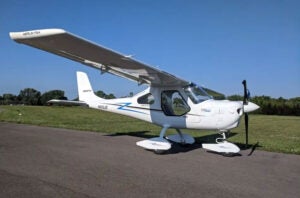
First introduced in Europe in 2013, the all aluminum single seat enclosed cabin Merlin LSA has sported a variety of engines, including a Rotax 582, a specially built four stroke V-twin and even an electric motor. In fact, the Merlin airframe has served as a test bed for all kinds of propulsion and aerodynamic innovations. At AirVenture 2023, Aeromarine chief designer Chip Erwin even showcased a Merlin model with twin propellers embedded in the wings. Erwin promises an even bigger surprise at Oshkosh later this month: a common-sense hybrid propulsion system for the Merlin.
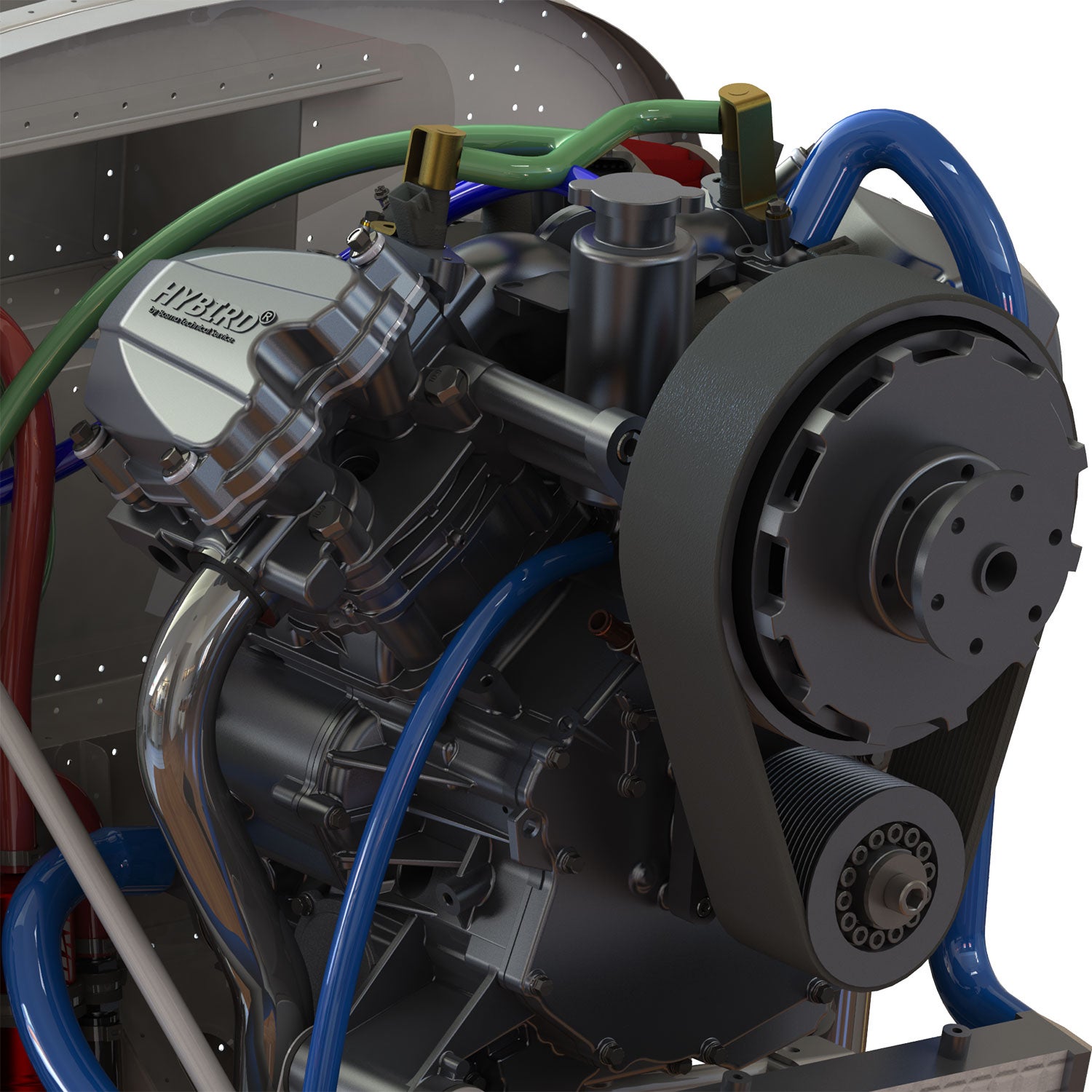
Erwin, who has done work for the Air Force Research Lab in Dayton, Ohio, has developed a parallel hybrid drive system for experimental aircraft that utilizes an electric motor to add to thrust generated by a piston engine during takeoff and climb, but shuts down during cruise. He points out that a major limitation of all electric aircraft is the need to lug around a heavy battery capable of providing thrust for a limited period of time. The advantage of a piston engine is that it can provide the reduced thrust necessary for cruise flight in a lightweight package, utilizing a relatively small amount of fuel.
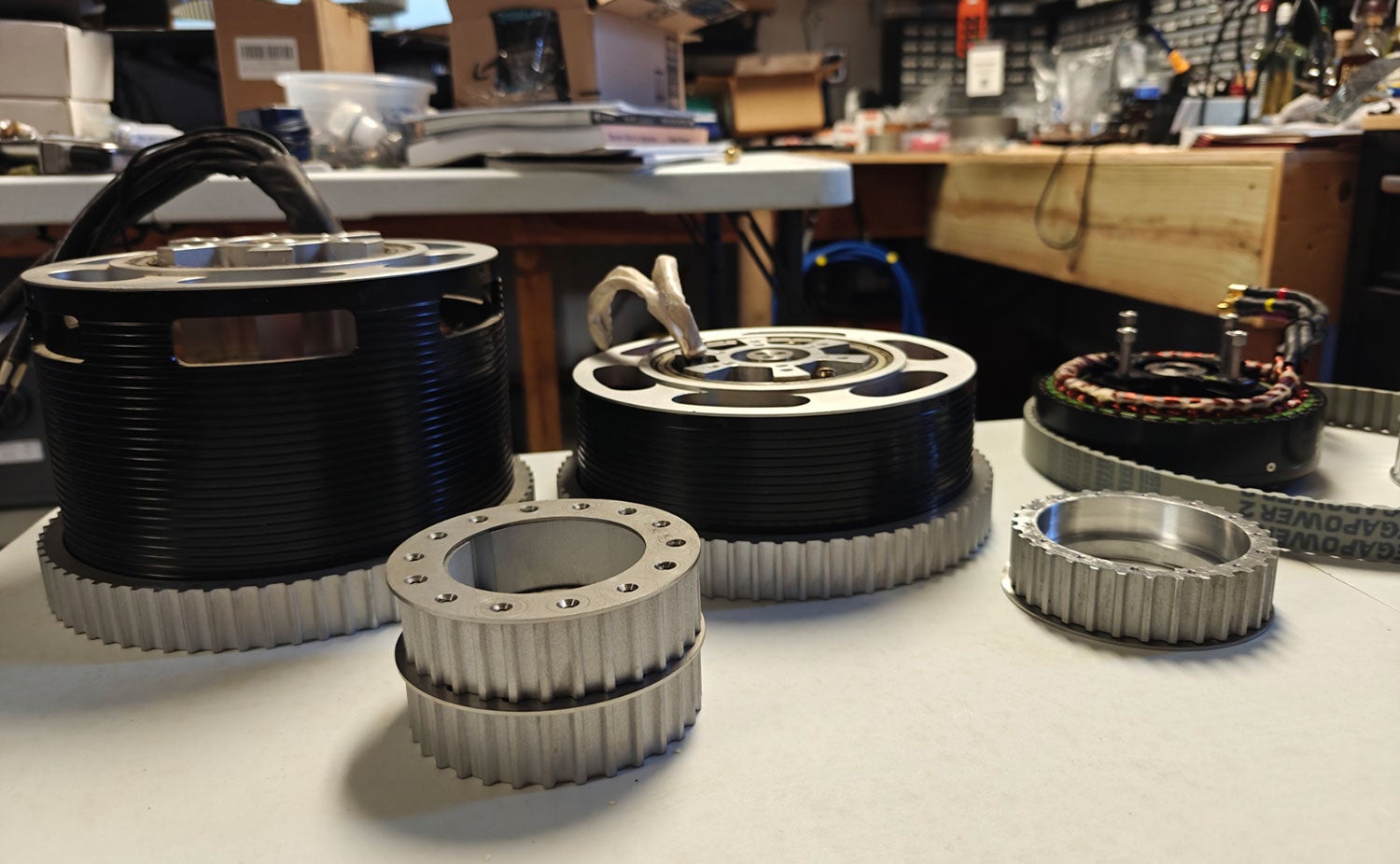
A typical flight plan for the hybrid system would entail using the piston engine, supplemented by the parallel electric motor, to provide the combined thrust necessary for takeoff and climb. Once a cruise altitude is reached, the electric motor would be shut down and cruise would be accomplished on the piston engine alone. Erwin points out that the electric motor would be free wheeling during cruise flight (through the use of a sprag clutch) resulting in insignificant drag to the thrust produced by the piston engine.
This parallel thrust setup allows the use of a smaller, lighter and more fuel efficient piston engine, supplemented by a light weight electric motor. Since the electric motor is only used for takeoff and climb, it utilizes a fairly small battery, which is recharged by the gas motor during cruise. Formula One race cars have been utilizing this concept for the past several years, using a small but powerful electric motor to provide added torque for critical phases of each race such as the standing start and powering out of corners. The Formula One batteries for these cars are the size of a laptop battery, discharging their energy for relatively short bursts and being recharged on the straights.
The parallel hybrid system is designed to provide greater efficiencies for light sport aircraft, resulting in lighter weight and increased range. We should be able to see it all in person at Airventure, where Erwin promises an impressive display.
An ideal solution for piston powered airplanes that have to pay both the weight and dollar cost of the heavy engine that’s needed only during takeoff and climb, that then is depowered to 70% during cruise, which is the majority of flight. Think how much useful load would be gained from a hybrid engine; time before overhaul could increase as the ICE engine would be run at less than peak output and the initial cost could potentially be less than a large bore engine.
Aircraft engines naturally operate at reduced power in cruise, because of declining air density. By 6,000 ft, most of them are at about 70% power at full throttle. With 1950s-style airframes, the excess power at sea level is then (just about) enough to provide a decent rate of climb for takeoff.
With very low-drag aircraft, however, you can run into an issue. If you size the engine for takeoff, then 70% power may produce a very high cruising speed, which may not be desirable (for example, you really don’t want to enter turbulence at much more than about 2.2 x Vso). But, if you size the engine for cruise, you may have poor takeoff performance (the Rutan LongEz seems to be an example of this).
So, a hybrid system may be a good fit for a very low-drag aircraft where the engine is sized for cruise, or for a STOL aircraft where you want better than “decent” takeoff performance.
There is another advantage of this hybrid powerplant.
Subject to the design and configuration of a hybrid parallel powerplant, if the piston engine fails during take-off, then the electric motor can continue to provide enough power for a few minutes to maintain altitude and permit a safe return to the runway.
Spot on, having that electric power for a few minutes might the difference of living or dying.