“Homebuilt” aptly describes where most project aircraft are assembled. But as you approach the final stages, it’s common to move from the home to a hangar with the expectation that someday soon (hopefully sooner than later) the flying starts.
During 2021, three builders were in the final stages of their RV-8 projects at our local airport. I got to know two of them, Steve Cogswell and Mike Britcliffe, by stopping by their hangars every so often with the usual (and not helpful) “How’s it going? Are you done yet?” greeting.
In many ways Steve and Mike represent typical builders. They love flying, are good with their hands and both are really, really smart (Mike retired after 30 years at Jet Propulsion Laboratory and Steve is an engineering consultant). But in one key area, they were miles apart.

One day I asked Mike, quite casually, how he enjoyed the experience of building his RV-8. His answer surprised me: “I didn’t.”
His response was in direct contrast to my conversations with Steve Cogswell, whose overall build experience was a positive one. Steve was first introduced to KITPLANES® readers in the July 2019 issue when I showed how to make a shop-built preservative fogger he invented. At that time, his RV-8 was about 50% done. I remember him being endlessly enthusiastic about showing me all the special details on his project. Although a man of few words, Steve is justifiably proud of his handiwork. Whether it’s under the cowl, inside the cockpit or out, Steve’s expertise as a master craftsman is clearly evident.
As for Steve’s building experience: “I really enjoyed the first two years.” (He purchased his RV-8 kit in 2017.) He didn’t say it in so many words, but my impression was tasks like bucking rivets and sorting out the miles of wiring for the electronics were less fun than other tasks, especially making, or remaking as the case may be, different parts in his home shop. It’s worth adding that Steve had built a KR-2 several years earlier. So in that respect, he had some idea of what to expect when building a homebuilt.
The first time I met Mike, he was surveying a batch of freshly painted RV-8 parts (wings, flaps, elevator, etc.) that had been carefully inventoried and sorted out for reassembly. The red gloss paint was stunning and very “Ferrari-esque.” The only thing missing was the fuselage, which was still at home in the garage.
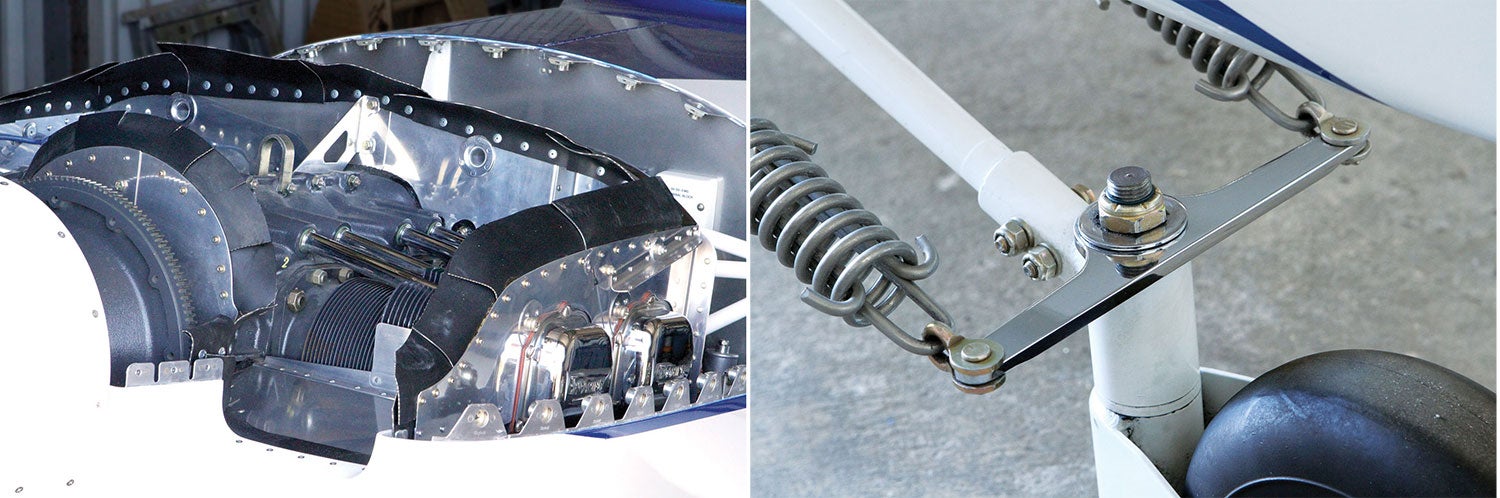
Backing up, Mike took delivery of his kit in stages, the first of which arrived in the spring of 2019. According to Mike, “I tried to stage the deliveries to keep the garage from getting too crowded. I completed the empennage in one month. The fuselage kit arrive in June, and the quickbuild wing kit in December 2019.”
“The engine arrived in April 2020, and by July I took everything except the fuselage to the airport for paint. It took several months to get the baffle kit, which was holding up the completion of firewall forward. I finally took the fuselage to the airport to paint around August.”
This was around the same time Steve moved his airplane to the airport. So it became routine for me to check in with each project. I’d drive by Steve’s hangar on the way to mine and, if it was open, I’d stop in. I’d do the same with Mike, except it was on my way home.
Mike and Steve both became involved in the local EAA chapter. Every so often, after a meeting, the group would visit one of their hangars to look at their RVs. The level of workmanship that both builders put into their projects was absolutely appreciated. Mike earned bonus points from everyone for how quickly his project came together.
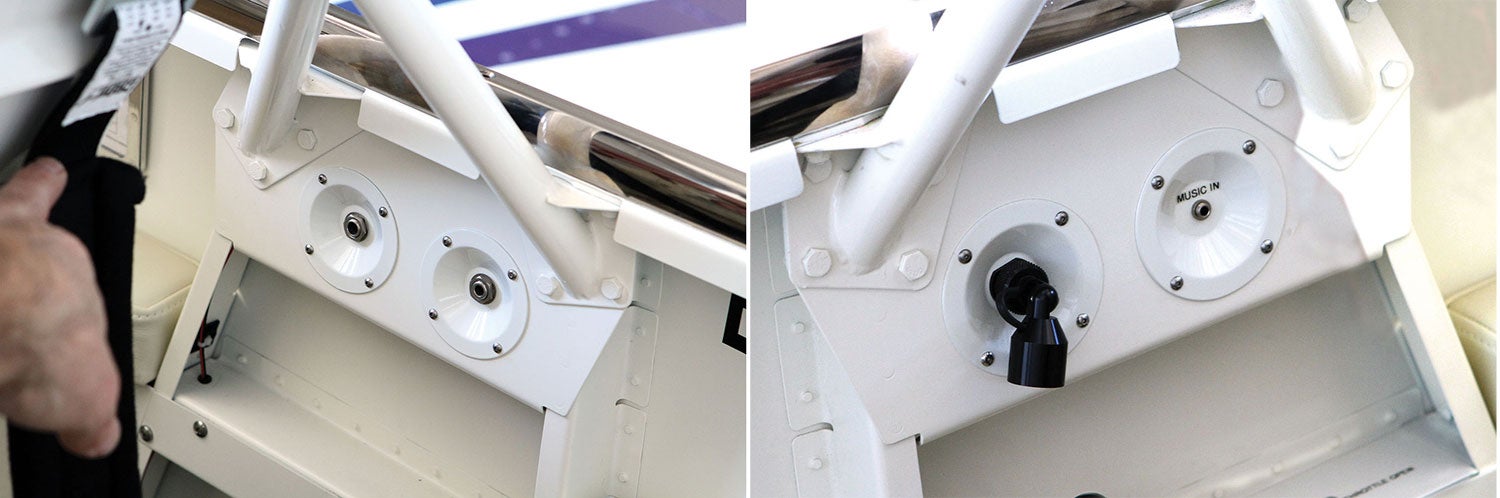
What we didn’t know or detect, at least until I asked, was Mike’s particular take on his build experience! According to Mike, the root of his frustration was his expectation that the Van’s kit would be perfect, or at least more thoroughly documented: “At JPL, every detail is defined to the letter. Building an RV-8, you get all these parts, drawings and basically a checklist of tasks. The further you get into it, the more you realize there’s a lot you have to ad-lib. You’d think the internet would help. But instead of answers, more often there were endless, and sometimes pointless, debates about how to do something.”
Mike went on to add: “Steve and I both wondered how interesting it would be to try to build one on your own without the internet. I probably would’ve saved six months.”
One hiccup in particular that got under Mike’s skin was deep into the build, right at the point where it was actually starting to look like an airplane. Key components of the landing gear didn’t line up right. By the time he got it resolved (with new parts from Van’s), it was another month added to the build.
There were payoff moments too: “It’s most satisfying when you get the fuselage done with the gear and empennage on. It finally looks like an airplane, and you step back and see the simple elegance of the design and the brilliance of what this guy [Van] has done.”
So, after all that, I asked Mike, “Would you do it again?”
“Knowing what I know now, probably yes. But I’m not planning on it. In two years? Maybe if a partially finished kit came up at the right price…”
That’s it for now. Time to get back in the shop and make some chips!
The -8 is an amazing to fly aircraft. However Mike’s experience is shared by more than a few. It is an old kit by todays standards. The kit and especially its documentation is nowhere near the quality level exhibited in the -12 and -14 kits. After much research and honest introspection I realized building one would definitely exceed MY frustration tolerance levels. Others do just fine as you noted.
I agree that the 14 documentation is professional and written by tech writers but I do feel the RV8 is much sexier than the RV14 which I plan to be flying my RV8 in the fall.
Kit planes are becoming to be expensive. And what most people could afford 25 plus years ago is now way over what people can purchase today. This is just what going on in the industry. What people looking for is low cost on build and tbo’s. There are some planes i have seen that can easy classified as ulterior lights vfr with a few redesigning on the engines compartments. Example: you take the midget mustang. Remove the flat 4 motor and replace it with a rotax 582/65hp with e=drive electric start. By doing this you remove over 200lbs off the air craft. The plane with flat 4 weights 525lbs. With the rotax 582 with a turbo/ 90 to 110hp. Weights 350lbs or less. The cost for midget mustang w/ flat four is around 65 to 75 thousand dollars, while with rotax 582/turbo cost under 40 thousand dollars. Thats a saving of 25 to 35 thousand dollars. And i can see that a lot of small planes in this class can easily turn into ultralights.