I’ve done quite a few first flights for new builders. I lost count when the number went over 40. Most of them have been completely uneventful, with the new builder thoroughly enjoying the fruits of their labor and experiencing their airplane in flight for the very first time. I do my very best to ensure the flight is completely theirs, with my only function being to step in for an emergency or unsafe condition. I will do coaching, such as “Increase the climb attitude,” as the sight picture is new for most builder-pilots.
The biggest part of the preflight briefing by me is that I always expect them to keep their eyes out the window and not get distracted by any alarms that may be going off in the cockpit. I assure them that I have responsibility for anything that happens inside the cockpit, and I will quickly advise as to the urgency and/or need for any action.
Among all the first flights, there have been some common themes. As I have no doubt they are occurring on other first flights, some of the more common themes should be shared.
What’s That?
We were performing the first flight on an RV-10 on which I had been the DAR. (I won’t test fly an aircraft if I haven’t been the DAR, as I want to thoroughly examine it first.) The usual briefing had occurred, with the reminder for the builder to keep his eyes outside. Just about the time we lifted off, we got an audible oil pressure warning, followed immediately by the pilot asking, “What’s that?” With the reminder to keep looking outside, I saw the oil pressure was at 90 psi, which is normal for a Lycoming engine at full throttle, especially on the first takeoff of the day. I responded, “Continue, no factor.”
My usual flight profile on first flights is to immediately turn 30° to 45° off runway heading once we are past the point of landing straight ahead. This makes for an easier turn-back to the departure runway in the event of an engine failure. Of course, this takes into account that the turn is not over populated areas versus an open area straight ahead. Each first flight requires understanding the local geography.
Just as he made the turn, I glanced at the airspeed indication and saw that it was all dashes. Hmm. Takeoffs in an RV-10 are quite fast, and breaking ground usually occurs in less than 500 to 600 feet with two people on board. I had called “airspeed alive” at the first indication and then hadn’t looked at it again.
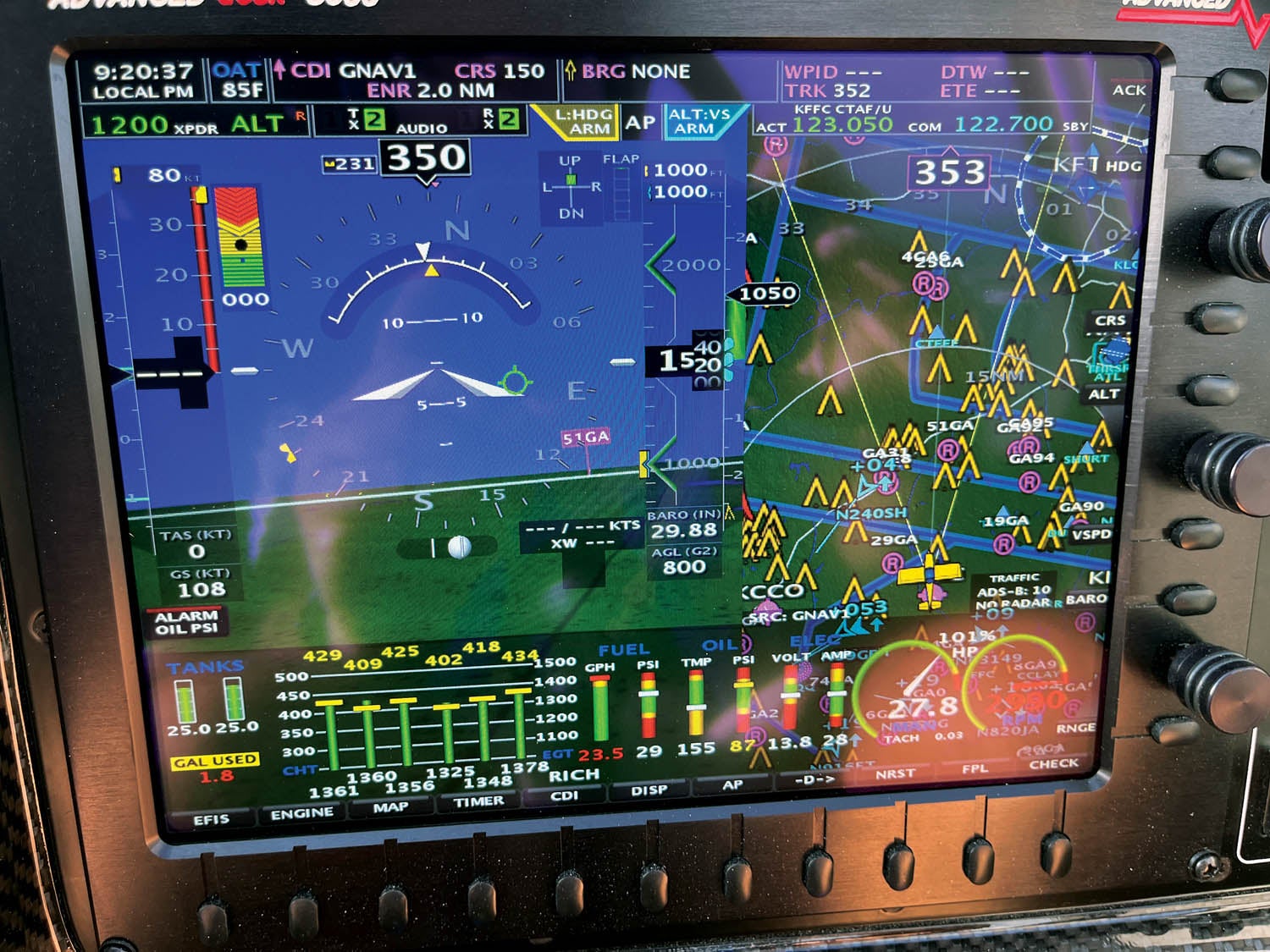
I pointed out that the airspeed was no longer indicating on either of the two EFISes or the G5. My guess was that we had a broken/disconnected pitot line or a plugged pitot tube. Groundspeed was working and the winds were calm, so I pointed out we had groundspeed and would continue the flight in order to break in the engine. We proceeded to climb over the airport to our planned altitude of 3000 to 3500 feet to be able to keep 75% power applied to the engine. About that time, we got our second audible warning regarding the CHTs, and again I stated, “No factor, continue.”
Trim Trouble
A couple of minutes after we leveled off and temps had stabilized, I looked over at the pilot expecting to see a big grin. Not so. He had a weird look on his face and I asked, “What’s wrong?” He said it was taking all his strength to hold the stick back. It was then I noticed both of his hands were on the stick in a death grip. I stated, “My controls,” and sure enough, there was a huge amount of back pressure required to hold the stick. I immediately reduced the power to almost idle and the aircraft slowed, drastically reducing the back pressure. It was clear we had an out-of-trim situation. Had the trim circuit failed? This could certainly be the scenario. I gingerly tapped the trim button on the stick grip, watching the indication on the EFIS, as well as feeling the pressure changes in the stick. Interestingly enough, the trim circuit indicator moved opposite the direction I expected it to, and the trim pressure on the stick was opposite as well! So, once I identified that it was just a backward circuit, I increased the power and we continued the flight for approximately an hour.
What really annoys me as a DAR is that I have seen way too many elevator trim circuits wired backward, with some pilots even arguing with me as to the expected direction of the trim tab. So, I always ask the builder to sit in the cockpit and activate the trim switch for Up and Down while I watch the trim tab. I had done that on this plane and it had moved correctly. It appears the builder had moved the switch opposite the normal direction when I asked him to activate it. Now I verify that the builder is moving the switch in the correct direction!
Bad Alarm Parameters
Here’s the big common theme I recommend all builders who have installed an EFIS or engine management system with audible alarms take to heart prior to that first flight. Many of these devices come with engine parameters already preset. From experience, I will tell you that many of them are wrong and will be a distraction on the first flight. Some may need to be reset after the engine breaks in, but for that first flight, you will want to set the ranges for a little more tolerance, especially with a new engine.
In the next Diagnosis column, I will give you a recommended range for all the engine parameters based upon my first flight experiences, as well as a recommended range for continued operation once you are out of Phase I testing.
Having no unwarranted distractions during the first flight really does keep the fun factor alive!
By the way, post-landing troubleshooting found that the pitot line and the angle of attack (AOA) line had been crossed at the junction where they enter the fuselage. Rectifying that allowed for normal airspeed indications on the second flight.
Dynon sells the pitot connection kit that includes different color air hoses for the AOA, pitot, and static sources. This will reduce the chance of mistaking the air sources during the build
Yep, they were there.