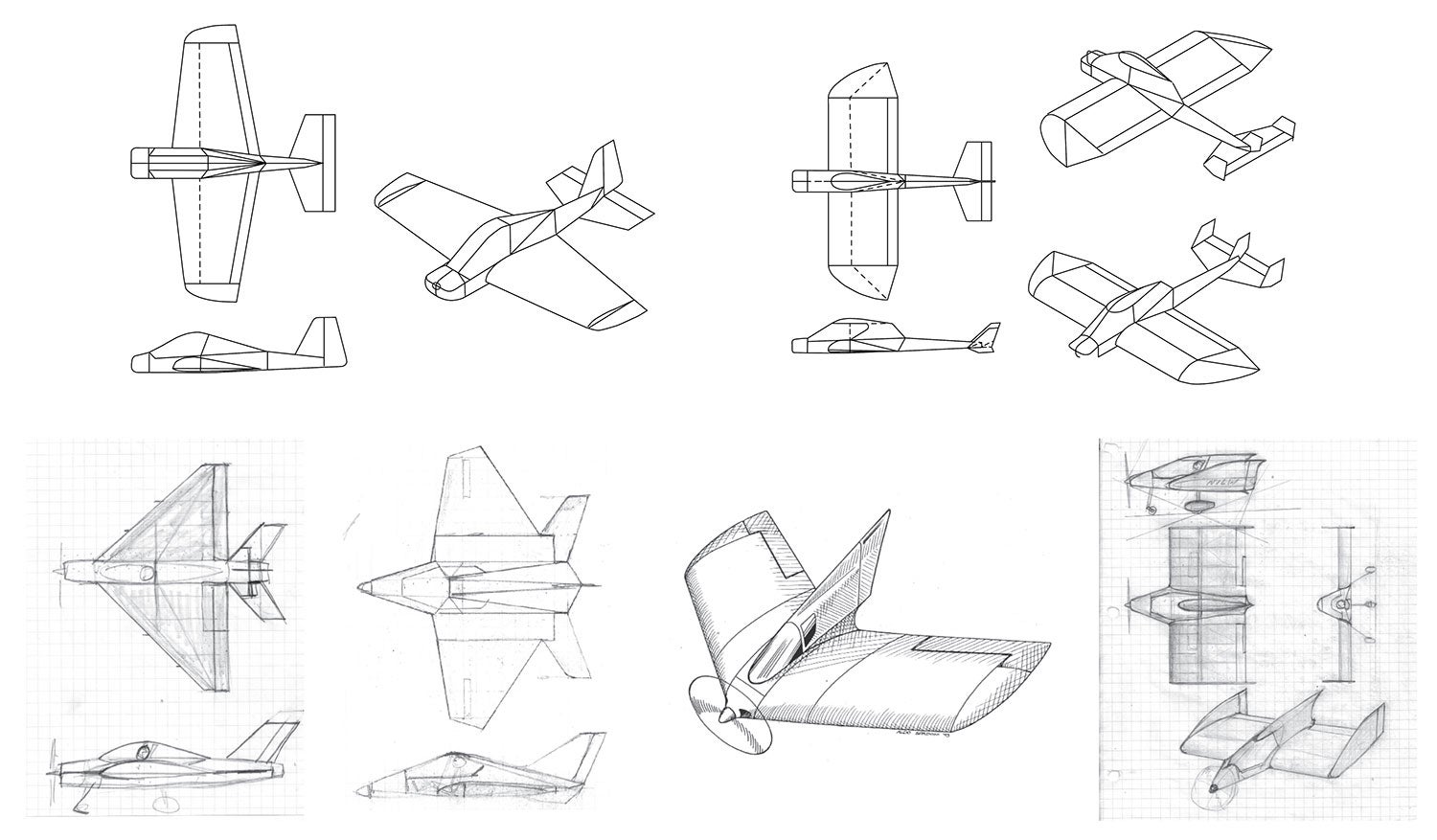
Most of our recent discussions on the process of designing an airplane were based on the assumption that the airplane has a generally conventional configuration. This certainly covers the vast majority of airplanes, which are monoplanes with aft-mounted tails.
Last month we took a look at how to approach innovation in a general sense and also touched on some unconventional configurations. Now let’s circle back to the very beginning of the design process and turn our attention to configuring the airplane.
Every airplane is designed to perform a specific mission. The design process starts with the needs of the operator of the airplane. The designer’s goal is to lay out an airplane that meets those needs.
The first task is to choose the overall configuration of the airplane. The configuration must fit the mission. A configuration that is appropriate for one mission might be a poor choice for another.
Designers will sometimes choose the basic configuration at the beginning of the process and not deviate from that initial choice. If the configuration they choose is relatively conventional and conservative, and the airplane is being designed around a well-understood mission, this can be the quickest and lowest-cost way to go—and it often works fine. With good detail design, this approach will usually lead to a successful airplane. It is unlikely to produce an airplane that is dramatically superior to other airplanes designed to perform the same mission, although it might be enough of an improvement to be a commercially successful product.
The risk in choosing only one configuration at the beginning is getting it wrong and pushing ahead by trying to make an unsuitable configuration perform the mission. It’s particularly risky to start with a single unconventional approach without considering alternatives.
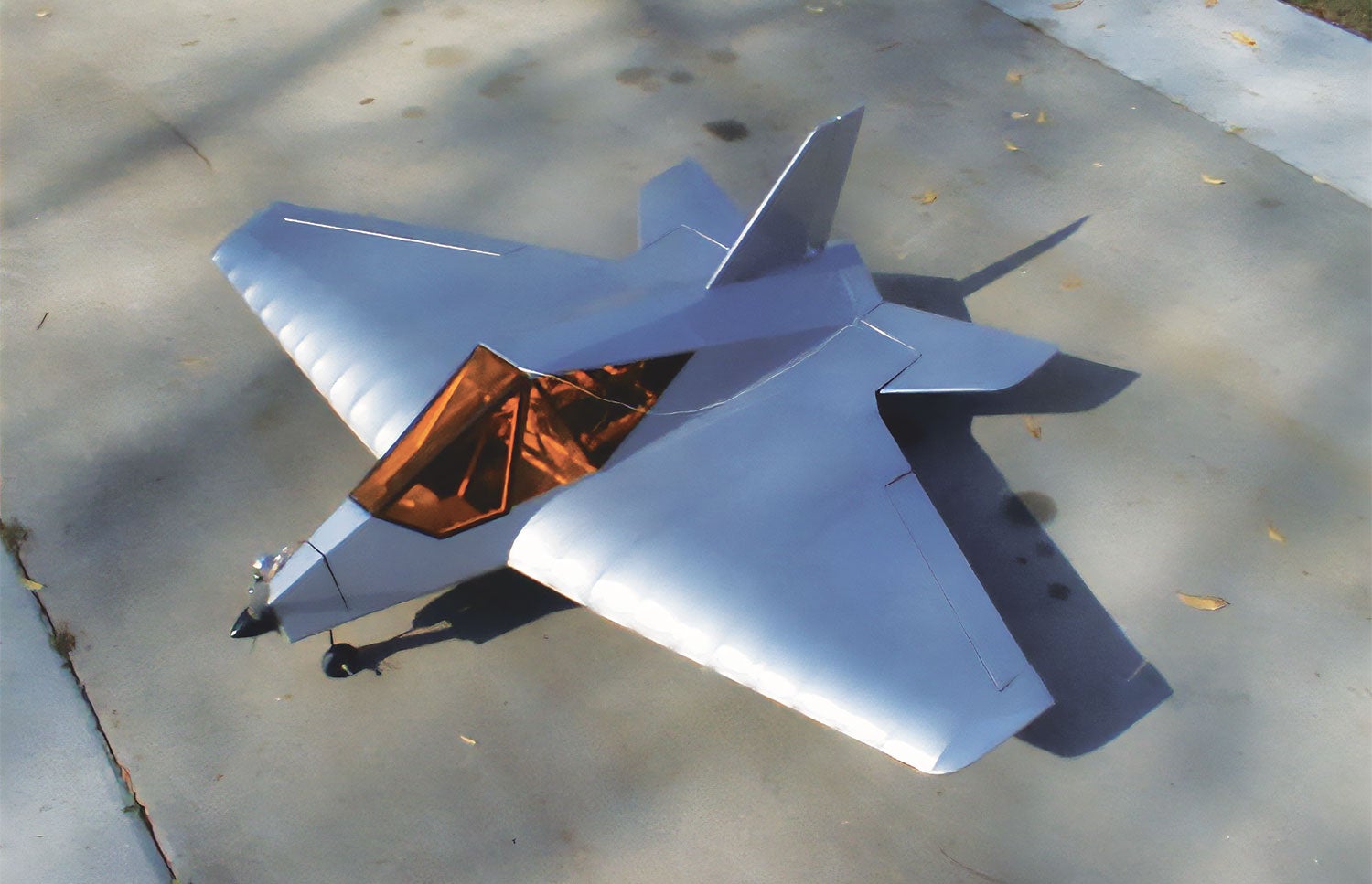
Analyzing Different Configuration Concepts
Many design efforts start by considering more than one configuration. At the outset of the program it may not be obvious which configuration is the best choice. There are several configurations that can produce airplanes that can perform the mission, but each one offers some potential advantage. It’s not initially clear which one would lead to the best airplane.
This is common on larger programs, although it’s not limited to those. The design team will start by laying out two or more configurations at the beginning of the program. These candidate concepts are then refined and analyzed in parallel until the relative suitability or virtue for the mission of the several options becomes evident. At this point in the process, the preferred configuration will be selected and no further work will be done on the competing concepts. This is referred to as the “down-select.” After the down-select, the design team moves on to refining the chosen concept.
The criteria used for the down-select can vary. It’s rare that the discriminator between concepts is absolute kinetic performance. Most of the time, the goal of the project is not to produce the fastest airplane or the one that carries the most load or that flies the highest.
It’s important to remember that a design that seeks to provide more absolute performance than the customer asks for, or maximizes performance in an area the customer does not consider important, is not likely to be a winner. Extra performance is likely to increase cost, and doing better at something the customer does not care about gains nothing.
The required performance is defined in the mission specification, and all of the candidate designs should meet that specification. Sometimes, only one of the candidate configurations leads to an airplane that can perform the required mission. In such a case, the down-select is obvious: We choose the only concept that can meet the requirements.
This is relatively rare, however.
Most of the time we can generate multiple candidate designs that meet requirements. Once we have several different designs that are properly sized and will perform the mission, we can down-select based on other considerations and choose the best for our customer. Several common discriminators are acquisition cost, fuel consumption, gross weight, manufacturability and operational considerations.
It’s likely that each of the candidate designs will be better in some areas and worse in others. It’s rare that one is overwhelmingly superior or inferior in all areas of concern. Which concept to proceed with depends on the relative importance of the discriminators to the end user or buyer of the airplane.
For example, cost is often a big driver. Which design is the better concept may depend on whether the buyers of the airplane are more concerned with initial price or operating cost. An airplane optimized for minimum selling price will probably lack some of the aerodynamic refinement needed to minimize drag and will have other compromises aimed at making it cheaper to manufacture. Accordingly, it will likely burn more fuel to fly the mission than an airplane optimized for maximum fuel efficiency.
A customer who is primarily concerned about financing the initial purchase of the airplane will prefer the lowest-price airplane, while a customer who is concerned about the long-term cost of operating the airplane will opt for the more fuel-efficient design and accept the higher purchase price in return for the long-term savings in direct operating costs.
This is one of the reasons there is a market for speed and performance mods for certified airplanes. The initial manufacturer made a cost-based decision that some amount of extra performance was not worth the extra selling price to the initial buyers of their airplane. They decided that they would sell more airplanes at a lower selling price, even with the slightly lower performance.
Once the airplanes are in service, some owners are willing to spend the extra money to get the performance increase and buy STC’d performance modifications from aftermarket vendors.
Principles of Down-Selecting
As we go through the process of defining options and down-selecting to a preferred configuration, it’s important to remember fundamental principles.
First: All airplanes, regardless of their configuration, operate under the same laws of physics. We can determine the performance of each design using the same type of analysis. There are some relatively simple first-principle parameters that can be used to compare physically dissimilar airplane configurations early in the design process and can help guide design decisions. As the designs mature, more detailed analysis will give a more accurate evaluation of each candidate, but the analyses themselves will be the same for all.
It’s important to do a full, independent analysis of each candidate concept. A common mistake is to directly apply a performance increment that is claimed for a new concept instead of determining its performance directly by analysis or experiment.
This often happens when an “advanced” research project reports a positive result. We might read, for example, that a new advanced airfoil showed a 15% drag reduction. It’s tempting to assume that if we simply use this airfoil on an otherwise conventional airplane it will reduce drag by the reported 15%. This may or may not be true, since the effect of the airfoil on the drag of the airplane is a function of multiple parameters that determine the flight condition at which the airplane operates. If the flight condition of the airplane does not match the flight condition the airfoil was designed to operate at, its aerodynamic performance will be different, and the reported drag reduction will probably not appear.
Analyzing each candidate configuration independently is the proper way to get to a meaningful comparison between them.
Second: The suitability of a configuration relates directly to how well it performs the mission. What may be a great configuration for one mission may perform poorly for another. Once we have a sufficiently complete analysis of each candidate configuration designed for the specific mission at hand, we have the information we need to select the one that will best meet the needs of the customer who will buy and operate the airplane.
Congratulations on 200 posts on Kitplanes Barnaby! You are my favorite author in the aviation world, I really enjoy your work.