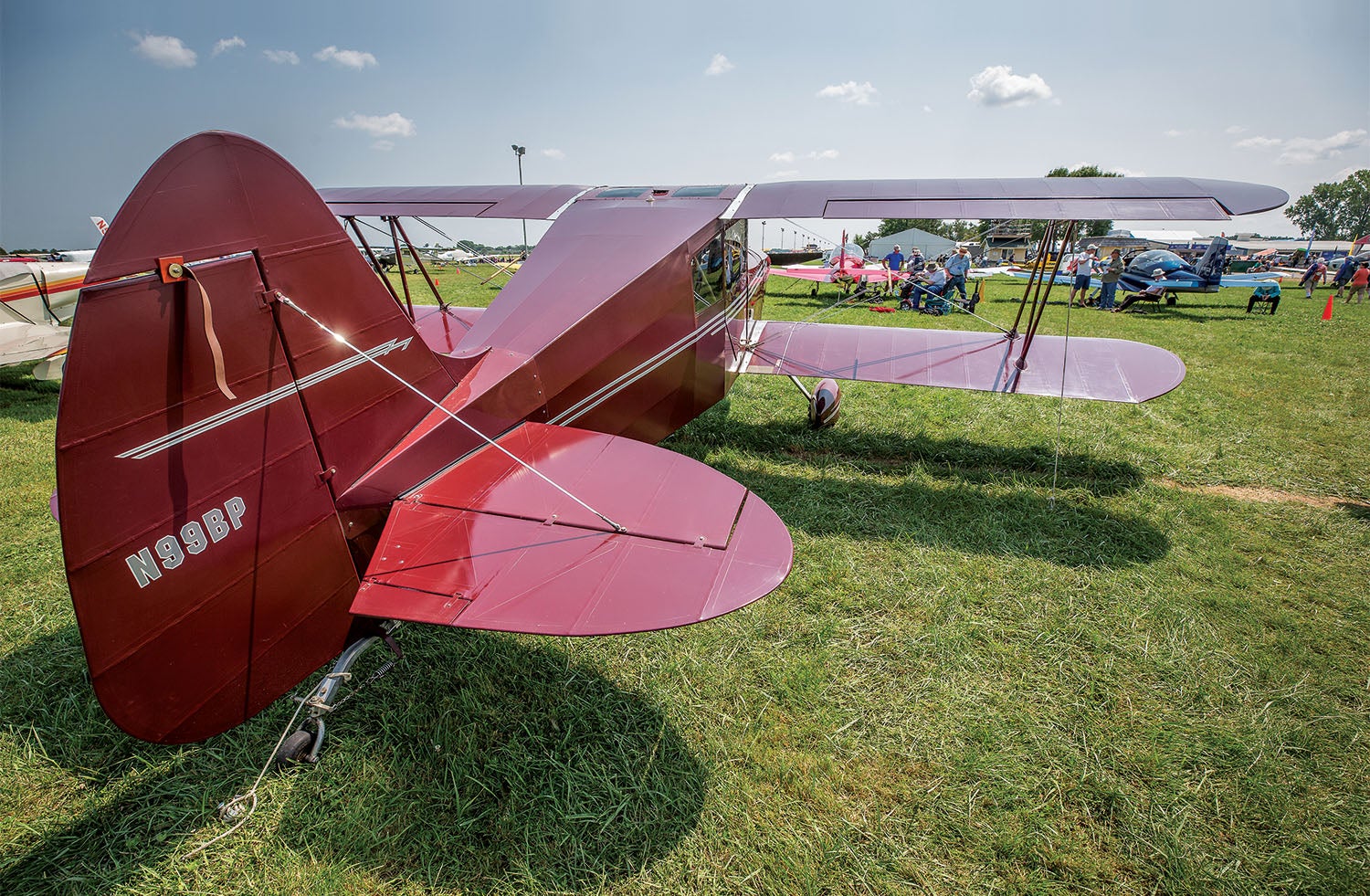
The fixed portion of the vertical tail of an airplane provides directional stability. The rudder provides directional control.
When the pilot deflects the rudder, it generates an aerodynamic side force (lift acting sideways) on the rudder and vertical fin. This side force, acting on the aft end of the fuselage, generates a yawing moment. Let’s take a closer look at the multiple ways the rudder is used to control the airplane.
Directional Control on the Ground
On takeoff, the airplane starts at rest on the ground and accelerates to liftoff speed. During the takeoff roll, there are several factors that might cause the airplane to turn. Among these are crosswinds, runway slope or crown and engine torque or P-factor. This situation is similar on landing, although the power-induced factors are absent. Both on takeoff and after touchdown, the pilot needs to control the airplane in yaw and keep it tracking the runway.
The directional control task on the ground is shared between the landing gear and the rudder. At low speed, yaw control comes primarily from the landing gear, using a combination of nosewheel or tailwheel steering and differential braking on the main gear wheels.
As airspeed increases, the rudder becomes more effective. Also, weight begins to shift from the wheels to the wings as the wings develop lift. With less weight on the wheels, the landing gear steering becomes progressively less effective.
After rotation (or raising the tail on a taildragger), wheel steering is lost and the rudder takes over the directional control task. Note that if the airplane has a free-castering nose gear, the rudder becomes more important since the only landing-gear steering comes from differential braking.
On landing the sequence of events is reversed: The rudder has the primary directional control duty at touchdown, and control authority transfers progressively to the landing gear as airspeed decreases.
Yaw Trim
In steady-state flight, the airplane should fly at zero sideslip. The pilot uses the rudder to trim the airplane in yaw and counteract any yawing moment that would tend to force the airplane to fly at a sideslip angle relative to the airflow.
The most common example of this is the propulsion-induced yawing moment on a single-engine airplane. P-factor, which arises from the spiraling motion of the propeller slipstream acting on the vertical fin, causes a yawing moment that varies depending on power setting and airspeed. It’s possible to compensate for P-factor by building in a fixed fin offset angle or using fixed trim tabs on the rudder, but this only trims the airplane at a single airspeed and power setting. Typically, they are set so the airplane flies at zero sideslip without requiring pressure on the rudder pedals from the pilot at the airplane’s normal cruise condition. The pilot keeps the airplane at zero sideslip (ball centered) at other flight conditions (like full-power climbs) by holding enough rudder to compensate for the other yawing moments acting on the airplane.
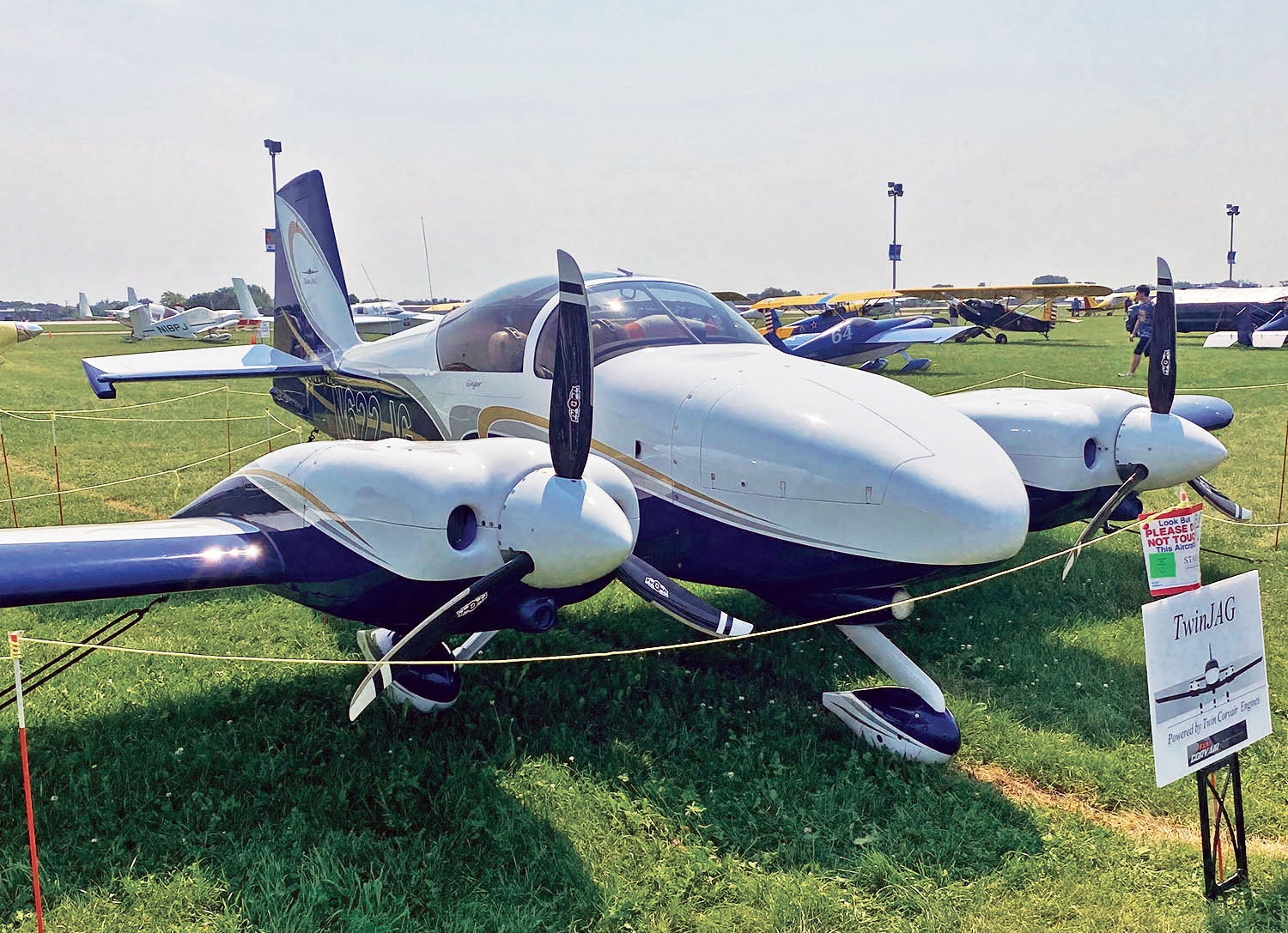
Multi-Engine Yaw Trim
Multi-engine airplanes must be able to continue to fly safely if an engine fails. If the engines are not mounted on the airplane centerline, the thrust asymmetry that occurs with an engine inoperative and the drag of the inoperative engine will generate large yawing moments.
The need to retain directional control and keep the airplane flying straight in this one-engine-inoperative (OEI) condition typically sizes the vertical fin and rudder of a multi-engine airplane.
When an engine fails, the pilot uses the rudder to generate a yawing moment to compensate for the thrust asymmetry and retain control.
The yawing moment the rudder can generate is proportional to airspeed squared. Because of this, there is a minimum airspeed at which the rudder can trim the airplane in yaw with a dead engine and all operating engines at full power. This speed (Vmc) is a critical parameter that has large effects on the safety and usable performance of the airplane. In particular, if Vmc is above the stall speed, then there is a range of airspeed where the airplane can fly, but is not controllable if an engine fails unless the pilot reduces power on the operating engine(s). In this situation, the full power of the remaining engine(s) is not usable to keep the airplane airborne and hopefully climbing.
Turn Coordination
The pilot initiates a turn by rolling the airplane into a bank with the ailerons. The ailerons and the roll rate itself both produce an adverse yaw. This means that the nose yaws in the opposite direction to the commanded roll and turn.
Uncorrected, this will cause the airplane to sideslip as well as bank. If the airplane is sufficiently stable directionally, it will still turn eventually as the sideslip acts on the vertical fin to produce a yawing moment into the turn.
In order to keep the turn coordinated (zero sideslip), the pilot uses the rudder to command enough yawing moment to offset the adverse yaw. How much rudder power is needed to coordinate is very much a function of the configuration of the airplane and the flight condition.
Airplanes with long wings and short fuselages, like gliders, will have more adverse yaw than airplanes with shorter wings and longer tail arms. Accordingly, the glider-like airplane will require more rudder power to coordinate turns and rolling maneuvers.
In general, more rudder is required to coordinate turns at lower speeds at higher angles of attack. It takes more aileron to command a given roll rate at lower airspeed, so the adverse yaw will increase also. More rudder is needed to overcome this extra adverse yaw.
A requirement to do a bank-to-bank turn reversal at low speed is often the critical flight condition for sizing the rudder. Both civil and military aircraft have explicit requirements to perform bank reversals at or near approach speed.
Commanded Sideslips
As we have seen, much of the time the rudder is used to keep the airplane flying at zero sideslip. However, there are some situations where the pilot needs to be able to command a sideslip and deliberately fly the airplane in a sideslipping condition.
Landing in a crosswind is such a situation. To touch down smoothly, the airplane’s velocity vector must be aligned parallel to the runway when the wheels make contact with the surface. Simultaneously, the centerline of the airplane should be aligned with the runway. If the airplane is yawed relative to the velocity vector on touchdown, the wheels will produce a side force, driving the airplane in the direction of the yaw. In zero-wind conditions, or if the wind is aligned with the runway, all of this happens naturally. If there is a crosswind, however, the situation changes.
The cross component of the wind drives the airplane sideways relative to the runway. To compensate, the pilot can either turn the nose upwind (crab) or put the airplane into a steady-state sideslip into the wind using a combination of rudder and aileron. In either case, the rudder is needed to command a sideslip at touchdown.
If the pilot elects to fly a crabbed approach, the rudder is used just before touchdown to “kick out” into a sideslip to align the airplane with the runway. On a slipping approach, the sideslip is established earlier and held until touchdown. The yaw control power needed to land in a specified crosswind is often the condition that sizes the rudder of an airplane.
Another situation where the rudder (along with aileron) is used to command a steady-state sideslip is the slipping maneuver used to steepen the landing approach without using flaps.