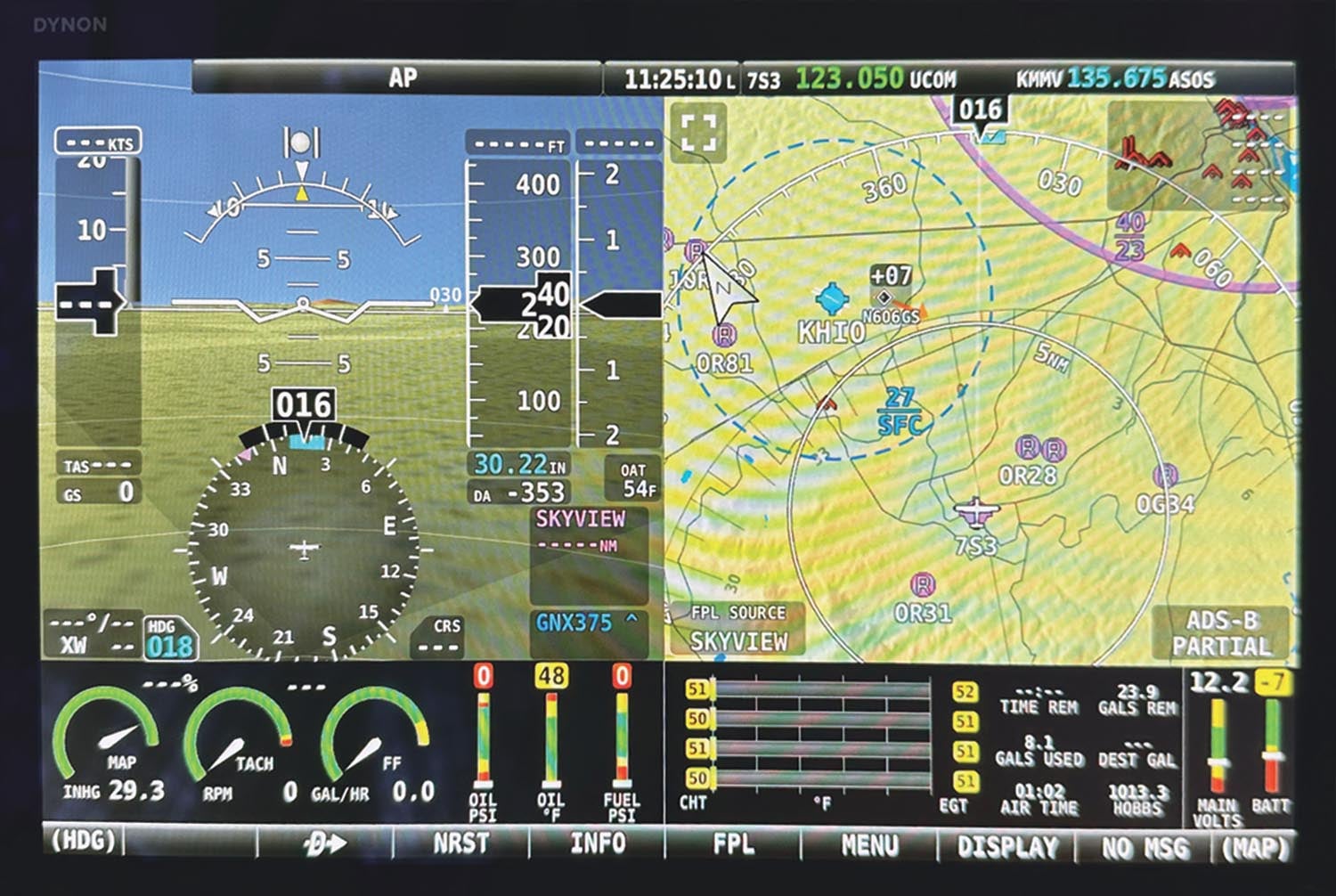
Humans are amazingly adaptable but sometimes we lack imagination. Here’s one example. When it came time to upgrade my airplane’s panel to full-size modern glass, it was after spending time with different systems, trying to understand the philosophies behind both the presentation and the ergonomics—switchology and knobology. After all, these are things you can’t often control but have to live with once invested.
Your first few minutes with any new display can be discomfiting. I vividly remember jumping in an airplane with the then-new Advanced Flight Systems big EFIS, which had a lot of forward-thinking features and presented a massive amount of data to the pilot. All the time. I worked really hard just picking out airspeed, altitude, vertical speed and heading. Somewhere on the display it probably showed the pitch trim setting in tenths of a degree and the brew-head pressure of the closest Starbucks espresso machine, but I couldn’t tell you what they were.
Fortunately, modern EFISes follow display conventions, so while there are differences in the way data is displayed it’s more similar than different, a result of constant refinement since the first tape-style displays appeared in Experimentals more than two decades ago. Even so, my research had caused me to form an opinion of the Dynon SkyView system on the newer HDX screen that hasn’t, I’m happy to say, survived actual use.
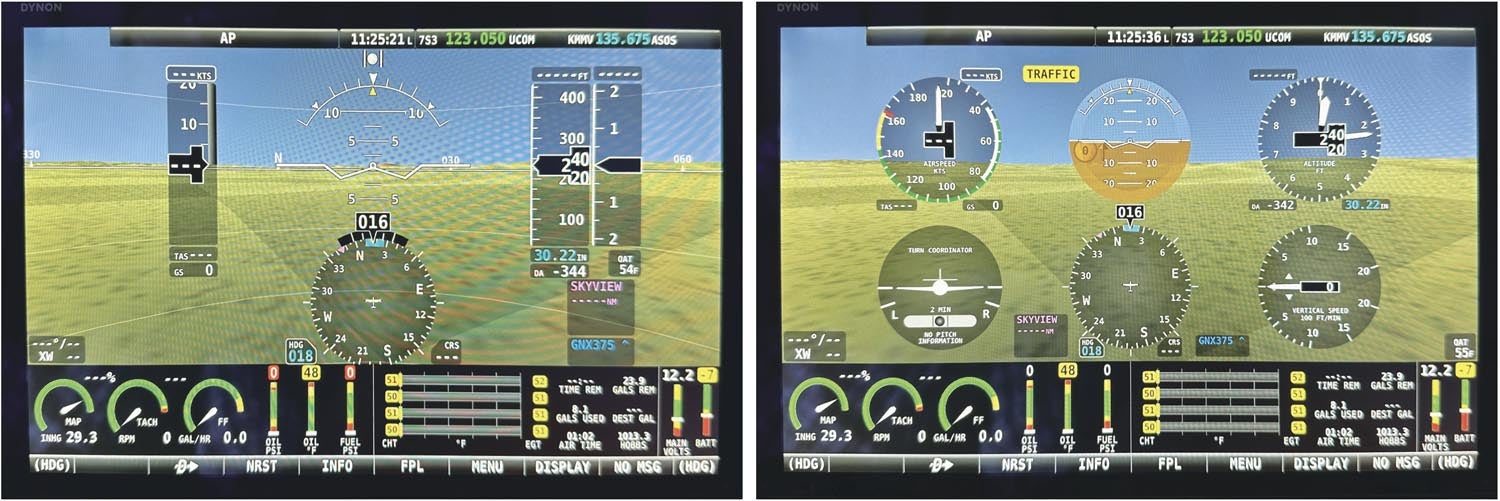
Whether you have the 10-inch or 7-inch display, Dynon crams a ton of information onto one screen. (They can each show the same things; the only difference is scale.) Moreover, you have the choice of one of three full-screen views—primary flight display (PFD), multifunction/map display (MFD) or engine monitoring—or, as is more typically used, a hybrid, with all three major functions shown at once. All are easily toggled on or off, and there are ways to tailor the displays to the way your brain works, to some degree.
When you look at the single screen with all the data present, it does at first just seem like too much. And this is after I spent a couple of weeks with the unit powered up at my desk so I could learn where things were and what the menu system did without having to fly the airplane as well. In actual use, over the first couple of hours, if you’d asked about the OAT or the oil temp, I’d say, “Ahhhh, give me a second.” Of course, I’d taken the trouble to set up all the colored ranges for systems monitoring, so the absence of red or yellow blocks was a good first sign. But I hadn’t yet formed a mental picture of what’s “normal” for the airplane in key phases of flight. That would come later.
Time, the Healer
I was also concerned that the semi-opaque data tapes overlaying the synthetic vision would inhibit really “seeing” the space around the airplane. My fears were quickly allayed. Again, the brain is an amazing thing, and I soon found it easy to absorb the data as needed and single out the items I was interested in at any moment. It’s like developing a good instrument scan, only that the items are all closely grouped; there’s not a lot of eye movement necessary to get the full picture, so to speak. Plus, I started getting in the habit of switching to the full PFD screen during practice instrument approaches because the secondary information on the moving map becomes less important than following the nav guidance.
All of these skills are really a kind of mind-muscle memory game. Keep flying the system, read the extensive documentation and understand how it’s intended to be used. Within a fairly short amount of time, you’ll have it figured out.
I do have one habit I’m still trying to break. Previously, I had a TruTrak autopilot commanded by the bugs on two Garmin G5 displays; the attitude indicator had the altitude bug, which the autopilot followed, and the HSI had the heading bug. The heading bug is always live on the single knob on the G5 but the altitude bug needs you to push the button first, turn to the right menu, push again and then set the value. I got in the habit of pushing once more to dismiss the menu. With the Dynon knob panel, all you need to do is turn the HDG/TRK, BARO and ALT knobs. If you, like me, push them after, they’ll sync to existing values, not the ones you just set. This is actually a great feature and a time-saver as Dynon intended.
So you fly and learn. The ultimate point is this: I may have wished for less information or the ability to strip the presentations bare, which you can partially do with a “six pack” configuration, but many of the data fields in the EFIS presentation are fixed. After flying the system for a few hours, I’m glad to have it all.
What About Redundancy?
I was around for analog instruments and the beginning of glass, when it was assumed that something would fail or that a display would brick at the worst possible time. So you build redundancy into the system. While it’s true I have a lot of eggs in the Dynon basket, now that I know how the system is designed and implemented, my mind’s at ease. There’s significant internal redundancies, plus I’m keeping both an independent EFIS, a uAvionix AV-30, and an iPad running ForeFlight at the ready. Each Dynon screen has its own backup battery, as does the AV-30, the iPad and the Sentry GPS/ADS-B In module. While it’s not as extreme as my old setup, which retained analog pitot-static instruments, I feel like there’s sufficient hardware and software redundancy in this arrangement to make me feel comfortable.
As far as reliability, so far so good. I had one autopilot servo brick during its first firmware update—but it’s been perfect in subsequent updates and in flight. Also, you don’t update them (or any of the other modules) in flight and it’s been my policy to avoid anything but database updates in the days before an important trip. In any case, the flying season has finally opened for me and I’ll find out for sure if my reasoning on redundancy proves correct in the months ahead.
Food for thought.
I built a RV-8 with dual busses that can be split. Each buss can be powered by its own ships battery (2 batteries on board – one forward and one aft) and each buss can power all critical items. (Note – the engine is not electrically dependent since I use P Mags) I installed two Advanced Flight Systems EFISs – one primary and the second is mainly used as an engine monitor, but it can also convert to the backup attitude/nav EFIS in case the primary fails. Additionally, each EFIS has its own backup battery. So, with multiple redundancies, I felt comfortable with using it in IFR. That is not to say that the RV is a stable platform in IMC, especially when hand flying – but that is another story for another time.
So, I am in VFR pattern, left base to final, in turbulent air, and I somehow bumped one of the multifunction buttons on the primary display. ( That is another subject worthy of discussion – that is, being able to make selections or changes on the EFIS during bumpy flight conditions) When I bumped the button, both EFISs went blank. Confusing, needless to say. Now I have no airspeed indications – in fact, I have no indications at all! So, I simply set a power setting that I knew would work (and my separate AOA was still functional), so landing was fairly straight forward. BUT, I thought – what if that had happened in IMC?!? Of course, in IMC one would simply engage the autopilot and command it to level flight, but there would still be that moment of confusion.
What happened was I had bumped a multifunction button that controlled the dimming function on the EFIS. I wired them such that dimming one EFIS simultaneously dimmed the other. I couldn’t think fast enough during a critical phase of flight to analyze what might have happened.
Lessons learned – 1. Know how to quickly readjust the dimming function. 2. While it is convenient, consider not wiring the dimming functions together – rather make each EFIS independently dimmable.
I certificated Tape Style displays,_indeed a fully electronic cockpit including EICAS on CRJ in early 1990s, and Boeing on 747 400 about 3 years prior.. Thats well over 30 years ago.
And nn De Havilland Q400, i certificated the first low speed cues based not just on AoA but also with a factor for ” blown lift” from the Dowty props and PW150s