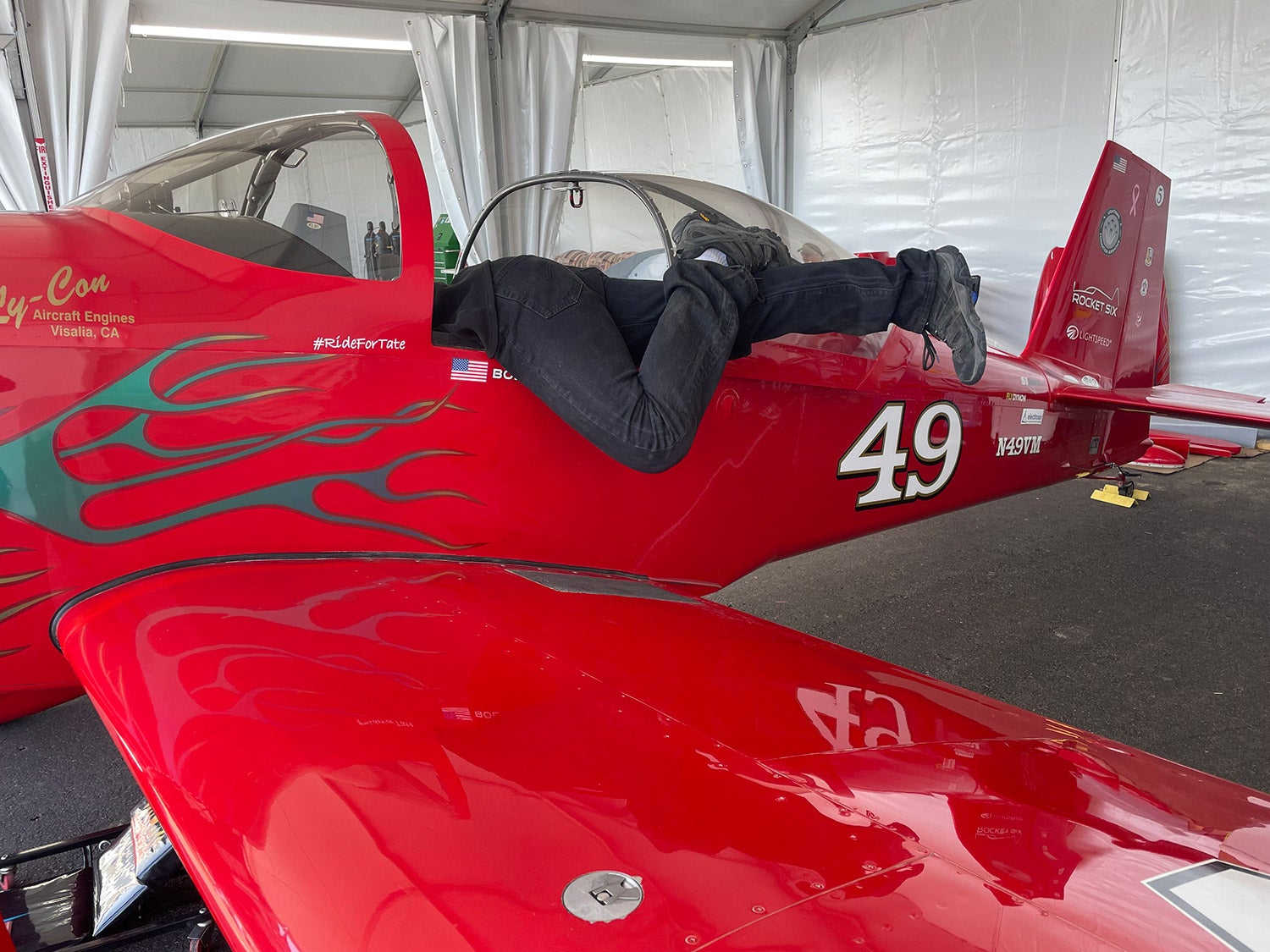
As competitive as he is, Sport Class President Bob Mills is first and foremost a pilot with excellent judgement. So when he taxied out for Sunday’s Silver heat with the rest of the field, he did what he always does – checked out the airplane to make sure it was ready to race. And it wasn’t. During his run-up, he noticed that his fuel pressure was reading only 11 psi on the mechanical pump, and while it rose to 19 psi on the boost pump, this was still below the normal pressure of 25 psi you want to see for a fuel injected engine. So despite almost two years worth of preparation, modification, and testing for this years race, Bob did what all good pilots would do—he scratched himself from the heat and taxied back to the pits. It was disappointing, but it was safe.
With his race day finished, Bob still had to figure out the problem, because he and his airplane needed to head home to Texas, so the crew got to work. They pulled the fuel filter first—it checked clean. Next, they set to work pulling the cowl to access the firewall forward aspects of the fuel system, while at the same time, thinking what else could cause the problem. Mechanical pump, boost pump, filter, lines, fittings, tank pickups—they were all discussed. The system was pressurized with the boost pump, and tanks were switched, to check for a pickup blockage—there was no change. Other experts from the racing field were brought in, and much discussion circled around the accuracy of the relatively old fuel pressure sender.
A crew member was sent to the local AutoZone for an old fashioned pressure gauge while others rummaged through boxes of AN fittings to find a way to connect the temporary gauge into the system. Finally, the gauge arrived, and was attached. The pump was turned on, and instantly, the gauge registered 32 psi – right where the pump regulator was supposed to be set, according to Robert Paisley, the pump builder who was also at the races! So what aborted Mills race was a faulty indication—not uncommon in the aviation world.
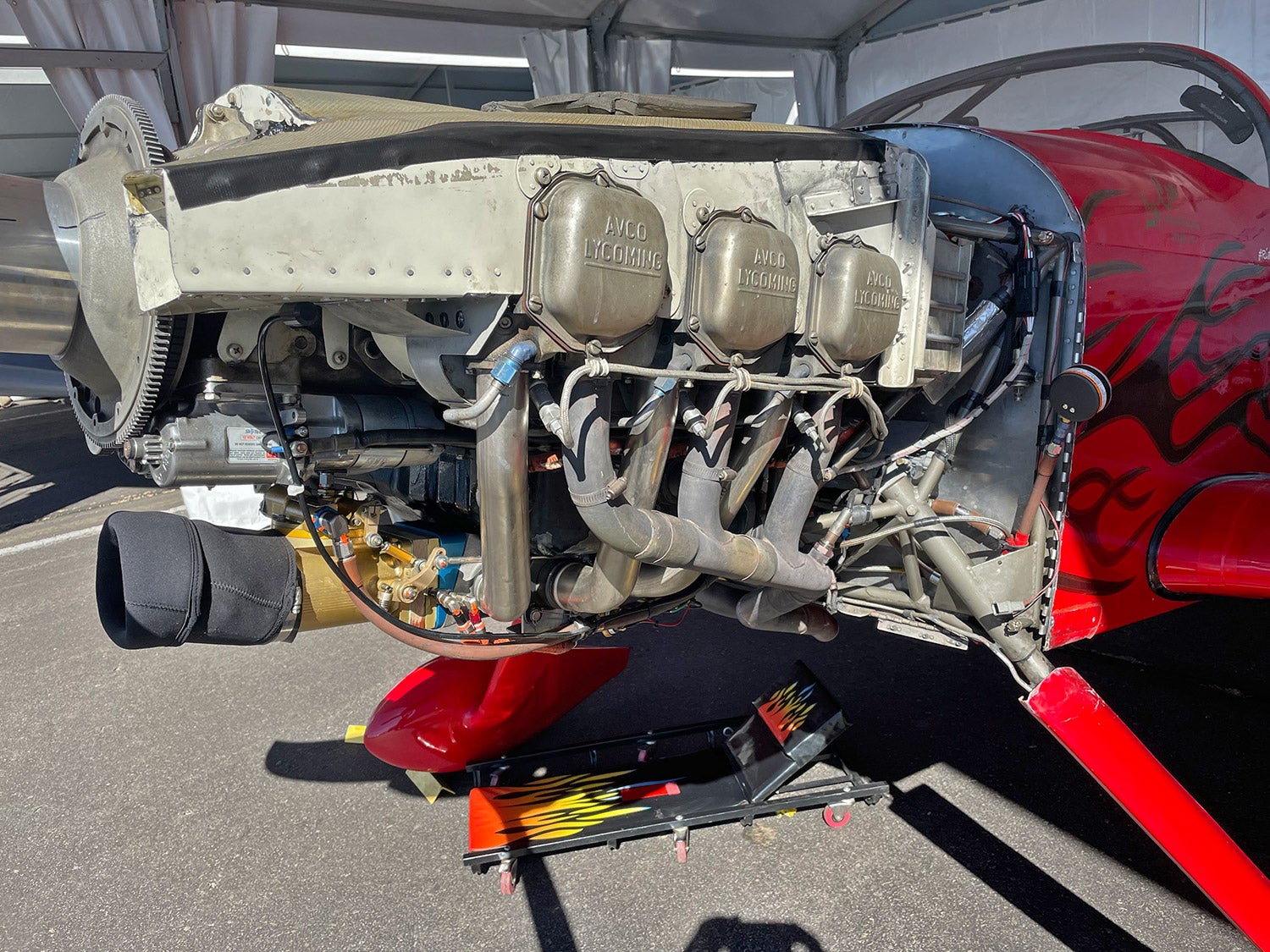
Paisely suggested that just be sure, the team should do a fuel flow test, and suggested that his pump should supply about 60 gallons per hour if operating up to snuff. A gallon jug was secured and the fuel lien to the servo removed. Pump on and it took 30 seconds to half fill the jug. That means a minute for a gallon, or 60 per hour… Bob was good to fly to Texas!
The real message here is that even when you’re really pushing to participate in an aviation event, it is always better to be safe than sorry, The low pressure could have been caused by an obstruction, a leak, or some other faulty component that could have caught Mills out on the race course. So he took the safe route and scrubbed even though the problem turned out to be only an indication. Does that mean he made a mistake? Absolutely not! He made the right decision with the information available and that is always a win in our book.
Fantastic self control; a win indeed!!! Thank you for reporting this valuable lesson.