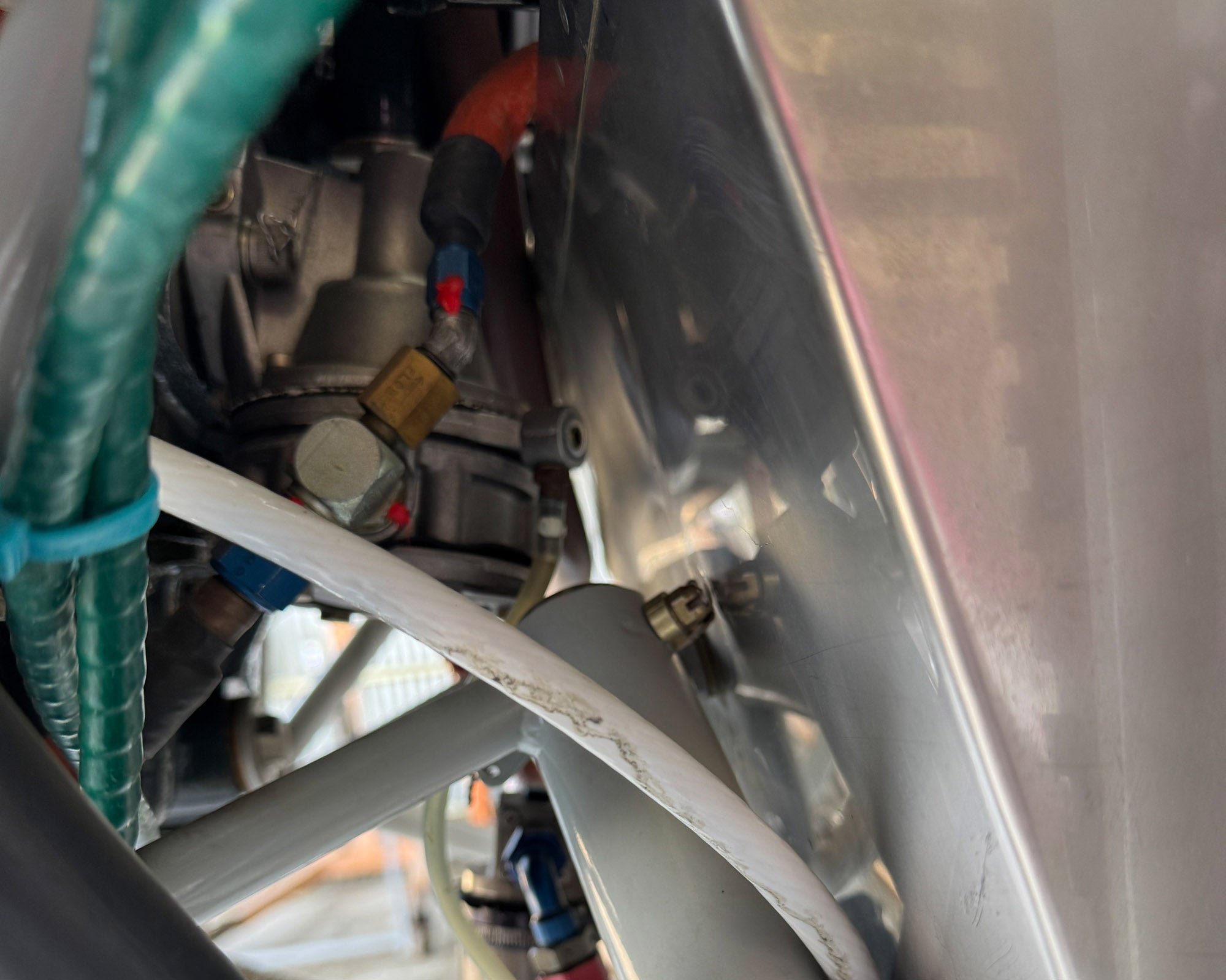
When you’re building an airplane that requires lots of “custom work”—one that comes from an older kit or plans and not from the modern realm where everything is provided (and fits)—it’s extremely helpful to visit other builders or owners of the same type to see what they have done and pick their brains for problem areas (with the kit—not their brains).
The F1 Rocket project is a good example. I spent a few hours with a friend who had the cowling off his own Rocket, camera in hand. Aside from lots of clever ideas on how to do things, I discovered a problem area where the fuel pump overflow port interferes with the firewall—there is no room for a standard elbow to stick out the back of the pump!
My friend’s solution was elegant. An accomplished machinist, he simply drilled and tapped the overflow boss from the bottom and installed a barbed nipple, then plugged the back of the port. This saved him close to 3/4 inch over the standard elbow solution!
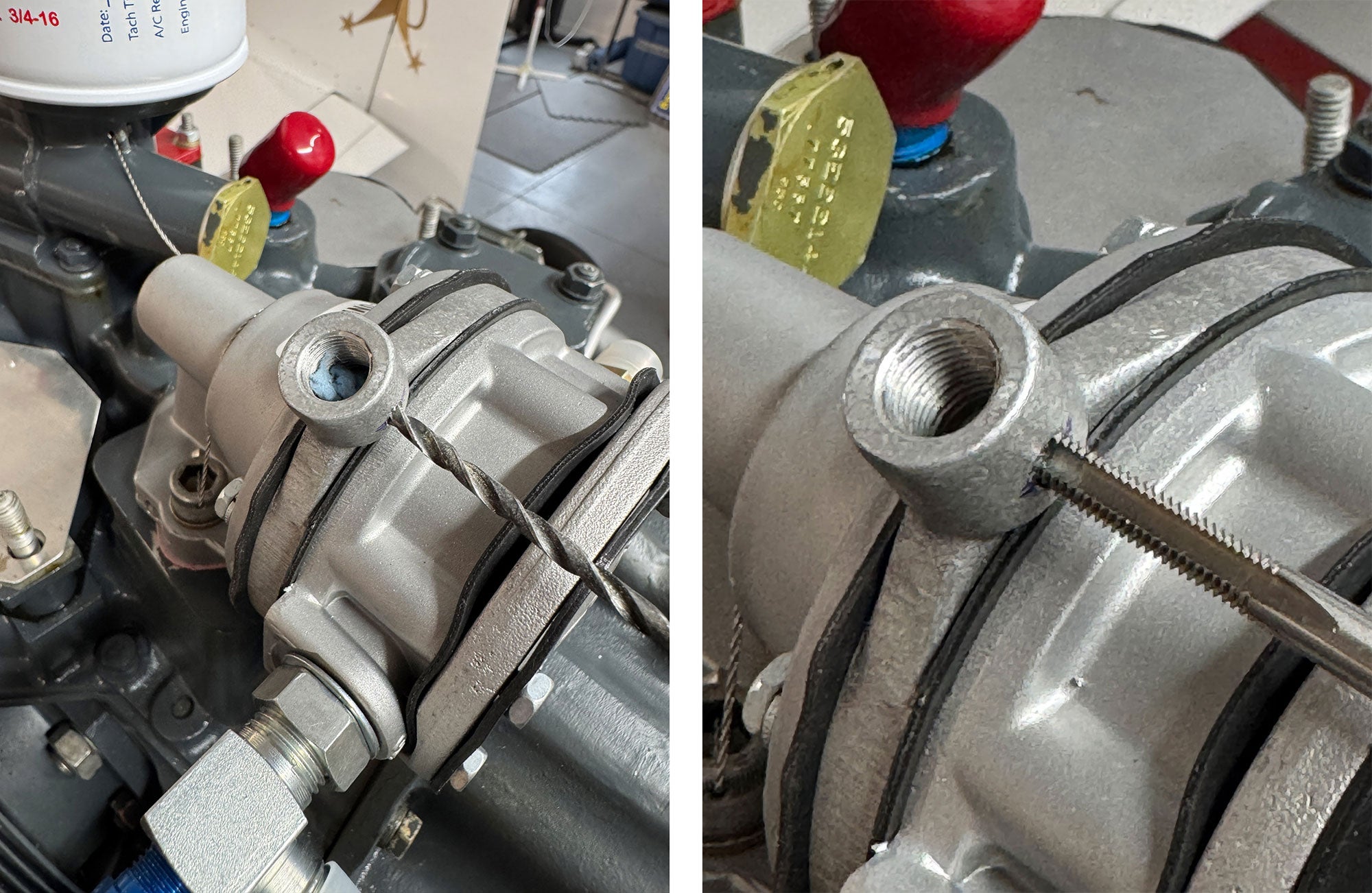
Not one to pass up a good idea, and with my engine on the work stand and the pump staring me in the face, I decided to duplicate his solution. After looking through online catalogs for an appropriate nipple, I decided that rather than pay $2.47 for the part plus a shipping charge of $15.00, I could make what I needed instead. The nipple simply required 10-32 threads and a narrow profile. After searching through my stock of 4130 steel rod and exchanging notes with my friend, he suggested, “Why not just use an AN3 bolt?” Brilliant!
I grabbed a longish bolt, chucked it in the lathe, and drilled out the center with a #44 bit (why #44? Because it was the first bit of approximately the right size to fall into my hand…). I then shortened the threaded portion, cut the head off the bolt, trimmed it to length, and voilà—I had a nipple! I cut a narrow grooved area for friction and to hold safety wire in place, and it was finished.
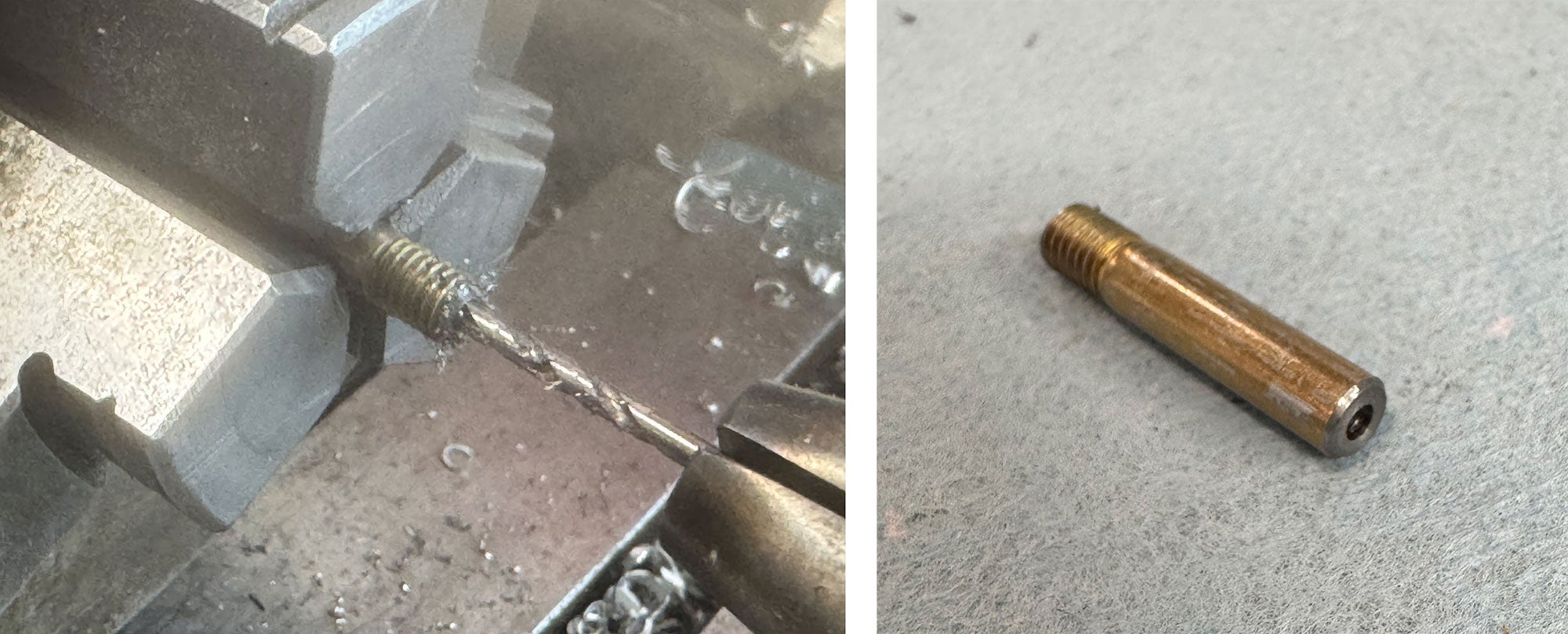
Next, I carefully center-punched the location to drill the pump boss, stuffed a bit of paper towel into the opening (to catch any chips), and cross-drilled the boss with a #21 bit (the hole size for a 10-32 tap). I borrowed a bottoming 10-32 tap from my neighbor Bob (“Home Shop Machinist” Bob), and the aluminum tapped like butter. A little red Loctite secured the nipple in place, and a 1/8-inch NPT plug capped off the project.
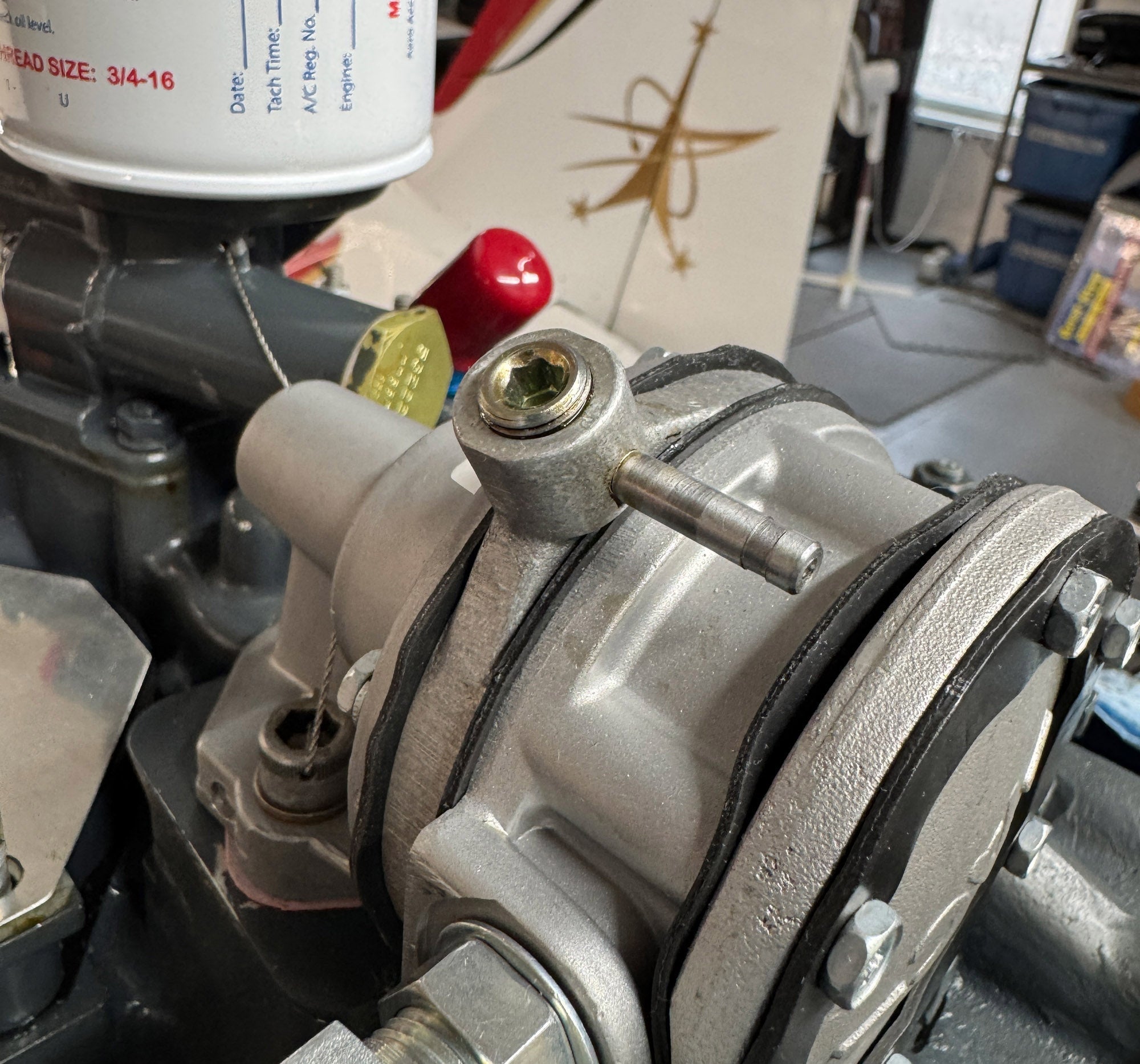
The entire job took less than half an hour. And yes, I now have a custom pump that can’t be easily replaced if it goes bad in the field. I probably voided any warranty as well, but I’ve had good luck with these pumps lasting the life of the engine, so I’m not too worried. It’s just something you have to accept sometimes with custom aircraft projects.
Not enough clearance for a banjo fitting?