We’re still marking time on the fuselage of the F1 Rocket while waiting for winter to give way to spring and temperatures to reliably stay warm enough to work on the canopy. After a week or two of engine work—replacing all of the rubber seals on the Lycoming that has been pickled for 25 years—I opened up the box of fiberglass parts and pulled out all of the tail feather tips. That’s seven pieces of glass that came out of the molds over twenty years ago: two for the elevators, two for the horizontal stab, one for the vertical stab, and two (top and bottom) for the rudder.
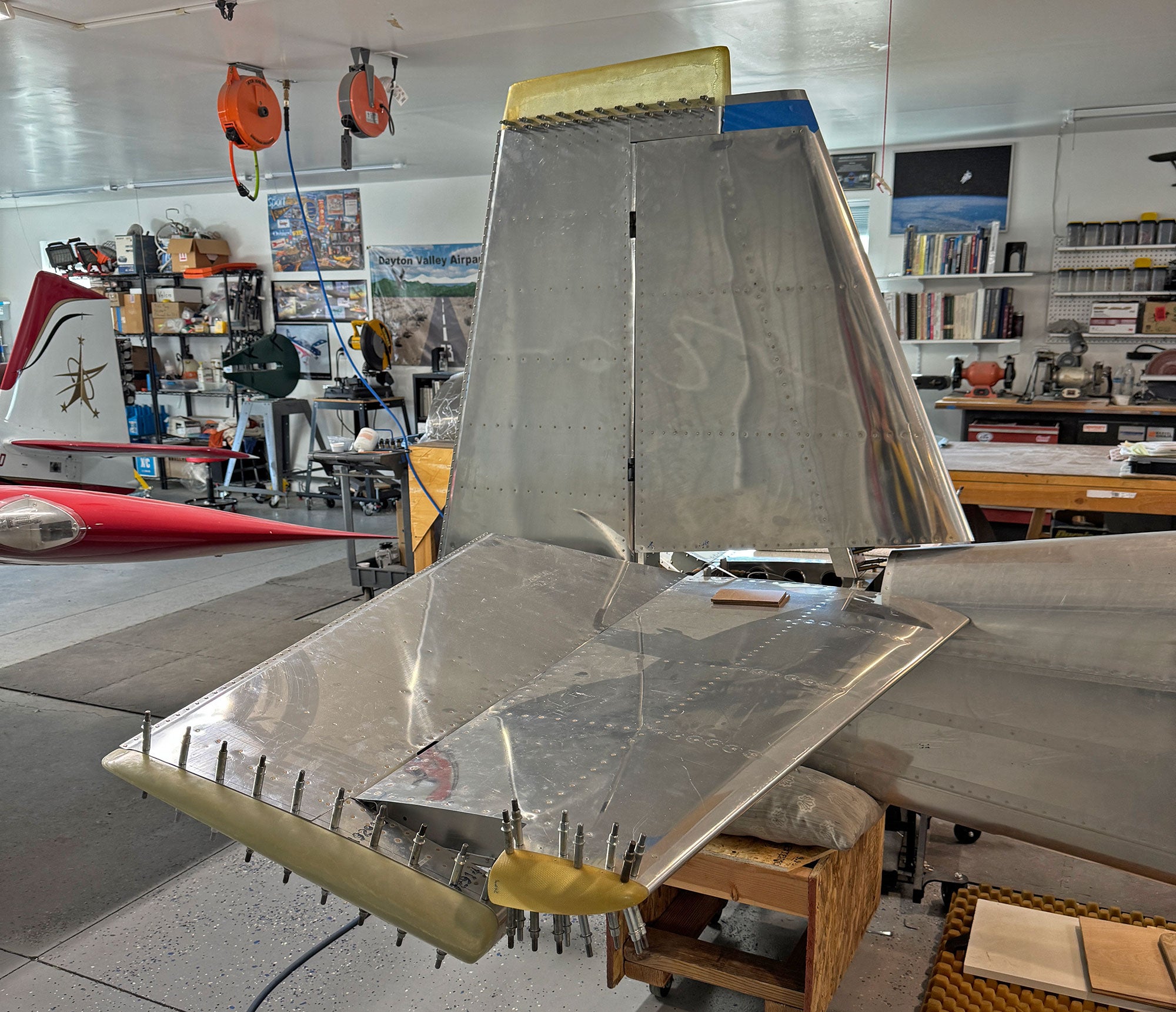
While the elevator tips were molded with flanges that slip inside the aluminum elevators, the rest of the parts simply have butt joints—you either have to build flanges or install them inside the aluminum and then build the outside up to match the mold line with epoxy and flox. The thing is—the parts fit so nicely when butted up against the structure that it would be a shame not to build aluminum flanges!
So out came strips of aluminum and the rivet fan (lots of evenly spaced holes are easier to drill quickly with the rivet fan than by measuring and drilling). The fitting was actually surprisingly easy—the only tricky one being the rudder bottom, because you have to make sure that it isn’t too deep. You have to make sure it clears the tailwheel spring, and that made me glad I had already installed it!
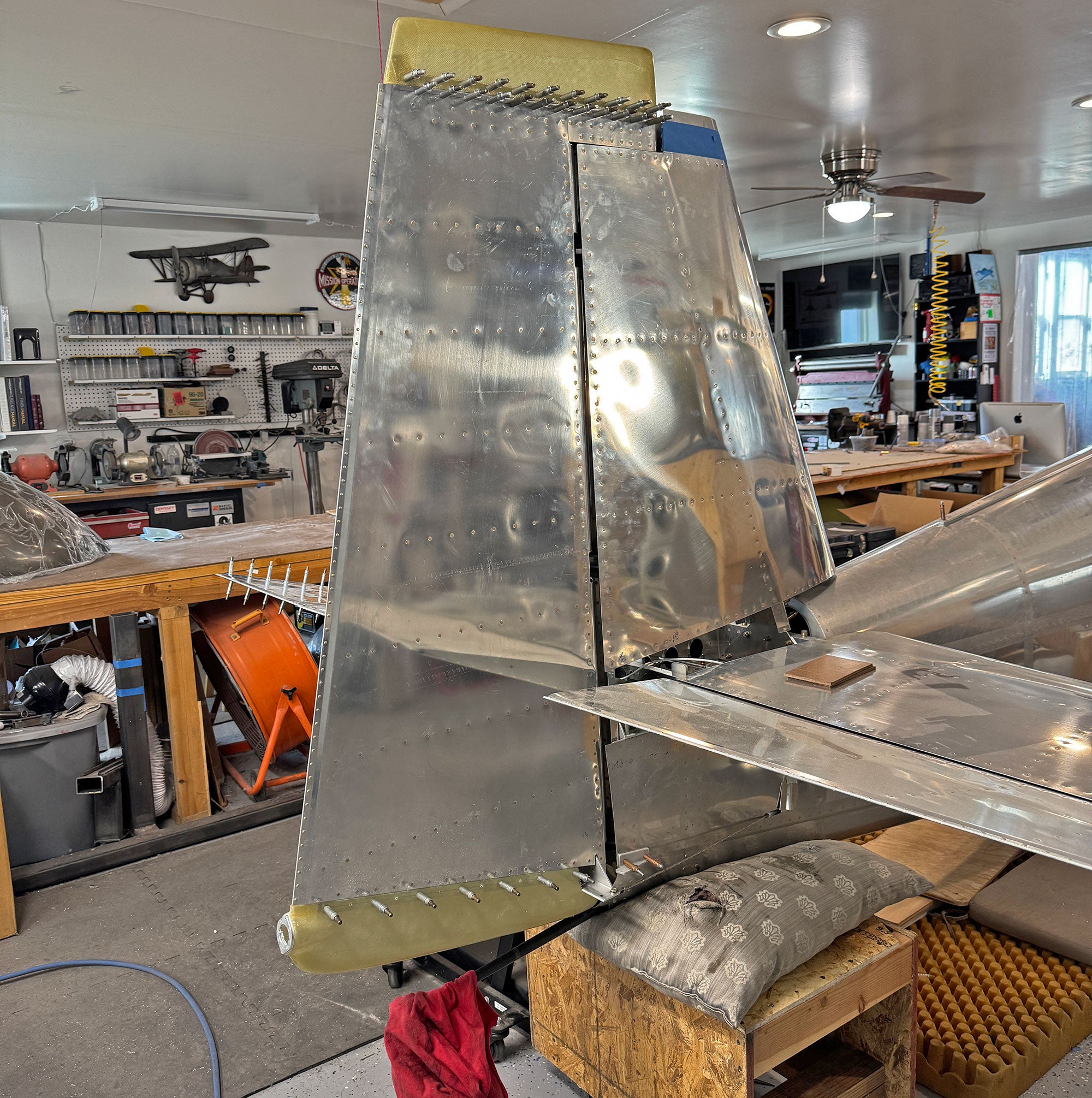
All in all, while I still have to dimple and rivet everything together, the parts fit nicely. With only the vertical stab tip left to go, I can say that the quality of these glass parts made long ago is excellent—and with a little filler and sanding, they’ll blend right in. In the balance of art versus engineering, this is clearly on the side of art—but as an engineer, I can appreciate that!