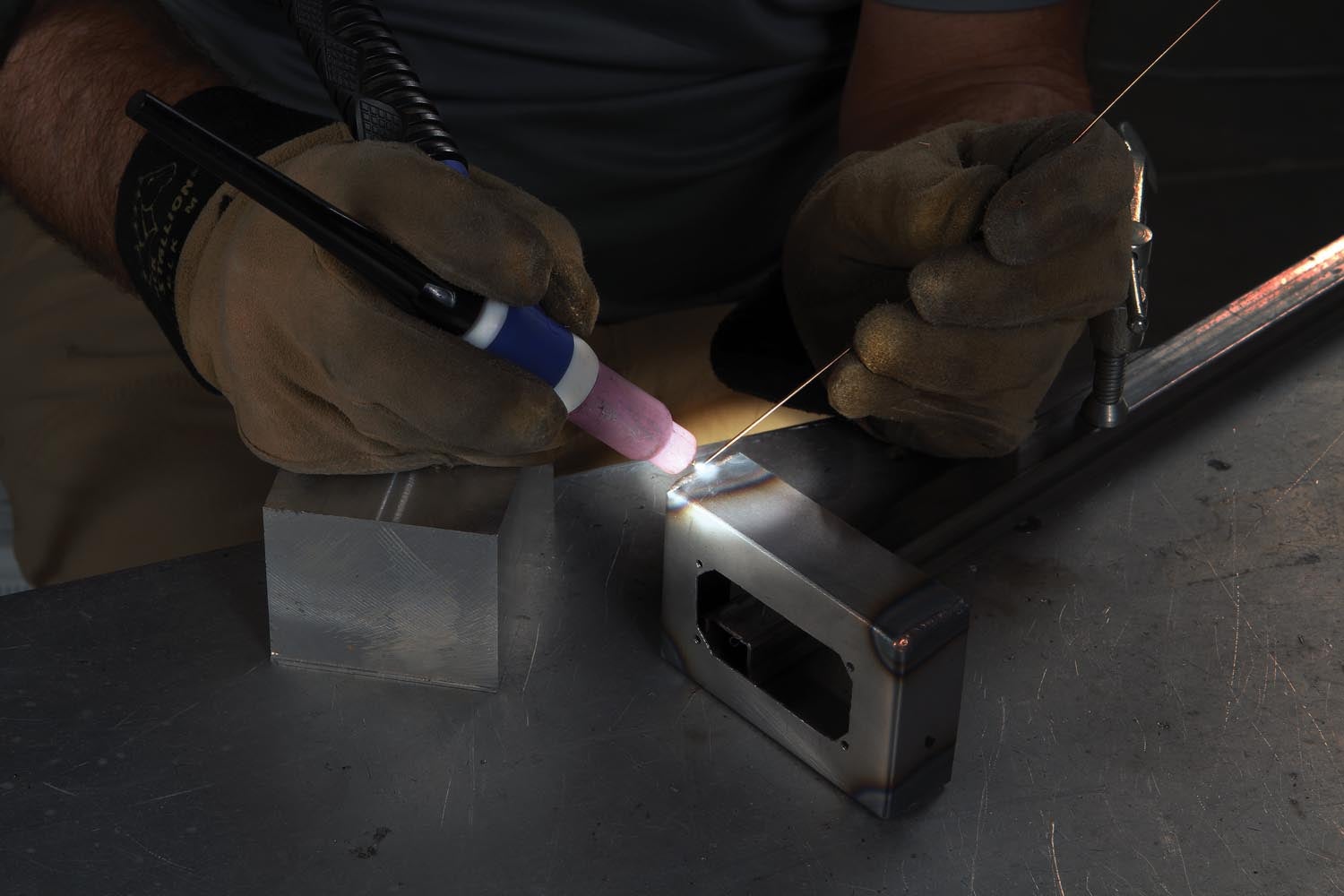
Last summer I had the chance to get some hands-on experience with TIG brazing. Other than a YouTube video or two, I knew next to nothing about it. My tutor, Mr. David from Lemoore, California, covered everything from the TIG machine settings, his favorite torch and why he’s using TIG brazing instead of TIG welding for an ever-increasing number of projects.
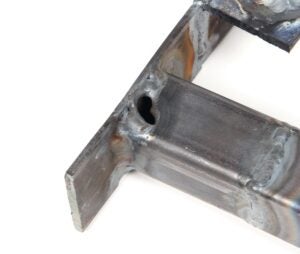
The first thing to know is brazing and welding are two different things. Welding, as opposed to brazing, is the joining of metals by fusing two or more parts into one. Most aircraft welding is done with either tungsten inert gas (TIG*) or an oxy-acetylene gas rig. In either case you heat up the base metals to create a small molten puddle, then rhythmically daub filler rod into the puddle as you progress along the seam. Brazing is sort of like hot glue for metal. While you do heat up the base metal, you don’t melt it or try to make a puddle. Once the joint is heated (but not melted), you daub the brazing rod, which has a lower melting point than the base metal, into the joint. For decades, if you wanted to braze, you needed an oxy-acetylene torch rig. Which was fine if that was your welding rig. But for most 21st century home shops, if they have a welding rig, it’s more likely to be a MIG or TIG machine than an oxy-acetylene rig. The development of specialized filler rod for both TIG and MIG means that brazing is a viable (and fun) option for home shops with those machines.
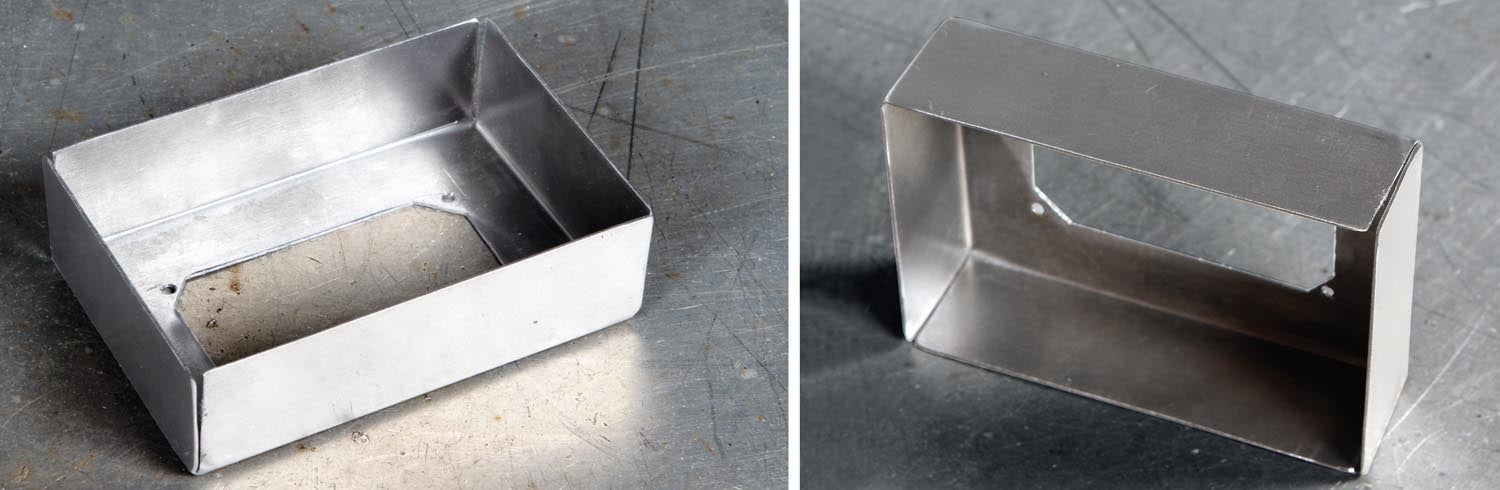
When to braze instead of weld depends on the job. For me, TIG welding thin sheet metal has always been problematic. Actually it’s not problematic—it’s impossible. I’m fine with steel 0.060 inch (16 gauge) or more thickness. Depending on the joint design, I can sometimes weld material as thin as 0.048 (18 gauge). An overlapping joint is usually OK. But a butt joint, forget it. I usually end up, eventually, if not immediately, burning through, which ruins both the weld and the part. The issue is, of course, one of practice and experience. I simply don’t weld enough on thin material to gain the necessary proficiency.
So when David demonstrated how easy it was to run a bead and get a clean “weld” on super-thin 0.028-inch (22 gauge) steel, I knew that TIG brazing had my name all over it.
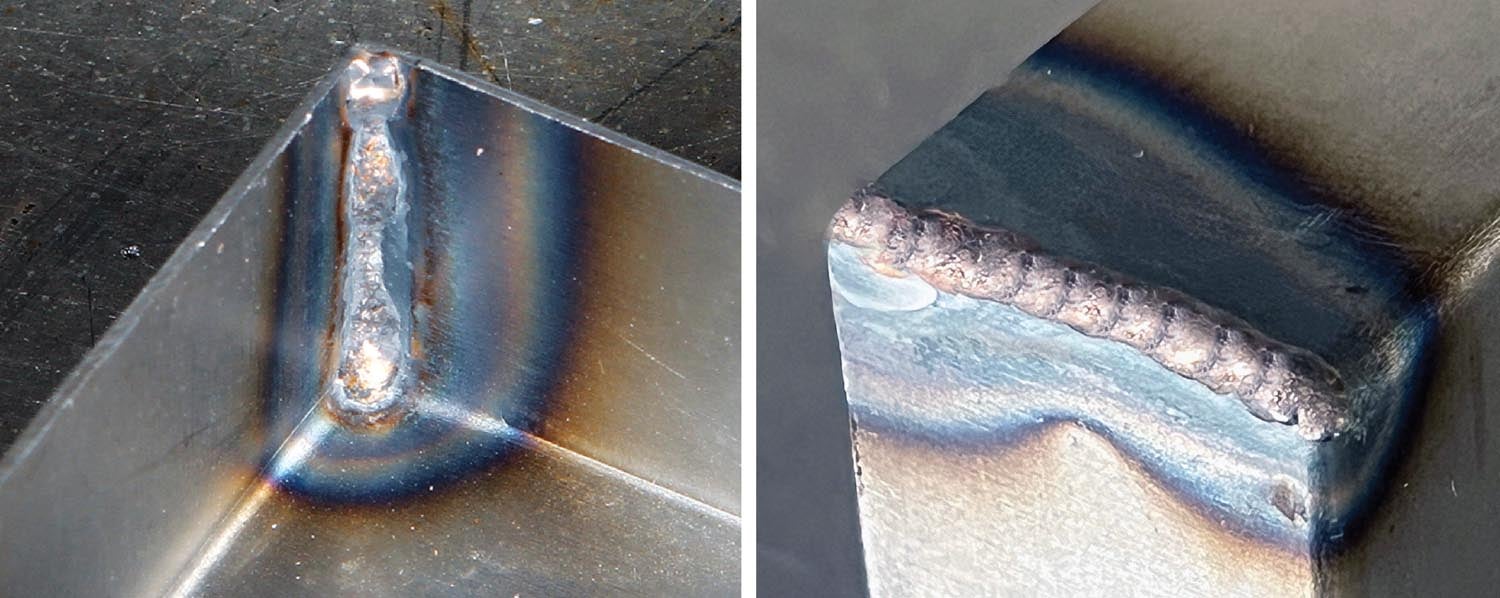
Although there doesn’t seem to be much application for it in kitbuilding, another advantage of TIG brazing with silicon bronze is the ability to join incompatible metals. You would never dream of welding copper to steel or steel to titanium. But it’s possible with TIG brazing. Yes, the joint is weaker than a normal welded joint, but it could be more than sufficient for nonstructural applications.
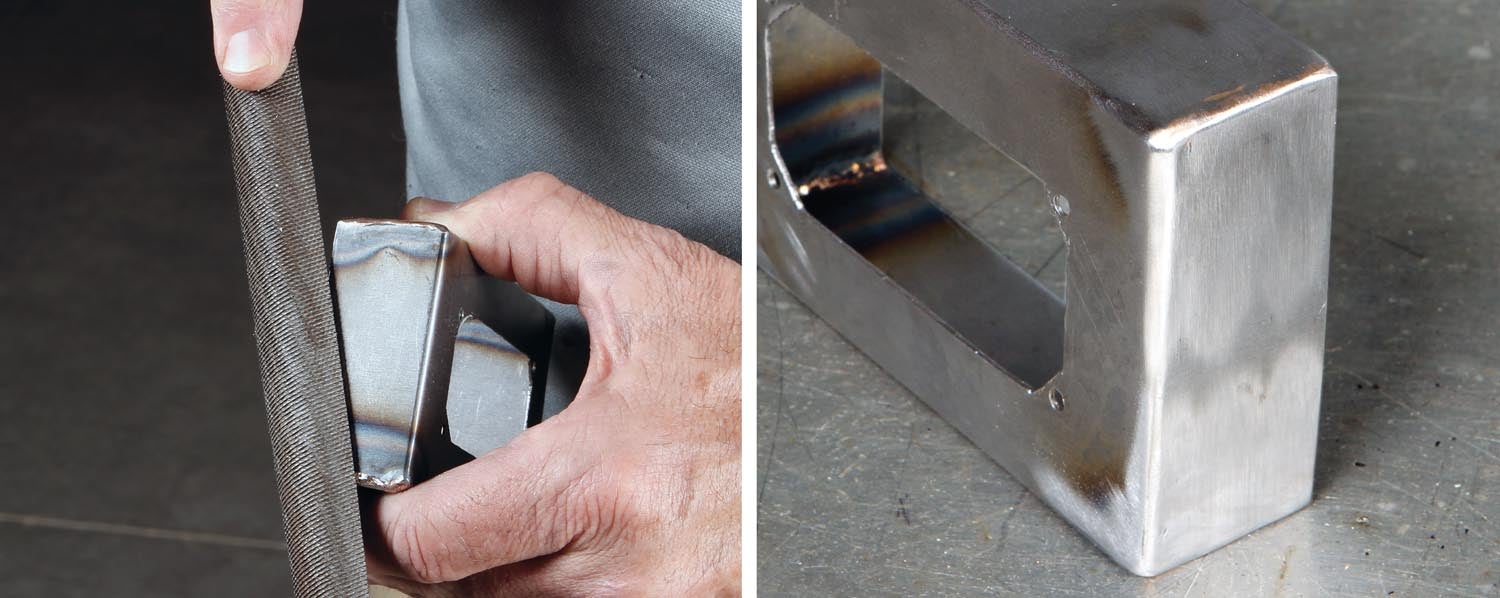
The final tip for successful TIG brazing is to clean and prep the surfaces to be brazed. Any dirt or grease will more than likely prevent the braze material from flowing into the joint. Also, watch the heat. If the base metal melts and mixes with the braze, the joint will be compromised.
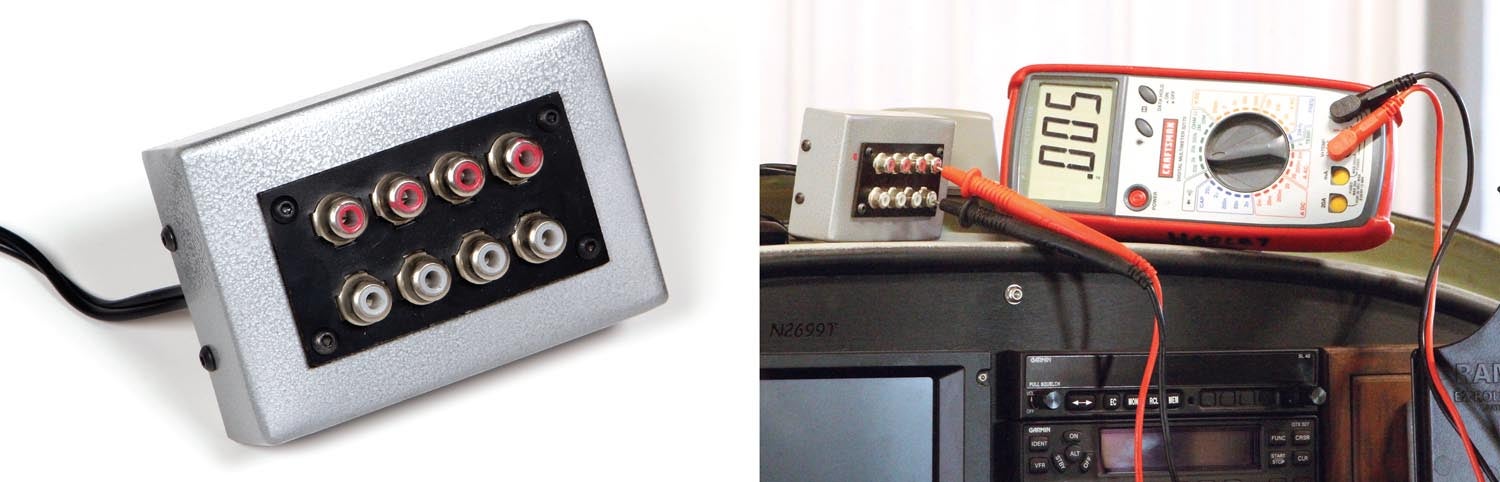
Silicon brazing is also a potential option for MIG welding machines. For more information, check out Silicon Bronze MIG Brazing Basics. That’s it for now. Time to get out in the shop and make some chips!
*The American Welding Society’s formal designation for TIG is gas tungsten arc welding (GTAW). But everybody just calls it TIG.