We’re all tired of talking about the COVID-19 pandemic, I’m certain, but there’s no denying it’s reached into every corner of our society, impacting our daily lives and putting its nasty little influence on Experimental aircraft. But not, actually, in the way you probably expect—hence the backward nature of this column’s title. No, in fact, homebuilding is thriving.
I have the great good luck to talk to many in our world and the “howzitgoin?” feedback is commonly, “We’re doing great!” I’ve heard this from airframers, engine people, avionics and other suppliers. After a sudden drop in demand for some businesses in the spring of 2020, the phones started ringing again in early summer and haven’t stopped. I hear that the suppliers in broad markets—think of Aircraft Spruce and Wicks, for example—had demand slacken slightly or hold steady in the early part of the pandemic, and then pick up after the initial shock.
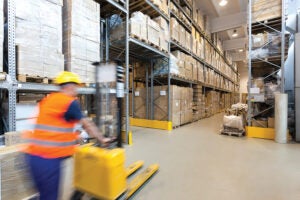
With just enough personal experience in e-commerce at a national distributor to offer a half-baked opinion, it’s been interesting for me to watch the supply chain dynamics play out. We all know that aviation is a relatively small industry overall, and there are plenty of places in the supply chain where there’s just one source. Actually, in many cases there are multiple sources, but only one or two are fiscally advisable. Where there are certified and non-certified versions of the same parts available—sometimes the same part—the Experimental version is usually a lot less expensive. I refer you to engine controls: Compare Aircraft Spruce’s house brand of mixture cables to, say, the McFarlane item. They may not be exactly the same, but the Spruce part is less than half the price.
In any case, the overall market had reached an equilibrium of sorts at customary volumes going into 2020, then COVID arrived. Manufacturers who were not considered essential had to shut down or greatly scale back last spring, crimping their capacity. Further up the food chain, manufacturers found delays getting raw materials as well as interruptions in shipping—to say nothing of the rapidly rising cost to ship goods. For just a moment, the inability to ship was matched to a slight downturn in demand.
But that didn’t last long, and what I noted during the fall and into early winter were continuing shortages of parts as well as delays getting items that were in stock. Maybe I noticed this so acutely because I was in the process of swapping engines and needing this part and that part, and not knowing what I needed until I got to any given stage. (It would be nice to create one “bill of materials” at the start of the project and have everything in hand before you start, but life isn’t like that.) So I’d order as I went, hoping to get most of the parts from Spruce’s California warehouse, the closest to me. What used to take three days to arrive turned into a week, sometimes more.
I asked my contacts at Aircraft Spruce about this and the answer was pretty straightforward. There were challenges at the warehouse level, with uncertainties about COVID exposure and plenty of turnover; there were the supply-chain issues; and, as it turns out, the primary shipper was also overwhelmed. For a short time, I thought the gap between getting a shipment notification and UPS acknowledging the package was Spruce’s fault, but it seems that the boxes got to UPS and sat there for some time before getting on a truck. In one case, the shipment left Spruce and never made it into the system. Where those baffle materials are today I do not know.
The point: A tough combination of supply-chain slowdowns, shipping issues and a few other factors have impacted many suppliers’ ability to send you what you’ve paid for. Patience is warranted—and, believe me, I’m working on it.
Pop Psychology
Meanwhile, builders found their way back to their hangars, basements or workshops in the spring and, from what I can tell, haven’t let up. Van’s Aircraft had one of its best months ever in the early summer. Think about that: The highest kit sales month in the company’s long and storied history, in the midst of a pandemic. Kitfox’s John McBean told me that his shop is as busy as ever and sees no immediate letup. He’s booked out for months on new kits and other projects.
For me, the next question is: why? I think for a lot of builders the pandemic has been a wake-up call, a reminder that the airplane project languishing at the edges of our daily lives is a desirable thing—an important thing. It’s also a demonstrably real thing, unlike Zoom meetings taken in our spare bedrooms where we comb our hair, put on a nice shirt but still have sweat pants and bare feet below the desk. At first, COVID, by taking away parts of our social and work lives, gave us an excuse to dust off the rivet gun and get back to work. What else were we going to do?
The gratifying thing, of course, is that it appears many, many builders are still going strong, still building away. If this is a case of making lemonade out of lemons, I say “drink up!”
Peak L/D In Practice
Reader George King says, “Barnaby Wainfan’s well written article made me think of a university competition of about 30 years ago. My daughter was part of a team of engineering students in their final year at McGill University (Montreal) whose final-year project was to compete in an international RC model competition. Using a given motor, they had to design and build an RC model airplane to take off, fly a designated course and successfully land while carrying the heaviest possible payload weight—the winner being the team whose model carried the greatest weight.
“Her team assembled a remarkable collection of talents and won the competition by a big and record-setting margin. The key to me was their understanding that carrying the maximum load meant flying at peak L/D, which meant the model would have to be flyable under complete control while being on the brink of a stall for the whole flight.
“Their aerodynamics whiz soon realized that most of the published airfoil information did not have the detailed info he wanted about the transition period between max L/D and stall, so they even built their own mini wind-tunnel to study the transition into stall of various high L/D airfoils, finally choosing one that combined extremely progressive stall characteristics with good peak L/D. His wing design must have closely followed the principles in Barnaby’s article, so the pilot could always maintain control despite the model being loaded to the point that it was always on the brink of a stall. Needless to say they got excellent marks for their project!”