see over the cowling) and we were still climbing at 1400 fpm. When we leveled off to get performance numbers at 12,500 feet, we were still climbing at 1400 fpm—now well above what I’d expect with a 160-hp Lycoming. Turbocharging is real!
Now a word on never-exceed speeds, or Vne. Lockwood is working with Van’s and the two are getting comfortable with a “split Vne” concept. Most RV pilots now know (because Van’s has published this many times) that Vne for most of their airplanes is actually determined as a true airspeed to prevent flutter. The RV-9’s Vne is typically set at 185 knots, but Van’s is close to approving a flutter-limited airspeed of 200 knots—but you also have to observe an indicated airspeed limit of 185 knots. (That is, Vne is 185 KIAS or 200 KTAS, whichever comes first.)
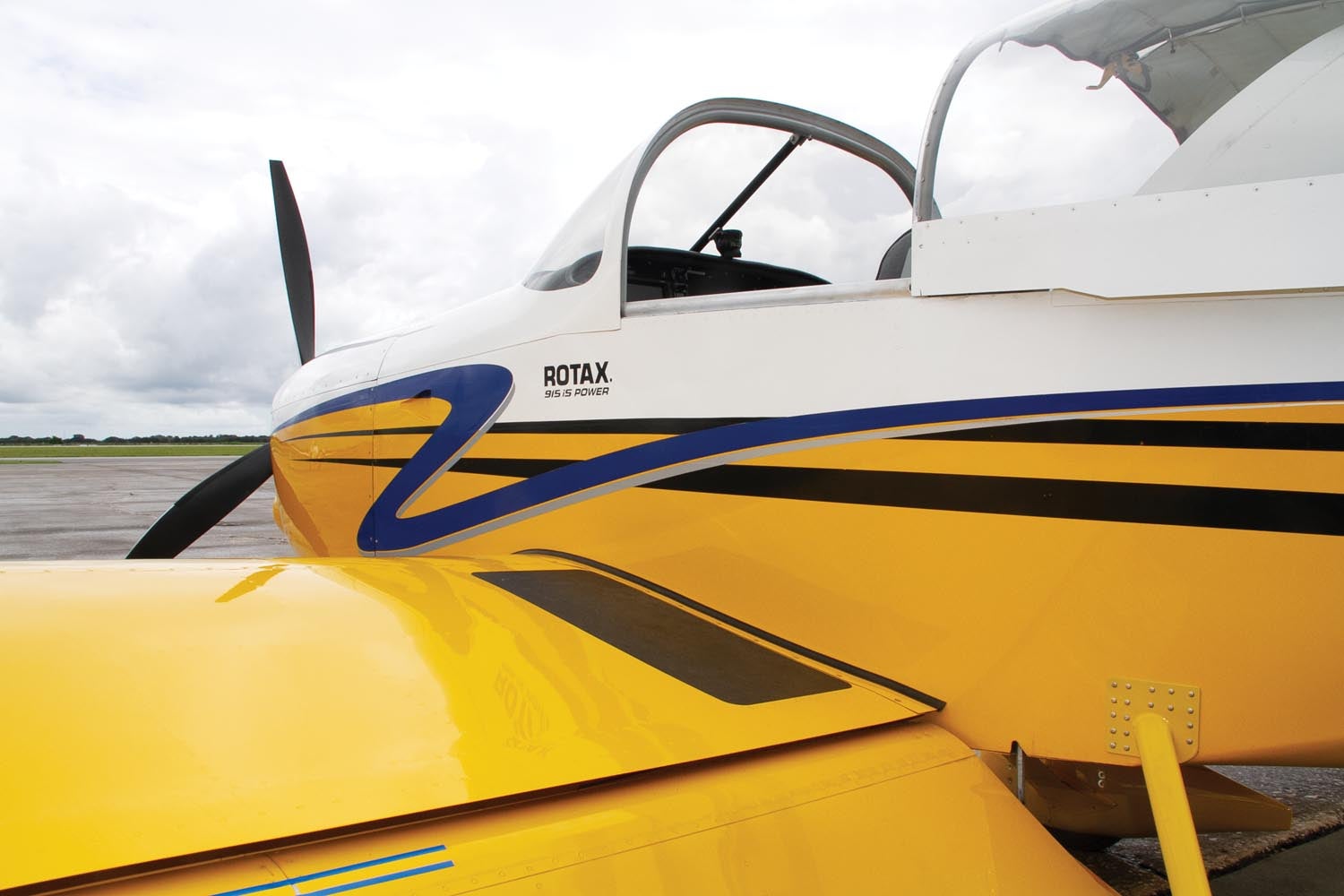
The only place where you are likely to see an IAS that high is close to the ground in a dive. So, practically speaking, it’s not a concern. But just like the faster RV brothers, the RV-9 with a Rotax now has to be flown carefully because it is very easy to drop the nose in the descent from a high-altitude cruise and end up right at the even higher 200-KTAS Vne. Incidentally, the limits are not yet officially approved, but they are moving in that direction.
So what were we seeing at cruise? Well, 12,500 feet above the Florida Alps (as Sebring is sometimes known because there are spots nearby almost 100 feet above sea level!), we were truing 173 knots burning 7.3 gallons of Swift 94 unleaded fuel per hour. That could have been premium unleaded or avgas—take your pick. Lockwood said, “Let’s see what it will do at 15,000,” so up we went. With the throttle full in, we saw 189 KTAS with a fuel flow of 10.6 gph. Now 10.6 might sound high for a Rotax—and that’s with it running very high power, and not in the Eco mode—but my RV-8 with an O-360 will not get into the 180s at that altitude and it would be burning more than 9 gph to reach the mid-170s. To have the RV-9A cruising in the 180s is more than remarkable—it’s pushing Rocket speeds.
About the Handling
Changing an engine is not just about speed, power and fuel burn. How does it handle and are there any corners of the envelope you need to avoid? We started down carefully, watching the airspeed to make sure we kept things under control. I tend to descend in smooth air close to the TAS redline in my RVs and only throttle back to keep the power below 75% when I get lower, since I am always running with the mixture lean of peak. The Rotax is doing that too—but the computer is managing it, so all the pilot has to do is keep the airspeed out of the red and throttle back to control the rate of descent. Honestly, this was very jet-like in the smooth air.
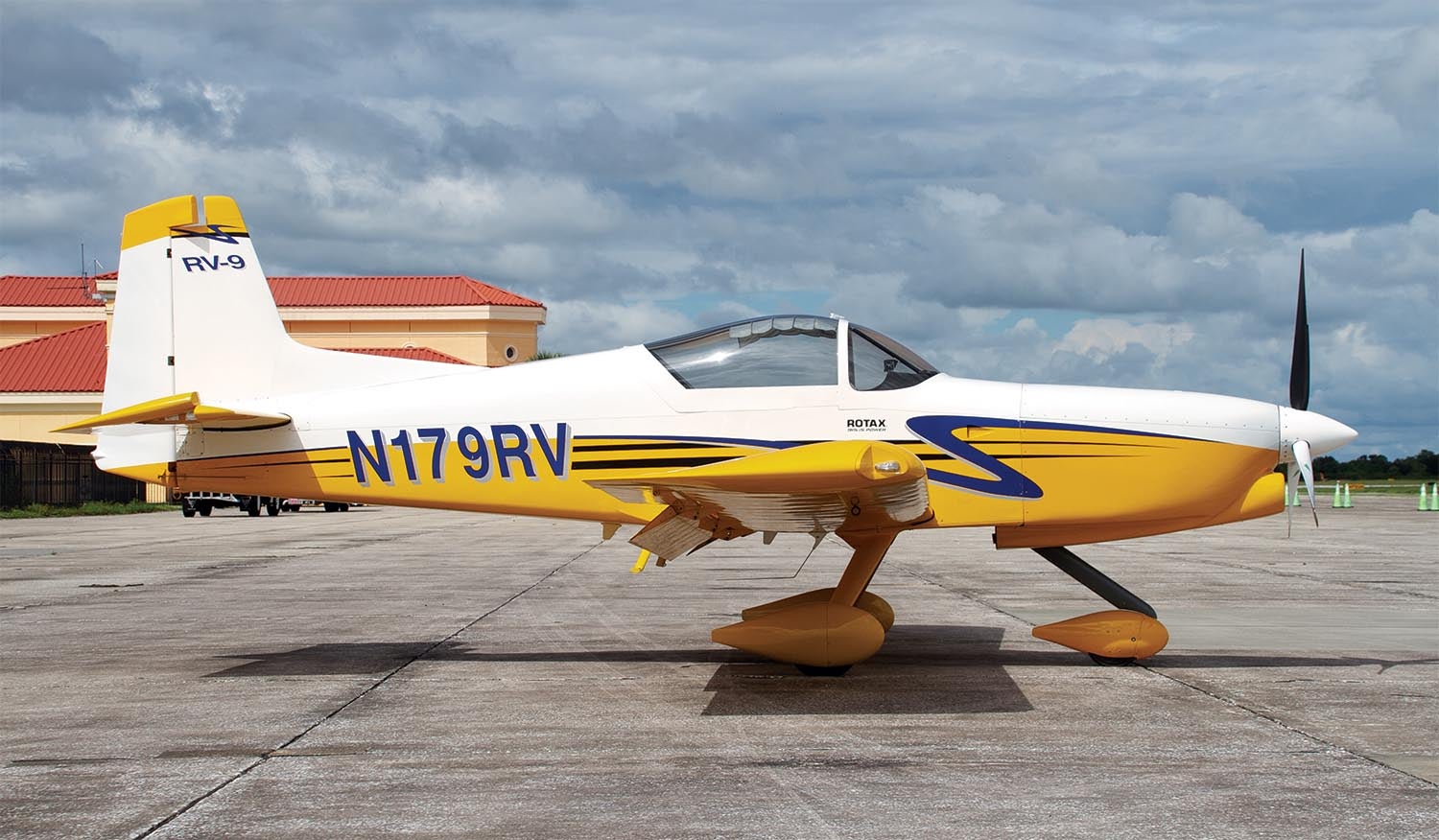
To sample the other end of the airplane’s spectrum, we leveled off at about 5000 feet to do a little slow flight and some stall work. Famed test pilot Len Fox had recently finished the official envelope expansion work, which included both stability runs and spin testing. In fact, he did more than 70 spins—not turns in spins, more than 70 actual multiple-turn spins (with a spin chute attached, but never deployed) to prove the aircraft. This gave me the confidence to slow it way down and let it nibble at the stall. It was…uneventful! RVs stall very nicely and this one was no different—plenty of aerodynamic warning and a clean but not extreme break. I stalled turning left and turning right and neither got my heart rate going. Recovery is simple—release back pressure and the wing is once again flying.
But how about stability? Well, at 75 knots, I eased into a full-rudder slip and felt out the controls—everything was positive. Letting off slightly on the pedal sent the nose back to center. I released the rudder all at once and the nose snapped back to straight-ahead flight—very stable. Lockwood had noted that with their first cowl iteration, they had left it very wide up front (typical Van’s shape) and pitch exhibited neutral stability. After narrowing it up considerably and reducing the “pitch area” forward of the CG, the airplane now is nicely damped with a short-period phugoid and a quick return to trim speed. All of that is engineer-speak for “it flies really nice and is stable!”
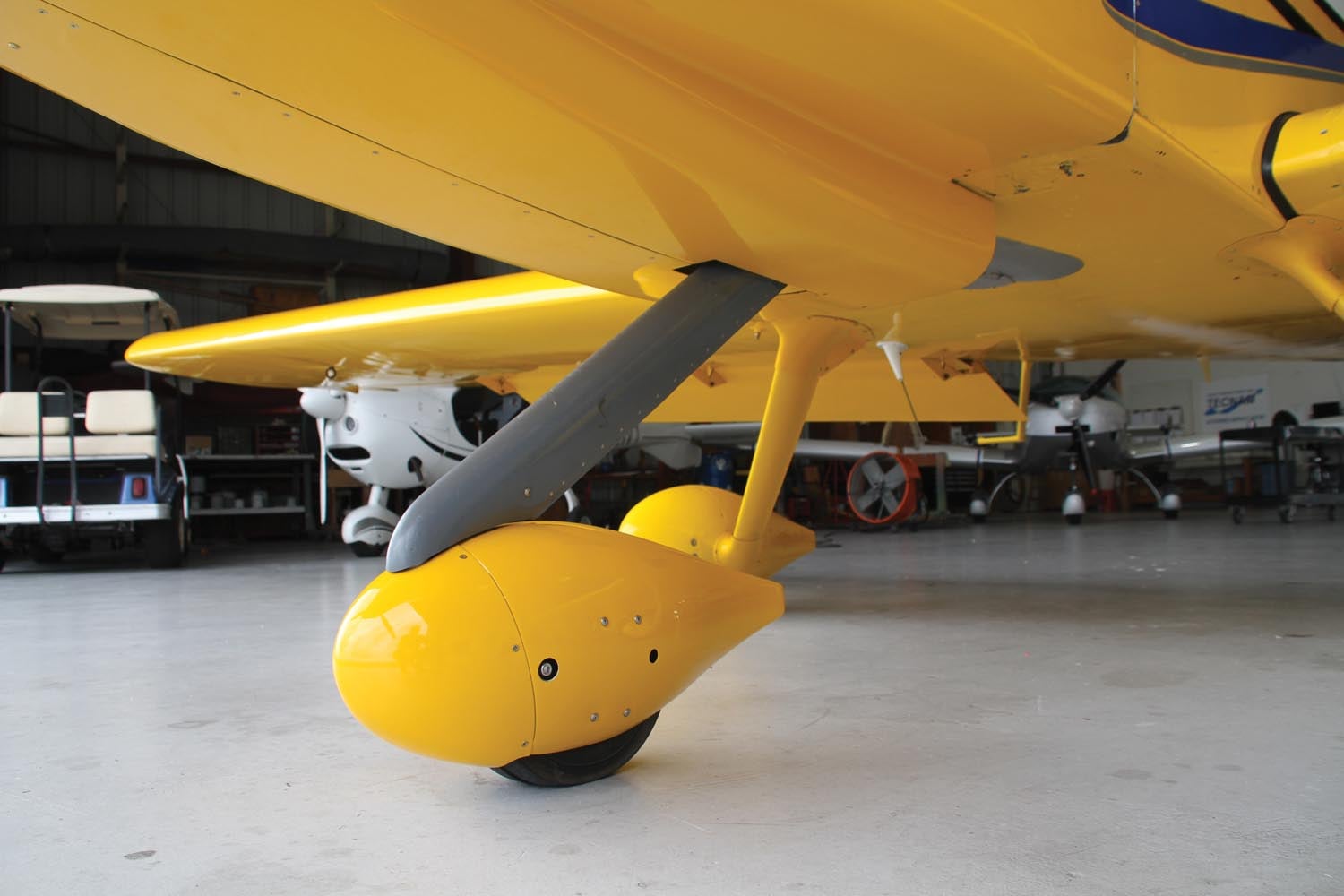
One note of caution if you’re doing extreme slips. The 915 (like the 912 iS and 916 iS) has a duplex fuel system, where it draws much more fuel from the chosen tank than it uses, with excess returned to that tank. Lockwood mentioned that with the fairly high continuous fuel flow rate out of the tank, the engine can skip a beat if you slip steeply toward the tank you’re using—the fuel is pulled away from the root-mounted intakes, starving the engine. I didn’t have a problem with this, but had made sure that when I slipped, I was using the “high” tank. So think about that if you’re doing extreme slips. I find that with the highly effective flaps on the RVs (especially on the -9), slipping is almost never required in a typical landing, so that is not really a significant issue.
The last thing we did was head back to Sebring for a landing, which was normal. Even though I don’t fly nosewheel-equipped RVs often, I somehow managed a good touchdown—honestly, these things sort of land themselves—and I was very happy with the entire flight.
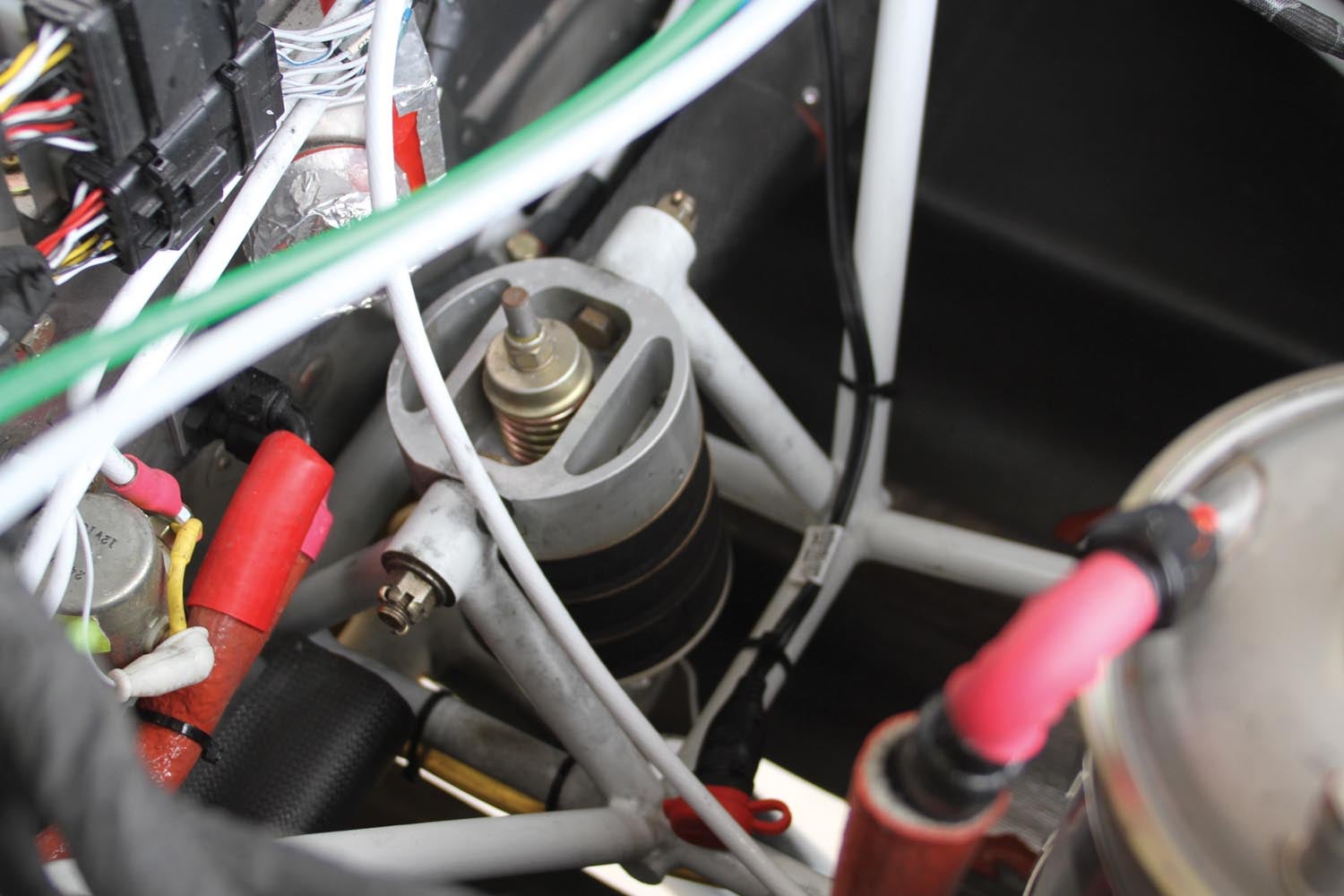
Lockwood’s Plans
So where does it go from here? Lockwood is pleased with how this experiment has turned out and is moving forward with plans to provide complete kits. He still has some refinements to do and will not sacrifice quality on things such as carbon fiber part molds, so he expects to be able to deliver kits by AirVenture 2024. He is hoping to bring the package to market somewhere in the range of $80K, which certainly is not cheap. But if you add up all of the components you need for a Lycoming installation—engine, prop and firewall-forward kits from Van’s—you get into the low $60K range. Looked at from that perspective, you can decide if the added performance at altitude (along with other benefits) is worth the extra coin.
We don’t expect Van’s to produce this package—it is Lockwood’s engineering and his “invention” to market. When asked about it, Van’s responded that they will be happy to sell a customer an RV-9A kit, just don’t order the FWF portion. (This means Van’s recent decision to stop allowing for kit deletions wouldn’t adversely impact this project.) The RV-9 has always been marketed to a slightly different builder/pilot than the aerobatic RVs. It is meant as a cruiser, albeit one that still handles well. Now with the Rotax, it is an exceptional cruiser, especially at altitude.
When the new MOSAIC proposal is turned into rules, the RV-9A starts to look even better. It’s one of two models that meet MOSAIC’s proposed clean stall limit of 54 KCAS—though it’s entirely possible the final MOSAIC rule will have different, more liberal restrictions in this realm. Even with the current rules, the Rotax-powered RV-9A would be a new-era LSA with amazing performance and a strong track record. Plus, unlike many current LSAs, the Rotax/Lockwood RV-9A will carry full fuel, two full-sized Americans and their luggage. I will not be surprised if we see a fair number of long-nosed RV-9As in the future.
See Larry Anglisano’s interview with Phil Lockwood.
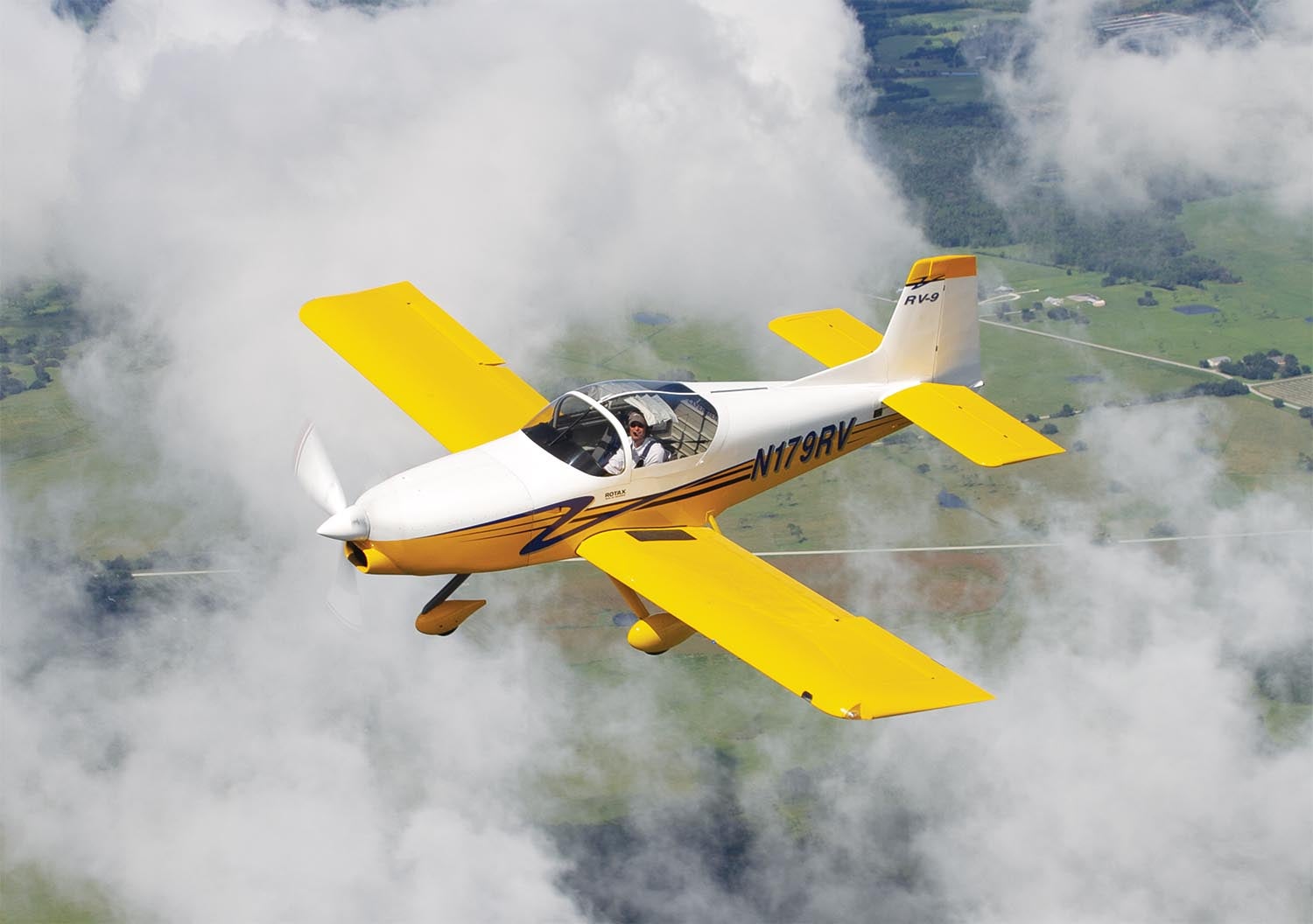
Now the that the Rotax 915/916 has krept into Lycoming O-320 (and it’s various clones) territory, expect a lot of this substitution in the near future.
MOSAIC is only going to accelerate the trend as will the impending demise of 100 low lead AVGAS.
Rans, for example, are offering the 915iS as an alternative to the Titan O-340 (although the allowable baggage capacity is reduced in thecase of an S-21 with a Rotax 915).
My only issue is that a Rotax 915/916 for O-320 engine swap tends to yield a disproportionately long nose to accommodate the W & B issues mentioned in this article.
A 915iS works on a Kitfox because the Series Seven Kitfox was designed around the 912. Put a 915/916 on an RV-9 and it looks like Pinocchio has been “economical with the truth.”. I’m sure you don’t notice the difference from inside the aircraft, but you will when you pull it out of that hangar to take a friend for a $100 hamburger.
We might have to wait for a new generation of designs developed to specifically to accommodate the Rotax 915/916 under the MOSAIC rulebook to realise these engines’ full potential in terms of performance and aesthetics.
In the meantime, expect a lot of current 912 compatible aircraft manufacturers to upgrade/revise their MTOW and offer the Rotax 915/916 as an upgrade option.