Many aircraft kits are designed around the use of blind rivets—also known as pulled rivets or “pop” rivets (POP rivet is a trademarked name). For Experimental aircraft, the blind rivet can give traditional solid riveting a run for the money. This is because if we compare the two riveting technologies (solid rivets versus blind rivets), there is one big advantage in that blind riveting needs access to only one side of the work to set the rivet. Compare this to traditional solid riveting that requires access to both sides as we need to hammer on one side and “buck” from the opposite side. Also, a substantial amount of practice and experience is necessary to perform solid rivet installation. Blind rivets can be installed by a novice, often the very first try!
The decision to use blind rivets in aircraft construction should always be left to the aircraft designer. You should not blindly substitute a blind rivet for a location where a solid rivet was specified (there are special rivets made for that). But as builders we should be able to understand and identify the variety of blind rivets available as we will no doubt require their use in some related project (for example: custom instrument panel construction). There are hundreds of varieties and sizes of these rivets available in general industry, so we will limit our discussion to those most commonly used in light aircraft construction.
There are four important characteristics of blind rivets we should be familiar with: the material used for the rivet body, the rivet diameter, the grip length and the head type. One of the best ways to become familiar with these is to grab a rivet supplied by your kit and try to identify these characteristics. Also take note of the specific application where this rivet is being used to appreciate how it was selected for that job.
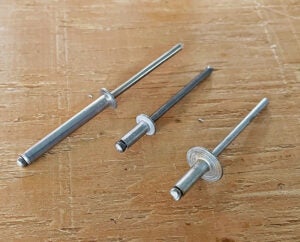
Rivet Material: The two most common materials used for the body of the rivet are aluminum or stainless steel. (The rivet stem or mandrel might be a different material than the body.) As you can imagine, a big decision in choosing these materials has to do with the desired strength of the fastener. If you think that an aluminum blind rivet should not be used in the structure of an airplane, be aware that one of the most popular kit aircraft sold and flying today (and for the last 40 years) is primarily constructed with thousands of aluminum blind rivets! (It’s found in the Zenith Aircraft family of planes.)
So, it is the creative, calculated use of these fasteners that makes them strong. One example of strength: a typical aluminum 1/8-inch diameter rivet has a shear strength in the range of 100–200 pounds. A stainless steel rivet of the same size is typically double that strength. Shear strength measures how hard it is to cut through the rivet body. If tensile strength is critical, stainless steel rivets have greater than three times the strength of aluminum blind rivets of that same 1/8-inch diameter. Tensile strength measures how hard it is to pull the rivet apart (pull the head off, for example).
Rivet Diameter: Just like any round fastener, you have a choice of the rivet’s diameter. Looking at a table of rivet specifications, we see that both shear and tensile strength increase as the diameter grows. Typical diameters used in kit aircraft include 1/8, 5/32, and 3/16 inch. The tiny 3/32-inch diameter rivet is wonderful for quick installation of small nut plates with small ears.
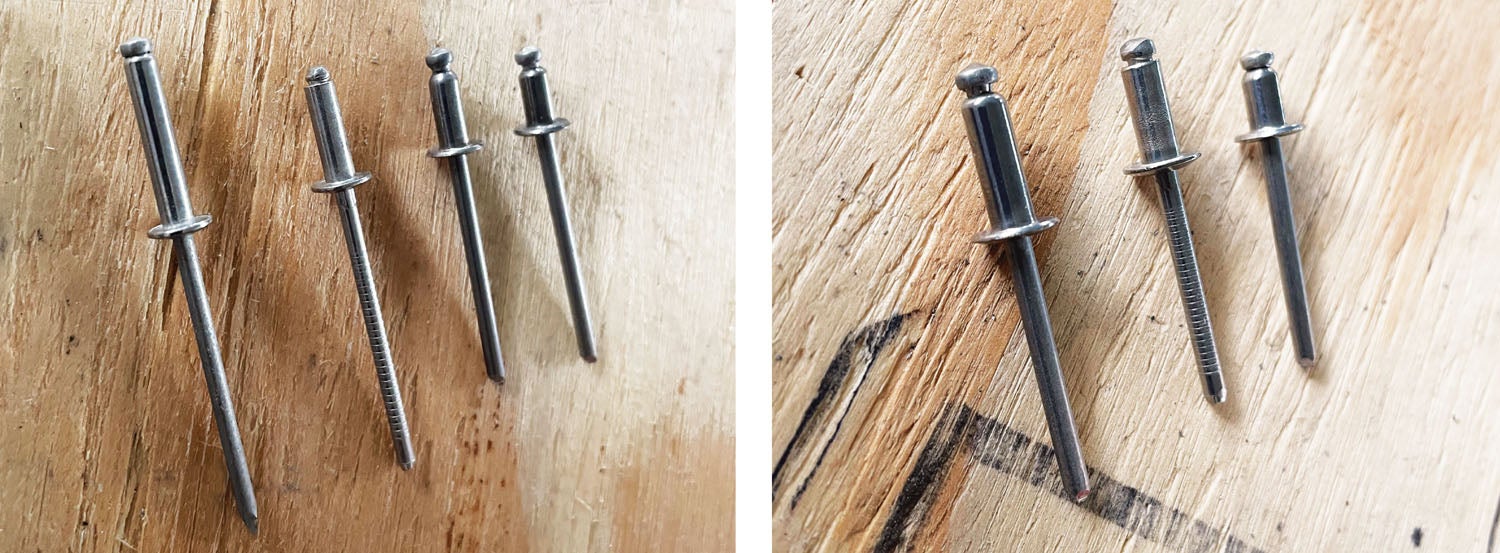
Rivet Gripping Length: This is an important and sometimes hard to measure characteristic. Because of the way a blind rivet is designed to hold your material together, it has a minimum and maximum range of grip. Grip is defined as the total thickness of the materials you are trying to hold together. You must choose a rivet that has a grip length range that matches your work.
Here’s the tricky part: You cannot pick up a random rivet and necessarily know its grip length. Of course, the grip length of that rivet will be shorter than the total rivet length—but by how much? Looking at rivet specification charts, you can compare a rivet’s total length with its grip length and calculate the difference. But as you keep studying the chart, you will find that size changes as the diameter changes. The good news is that you typically only work with a small number of blind rivet sizes and then can learn to identify grip lengths of those that you work with often.
Head Type: The part of the rivet that remains visible on top is the head, and there are a couple of popular styles we use. The dome head is typical and easy to identify; the countersunk head requires a dimple in your material in order to sit perfectly flush. Blind rivets can also have an extra large dome (such as used on soft engine baffling material) to keep the head from pulling through.
Much can be learned from looking at blind rivet catalog specification tables that allow you to see what diameters, grip lengths and head styles are available. The shear and tensile limits are also listed here. Sometimes, our popular aviation supply vendors do not show these tables. This may be because they are providing replacement rivets for popular kits and only rivet sizes are shown to make it easy to select.
A large-scale industrial supplier like McMaster-Carr has very detailed specifications of all the rivets they carry. Purchasing unknown rivets from a hardware store might be OK for non-critical projects. But by understanding the blind rivet specifications required for your project, you can make informed choices when obtaining rivets for more critical needs. Plane and simple!
This is not a very in depth article. There are many more types of rivets. Zenair aircraft are put together with a different spec rivet called AVEX rivets. There are closed rivets for fuel tanks. Some rivets have aluminum mandrels for area where minimal strength is required and are much easier to remove. Drilling out an aluminum rivet with a stainless steel mandrel can be very tricky. What the author went into was a very basic description of hardware grade rivets. Most builders will be beyond this level of knowledge.
Of course Ray , but this was a good place to start for some of us . AVEX rivets ….I’ll go look it up ! LOL .
I’d like to know more about removing blind, or pop rivets…..drilling or grinding, or what ever where the material being held together is not damaged……..or, where to go to find an in depth article on doing just that.
John
I have been an IA fir over 30 years. I realy like the articals you write , very clean and direct.
I am putting tigether an inspectors class for Light Sport Repairmen. I would like to talk to you about using some of your videos and or articals with in the sylabus
Could you give me a call to discuss this
Ron Edson
207-595-1271