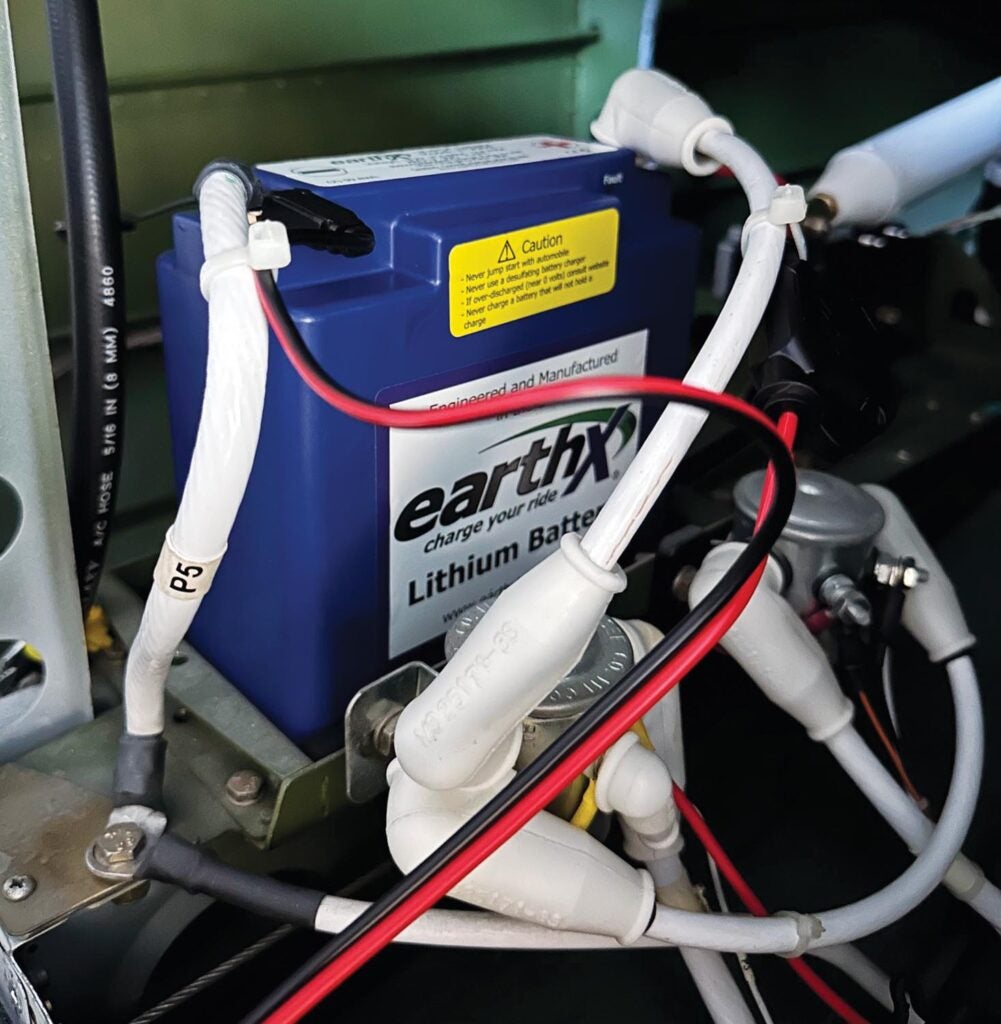
We’ve all been there. The airplane is pulled out and baking on the hot ramp. Preflight complete. Passengers and bags are loaded and ready to go. Systems powering up seem normal. Battery voltage is a tad low, but still above 12 volts. Hit the starter and you’re rewarded with a weak quarter turn of the prop and then some pathetic clicks as the volts drop off a cliff. Arrgggh! I hate this kind of triptus interruptus. I should have realized that I was due as in over nine years of using Odyssey PC680 batteries, I was averaging about three years per, and it had been about three years since the last installation.
Lead-acid batteries, even in the more up-to-date absorbed-glass-mat format, are very old technology. Modern lithium-based batteries were making inroads during my build period, but I had seen published evidence of charred remains in both RC models and early Boeing 787s. According to EarthX, their battery chemistry is different than the aforementioned battery types and is safer and more stable. Back then I was being cautious and decided to hold off to let the technology mature and prove itself.
Technological innovation is an aeronautical tradition, but early adopters pay a price. Efforts to maximize energy efficiency can produce temperamentalism as a byproduct. I started my airline career flying Boeings with Pratt & Whitney JT8Ds and finished with the latest CFM Leaps. The latter are certainly more efficient, but there’s no doubt the newer technology has kinks to be worked out while the Pratts are, shall we say, fully unkinked. Hyperefficiency is good, but there is a legitimate fondness for the old Pratts. As the mechanics used to say, “They may be thirsty but if you toss gravel into the front, you’ll get sand out the back.”
Batteries of Today
Back into the battery market once again, I decided to take a renewed look at the modern offerings now that they have had time to prove themselves. Like next-gen engines, new battery science uses exotic materials and computer-chip control to squeeze more power, efficiency and longevity out of your battery box. After studying the market offerings, I decided to purchase an EarthX LiFePO4 for my RV-10 and give it a try. As I’ve mentioned before, I am not a technical type. I’m not going to tear the thing down and do exotic tests, showing the results on charts and graphs. I’m just sharing my experience from the standpoint of John Q. Enduser on the process of installing and using this new technology.
For my RV-10, I ordered the ETX900 directly from the manufacturer. This is the unit they recommended for my application. At $449, it is roughly 2.5 times the going rate for the Odyssey I was replacing. Obviously, the promise (hope) of longer service life is a big part of justifying the higher cost. The package arrived within a couple of days, which was a pleasant surprise considering the supply chain follies of the recent past.
One of the primary advantages to installing lithium batteries is weight savings. Those savings are significant. In unscientific home testing, the Odyssey showed 14.2 pounds and the EarthX registered a svelte 4.7 pounds—nothing to sneeze at. To put it another way, the savings effectively countered the two W&B adds I’ve made since the first flight, being the Dynon yaw damper servo and the B&C standby alternator. Rarely does any upgrade equate to a weight savings like this one does.
The Second Generation
One of the things that helped to assuage my hesitance at adopting a new-tech battery is that the current model recommended for my application is labeled a “Gen 2” product. According to EarthX, this second-generation battery has new cell construction that reduces the risk of a thermal runaway by 400%. It also has 20% longer shelf life, enhanced short-circuit and overvoltage protection and is easier to recharge when in its “discharge protection mode.”
These new battery designs require active onboard management and monitoring to protect the battery and its host. In the EarthX, the battery management system (BMS) consists of an integrated circuit board encased atop the battery. The BMS balances the individual cells and monitors charge and discharge. Some of the improvements integrated into the second-gen series came from enhancing the BMS. For BMS operational monitoring, the battery case includes an LED to display abnormalities by specific flash codes, plus there’s a pigtail lead to connect to an external warning light or EFIS widget for the same purpose.
Installation
Installation of the battery is quite simple. By design, the battery is non-spillable and can be installed in any position or orientation. Its light weight makes mounting decisions even easier. There are various mounts and boxes available from EarthX and other vendors for horizontal, vertical, firewall and so on. Some builder forums have links to software offerings for those interested in 3D printing their own box. In my particular case, I found the footprint of the battery to be practically identical to my previous Odyssey 680 batteries and the standard Van’s mounting tray to be sufficient with the same spacer blocks I had previously used.
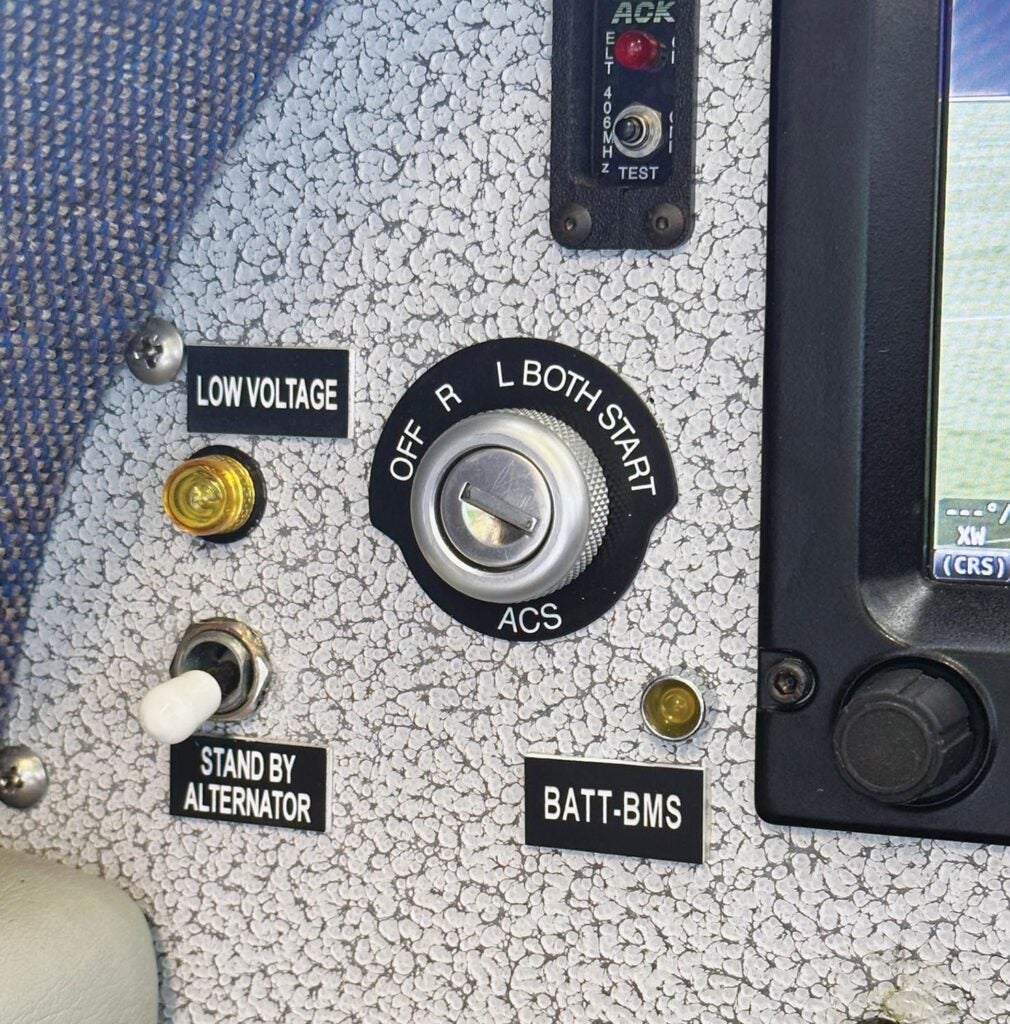
Where the installation process gets slightly more complicated involves accommodating the BMS indicator light. In the Van’s RV-10, the standard location for ship’s battery is in the empennage just aft of the cargo compartment bulkhead. The good news is that when I built and wired the airplane, I ran an extra five leads from the aft area to the instrument panel area. Therefore, I had an available lead already run and ready to go. The bad news is that after installing things like a 406 ELT with GPS, a yaw damper system and some lighting upgrades, the BMS install consumed my last available lead. Fortunately I also ran a fish string when I built for the next upgrade I haven’t thought of yet. Note to builders—run plenty of well-marked extra wires.
Now back to the BMS indicator. The cockpit indicator can be either a widget programmable into most EFISes or a separate (amber) light installed in an appropriate place so as to be readily noticeable. I vacillated on this decision until I ultimately decided to install a separate physical light and ordered the $29 LED assembly option from EarthX, though any similar light rated for the appropriate voltage would work. My reasoning was that with the way my twin 7-inch Dynon SkyView displays are configured, I don’t really have any available screen real estate for an additional widget, especially for one that hopefully will never be used. Also, I have a far corner of my panel where I already had an indicator light for my B&C standby alternator and decided that the BMS indicator would be easy to install and would look “at home” there.
The actual wiring of the warning light is easy enough. The lead from the BMS pigtail takes the circuit to ground when activated. Power for the light can piggyback off of any positive terminal downstream of the master switch. The light only illuminates if there is a problem and, depending upon the anomaly, will illuminate steady or flash either fast or slow.
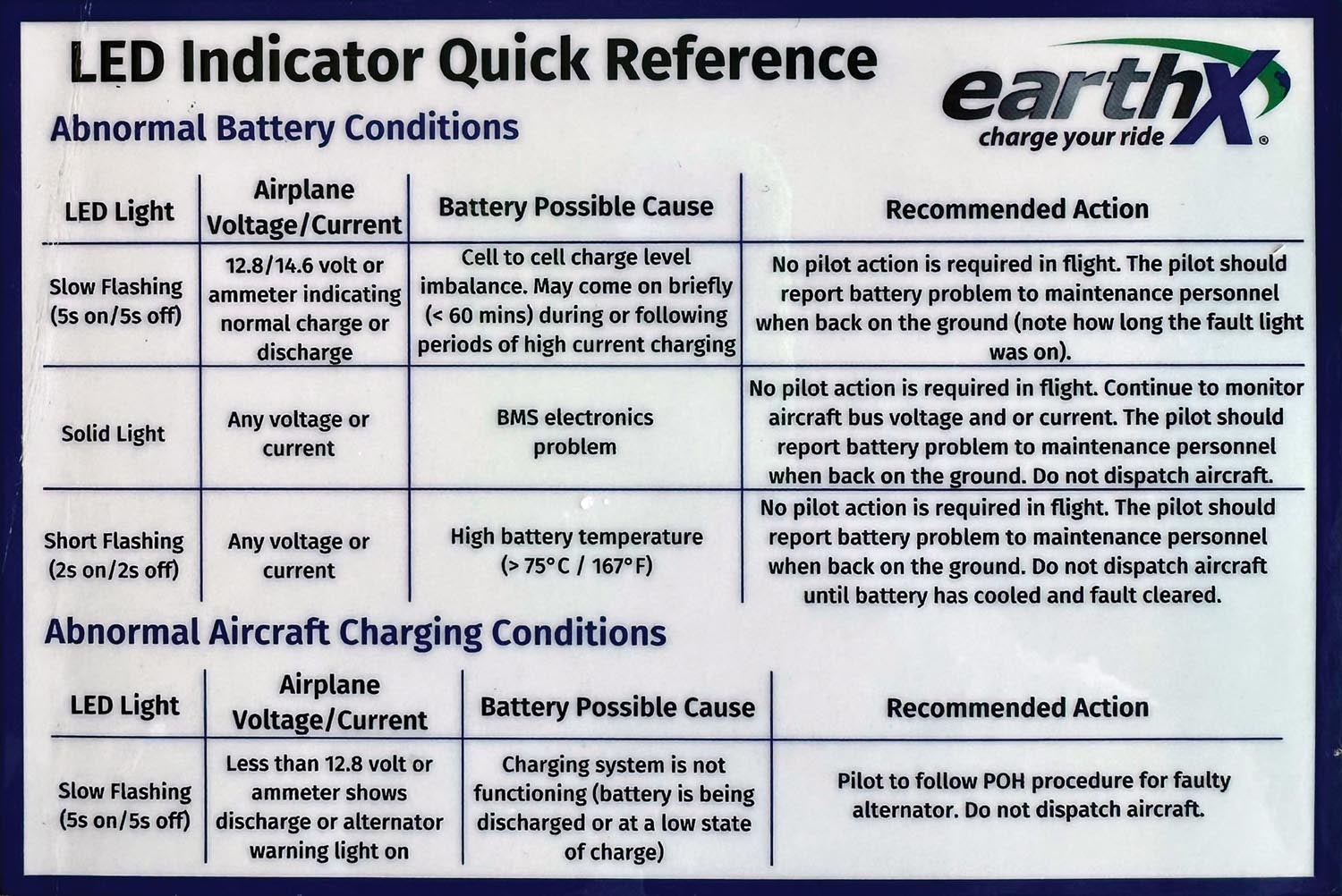
My only quibble with the design is that there is no way to test the system for functionality. After over 35 years of airline flying, that seems odd to me. In airliners, practically every warning system gets tested daily if not every flight. As confirmed with EarthX tech support, as close as one can come to a system test is to unplug the BMS lead at its pigtail at the battery and then touch the terminal end to battery ground. If the positive side has power, the light will illuminate. That will test the light circuit but not the BMS itself.
Power Up
The real test for any starter battery is actually starting the engine. In my case, an IO-540 with higher-than-standard compression. As I got ready to engage the starter, I had a new magic battery that had zero external charge since removed from the box, plus about 20 minutes of panel operation. It showed 13.1 volts on the Dynon. For about 900 hours of Odyssey starts, I was used to a “soft” starter engagement that would intensify after the prop started turning. This time was different. It is hard to describe, but it was like the starter got hit with a hard punch. The effect was immediately noticeable: The engine started quicker and more energetically.
Like most builder/operators, I severely dislike dispatch reliability problems and appreciate bang for the buck, even if at a higher initial investment. I’m still new to the lithium world, but so far I am impressed and satisfied. If the projected life span increase pans out and the battery never gets angry on me, I’ll be glad I got the lead out.
Some comments;
For reference, for the C182, and the O-470 engine, Cessna recommends a battery like the Concorde RG35 which has 33 amp-hours capacity and 440 amps cold cranking current. So, the PC680 was less than 1/2 the battery needed , at 170 CCA.!
The IO-540 may require more than 400 amps to crank the engine, especially with high compression pistons. !
I have some reservations on using a lithium battery with a ‘battery management system’, which can disconnect the battery from the buss under overload, low voltage, and other conditions, resulting in total electrical loss.
I noticed in the picture of the battery and connetions, that the started contactor is ‘hot’ all the time, since it bypasses the master contactor, directly wired to the battery !!….not a recommended connection.
Also the starter contactor should be mounted ‘upside down’, so that a strong downward jolt will not close the started contactor armature, and activate the started. There is a weak spring that opens the armature connection.
Thanks for reaching out. The second relay isn’t the starter relay, it is the external power relay. https://www.kitplanes.com/plug-in-power/
The starter relay is on the firewall per the plans.
Ok, I feel better about that now.!
That is a good observation regarding battery management systems that I hadn’t considered.
And good reminder to people that they need to know the full requirements any battery needs to meet within their aircraft, not simply voltage and capacity.
I am not an electrical expert. However, it defies logic to me that taking a battery offline is going to cause a complete electrical failure. It seems to me that the alternator (I have two), would power the busses just like they do on an engine that was jumped or hand propped due to a dead battery.
These BMS systems are FAA approved on certified aircraft, even airliners.
The feds require an indicator light to announce in the cockpit that the BMS has been triggered. Why would that be necessary when a full electrical power loss (if that were a likely result) would be indication enough?
I waited for a while when the lithium systems were new to let the bugs work themselves out, but IMO, that time has passed. I wrote the article prior to OSH, but after a thorough workout in tough conditions (crazy heat), no battery has ever started my 540 as robustly as the EarthX. The weight savings is just a bonus. YMMV.
Myron,
I am an electrical engineer, and a pilot owner, [ Cessna 175B].
An alternator has no residual magnetism as a DC generator does, so the field circuit must be externally energized , a max of about 4 amps.
So, without the battery there is no field power and the alternator produces ‘0’ power.
Jump starting an aircraft with a lead-acid battery will have some residual power to energize the alternator field and produce power with the engine running.
Try, disconnecting the battery and hand proping the engine and see that the alternator remains off-line.
With a lead-acid battery discharged to the point where all the avionics shut down, about 11 volts. If the master is turned off, and wait 10-15 minutes, the battery will recover to above 12 volts and some small load can operate for a short period, like a radio, or VOR,
The BMS indicator light is a status indicator. It goes off if the BMS detects a fault and disconnects the battery from the buss.
Yes,the EarthX ETX900 has a great 400 CCA and with it’s higher voltage, will spin the starter a bit faster.!
So would the RG35 with 440 CCA.
The weight savings is about 18 lb, or 3 gallons of avgas…no great savings.
I’ll keep my hefty and out-dated lead-acid battery and forgo the fire.
Expect your alternator to produce maximum charge (60A for my RV) after engine start – especially if the engine has not been started or the battery charged for awhile. I sometimes have to run on the ground for 15 minutes to avoid max charging during takeoff. The LiFePO battery certainly produces high CCA and then it demands, and can accept, very high recharge rates. Sadly, don’t expect the promised longer service life.
i have gone thru 3 of these batteries in the early days. One was warrenty, the rest were garbage. The latest one has been in for 2 years. fingers crossed.
I just spoke with EarthX tech support and they confirmed my supposition that a BMS disconnect of the battery of an operating engine with a properly operating alternator would have no effect on the electrical system. Their comment was that the electrical system will remain powered until “you run out of gas”
Now if the BMS trips because the alternator previously failed and the battery subsequently fully discharged, that would be a different story but no different than any battery.
Thanks to all for your comments. It keeps us on our toes.
My British motorcycle would kick-start and run ok without a battery, BUT it required a large value capacitor of about 10,000 UF, a large can, to smooth the voltage spikes and provide the power to run the ignition.
Since most aircraft engines run on mags, no problem with the engine. There may be issues with a ‘noisy’ voltage on the buss, with electronic ignition units. With no battery, the 3 phase rectified voltage will have a few volts of ‘ripple’, which may be heard in the radio. I don’t know what affect this may have on other avionics.?
Turning off a large load will cause a higher voltage spike, which could be high enough to damage some sensitive devices , and could be high enough to trip the overvoltage relay. Then ‘no volts’.
Thank you Myron for using an EarthX battery and writing this article in an attempt to shed light on this newer technology available in the aircraft industry.
EarthX has been very active in the experimental aircraft market for over a decade now and is the most trusted and used lithium battery, not only by individual aircraft owners, but also from the OEM’s, such as Van’s Aircraft. EarthX is also the first company in history and in the world to receive FAA TSO approval on 14V and 28V batteries for the certified General Aviation market as a testament to the safety and viability of this battery advancement.
As this article is specific to EarthX, batteries, it should be noted that EarthX developed specific batteries for the aircraft market (ETX Hundred Series) with over a decade of data and engineering synergy with not only aircraft manufacturers, but also engine manufacturers to develop the most robust charging systems. Not all lithium batteries nor BMS’s are the same.
It is important to research and understand anything you install in your aircraft. EarthX has a detailed manual to explain and illustrate what the BMS does along with other technical details at http://www.earthxbatteries.com.
Per the comment above that states that if the BMS status indicator is activated, it will disconnect the battery from the buss. At no time will the BMS status indicator suddenly activate and disconnect the battery instantly from the buss while in flight. Ever.
Your aircraft has indicators to alert you on such things as oil, fuel level, high/low voltages, amperage, etc.
The BMS also has an indicator to alert you to something is outside of normal and will be a redundant indicator to what is happening with your charging system in flight, such a low or high voltage. The indicator can also provide an alert to something outside normal with the battery itself and this should be investigated. A lead acid battery has no way of alerting you to what is happening internally, and this is one of the advancements in this area of technology.
All batteries will eventually stop working, this is the nature of the science as they do have a lifespan. How they are used, what they are used in, how they are maintained, what type of environment they are used in (hot or cold) etc. will make the lifespan a variable. The typical lifespan is 4-6 years.
We welcome you to explore the EarthX website as we do have a lot of information to help those who want to educate themselves on the technology of a LiFePo4 battery.
Kathy, you should have mentioned that you are the Global Sales Director for Earthx Corporation.
Thanks for the additional info and the links to the battery data.
You can read more about lithium batteries here: https://www.kitplanes.com/understanding-lithium-batteries/
Did you change your voltage regulator setting, as Lithium Batteries have different charging profiles than AGM Lead Acid batteries?
Funny you should ask that. I checked with B&C and they said that there was no need to change any settings, but I would caution everyone to verify with their own vendors.
I agree, if your V-reg is set somewhere in the 14.0 to 14.5 volts range.
a lead-acid battery should be charged at 14.0-14.2 volts, Concorde has a nice chart on charging voltage vs battery temp.
I could not fine a similar chart for the Earthx ETX900, but from the install manual and other data it looks like a charge voltage of 13.8 to 14.5 should be ok…. ??
I installed mine into a stainless steel box on the firewall with a cooling duct and a temperature sensor, plus the remote LED indicator. This gives me peace of mind.
This summer for the first time due to extreme hot temperatures after start while taxing out with the engine at 1000rpm I got the LED flashing due to charging at high temp. I quickly figured out what was happening and turned the battery off for the remaining of taxi and takeoff. While established in the climb I turned it back on and no problem. After start the battery gets quite drained and the alternator changes it at full blast couple with the fact on ground there’s not enough cooling air but inside the cowling is an oven created the perfect storm. Luckily with my design seeing the temperature I found it out. I now installed an extra shield from the exhaust to prevent this again.