Have you ever had project creep? The gradual cumulation of ideas and what-ifs that makes a straight path meander is all but guaranteed to add time and complexity. But it can also lead to a much better end result. Witness the evolution of Allen Floyd’s Long-EZ, Excalibur.
Allen, who hails from Erie, Colorado, fell in love with Burt Rutan’s Long-EZ when he was working the line at an FBO in high school. He bought the plans to build the airplane of his dreams soon after graduation in 1983. Life got in the way, as it does, and it was years before he began construction. The build itself took more than 13 years and included the design and incorporation of multiple modifications and enhancements. While some are improvements that have been proven by previous builders, others are unique to Excalibur.
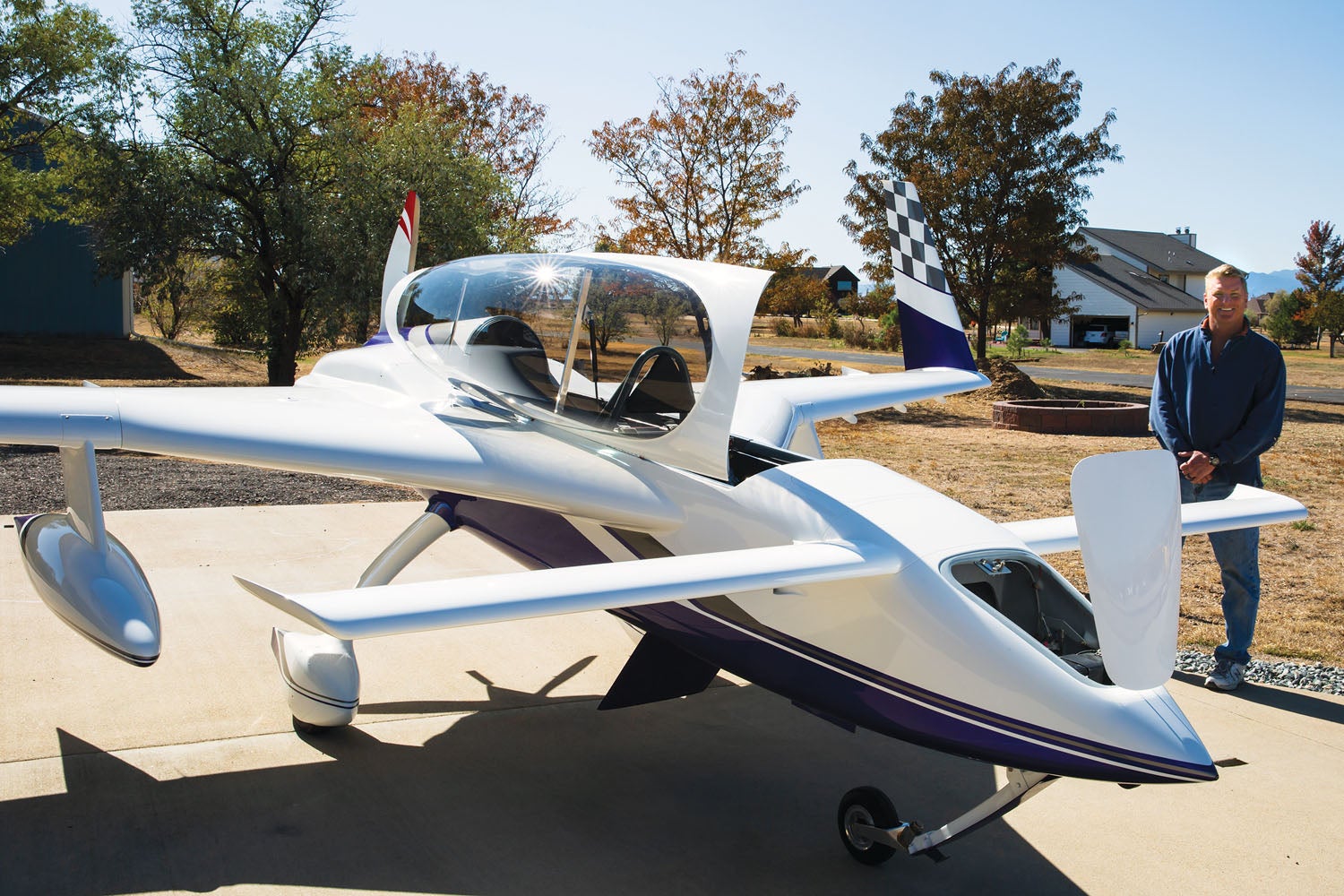
It didn’t help that partway through the build Allen discovered the Sport Air Racing League, and a dedicated focus was placed on squeezing every bit of speed out of the airframe. Narrowing the focus to create the fastest aircraft he could added at least two years to his total build. Everything had to be cleaner, smoother, lighter. Many parts he previously built were reconstructed with his new goals in mind.
While there has been a great deal written about the Long-EZ, we’re going to focus on the details that make Excalibur such an outstanding example of craftsmanship.
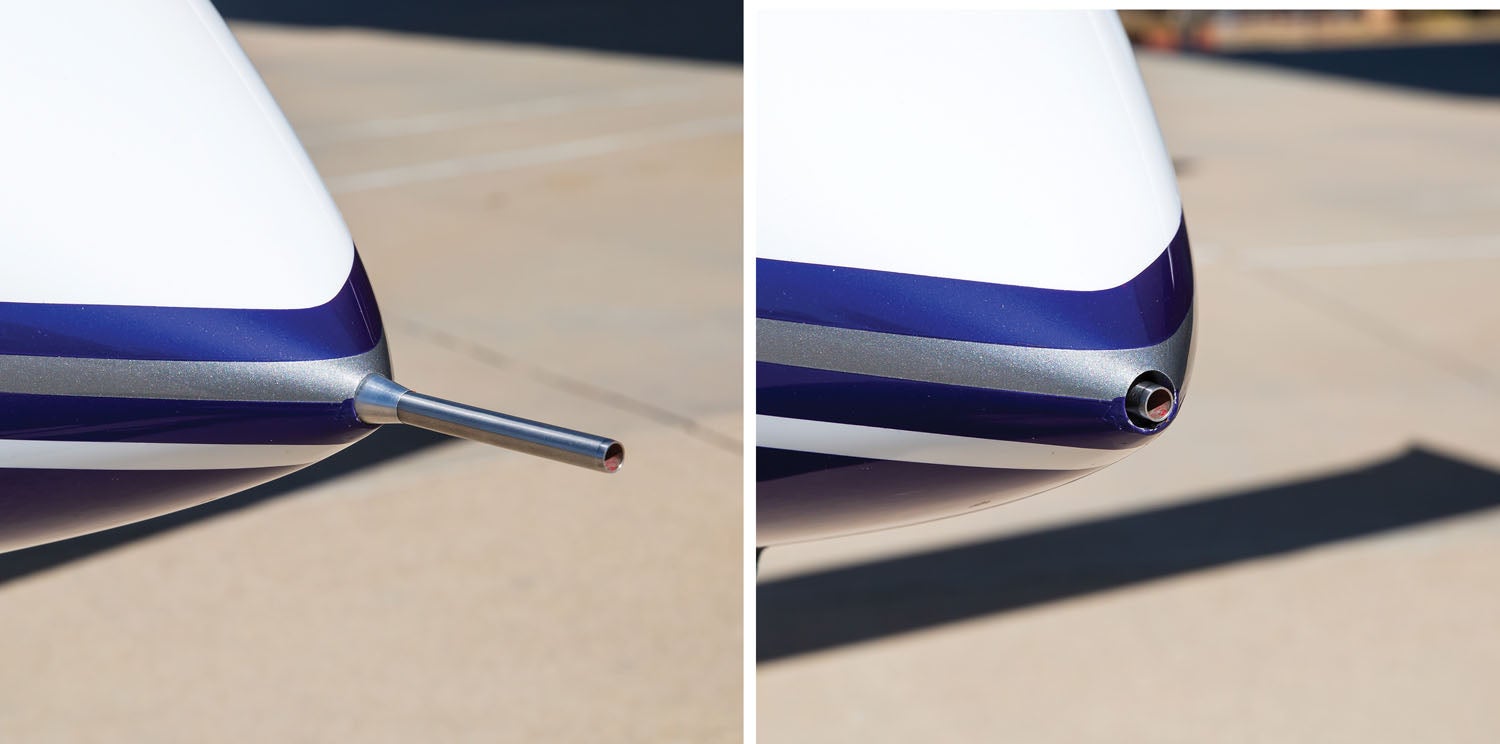
Nose Job
Allen describes Excalibur as a Long-EZ NG, with NG standing for “next generation.” Look carefully at the nose and you’ll see that the snout is longer than standard. This streamlines the airflow, reduces drag and helps with the CG, given that Excalibur has a larger, heavier engine than the original plans.
At the very tip is a retractable heated pitot tube. You might be thinking, why a retractable pitot tube? Well, this is Allen’s design to prevent someone from tripping over the pitot tube when the aircraft is parked in the “kneeled” position with the nose gear retracted and the nose on the ground. This known hazard typically results in damage to the pitot tube, but on Excalibur the problem is eliminated.
Within the nose is the avionics bay, accessed through a large hatch with a remotely actuated latch. Underneath the nose is a carbon fiber “bumpersnoot” pad to protect the nose in case of a gear failure.
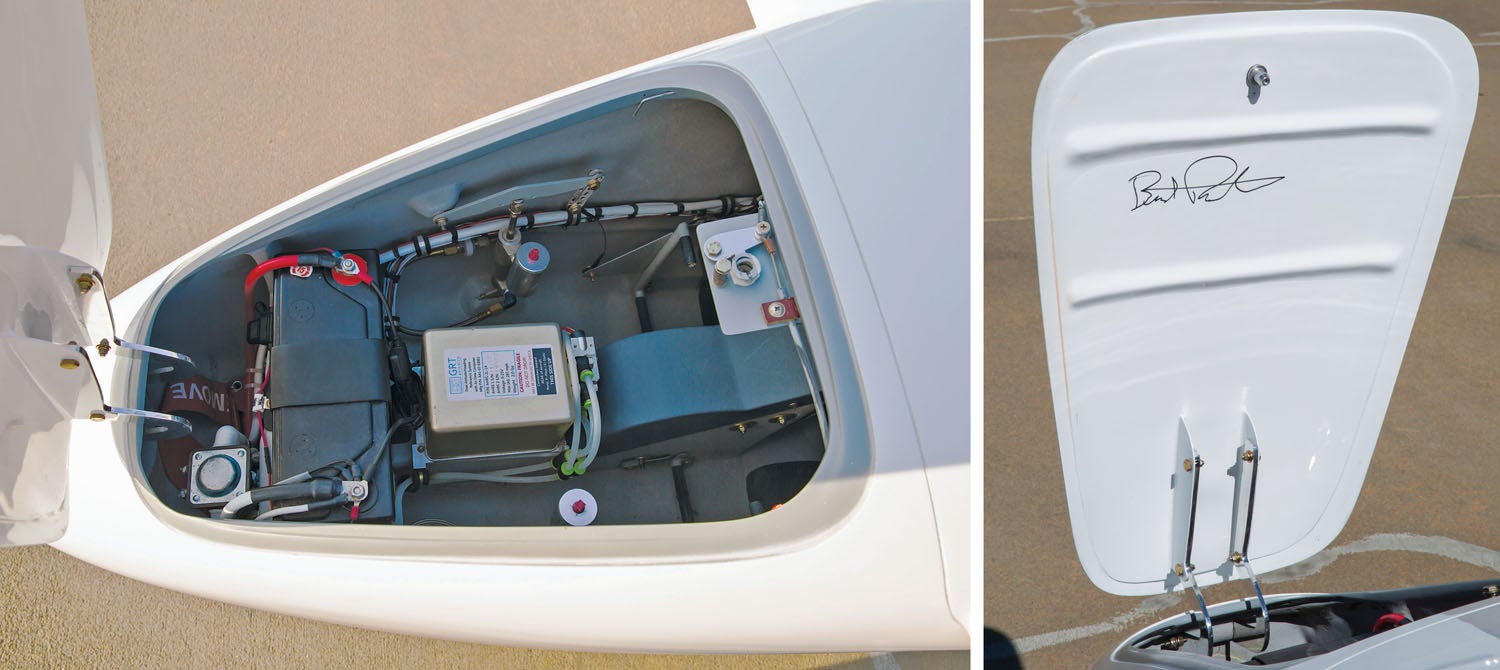
As you move further aft, you’ll notice that the retractable nose gear has enclosing gear doors. Usually a Long-EZ doesn’t have these doors. This area without the doors creates an area of turbulent airflow. Turbulent airflow is not your friend in a sleek airframe design as it increases drag and reduces potential airspeed. Closing in and smoothing the underside of the nose eliminates this drag, and there is now clean, streamlined airflow all the way back to the engine cowl inlet. Right behind the nose gear doors is a retractable LED landing light (again designed with drag reduction in mind), followed by a belly air brake.
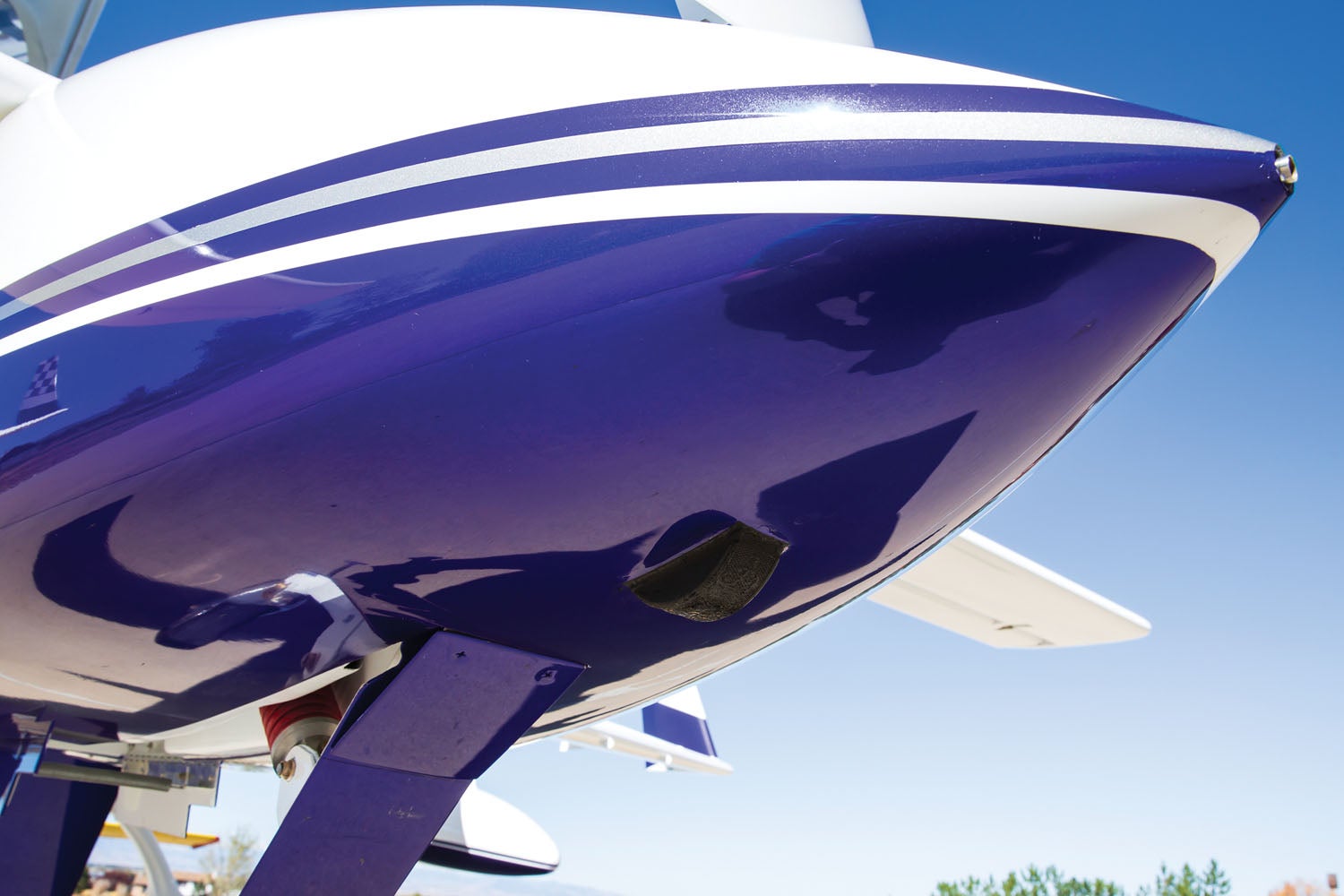
More Airframe Mods
Central to Allen’s aerodynamic efforts is the lightweight engine cowling. It was fabricated using the vacuum bagging technique and utilizes carbon fiber to drastically minimize weight. It took about 18 months to design and build the cowl as well as the associated baffling. Everything was designed and set up to maximize cooling while minimizing the associated drag. As you’re likely catching on, each and every aspect of the plane was evaluated and designed to contribute to this goal. None of the drag reduction would be effective if the air going into the NACA vents wasn’t flowing smoothly and cleanly.
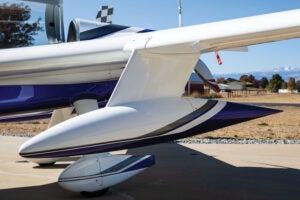
Next to the ailerons are flow fences, which increase aileron effectiveness and also shift the CG slightly aft, unloading the canard and adding speed. There are similar trailing-edge fences on the wings. The winglet tips are reflexed to maximize the aerodynamics, and the main landing gear is encased in custom airfoil fairings that go down to low-drag wheel pants. Out at the tips the lighting incorporates—I know it’s surprising—low-drag LED navigation lights and strobes.
There usually isn’t much room for storage in a Long-EZ, which makes long cross-countries and overnight trips difficult. Allen overcame this issue by installing hard points in each wing for attaching removable external pods that can carry 35 pounds each. While they aren’t plumbed for fuel, they do allow the Long-EZ to carry more than a toothbrush during travels.
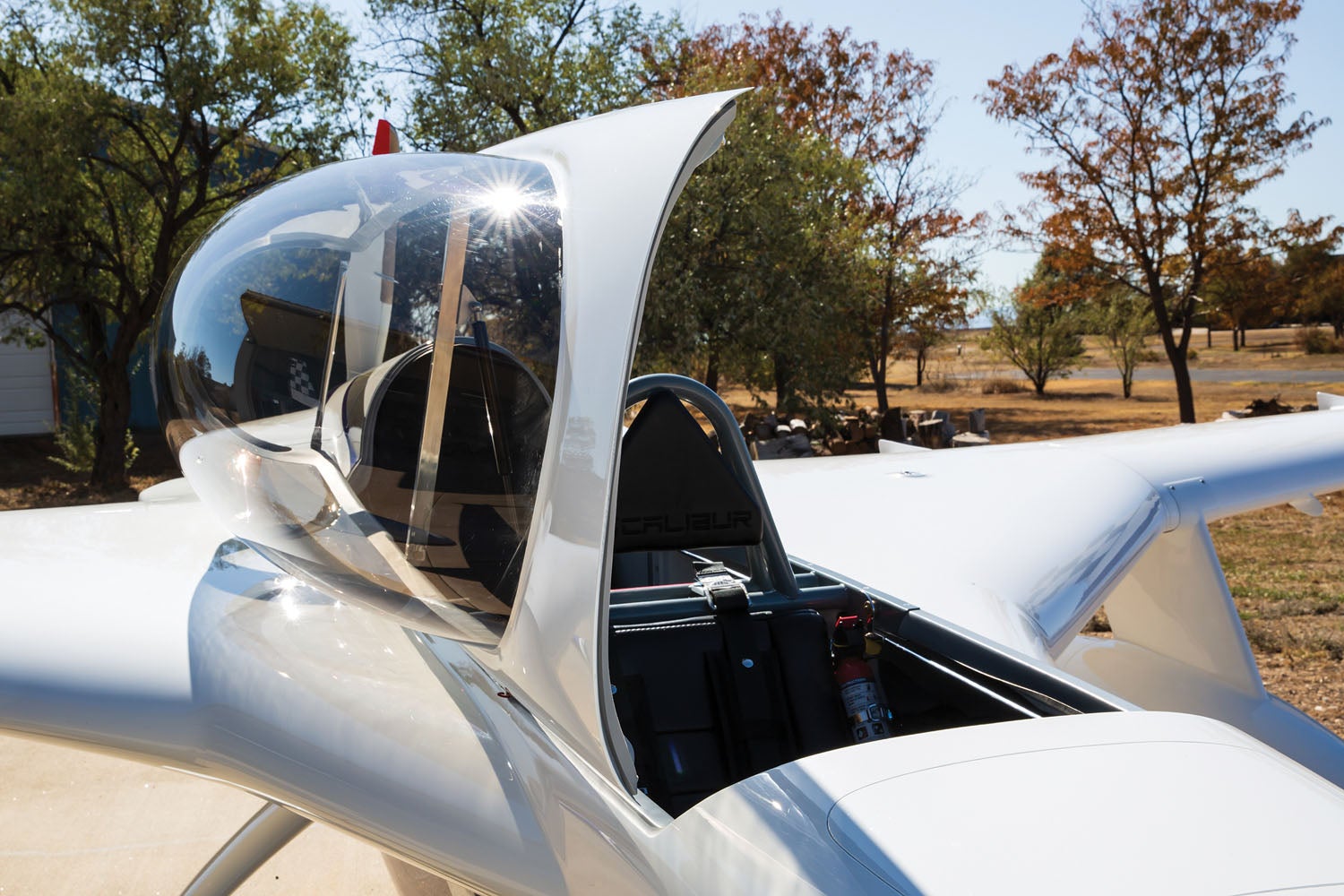
Canopy, Cockpit and Avionics
The canopy was produced by Todd’s Canopies and is embedded into a carbon fiber frame. It sits lower and has a smoother transition, a look that Allen describes as “slinky,” which creates a smooth flow aft.
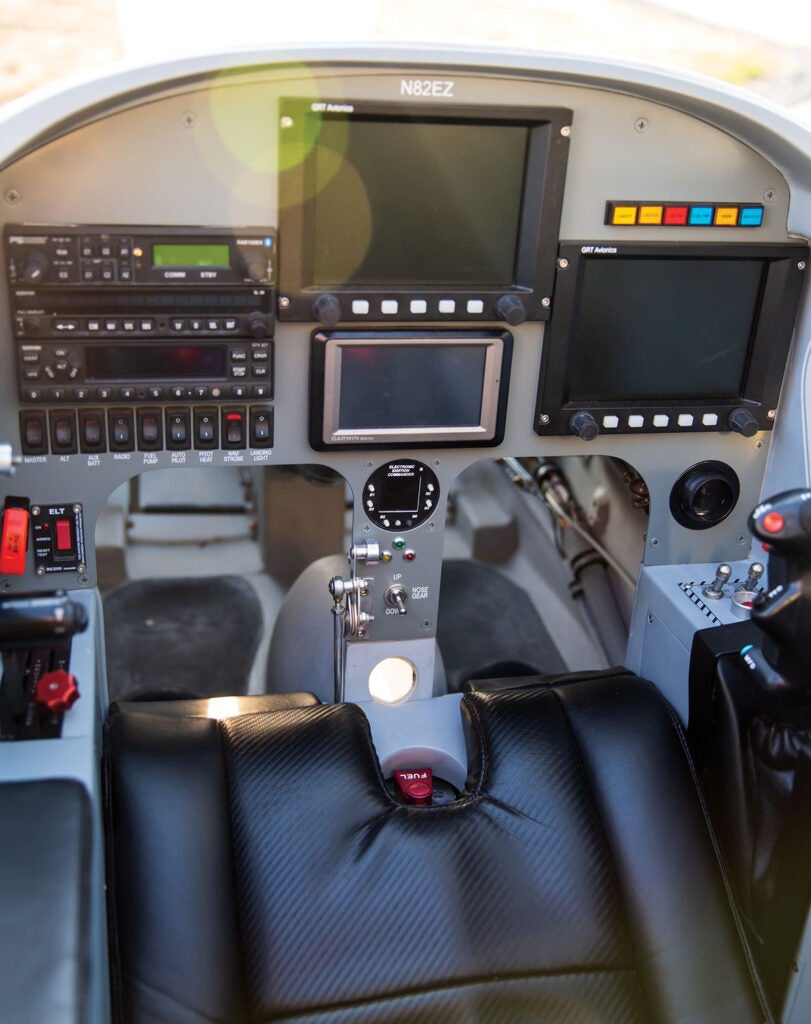
magnetometers and triple-redundant GPS units.
The cockpit was inspired by exotic racing cars and is very nicely appointed. The avionics suite includes a Grand Rapids Technology (GRT) electronic flight instrument system (EFIS) with primary flight display (PFD) and multifunction flight display (MFD) along with dual AHRS/magnetometers and triple-redundant GPS units. The ergonomic IFR panel is set up to utilize hands-on throttle and stick (HOTAS) functionality. There’s also a two-axis autopilot to allow for enjoyable cross-country flights. Fuel levels are easily readable in both the digital systems and the mechanical sight gauges. Nicely rounding out the cockpit is XM weather/radio, heated lumbar supports in the seats and side consoles that are molded to give more hip room.
One thing that is commonly overlooked by engineers and builders is what maintenance will look like down the road. Allen designed the interior panels and consoles as well as the inspection panels to be easily removed, simplifying future maintenance chores.
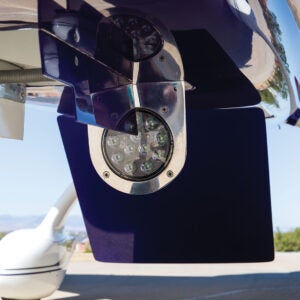
Another thing Allen didn’t overlook were safety features that would protect him in the event of an accident. The cockpit is surrounded by a custom-made 4130 steel roll cage structure with padded headrests. Sticking with his focus on the details, the canopy is secured with a rotary latch and all the controls have precision bearings giving the control stick a silky smooth feel.
Aside from the steel roll cage, there are numerous other safety modifications that Allen incorporated under the composite skin. The nose gear has a manual extension backup, and the structures inside the nose are protected by a multi-layer Kevlar skid pad. The seats are made with energy-absorbing foam and the pilot and passenger are strapped in with four-point Hooker harnesses. The electrical system is wired through a Vertical Power module that grounds each switch but doesn’t have actual voltage going through them. The electrical system is mostly solid-state and has a backup battery system. Another nice touch that combines safety and weight savings is the firewall being manufactured of titanium.
Engine and Prop
Under the cowl is a Lycoming IO-360-A1A with Airflow Performance fuel injection, NFS pistons with 10:1 compression, dual electronic ignition with in-cockpit telemetry and timing curve management to take advantage of changing timing for more efficient fuel burn. There’s also a crankcase vent recovery system, custom carbon fiber cylinder baffles and custom exhaust with low-drag profile exit tips. The latter blends custom rectangular outlets into the cowl design to create less drag and produce more power.
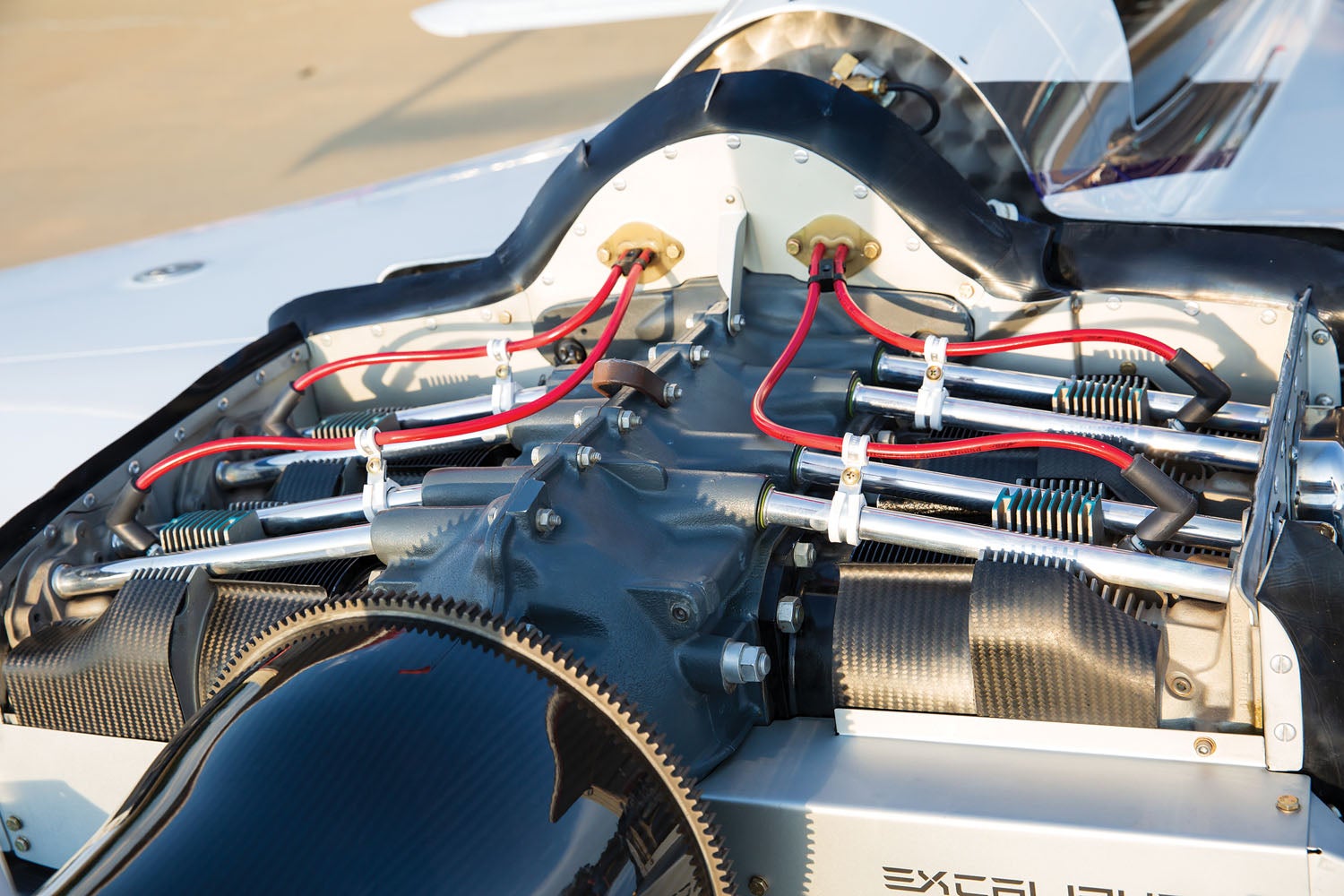
The three-blade composite propeller is custom and personally designed by Craig Catto, owner of Catto propellers. When developing this prop, Craig built a GoPro camera into the hub so he could watch the airflow over the blades. This led to the development of small airflow fences midway down the propeller blades. Those, combined with the carbon fiber pressure recovery spinner, greatly help to minimize the drag usually associated with pusher props. The prop is mounted using Belleville washers to keep a constant tension on the bolts regardless of temperature or humidity.
Aside from Craig Catto, invaluable assistance needed to complete Excalibur came from composite expert Burrall Sanders, owner of Freeflight Composites at Meadow Lake Airport in Peyton, Colorado.
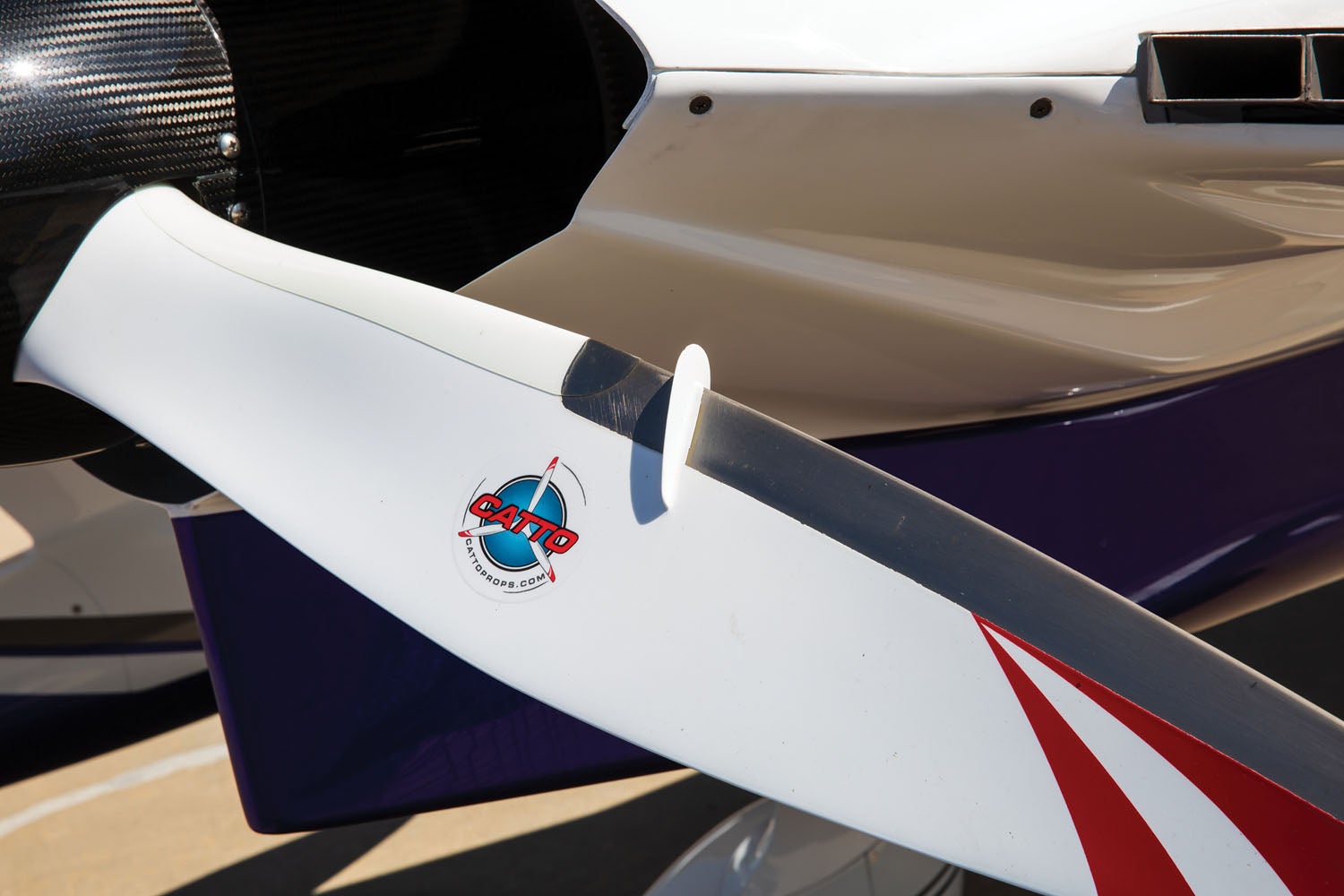
AirVenture Accolades
Allen debuted Excalibur at AirVenture Oshkosh in July of 2019. His efforts were recognized and rewarded with not only the Grand Champion Plansbuilt Gold Lindy but also the Stan Dzik Memorial Award for Outstanding Design Contribution. It is believed that Excalibur is the first aircraft to ever receive both awards in a single year. Being quite a character, Allen, tongue-in-cheek, quips that since AirVenture 2020 was canceled, Excalibur is the only aircraft to ever hold both of these awards for two consecutive years!
After more than 3226 hours of building, at the end of what must have seemed like a never-ending project, everything was finally completed. The end result is an aircraft that is safer, higher performing, fuel efficient and aesthetically pleasing. Allen will admit to cruising at 215 knots at 2700 rpm, but he won’t divulge an absolute top speed. After all, he’s got to save something for the races.
Photos: Julia Apfelbaum.
Very nice plane
To Jonathan & Julie Apfelbaum I love the changes you made to the design of your Long EZ .It is beautiful inside and out and I love your paint scheme. The Long EZ I’ fly has the Lycoming 0 235 and that is a little week on power. My brother built it and flew it in 1988. when he first flew it. I have been flying it for 9 years Now at the age of 75 I find it a lot harder to get in and out of then my cherokee. I still love the Long EZ’s..
Very nice article I have always wanted a long EZ but when you have a wife and kids that want to go when traveling to the islands in the northeast. After 50 years of flying and working on aircraft I am hoping to find one I can afford even if I only have it a few years before I get too old to fly .
No retractable landing gear hmm… a nice as the rest is that might be the last major advantage he could gain.
But then he would loose about half of your fuel capacity.