I originally designed my SR-1 race plane with a single wing tank. I subsequently decided to add a header tank for several reasons. First and foremost, the wing tank is wide and flat; the wing has almost no dihedral and a very shallow sump. Although I incorporated flapper doors between the outer left/right bays and the inner bay, I was concerned that uncoordinated flight at low fuel levels might unport the pickup and result in the engine quitting. (It would be nice to preserve slipping as a landing maneuver option for the pilot, but this is also exactly when you don’t want an engine out, especially in a plane with a poor glide ratio and high landing speed.)
I also realized that adding a header tank would provide enough fuel to pursue longer distance records. Additional fuel will bump the SR-1 from the 300kg c-1a/0 to the 500kg c-1a class, but it will be quite competitive in the higher class as well. In this case, fuel in the wing could be transferred to the header tank, which has a much lower risk of unporting due to its geometry. The downside of the header tank is of course extra weight, which is a constant concern in this project, so the build documented here represents an attempt to build as light a tank as possible. In addition, the tank has been designed to be easily removed both for servicing and for the time-to-climb record, when the airplane will be stripped of any unnecessary weight.
I’m not going to discuss fuel system architecture here (i.e., layout, vent lines, line size, valves, etc.). That has been well documented elsewhere. See, for example, Ken Krueger’s “Light Aircraft Fuel System Design” series in the December 2015 and January 2016 issues of KITPLANES.
From a fabrication point of view, my primary concerns were weight and that the tank not leak. Leaks in composite tanks tend to originate from pinholes, seams and through-holes (for fittings). Solutions to these issues needed to be as lightweight as possible. Let’s start with pinholes.
Pinholes: If you hold up two layers of overlapping fabric, you’ll see a moiré pattern of pinholes. Most of these will be filled with resin during the layup, but not all. Techniques used to reduce pinholes include additional layers of cloth, “anti-aliasing” the cloth by having adjacent layers at different orientations (say 0°/90°, 45°/45° and 30°/60°) or using more layers of lighter cloth with a tighter weave that reduces the size of the pinholes.
In addition, a resin-rich layup will tend to have fewer pinholes than a drier layup, but it will be heavier. Tank interiors can also be painted with a novolac coating like Rhino 9700 (available at Aircraft Spruce), which is a highly chemical resistant, thixotropic epoxy. The latter property means it will stick to vertical surfaces without sagging and is thick enough to function as an impermeable seal. Again though, there is a weight penalty.
Seams: One way to avoid seam leaks/delaminations is to avoid or minimize bonded seams altogether. This can be accomplished by making a male mold out of something like blue foam, which is then completely enveloped in a single layup. The captured mold is then dissolved out with gasoline or other solvents. I find this approach messy and environmentally unacceptable and would not recommend it. Properly executed, bonded seams are extremely reliable. Placed high in the structure, time exposed to fuel and hydrostatic pressure will be minimized. As you’ll see in the build sequence, I used what is sometimes called a pi-joint (because it is shaped like π) to ensure a leakproof seam on a blind closeout.
Through-holes: Like seams, some fittings may be able to be located “high and dry” (think vent lines), but others like the fuel pickup are going to be almost always submerged and at the highest hydrostatic pressure. My approach with all fittings was to adopt double-sided bonds in which fittings are bonded on both sides of the tank wall (i.e., the fitting is sandwiched by carbon on both sides), and the fitting has both a mechanical (i.e., a bolted assembly) and bonded component. I’ve seen pictures of aluminum tubing passed through the wall of a tank and gooped up with epoxy on both sides—that approach may be easy to execute and initially leak-free but appears to be susceptible to leakage in the longer term. It is nothing you would ever see in an engineered aerospace structure.
With those considerations out of the way, let’s move on to the actual construction.
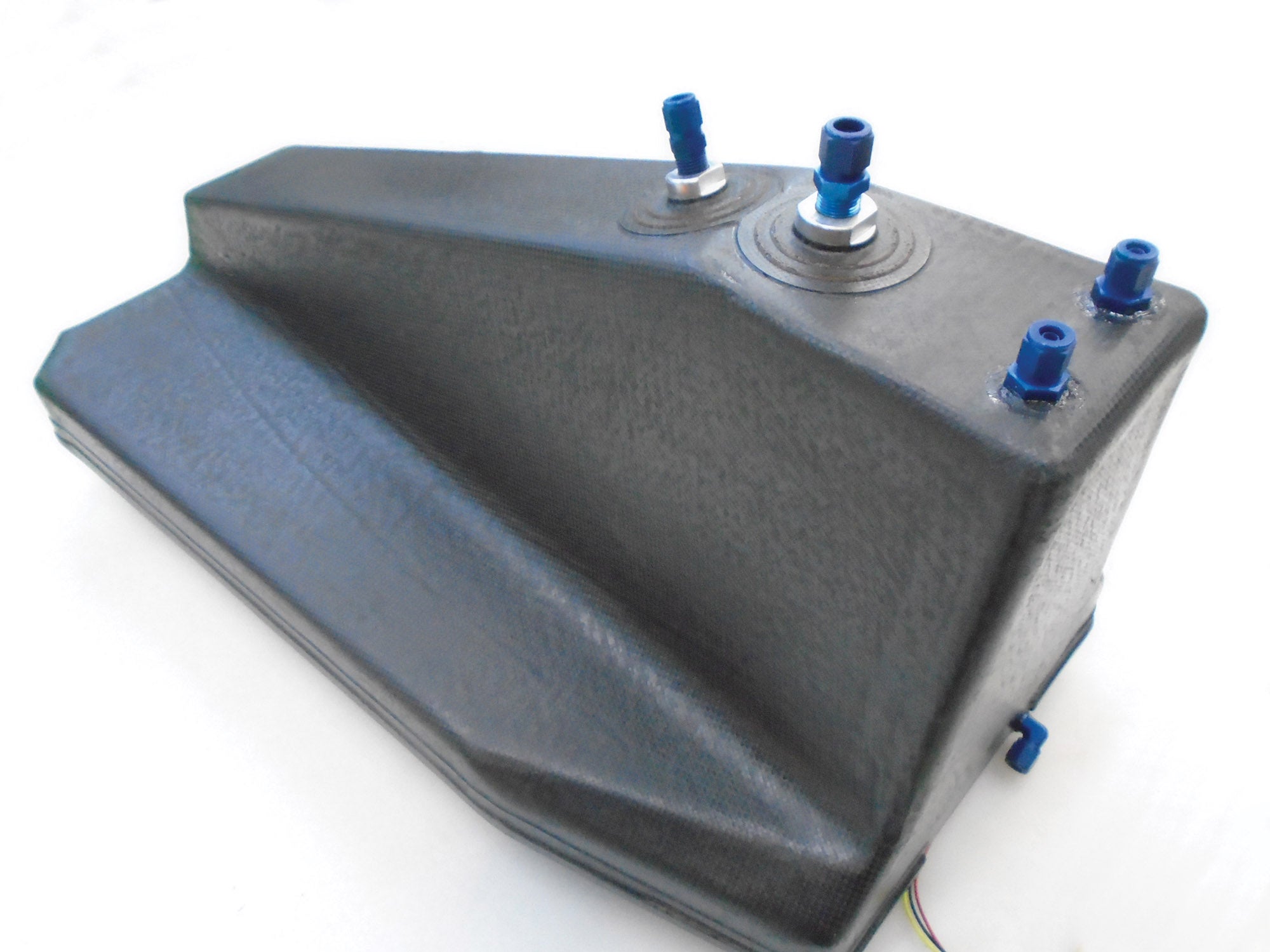
Building the Tank
The space over the pilot’s legs is not an uncommon location for header tanks and was the obvious (and only available) location in the SR-1. The dimensions were constrained fore and aft by the firewall and avionics bay bulkhead respectively; the top of the tank conforms to the upper fuselage, and the bottom of the tank provides clearance for the pilot’s feet. Although most SR-1 components are fabricated in female molds, I decided to use a male mold for the tank.
This choice was dictated by the aforementioned requirement for a light, leak-free tank. Vacuum-bagging was a must to achieve light weight and low void content (unbagged wet-layup composites typically have a significant quantity of voids between layers). Vacuum-bagged molded parts have an A-side and B-side; the A-side is the side against the mold and thus is an exact (inverse) replica of the mold surface and dimensions. The B-side is the other side of the laminate and is a little rougher looking since it just has the bagging materials pushing against it.
In cases where a “Class A” finish is required on both sides, manufacturers use a double-sided mold, caul plate, etc., to give the B side a nice finish as well. That is rarely required in a project like this; for example, I want my A-side wing skins smooth and accurate on the external face, but I’m not overly concerned about aesthetics or smoothness on the internal-facing B-side. For the tank, having a smooth, glossy surface for the interior of the tank is desirable from the standpoint of creating a non-porous surface. The external dimensions have enough clearance from surrounding structure that tightly controlling external dimensions vis-à-vis a female mold was not necessary.
Once I decided on my mold approach, the next decision was whether to fabricate the mold by hand or machine it. As a rule I tend to avoid hand-fabricated molds—I like the ease, precision and part quality of CNC’d (or 3D-printed) molds. However, from a time and cost perspective, for this particular project a hand-built mold had the advantage, and as mentioned above, there was no interfacing driving super-precise tank dimensions. The hand-built approach worked well here.
The first step was to fabricate a mock tank with hot glue and foam board, which allowed me to quickly confirm the necessary clearances. I then disassembled the foam board tank and used the pieces as templates to fabricate a male mold. Other than the top of the tank (which follows the curve of the upper fuselage skin), all surfaces are flat, which allowed the use of melamine-faced MDF for the mold. Melamine releases from the layup easily (assuming you properly wax and release it!), which is why I often use it for flat-surfaced molds.
Step by Step
1. Exterior view of the melamine mold for the tank bottom.
2. Tank bottom interior. I was a little concerned about the ability of the mold to withstand vacuum pressure, thus the interior ribbing.
3. The mold is filled with X-30 expanding polyurethane foam. Radiusing the corners removes the melamine, so these areas are taped over with foil tape as the underlying MDF is porous and doesn’t release well.
4. The X-30 is carved away and a few layers of Bondo are spread on top.
5. Bondo can be sanded to a smooth finish and releases well with wax and PVA. Note: Keep the layers of Bondo relatively thin, no more than ¼ inch. Bondo gets quite hot when it cures; thick layers can generate enough heat to melt the foam underneath.
6. The mold was waxed (I typically wax three times: twice with Meguiar’s carnauba wax and once with Partall #3), sprayed with PVA (four coats: first coat light, subsequent coats heavier) and left to dry between coats. The mold was then coated with a thin film of resin mixed with Cabosil to a consistency like Vaseline. The resin used was Jeffco 1307 with medium hardener 3176. (See “Epoxy and Fuel Resistance Tests” in the May 2018 issue of KITPLANES.) This layer is key for pinhole prevention.
7. The tank is multiple layers of 6-ounce carbon alternating 0°/90° and 45°/45°.
8. Layers are wet out on plastic before transferring to the mold. I suggest five to six layers of fabric for a daily driver—this should avoid pinholes and provide good structural strength (this assumes no foam core).
9. The layup is treated like a typical vacuum-bagged part (laminate followed by peel ply, perforated ply and breather). One exception is that I only pulled about 15 inches of vacuum in order to keep the laminate slightly more resin rich.
10. Compressed air was blown in (through the future drain hole location) to pop the part off the mold.
11. After trimming, the tank was filled with water for an initial leak test.
12. The lower tank is placed back on the mold, and the lid is fabricated identically to the lower tank. The edge of the lid wraps down over the lower tank; this will form a flange to bond to the lower tank.
13. Splash molds are created from the lower tank and lid to fabricate the baffles. Tooling wax (0.050-inch thick) is used to create a bond gap—i.e., the mold is slightly undersized to the tank interior. The thickness of the tooling wax accounts for the thickness of the baffle flange (approximately 0.025 inch) and the bond line (approximately 0.025 inch). The tooling wax is applied at the location of the baffle, then covered in packaging tape. Bondo is then spread over the tape, and an undersize MDF baffle dropped in place. Use a Popsicle stick to make sure the Bondo completely fills the gaps between the MDF and the tank. After the Bondo cures, the MDF baffle is popped out. It will have the exact shape of the tank, minus the gap for the flange and bond adhesive.
14. This picture shows a baffle mold already fitted to the lower tank, ready for splash molding to the lid. The silver foil tape catches any Bondo that squeezes out between the baffle mold and the lid.
15. The baffle is fabricated identically to the tank skin. See my February and March 2018 KITPLANES articles for how to mold flat, flanged parts like the baffles.
16. Longitudinal baffles are an inverted V-shape. Here, tooling wax is laid down to prep for the splash mold.
17. Splash mold underway.
18. Finished baffle mold covered in foil tape.
19. Finished longitudinal baffle.
20. Longitudinal and transverse baffles bonded in place. Also shown is a vent line.
21. Due to space constraints, a sub-flush shelf for the sending unit was molded in a 3D-printed mold. The vent lines also pass through the shelf. Although carbon fiber is electrically conductive, composite tanks should generally have a dedicated ground. See David Gall’s article in Contact! magazine. The grounded probe of a capacitive sender can serve this function.
22. Domed (i.e., fuelproof) nut plates from Click Bond were used for mounting the sending unit.
23. A flapper door allows fuel to flow to the sump but not back out.
24. Be sure to seal any holes or rivets with superglue (a thin CA like Jet Instant wicks nicely) and/or use bond beads when bonding aluminum to carbon to avoid galvanic corrosion. Fiberglass is not conductive and does not pose a galvanic corrosion issue.
25. Through-fittings were of two types: threaded-bung and permanently bonded. Bung fittings were used for the main fuel outlet and tank drain. Because the bung is bonded to the bottom of the tank, the union threaded into it sits below the floor of the tank, allowing the tank to be completely emptied through either the drain or fuel outlet. AN867 weld bungs were machined with flats on the neck and the base machined flat to accept a “bond washer” that encapsulated the bung when bonded to the tank. Flats on the bungs are extremely important as torquing in the union fittings without holding onto the flats could potentially delaminate and/or spin the bung.
26. Bond washers were fabricated from 3D-printed molds. To avoid squeeze-out from bonding to the finger strainer mesh, flash tape was applied around it. Likewise for the drain, a yellow plug was 3D printed to keep squeeze-out out of the hole.
27. Because my solvent exposure tests did not look at structural adhesive, all bonds for the tank were made using Jeffco 1387, with Cabosil and flox added for thixotropic and structural reinforcement, respectively. In addition, bond line controller glass beads (from Rock West Composites) were added to avoid galvanic corrosion.
28. Bulkhead fittings were used for the fuel transfer and fuel return lines. These are inserted through their respective holes, the opposing nut threaded on and then the whole assembly brushed with epoxy to seal before torquing tight. Heat shrink tubing is used to protect the B-nut threads from epoxy during assembly and is removed after cure—just reheat with a heat gun and pull.
29. This photo shows the fuel transfer and return lines (left) and fuel pickup (finger strainer) and drain hole (right). Also shown is the one-way flapper door to prevent fuel from leaving the pickup area at high angles of attack. (Blue tape is masking for the sump baffle.)
30. The flange of the lid fits in a slot around the perimeter created by a set of four joggled strips that bond to the perimeter of the tank.
31. The four strips that bond to the perimeter of the tank. During closeout, this slot is filled with the epoxy/Cabosil/flox mixture. When the lid is pressed into the slot, adhesive flows to both sides of the slot and creates a fuel-proof bond on both sides of the lid flange. This is more work to set up, but virtually guarantees a leak-proof assembly. This is especially important since access to the inside of the tank is impossible once it is closed out, and sealing leaks from the outside of the tank can be difficult.
32. The tank bottom prepped with a perimeter of 0.060-inch tooling wax to create the joggle strips shown in Photo 31.
33. Fill cap and scupper. The cap is a modified version of the cap shown in the original Long-EZ plans (Pages 21 through 25). It works well and is significantly lighter than off-the-shelf caps. It bonds directly into the neck of the scupper. (As with all metal-to-carbon bonding in this article, spacer beads are used.) The scupper serves to collect any spilled fuel. The scupper here was fabricated in a 3D-printed mold using a woven carbon sleeve.
34. Tank and lid masked for closeout.
35. Closeout adhesive applied to the baffles. Masking tape keeps the process tidy and is removed before closeout.
36. Lid bond slot filled with closeout adhesive.
37. Lid assembled to main tank and weighted down to ensure good bond contact with baffle flanges.
38. The tank is pressure tested with the balloon method (see Van’s Air Force forum for tips on this test). The neck of the balloon is slipped over the drain fitting and sealed with string. A length of aluminum tubing with a Schrader valve bonded in one end and a flare/B nut is attached to the fuel outlet. Note the plumber’s tape on the fuel transfer/return fittings; Teflon tape should not be used in fuel systems, but for the leak tests it helps prevent air leaking through the fittings.
39. Carbon brackets with G10 hardpoints are bonded to the rear of the tank.
40. Forward brackets include nut plates. The tank can be dropped and removed from the airplane by removing the two rear bolts and two front screws.
41. Tank being prepped for static load testing. Foam under the tank isn’t supporting the tank; it’s just there to prevent damage to the tank in case a bracket fails during the load test.
42. Tank supporting a 7G test load.
Final Thoughts
Fabricating a custom tank is a significant amount of work. Inasmuch as I hope some readers can use these fabrication articles to guide their own DIY efforts, I also hope they’ll convince folks of the huge timesaving benefits of kits and why builders are often warned of going “off script” with modifications. To be sure, there is immense gratification in creating your own custom parts—just be sure to understand the significant time investment.
Many thanks to Andy Chiavetta for advising me during this project (as he has on many others).
Photos: Eric Stewart
Eric,
Could you explain your technique on this?
“bond beads when bonding aluminum to carbon”
Super impressive work, as per your usual. Great to learn from.