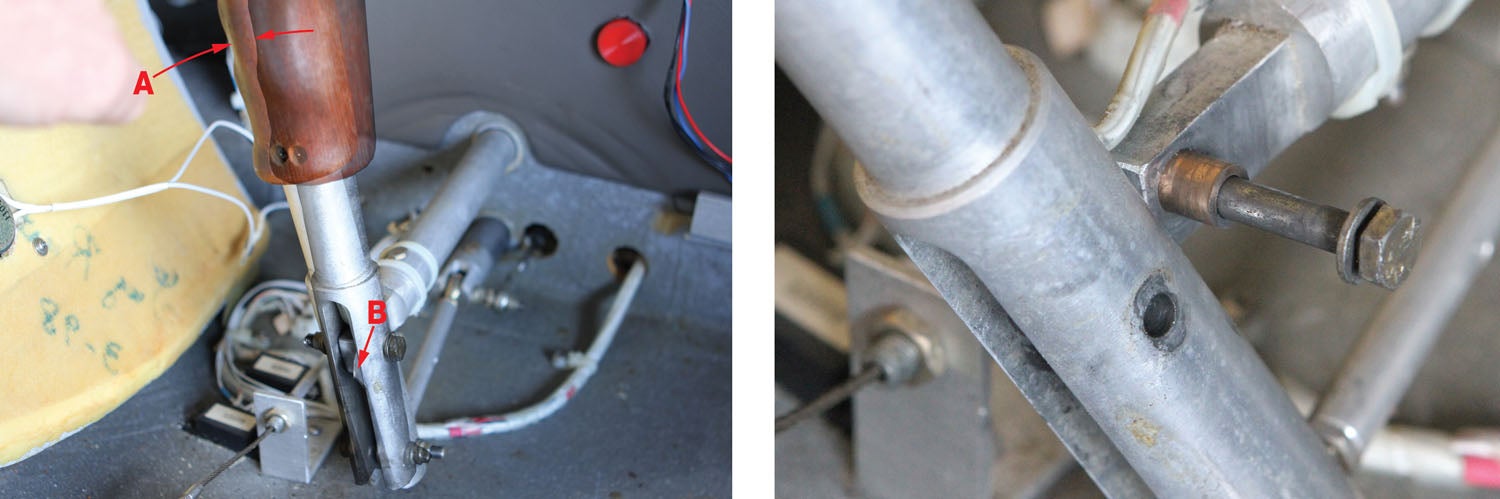
Late in 2021 my buddy Kevin King was in the middle of upgrading the panel on his SQ-2000. He was swapping out the original—and no longer supported—Blue Mountain EFIS for a new Grand Rapids unit. In the midst of sorting out all the wires and whatnot while waiting for the new display (which was on backorder due to COVID, of course), Kevin figured it would be a good time to deal with his “wobbly” control stick. He asked me to check it out and, sure enough, when I moved the stick front to back, there was a significant “clunk clunk” feel before any control surface movement. Kevin mentioned he had added a shim a while back, which helped, but he wanted to eliminate the clunking entirely. After pulling away the floorboard to reveal the mechanism, it was clear the problem was a loose fit between the elevator control bar and the stick. All in all, this was going to be a relatively easy fix for the home shop machinist!
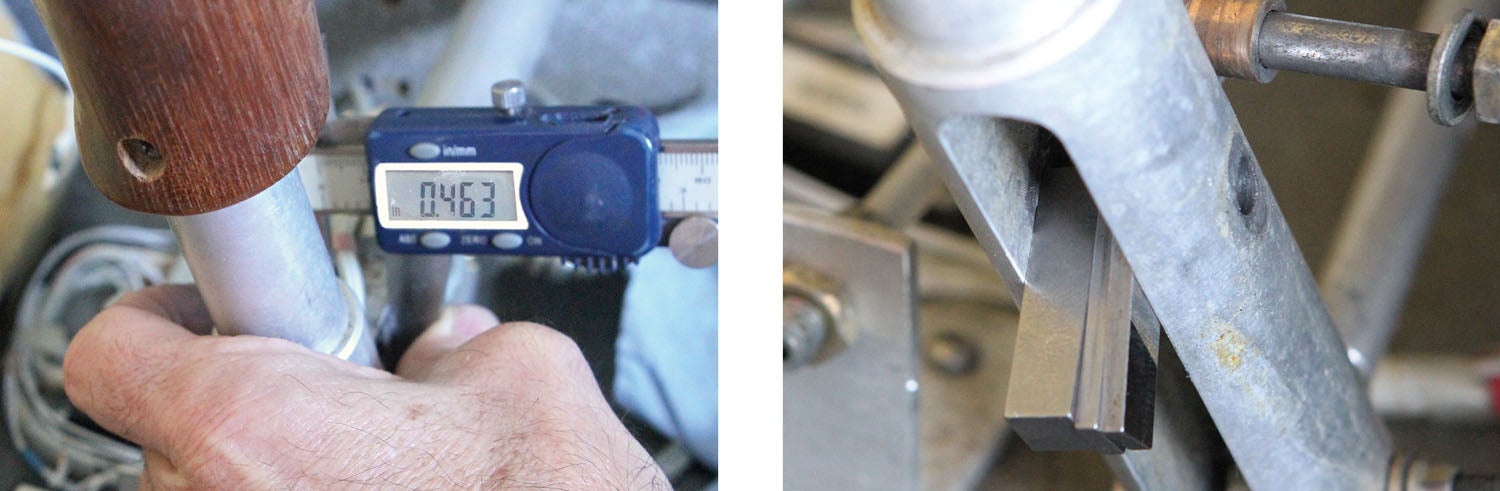
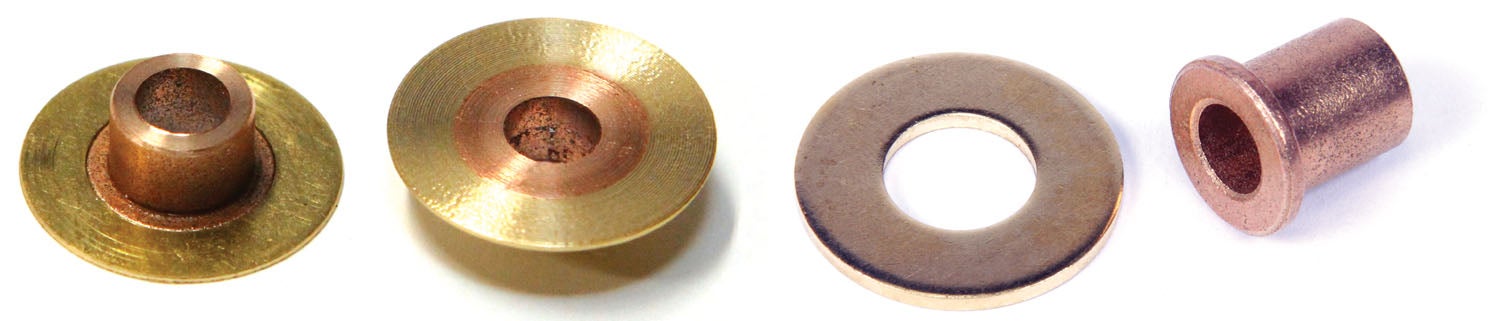
The typical fix for side-to-side play in a pivot is to add a set of close fitting shoulder bushings—sometimes called hat bushings—to eliminate the slack. The terms “close fitting” or “close running fit” describe the ideal dimension between two moving parts that is “just right” in order to eliminate slack yet still retain, as near as possible, smooth movement.
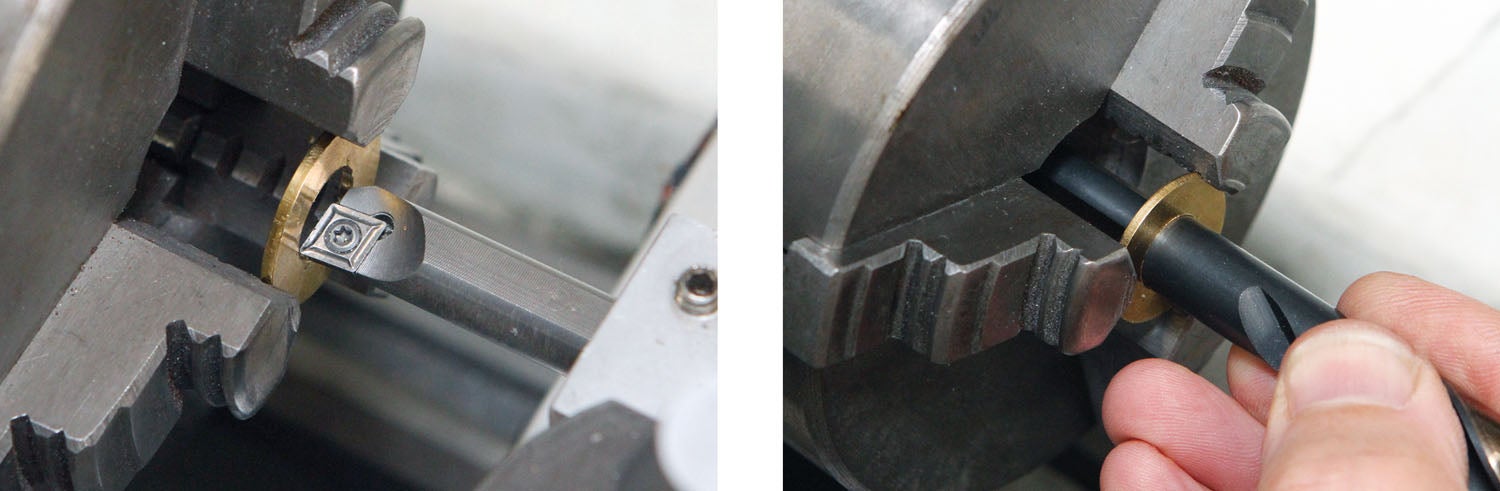
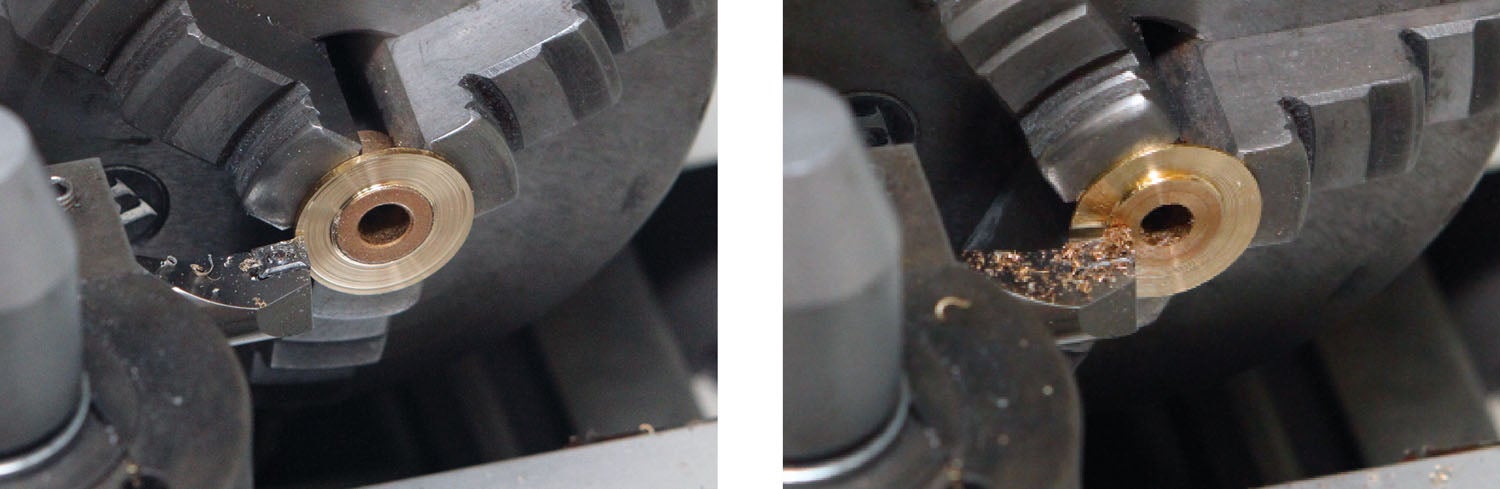
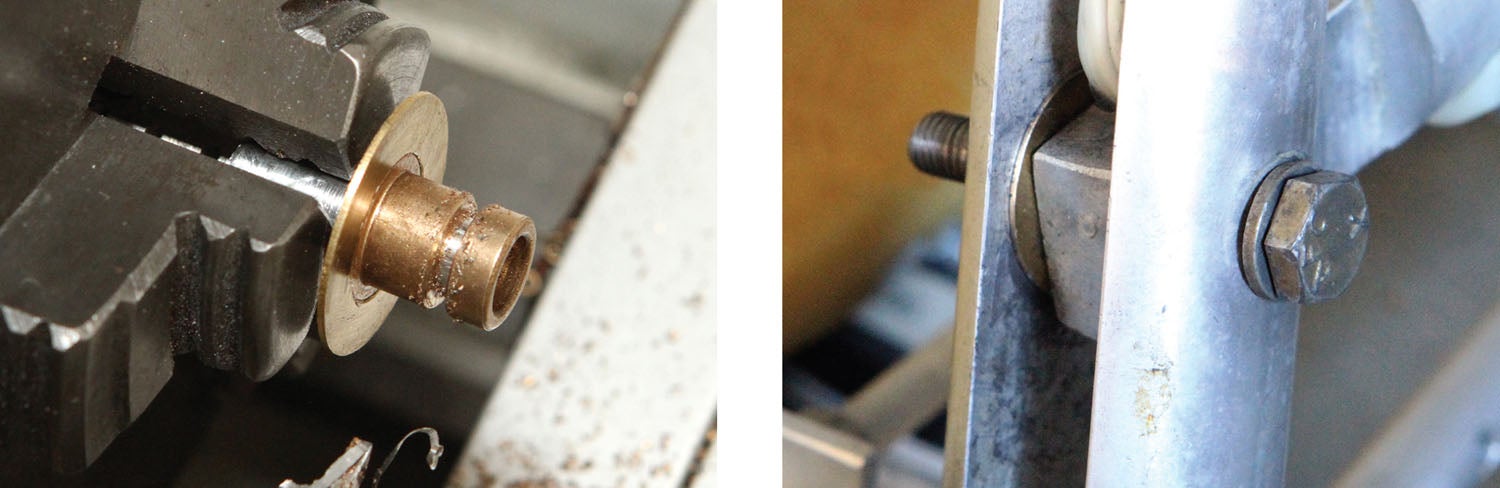
I thought about making a set of plastic bushings out of a low-friction material like Delrin or nylon 6. But since the original bushing was brass and the amount of leverage acting on it had, over time, caused it to bell-mouth, which made the stick wobbly, I concluded that a soft (compared to metal) plastic bushing may not be the best option. Brass was the obvious choice, but then it popped into my head that this might be a good application for an Oilite bearing.
Invented in the 1930s by Chrysler for use in water pumps, Oilite bearings are bushings made from a porous copper alloy that is vacuum impregnated with lubricating oil. They’re inexpensive, durable and essentially maintenance free (though if used in static applications like this, it doesn’t hurt to daub a drop of oil on them once a year or so).
One drawback to using Oilite bushings for this application was that the shoulder diameter of the 1/4 ID x 3/8 OD bushings were only 1/2 inch in diameter. I really wanted a broader flange to better support the stick against the control bar. Another, albeit slight, drawback to using Oilite bushings for this application was that they needed to be trimmed to fit. While they can be machined, super-sharp cutters are recommended because machining typically can clog the pores of the bushing and inhibit the benefit of the imbedded oil.
I decided on a hybrid assembly using the Oilite bearings for the pivot and large-diameter brass washers press-fit to the flanges of the Oilite bearings.