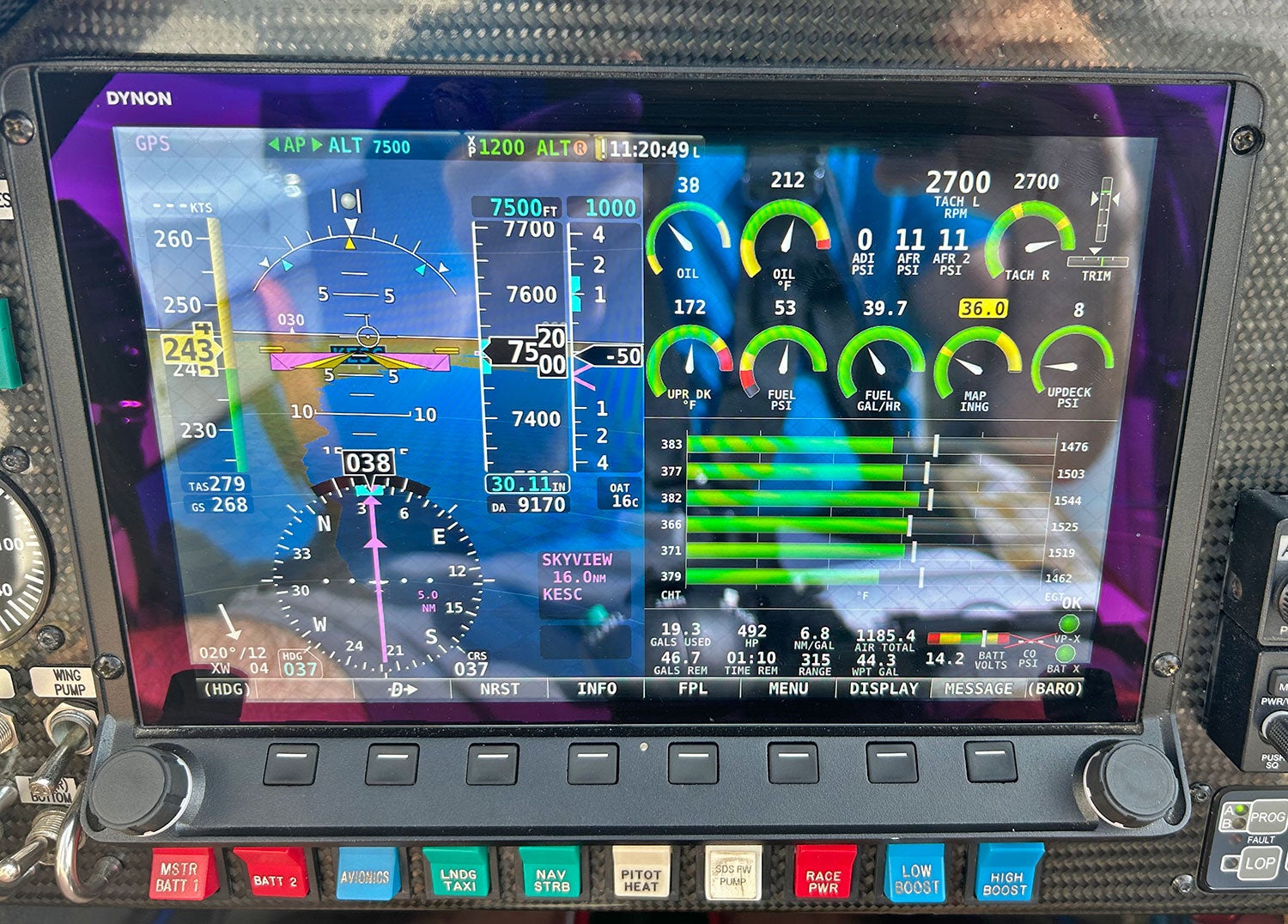
During the AirVenture Cup point-to-point race last Sunday front runner Andrew Findlay suffered a major engine failure in his One Moment Racing Lancair Super Legacy. Fortuitously he was almost over the third turn point, the airport at Escanaba, Michigan and was able to glide to a windmilling landing there.
Coincidentally we were also participating in the race as co-pilot in Tim Slater’s Glasair III and heard Andrew’s radio calls as he managed his descent. With over a decade of Sport Class racing experience Andrew can claim a distressingly large number of engine out landings, so while never routine, he at least can draw on previous knowledge. Asked how many of the suddenly quiet glides he’s made he said, “I’m in the double digits now. I’m either doing something right or something wrong!”
The initial assessment is somewhere between a broken crankshaft or similar malfeasance in the rear or accessory section of the Continental IO-550. A more definitive answer awaits engine teardown. This is the same race engine Andrew ran at Reno last September at over 90 inches of manifold pressure and 900 horsepower, meaning it has been highly stressed and subsequent mechanical failures, while not a certainty, are hardly surprising.
Disappointingly to us, rumors began circulating at Air Venture that Andrew’s engine failed due to detonation. These, at best, ignorant remarks likely got started because Andrew was running UL100E unleaded gasoline produced by Lyondell/VP Racing, one of the fuels currently in PAFI testing.
Always transparent with his race data, Andrew and Lyondale/VP Racing Fuels gave a seminar today at AirVenture as well as personally reviewing his engine data with us. The short answer is there is no possibility his engine was detonating during the Air Venture Cup. This event, unlike the short, very high power pylon races at Reno is a 400 mile point-to-point event run at more endurance-oriented and certainly fuel conserving settings. So, where Andrew would run over 90 inches at Reno, he was was running 35 inches and 2700 rpm during the AirVenture Cup.
Furthermore, Andrew’s Continental is modified to survive 100 inches of manifold pressure, including a 6.5:1 compression ratio, ADI and spray bar water cooling. All of these factors contribute to detonation resistance, and after bore scoping and reviewing Andrew’s extensive engine data logging the facts unambiguously show the power settings, temperatures and pressures (all normal) simply would not support detonation with any fuel approaching 100 octane.
Andrew’s summation of the event was while cruising level approximately 60 miles from Escanaba at 35 inches and 2500 rpm with all pressures and temperatures in the green, “I got a really bad audible [engine] noise [metallic].” He pitched for best glide, reduced throttle and rpm initially rose to 3200 rpm indicating the propeller governor was no longer on the job. Later, reviewing the data logging showed a 4 psi oil pressure drop just before the engine failure.
While windmilling down Andrew checked throttle response and the engine did run, but without rpm control and much metallic noise, so he switched off the ignitions. The CHT’s cooled quickly in the glide, but the oil temperature continued to rise, suggesting high friction somewhere.
Post landing the engine would rotate by hand, but with 10 degrees of backlash and not smoothly. Bore scoping looked normal but the oil is full of metallic sparkles.
Like Andrew, we’re awaiting an engine teardown for a detailed determination of what let loose. But after what this engine has been through any mechanical decoupling is no surprise.