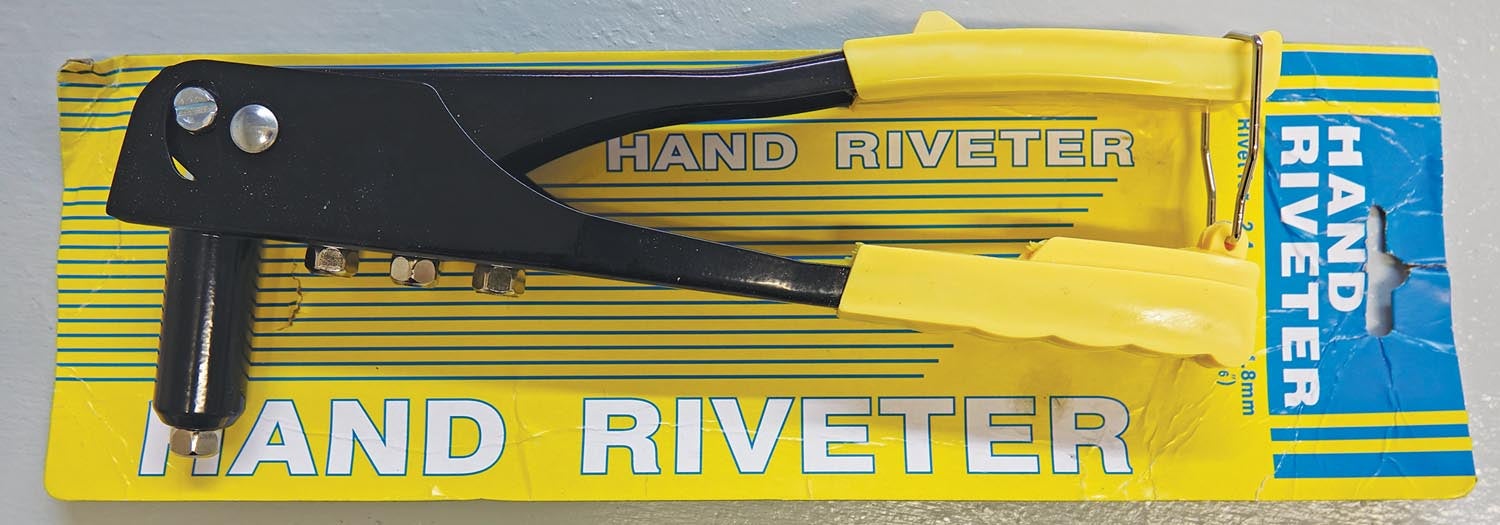
While building my Panther tail kit, I came upon this note in the assembly manual in the elevator joiner photo: “This rivet is impossible to install with the head showing. You can install with the tail showing or leave it out.”
We pilots are a detail-oriented bunch. Double that for pilot-builders. We can’t have 13 rivets facing one way and one rivet facing the “wrong” way, can we? And we can’t deliberately leave a rivet out—we’d never be able to sleep, even knowing that it’s structurally perfectly fine without that 14th rivet.
So what’s the alternative? Well, it’s just the size of common blind-rivet tools that makes this particular placement impossible, so a more compact tool could overcome the limitation. It’s likely there are other places, in other kits, that have similar restricted spaces where this could come in handy.
Since such a tool would only be used in rare instances, in very limited spaces, it wouldn’t need to be a fast tool. Even if it took a minute to pull one rivet, that would be better than the insomnia-inducing alternatives.
So here is a blind-rivet tool you can fabricate that greatly reduces tool space requirements.
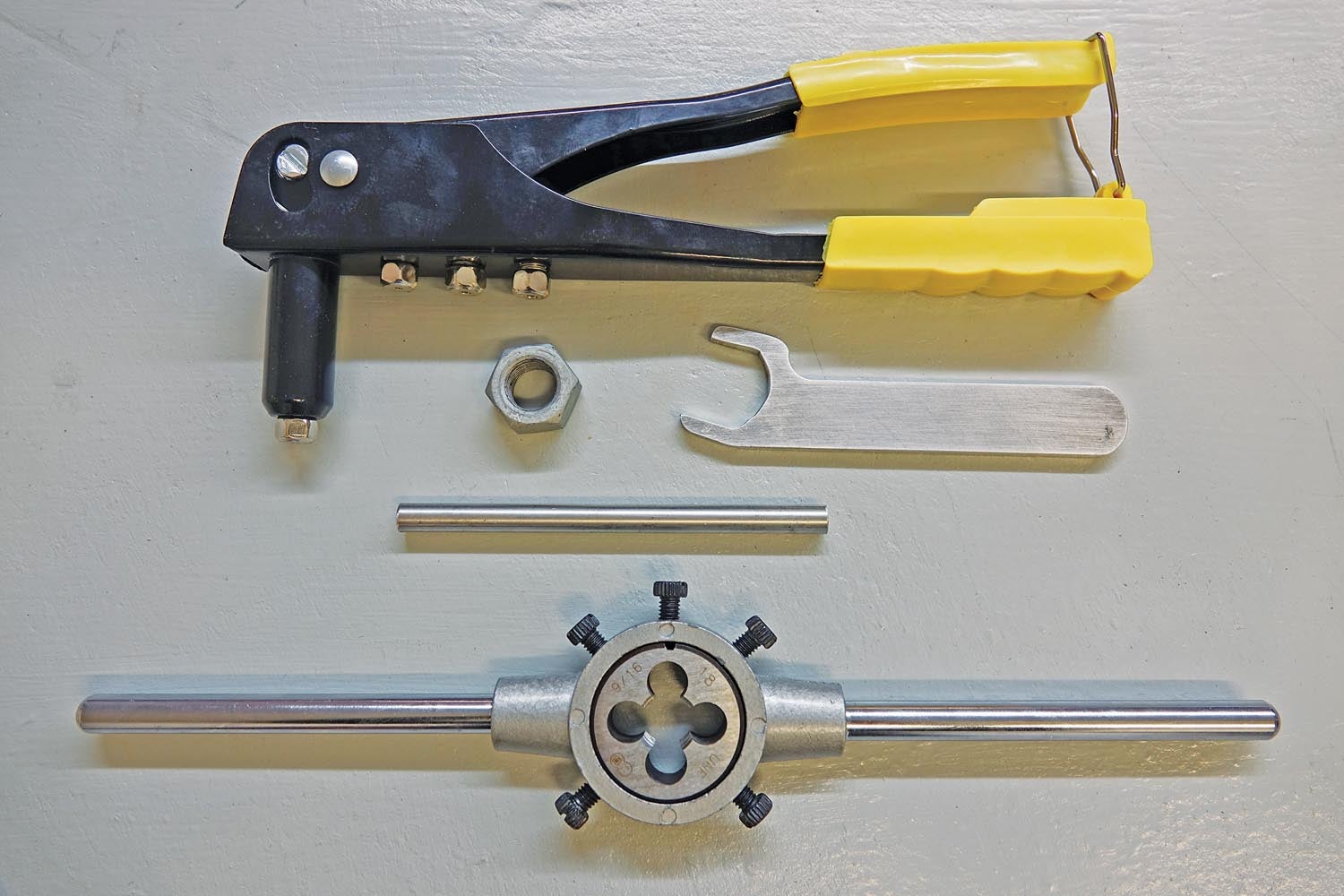
Most of the needed parts are cannibalized from an inexpensive off-the-shelf blind-rivet tool. You can usually find one of these on eBay for as little as $12.
In addition to the cheap blind-rivet tool, you will need:
- One 9/16-18 UNF threading die and handle
- One 9/16-18 UNF hex nut
- One 4-inch length of 5/16-inch steel rod
- One 7/8-inch open-end wrench
To disassemble the blind-rivet tool, rotate the pivot pin 180° to disengage from the internal spring. Push the pin out, being careful of the spring as it may fly out.
Remove the pull-tube from the barrel. Remove the gripper jaws, jaw-pusher and spring from the pull-tube.
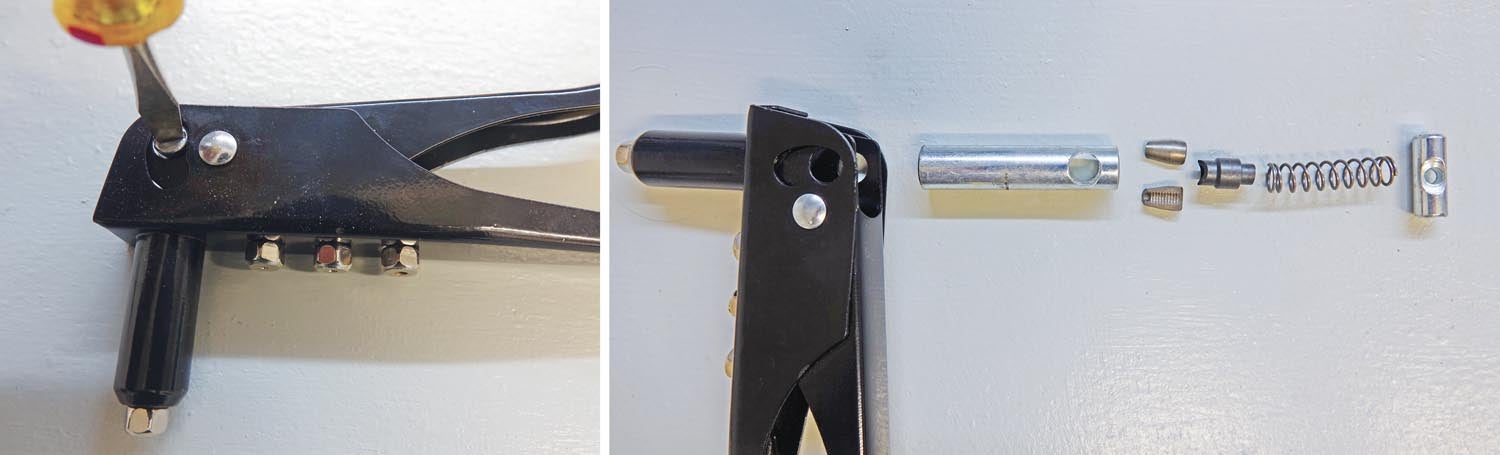
Most of these tools seem to use nearly identical parts, but check to make sure the pull-tube on yours has a diameter of approximately 0.530 inch. This is close enough to nominal for a usable 9/16-18 external thread.
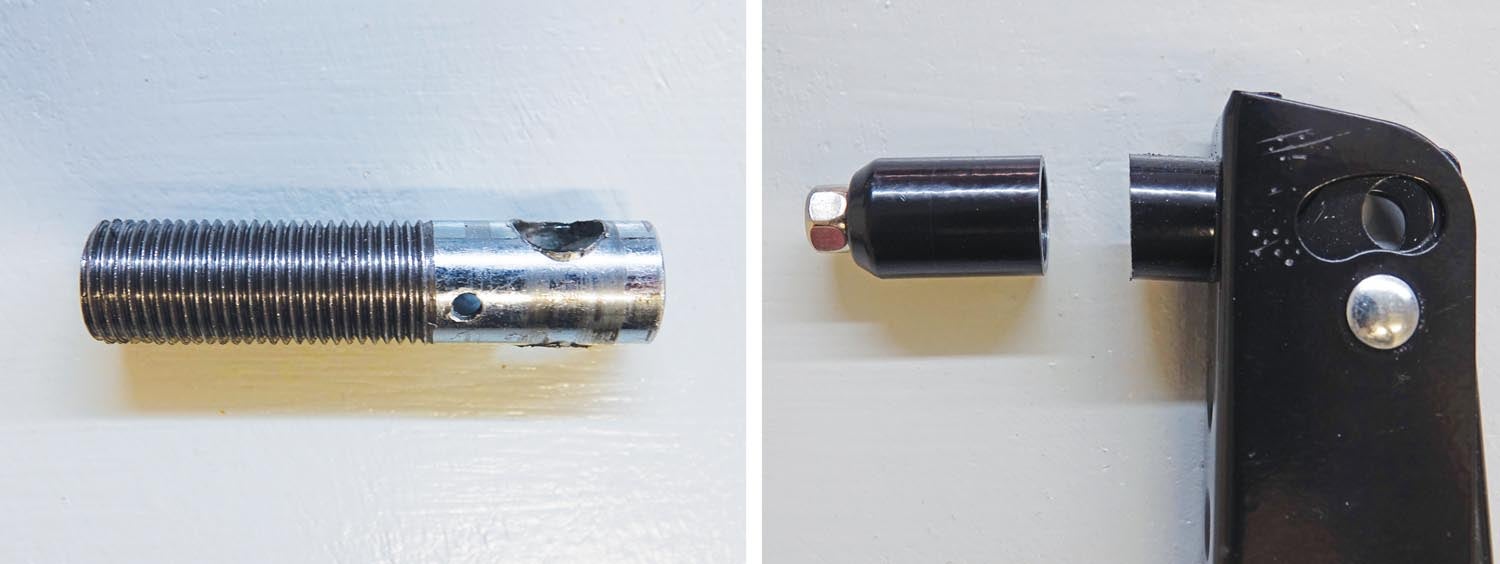
Use the 9/16-18 die to thread the lower 11/2 inch of the pull-tube. Cut the barrel off to a length of 1-1/8 inch.
Reassemble the gripper jaws, the jaw-pusher and the spring back into the pull-tube. Compress the spring and insert the steel rod through the hole. Lightly grease the threads of the pull-tube. Spin the hex nut all the way onto the pull-tube. Install the appropriate-size nosepiece onto the barrel if not already installed. Slide the barrel onto the pull-tube.
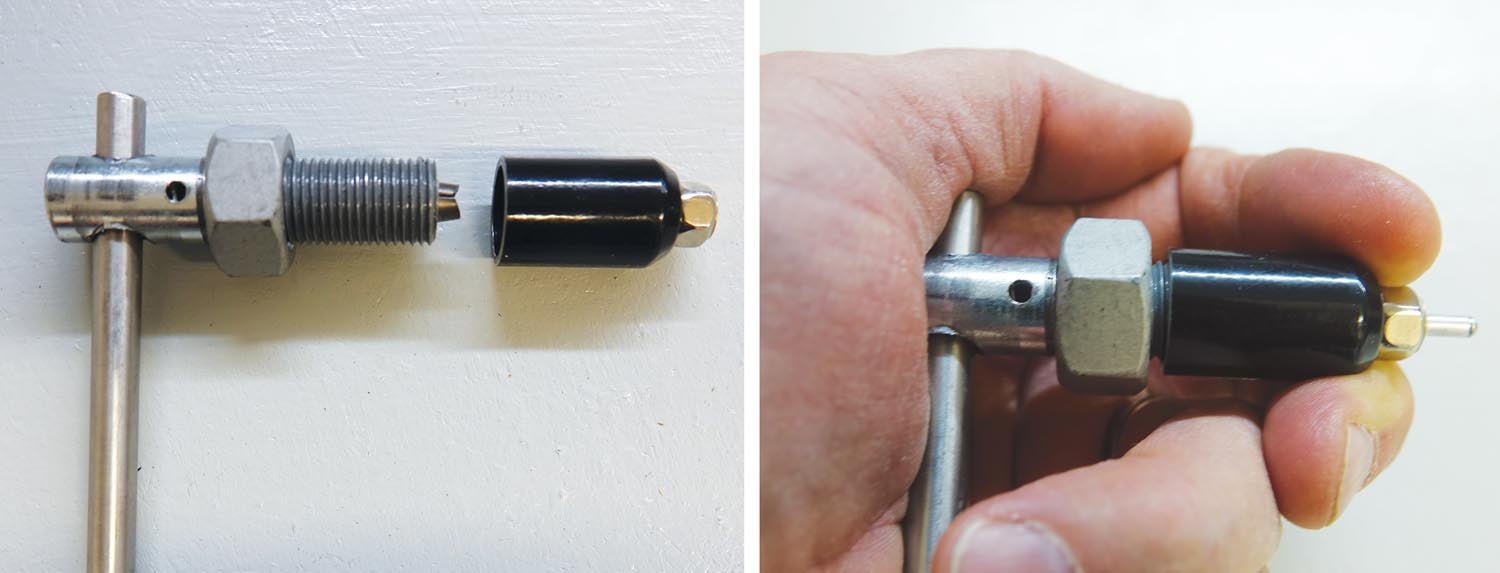
Pull the barrel against the spring pressure toward the hex nut. This will cause the jaw pusher to open the jaws. Insert a rivet into the tool.
Position the rivet in the “impossible” hole. Use the rod to hold the pull-tube stationary while turning the hex nut clockwise with the 7/8-inch open-end wrench.
Use your shortest 7/8-inch wrench or shorten one if it’s too long for the space you’re working in. Or you can make your own open-end wrench. I made a crude one from 3/16-inch thick aluminum. The torque on the tool to pull a rivet is pretty small, so the wrench does not need to be super strong. In some locations a 7/8-inch crowfoot wrench might be useful. Continue turning until the stem breaks. Done!
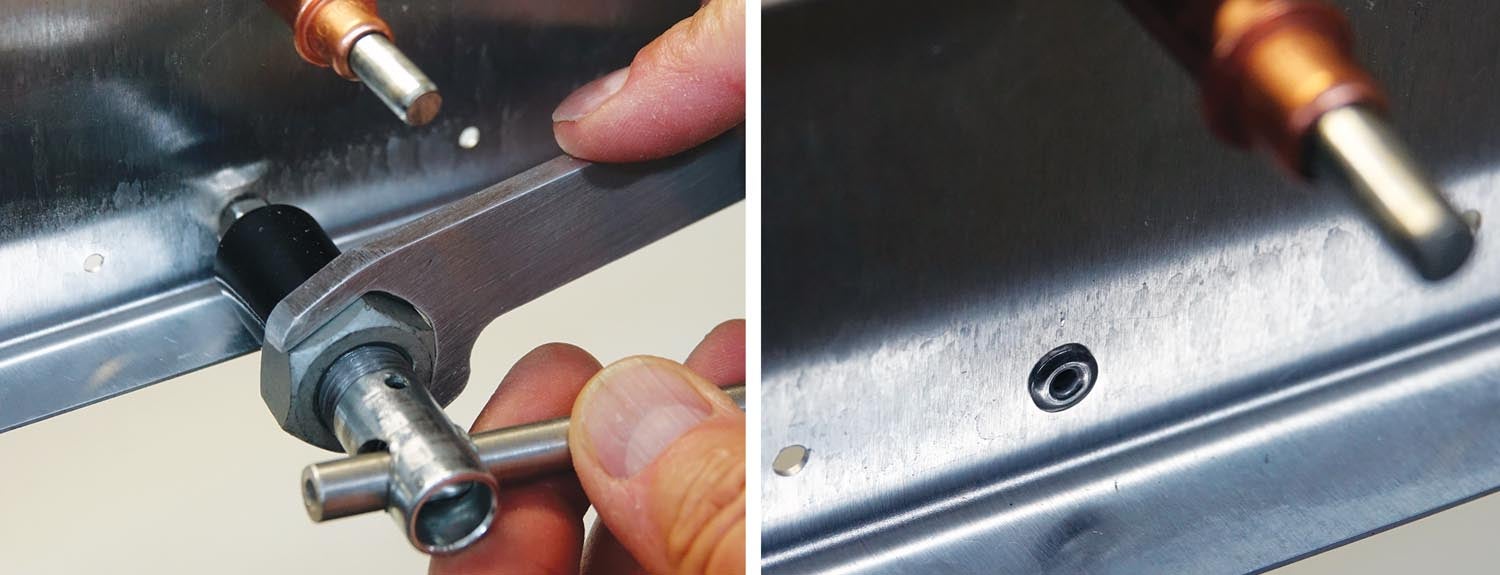
To release the rivet stem, spin the hex nut all the way back up the pull-tube, then pull the barrel toward the hex nut as before to open the jaws. Sometimes the impossible has workarounds!
What a great idea! thanks for sharing.