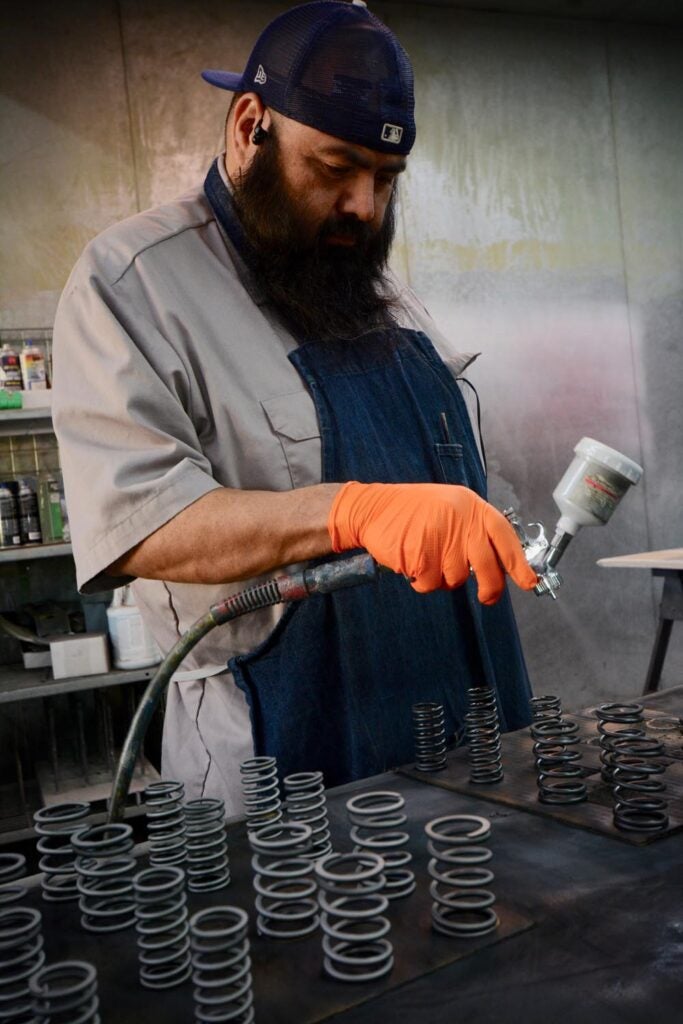
If it weren’t for the snow-capped Sierra Nevada’s floating distantly in the haze, Visalia, California, might pass for Kansas. The terrain is unremittingly flat, the roads checkerboard at right angles, and farming is what matters. Irrigation ditches and muddy tracks entering and then tapering off on the county roads are too numerous to notice, and the vastness in the crop rows and vault of open sky keeps human activity properly scaled inside nature’s expanse.
But it is California. The land work is mainly agribusiness, row crops defer to orchards of nut and fruit trees, and corn is something that happens elsewhere. Those majestic peaks suggest things aren’t the same everywhere while State Route 99 rumbles and roars its endless nose-to-tail hustle of tractor-trailers and passenger cars traversing the world’s fifth-largest economy.
A couple miles from that highway an industrial park sprawls before giving way to the main business of California’s central valley. And there, sandwiched between a multiacre pallet manufacturer and pump specialists, an unremarkable cluster of single-story metal buildings and open yards make up the Ly-Con Aircraft Engines huddle. One is tempted to say “campus” to describe this jumble of buildings, yards, shipping containers, and open-air pallet racking stacked with tired aviation hardware, but the connotation is too collegiate. Likewise, “village” is too visually congenial and hamlet dismissive of the overpowering mechanical nature of the place. But if the correct label is elusive, there’s no doubt exceptional general aviation engines emerge from here.
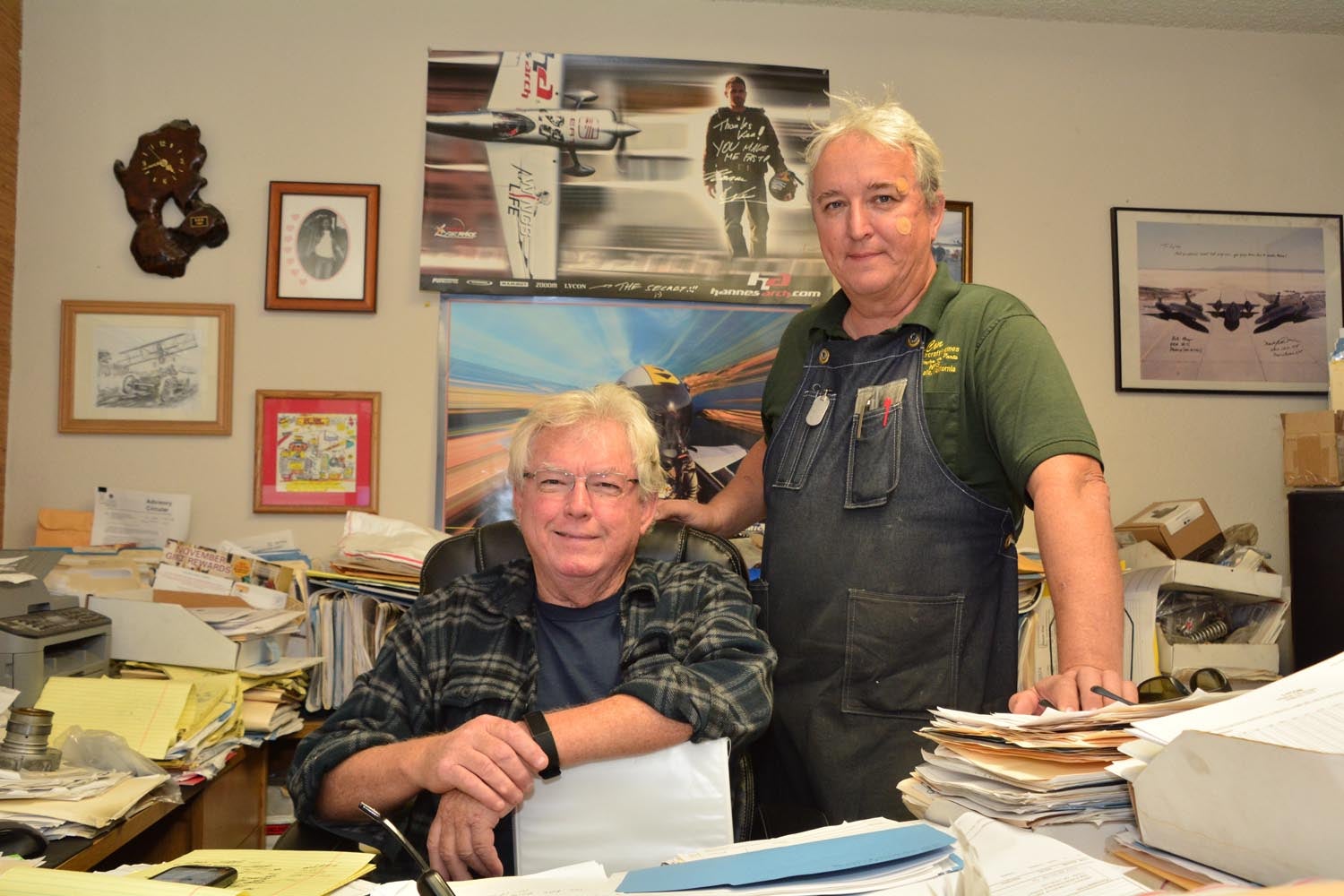
‘Tunnell’ Vision
Central to the Ly-Con story is founder Ken Tunnell, a native of the next big farming town down the road, Porterville. Just 23 years old and starting to settle from a rambunctious youth along with a three-year stint in the Marine Corps, Ken had already been working in a five-man aviation engine shop when in March 1980 he thought he could do better by opening his own place. His dad borrowed against his modest retirement to purchase a few basic machine tools in exchange for a stake in the business, and married-with-a-mortgage friend Bruce Bennet came on board three months later when Ken was sufficiently established to afford employee insurance. Ken recalls Bruce as a great engine guy, but he left Ly-Con after a couple of years to pursue his own interests.
In the beginning Ken says Ly-Con was like everyone else in that it would take new parts out of the box and start assembling engines. But as the engine count grew, Ken realized new parts weren’t always perfect—or even correct—and customer comebacks didn’t make them happy or make money.
And so the Ly-Con obsession with measuring, verifying, and accurate machining began. This now 44-year fascination with improvement through better processes and tools has been Ly-Con’s hallmark and the main generator of its worldwide reputation for dependable, powerful engines.
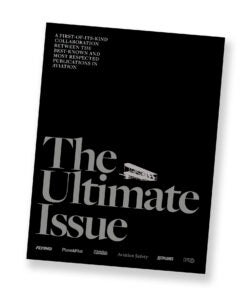
It’s likely the dogged zeitgeist of the place has been set by its geography. Visalia and Porterville are successful, somewhat isolated farming towns. Getting up in the morning and getting to work is native to the area, as is the resolve to use the best tools at hand and to get better ones tomorrow. Ken and his 36 employees are all salt of the earth, typically self-taught but ready to work and willing to try something new or learn from others. Their methods are empirical, and if there’s not a single engineering diploma hanging on the office walls—or a pilot’s certificate in anyone’s wallet—there are a hundred signed photos from pleased customers showing off every sort of flat-engined airplane winging via Ly-Con power.
A textbook definition of a mom-and-pop store, Ly-Con remains Ken Tunnell’s fiefdom, with just wife Darla (accounting) and brother Bryan (racing shop) also involved. There’s the efficiency of a benevolent dictatorship in the arrangement but also the bottleneck of everything going across Ken’s paper-covered desk. As the business has grown, so have the responsibilities, including the impedimenta associated with FAA Repair Station status and doing business in the Golden State. Ken and Darla have been at the shop seven days a week forever, and if there is a complaint from the field, it’s that Ly-Con is a slow shop, a place where engines languish and getting Ken on the phone is tough to do.
It’s tough because there is so much to attend to, and once you get Ken on the line, he tends to stay there until things are fully settled. He isn’t one to cut corners, and projects can pile up. He says most of the caterwauling is from customers hoping to speed up things, but dawdling on the payment continuum or from pilgrims thinking engine shops keep rebuilt engines on the shelf waiting to go. With an average turnaround time of eight months, the reality is Ly-Con’s delivery schedule compares well with the year or years now common from the OEMs.
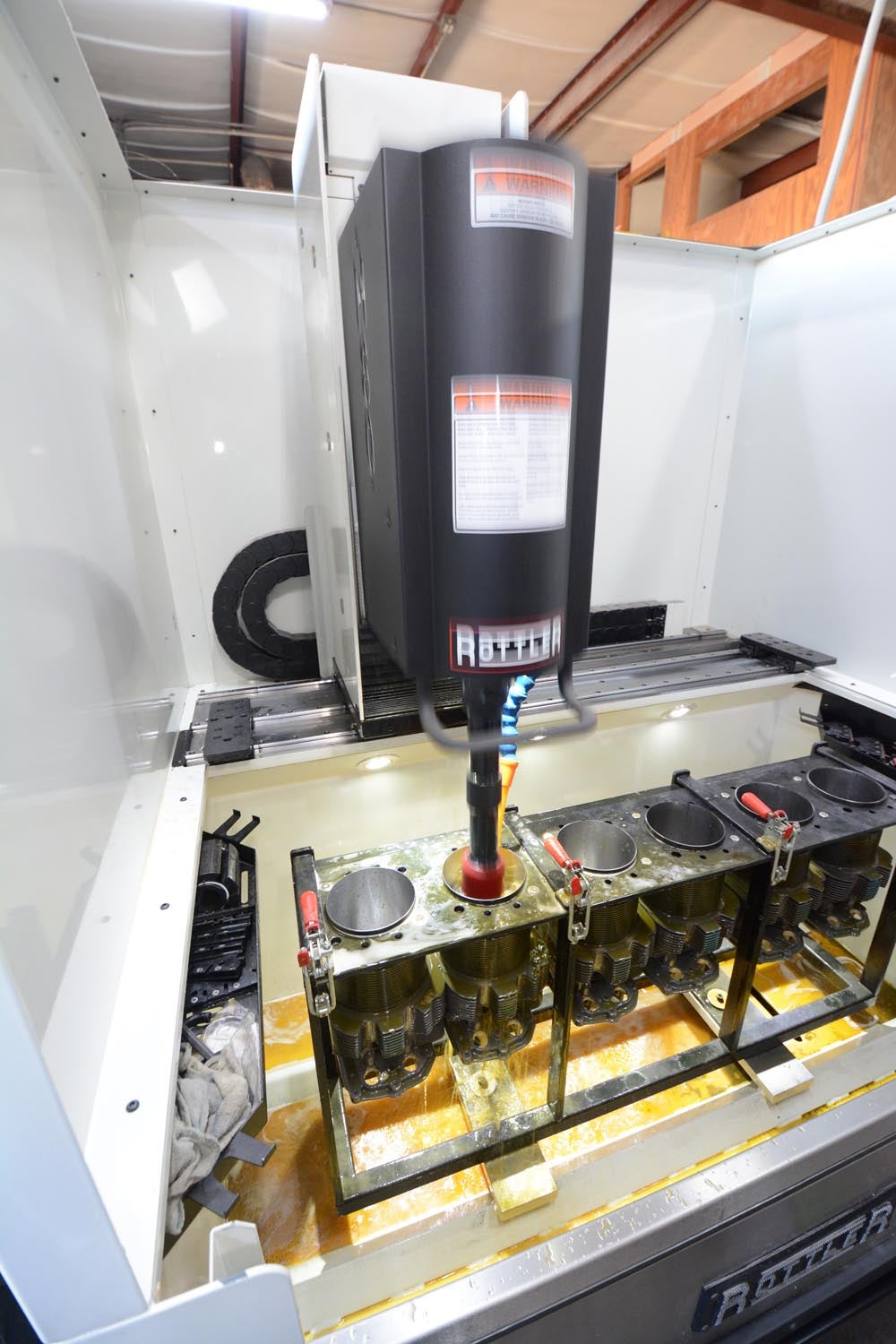
Early On
Today, Ly-Con is noted as a horizontally opposed specialist with a strong sideline on performance engines, but those are learned behaviors.
“When we first started, we did [Pratt & Whitney] 1340s and 985s due to crop dusting around the valley,” recalls Ken. “But it was 250 man hours to do a radial and 40 hours to do a flat motor, and you made about the same money. So we started leaning toward flat engines and away from radials. But we did some [Warner] Scarabs and Franklins before they all faded away.”
One niche picked up via Bob Penland was helicopter engines.
“He taught us the VO (helicopter) engines,” Ken says. “Penland in Long Beach was the helo king in those days. We still do 435s, 540s, and all that stuff…We still build ’em for helos all around the world—Germany, Canada, New Zealand. People are scared of ’em, but if you do a good job, they’re a really durable engine.” He adds with a grin, “Unless you don’t have a prop governor and overspeed ’em!”
In the early years Ly-Con was just one of many engine shops in the valley, so capitalizing growth in the company was difficult. Characteristically unafraid to try something different, Ken saw an opportunity when Rocky Harrow, another local machinist, ran into trouble. With the bank ready to repossess Rocky’s shop, Ken paid off the debt then moved Rocky and his entire operation, including a lathe, mill, and pantograph, into Ly-Con.
“We brought him into the shop to do machining, reground lifters, connecting rods, that sort of stuff,” Ken says. “And so I spent some of my time hustling machine shop stuff. We made helical gears for a printing press company. I got the right wire and spray welding on the gears so Rocky could go portable to fix those gears when they dropped a screw in them or something.”
Eventually Rocky left, but by then Ly-Con was established in the aviation engine scene, with good contacts and a growing customer base.
“We were on the [Visalia] airport for nine years,” says Ken, noting he made the painfully disruptive move to the company’s present industrial park location a couple of miles away in 1989.
He says he was encouraged to relocate due to a 60 percent rise in rent in just two years, along with a court order kicking them out after he disputed the rent increases.
“We almost went out of business because of the move,” he says. “We were just five people and 3,000 square feet, but it took [electrical utility] Edison a long time to put in three-phase power [and there was no money coming in the meantime.]”
Ken came to see the move off-airport as a plus.
“It was a lot cooler being on the airport, but you can’t own anything at the airport, the city owns it,” he says. “Here you can build equity in the real estate, so it was a blessing getting off the airport.”
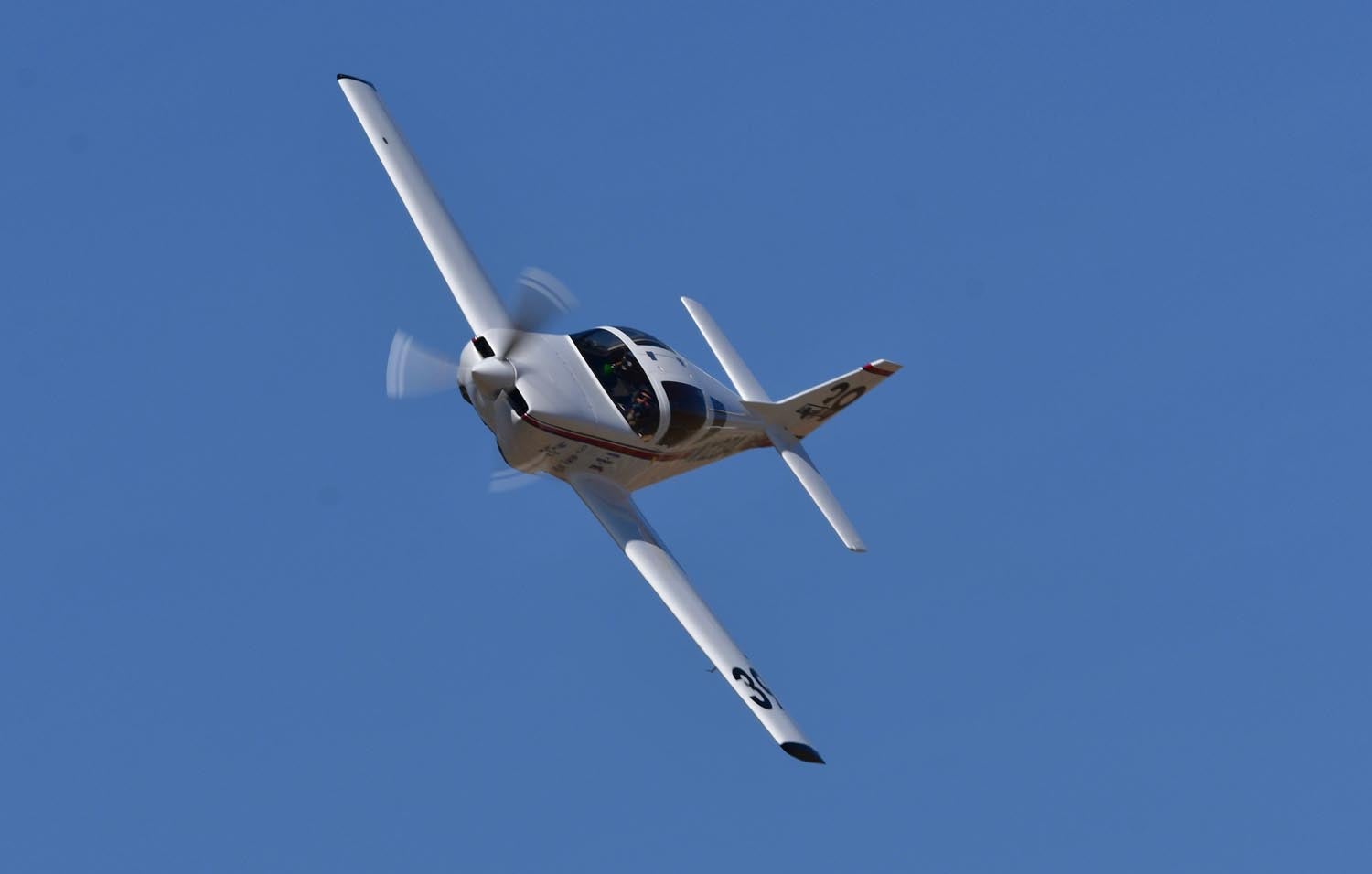
Enter Performance
Earning competence with stock rebuilds marked Ly-Con’s start, so when Ken hooked up with Southern California speed guru Steve Mehalick, the company was ready to add performance. The pivot was John Harmon—just down the road in Bakersfield—building the first two Van’s RV-3-based Rockets. The first used a stock Lycoming, but backer Jim Ewing wanted more horse pressure in his Rocket engine that Ly-Con was building. So Steve taught Ly-Con about porting, high compression, and other power-building tips he’d learned working with Dan Gurney, JE Pistons, Jim Fueling, and others in the extensive Southern California speed scene. Ken credits Steve’s knowledge and industry contacts with quickly pushing Ly-Con to the front ranks of performance aircraft engine builders, and it was a tough loss when Steve medically retired far too early 20 years ago.
Ly-Con’s other performance pioneer was Sean Tucker.
“We did his stuff for 43 years,” says Ken. “He was a crop duster in Salinas…He used to hock his house to get parts to do his engines.”
Sean didn’t have to hock his house forever, and Ly-Con rose up the performance ladder with his outstanding career. Other major aerobatic acts gravitated to Ly-Con’s thumping, lightweight parallel-valve AEIO-540 engines, including Jim LeRoy, Skip Stewart, and about three-quarters of the Red Bull Air Racing field until they went to spec engines from Thunderbolt to limit costs and performance.
Improving performance is catnip to Ken. He can come across as aw-shucks, but that’s just his native impishness papering over a deep competitive streak.
“I just like to have the best stuff,” he says. His attraction to the latest tools also means satisfaction in turning out no-excuse stock engines plus winning races and being the big dog on the pro airshow scene. He really doesn’t like second place.
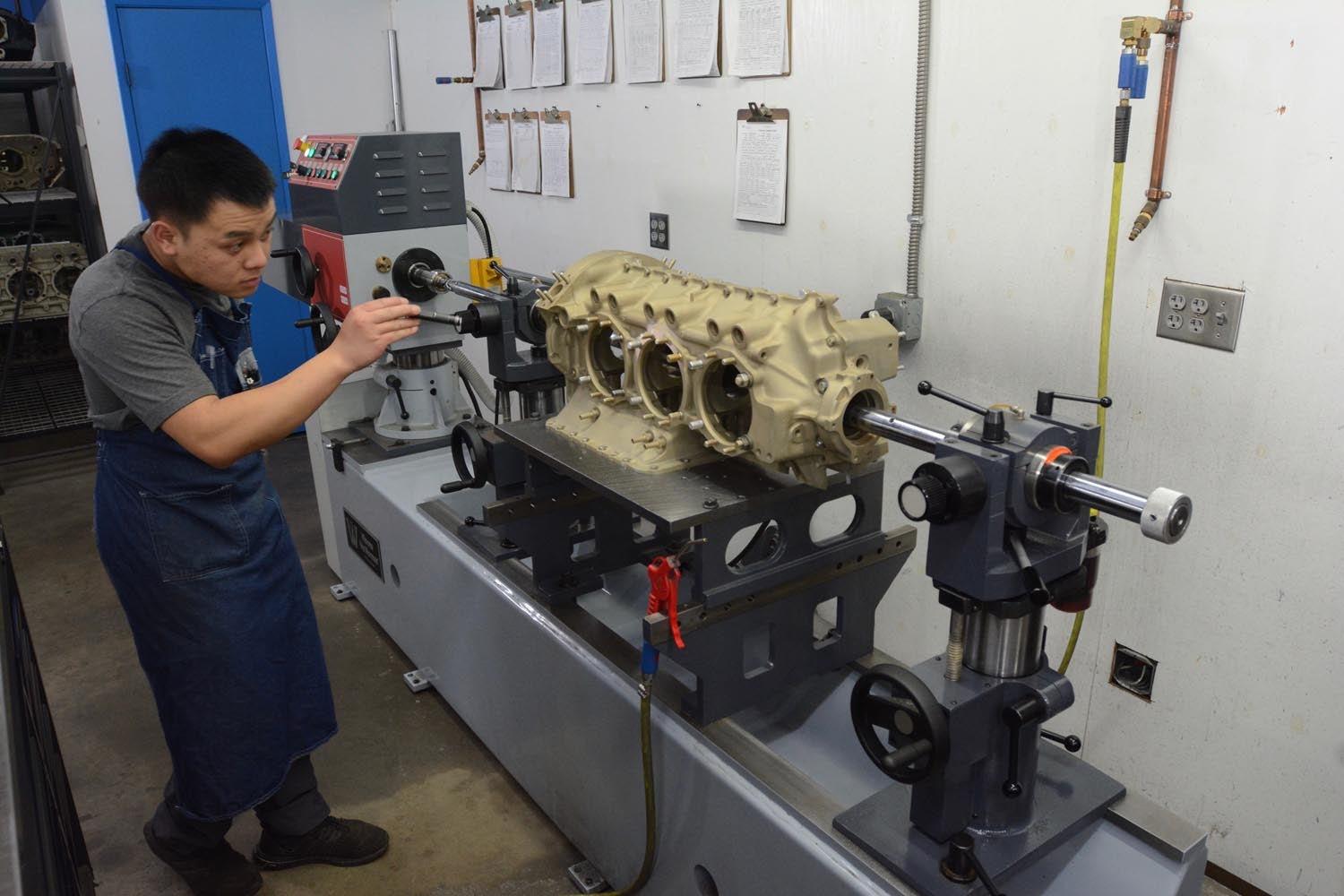
No doubt the most visible of Ly-Con’s power habit has been air racing, with the Formula 1, Biplane, and Sport pits at Reno, Nevada, presenting an almost embarrassing array of Ly-Con stickers. Like the early Red Bull series, Ly-Con’s penetration of Formula 1 was typically more than half the field, and it was something similar in the hot-rodded Biplane class. The Biplane efforts have been capped so far by overwhelming Ly-Con power (think almost 400 hp from a naturally aspirated IO-360) in Phantom pushing lap speeds over 260 mph. In the major-league Sport Gold division, Ly-Con provided the 580-cubic-inch foundations for class dominator Jeff LaVelle’s 410 mph Glasair III along with numerous other competitors.
All of these engines bend the status quo when it comes to power, but the 900-plus hp under LaVelle’s cowling truly stretches the imagination regarding what’s possible with the same cases and crankshafts the rest of us fly behind.
For sure, Ly-Con’s push to performance has paid dividends for all its customers. It was broken counterweight ears on the hardcore tumbling aerobatic engines that led to the cryogenic solution Ly-Con now offers. If a daily driver customer balks at the thought of 10:1 compression pistons, Ly-Con can authoritatively speak to what happens not only at 10:1 compression, but 11:1, 12:1, even 14:1 because it has built and run numerous engines at all of those power levels. Or 5.5:1 compression for turbo fans. The same goes for about every sort of power trick imaginable because Ly-Con has firsthand experience developing those engines, along with the customer feedback plus tearing down and eyeballing the results.
In the Shop
Today Ly-Con’s 36 employees work on a 3.2-acre lot holding four buildings, two dyno cells, one vertical test stand, and several yards full of shipping containers and pallet racking containing the company’s extensive core engine collection. There are approximately 26,000 square feet under roof and 7,000 square feet of working shop space. You’ll have difficulty finding an unoccupied horizontal surface large enough to set down your coffee cup.
Collectively, the facilities support an FAA Repair Station, including engine and engine accessory overhaul. The FAA sees Ly-Con as two entities, one repairing and building certified engines, which makes up about 70 percent of the overall business, plus the experimental engine work making up the remaining 30 percent. The certified and experimental work pass through the same workstations—that is, there is no separate building or shop dedicated to either class of engines—but the parts, processes, and paperwork are carefully segregated to ensure compliance.
Organizationally there is the business office, teardown, cleaning, inspection, painting and coating, welding, porting, cryogenic, case, accessory, assembly, dyno and shipping shops or stations.
The parts department is its own business—Kendra Air Parts Inc.—but located with the rest of Ly-Con. There’s a room dedicated to Ly-Con’s proprietary line of NFS pistons too.
You could also say manufacturing is a Ly-Con subset as it makes its own adjustable oil pressure regulators and dabbles with custom valve covers and other miscellaneous parts, but this work slots in among the regular jobs. The same might be said about the more experimental work, such as flow testing cylinder heads or
trying new coatings, but again those workstations are shared with the mainstream certified efforts.
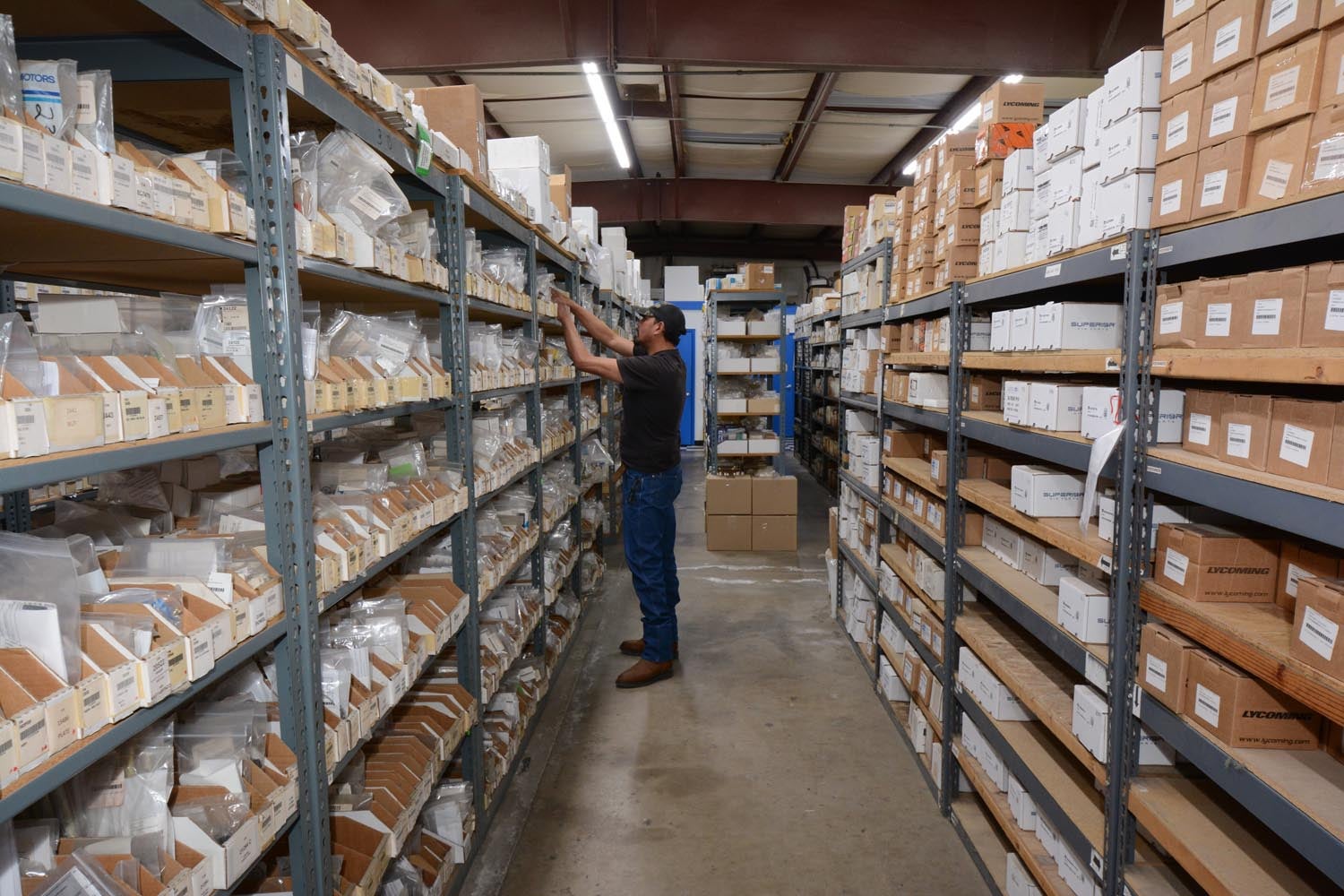
The Machine Age
Consistently adding new machining and testing capabilities means Ly-Con reached the usual level of in-house capabilities long ago. Those few specialized machining steps—crank grinding and machining engine cases are good examples—are or were farmed out to specialists just like every other engine builder. With the basics covered, Ly-Con eventually moved into unusual capabilities rarely offered by an aircraft engine builder, mainly driven by its need to step up its experimental engines as the aerobatic and racing customers asked for more power or ran into longevity issues.
One of the first of these was a wet flow bench for flowing carburetors and fuel injection parts but also key to developing cylinder head ports. By adding on to a commercially available automotive performance flow bench designed to move just air, the fuel bench does the same task but while flowing air and solvent. The combination fuel and flow benches have been educational as carburetors, injection, and cylinder heads got tuned up for racing, as well as serving as a great calibration tool for verifying performance of stock parts for certified applications. Originally built with analog instruments, the fuel bench was later upgraded to digital data acquisition and remains in daily use.
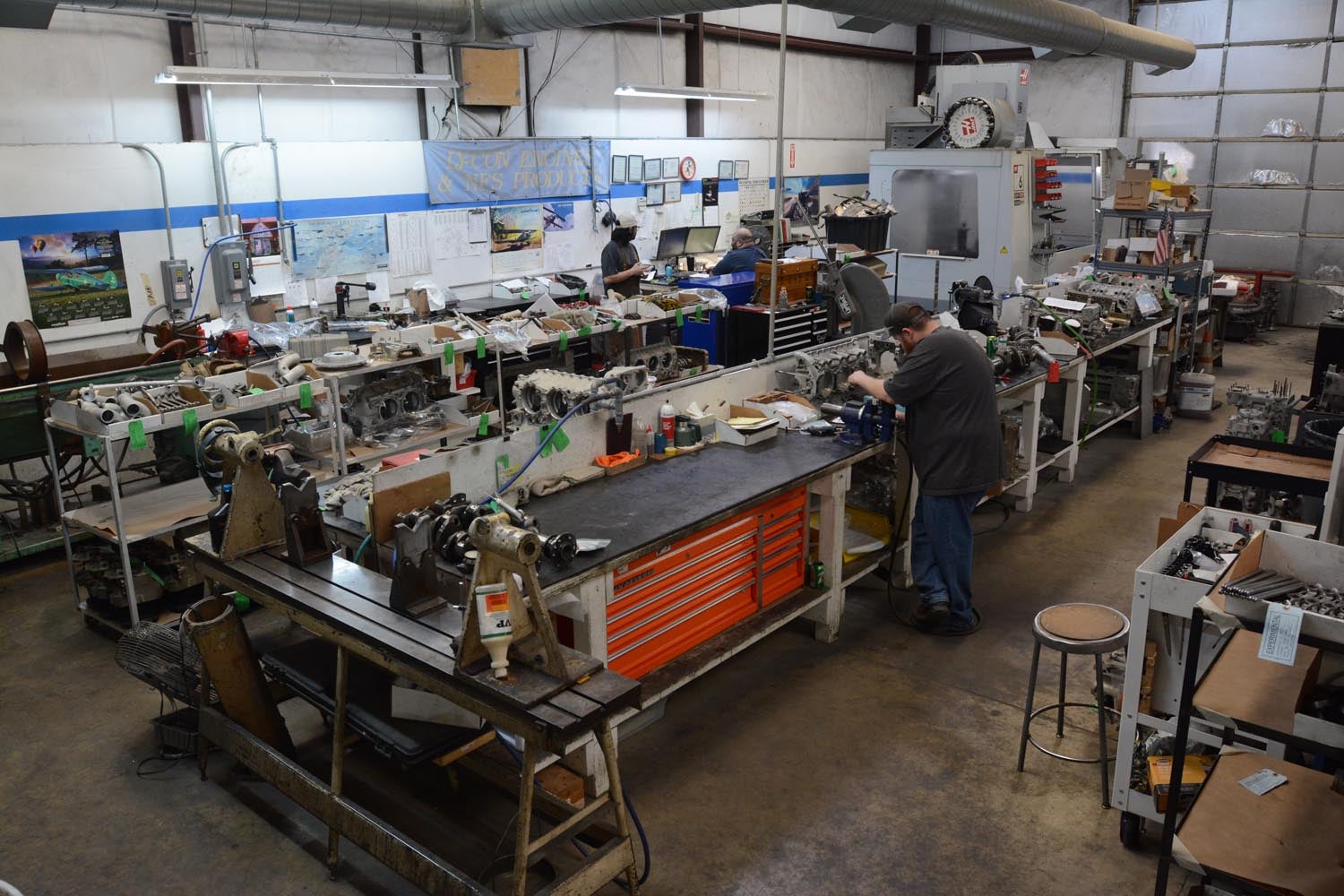
A fundamental part of engine building is improving the ring seal between the cylinder walls and piston rings. This has always been a sloppy thing in big-bore, air-cooled airplane engines—it’s the nature of these beasts—but Ken Tunnell has always been improving ring seal both to increase engine power and reduce oil consumption, along with speeding engine break-in and thus avoid oil-slurping during the engine’s entire lifespan. Key to this is precision in honing the cylinder bores along with experimenting with piston ring material. Building so many racing and aerobatic engines gives Ken the opportunity to continuously try different ring/bore combinations, and making some rather large investments in the latest cylinder hones has allowed improving the cylinder finish and chokes. For decades a Sunnen CV-616 hone has been swirling out the cylinders at Ly-Con, but after reaching the limits of that machine on the latest experimental jugs, a new Rottler automated hone was added. That’s a six-figure investment, but Ken needed it for the increased precision, plus, as an automated machine, it will speed cylinder production throughout Ly-Con’s workflow.
Sixteen years ago when Ly-Con wanted to improve crankcase parting-line sealing by replacing the stock sewing thread method with a rubber O-ring set in a machined groove, it needed the hugely increased precision and speed of an automated milling machine for this complex tool path. That meant funding the purchase of a 20 hp CNC machining center, a first in aviation engine rebuilding. Of course, the five-axis Haas Automation CNC mill has since improved or supported all sorts of tasks previously done manually or not at all.
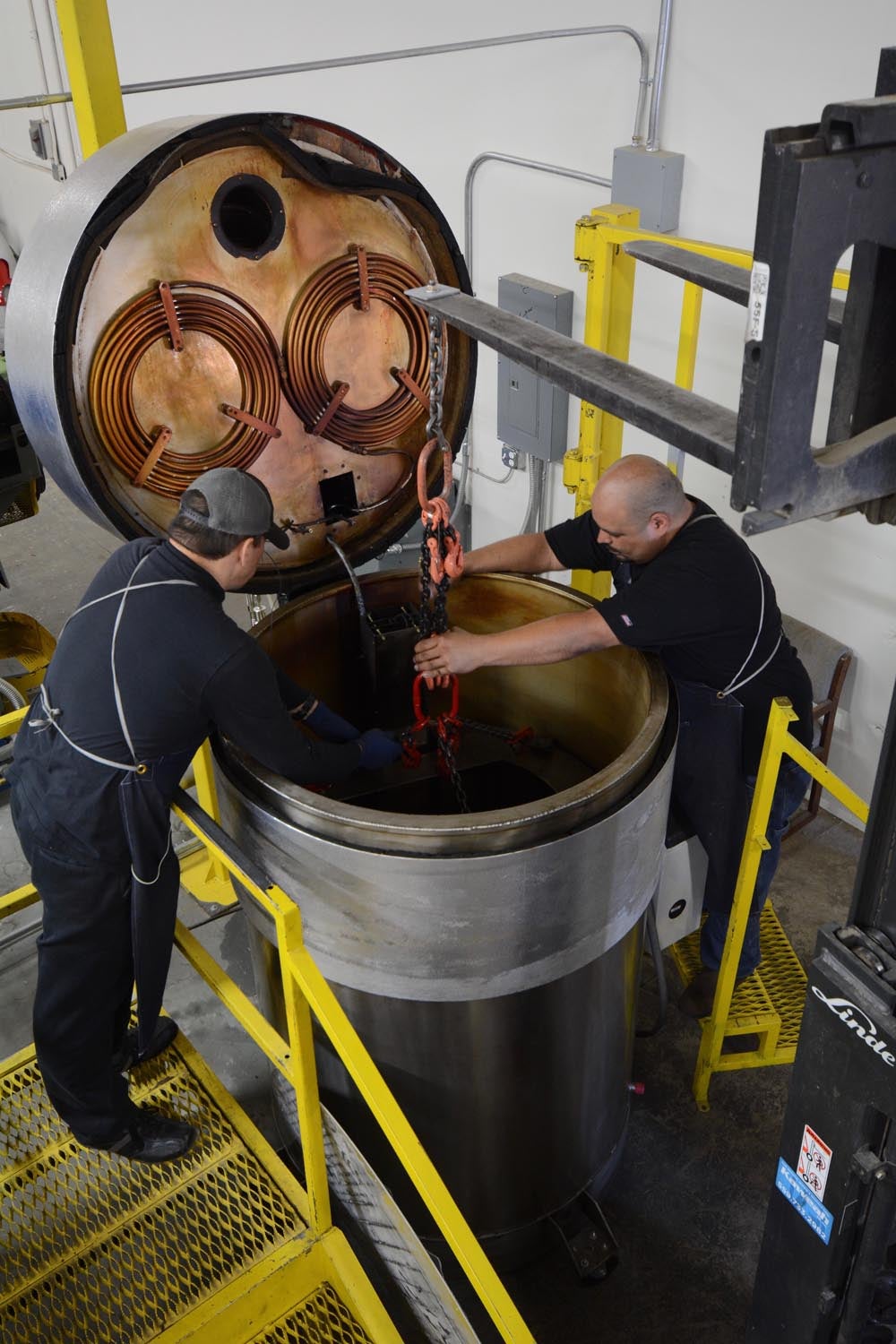
Another unique Ly-Con capability is cryogenic heat treating. This is the use of liquid nitrogen to chill parts to minus-305 degrees Fahrenheit then heating them to 300 F before bringing them back to room temperature. It normalizes the crystalline structure of metal (and other materials) and has proven a godsend in strengthening crankshafts in high-power engines. With “cryo” proving useful throughout an engine, Ken bought out an entire cryo facility and set it up inside Ly-Con. It’s proven popular with performance customers and suggests the way to greater longevity on stock builds as well.
Another big plus are the two engine dynos.
These have been upgraded over the years with good data acquisition systems offering major benefits. First, customers have objective data on how their engine runs, the engines are delivered leak-free and fully vetted as to function along with being well along the critical break-in period. Furthermore, the dynos prove whatever was done in the shop. Especially for the experimental engines, the dynos close an essential feedback loop on what works or doesn’t when improving engine builds. Having just brought both dynos to identical specification and data capabilities has sped workflow as it’s no longer necessary to wait for one or the other dyno to open up for a specific testing need.
Increasingly coming on line at Ly-Con is a small shop dedicated to servicing engine cases. This is unique for an engine builder because, as long as anyone can remember, case align boring has been the private domain of Nixon on the West Coast and, especially, Divco, in Tulsa, Oklahoma. But now Ly-Con has purchased its own align boring machine, along with a smaller CNC center and repurposed mills for various supporting tasks, allowing full servicing of engine crankcases for its in-house needs (no one in Visalia is out to corner the market on case rebuilding). This case shop is still new and developing its working protocols, but it’s primarily designed to give Ly-Con more control over this critical aspect of engine building and hopefully a small gain in profit margin eventually.
The latest gizmo is a laser welder in the welding shop. Barely unpacked during our visit, the welder promises to allow heretofore impossible aluminum repairs, but that’s something still theoretical. Like many of the ideas Ly-Con has brought to fruition as FAA-approved processes, laser welding is something the Visalia team will practice with on scrap parts, and if those work, it will move to dyno testing, followed by use on experimental engines run by trusted customers willing to try something new. Applying for a process approval for certified engines remains well in the future, assuming it even works and makes business sense. If it doesn’t, it won’t be the first time what sounded like a great idea didn’t pan out.
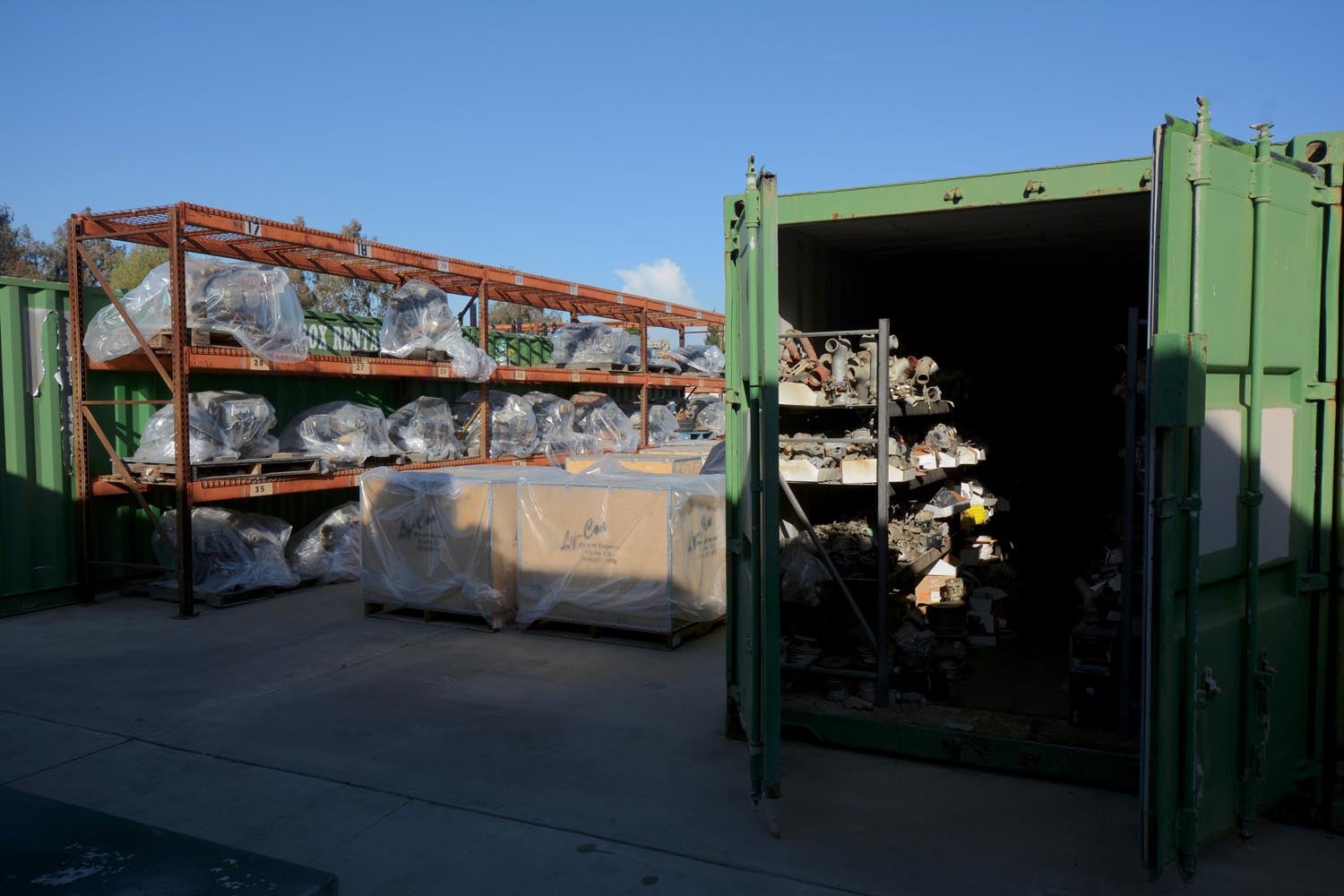
Basics First
While Ly-Con is well known for its innovation and performance successes, sometimes Ken Tunnell laments the shop is perceived as something out of left field, a place for wild experimental engines, when the reality is its livelihood is dependable daily driver overhauls, inspections, IRANs, prop strikes, and all the other work found in the certified world. It’s understandable as racing garners much publicity—and hardly any income considering the work and sponsorships involved—while the certified overhauls are the true work but take place in relative obscurity.
In reality the performance and certified work is complementary. Racing has improved the breed, the lessons learned around the pylons or in front of the airshow crowds inevitably finding good employment in the certified world. Ultimately building great performance engines—and daily drivers—is all about making the flat parts really flat and the round parts really round. There are no secrets, just a will to best understand the engine’s needs and a near slavish adherence to eliminating oversights through constant checking.
In the end that’s really what goes on at Ly-Con.