Two hours’ drive east from Prague, across rolling green countryside and along poppy lined roads, lies Vysoke Myto, a quiet Czech town that is home to the production facilities for JMB Aircraft. For 20 years, the factory has produced the VL3, a sporty and fast two-seat retractable with a composite airframe, generating hundreds of airplanes that fly mostly in Europe.
Purchased by Jean-Marie Guisset in 2012, the Belgian company’s development has centered on refining the airframe design and its production facilities. JMB improved the efficiency of the wing and refined the interior and avionics, while marrying the airframe to ever more sophisticated and powerful Rotax engines. These changes turned a niche airplane into a serious two-person cross-country machine. In fact, JMB boasts a nonstop westbound crossing in a VL3 between Reykjavik, Iceland, and Goose Bay, Canada, on the way to EAA AirVenture last year.
Building on this success, the company announced the completion of a 21,000-square-foot final assembly building adjacent to its local airport in October 2023. However, the story of this upstart aircraft producer took an unexpected turn in 2022 when JMB agreed to a partnership with Evolution Aircraft, with ambitions to apply their existing production expertise to the much larger and heavier turbine-powered four-seat speed machine with pressurization.
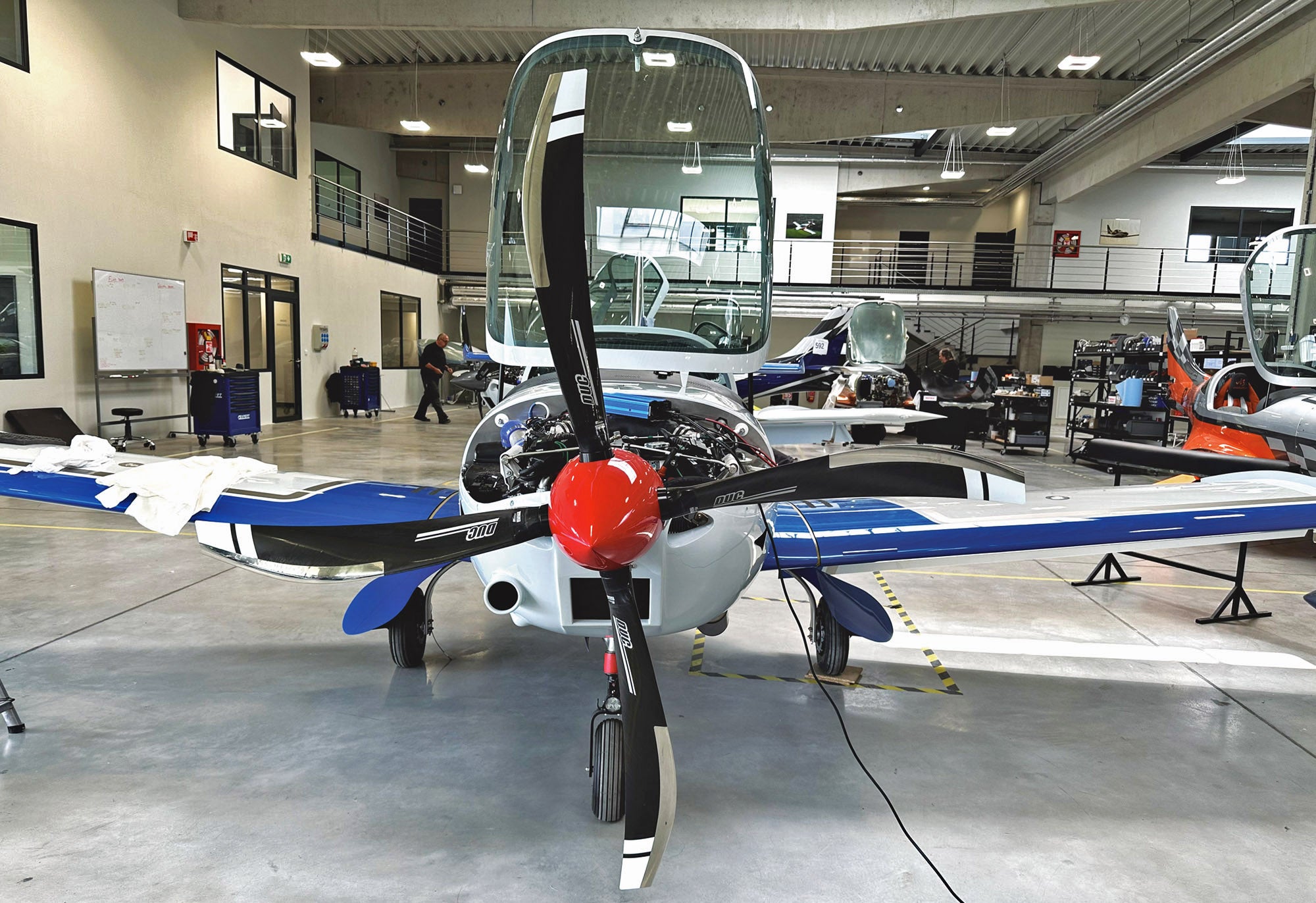
Evolution Aircraft was founded by Bob Wostenholme in 2003. Bob leveraged his prior ownership of Lancair to design and construct the Evolution; its first flight took place in 2008. This aircraft is in many ways the ultimate expression of what is possible in the owner-built world. Unlike the Epic LT, whose design ultimately transitioned into a certified aircraft, the Evolution remains a highly complex to construct, but highly capable, Experimental design. Indeed, after two high-profile accidents, the build quality challenges of selling kits for construction in multiple shops around the United States were unmasked. To address these concerns, Evolution aircraft centralized their production to one exclusive facility in order to guarantee uniform standards. Their stated goal is to achieve certified aircraft build quality in the Experimental market.
Initially, the plan was to build the Evolution in its existing facility in Redmond, Oregon. Given Oregon’s long tradition of working in composites, this seemed the logical place to consolidate the Evolution’s efforts. However, considerable resources were needed to produce this sophisticated aircraft but without the economies of scale that come from producing a large number of aircraft per year. Enter JMB Aircraft, a company already producing composite aircraft in substantial numbers—their current production line targets 75 VL3s rolling out of the factory each year.
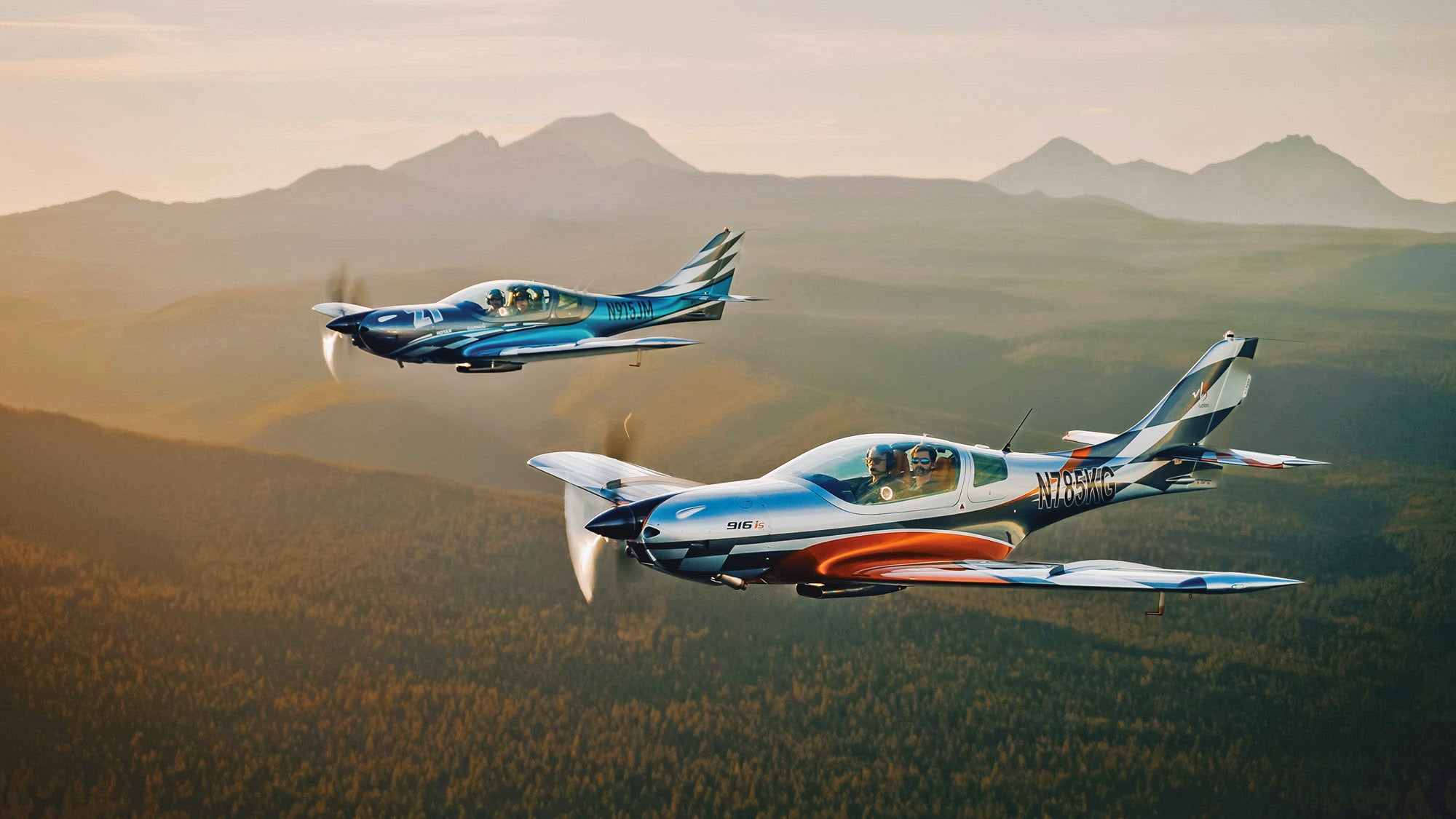
Market Changes Coming
JMB Aircraft has ambitious expansion plans that should be facilitated by changes in the U.S. market. Currently, the VL3 can be registered as an Experimental aircraft in the U.S., but with the expected adoption of MOSAIC by the FAA at some point next year, this should allow the plane to be certified in the new category fully built. Currently in Europe, where there are hundreds of examples flying, the company is limited to a 600 kg (1320 pound) gross weight.
When every kilogram counts, the company has refined its composite work to an exacting degree. In fact, they have often swapped production airframes for European builders with U.S. ones (if the U.S. one next on the line is a little lighter), as U.S. experimental aircraft are not subject to this weight restriction.

The performance and efficiency of the VL3 and its aesthetic appeal are its chief selling points. When installed with the latest Rotax 916 iS engine, this two-seat aircraft boasts a cruise speed of greater than 200 mph and a useful load of 517 pounds, all while staying at or slightly below the magic maximum total weight of 1320 pounds. Freed from the current LSA and Microlight limitations, the VL3 can go to 1653 pounds at max gross.
With its steady introduction to the American market, the capabilities and efficiencies of the Rotax-powered VL3 are becoming more widely known. This has led JMB to invest in new facilities near its old factory in the Czech Republic directly at the airport. Their new final assembly building gleams in white. The structure was built with the owner experience in mind.
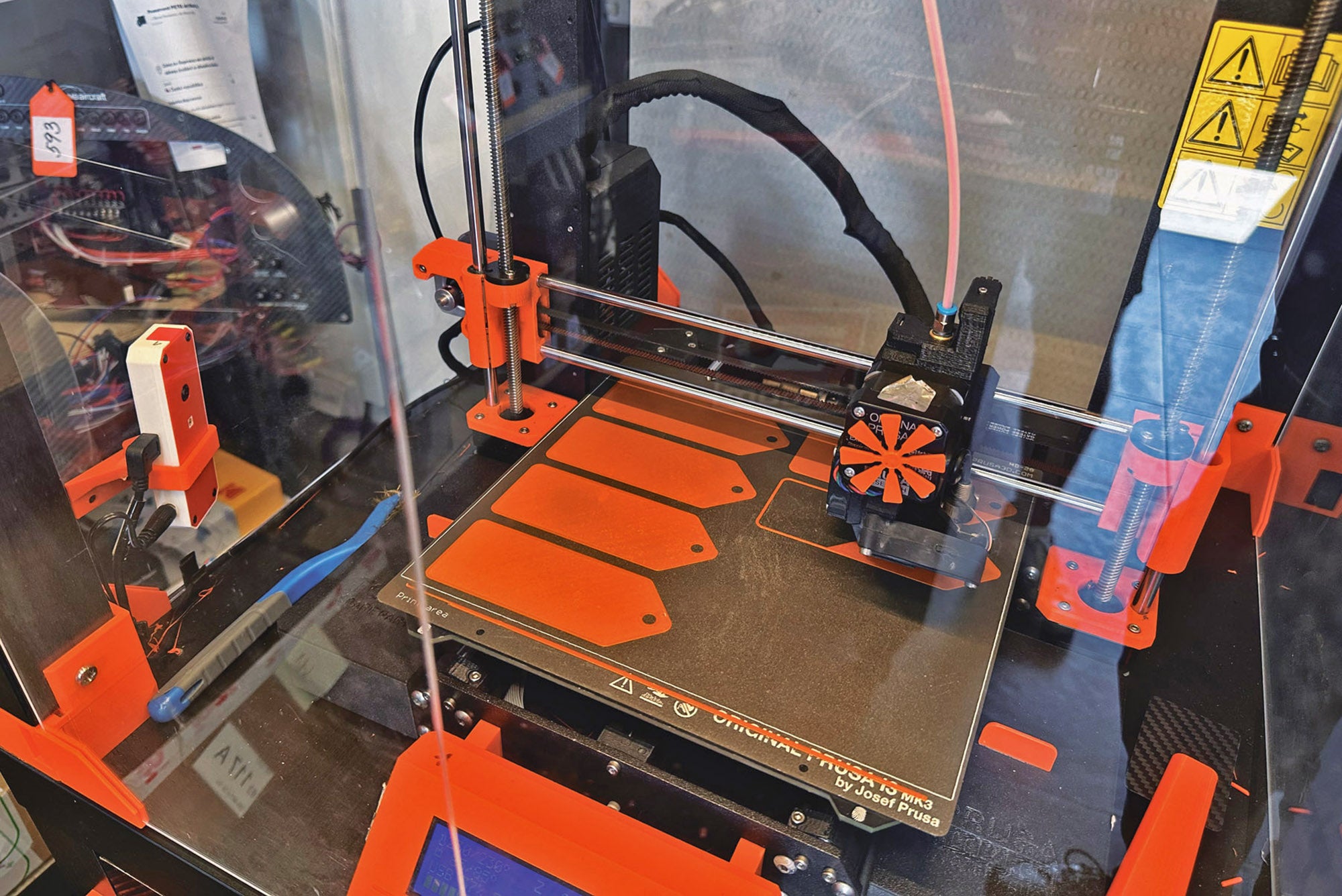
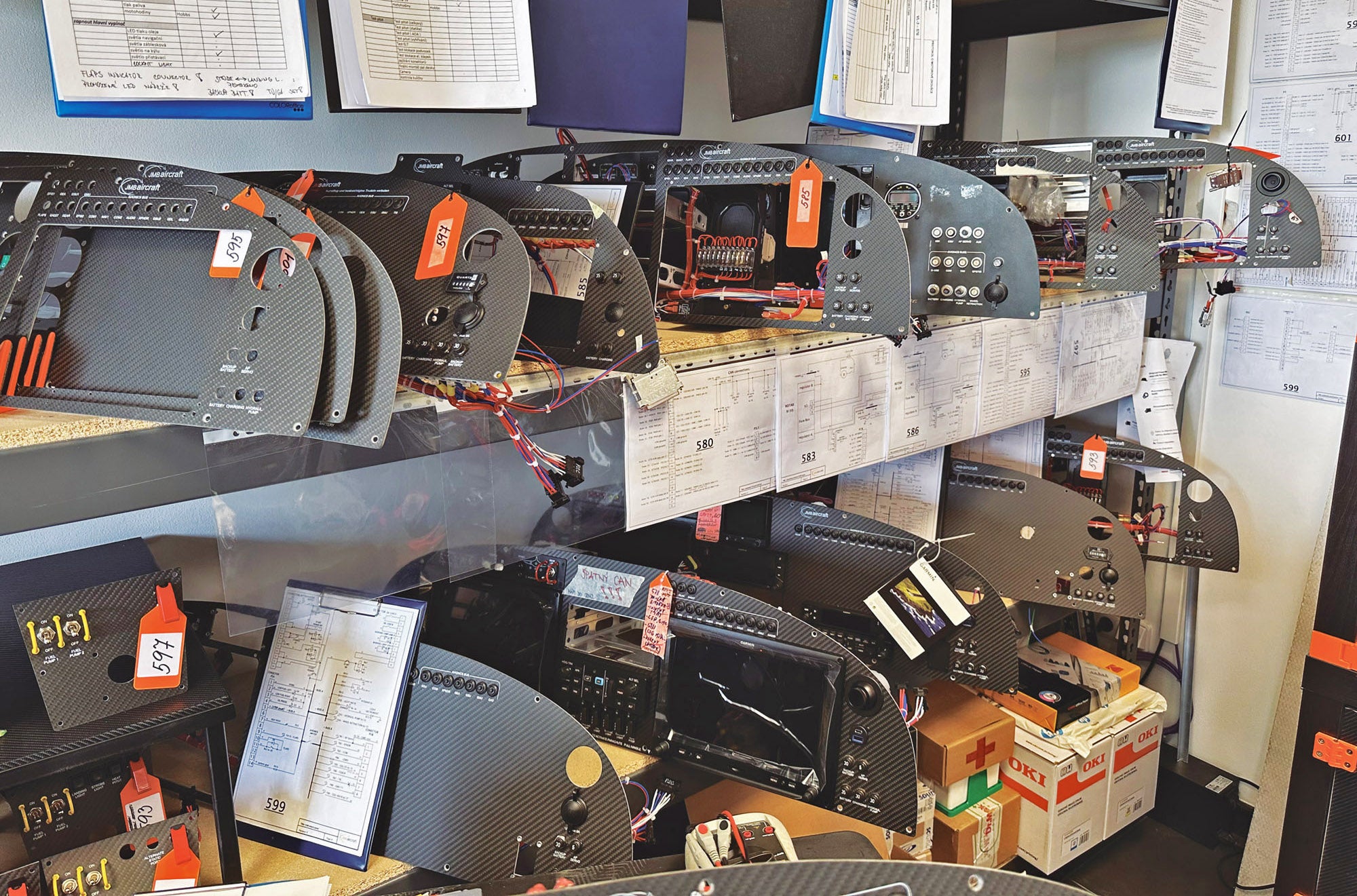
There are offices for customization and design meetings. The production floor is lined by a terrace where construction can be viewed from above. There are no fewer than 25 aircraft on the production floor, being fitted with their avionics, landing gear components and control surfaces.
The avionics shop is just off the production floor and the walls of the avionics department are papered with the customized panels for each owner/builder’s airplane. The custom-cut carbon fiber panels line the shelves of the shop, all in varying states of completion. JMB Aircraft has plans as well to build another 43,000-square-foot adjacent structure within the coming years, moving more of the production line to their new space and allowing a larger portion of the old factory to be used for development of the Evolution.
A short 10 minutes’ drive across town, and away from the airport, lie JMB’s original factory buildings. These are repurposed Communist-era structures, fully outfitted for each stage of composite aircraft production. These buildings are much rougher around the edges than the company’s new facility. Their low-slung anti-aesthetic architectural style reminds one of the bygone era in which they were built. However, once inside the buildings, the most modern wet composite molds and frames fill the space, wherein workers are busily applying layers of resin and sheets of carbon fiber.
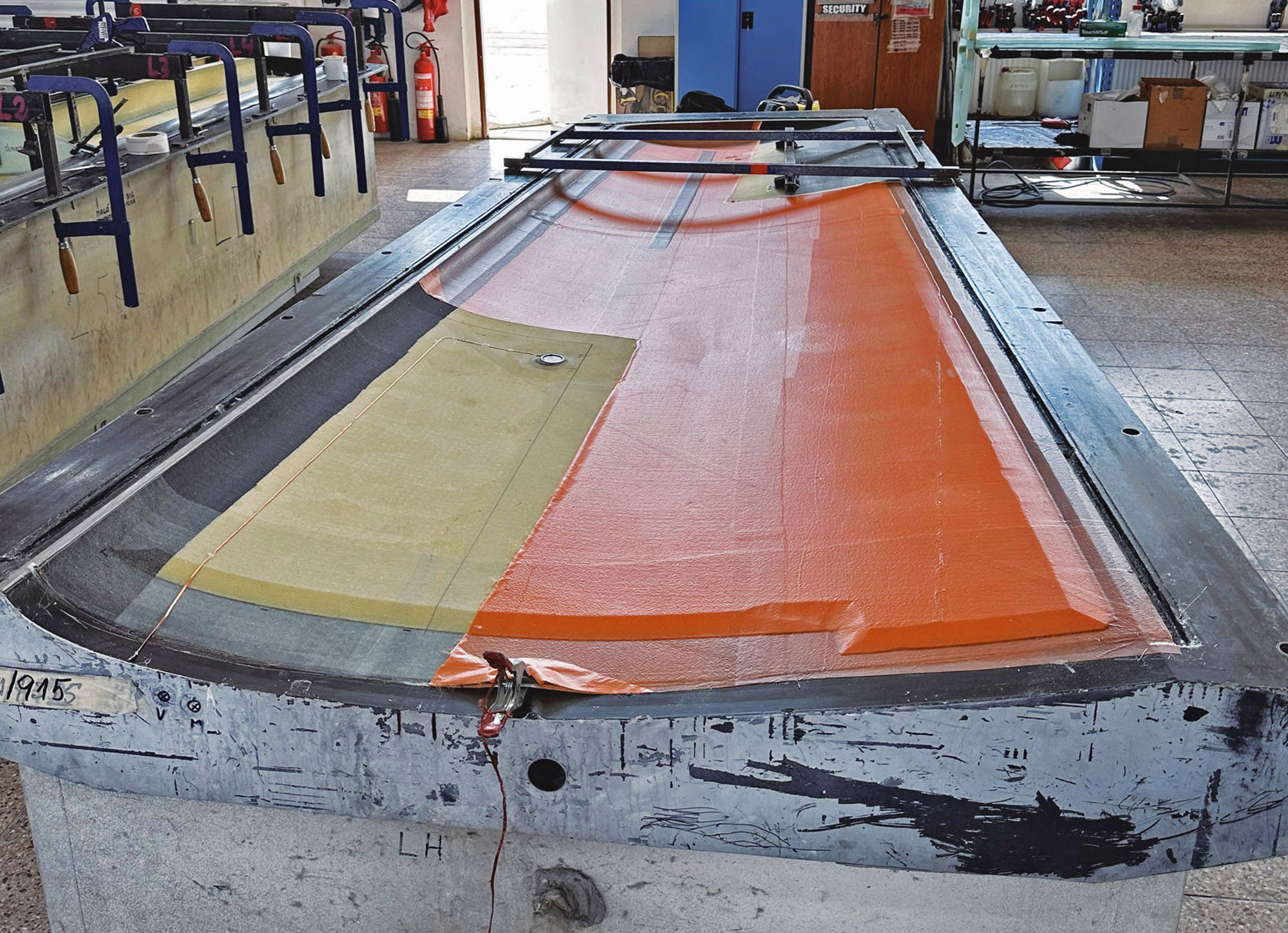
JMB Aircraft employs 165 people, many of whom work to create the fuselage and wings, shaping, sanding and fitting each piece to the most exacting standards. This part of the facility also houses the paint and clear coat rooms, where each custom design is masked and painted. To save weight for the European market, no two colors are ever overlaid. The paint is applied with such precision that it is impossible to feel the transition from one color to the next, creating what is perceived to be a perfectly smooth surface to the touch.
There is even space within the factory for the complete production cycle for aircraft interiors. The interior shop walls are lined by rolls of different colored leather and spools of seemingly hundreds of different colored threads, while the leather workers cut and stitch their patterns one seat at a time.

Walking farther through these cavernous facilities, one arrives at the comparatively quiet and sparsely staffed Evolution production area. The Evolution is impressive by any measure. Fitted with a 750-shp Pratt & Whitney PT6A turboprop, owners can expect cruise speeds of 290 knots, lifting a useful load of almost 1900 pounds. All that performance can be had for an estimated build cost of between $1.6 to $1.8 million.
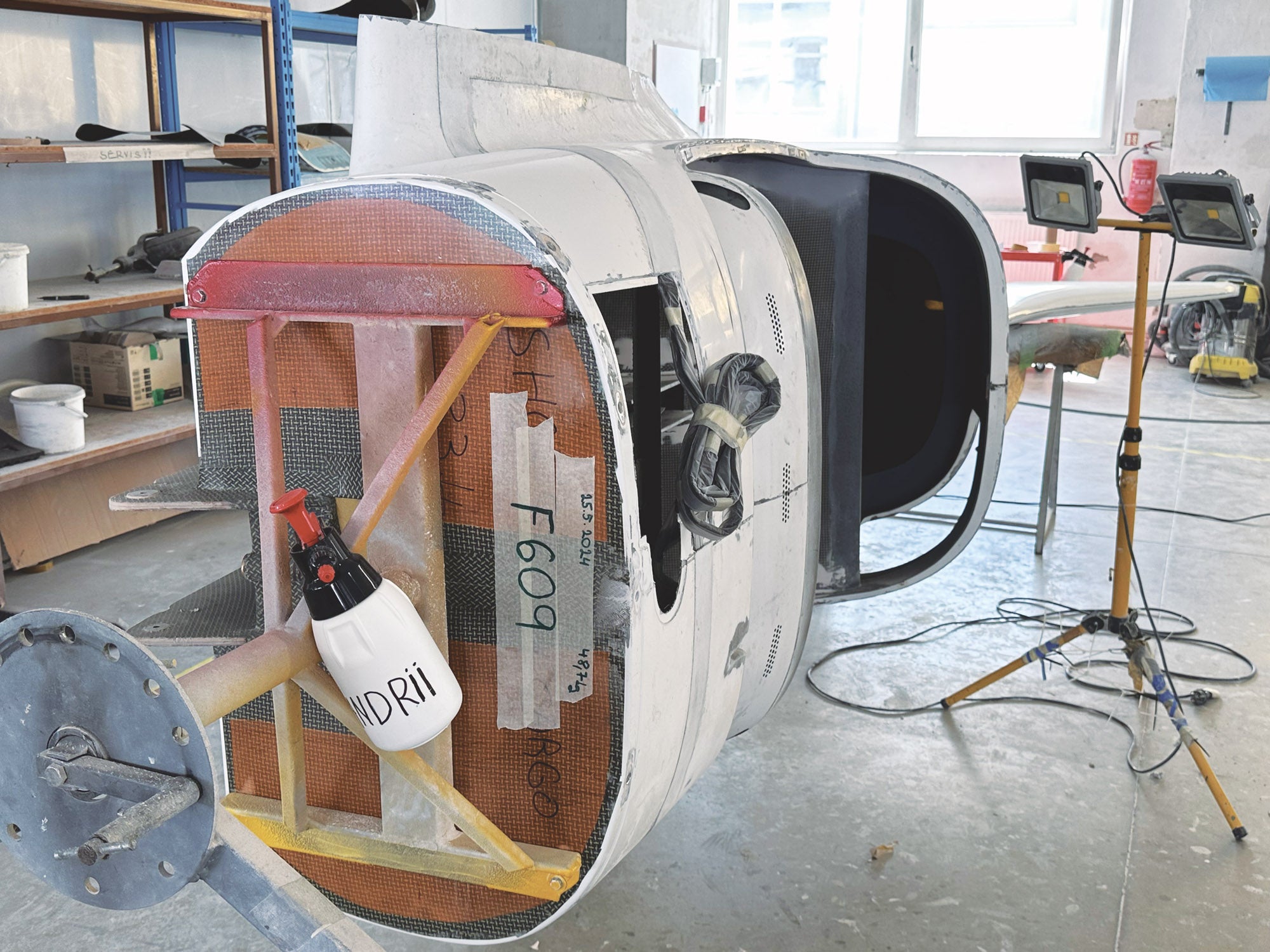
The company currently has two airframes under production. The pre-impregnated (pre-preg) composite work on the Evolution requires a different skill set from the VL3’s wet-laid carbon fiber, and the company rotates the original composite artisans from Redmond to the Czech Republic in three-month blocks to complete this work. The fuselage of each Evolution appears massive in comparison to the dozens of much smaller VL3s on the line.
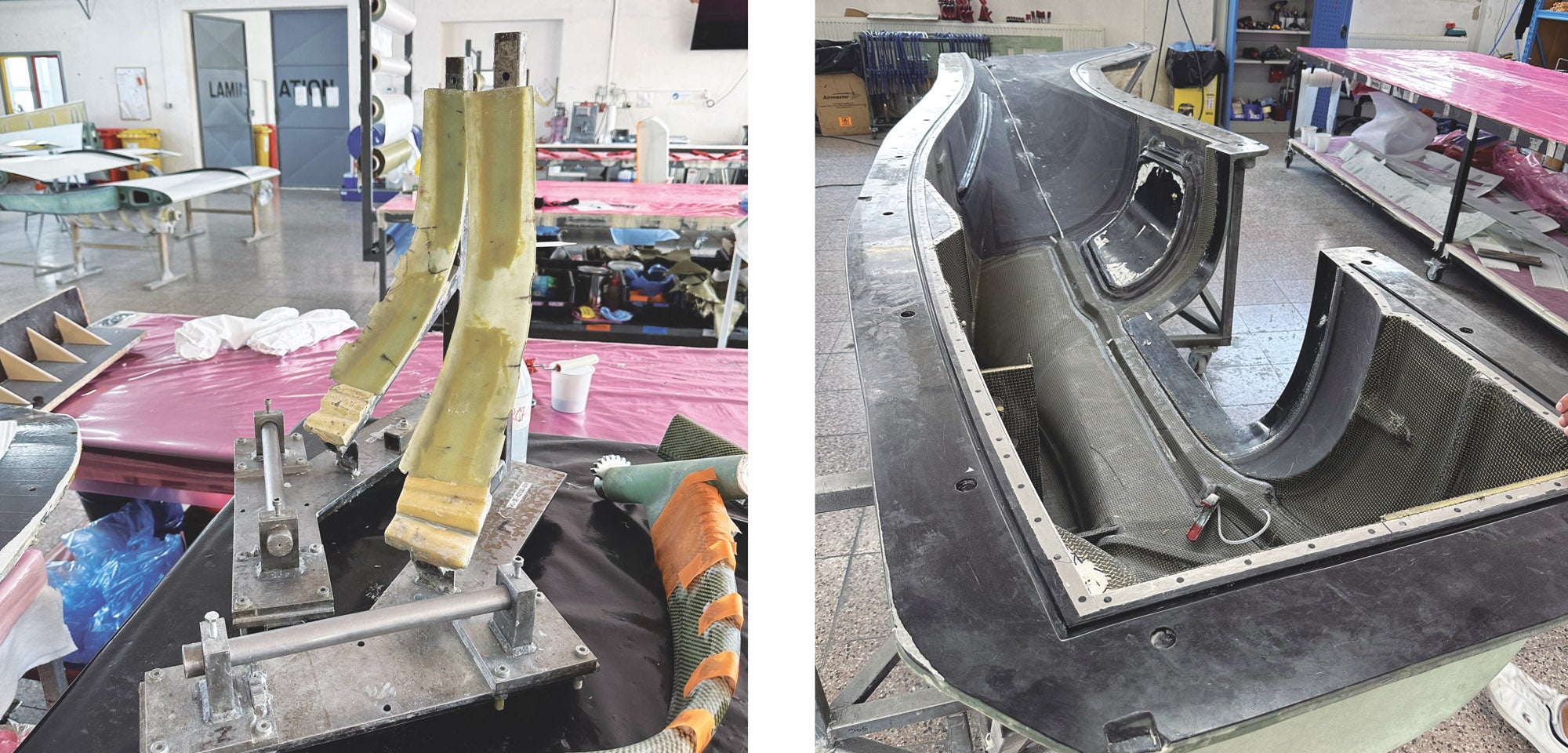
Currently the company is building two Evolutions for existing customers, and those two imposing black carbon Evolution fuselages are far from completed. Their two brand-new Pratt & Whitney engines sit untouched in their crates on a rack not far from their future airframes.
But, after crating and shipping its molds and tooling from Oregon to Europe, the line is now up and running. Evolution Aircraft plans to shepherd these two fuselages through each subsequent stage of the production process on the VL3 line to establish the workflows needed for a full production line. Once the highly skilled composite work is completed, Evolution Aircraft plans to have its owners participate in a shared building process that should take around six weeks of steady work to complete. This would satisfy the “major portion” rule the FAA requires while still ensuring construction standards that approach the certified world. After refinement of the full production cycle, including developing the schedule for the owner-built parts of the process, Evolution Aircraft expects to meet significant demand in the U.S. market.
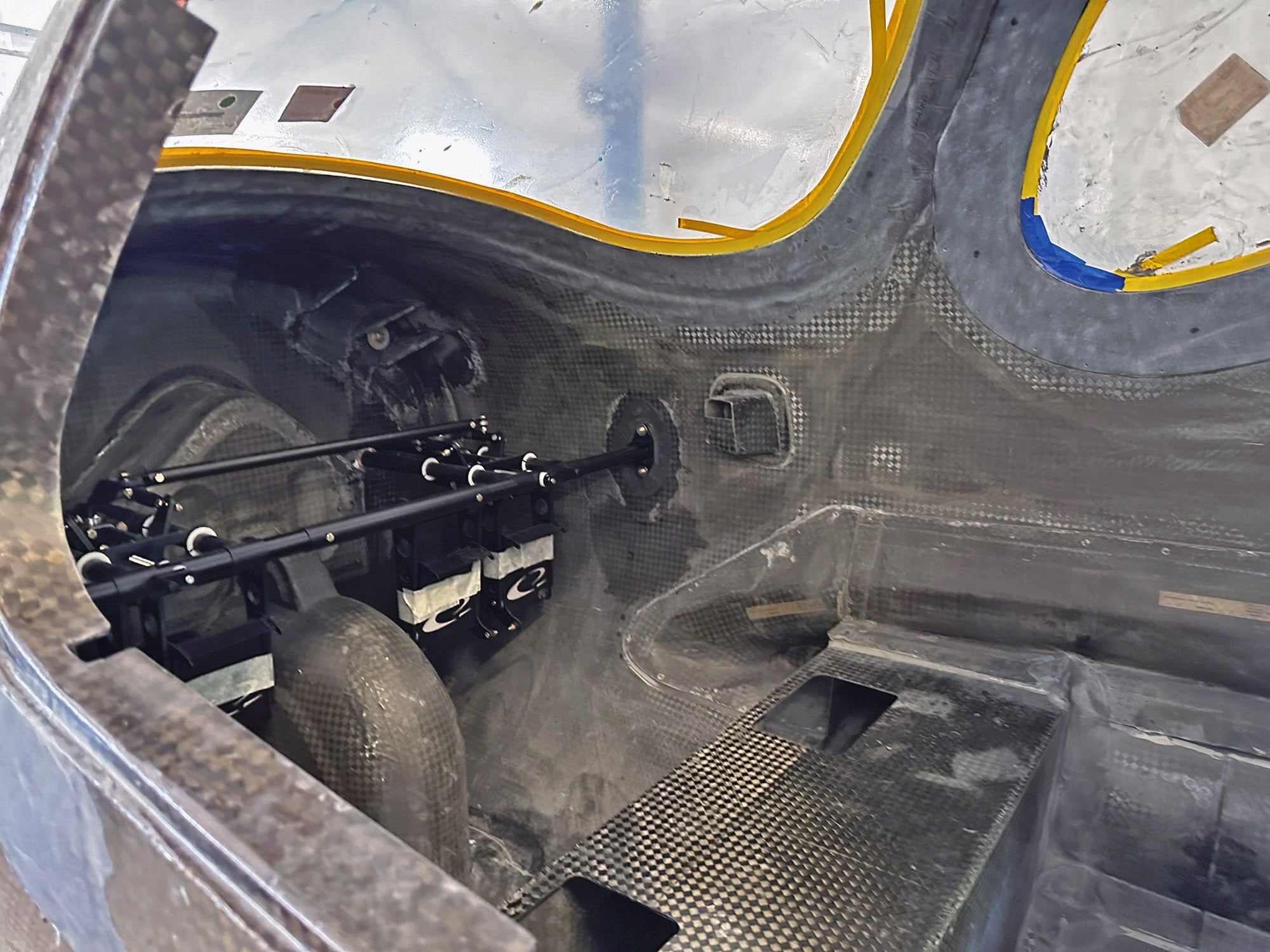
The prospects for the future of the joint Belgian-American company building airplanes in the Czech Republic appear bright. Already, 75 VL3s are flying off the production line each year and with the prospect of MOSAIC, there will likely be considerable demand in the American light sport market as the capabilities of the aircraft become more well known. As for the Evolution, the marriage of a capable design with the production resources and professional build quality of JMB Aircraft offer a clear and clever path forward.