Home for Mike Hongisto is Carlton, Minnesota, a small town 21 miles southwest of Duluth that counted 862 residents in 2010. “Since I was a little kid, I’ve wanted to fly, but I couldn’t afford it until after I finished college.” In late 1993, he made a winning bid in a Duluth radio station’s fundraising auction for 40 hours of Cessna 172 time and 20 hours of dual instruction and earned his private ticket in early 1994.
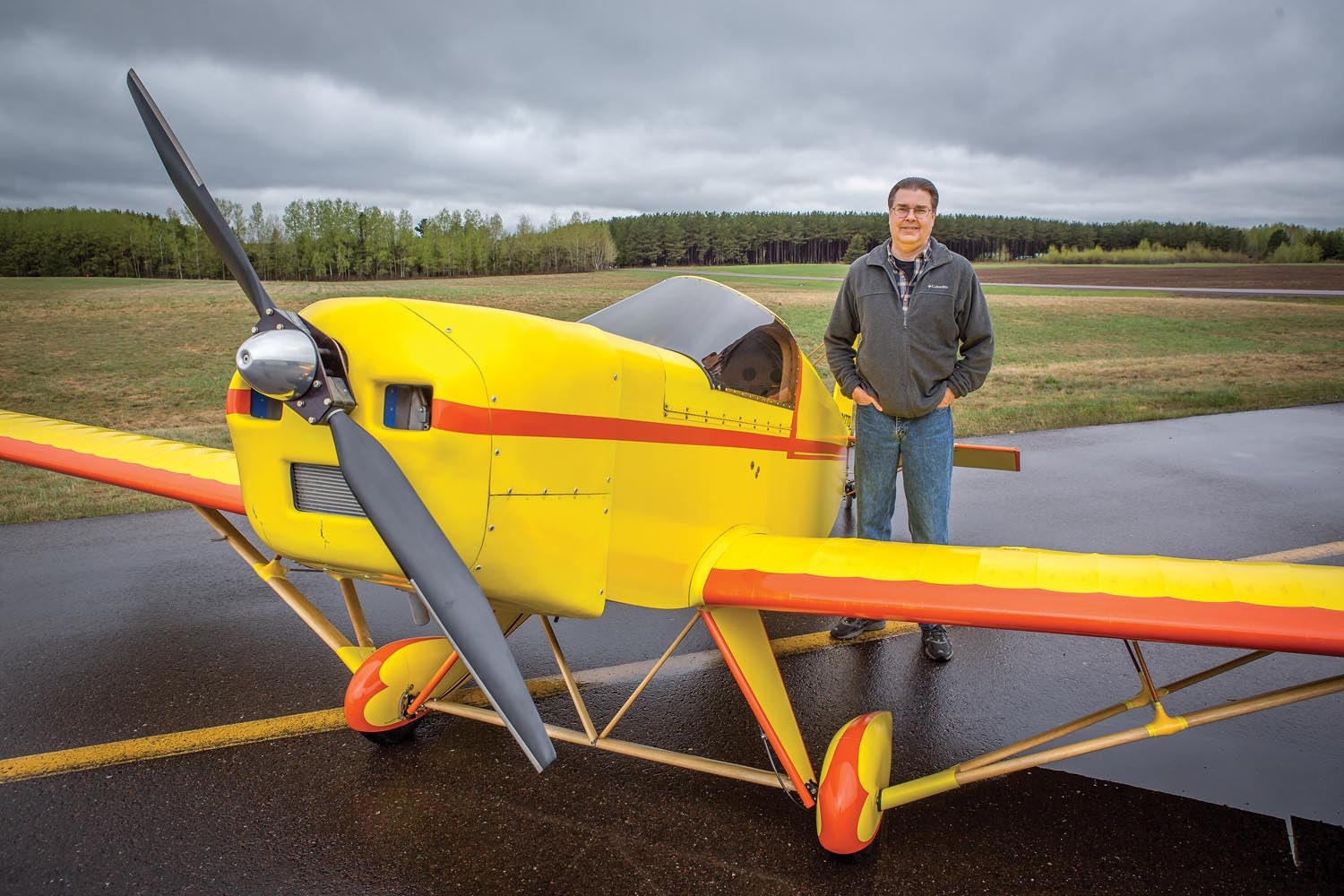
Climbing the corporate ladder in the natural gas industry moved Hongisto around the nation, and he owned a Grumman Cheetah, and then a Beech Bonanza, for trips home. Stepping off the ladder in 2002, he returned to Minnesota. “I’d planned to take a couple of years off and build the house I’m now living in, and then get into consulting.”
About six years later with his house three-quarters finished, Hongisto started looking for an airplane to build. It was part of his plan, and he built his house with this project in mind. It has an attached three-car garage with slab heat. During the winter, “I can just walk out of the house in a t-shirt and jeans and go work on the airplane.”
But what airplane to build? “I didn’t need six seats anymore,” said Hongisto. “Most of my flying is solo, so I was looking for something that is light and sporty and, hopefully, easy for a first-time builder. And I wanted wood. I’m familiar with it. I built my house and most of its cabinets, and an airplane isn’t all that much different than cabinets.” Besides, he had most of the tools he needed.
He looked at the Mini-MAX first. “But I didn’t fit in that, and there was no way to modify it because of the way the spar was set up, so I gave up on that idea,” said Hongisto, who is a long-legged 6-foot-5 and weighs 200 pounds. “Then I heard about the Fisher Avenger,” and he traveled to Edgeley, North Dakota, to sit in it.
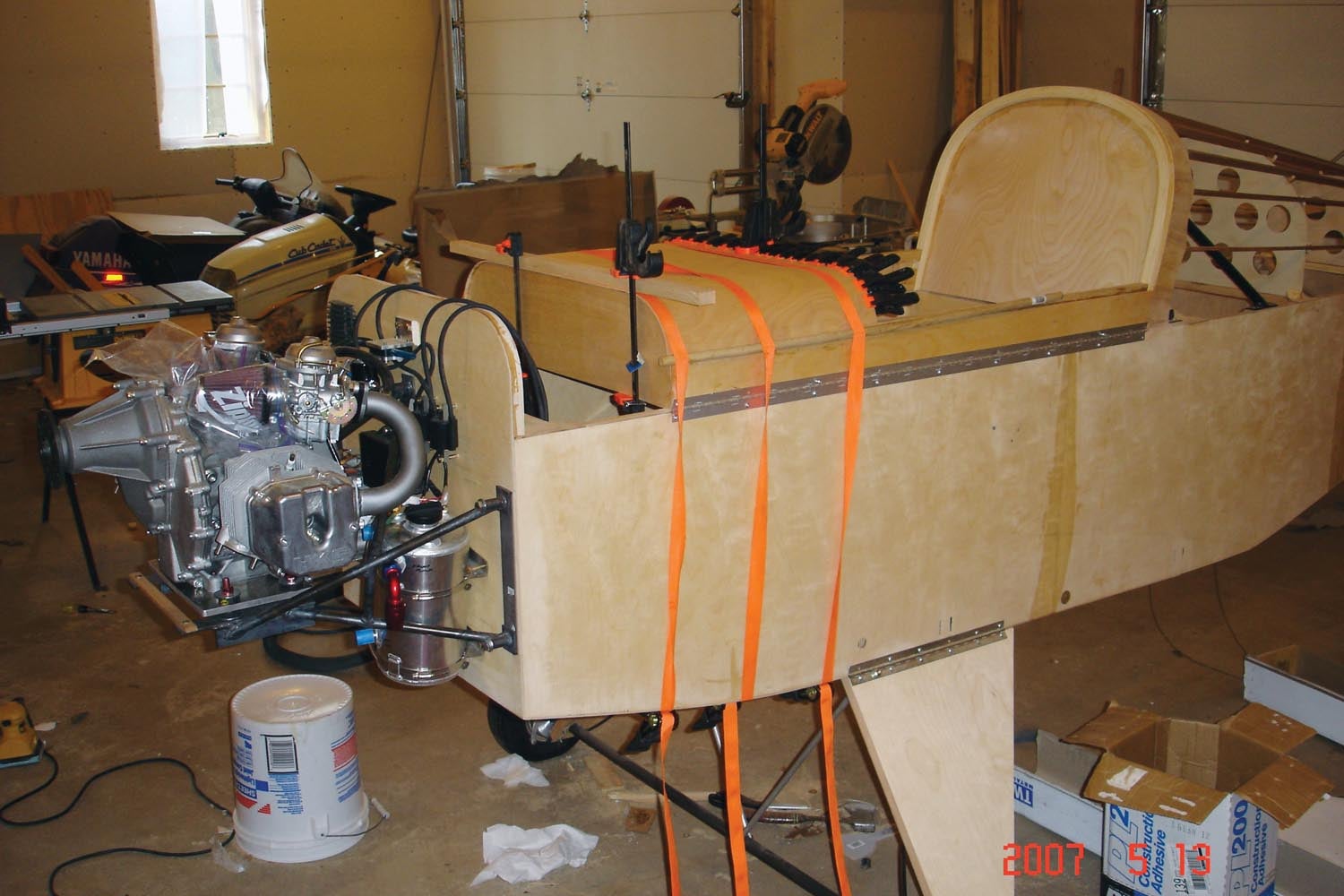
“It was real tight, but the way the spar was situated, it looked like I could move the seat back.” Sitting in the Avenger was as far as the visit went. “I had no idea how it flew. I just had the general specs at the time.” With modification in mind, he bought just the plans, and “I sat on them for two years. When I started digging through them, I discovered that the VNE was pretty low, which meant a slower cruise speed, and I was looking for something a little faster. Then I decided to just go ahead and build it, hoping it wouldn’t cost too much or take too long.”
Bespoke Building
“Fisher predicted a 400-hour build time, which was wildly inaccurate,” said Hongisto. “If you got the kit, maybe, but being a first-time builder, and changing a lot of things, I think I had about 2,000 hours in it before I finished the 21-month project. I started in August 2007 and finished in May 2009.”
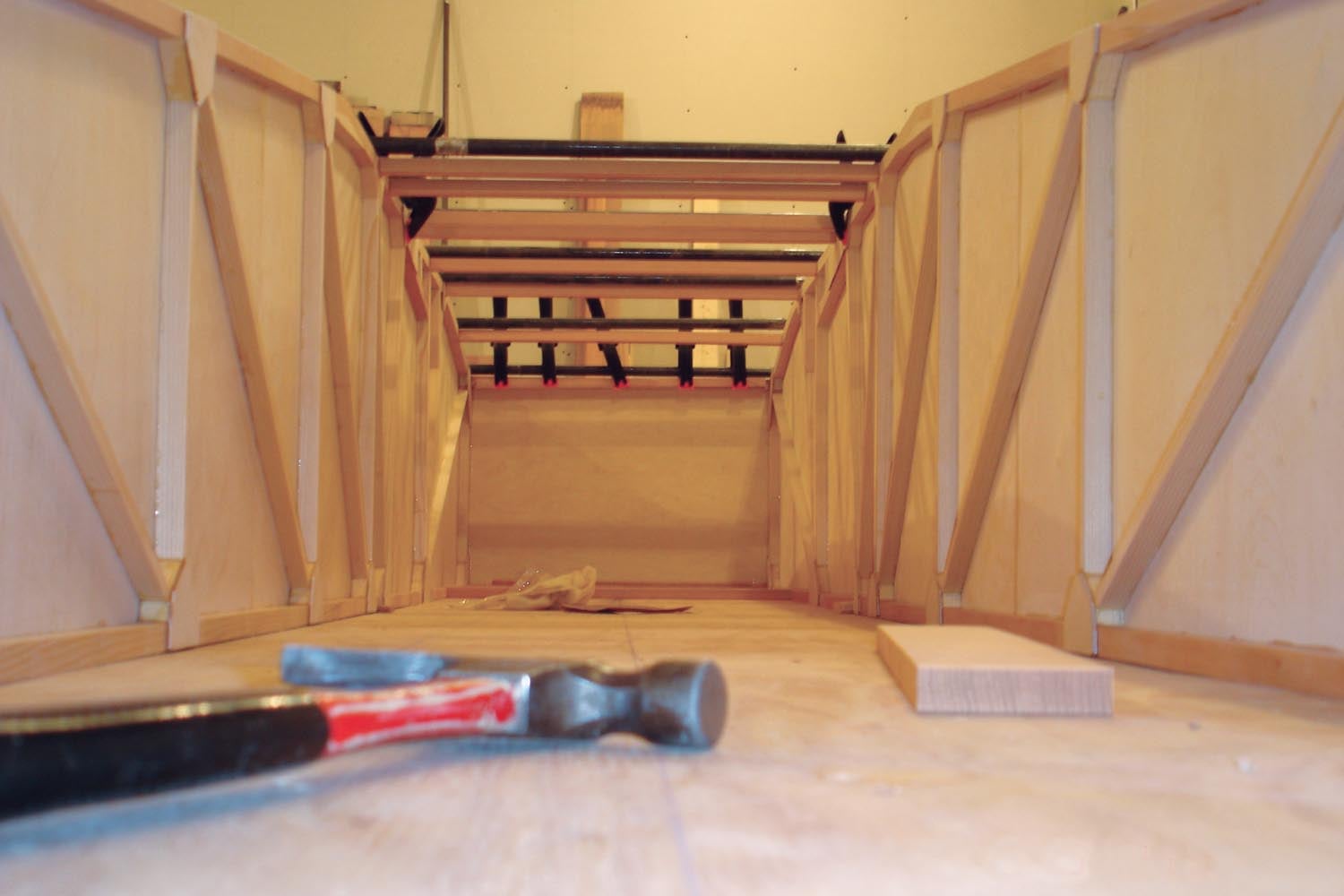
The Avenger’s construction manual explained the airplane’s parts and how they worked together. “You get full-size plans that you roll out on the table and build on top of that.” Creating a bespoke airplane is one benefit of building from plans; when assembling a kit, builders cannot make many changes.
After spending a “fair amount of time studying the manual and looking at the plans, I had a general idea of what needed to be done. But you really don’t know what you’re getting into until you start doing it.”
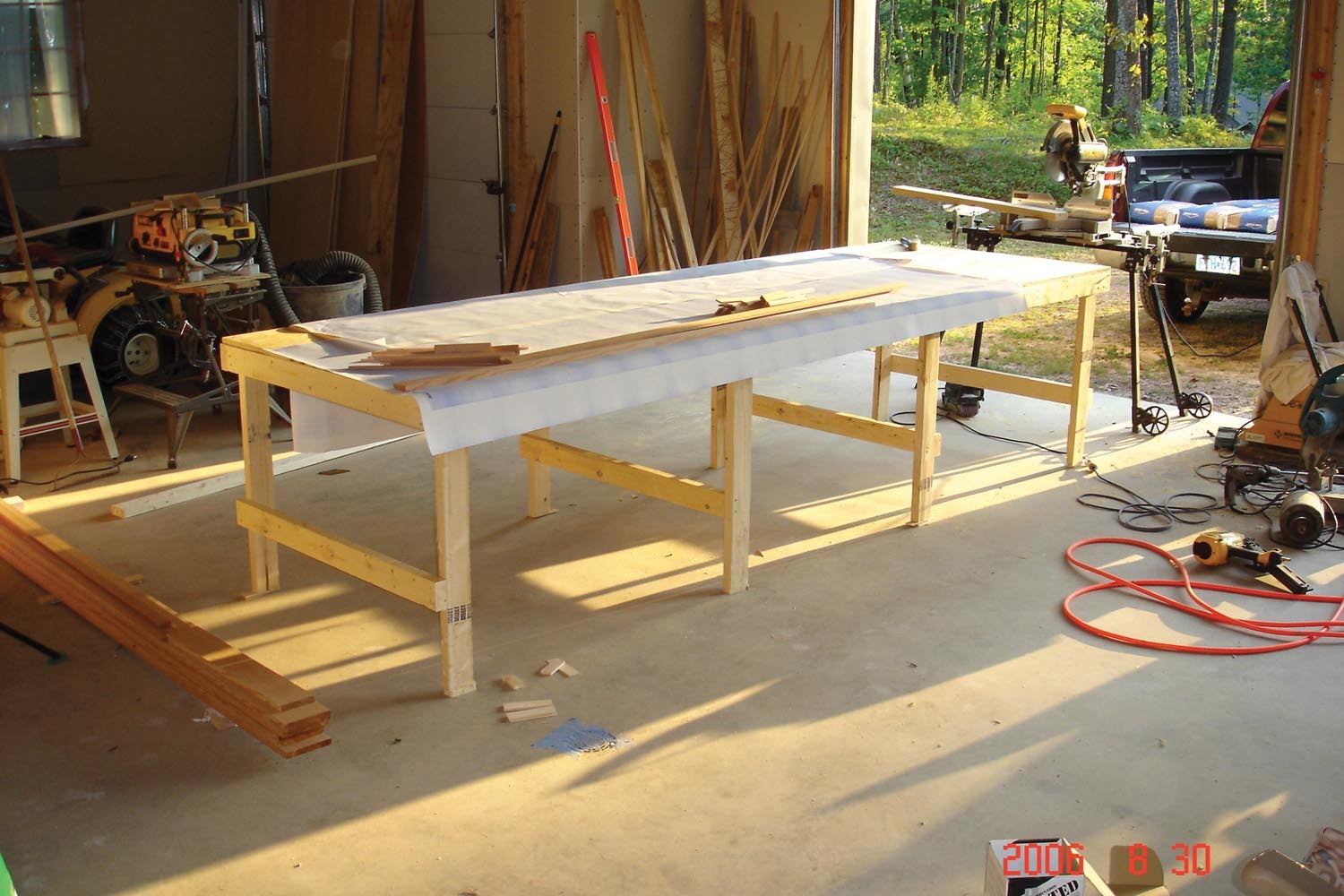
To make room for his 36-inch inseam, Hongisto moved the Avenger’s seat back 3 inches and tilted it back three-quarters of an inch at the top. “That made the project doable and made it a more comfortable airplane.”
To make it even more comfortable, he made the fuselage 2 inches wider. Stock, it measures 24 inches exterior to exterior. Increased comfort was not his only motivation. Hongisto planned to use a two-cylinder, 60-hp HKS 700E engine, and with the 26-inch wide fuselage, “it fit without its cylinders hanging in the breeze.”
Except for the wider fuselage, “the longerons, spars, and external dimensions are stock” he said. “I stayed away from structural changes. Not knowing what I didn’t know, I didn’t want to venture out and affect the safety of the aircraft.”

Building the wider fuselage was less involved than the stock design because it was parallel from the cockpit to the firewall. “The plans had you taper the fuselage forward to the narrower than 24-inch firewall so the cylinders of a half-VW engine would be in the slipstream.”
When searching for an airplane to build, “my goal was something I could fly nonstop to Oshkosh with all my gear, a tent, sleeping bag, clothes for a week, everything except food. Because of that, I needed a baggage area behind the seat, not a fuel tank.”
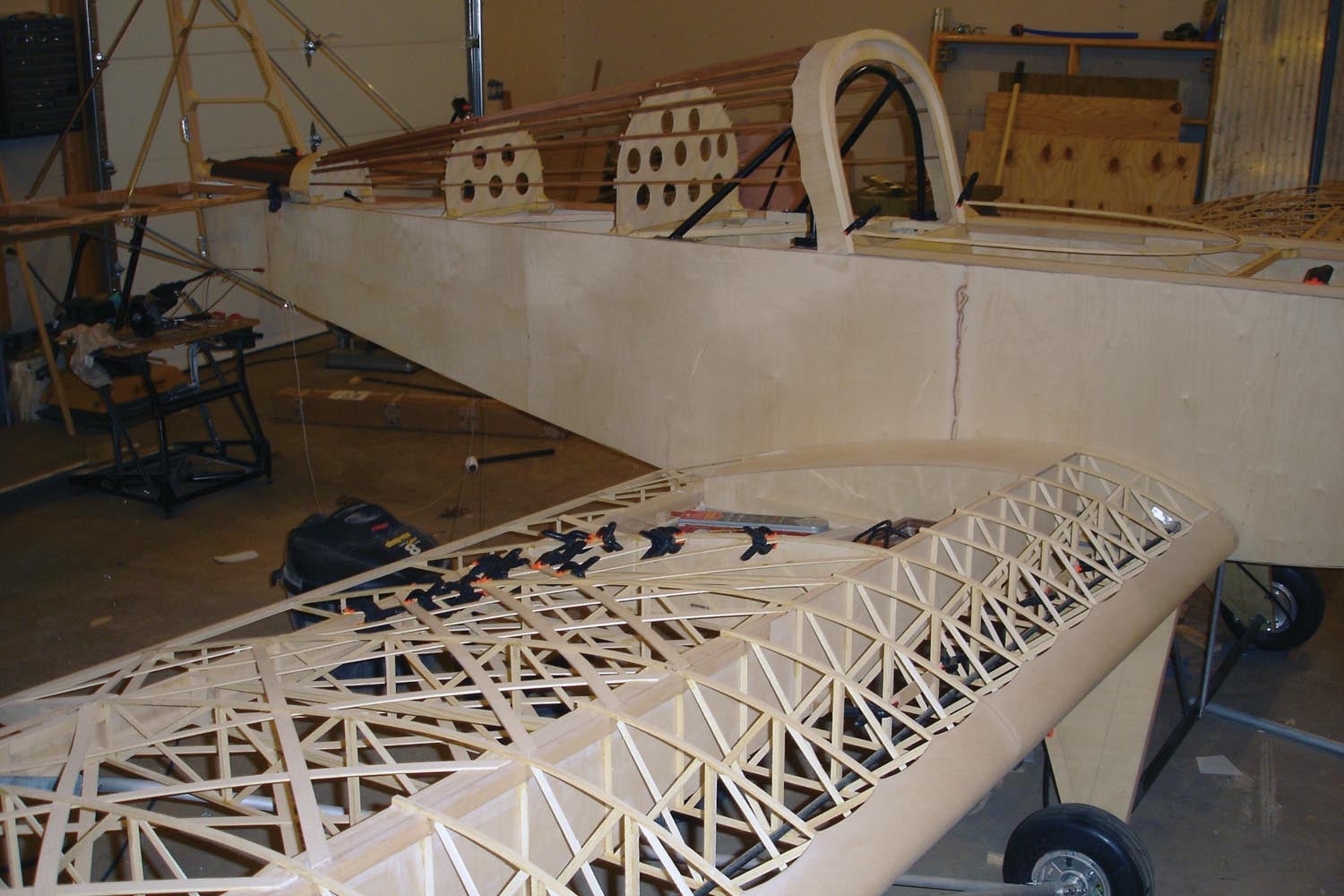
Born in 1994 as a Part 103 ultralight, the Avenger had the standard 5-gallon plastic gas can behind the seat. After Hongisto evicted it, he built two fiberglass wing tanks, each holding 8.2 useable gallons. Three Facet electronic fuel pumps feed the engine, one for each tank and the third connected to the header tank Hongisto built into one of the tanks to ensure an uninterrupted fuel flow when in a nose-down attitude.
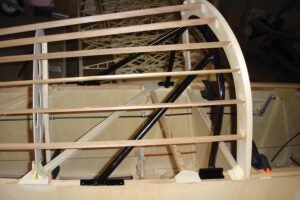
The air-cooled two-cylinder, four-stroke HKS 700E has been around for roughly 20 years, Hongisto said. “I’ve got 1186 hours on it,” and the 60-hp horizontally opposed Japanese engine “has a good reputation, and it’s reliable; there’s never been an in-flight failure recorded.”
When going somewhere, 5800 rpm gives him a 100-mph cruise at 3 gph. “When I’m flying with the Cubs and Champs and Chiefs around the Cloquet Carlton County Airport (COQ), it’s 2.25 to 2.5 gph at 85 mph.” The HKS turns a 66-inch Warp Drive prop. “I paid about $11,000 firewall-forward for the engine, hoses, oil cooler, and all the accessories. It’s a pretty expensive part of the airplane, but also one of the most important.” An EarthX lithium battery and electric starter brings the engine to life.
Building a set of streamlined wheel pants was the most challenging part of the project, and Hongisto is glad that he started working on them after the Avenger was flying. Based on the tire size, he shaped their outline in Styrofoam. “Trying to get that aerodynamic shape and then figuring out how to mount them was probably the most difficult part of building.”
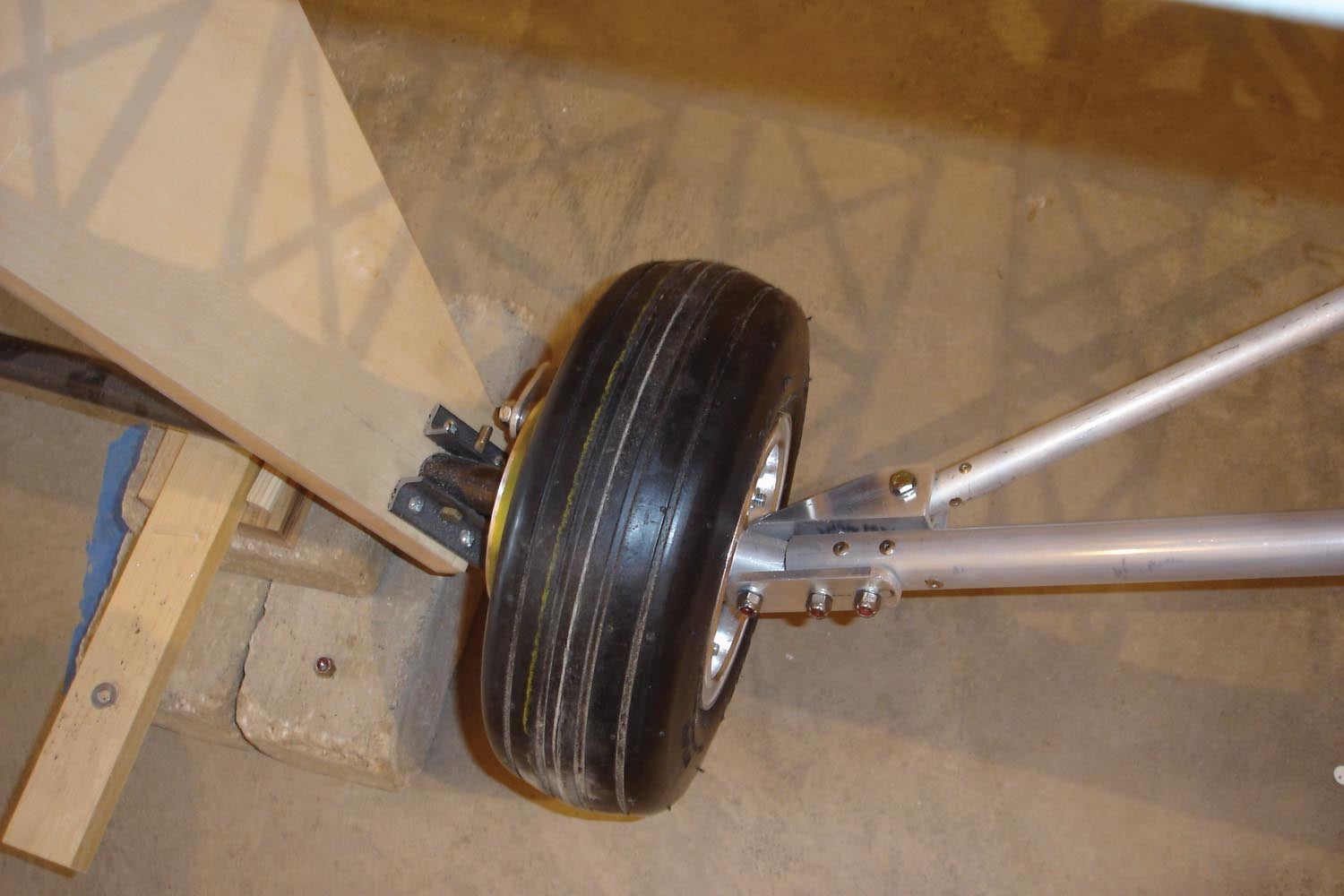
Building Books
When the first-time builder had questions, Hongisto turned to reference books. “I did call EAA on the fuel tanks and cowling, asking what type of fiberglass to use and how many plies or laminations to use.”
Hongisto spent a lot of time with EAA’s Wood Aircraft Building Techniques because he bought this material from local lumber yards. “If you go to a lumber yard and ask to see their aircraft wood, they just look at you like you’re goofy,” he said. “Because I was building my house, I was at the lumber yard a lot. At Menards, they’d see me pulling wood off the pile and looking at it carefully, and they’d ask, ‘Can I help you?’ After I said I was building an airplane, they said I was on my own.”
The EAA book taught him what wood worked where and what traits separated good lumber from bad. “I used Douglas fir, some hemlock, pine for the ribs and fuselage pieces when I could find them long enough and some cedar for the deck aft of the canopy. Dimensionally, Doug fir is 23-percent stronger then Sitka spruce; it’s also 26 percent heavier.”
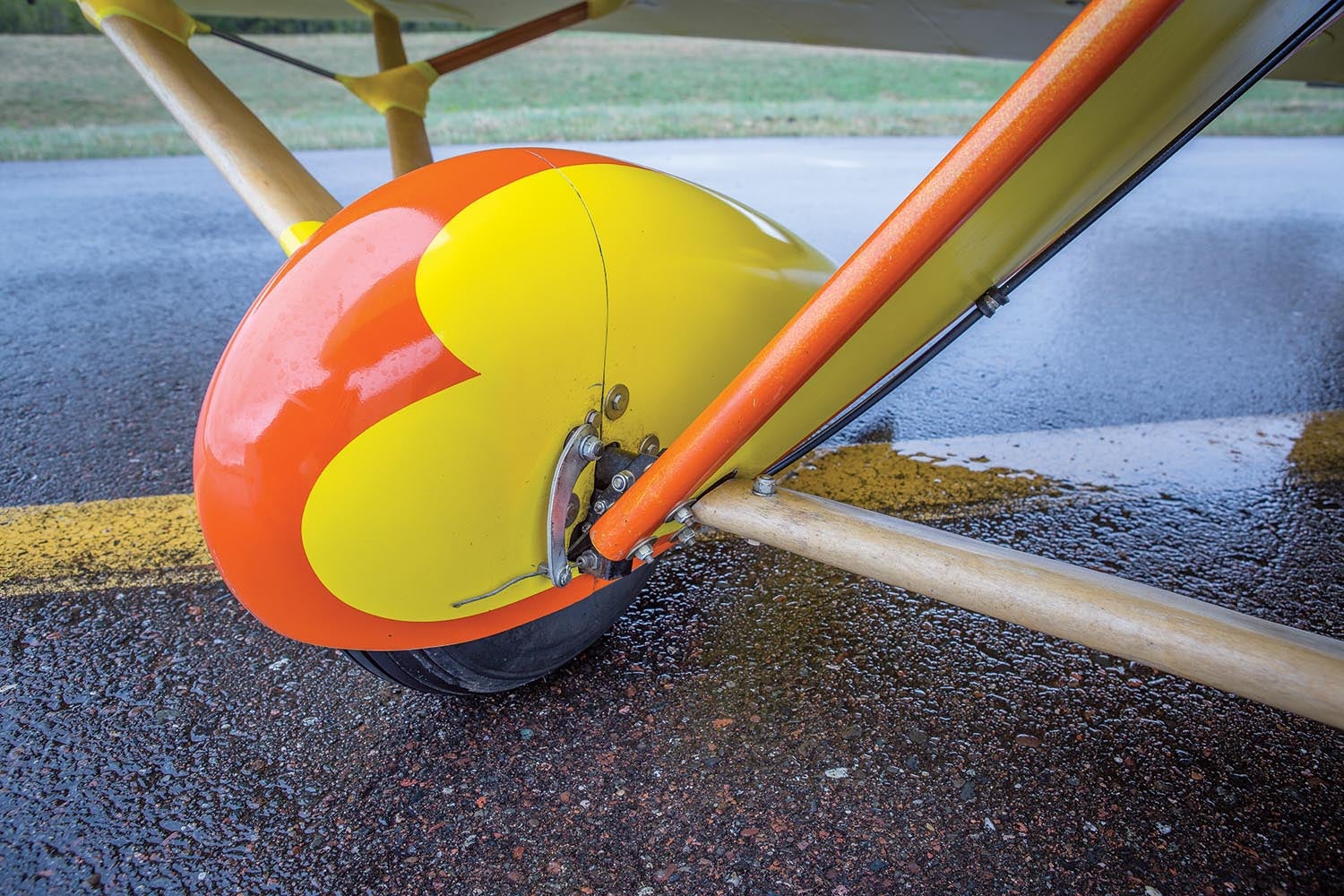
Hongisto bought the Avenger’s spruce wing spars from Aircraft Spruce & Specialty. “I didn’t want to mess with the integrity of the wings,” he said. Shopping for aircraft wood at the local lumberyard “is not something I’d recommend because it takes months and months” to find the necessary quality.
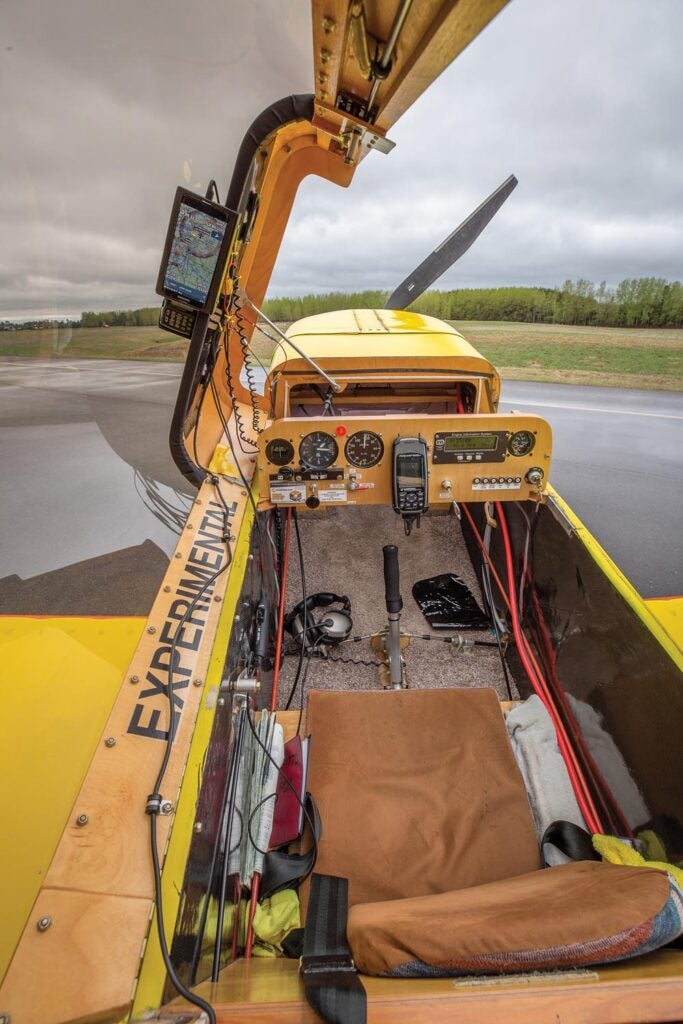
And then there is the empty weight to consider. “Putting the airplane on the scales was interesting,” Hongisto said. “It was overweight! It went from 150 to 520 pounds. Wondering if I’d built an expensive paperweight, I called EAA’s tech counselor the next day. I knew I had more horsepower than the original plans, so the power to weight ratio was okay. Looking at the g loading, if I decreased it from 4.4 to 3.2, I’d stay within the design specs. Explaining this to EAA, they agreed with my load reduction, and they said they get calls like mine all the time.” On the plus side, he noted that the increased wing loading makes for a smoother summertime ride.
The bigger fuselage and more than doubling the fuel capacity with the wing tanks added to the weight gain. So did the brakes. “The original plans didn’t have them. That seemed ridiculous, so I added simple mechanical toe brakes.” He also replaced the plan’s aileron and elevator push-pull tubes with push-pull cables. The stiff cables run inside a protective sheath, and the only exposed parts are where it connects to the stick and control surface.
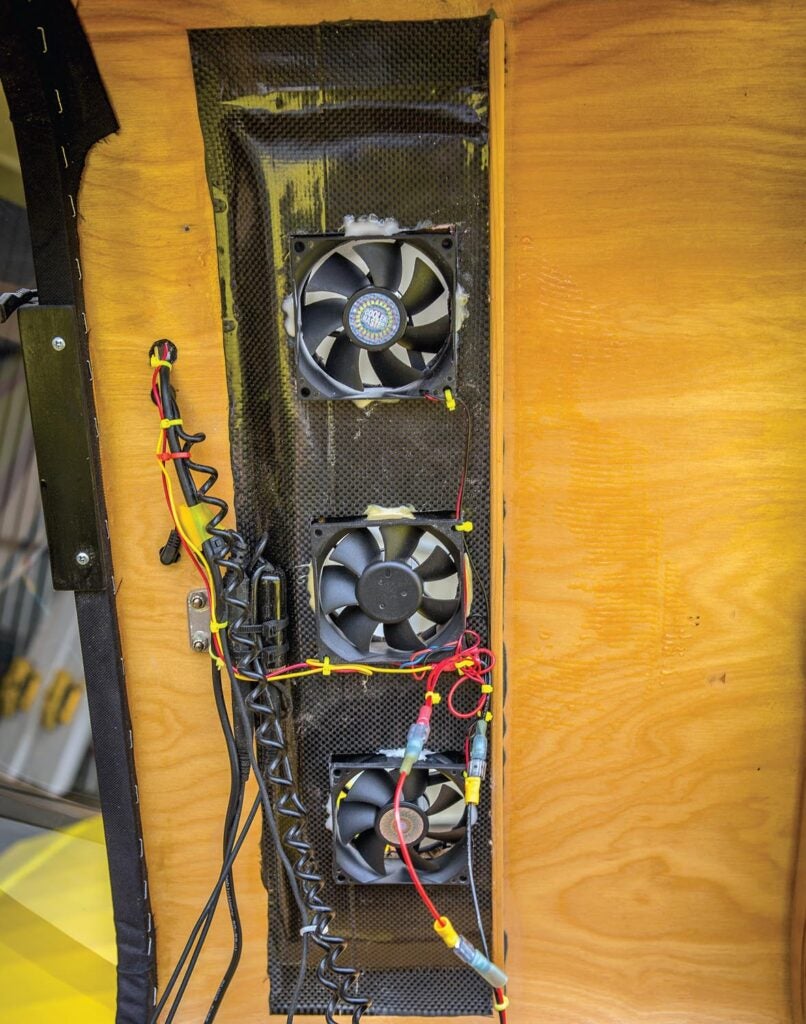
The instrument panel is VFR Spartan. A compass, altimeter, and airspeed indicator balance a GRT Avionics Engine Information System. “It has everything you need in a compact package. I installed it myself, and it’s worked perfectly since day one.” He wasn’t so lucky with the electronic fuel gauge. “It started picking up some interference from someplace, and it wouldn’t read right, so I abandoned ship’s power and built an AA battery bank to power it.”
To navigate, Hongisto mounted a handheld Lowrance Airmap 100 GPS to the panel, a handheld radio to the side, and on the glareshield, a cell phone running Naviator, a full-featured aviation app with GPS moving map. There’s no transponder or ADS-B, and no plans to install them. “I don’t fly in that airspace.”
Borrowing from the MiniMAX, Hongisto designed and built his own canopy. Yawning wide to the left, it provides easy access to the baggage compartment behind the seat. Today’s Avenger kits give builders an option of fresh-air flying, but flying without the canopy would make the turtledeck a huge parachute.
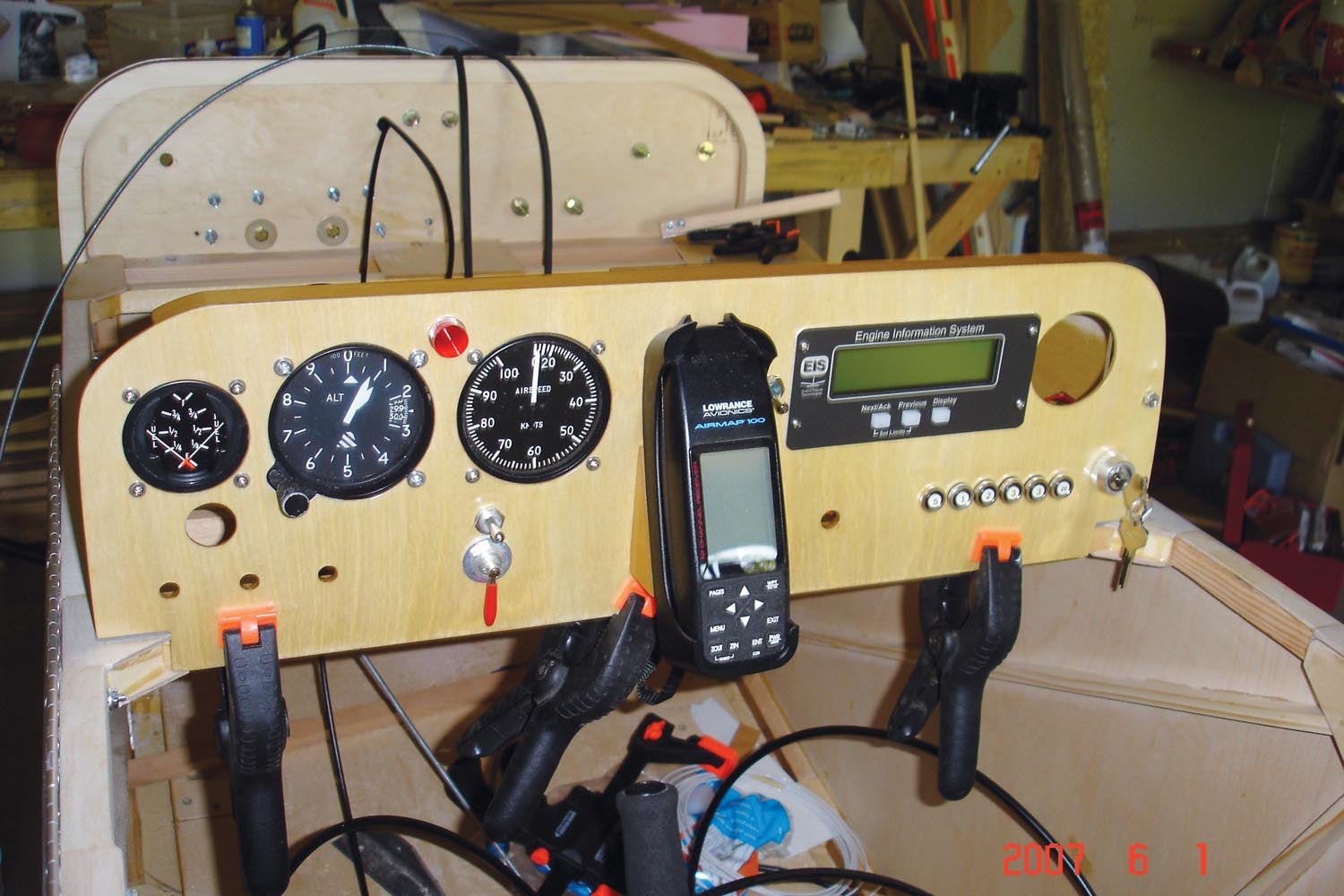
Hongisto dressed the Avenger in Polyfiber, and said, “I have a 75-pound paint job.” Designing the paint scheme was one of the hardest parts of the project. “What do I want this thing to look like when I’m done with it? I’m not an artist. What color, what accent stripes make it look like an airplane I want to be in?” He must have gotten it right, he said, because “when a bunch of us go to a fly-in, [the Avenger] always draws a crowd.”
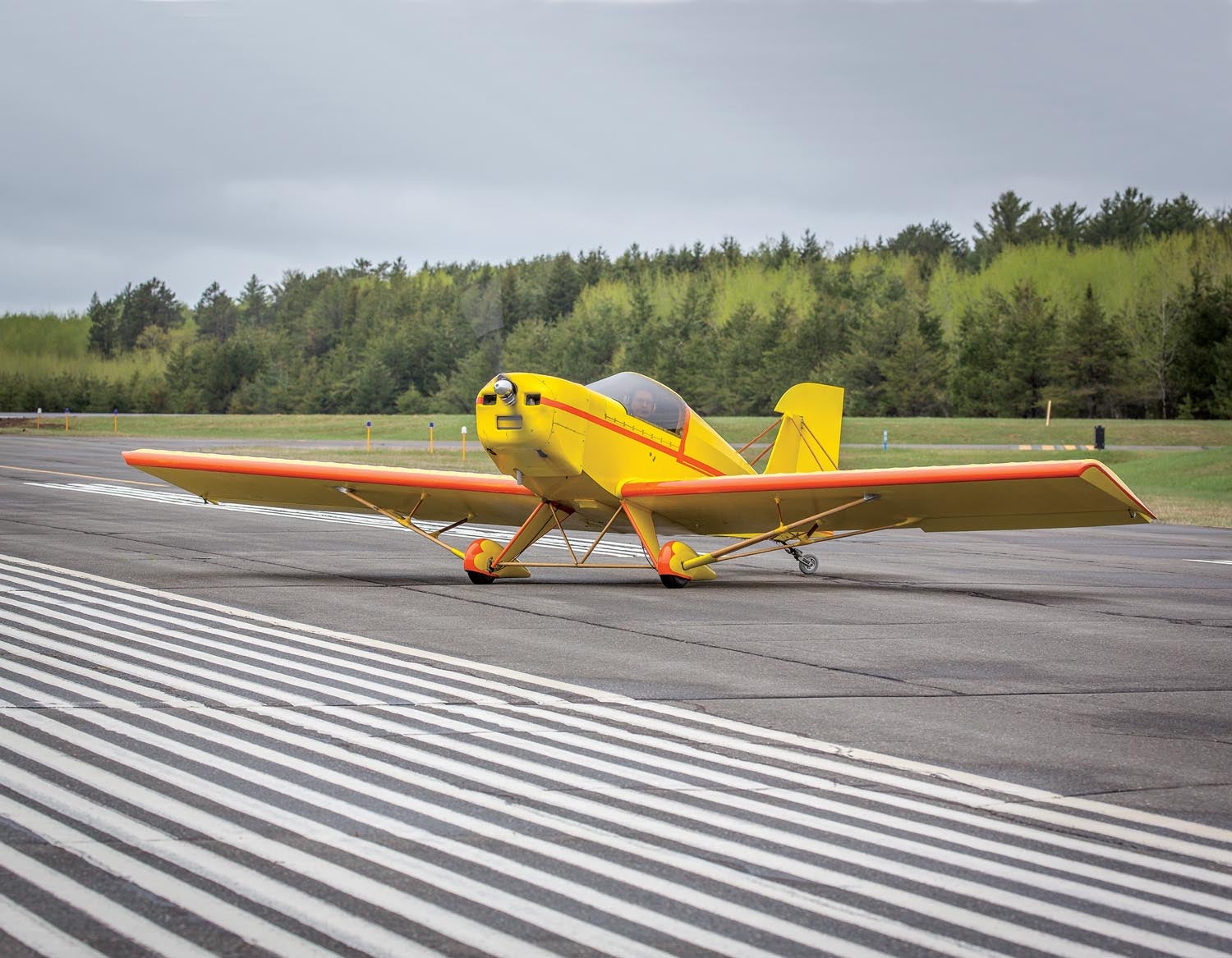
Year-Round Flyer
The Avenger made its inaugural flight in May 2008 at Cloquet. Hongisto prepared for the flight by earning his tailwheel endorsement in a Citabria, which was a tight fit for him. “I didn’t mess around with any high speed taxi tests because the airplane basically takes off and lands at that speed. After a series of normal taxi tests, I just went ahead and flew it. My first takeoff was a bit of a mess, but it was okay in the air.”
With a 40-hour Phase I test time, and a desire to make his first cross-county pilgrimage to EAA AirVenture Oshkosh 2008, Hongisto was up and in the air every morning at 0500, or whenever the sun rose. The neighbors could always tell when he was flying because the engine had straight pipes. At the 150-hour mark, Hongisto decided it was time for a muffler. His fourth design worked best. “My dad put a different exhaust on his Dodge diesel, and a tapered section of the old one worked in the space I had in my cowl.”
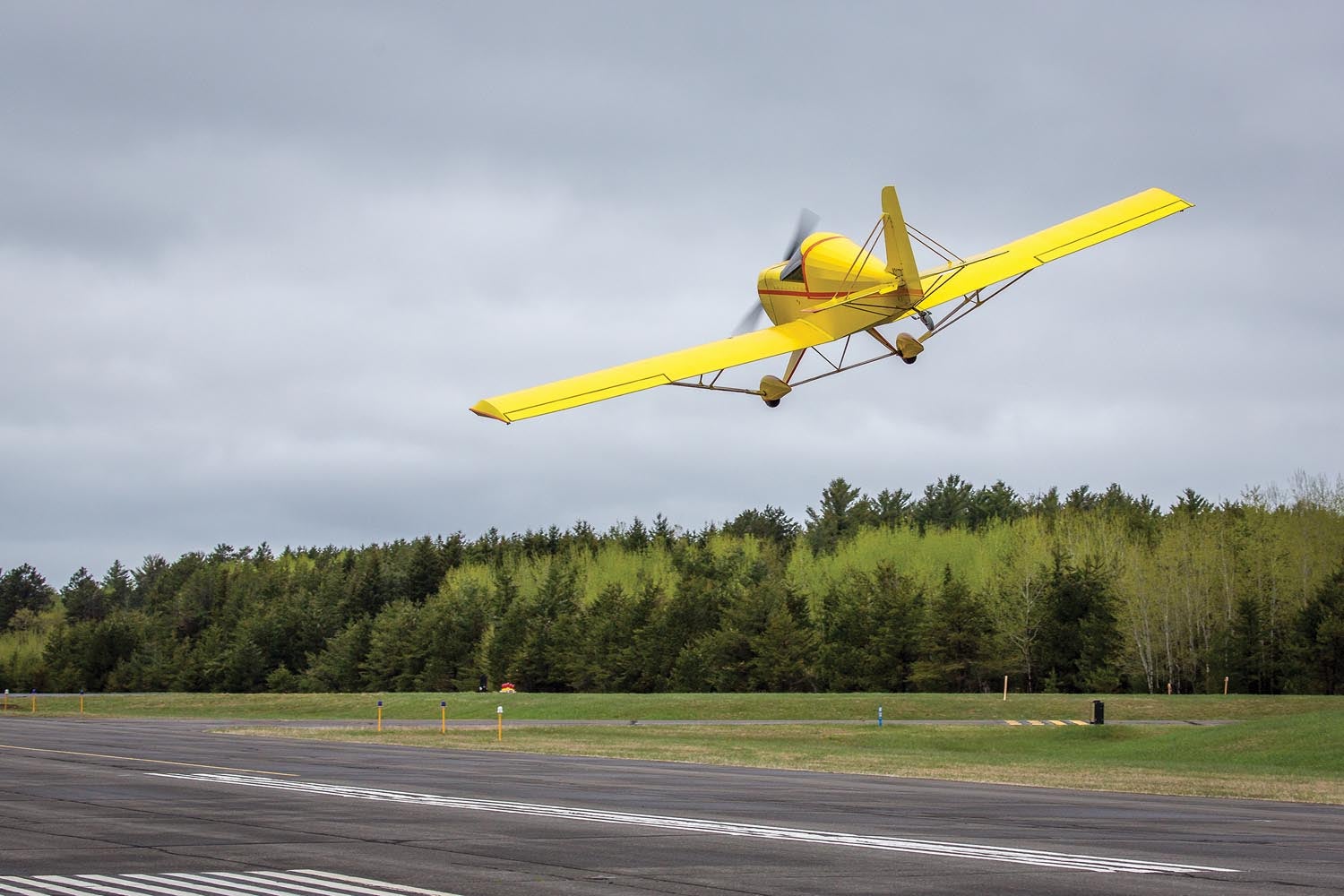
To eke out every mile per hour, Hongisto streamlined all of the round struts with fairings and solid pieces around the tail braces. “I’ve covered most of the strut junctions, and I made wing root fairings out of fiberglass,” and he sealed the aileron gaps. This effort increased cruise speed to more than 100 from 75 mph.
The fabric that covered the stringers on the slab-sided fuselage was a drumhead in the prop blast, so he replaced voids with three-quarter-inch Styrofoam and covered the cockpit sides with carbon fiber panels. “That did two things, it got rid of the drumming by stiffening the fuselage, and it insulated the cockpit. With cabin heat, I flew it to Oshkosh for the ski plane fly-in when it was 21 below.”
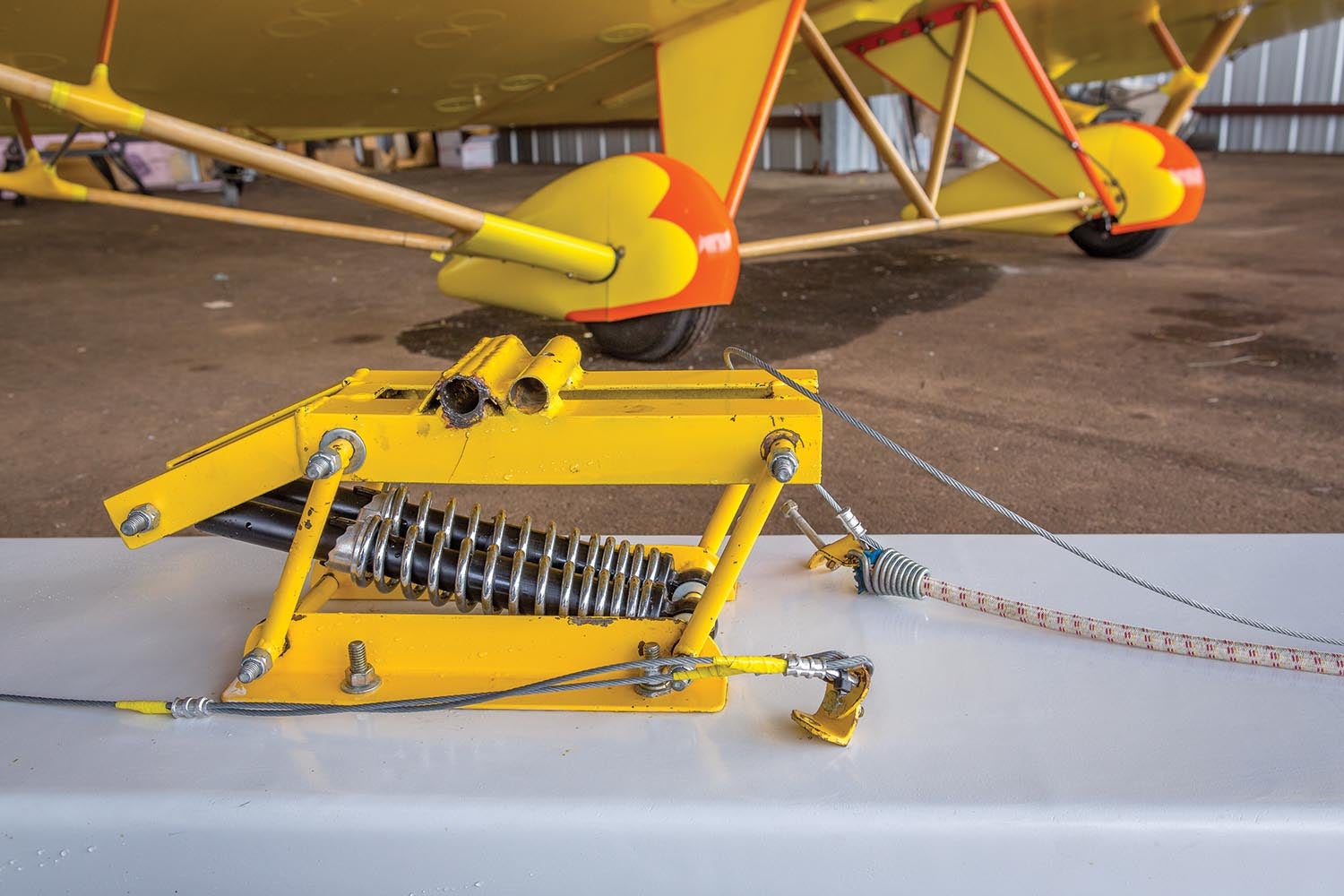
A computer cooling fan centered in the glareshield “got rid of most of the frost on the windscreen, but I was still scraping frost off the sides,” he said. “Putting fans on either side of the center fan solved that problem.”
When the Avenger was 3, Hongisto decided it was time to join a “bunch of buddies at the airport who flew their Champs and Chief on skis—go flying in winter—I gotta do that!” So he bought Advanced Composite Techniques, Zeke Smith’s book on the structural aspects of foam and fiberglass.
He made a 2-foot-square test panel with two plies on top and bottom. For a static load test he jacked up the front of his truck, and “it held up and didn’t delaminate.” After removing his truck, “to simulate landing on snow I beat on the bottom with a hammer, and I couldn’t delaminate it, so I decided that it would probably work as skis.” The 15-inch by 5-foot snowboards cost him 15 mph.
With its Douglas fir struts, the Avenger is a rigid-gear airplane. “The tires are its only suspension, so I normally just fly from pavement,” Hongisto said. Snow is a different matter, so he built trailing-link shock absorbers into the skis themselves. “It gives me about 3.5 inches of travel, so it is smoother landing on skis than on tires,” and it increases the ground clearance of the gear’s trapeze strut, which is why the skis are 4 inches thick. The skis’ only real downside is that changing the gear is a daylong process that involves disconnecting the bottom struts, changing the axles, hoisting the whole airplane up, and putting the wheels and brakes back on.
Around the time he finished the Avenger, with his eye on the airlines, Hongisto was working on the necessary ratings and certificates. Now 52, he’s a CRJ-900 captain for Endeavor Airlines out of New York. “The CRJ has a lot of adjustability for short and tall pilots, but it is the best seat in the house with a view you’ll not get in any other job.”
The building bug is starting to nibble again, “but I find myself with no time to do so,” he said. “I’m flying four days a week, home for three, and I have a 1,000-mile commute.” So he’ll bide his time in the Avenger, flying year-round with the Cubs and Champs and Chiefs and making his annual 3-hour cross-country camping trip to Oshkosh.
The airplane has been eminently reliable. “I’ve had very little go wrong in 1186 hours. I broke a tail spring when I was trying to pull it up on a snow bank when it was on skis, and the tail was bouncing up and down.” Every flight is a reward, a measure of satisfaction earned by achieving something he has always wanted to do—and doing it on his own. “I took the time and did it, and did it successfully.”
Photos: Mike Hongisto & Scott M. Spangler.
“…when assembling a kit, builders cannot make many changes.”
According to who?
According to the greatest aviation authority ever, Mr. Gream Reeper. Play around too much with a plans built design and its aerodynamic and aeronautical fine-tuned qualities and M. Reeper will sue you. Problem is, he always wins.
Thank you for a very enjoyable read. Regrettably I never had the time or space to build. So I owned a Dakota and a CT for many years.. Now at 77 insurance is impossible to get. Fly while you can.