
One of the many decisions presented during the swap from my old O-320 to the new, more powerful Titan IO-340 in my GlaStar was what to do about an oil cooler. Mine had the typical eight-row cooler mounted behind the aft, left cylinder and it worked fine for the 320. Differing opinions had the 10-row as a suitable upgrade, but Bill Genevro of Airflow Systems (maker of oil coolers and ducts) strongly advocated for a jump up to a 13-row 2006X cooler fed by a 4-inch duct.
Since the cost differential between the 10-row and the 13-row coolers was minimal (less than $100) and the ducting costs only slightly more, it seemed a reasonable choice. What’s more, I had to engineer a new cooler mount anyway, so the difference was small there, too; the bigger cooler is about 3/4-inch longer (or taller, depending on how you look at it).
I had been warned that the bigger cooler might make the oil too cool by the time winter arrived, though I was happy with the overall setup during the summer and fall, when the oil temps were rarely more than 190° F in cruise. Also, since the big cooler helps provide so much thermal inertia, my peak oil temps tended to be in cruise rather than during the climb.
Then winter arrived. Despite closing the ground-adjustable cowl flap all the way, my flights in November and early December resulted in peak oil temps below 160° F, and that’s just not warm enough to boil out the condensation caused by combustion. Genevro warned me that I might have to put a restriction in the air duct for winter flying. He was right.
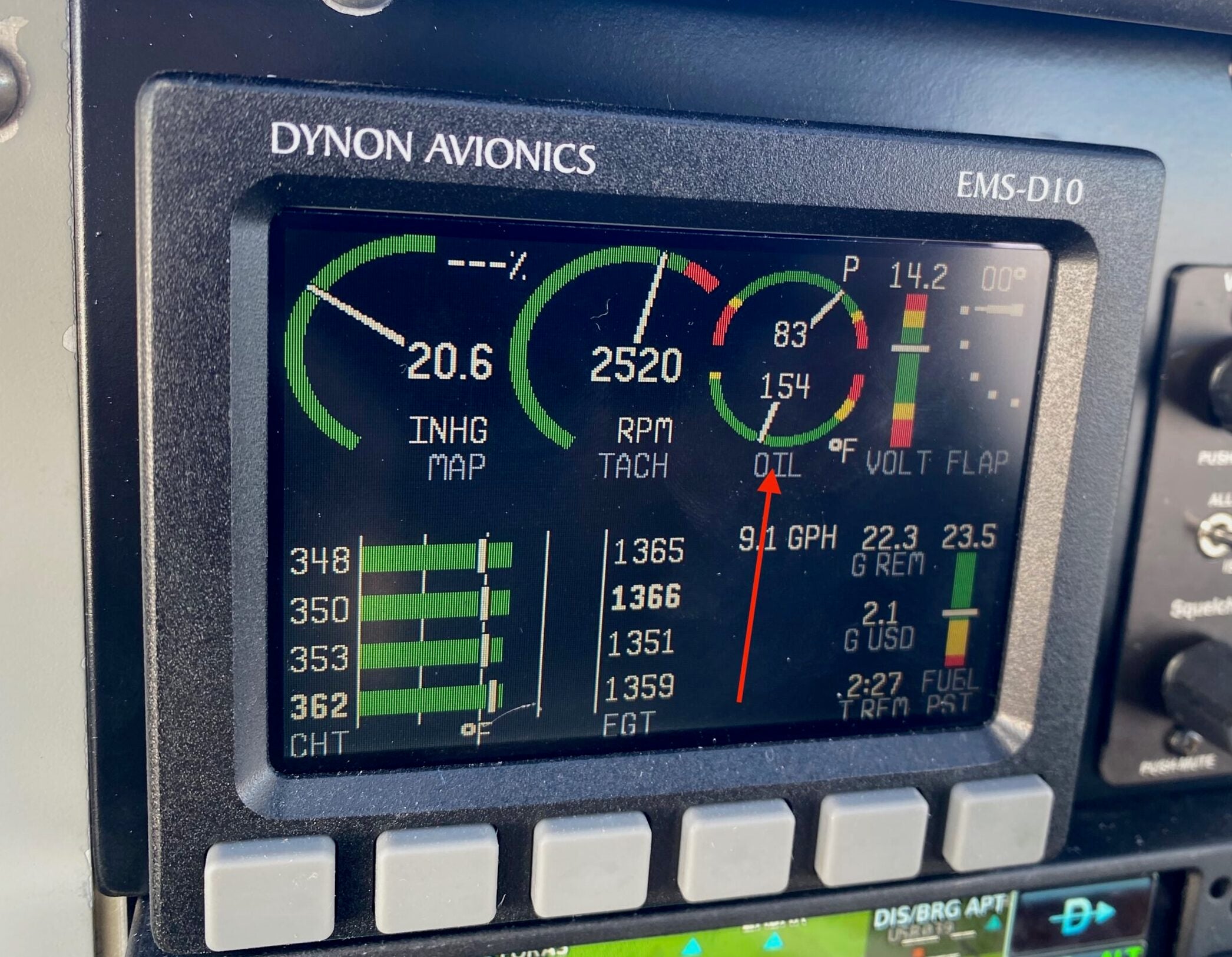
The good news is that installation duct valve (Airflow part number ASOCD-45-13BV) was fairly easy. I had a locking push-pull control from a previous project to complete the install—in fact, we’d mis-ordered a control for my Sportsman back in early 2006, and this unused control had been hanging about in my spares pile since then. (Useful motto: Don’t throw anything away!) It took about 2 hours to complete the installation, which also involved trimming the 4-inch SCAT tube.
In flight, the results are terrific. In the cool temps of an Oregon late fall/early winter, I’ve found it best to start, taxi and even complete the takeoff and initial climb with the duct fully closed. It’s not a perfect fit, so no matter what, some air flow is getting to the cooler. The oil comes to temperature a bit more quickly and the ideal temp of 180° F occurs sometime near the end of a long climb (usually above 8000 feet) or soon after leveling off in cruise and leaning the mixture. (I do trim fuel in climb, then typically fly lean-of-peak EGT in cruise.) It’s easy to find a setting that gives me 180-190° F, and I haven’t found the need to mess with the control very often in flight.
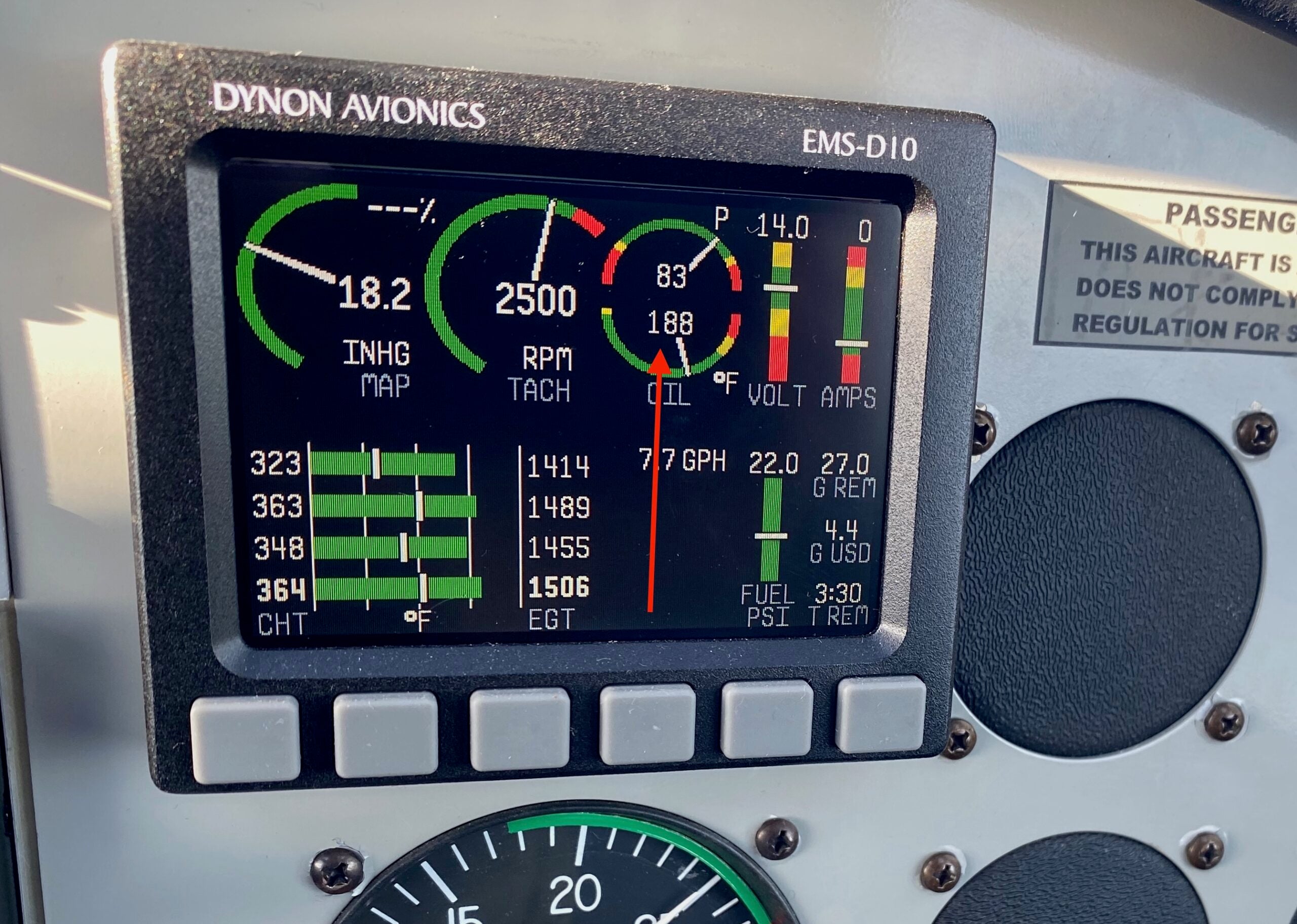
So far, I have not had the duct more than half open in cruise, and typically close it fully for the descent. Since the cooler borrows air from behind the #4 cylinder, I expected there to be some difference in cylinder-head temp distribution on that side with various settings. Nope. The position of the valve doesn’t seem to influence CHT at all; it stays rock steady over the course of a 30-minute test, which should be long enough to note a difference. Unchanged, too, are cruise speeds—my airspeed indicators didn’t change a single knot.
We weren’t sure if I was going to need the duct valve when this project started but with hindsight, I would have installed it from the get-go. The price difference between the 4-inch “doghouse” duct and the one with the valve is about $80. It’s not nothing, but a small fraction of what the overall engine replacement cost, so there’s that.
In theory, the oil-cooler bypass valve (the vernatherm) is supposed to manage temps, but it’s a far less than perfect design that never fully shuts off the flow to the cooler. And that means some other way to handle a cooler sized for worst-case summertime temps is called for, and this particular application fit the bill.
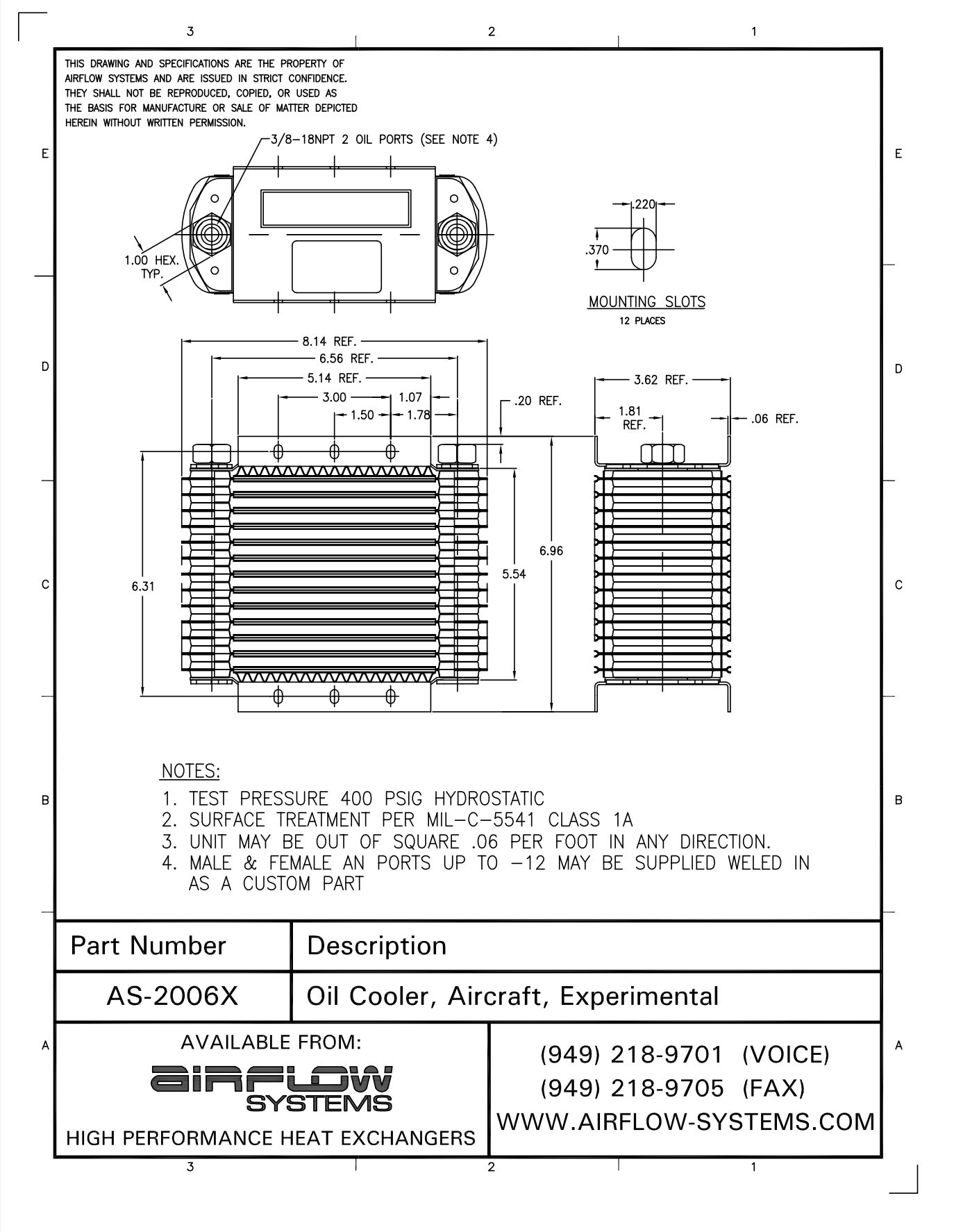
That looks very cool. Heh-heh….
Would Vic Syracuse say we need a washer and cotter pin on the right-hand end of the pin through the control lever? Yeah, I know – installation wasn’t complete at the time the photo was taken.
I should have put a disclaimer in the photo that it was of the not-quite-finished installation. There is, in fact, a washer and cotter pin securing the wire clip.
I have been using this since many years on my GlaStar with a Lycoming O-360. Our oil cooler is oversized and with a fully opened butterfly valve the oil temp never arrives to 176 F. The only occasion when I left it fully open was at 1000 ft over the Dead Sea in Israel in May OAT 110°F.
Very-Very useful part highly suggested.
This looks like an excellent solution for those of us in the far north. I love the idea of having an inflight controllable damper much better than the typical screwed on ones, or worse, foil tape that are traditionally used. I know far to many pilots that have made emergency landings to uncover their oil coolers during an unexpected warm snap mid winter. Thanks for sharing this.
Continental states they like oil temps of 220 degrees on the 0-200. Startled me to lean for every gallon of gas burned a gallon of water vapor is produced.
My Tri Pacer had cooling issues in the winter. A $2.00 piece of galvanized steel sheet bent strategically and slipped over the oil cooler did the trick.
By the way..same thing for my Tailwind W10.
Hi,
I am flying a RV8, Lycoming O-360. I am breaking in the engine . At take off cht goes to 400 F until I reduce to 2100 rpm.But oil temp is at 140 F , rather low . At this temp there is no flow through the oil cooler. Hat could I do to warm the oil?
Thanks