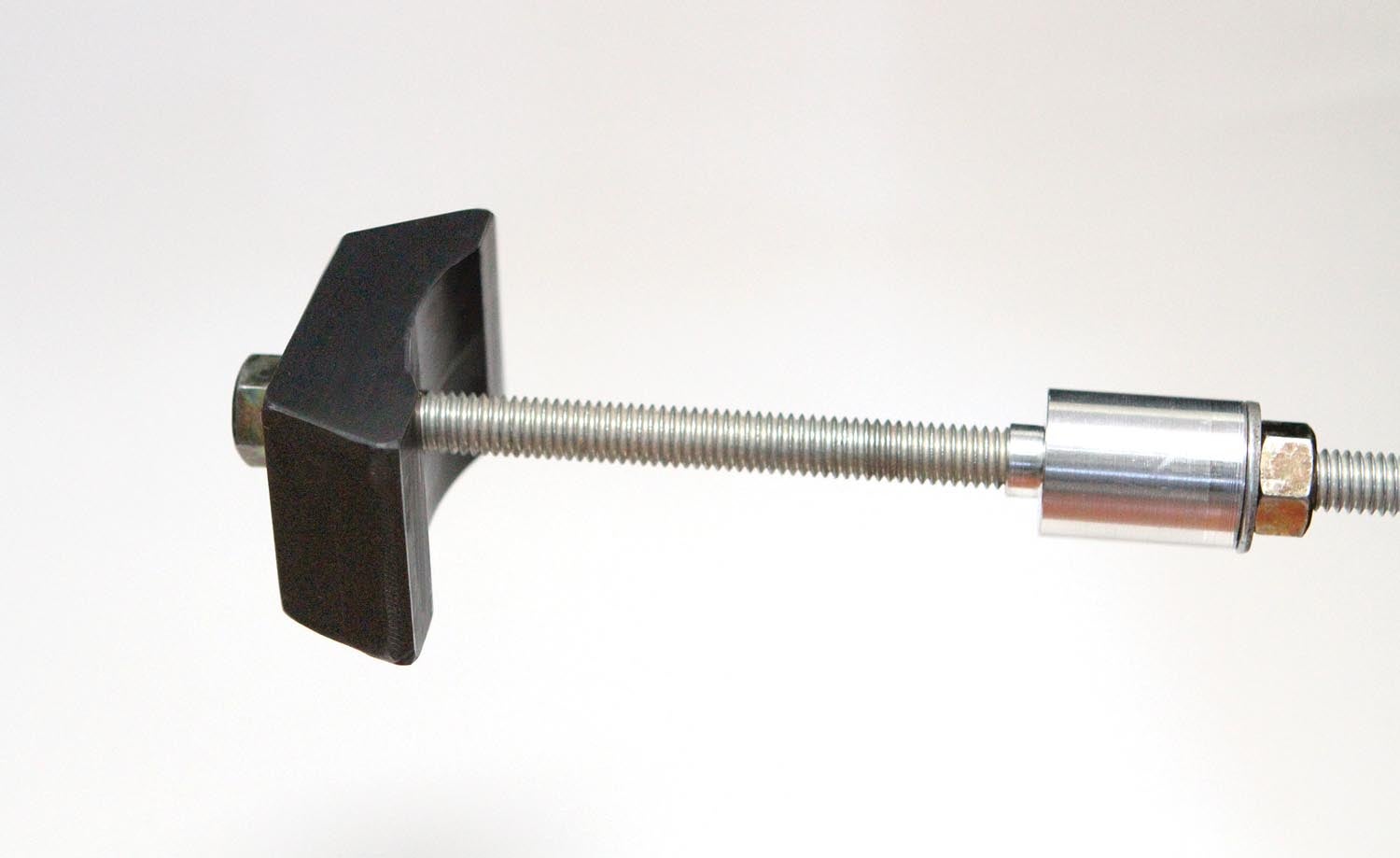
Fly cutting is a great way to put a “finish” on a flat and true face. The sweeping tool marks are not only instantly recognizable, they are, to my eye, infinitely more attractive than the swirly patterns made by an end mill. I covered the basics of fly cutting on plane surfaces in the February 2015 issue (“Fun with Fly Cutters”). But as this month’s project will demonstrate, fly cutting can also be used for coving. Because I was after a precision radius, I used a boring head, which allows you to precisely dial in the radius of the cutter path. For more on boring heads, see the October 2015 issue (“Boring on the Vertical”).
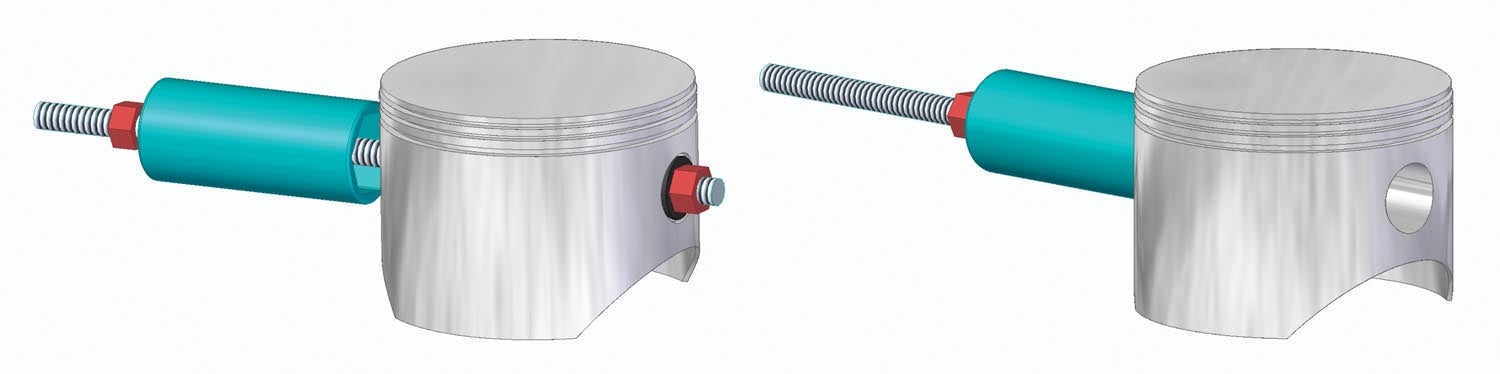
The task at hand was to make a tool to gently press a piston pin onto a connecting rod. I made this tool for my friends who are not yet 100% sure they’ll need it, but since removing the piston pin required a makeshift drawbar to pull it out, there’s logic in the idea that some gentle persuading may be necessary to reinstall it.
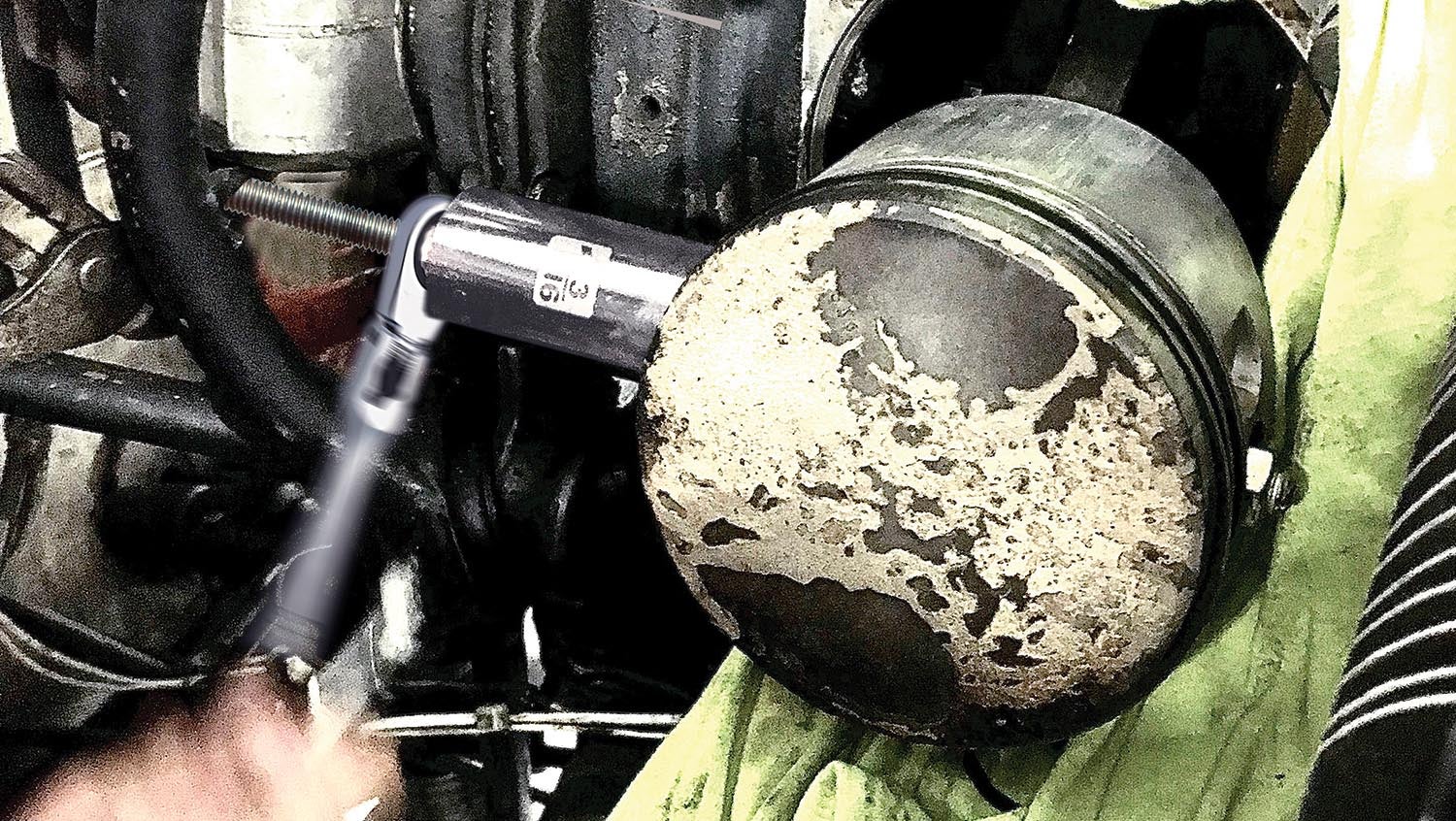
The engine in question was down because of a cracked exhaust port on one of the cylinders near the firewall. Not a common issue, but it happens. The typical fix is a replacement cylinder assembly, which includes the cylinder with valves, the piston and rings. You reuse the rockers and piston pin at your discretion. Lately, anybody who’s needed a replacement cylinder assembly for any of the popular legacy engines knows that the wait times have been excruciating. There was nothing to do but bide our time. So when the word came down that delivery was imminent, the teardown could finally begin!
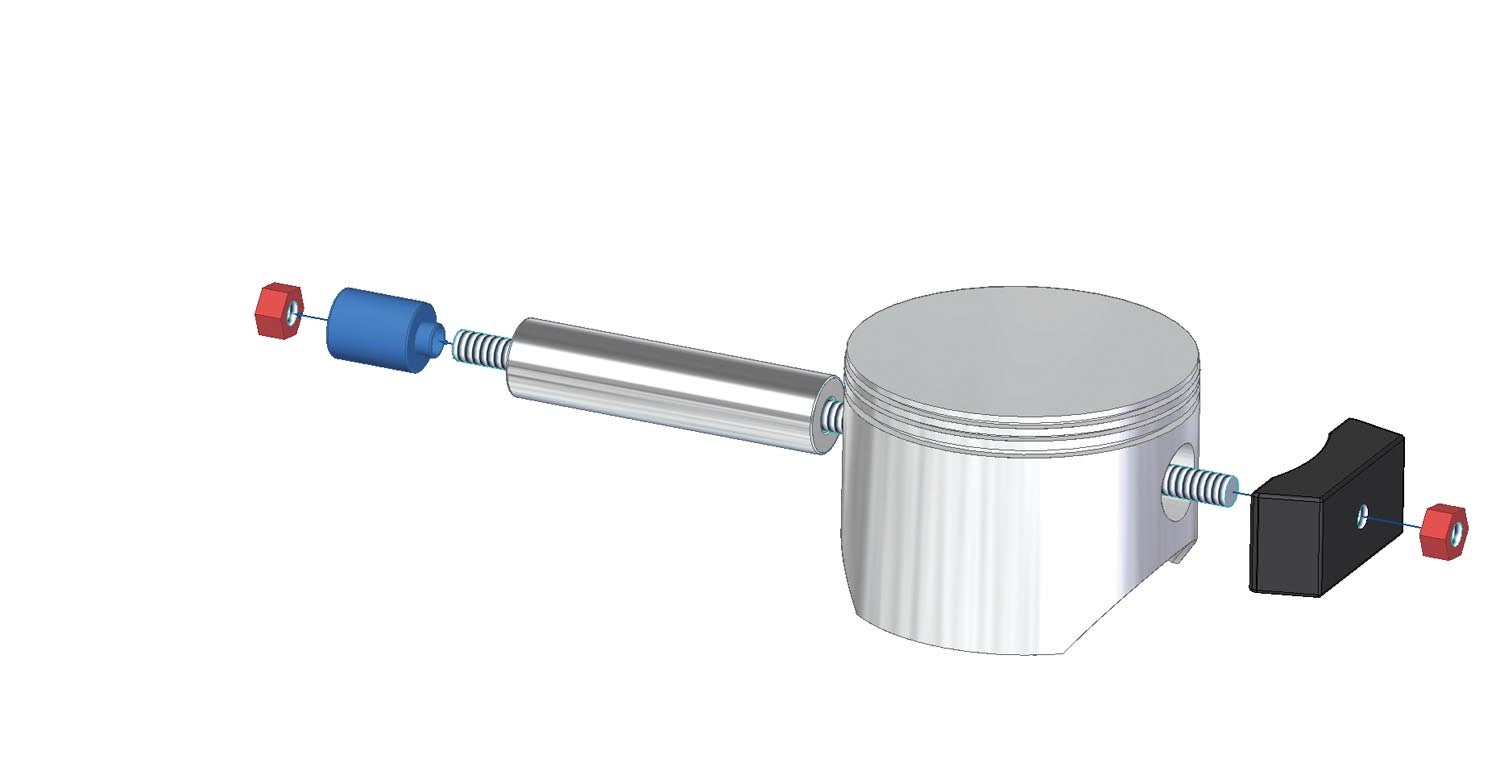
It was a Saturday afternoon when I got the text: “Do you have, or could you make, a piston pin removal tool?”
“No and maybe” was the answer. I grabbed my calipers and some graph paper and headed to the hangar to see what was what.
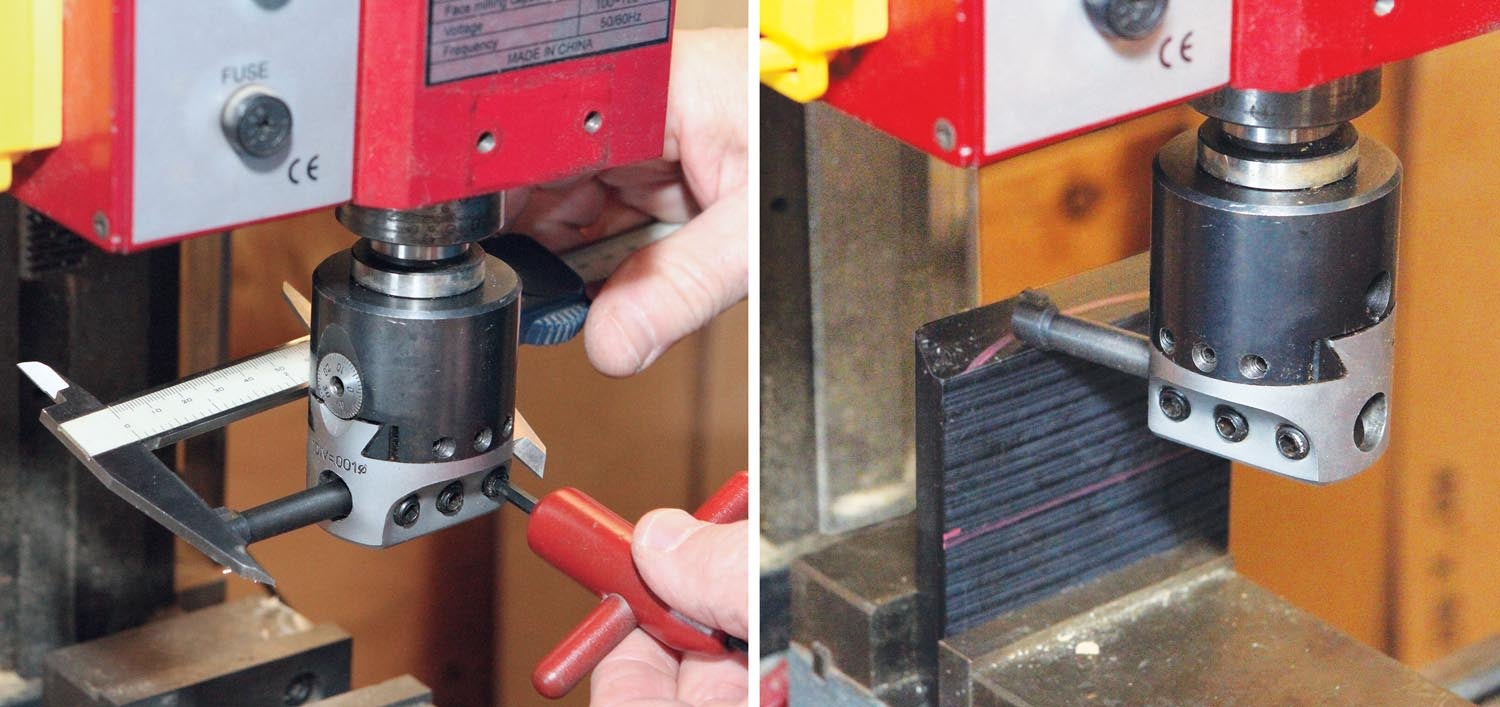
There are two types of piston pin removal tools: push and pull. For aviation, the predominant type seems to be the ACS push tool sold by Aircraft Spruce and Aircraft Tool Supply. No one seems to offer a pull-type tool for aircraft engines. The ACS tool is nice, but it is for rebuilding or refurbishing complete engines. In our situation, where we were removing and replacing one cylinder assembly, there’s simply no way to make it work if an adjacent cylinder is in the way.

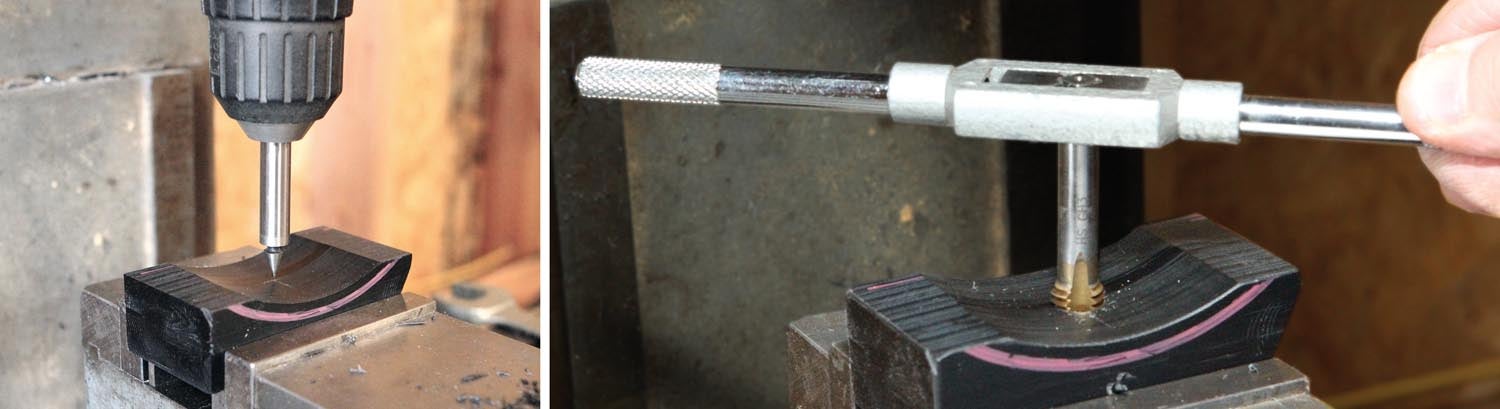
A few chin rubs and head scratches later, we concluded that we could put together a shop-made puller with some all-thread and tubing. While we had to be careful not to damage the pin or connecting rod, the piston was going to be replaced, so there was no need to worry about it getting dinged during removal. As luck would have it, I had a foot-long section of 7/16-14 all-thread with a couple of nuts and washers, but no suitable tube to provide clearance to make a drawbar sleeve. Then the light went off: a socket! Sockets come in handy all the time when you need a right-size sleeve or bushing on the arbor (or hydraulic) press. All we needed was a 1/2-inch drive (deep) socket big enough for the pin to be extracted. The OD on the pin was 1.125 inch, so any socket 1-1/4 inch or larger would work!
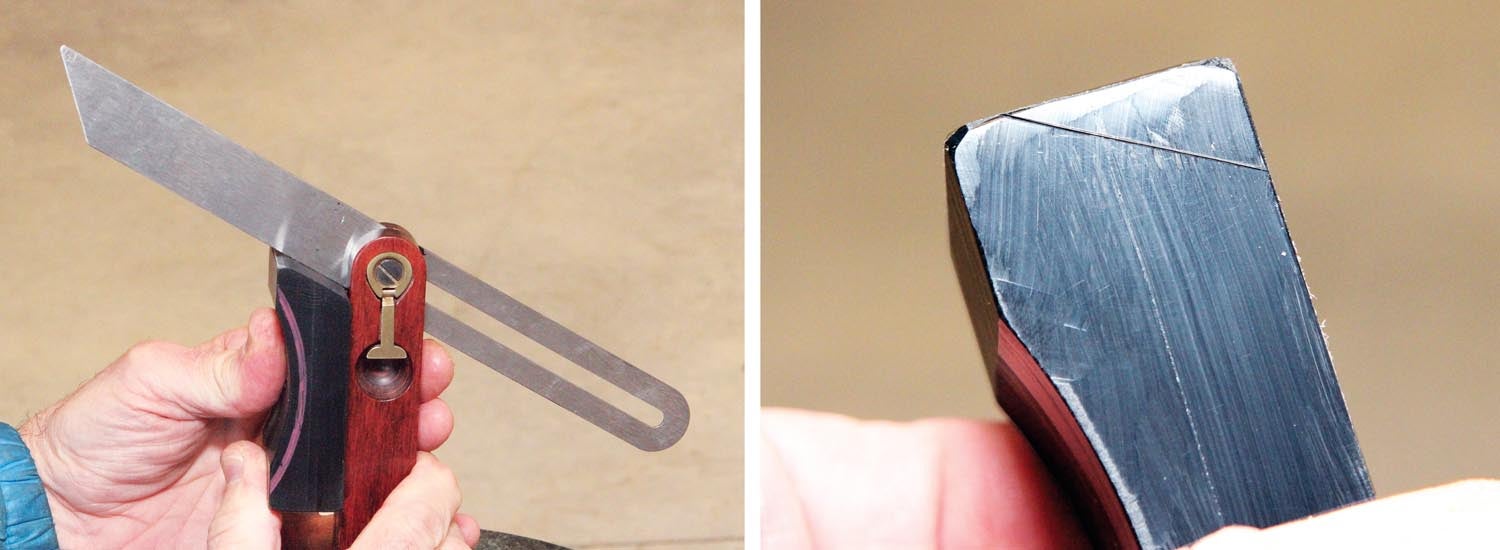
Once the pin was removed our attention turned to putting it back. The fit is not a tight press fit, but definitely tighter than you could possibly remove by hand. Reinstalling the pin carried the burden of doing absolutely no damage to the new piston.
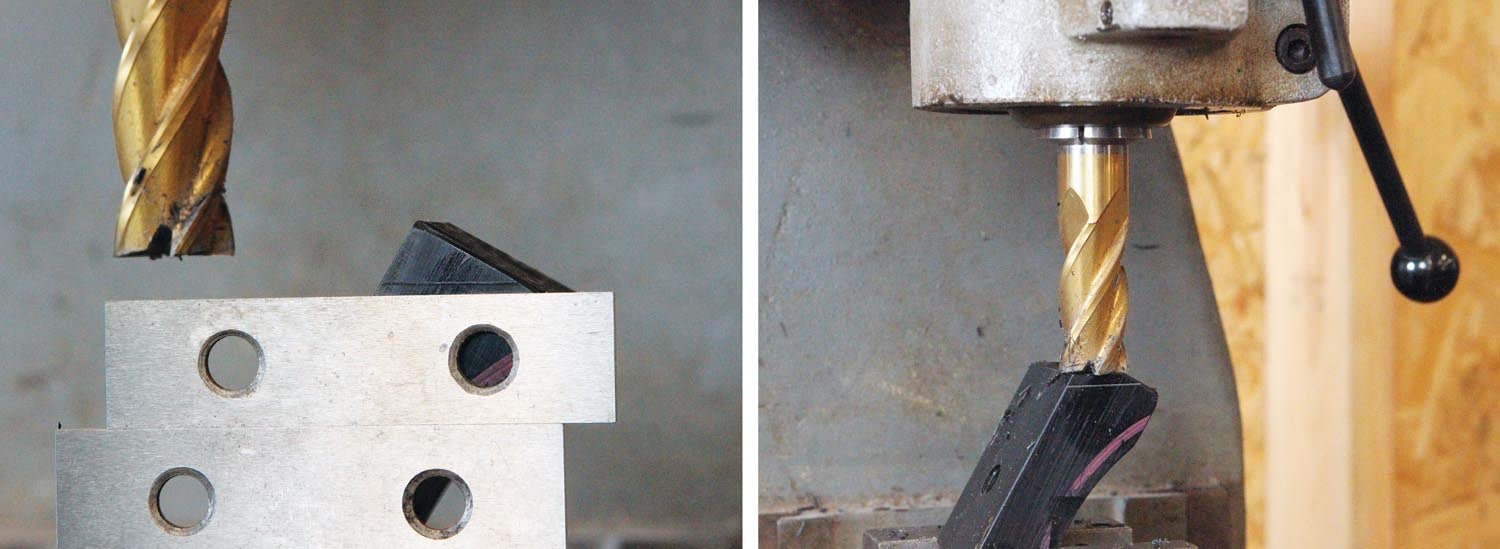
Which bring us to the main feature of the press: a Delrin pad machined with a cove to ever-so-gently cradle the piston while the pin is pressed back in place.
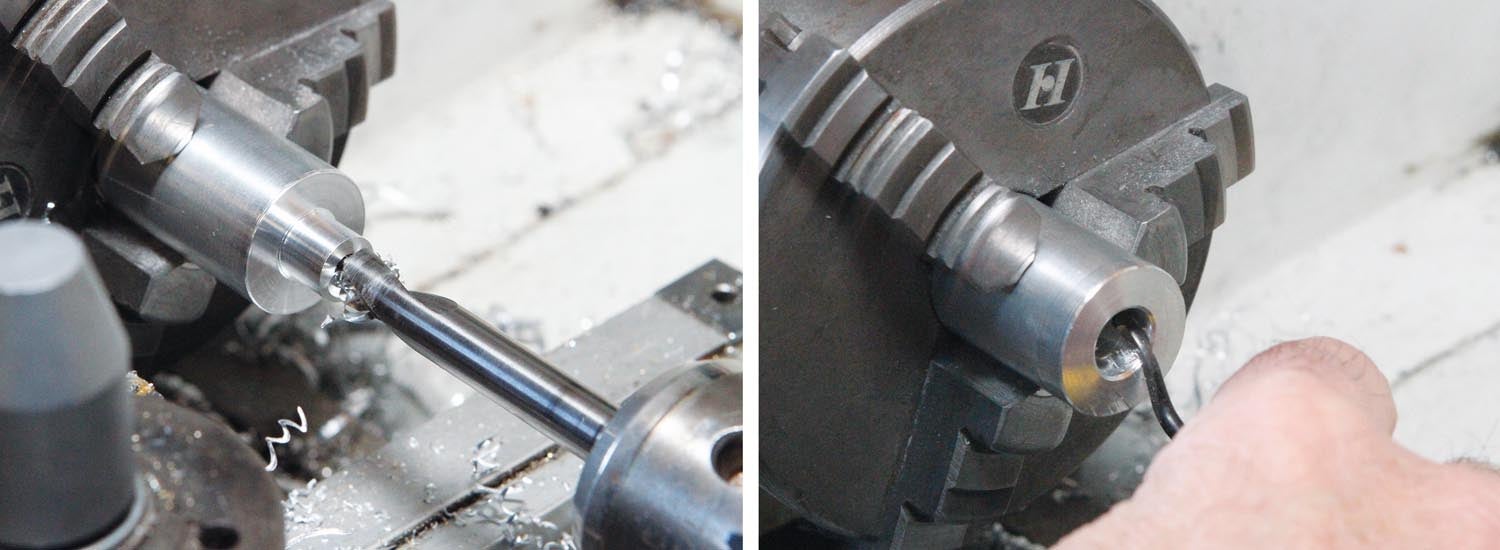
The deadline to turn in this column was before we had a chance to see how it works. The hope is, everything should slide together without much, if any, force. But, just in case, we’ll have our shop-made press ready to go. I’ll post an update on the KITPLANES® website to let everyone know how it turned out.
That’s it for now. Time to get back in the shop and make some chips.