As most of you know, I’ve been writing for KITPLANES since I had brown hair. As a matter of fact, my first article was in the predecessor of KITPLANES in October 1977. I’ll save you a lot of math. That was 550 monthly issues ago. I’m sure all of you have kept all of those issues in your files, but for those of you who have just recently signed on to this world-class magazine, I can tell you that in 175 of them the word “wire” was used, and in at least five of them it was the lead topic. That’s a lot of Weir’s words, which weigh weightily with wire. We need to winnow the wisdom of Weir’s words. Ahem.
First of all, let’s come to a definition of wire. Of course, we all know what wire is…round metal (mostly round) thin threads meant to either constrain cattle or transmit electricity. I think it is the second one we need to deal with, barbed wire notwithstanding for the first one.
Now, some stuff you may never have considered before. What is the most conductive metal? Another way of saying that is, what metal provides the easiest path for electricity to go from one point to another? Ask that around the chapter barbeque and the most predominant answer will be gold. The predominant answer will be wrong. The correct answer is silver, followed by copper, gold, aluminum and then a whole bunch of stuff we don’t have to deal with.
Silver wire, for those of you who are building reasonable aircraft, is not available. After 65 years in this business, I’ve never seen silver wire.
So, copper wire is our metal of choice. Not quite so fast. Have you ever seen those beautiful roofs in the cathedrals of Europe? Mostly all green. The green is what we call verdigris and is a copper amalgam. They started out copper, but the years of exposure to a polluting atmosphere turned them into literally translated (ver [green] gris [made gray with vinegar]), but hardly what we want on our airplane wires. And verdigris forms on copper nearly instantly on exposure to polluted air.
There is a solution, perhaps not an optimum solution, but a practical one. Coat copper wire with a very-very-thin coat of tin (or tin’s son from the marriage of tin and lead: solder), and then you have an excellent conductor with a thin coat of “pretty good” conductor. The best of all possible worlds.
One more refinement and we are ready to go. Those of you familiar with house wiring know that Romex (solid copper house wire) doesn’t take a lot of flexing or vibration to work-harden and break. Since there is a fair amount of vibration in most of our aircraft, especially those of you “privileged” enough to fly behind a Jacobs radial (they don’t call them “Shakey Jakes” for fun), we had best figure out a way to keep solid wire from breaking.
The best way (so far as we can tell) is to use a lot of very small wires in parallel instead of one big solid wire. We call this “stranding” and it is designated on the wire spool like this: AWG #24 Strd7/32. Thus we have a #24 gauge wire made up of 7 strands of #32 wire wound in a spiral, and it is virtually impossible in the real world to flex this wire enough to break it. Yes, there is a mil-spec that dictates how many times a machine could bend this wire at a given bend angle to break it, but for our purposes (not being willing to sit there bending it back and forth a few thousand times to finally break it), it is not prone to flex breakage.
Somehow along the way, we needed to codify our wires so that the early engineers amongst us could specify what wire size we should use for a particular application. Since the electrical systems evolved prior to the United States’ entry into the world order, our predecessors picked systems for each country according to their measurement systems. It was a cacophony until somebody noticed that nearly every country eventually signed onto the United States system and thus was the universal adoption of the AWG (American Wire Gauge). England, of course not being too thrilled with those upstart colonies that beat them fair and square in 1783, adopted an identical system called the Browne & Sharpe Gauge (aka Birmingham Wire Gauge or Stubbs Iron Wire Gauge).
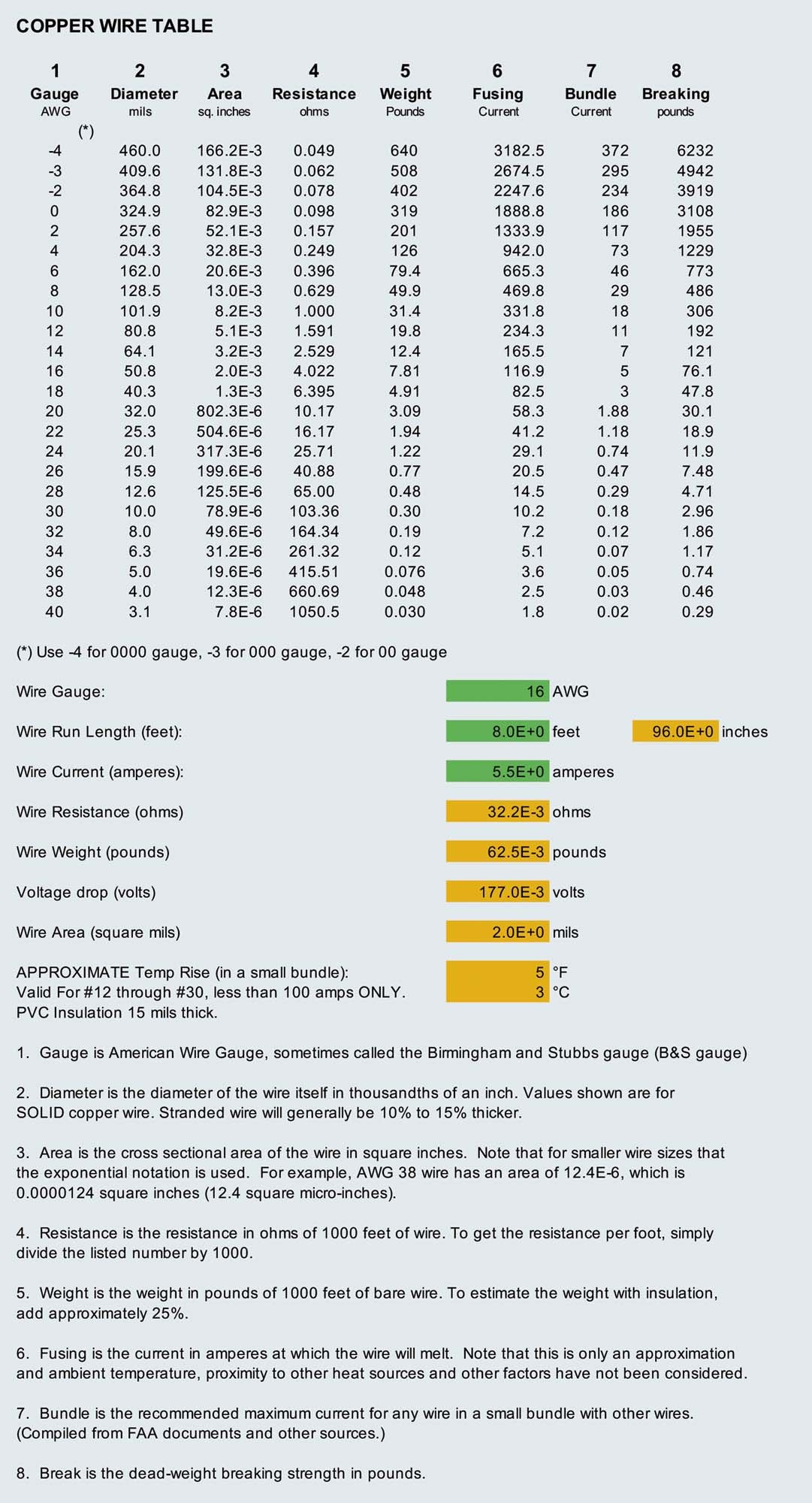
I think that the above copper wire table (downloadable as a true spreadsheet from www.rstengineering.com) might be a valuable addition to your collection of digital electronic tools.
More of Weir’s Weird Wires next month. Until then…Stay tuned.
In the image of wire in this article, I noticed some nice wire labels. I wish I knew how to get that done.
Jason, see here:
https://www.kitplanes.com/plane-and-simple-11/
https://www.kitplanes.com/my-new-toy-rhino-label-maker/
There are several brands of labelmakers that will print on heat shrink tubing. I use a Dymo Rhino, but Brother P-Touch is also very popular.
Very handy! And needed for aircraft wiring . . .
Another great label maker for electrical work is the Epson LW-PX700. Its capable of printing on 1/8 in heat shrink tubing that shrinks completely on 22 AWG Tefzel wire. You can also plug it into your computer and print multiple labels in one batch from a spread sheet or text file. It has a great feature where it puts a “half cut” between multiple labels on heat shrink tubing, so you can print a string of 20 or 30 (or more) and then tear them apart (with your fingers) as you build your harness. I found this to be very handy. It also prints all the regular vinyl labels as well. Its priced around $120.
I’ve had experience with tinned, stranded copper wire. Not a big fan. If it gets warm, it can succumb to thermal-mechanical fatigue. The tin-oxide that forms increases resistance (and expands) which increases heat. So keep it cool (right size the wire) and cover/seal (keep the oxygen out). Otherwise, maybe a silver solder which is where I thought you were going with this. The copper oxide conducts better, btw.