Experimental Amateur Built Aircraft are all about “recreation and education” and both can continue for as long as you are involved in the field. I have been working on airplanes for over fifty years, and hold an A&P certificate, but it wasn’t until recently that I finally had the time and resources to begin to learn how to weld. Sheet metal, composites, wood, tube and fabric—all of these I had encountered and needed to learn along the way, but welding had eluded me. So this year I settled in with a TIG machine and a bunch of scrap, slowly going from burning holes in my scrap to actually making reasonable training welds. I progressed onto making shop equipment, tools, and now dare to make the occasional (non-critical) airplane part. But I am still learning.
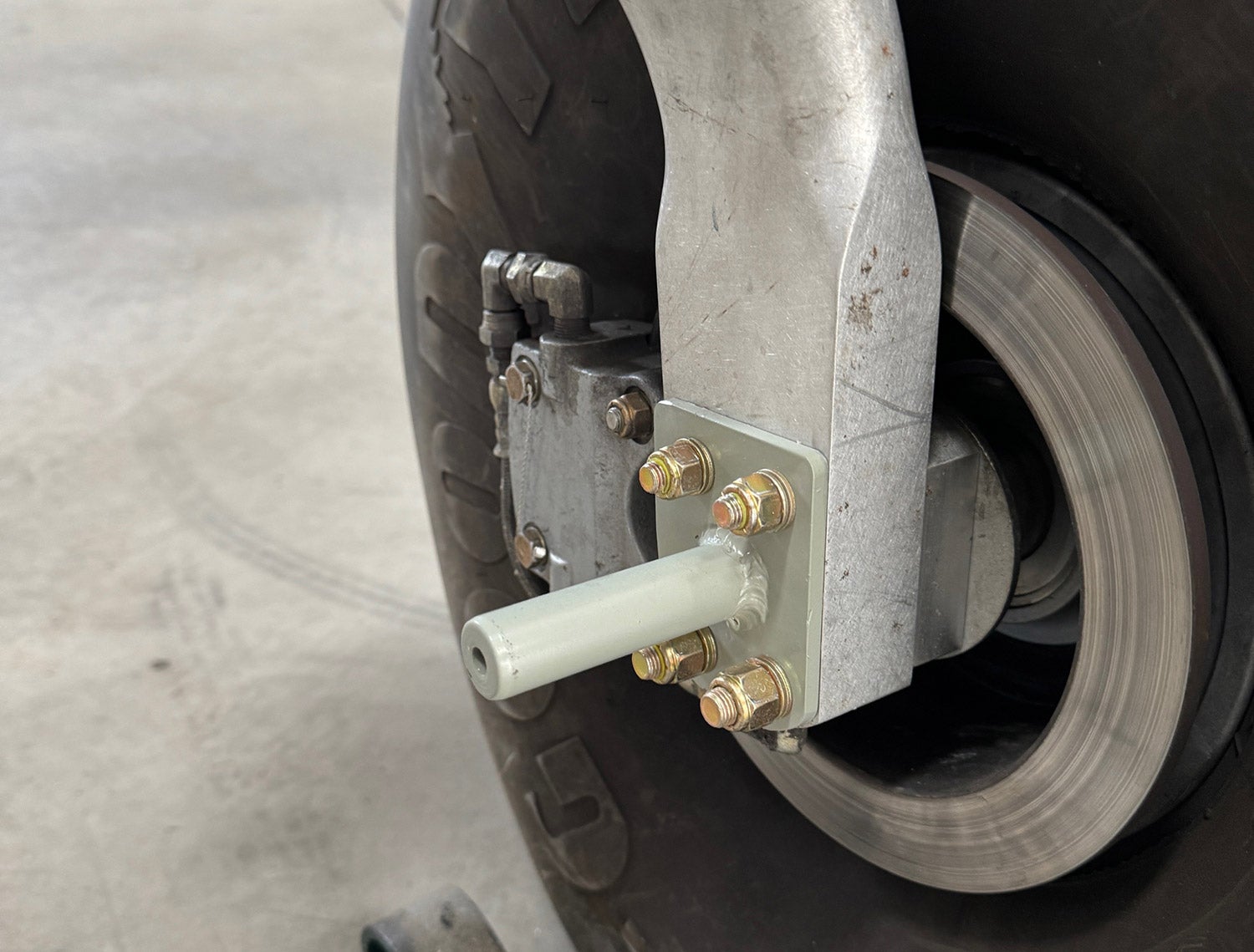
My most recent project was some jacking points for our big metal bush plane. For some reason, the design incorporated no good way to get the plane off the ground for wheel and tire maintenance- that reason probably being that it was original designed as a floatplane. Over the years, I have maintained it using straps wrapped around the gear legs and lifted it with an engine hoist. I wanted to use a simple hydraulic jack, but there was no place to “grab” down by the axle – hence the need for some jack points extending inboard from the axle attachment nuts.
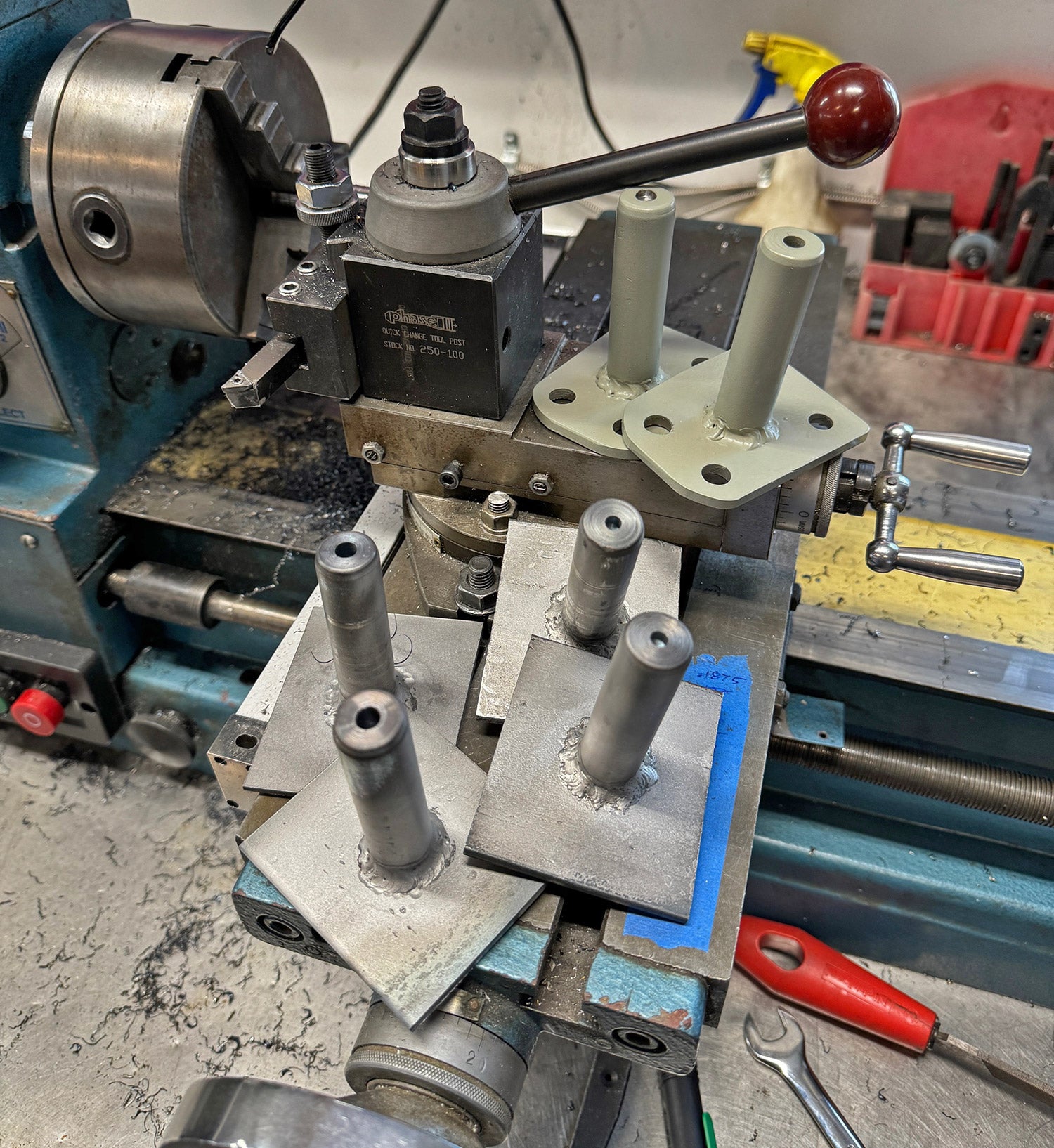
The project was certainly educational, and those of you with lots of experience welding will chuckle at my expense when I say that the first set taught me that I had to tack weld the shaft to the base plate before welding around it—yup, it ended up crooked. the second attempt I did the tack welding, but didn’t have it clamped tight enough, so it still moved a little, and once again, it was crooked. On my third set, I figured out a way to truly clamp the shaft and baseplate to the welding table so they couldn’t move when I tack welded… and yes, when I chucked up the welded part in the lathe to clean up the base, the final pair were nice and true! Of course, the parts for each assembly (the shaft and the baseplate) had to be shaped on the lathe each time before welding, so I got to practice my machining skills numerous times as well.
In the end, I didn’t just end up with the jack points (which worked out really well in lifting the airplane) – I also ended up spending educational (and entertaining) hours in the shop perfecting my machining and welding skills which is what this endeavor is all about