The wisdom of installing personal restraints in your homebuilt aircraft is not debatable; only the type and manner of their fitment is under discussion. Given that lap belts are going to be needed for airworthiness certification, it makes a lot of sense to put in shoulder harnesses as well. Builders agree: We just don’t see many modern homebuilts rolling out without at least a single shoulder harness.
It would make sense to understand what standards certified aircraft are required to meet, and how we can improve on those requirements, under the freedom of Experimental/Amateur-Built certification. Most homebuilt airplane designers work with FAR Part 23 standards in mind, which assures some common starting point even though deviations are permitted in the Experimental category. The important fact is that no kit designer wants the liability of creating a design with less-than-defensible restraint systems, or at least recommendations.
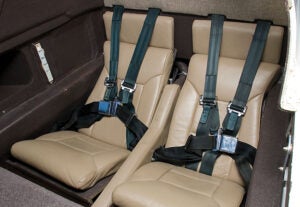
Paragraph 23.561 requires occupant protection from serious injury when subjected to accelerations of 9 G’s forward, 3 G’s upward and 1.5 G’s sideward for normal and utility category airplanes. For acrobatic category, the upward load is set at 4.5 G’s. For testing, older certification standards specified an occupant weight of 170 pounds, now more realistically changed to 215 pounds in newer aircraft. In addition, the testing criteria assumes a 1.33 “fitting factor” as a safety margin when calculating loads.
Under paragraph, 91.205, shoulder harnesses became mandatory for front seats in airplanes manufactured after July 18, 1978, and all seats had to be equipped with a shoulder harness or restraint system if the aircraft was manufactured after December 12, 1986. Technical Standard Order (TSO) C114 covers the specifications for torso restraint systems and TSO C22 covers safety belt specs. Look for such labeling, or its equivalent, on the restraint you’ll be installing if you want to be sure it meets the FAA’s standards.
In most cases, it’s simpler and cheaper to purchase pre-made seat belt and harness kits from aircraft supply houses than to create your own. Many restraint manufacturers have assemblies specifically designed for popular kit aircraft.
In general, 2-inch or 1.75-inch webbing with a thickness of 0.04 to 0.06-inch is used, usually meeting or exceeding a 1500-pound strength requirement. However, the amount of pull on the entire system during certification testing is going to be approximately 2500 pounds. If using both lap belt and shoulder harness to meet the required loads, 60% of the strain is to be attributed to the belt and 40% to the shoulder harness. The nylon webbing that was once used in restraints can stretch between 17% and 20% under a 2500-pound load. Dacron webbing stretches about 8% under the same load. Most belts and harnesses sold today use polyester webbing. In any event, one should avoid an excessive length of webbing when considering how to do the installation. One solution to the stretching issue is to use a link of flexible steel aircraft cable to reach from the airframe attachment to near the seat position, so the belt’s attachment point minimizes webbing length.
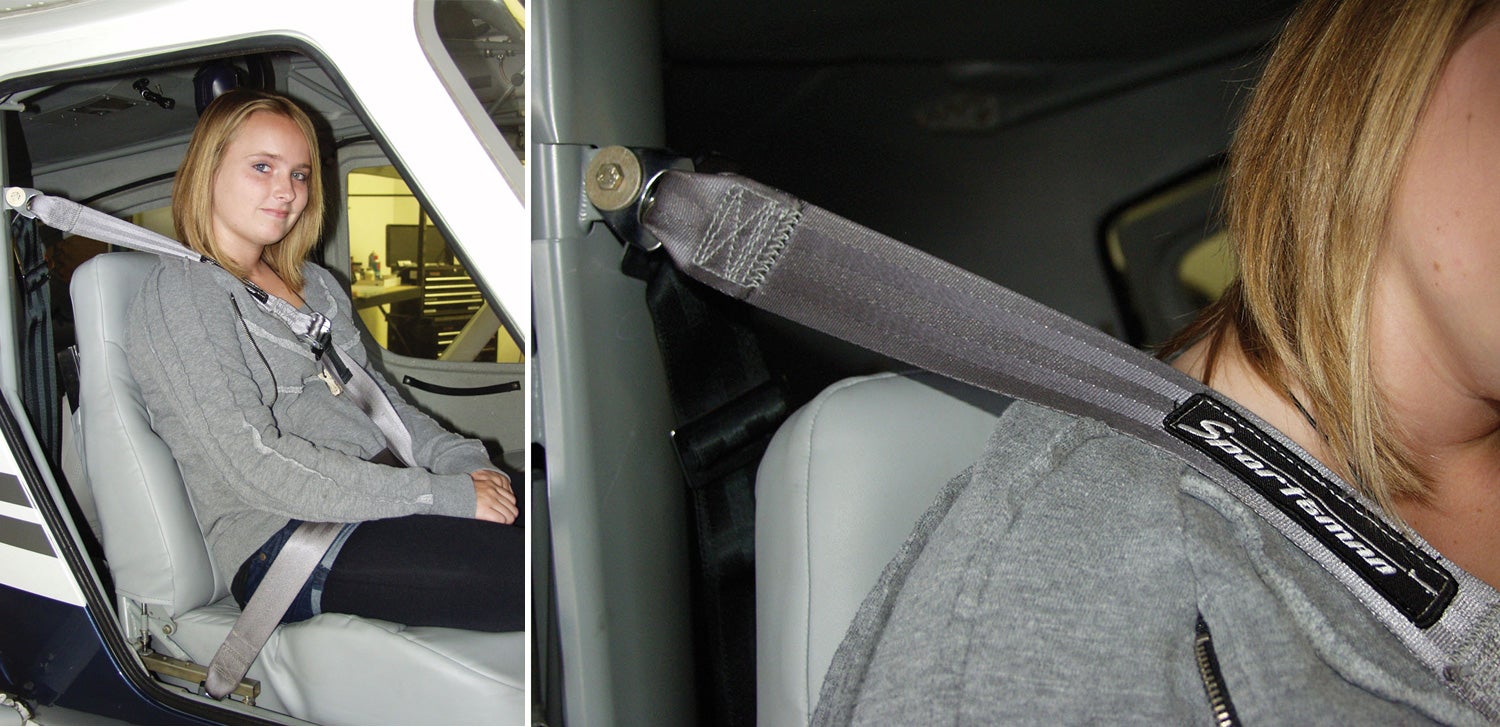
Placing Attachments
Proper mounting of the seat belts and shoulder harnesses is critical. The lap belts should attach so as to slant at approximately a 45° to 55° angle relative to the longitudinal axis of the aircraft (which allows for some adjustment of seat position), so the belt remains over the hips and pelvic region during a crash, rather than across the thighs or abdomen. The shoulder harness, as part of a total system, must not contribute to migration of the seat belt or displacement of the occupant from the seat. To do this, shoulder harness attachments and guides should lead harness straps to approach from behind the shoulder in a range from 5° below horizontal to 30° above.
Lap belts are simple, with few options; shoulder harness restraints, on the other hand, are available in various forms, from single belts fitting diagonally across the body like automobile restraints, to dual belts across both shoulders, usually attached to a single fitting directly behind the seat. Five-point restraints, incorporating a “crotch strap,” are commonly installed in airplanes used for aerobatics, properly termed a “negative G” strap, to prevent upward migration of the lap belt. For crash protection, the single shoulder harness is perfectly suitable, if properly installed and adjusted in conjunction with the lap belt. Dual harness spreads the load of a crash but can allow “submarining” of the body in some circumstances, unless a crotch strap is added. For serious aerobatics, IAC competitors must wear a dual lap belt as part of the five-way harness, and ratcheting adjustment devices are part of harnesses specifically designed for aerobatics.
To perform properly, a single-belt shoulder harness must lie across the shoulder and chest, crossing at the midpoint of the shoulder and extending to the opposite hip, at an angle that neither touches the head and neck nor permits the harness to slip off the shoulder. The lower end of a diagonal single-belt harness should not connect to the mid-point of the lap belt, but at or near the belt’s attachment beside the hip.
Dual harnesses, extending over each shoulder and connecting to a common release point with the lap belt, depend on having the lap belt rising from attachments 45° behind the hips, in order to prevent the lap belt from being pulled upward in a crash. If the harness originates at a central attachment behind the seat, an adjustable yoke can be used to prevent neck injury from having the two harnesses lie too close together. Connecting the dual-strap harness to a floor attachment requires having guides at the top of the seat back to keep the geometry correct. The seat back must rise to shoulder height, typically about 25 inches above the seat cushion.
If attaching belts and harnesses to the seat structure instead of the airframe, consideration has to be given to the strength of the seat’s mounting, which now assumes the task of retaining the occupant in a crash. While having the belts on the seat frame is an attractive option, allowing you to adjust the seat after tightening your belts, hard-point attachments to the airframe are probably more preferable.
Seat belt end fittings are available in quick-disconnect style, as well as simple bolt-on types. If using a quick-disconnect fitting, be sure to install a cotter pin to immobilize the swiveling arm that allows it to unhook from the attach point so it can’t be tripped inadvertently and come loose.
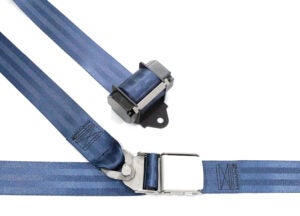
The Reel Thing
Retractable reel shoulder harnesses have the advantage of avoiding having to adjust the strap length for different individuals and allowing some freedom of movement; however, some individuals object to the constant pressure of wearing the steady tension of a reel-type harness. Mounting of the reel must allow extension and retraction in a straight line to avoid binding or wear on the webbing, preferably with a guide as part of the reel assembly.
There are different types of retractable reels, commonly referred to as “inertial reels.” All of them are designed to lock against extension of the strap in a crash, but one style locks because the webbing extends, under an acceleration of .75 to 1.5 G’s, while the other type only locks if the mounting structure and reel are being accelerated. In addition to these emergency locking retractors, there are also automatic locking reels that only permit extension to buckle in, but lock up as soon as retraction begins, leaving 6 inches or so of free movement thereafter.
Buckles must utilize metal-to-metal latching, rather than threading a belt end through a latch, and it should be possible to release and escape from all belts by a single action, ideally with only one finger. Maximum release force required should be no more than 12 pounds, without G-loading or suspended weight. The usual aircraft seat-belt buckle will have a lift-handle release that allows the two halves to slip apart, the single-strap shoulder harness being carried away by the released seat belt. Dual-strap shoulder harnesses are normally connected to the buckle’s inserting tang by slide-on fittings, disconnecting as the released lap belt pulls apart.
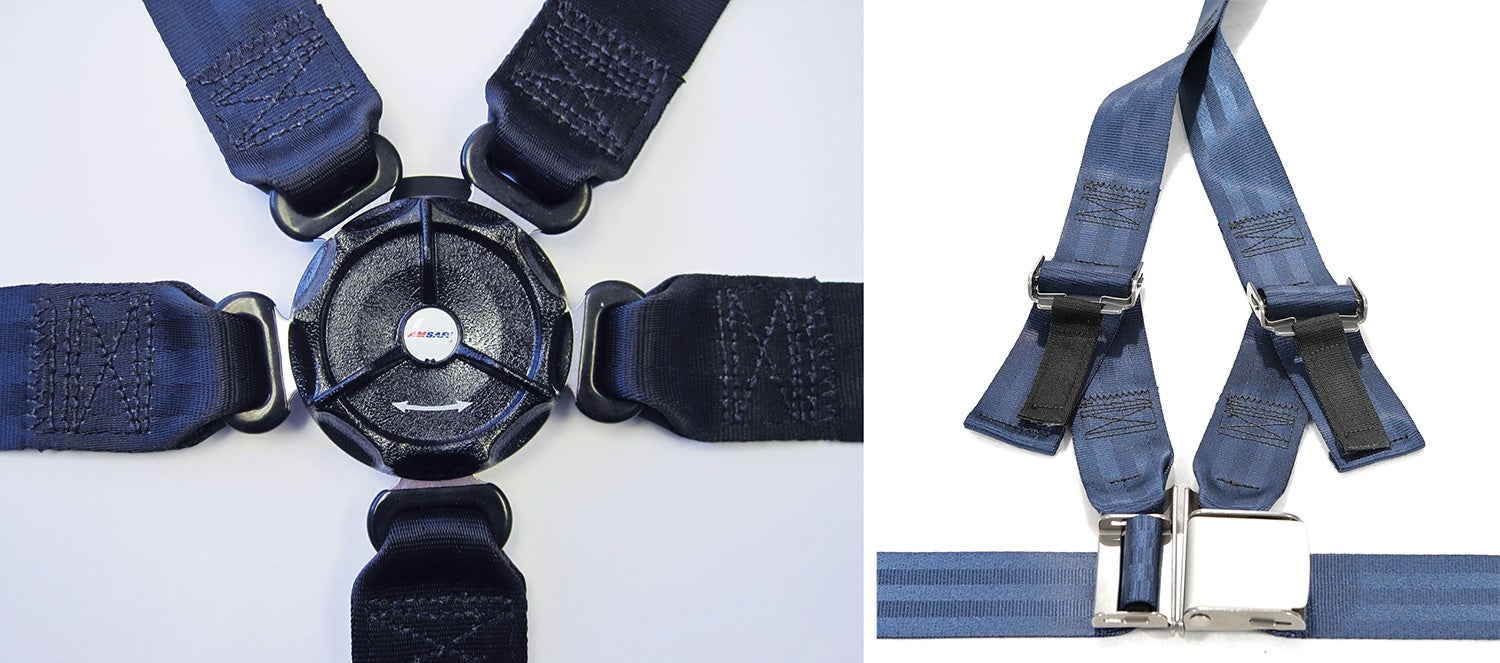
Rotary buckles are another popular option, incorporating insert slots for the fixed portion of the lap belt and two shoulder harnesses, as well as a negative-G crotch strap. They can be quicker to don and easier to release with a deliberate twisting action, while remaining secure against accidental snagging of a release lever. Military-style buckles use a hook-and-latch fastener.
Making Solid Points
Installing the attachment points connecting restraints to the airframe will usually require reinforcement of the structure to prevent them from tearing away in a crash. The fittings supplied with belts use a single bolt loaded in shear, leaving the fitting free to swivel around the bolt as the belt moves. These fittings attach to a tab riveted or welded to the airframe, with intercoastal reinforcement between stringers, in the case of metal structure. If attaching shoulder harnesses to an overhead wing carry-through, the spar hat section will need reinforcement riveted inside.
If connecting belts to tubular structure, it’s important to locate the fitting at a tubing cluster, rather than in the middle of a single tube. The load path is thereby spread across the structure, rather than concentrated. Section 9 of our old friend, the AC 43.13 manual, shows some acceptable methods of attaching fittings to structure. Of course, composite construction simplifies mounting the attachments; just pick a spot, lather on extra layers to reinforce the load and mount the metal tabs.
Hopefully, your kit supplier has established suitable attach points for restraint systems as part of the fuselage assembly. If you’re installing belts and harnesses on your own, bear in mind the proper geometry and crashworthiness of these life-saving items. Take no shortcuts when it comes to preventing injury in an accident.
Who’s Making It?
Many aviation supply companies offer off-the-shelf seat belt and shoulder harness components, and there are several custom manufacturers that can produce exactly what you need for your homebuilt, with the color, style and accessories you want. Perhaps you want some padding under your shoulder harness straps, or you have a girth problem that requires extra length. Here’s a short list of some providers that will get you buckled up as you start thinking about restraints in your project:
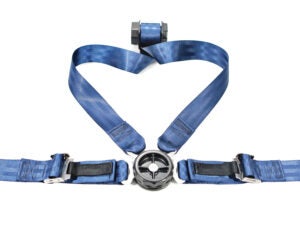
Aircraft Belts, Inc.
Long famous for replacement and refurbishing of certificated airplane restraints, ABI is expanding into the Experimental aircraft market. By mid-2020, in time for AirVenture, it will offer a low-cost non-TSO’d four-point restraint with a rotary buckle release, in a full choice of webbing colors. Pull tested to 3000 pounds, the new harness system will be sized to fit RVs and other popular Experimental aircraft, for which the TSO process is not required.
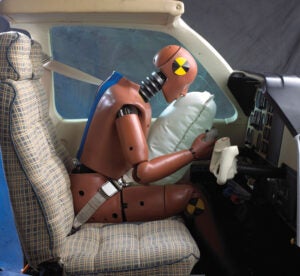
AmSafe
As a primary supplier of airliner and military restraint systems, AmSafe has belts for a wide variety of general aviation aircraft. For even more crash protection, AmSafe markets an airbag system, suitable for certificated and Experimental airplanes, that inflates in a crash situation to reduce injury. Unlike dashboard-mounted automotive systems, the bags in AmSafe’s State Of The Art Restraint System (SOARS) are contained in the harness. If it detects a sustained acceleration of 9 G’s or more, SOARS automatically inflates a pillowing cushion away from the occupant, reducing head and torso injuries.
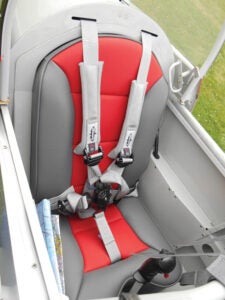
Crow Enterprizes
Family-owned Crow Enterprizes is well known for auto racing safety harness, but it also has a full line of kits for Experimental and certificated airplanes. You’ll find Crow gear in RVs, Sonex, Cub clones and lots of others. Lengths and hardware are customized for the individual model of aircraft.
Hooker Harness
One of the premier suppliers of competition aerobatic restraints, Hooker Harness can fit belts into your sport and certificated airplane as well. The company pioneered the ratcheting belt tightening device in 1982, which will take up the two to three inches of slack that gives novice aerobats a start when they come off their cushion during a hesitation slow roll. Conventional sets are available for certificated airplanes, but Hooker has sport and Experimental airplane harnesses for Van’s and other kits, as well as military-style belts for the warbird crowd.

Simpson Race Products
Another race car harness builder, Texas-based Simpson Racing also does aircraft belts, shipped from its North Carolina facility. The newest line of complete harness systems from Simpson Performance Products features five-, six- and seven-point aviation harnesses for a wide variety of Experimental aircraft, aerobatic planes and historical/military restoration planes. Simpson harnesses use premium polyester webbing only.
Bottom-Lining It
No matter whose belts you choose, be sure you’ve installed them to the manufacturer’s specs and have followed the recommendations of your kit creator. There are many places where going off the path where design is concerned is just one nice feature of building your own. Just not with restraints.
Photos: Kevin Wing, Marc Cook and Courtesy of the Manufacturers.