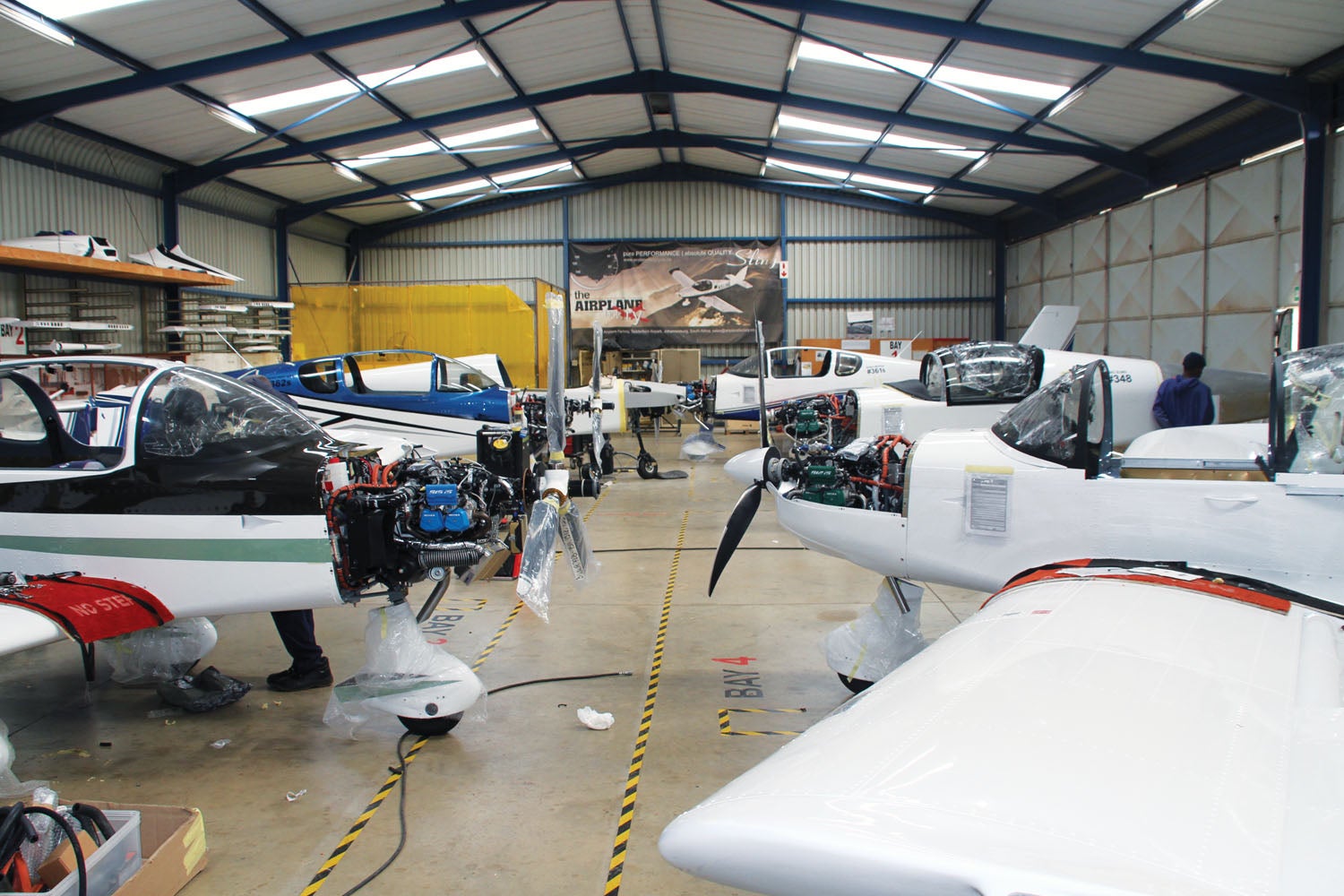
During my recent visit to Sling Aircraft in Johannesburg, South Africa, to fly the new High Wing on this month’s cover, I was given complete access to the factory facilities and personnel, and learned a lot about their design and production capabilities. I spent a great deal of time with company founder Mike Blythe, who toured me through all of the facilities and shops that are part of this complete and vertically oriented company.
Because Sling makes kits and delivers completed, licensed aircraft in countries where this is legal, they don’t just manufacture parts and package them up for shipment. A very large part (probably more than half) of their total floor space is taken up with actually building and assembling aircraft. Blythe and I spent a lot of time looking at airframes and engines in various stages of completion, and I realized that they have as much skill in completing an aircraft as Cessna or Piper.
Building After Building
Sling is a very vertically oriented company, doing as much as they possibly can in-house, with very little outside contracting. Because of this, a factory visit involves dropping in on many different hangar-like buildings, each with its own production specialty.
Engineering is housed in its own corner of a building, with space for 20 (or so) engineers and draftsmen. A combination of desks with lots of computer screens (everything is done in CAD these days), 3D printers (for prototyping small parts), to bits and pieces of airplanes lying about—it is just what you’d expect of an engineering group. What impressed this old engineer was the extent to which the individuals were given the freedom to exercise initiative. One young engineer had a rivet puller in her hand as she was building a vertical tail test article. They’d found some buckling in the spar-attach area, and she had analyzed the failure, quickly fabbed up some doublers from raw stock and was building a new component with those doublers so that she could take it out and test her new part herself, making this a complete failure/analysis/fix cycle, all under her control. The engineering team was also supporting the rest of the factory with modifications to parts for all the aircraft designs—continuing engineering to manage the inevitable changes that come as a fleet matures.
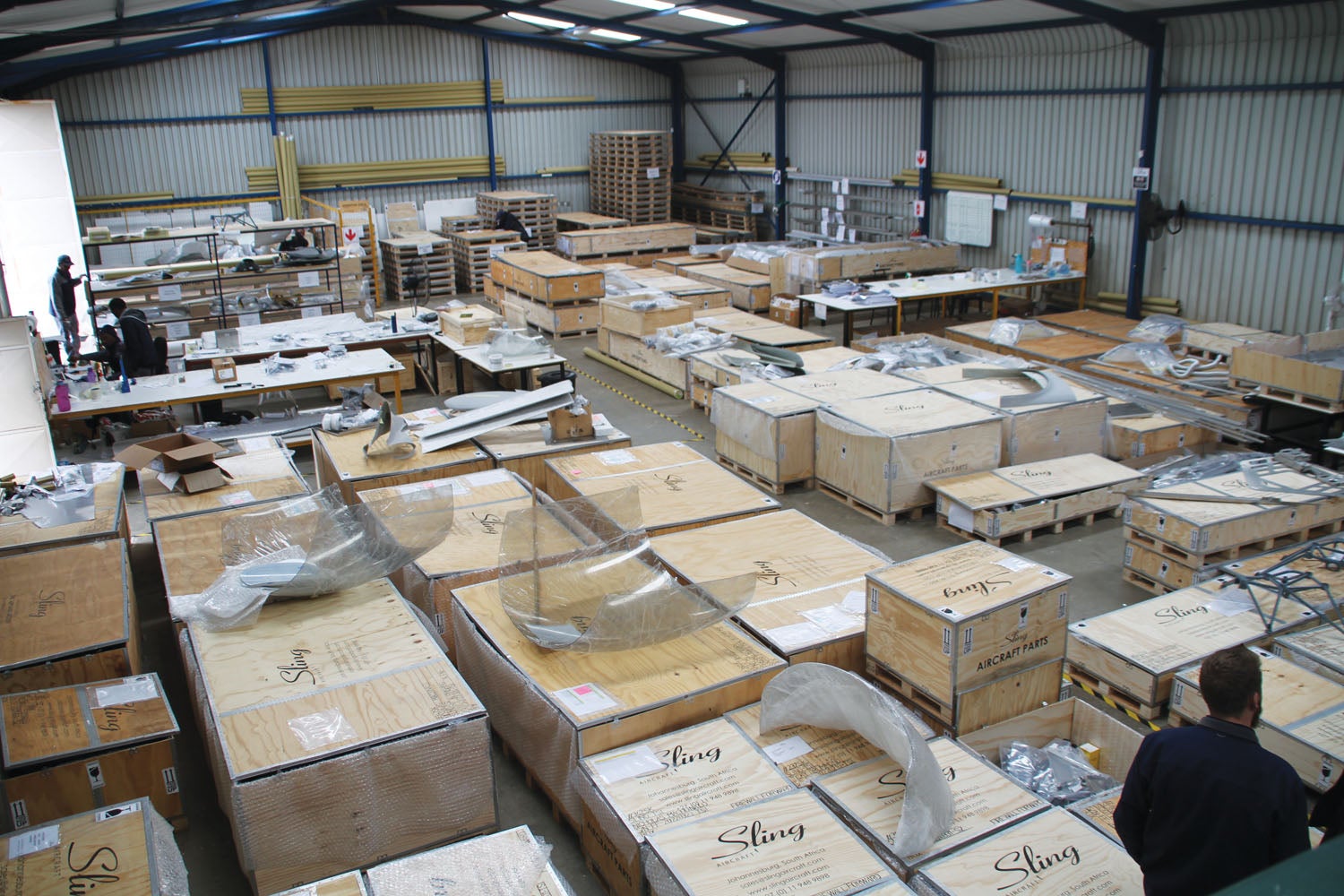
It Starts Off Site
To see where the fabrication of Sling parts begins, we actually have to leave Tedderfield airport and take a trip into an industrial area about five miles away. There, Sling maintains two facilities—one for sheet metal and one for composites. The sheet metal facility turns raw aluminum stock into shaped and punched parts using several large CNC punches, router tables and forming presses. The output is a large number of ribs, bulkheads and skins, ready for the kit production line.
Next door, but in the same compound, is the composite shop. Sling’s four-seat aircraft have used a fiberglass canopy top since the beginning, and all Slings have fiberglass fairings, cowlings and wheel pants—all produced in this facility using manual layups, resin infusion and large curing ovens. With the advent of the High Wing, they entered a major design program to build an entire cabin, which is quite complex as it included both fiberglass and carbon fiber, along with aluminum and steel structural attach points. Also included in the layups are copper mesh for ground planes and lightning protection. While I was visiting, they were in the process of refining molds and production tooling for serial production—it is an impressive operation!
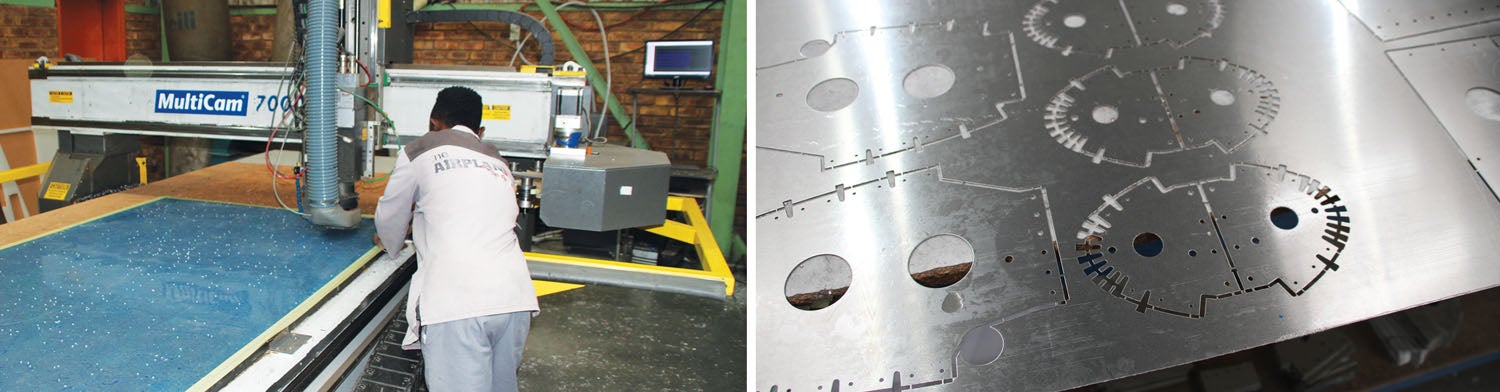
Back to the Airport
Back at the airport, the parts go to a variety of places. First, there is the stock building, where stacks of cowlings and wheel pants were up on a mezzanine, and shelves held more ribs than I could count. Remember that the Sling wings are tapered, meaning there are a lot of different ribs. Another area is stock for commercial parts they buy—mostly hardware and accessories. It’s interesting that they source a lot of their AN hardware from Aircraft Spruce in the U.S., meaning the parts come all the way to South Africa before many of them end up—you guessed it—back in the states! Also in the stockroom are lots of tires, tubes, cables—all the things that you need to purchase to finish an airplane. Quality control stamps are on everything—put there by Sling folks in the receiving department after careful inspections. Mike Blythe is a fanatic about organization, order and quality, and it shows in the facilities and the people at Sling.
Some of the parts that come out of the punch presses go to subassembly areas in another of the Sling hangars. Specifically, they have a whole area dedicated to building spars. Sling spars are built of flat and bent aluminum—the flanges simply being 90° bends in thick aluminum stock, rather than separate bar stock. The spars are of the laminated type, so they can carry the strength requirements from root to tip by changing the layer count and thickness. Since the spars use solid rivets and the Sling kits do not require solid riveting by the end builder, all of the spars are built at the factory and shipped finished.
Sling has solved the problem of deciding how to prime the parts of your kit project for you—they Alodine every aluminum part before it is packaged! One of the bays in their assortment of factory hangars is dedicated to the process of removing all the protective plastic from the aluminum pieces that come from the punch shop, then dunking the parts in a series of tanks that eventually leave them with a nice gold finish. They even Alodine the rivets for you! Alodining every part at the kit factory saves the builder a lot of time and effort, since they not only don’t have to agonize about the internal priming, they also don’t have to remove all the plastic from every part!
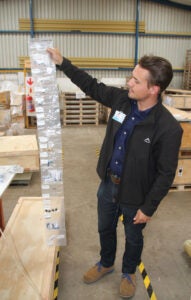
At the Docs
Sling has a complete documentation and instruction system, including color photographs as well as three-view and isometric drawings to lead you all the way through the build. To supplement this, they package hardware in heat-sealed strips of pouches sorted for each subassembly. The strips are designed so that the builder can hang them on the wall, then slit the top of each pouch to make a string of envelopes that are easy to access during assembly.
Sling has also thought hard about how to make the kits go together with a minimum of jigs and fixtures, and where they do need building fixtures—such as to ensure proper washout in the wing assembly—they have cleverly designed fixtures that are light, inexpensive and easy to use. To get the proper washout in the wing, for instance, they provide two simple bent-aluminum stands. You bolt the ends of the spars to these fixtures, then use a level and shims to set them up once on your build table—and the proper wing twist is ensured.
When it comes to parts and assemblies that do not need to conform to the 51% rule for American builders—panels, engines, upholstery—Sling uses its own fabrication shops. I visited the upholstery shop where they cut foam from raw stock and shaped it into seat cushions. In another building full of workers with sewing machines and stocks of leather, Sling makes the seats, sidewalls and baggage compartment covers. I asked if all of the materials met self-extinguishing standards for flammability, and Blythe told me that most do, and they are working to find substitutes for those that don’t.
Similarly, Sling has a shop dedicated to wiring—both of airframe harnesses and panels. I watched as workers used wire boards to lay up panel harnesses for their mostly Garmin panels, and the work was neat and clean. This shop is primarily serving the finished airplane customers, but pre-built panels can be obtained from Sling or one of the many companies that do that kind of work.
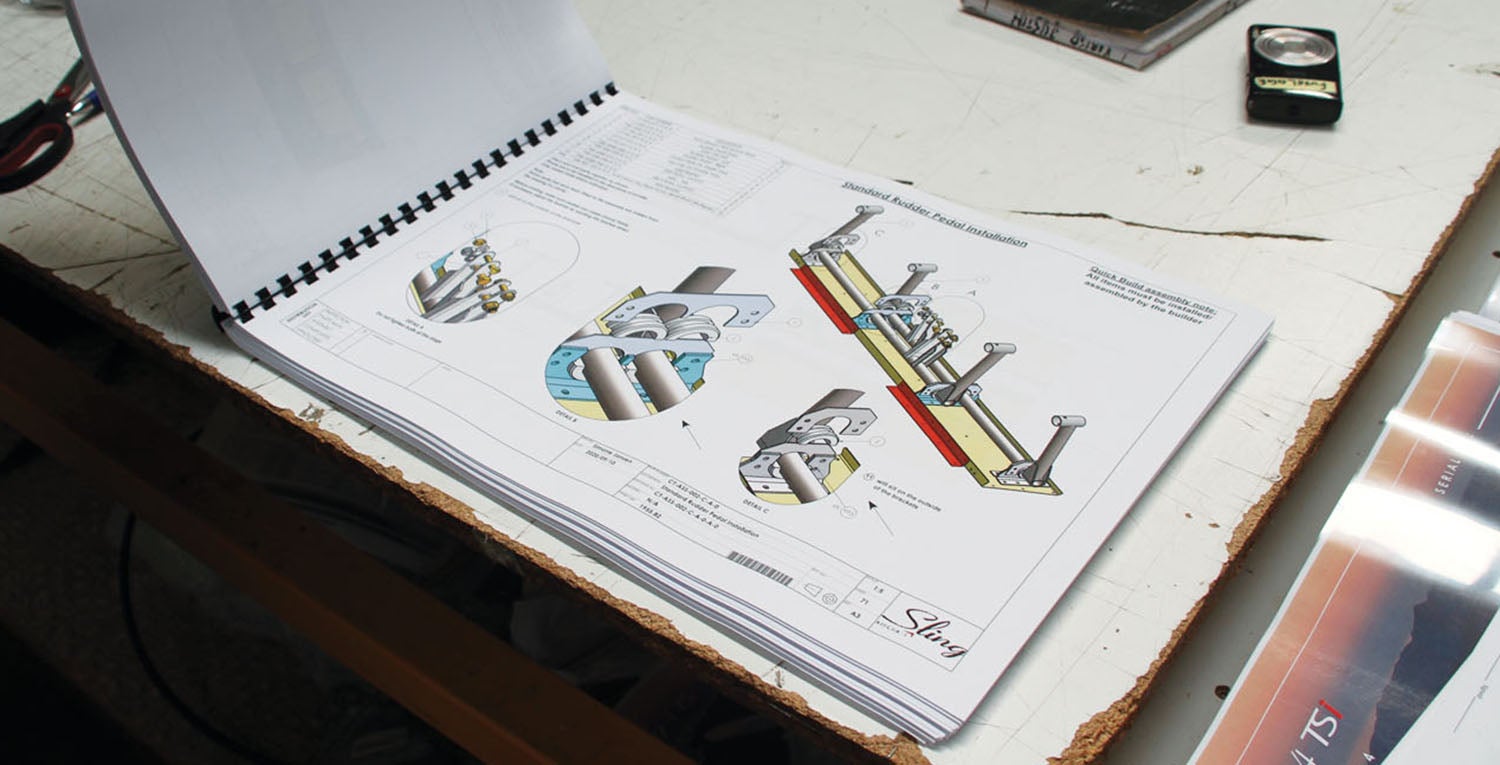
A Complete Industry
The Sling Aircraft factory is a great example of what you can do when you control everything from the raw materials to the finished product. Such complete control over all aspects of design, testing, prototyping, production and quality control has been an ongoing goal of Sling’s founders and leadership, and it shows in their product as well as the satisfaction of the workforce. Wandering around the factory with founder Mike Blythe, it was obvious how much of a team attitude he has fostered among the workers and how everyone felt empowered to bring problems to light, rather than covering them up—a good sign of a healthy aviation environment.