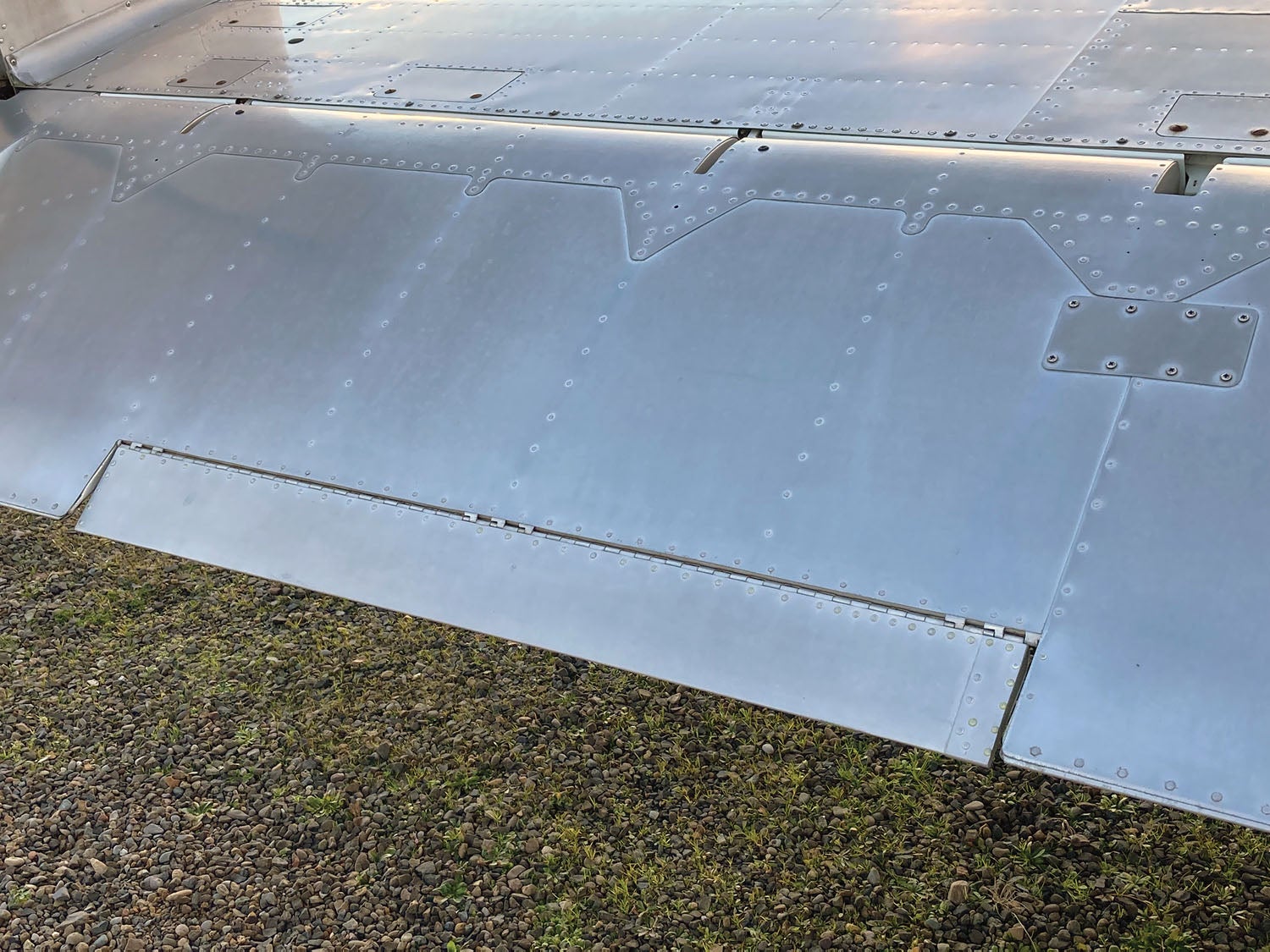
For an airplane to maintain steady-state level flight it must be trimmed in pitch. The airplane is trimmed when the net pitching moment acting about the CG is zero.
We saw last month how the horizontal tail trims the airplane by lifting up or down on the aft end of the fuselage to produce a moment that counters the moments generated by the rest of the configuration. While the airplane itself is in trim when the pitching moments are in equilibrium, this is not enough for the pilot to experience the airplane as trimmed.
If the pilot must exert a steady-state force on the stick to keep the elevators in the position required to keep the airplane in trim, then from the pilot’s viewpoint the airplane is not yet trimmed. For the pilot, the airplane is trimmed only when it is in steady-state flight and the net stick force required of the pilot to maintain that flight condition is also zero.
The trim system addresses both the need to bring the airplane itself into pitching moment equilibrium and to alleviate the stick force the pilot must exert to keep it there. There are several different trim mechanisms that address the need to zero out stick force as well as trim the airplane overall.
Trim Tabs
On an airplane with a fixed horizontal tail plus elevator tail configuration, the incidence of the horizontal tail is set at a compromise position, usually chosen so the airplane trims at cruise with elevators in trail. This trims the airplane to one airspeed. To trim to any other airspeed requires a steady-state elevator deflection, so some additional mechanism is needed to trim out stick forces. The most common system used is a trim tab.
Trim tabs are small surfaces hinged to the trailing edge of the elevator. Deflecting the tab causes it to generate a force up or down on the trailing edge of the elevator. This force changes the position at which the elevator floats. The pilot can trim out the stick force by adjusting the tab to make the elevator float naturally at the position that trims the airplane.
Trim tabs are extremely common and effective and are a feature of a large number of aircraft. There are a few issues that must be taken into account, however, when designing a trim tab system.
The first is that the tab reduces the effectiveness of the surface it is trimming. For example, to trim an airplane nose up, the tab is deflected trailing-edge-down relative to the elevator. This produces an upward force on the trailing edge of the elevator that drives the elevator trailing-edge-up, but this upward force itself is in the opposite direction to the direction the elevator force itself must act to trim the airplane. Accordingly, the elevator must deflect a little farther to compensate for the force being generated by the tab.
A second design challenge for a trim tab system is that the tab must deflect relative to the elevator while the tab hinge line moves up and down with the elevator. The linkage that controls the tab must cross the elevator hinge into the elevator itself and carry the signal from the pilot across the elevator hinge without binding, interfering with elevator deflection or letting elevator deflection cause the tab to move relative to the elevator. There are a variety of ways of achieving this, but some mechanical complexity is involved in making it work well.
There is a second concern inherent in the design of the trim tab linkage. Because the tab itself can drive the elevator deflection, relatively small deflections of the tab can produce relatively large forces.
Free play in the trim tab linkage can allow the tab to flutter. If the tab flutters, it can drive a flutter of the entire surface, which can be catastrophic. Two of the most tragic accidents at the Reno Air Races, the crashes of Miss Ashley and Galloping Ghost, were both the result of tab flutter that led to catastrophic failure and loss of control of the airplane.
It’s important that the trim tab linkage be tight, allowing a minimum of free play on the tab. A few designers have incorporated mass balance on the tab itself to minimize the chance that the tab will flutter, even if there is some looseness in the tab control linkage.
All-moving tails, which will be discussed in more detail later, have anti-servo tabs geared to the motion of the tail. Linkage that drives the anti-servo tab is adjustable to change the position of the tab relative to the tail to affect trim.
Spring Trim Systems
Another way to trim out stick force is to use a system of springs to put force directly onto the stick to counteract the aerodynamic forces. Adjusting the spring tension can bring the stick force to zero.
Spring systems are simple but they have some issues. The first of these is that the pilot must work against the spring to maneuver the airplane. A spring strong enough to trim out steady-state stick force is also strong enough to affect the force the pilot must use to maneuver.
Spring systems can also significantly affect the pitch stability of the airplane. On a tab system, both the tab forces and the elevator forces vary the same way with airspeed, so the trimmed floating position of the elevator does not change with airspeed. On a spring system, the force exerted by the spring is constant, while the force on the elevator varies with airspeed. This means that if the airplane is disturbed in pitch and the airspeed changes as a result, the position of the elevator will also tend to move as the aerodynamic force on the elevator changes.
If the trim spring is pushing the elevator trailing-edge-down, this effect will be stabilizing in pitch. If the airplane is disturbed nose-up, it will slow down. The aerodynamic force on the elevator will decrease, and the constant spring force will drive the elevator trailing-edge-down, causing the airplane to nose down toward its original trimmed angle of attack. If the airplane noses down, the opposite will happen. The elevator will move trailing-edge-up, opposing the nose-down disturbance.
If the trim spring is pulling the elevator trailing-edge-up, all of this is reversed, and the effect of the trim spring will be to reduce the speed stability of the airframe.
On some airplanes, the stabilizing effect of a “down spring” is used directly, and they incorporate a spring that exerts a constant trailing-edge-down force on the elevators to augment speed stability while overall pitch trim is provided by a tab system.
Variable Incidence Tail
A variable incidence tail system allows the elevators to float and carries the trimming load on the fixed portion of the horizontal tail. The elevators may have fixed tabs to adjust the float position so that the elevators are aligned with the horizontal stabilizer when the airplane is at its nominal cruise condition.
Changing the incidence angle of the fixed portion of the horizontal tail changes the aerodynamic force on the tail and trims out pitching moment to bring the airplane to equilibrium. Trimming the airplane this way also trims out the stick force since the pilot can adjust the tail incidence while allowing the elevator to float. No additional mechanism to directly alter stick force is needed.
To implement this approach, the tail must be hinged, and the linkage controlling the incidence of the tail must be strong enough to carry the forces on the tail. The control mechanism must also keep the tail firmly constrained at its set angle. Any slippage or unplanned release of the tail control linkage will lead to loss of control of the airplane.
Another concern with variable incidence tails is that the gap between the root of the horizontal tail and the side of the fuselage is likely to be open at least slightly in order to allow the tail to move relative to the fuselage. Air leakage through this gap will add drag and also reduce the effectiveness of the tail, requiring the tail to be larger and to move more in order to properly trim and stabilize the airplane. A good gap seal at the root of the stabilizer is an important feature of any variable incidence system.