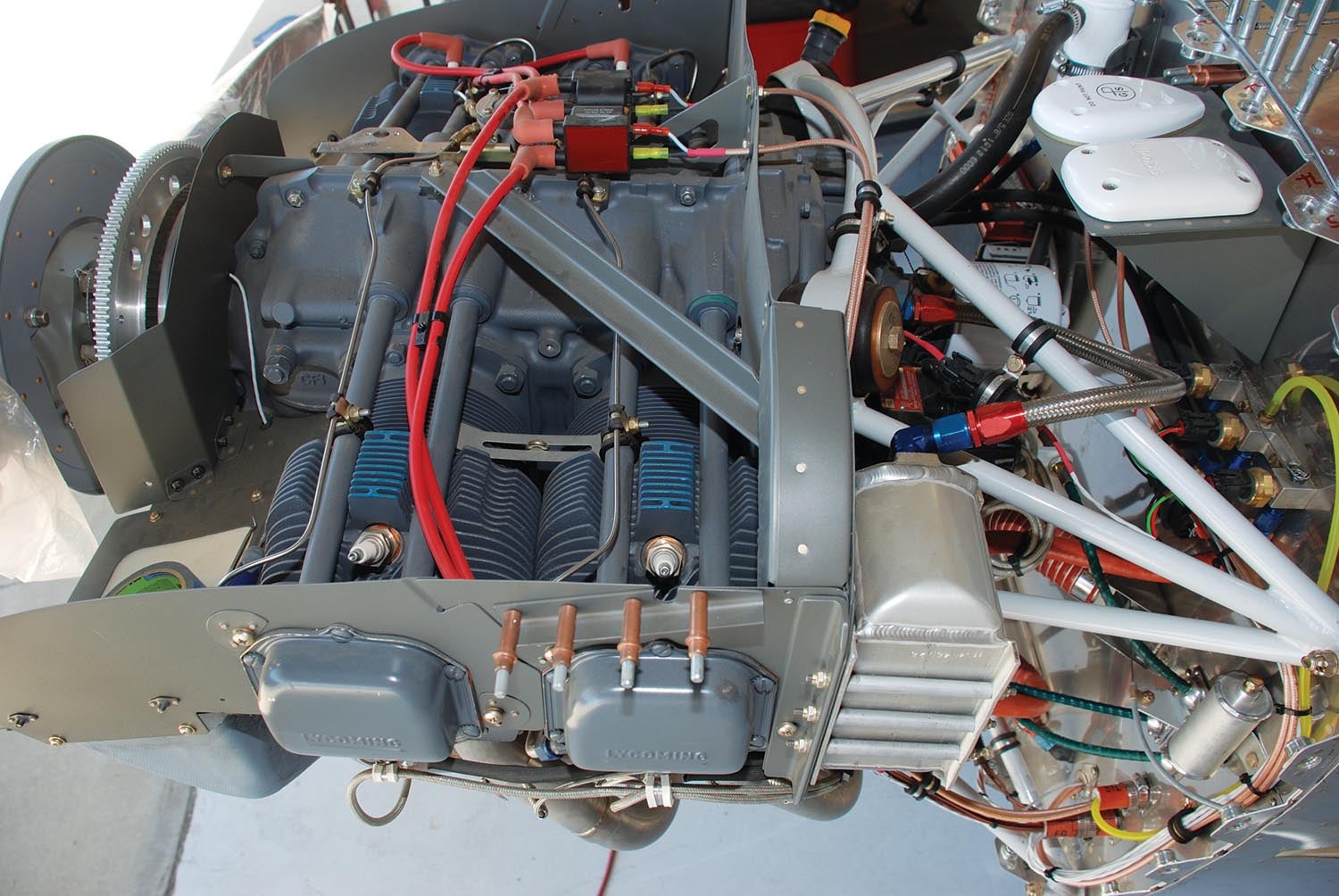
There are several things to consider when it is time to decide what hose material to use in your airplane project: compatibility with common aviation chemicals, pressure rating, temperature rating, service life, and cost. Not every hose offered by an aviation parts supplier will satisfy all of these criteria for any particular application. Also, your search for suitable hoses and fittings need not be restricted to aviation vendors. The automotive world has products that are perfectly well-suited for Experimental airplane use and may offer more options and lower prices than traditional aviation sources. However, the use of automotive products does require a higher level of diligence on the part of the buyer.
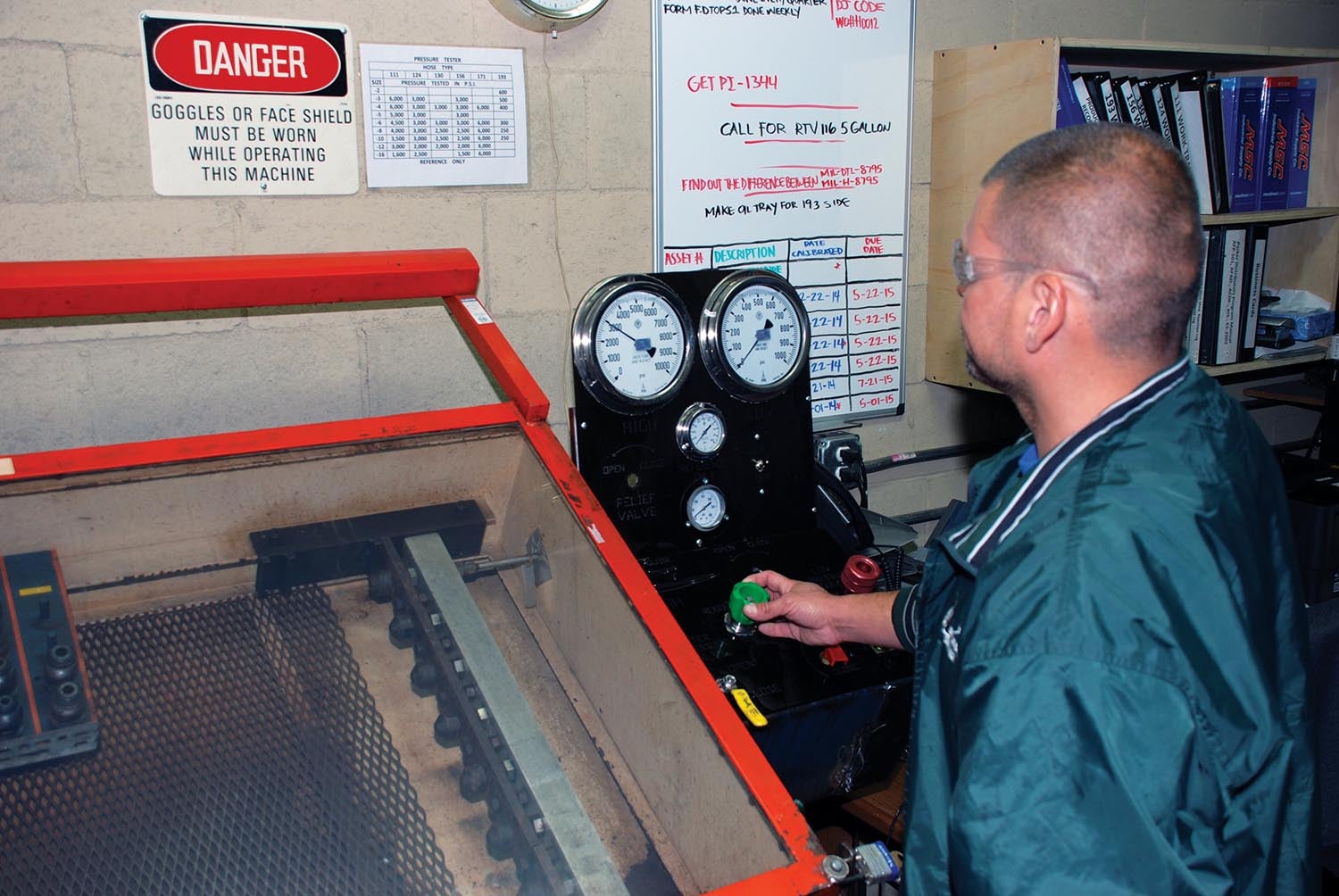
Chemical Compatibility
Aircraft hoses need to be compatible with avgas and engine oil to be sure, but in some cases compatibility with ethanol is also a concern. For example, Rotax engines prefer unleaded auto gas and allow for up to 10% ethanol. A fuel line that was not resistant to ethanol would be a poor choice. This becomes a greater risk when using hoses where the material used is not readily identifiable. Also, please note that the new unleaded aviation fuels on the horizon may present compatibility problems with rubber parts that are not known at this time. Chemical compatibility is something that is of special concern when using automotive store hoses. Not all of them are as chemical resistant as you might think. Be sure to read the manufacturer’s literature on any automotive product you plan to use to make sure it is suitable, and if you can’t clearly identify the product, don’t use it.
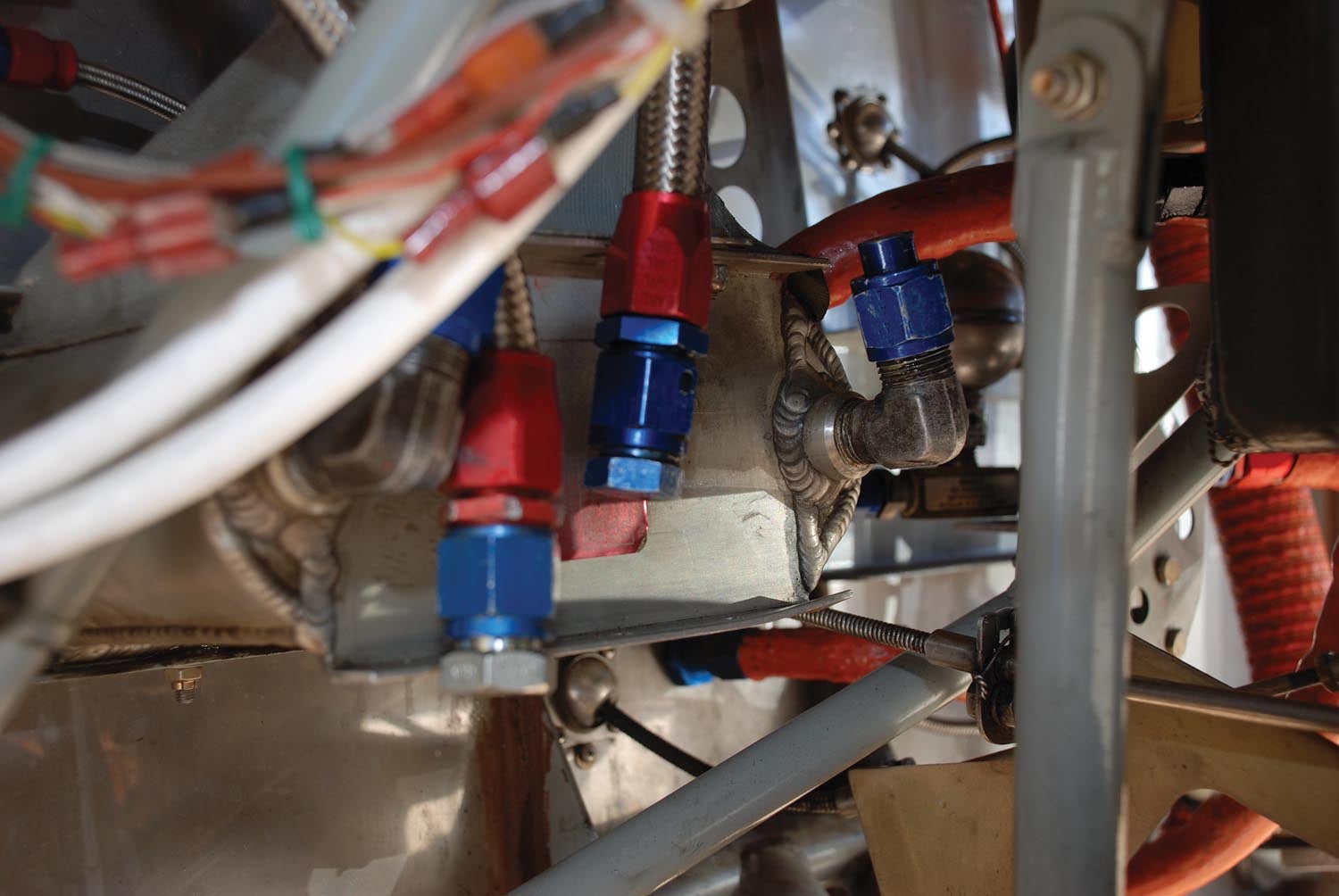
Pressure Ratings
Common Aeroquip and Stratoflex hoses used in aviation have pressure ratings that far exceed those required for fuel and oil lines where pressures rarely exceed 100 psi. However, brake systems will see much higher pressures. The best choices for flexible brake lines are the stainless steel covered Teflon hoses such as Aeroquip 666 or Stratoflex 124. In the small -3 size Aeroquip switches to a part number of 240-3, rather than 666. Aeroquip also makes a stainless/Teflon hose rated at 3000 psi designated as AE246. Hydraulic landing gear systems would be best served with the higher rated hose.
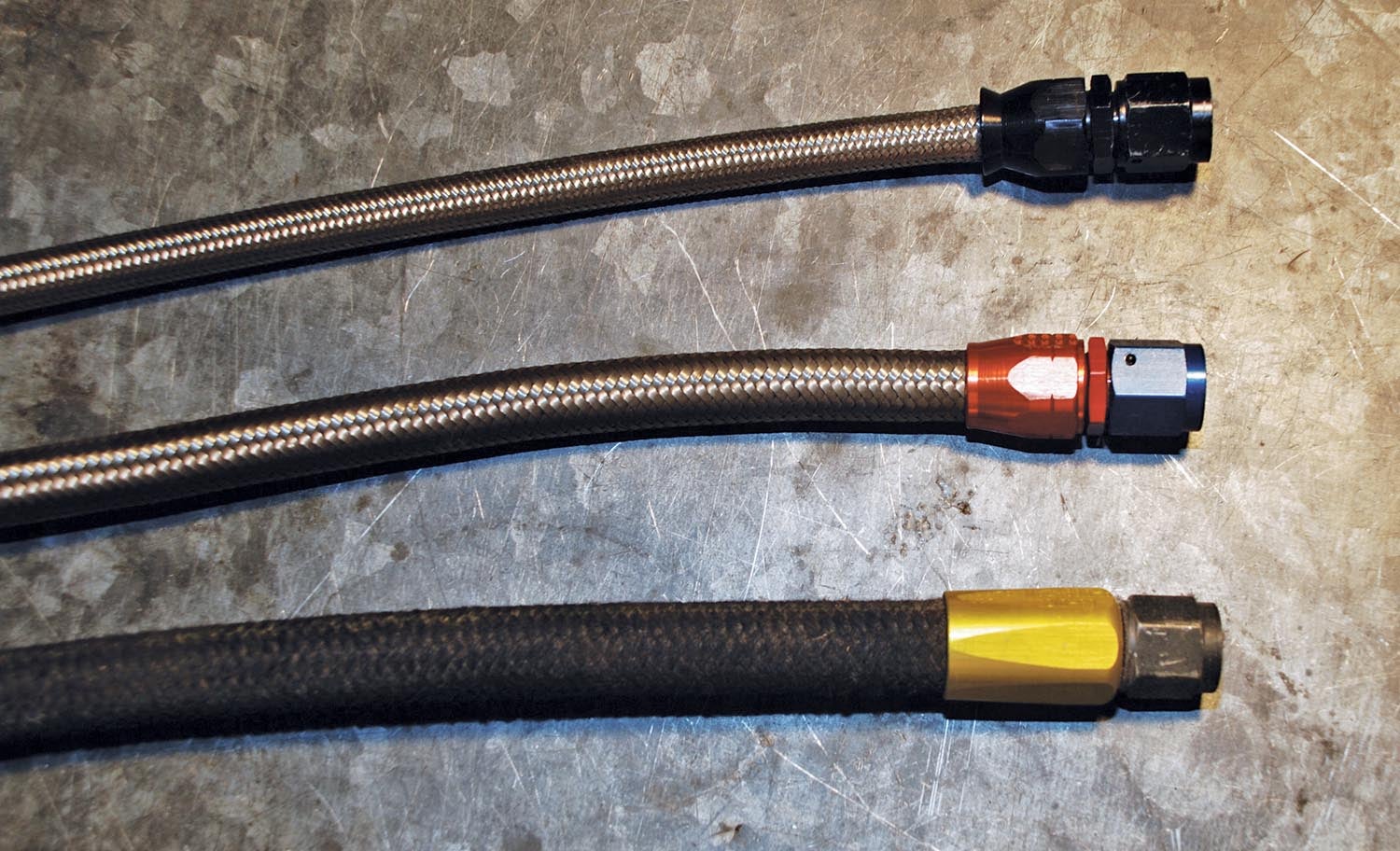
Temperature Ratings
Aeroquip 303 and Stratoflex 111, which are easily identifiable by their black rubber exteriors, have a temperature range of -65 to +250º F. This is adequate for most aviation applications with non-turbocharger engines. The upper limit of 250º F does not leave a very comfortable margin above a possible maximum oil temperature of 240º F, but that temperature should never be seen in normal operations. Oil lines near turbochargers could see higher temperatures than 250º F, so these hose materials are not recommended for such applications.
Aeroquip 601/701 and Stratoflex 156 hoses, the familiar stainless steel covered rubber hoses so many builders like to use, can handle higher temperatures up to 300º F. This extra 50º can provide some peace of mind in certain installations where heat is a concern, plus this hose looks so much better when you are showing off your engine installation.
If high temperatures are a major concern, you should look to Aeroquip 666 or Stratoflex 124 hose with an upper temperature limit of 450º F. This would be the best choice for an oil line to a turbocharger, for example, or one that must be run very close to an exhaust pipe.
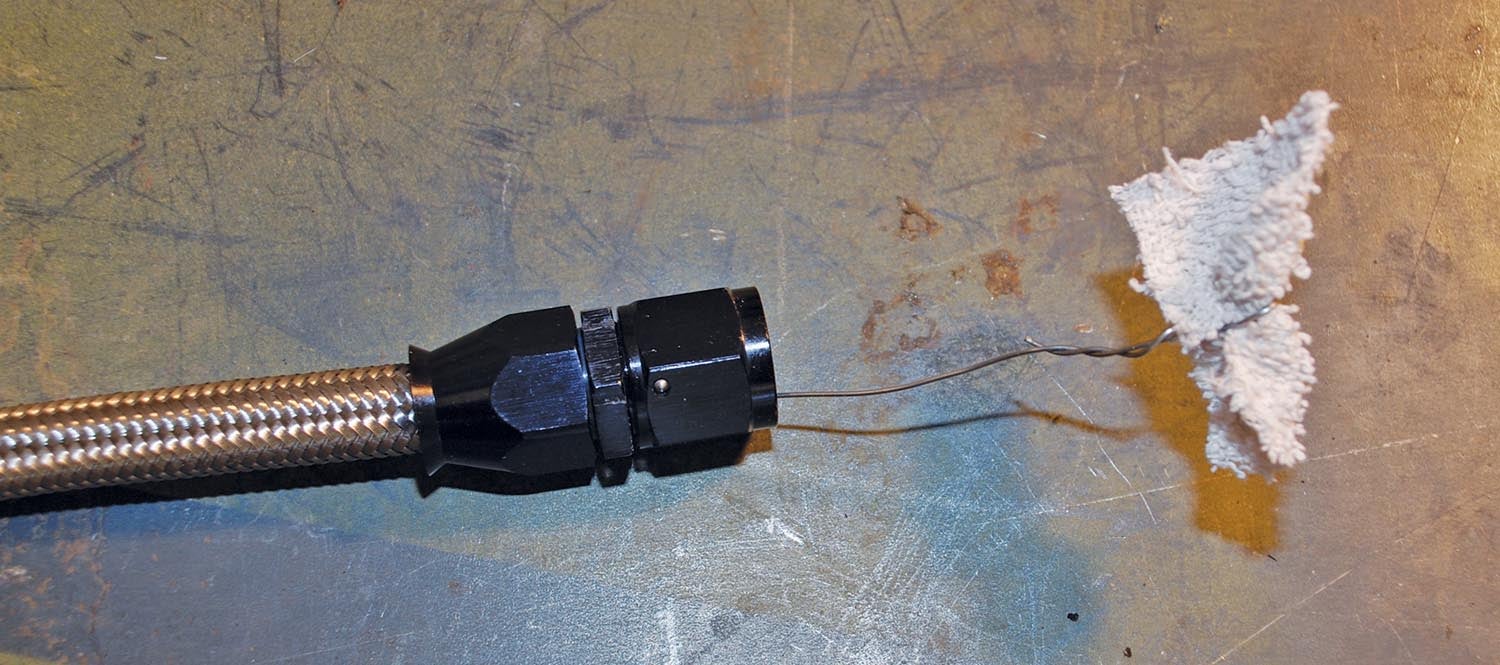
Service Life
When a hose has become damaged or brittle or when firesleeve gets soaked with oil or gasoline, it needs to be replaced. If a fitting shows any signs of leaking, it has to go. If there is abrasion on a stainless steel hose that breaks more than two strands of wire in one location, that is no longer acceptable. If the outer covering of a rubber hose (AE030) has been penetrated by chafing or there is a bubble, bulge, or crack in the hose anywhere, it should be replaced. Firesleeve that has been damaged or soaked needs to be replaced. The underlying hose may be savable if it isn’t the source of the soaking. Heat damage such as blistering or permanent discoloration of the outer hose material is also cause for replacement. These things seem fairly obvious. Fuel and oil lines must be in unquestionably sound condition since so much depends on them. If you are building a new project, you wouldn’t even consider using any hoses that were not in like-new condition, or at least you shouldn’t.
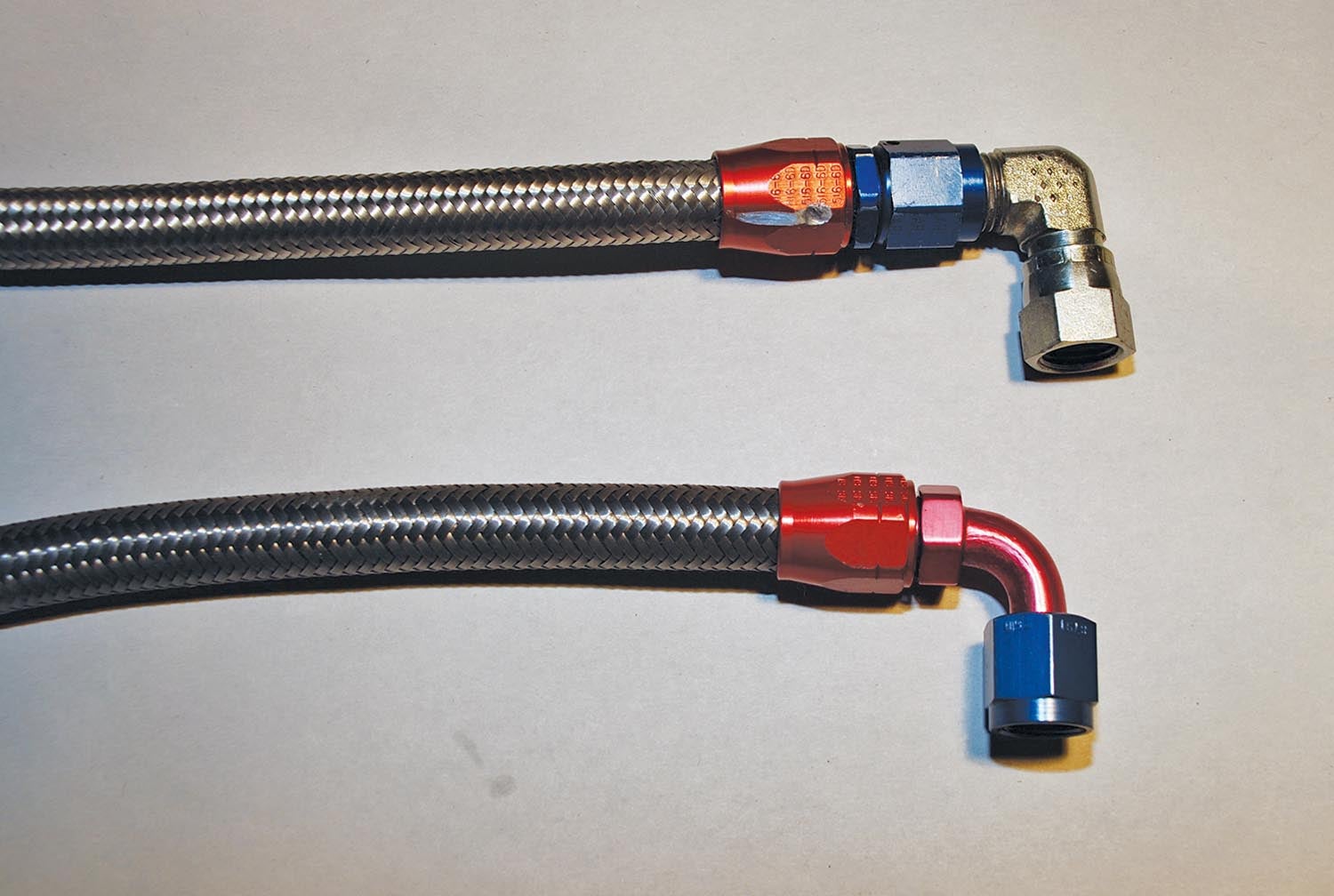
The tougher part of service life, and a strong argument against using like-new used hoses, is the factory recommended age limit on all rubber hoses, including stainless steel covered rubber hoses. These hoses have a shelf life, whether placed in service or not, of 10 years. Certainly, once in use a 10-year limit must be observed. However, in the engine compartment where there is a lot of heat and chemicals to stress hoses, a five-year limit is considered standard, at least for commercial operators.
Since it is a rare Experimental pilot who can log more than 100 hours in a year (usually it’s more like 30 or 40), it seems to make sense to be more generous when it comes to service life.
However, it is hard to get past 10 years no matter how generous you want to be. Technically, there is no legal limit to hose life in an Experimental/Amateur-Built airplane, but safety should be your first concern. It is tough to take a great looking hose and toss it out because of a date on the calendar, but that’s what prudence requires.
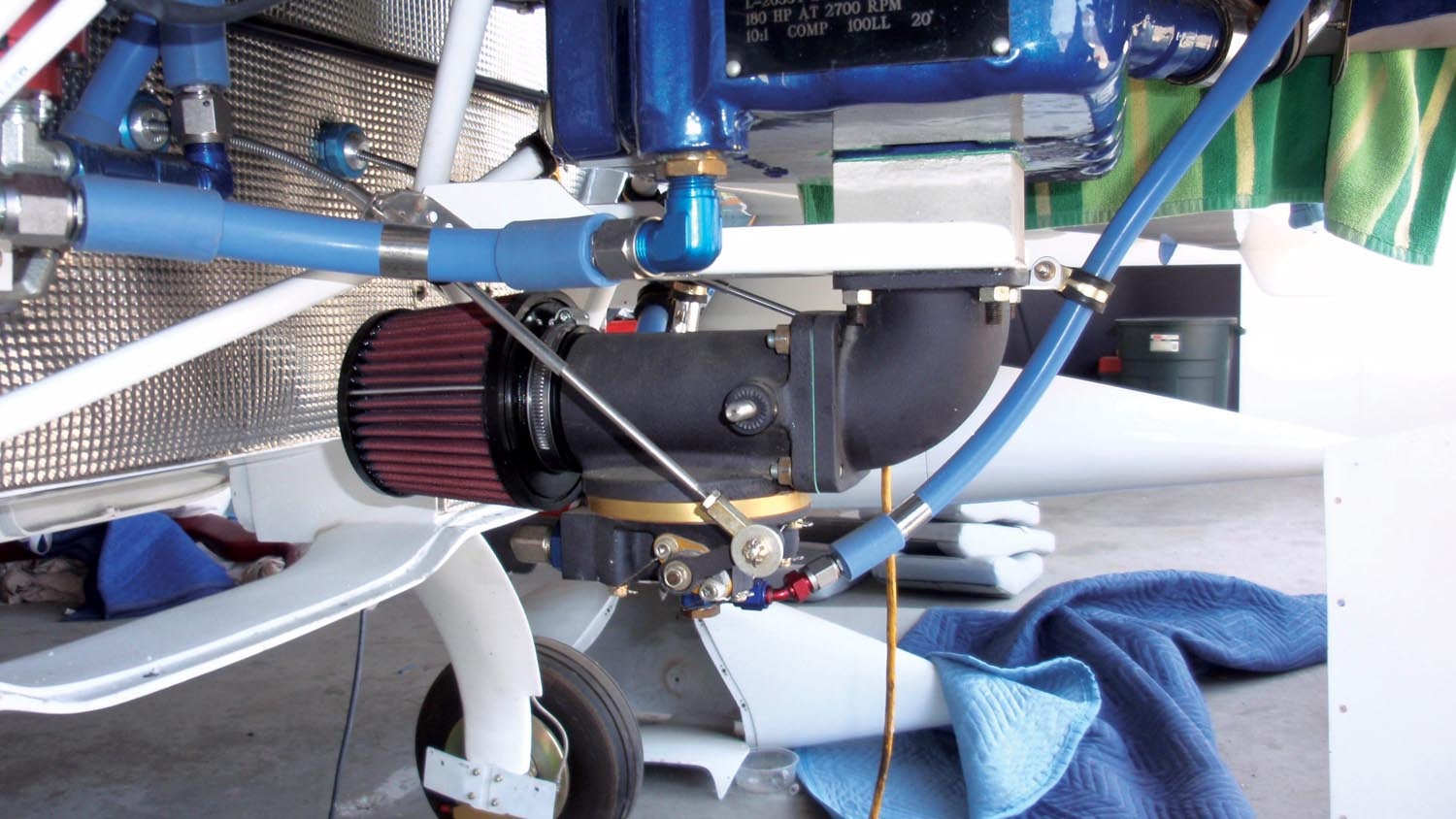
The alternative to junking your hoses every so many years is to use Teflon (PTFE) hoses with a stainless steel covering. These hoses are more expensive initially but have no calendar life limit. Aeroquip 666 and Stratoflex 124 hoses fill this bill. Of course, they cost more, but using a non-aviation vendor can help soften the blow.
I cannot find a recommended service life for firesleeve material. Certainly, it should be replaced when its condition has deteriorated. The most common problems are heat or abrasion damage and fuel or oil soaking. A calendar life limit of 10 years seems reasonable for installation where usage is low such as we typically see with E/A-B.
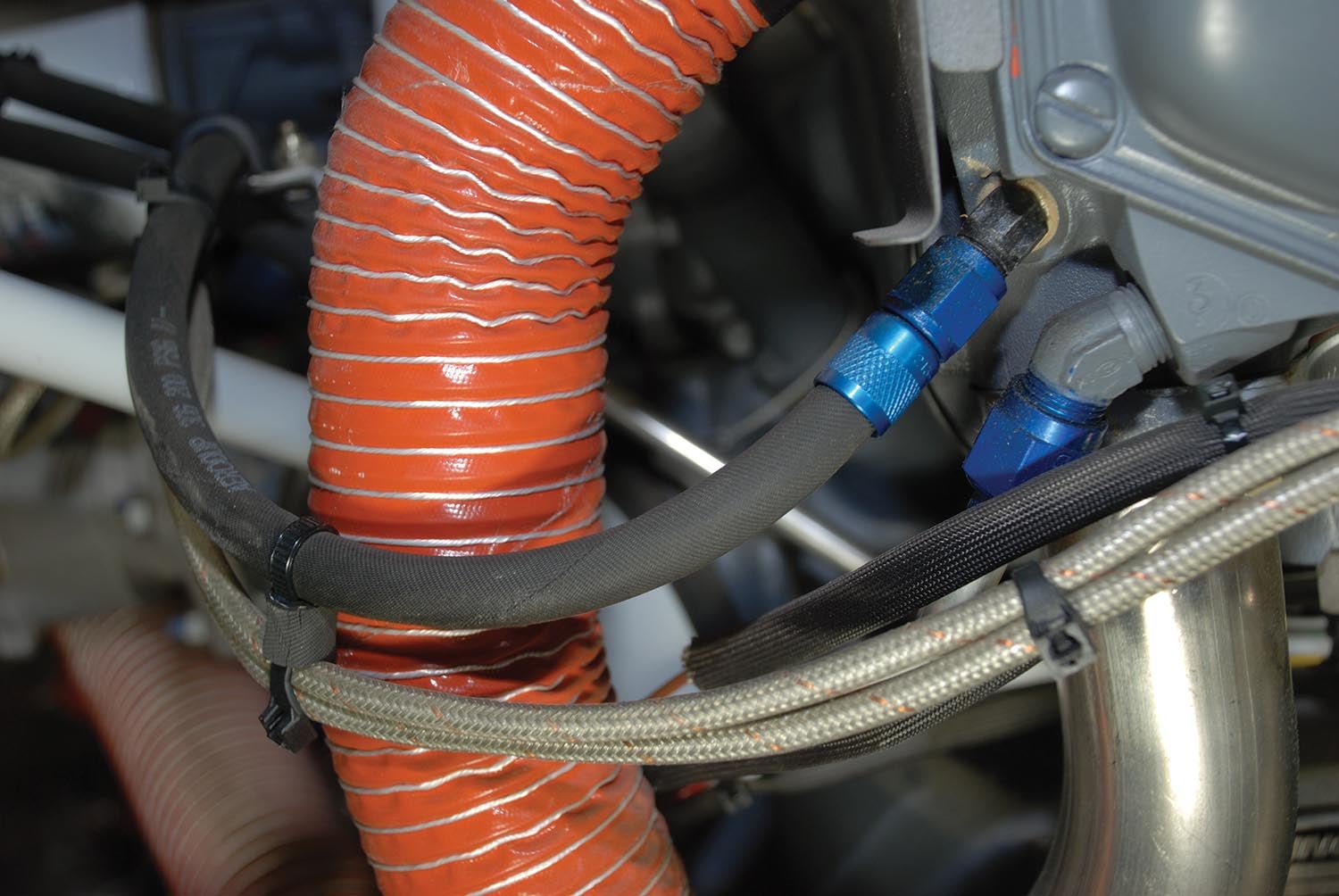
Firesleeve isn’t just for protecting hoses. It can be very useful to protect control cables or wires that are exposed to excessive heat. Especially with wires, the first choice should always be routing them in a way that avoids heat, but sometimes it is very difficult to do that. Control cables to forward-facing fuel injection servos always seem to be routed in such a way as to come between the engine and the exhaust system. Firesleeve over these cables can be very helpful to preserve the proper function and extend the life of these controls. Even though firesleeve is considered “fireproof,” what that actually means is that it is rated to handle up to 2200º F for five minutes and 500º F continuously.
Push-on Hoses
Some hoses are the push-on type with no pressure requirement, or a very low one in the case of vacuum hoses. The crankcase vent hose is a good example of this type of hose. Vacuum hoses have now become nearly obsolete, but older planes (like mine) do still have such hoses. Here the main concerns are heat and fuel/oil resistance. Rubber hoses with stainless steel covering can be use in these cases if aesthetics is a major concern, but most people are satisfied with rubber fuel line-type hoses. These hoses work best with what are called barbed fittings. These fittings allow the hose to slip on fairly easily but prevent it from coming off. In all cases, some type of barb or bead should be incorporated to help prevent the hose joint from coming apart. Of course, hose clamps in conjunction with barbed fittings give the most security.
Can these types of hoses be used for aircraft fuel and oil lines (pressure lines)? Yes, they can, but it is hard to consider that the best practice, unless you have an engine that does not allow for standard AN fittings. Many Rotax and Jabiru engines will only accept push-on fittings where the fuel line connects to the carburetor, so you really don’t have a choice. However, given the option, screw-on AN hose fittings are preferred.
Flexible Hose Chart
Designation | Description | Fittings | Sizes Available | Pressure-psi | Temperature |
---|---|---|---|---|---|
Aeroquip 303 | Reinforced rubber with cloth covering | 491 | -3 thru -32 | 3000/2000* | -65˚ to 250˚ F |
Aeroquip 401 | 601 hose with integral firesleeve | 816 | -3 thru -20 | 1000 | 500˚ F cont/ 2200˚ F for 5 min. |
Aeroquip 601/701 | Rubber with stainless steel covering | 816 | -4 thru -32 | 1000 | -65˚ to 300˚ F |
Aeroquip 666 | Teflon with stainless steel covering | F66000 | -4 thru -12 | 1500 | -65˚ to 450˚ F |
Aeroquip 240 | Teflon with stainless steel covering | F66000 | for -3 | 3000 | -65˚ to 450˚ F |
Stratoflex 111 | Reinforced rubber with cloth covering | 300 | -3 thru -48 | 3000/2000* | -65˚ to 250˚ F |
Stratoflex 124 | Teflon with stainless steel covering | 524 | -3 thru -24 | 1500 | -65˚ to 400˚ F |
Stratoflex H/J | 124 hose with integral firesleeve | 524 | -3 thru -24 | 1500 | 500˚ F cont/ 2200˚ F for 5 min. |
Stratoflex 156 | Rubber with stainless steel covering | 676 | -3 thru -32 | 1500 | -65˚ to 300˚ F |
*3000 psi rating in -3 and -4 sizes. 2000 psi in larger sizes
Roll Your Own vs. Factory Made
If we are talking about best practices, it is hard to avoid the question: Is it the best practice to make my own hoses from fittings and stock hose, or do I really need to have a professional shop make them for me? Shop-made hoses have two distinct advantages. One, they are tested to twice the rated pressure of the hose and fittings (test pressures of 3-6000 psi). And two, they are available with machine-swaged fittings that cannot be duplicated by most people working in their home shop or hangar. These are distinct advantages of professionally made hoses. The downsides are that they are pretty expensive and any discrepancy in communicating the desired length to the hose maker may result in an unusable hose.
Homemade hoses have the advantages of being less expensive and easier to get made to the correct length (more on this later). The downside is that an incorrectly installed fitting could fail at a very bad time. Many years ago, in my off-road racing days, I had a hose fail and pump all of the oil out of my engine in what seemed no time at all. Luckily, I simply pulled off the course and waited for the tow truck. Since then I am much more careful about how I assemble hoses, and I have never had another failure. The bottom line is that if you use new material and fittings and carefully follow the manufacturer’s instructions, there is no reason why you can’t put together a high-quality hose in your own shop, but if you are careless in your assembly process, you can get yourself into trouble.
Few people will be equipped to test their new hoses to twice the rated bursting pressure, although it is possible to get a pump that will achieve those pressures for around $150. If you decide to test your hoses, it is much safer to use a hydraulic pump than a high-pressure air pump. In any case use extreme caution and be sure to enclose the hose being tested in a sturdy container of some sort. If a hose fails at 3000 psi, flying debris can do some real damage. This is one place where factory-made hoses have a real advantage.
The final concern with hoses, factory made or otherwise, is making absolutely sure they are clean inside before installing them. At the very least blow them out with compressed air. Better yet, pull a cloth cleaning patch through each hose with a piece of safety wire.
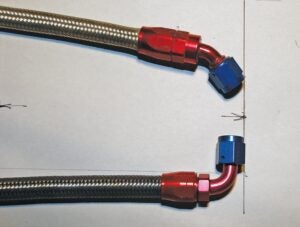
Ordering Hoses
If you decide to have a professional shop make your hoses, you will need to take accurate measurements to get the correct lengths. You would hate to pay $50 or more for a hose only to have it come up an inch short. The best approach is to first install the AN fittings at the points where the hose will attach, such as your fuel pump or oil cooler. An AN816 nipple or an AN822 elbow would be some of the more common fittings you might use. Then take a length of inexpensive rubber hose of about the same diameter as the hose you plan to use and run it from one connection point to the other. Be sure to use the exact same routing you will use for the final assembly. Hold the beginning end on the end of the far end of the threads of the flare fitting, and run the hose to the end of the threads of the other flare fitting. You can then easily measure the length from the end to the mark. Please verify with your hose maker that this is how they want you to determine your hose length before you submit your order.
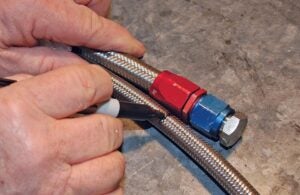
If you plan to install a 90º fitting on one end of the hose, you can get a very close approximation of the correct length by temporarily installing a 90º swivel female to male fitting. Then measure to the far end of that fitting. To be sure you should talk to the hose maker to verify your mutual understanding of the length measurement for any hose with an angle fitting on the end.
Another advantage of professionally made hoses is that you can get them coated with silicone rubber in lieu of installing separate firesleeve. This coating gives similar fire protection and is much less vulnerable to oil or fuel soaking. Be sure to specify this when you order your hoses.
To Firesleeve or Not
There is little argument about using firesleeve on fuel lines, but there is much debate about whether to use it on oil lines. Oil lines do carry a flammable liquid, even if it is less so than avgas. Most people do not protect oil lines, and that has been my personal practice. Is that the best practice? Arguably not, but that is your choice. I would not question anyone who chose to protect their oil lines just as they did their fuel lines. If you make your own hoses, it doesn’t cost very much more to protect your oil lines.
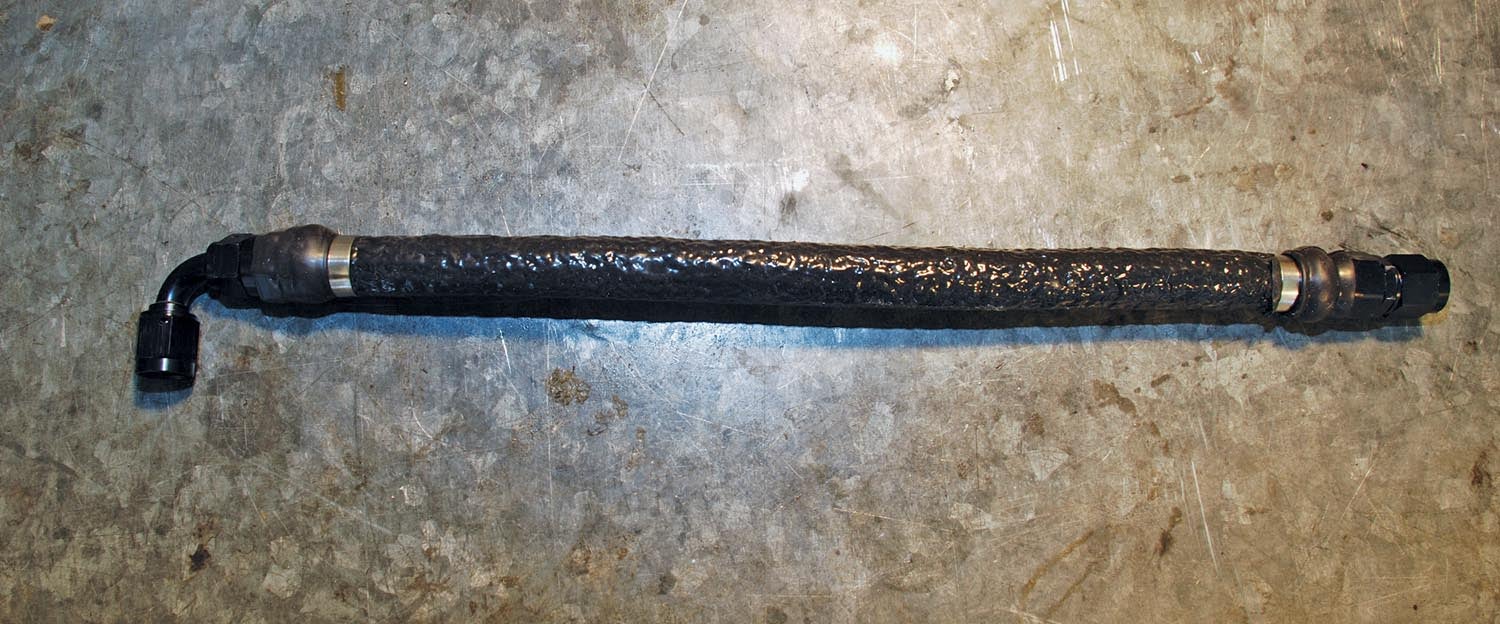
Installation Concerns
The best hoses can be rendered unsatisfactory by poor installation. Be sure hoses that run from the airframe to the engine have enough slack in them to allow for engine movement. Think about routing carefully and the excessive use of angle fittings. Fuel flow is reduced by tight bends and angle fittings. Be careful not to let hoses twist when you tighten them. You may need two wrenches for this. You never want to put unnecessary stress on a hose during installation or set up a potential chafing situation. Your trusty copy of AC 43.13-1B has more on this. And lastly, avoid heat as much as you can. Pick a route that keeps your hoses away from hot exhaust pipes as much as possible, and protect all hoses from heat if there is any doubt about proper clearance.
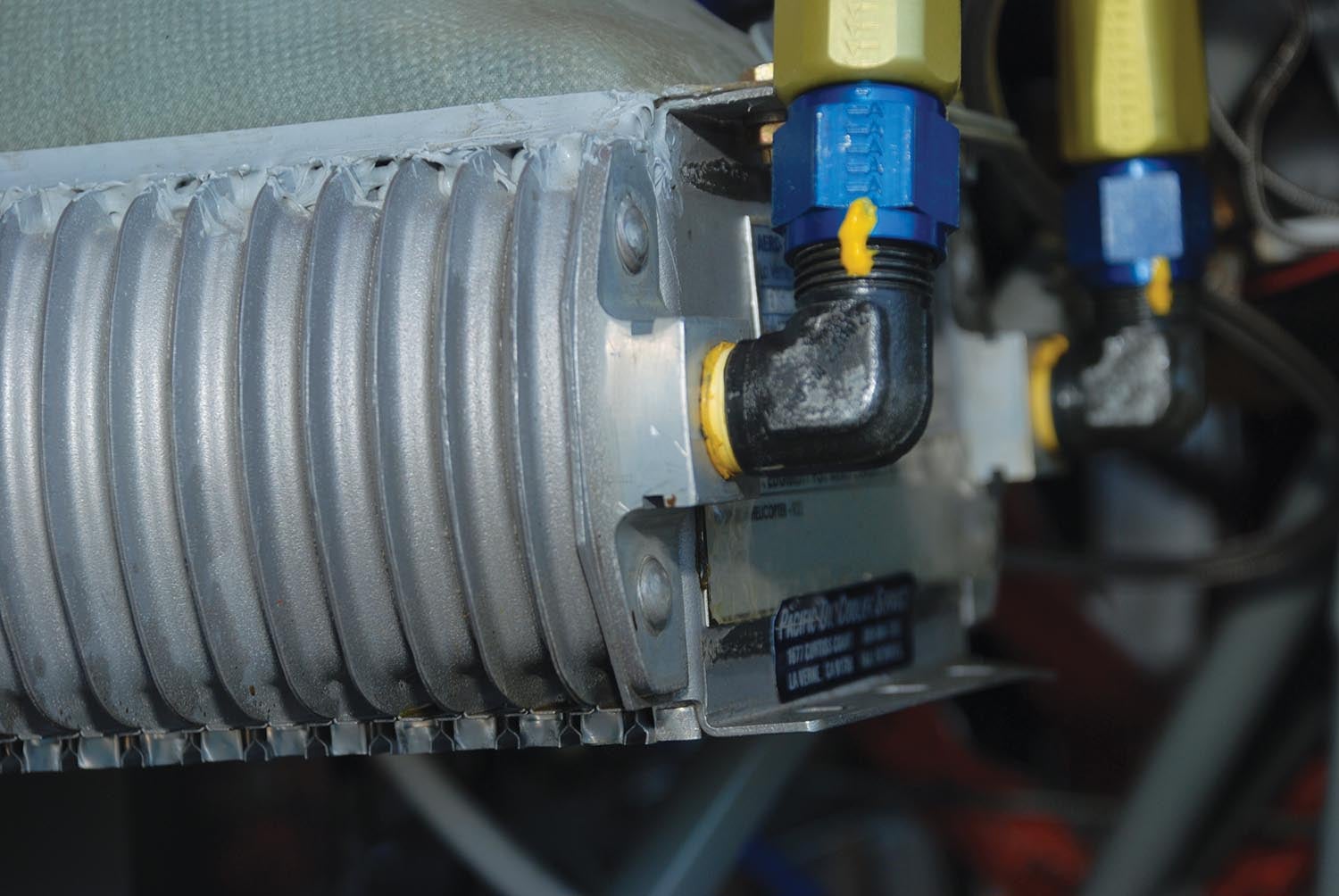
Conclusion
Professionally-made hoses are no doubt the best option for anyone who lacks confidence in their ability to fabricate their own. These hoses offer advantages that cannot be duplicated by most amateur builders—swaged fittings, integral fire protection, and high pressure testing. On the other hand, it is possible to make good quality hoses in your own shop with bulk hose and fittings that are readily available from many sources.
Whatever you decide to do remember these important points: Measure twice and cut once; these hoses don’t stretch. Be sure you communicate clearly how you made your measurements if you have someone else make your hoses. And be sure your hoses are absolutely clean before you install them.