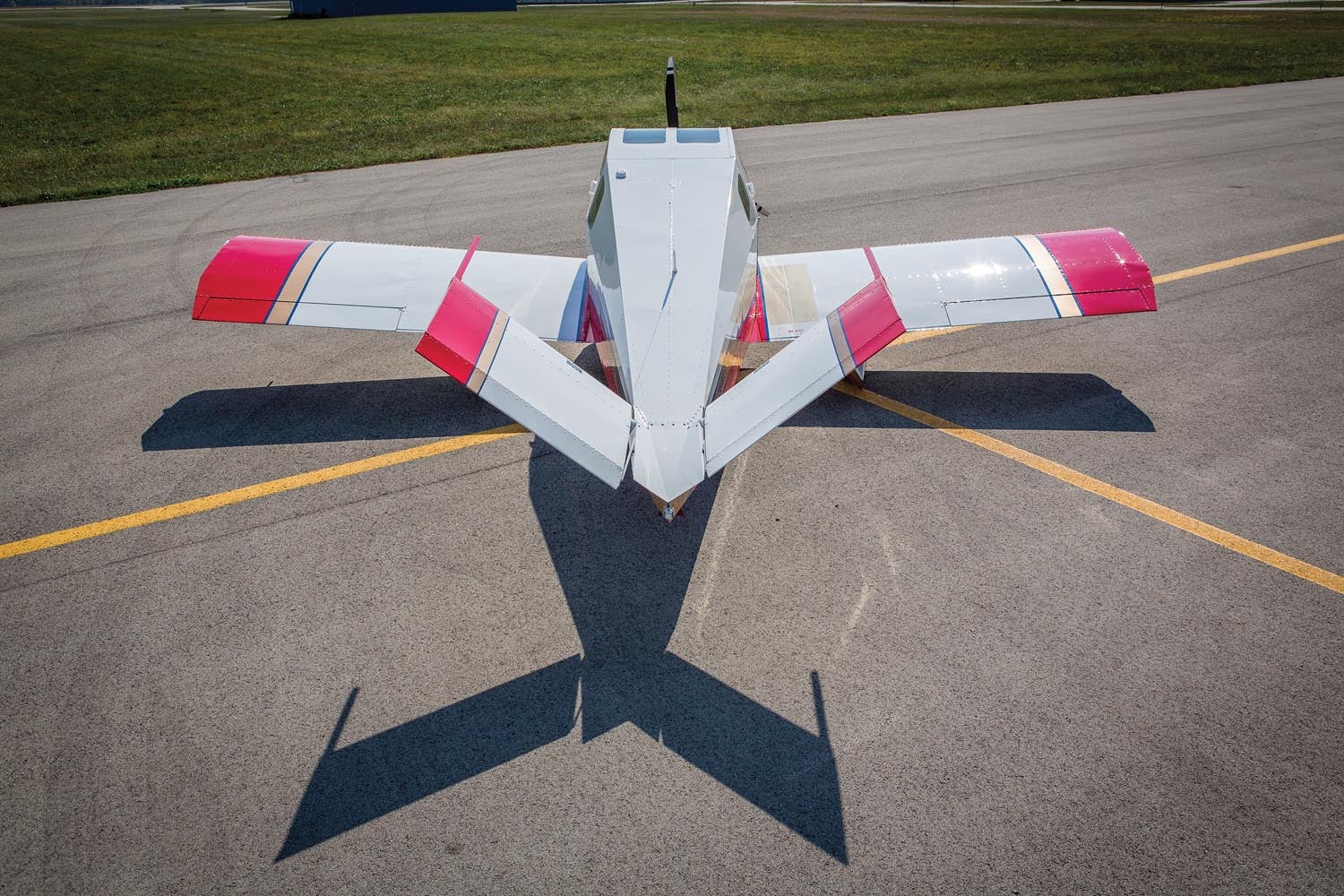
A V-tail is a configuration where the horizontal stabilizer and vertical fin are replaced by a pair of surfaces mounted at a high dihedral angle (usually about 45°). Because these angled surfaces can produce both vertical force and side force, the two V-tail surfaces can replace the three surfaces of a conventional tail. The movable surfaces on a V-tail (called ruddervators) move collectively for pitch control and anti-symmetrically for yaw control.
V-Tail Concepts
At first look, it appears that by getting two surfaces to do the work of three, the airplane can have a smaller total tail area, which should reduce both drag and weight. This idea is still cited as a reason to use a V-tail configuration. In fact, with one small exception, this isn’t true in reality.
Tail Area: V-tails generate side force when the airplane is sideslipping and pitch force in response to an angle of attack change, thus generating stabilizing moments in pitch and yaw. Likewise, deflecting the ruddervators symmetrically produces a pitching moment, and deflecting them anti-symmetrically produces a yawing moment to control the airplane.
Two common misconceptions are that the effective area of the V-tail in yaw is the side-projected area of the tails, and the effective area of the V-tail in pitch is the top-view-projected area of the tails. These ideas are the foundation of the belief that the total tail area could be smaller with a V-tail than a conventional tail.
Unfortunately, this is not the case because the aerodynamic force generated on a V-tail surface acts normal to the plane of the surface, not directly sideways for yaw or vertically for pitch. Accordingly, only part of the force the tail surface generates actually stabilizes or controls the airplane, while the rest is canceled out by an equal and opposite force in that axis generated by the opposite-side V-tail surface. For example, in pitch the V-tails generate symmetric forces normal to the tails. Part of this force is oriented vertically and contributes to pitch control or pitch stability. The other component of force is oriented horizontally, and those forces are equal and opposite on the two tails and provide no net contribution to pitch stability or control.
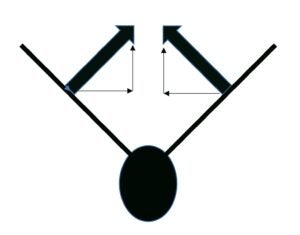
Similarly, the yaw lateral component of force on each tail does contribute to yaw stability and control, but the vertical components are equal and opposite and generate a rolling moment that may or may not be desirable.
The net result is that in order to provide the same stabilizing influence in pitch and yaw as a conventional tail, the total area of the V-tail surfaces must be the same as the total area of a properly sized vertical fin and a properly sized horizontal tail. This means there is no net reduction in tail area or wetted area of the airplane using a V-tail.
The wasted force (e.g., the lateral component when trying to trim in pitch) means that the V-tail surfaces need to generate more total aerodynamic force to produce a given trimming or stabilizing influence. This results in extra induced drag, which increases trim drag and also the loads on the tail structure.
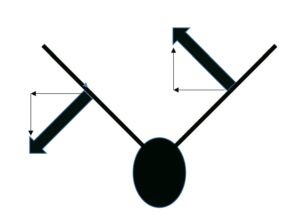
There is no reduction in skin friction drag because there is no reduction in wetted area, and there may be some increase in trim drag because of the cost of the “wasted” aerodynamic force on the tails.
There is a weak argument that because a V-tail has fewer junctions between the tail surfaces and the fuselage there will be some reduction in junction and interference drag.
Structure: The V-tail has significant structural disadvantages with respect to a conventional tail. Because of the dihedral angle between the tails, there is no continuous carry-through structure like there is on the horizontal stabilizer of a conventional tail. The V-tail surfaces individually are larger than either the vertical tail or the horizontal tail panels of a conventional wing tail. Both of these factors make the structure of a V-tail heavier.
As we have just seen, the aerodynamic forces on a V-tail will be larger than those on a conventional tail because only part of the total load on the V-tail panels actually produces stabilizing and controlling influence on the airplane. The wasted force we just saw still adds load that the tail structure must withstand, even if it does not help stabilize or control the airplane.
Flutter: V-tails are more prone to flutter than conventional tails, as sadly illustrated by some of the problems experienced by early model Beech Bonanzas. Because the left and right ruddervators are not interconnected and can deflect anti-symmetrically, they can produce large torsional forces on the fuselage. This makes a V-tail airplane more susceptible to a flutter mode where fuselage torsion couples with anti-symmetric flapping of the ruddervators. It’s particularly important to ensure that the control surfaces of a V-tail are properly mass balanced.
Overall, the V-tail is likely to be heavier than a conventional tail and will probably have the same or higher drag than a conventional tail producing the same total stabilization and control power.
Stability and Control Issues
Adverse Roll: When the ruddervators are deflected anti-symmetrically to command yaw, the aerodynamic forces on the tails are up and sideways on one tail and down and sideways on the other tail. The sideways forces act in the same direction and produce the commanded yaw. The vertical forces produce an uncommanded roll in the opposite direction to the commanded yaw. This large rolling moment due to yaw-control deflection of the tails also produces large torsional loads on the fuselage and is likely to force the fuselage structure to be heavier.
Dutch Roll: V-tails produce a lot of yaw/roll coupling due to their high dihedral. This can reduce Dutch roll damping. The usual cure for low Dutch roll damping is to increase directional stability. If we try to do this by enlarging a V-tail, we also increase the yaw/roll coupling, which works against the desired effect of enlarging the V-tail. It might be necessary to adjust the dihedral of the wing to help offset the rolling moment produced by the V-tail.
Pitch-Up: As the angle of attack of the airplane increases, the V-tail surfaces move down relative to the wing. This can immerse them in the downwash of the wing, which will produce a negative angle of attack change on the tails. This produces download on the tail, which drives the nose up. V-tail configurations can be prone to nonlinear pitch behavior and pitch-up at the stall.
Why Use a V-tail?
A V-tailed airplane will probably be heavier than an airplane with a conventional tail. V-tails have no drag advantage, are more flutter prone and introduce the possibility of pitch stability issues. In spite of this, there are some special cases where it can be a good design choice.
Tail Ground Clearance: Some sailplanes have V-tails to give the tail adequate clearance from the ground when the glider is on the ground with one wingtip resting on the ground.
Wake of Upstream Components: Some airplanes have features that produce a turbulent or separated air wake in the area where a conventional horizontal tail would normally be mounted. A V-tail is one approach that can move the stabilizing surfaces up and out of this wake. While this can work, there is always the risk that the V-tail will move down into the wake at high angles of attack.
Fewer Parts: A V-tail has two panels instead of three, and they can sometimes be made symmetrical left/right, which simplifies the manufacture of the airplane. On an airplane with a powered control system, a V-tail configuration can have fewer (albeit larger) actuators than a conventional tail.
A final reason to use a V-tail has nothing to do with the aerodynamics of the airplane. Several military airplanes (notably the Northrop Tacit Blue and YF-23) have V-tails to reduce their radar signature.
Aeronautical Engineer Molt Taylor of Aerocar fame designed his Mini IMP with an inverted V tail because he insisted the aerodynamic forces would actually assist aircraft roll rather than work against it as in the Bonanza (upright) configuration.
What is the plane in the top photo??
It is a Davis DA 2 two seat non- kitted home built airplane. It is somewhat small in size and produces good performance with Continental 65 – 100 hp. engines.
Fine, as all works from mr Wainfan. Would same consideraciones apply to an ‘A’ tail, or ‘inverted V’, supposedly inducing roll in right sense when baking?
Blessings +
Would that it were true. A carefully designed VTail is as safe, stable and lightweight as fully efective convential tails within its certified operating range. 1- Bonanza V Tail area = the equivalent of two conventional surfaces, not three as alleged; the T34 tail is actually 3 Vtail surfaces of the same size as the 2 on a Bonanza. It should be apparent the leading edges of 3 surfaces have more drag than 2 of the same size. Likewise the statement “V Tails are heavier” is untrue. 2-The Bonanza Vtail is not in itself the cause of flutter. Flutter is induced by unbalanced tail surfaces on the Bonanza as it is on any other unbalanced surface at sufficient speed. Balance of those surfaces is critical, however. Early Bonanza accidents preceded by deformation of the Vtail were caused by insufficient structural support of the leading edge of the fixed areas; not by the control surfaces. This was solved by fairing in those areas, additional internal support there and subsequent use of sub spars and thicker skins. In all recorded cases of failure the plane was flown either above Vne, as in a dive, or in the yellow during turbulance; ie.e beyond its certified limits. 3-The V Tail Bonanza is not unstable in pitch, nor does the nose pitch up during stalls below Vne. If uncorrected the nose will pitch further down and a tightening spiral will develop. 4-Bonanza VTails do not lose effectiveness at higher angles of attack like Vx.
The differences between theoretical and actual design of VTails mentioned here illustrate the extreme of its design limits. As a well-developed design, the Beech VTail suffered from none of the shortcomings mentioned when flown as certified. Beech phased out that tail in favor of a conventionial arrangement to satisfy marketing purposes based partly on old wives tails such as “the forked-tail doctor killer.” It has been flown safely for hundreds of thousands of hours at greater speed than the majority of piston GA aircraft.
Thank you for this discussion. I made me think of flaperons. Can you speak to these at some point in the future? Is there value to them, or do the just create more complexity and weight to the airplane?
I appreciated Mr Wainfans views but given his information and mostly negative ideas about V-tail aircraft, why are almost all the new EVTOL aircraft as well as the 280 Valor tilt rotor using V-Tails? All the latest engineering data from those new airframes suggest the V-tail configuration will actually reduce weight as well as drag. I know several engineers working on the 280 Valor program and they state emphatically that the V-tail configuration is superior to other configurations. Just wondering where the disconnect is?
I recently acquired a V tailed Hummingbird model 103 used ultralight. I have been involved with ultralights ever since the early 80’s. I need help trying to figure out, in relation to the main wing root, where should the root of the V tail be? A little up, a little done, or the same as the wing root?