Once the size and planform of the wing have been determined, it’s time to choose (or design) the airfoil. The airfoil must provide the right aerodynamic characteristics to give the airplane its best performance and acceptable flight characteristics. The most important thing to understand about selecting an airfoil is that the airfoil must be evaluated at the actual flight conditions that are important for this particular airplane.
Periodically, a new airfoil or family of airfoils appear that are widely publicized as “advanced” or “new high-performance” airfoils. Designers and builders will be very tempted to adopt this new technology to improve their airplanes.
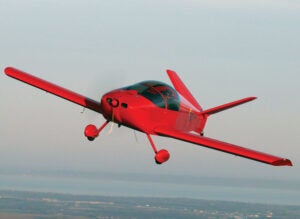
Often the new airfoil was designed for airplanes with a far different wing loading, cruise speed or cruise altitude than the new airplane a designer is working on. This makes it inappropriate for the design in progress. The new airfoil may actually perform worse at the actual flight conditions for the airplane than another choice.
The same concern applies when modifying an existing design to try to improve its performance. A trap more than one modifier has fallen into is when they substitute the new “advanced” airfoil for the one in the original design. Hoping that they will see a performance improvement, they are sadly disappointed when they find their “improved” airplane performs worse than a stock one.
Airfoil Evaluation
To evaluate an airfoil properly in the context of a specific airplane and choose the right section for the wing, we need to look at three flight conditions: cruise, landing and takeoff. Each one is characterized by an altitude, airspeed and configuration. There are also two configuration features to consider: skin condition and flap setting. We’ll look at those first, then delve into the three flight conditions.
Skin Condition
Skin Condition, which applies to all three flight conditions, is the surface quality of the skin of the wing. Skin surface quality is determined by how the wing is built. For example, a composite-skinned wing or a metal-skinned wing with flush riveting can be quite smooth. A metal wing with lap joints between skin panels or rivets with exposed heads can be quite rough.
Some airfoils are more sensitive to surface roughness than others. Any airfoil designed to have laminar flow for low drag must have a smooth skin. Any significant roughness or excrescences on the wing surface will trip the laminar boundary layer, causing it to become turbulent and greatly increasing drag.
Flap Setting
If the airplane has flaps, the flap setting is part of its aerodynamic configuration. The flaps are routinely deflected for approach and landing. Some airplanes also take off with some flap deflection.
Cruise
The first flight condition to consider is cruise. The goal is to minimize cruise drag to get the best performance.
To get the lowest cruise drag, we need to consider the product of wing area times drag coefficient in cruise. The best airfoil/flap combination is the one that meets stall speed requirements and yields the lowest value of wing area (S) times parasite drag coefficient (CDp) at cruise conditions.
Minimize: S * CDp
The wing for many types of aircraft is sized by stall speed, which we will discuss in the next section. For others, the wing size is optimized for cruise performance. In either case, once the wing loading is known, we can start matching the airfoil to the cruise condition.
The first step is to determine the lift coefficient (CL) of the wing at cruise conditions. It’s vital to calculate CL at the planned cruise speed, altitude, and gross weight. For most airplanes this will be very different than the value one would get at sea-level condition or at maximum speed.
Airfoils are designed to function at their best at a specific “design CL.” When choosing an airfoil for an airplane, the design CL is the cruise value. Compare the drag coefficient of candidate airfoils when they are at this design lift coefficient to find the one that has the lowest drag at the actual cruise condition of the airplane you are designing.
Landing and 1G Stall
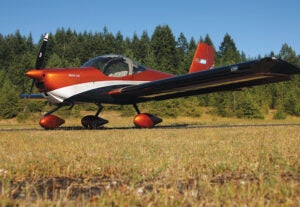
The primary concern in the landing configuration is stall speed. Stall speed is a function of the wing loading of the airplane and the maximum lift coefficient (CLMAX) the wing can develop. Once the CLMAX is set, it determines the wing loading and hence wing area the airplane must have to meet a given stall speed.
For many airplanes, the wing is sized by a stall speed requirement. The wing size needed to meet the stall speed requirement is larger than the optimum wing for cruise performance. Because of this, the maximum lift performance of the wing is relevant to cruise performance because the higher the CLMAX, the smaller the wing can be. Reducing wing size reduces wetted area and, all other things being equal, reduces the parasite drag of the airplane in cruise.
Where the tradeoff comes in is that changing the airfoil to increase CLMAX may also increase CDp. The optimum section is the one that gives the minimum value of ( S * CDp ), so the relative change in wing size and airfoil CDp must be evaluated for each candidate section.
It’s also important to make sure we evaluate stall speed to set wing loading properly.
Regulations vary, so the stall speed must be evaluated in the proper configuration. For example, in the U.S., a single-engine airplane certified under FAR Part 23 is required to have a stall speed no greater than 61 knots in the landing configuration. Landing configuration in this context can include deflected flaps or other high-lift devices.
U.S. Light Sport (LSA) regulations specify a stall speed of 45 knots or less in the cruise configuration. This means the airplane must meet the stall speed requirement with all high-lift devices (if any) stowed.
In the flaps-up configuration, the CLMAX of the airfoil determines the CLMAX of the wing.
The CLMAX of the airfoil alone is not the same as that of the complete wing because of the 3D distribution of lift coefficient along the wing that we discussed a few months ago, but the higher the maximum lift of the airfoil is, the higher the maximum lift of the wing will be.
If the critical condition (either regulatory, or for performance reasons) is in a landing configuration with high lift devices deployed, then the CLMAX of the bare airfoil is of secondary importance. What counts is the lift characteristics of the wing with the high-lift system deployed.
The airfoil characteristics will still come into play because the flaps are rarely full span and because flaps tend to produce a constant increment in max lift. That said, the CLMAX value that counts is for the wing with the flaps down, and that is what should be used to evaluate the wing’s maximum lift and set wing loading.
No-flap CLMAX is not that important unless the airplane has no flaps. A common mistake is to overvalue clean CLMAX.
Takeoff
The third flight condition/configuration we need to check is takeoff and initial climb. This rarely sizes the wing, but we do need to be mindful of both maximum lift and drag of the wing in takeoff configuration.
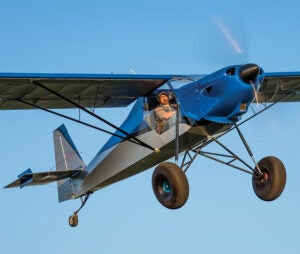
The CLMAX of the wing in takeoff configuration and the wing loading define the stall speed in that configuration. That stall speed in turn is one of the major parameters determining takeoff distance. It’s rare that takeoff distance sizes the wing, particularly if the wing is sized to meet stall speed requirements in landing configuration, but it does happen, particularly for an airplane with a purely cruise-optimized wing.
Drag is also important because of climb performance. Once the airplane lifts off, it must be able to climb away and clear obstacles.
As with landing, it is important to do the evaluation with the flaps in the proper configuration. Most single-engine airplanes take off with the flaps up because they have acceptable takeoff distance and lower drag in this configuration.
Higher-wing-loading airplanes, or airplanes with extremely short takeoff distance requirements, may take off with some flap deflection to reduce liftoff speed and takeoff roll. For these airplanes, the wing design and airfoil choice should be evaluated with the flaps in the nominal takeoff position.