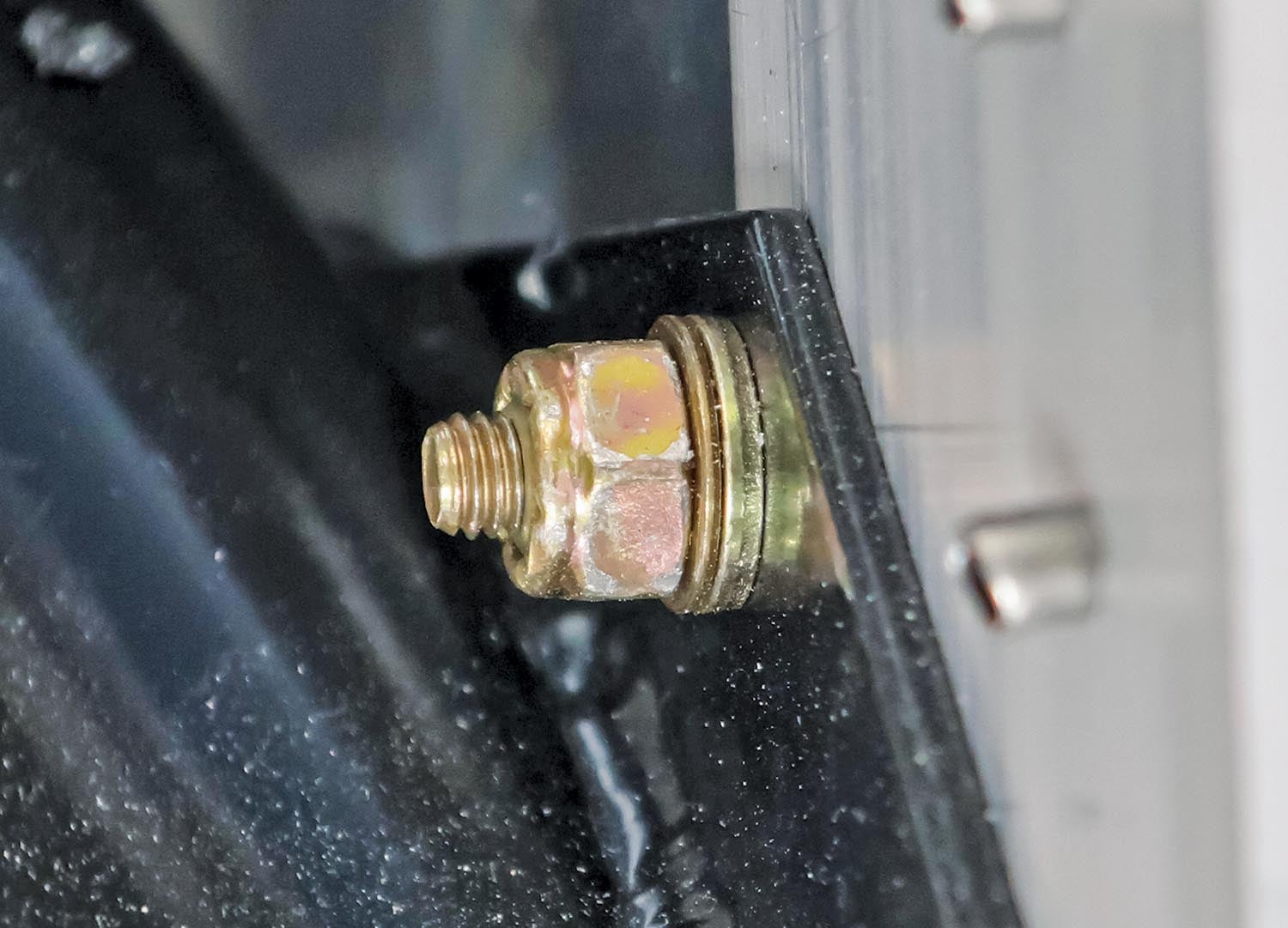
Not a week (sometimes a day) went by during my Sonex career that I wasn’t asked about washer usage on threaded fasteners. Often, a debate (sometimes an argument) ensued. Who would think the diminutive AN960 washer (and its sickly sibling, the AN960L washer, which is half the thickness) could be contentious? They are the hardware equivalent of the penny. We drop one and reach for another, the runaway already dead to us.
But washers, like pennies, wield considerable power for their size. A penny is the difference between being a millionaire and having $999,999.99. A washer can be the difference between a proper bolt installation and an unairworthy one. Unlike pennies, however, extra washers don’t add value. They add weight. And cost. Here, I take you on a guided journey through washer best practices, focusing on why washers are used on threaded fasteners. As someone once said, “If you know the why, you know the how.”
An Audit of Standards
Best practices, a fancy term for common sense, means something should be done “in the best way.” The homebuilder’s bible for best practices is Advisory Circular 43.13-1B, Acceptable Methods, Techniques, and Practices—Aircraft Inspection and Repair. It’s a mouthful, it’s online, it’s free and every homebuilder should have it. AC 43.13-1B, Section 5, Washers states: “Plain washers are widely used with hex nuts to provide a smooth bearing surface, act as a shim to obtain the proper grip length*, and to position castellated nuts in relation to drilled cotter pin holes in bolts.” There’s no mention of placing a washer under the head of a bolt. My 1991 edition of the venerable Standard Aircraft Handbook states, “The plain washer, AN960, is used under hex nuts,” and goes on to repeat, almost verbatim, the text from AC 43.13-1B. But two pages later it contradicts itself with the statement: “Be sure that washers are used under heads of bolts and nuts unless their omission is specified.” It doesn’t say why a washer should be placed under the bolt head, leaving us to argue amongst ourselves.
Washer usage disagreements spring from conflicting guidance, as outlined above, from personal experience (maybe a company where you worked had a washer usage standard—one under the nut, one under the bolt, no exceptions), the online advice of user I_Know_Everything or because construction documentation is inaccurate for your particular assembly. There are places in Sonex plans where tolerance stacking (the net impact of the acceptable variations in the thickness of parts and the grip length of fasteners) renders the plans-specified washer installation a crapshoot. What’s a builder to do? Ask what the washer does, that’s what.
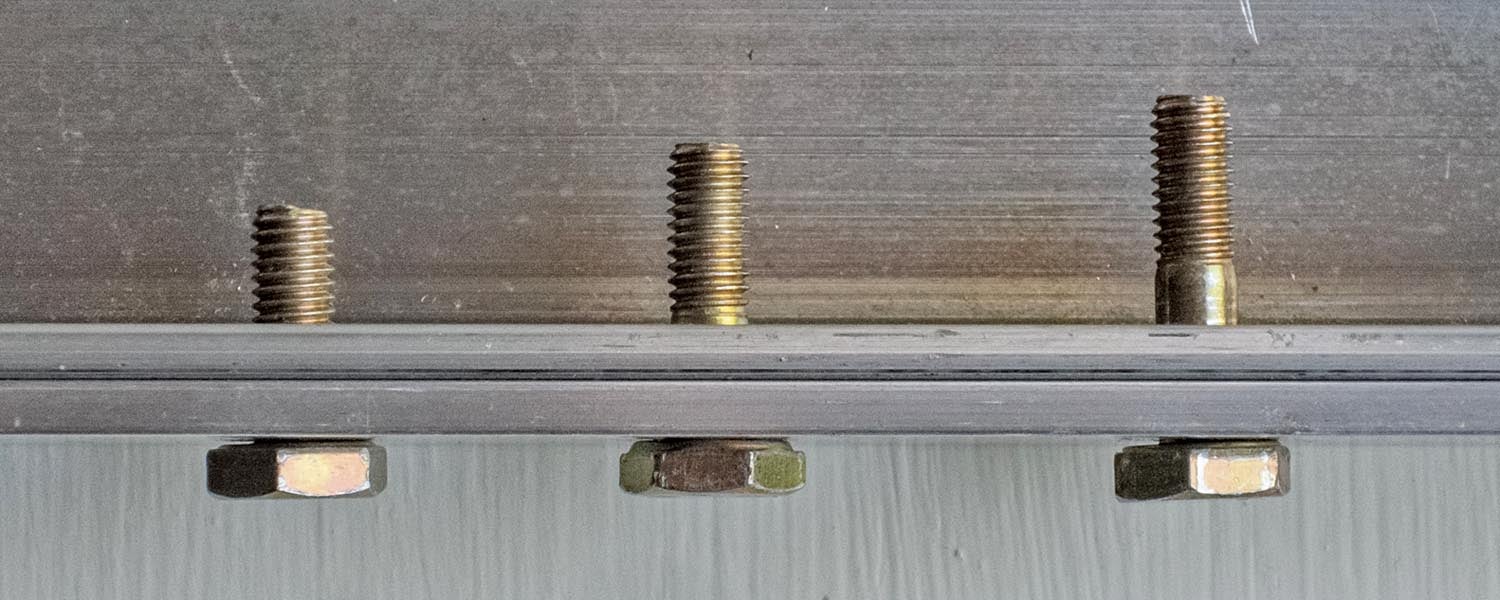
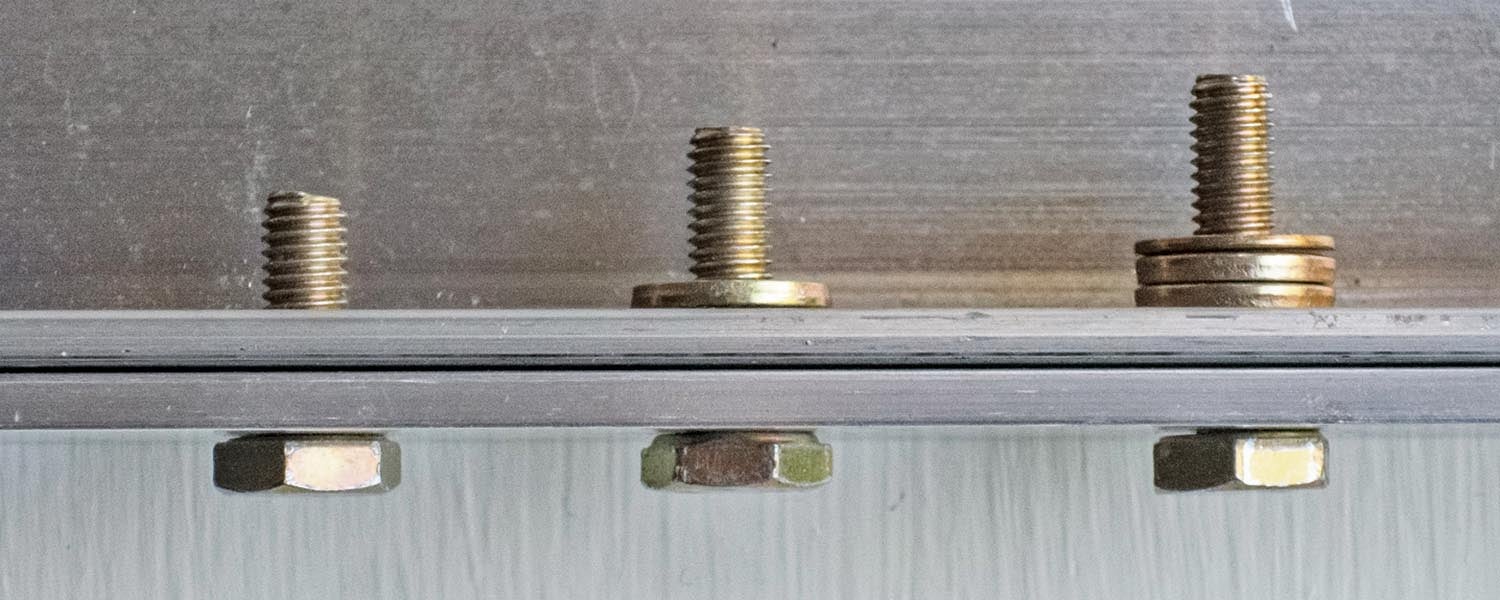
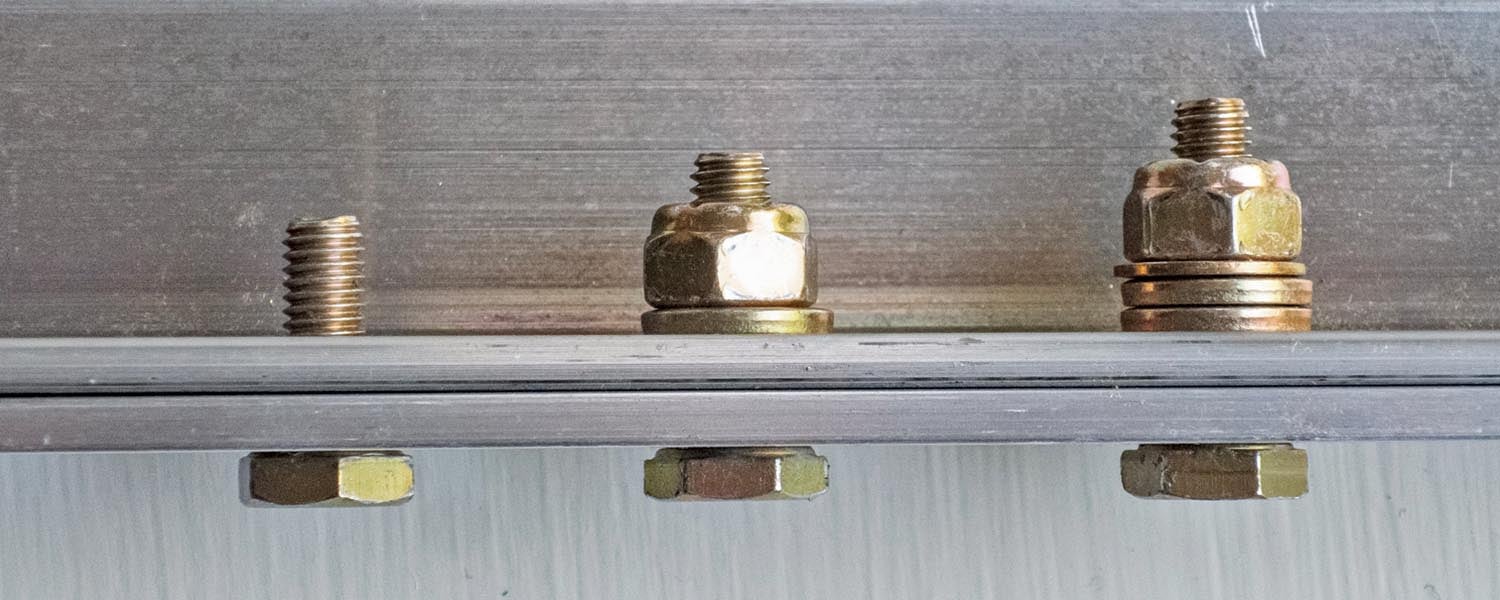
What Do AN960 Washers Do on Threaded Fasteners?
The AN960 plain washer positions the nut correctly on the fastener’s threads. It’s that simple. Best practices dictate the nut must neither bottom out on the fastener’s shank nor leave fewer than 1.5 threads of the fastener showing. To those who’d argue a washer must also be placed under the head of every bolt to protect the airframe’s surface from damage when the bolt is tightened, many certified aircraft manufacturers disagree. I explored the hangars of an aircraft repair facility to see how everything from Cubs to Caravans, Cessnas to Cirruses are assembled. For the majority, washers were absent from under bolt heads.
The best way to protect the airframe’s surface is to prevent the bolt from turning while the nut is tightened. Turning only the nut also prevents radial scoring of the fastener’s shank. (Radial scoring can occur when a bolt rotates against sharp edges.) To underscore that washers aren’t required under a bolt head, flush screws and washer-head screws are meant to be installed without washers under their heads.
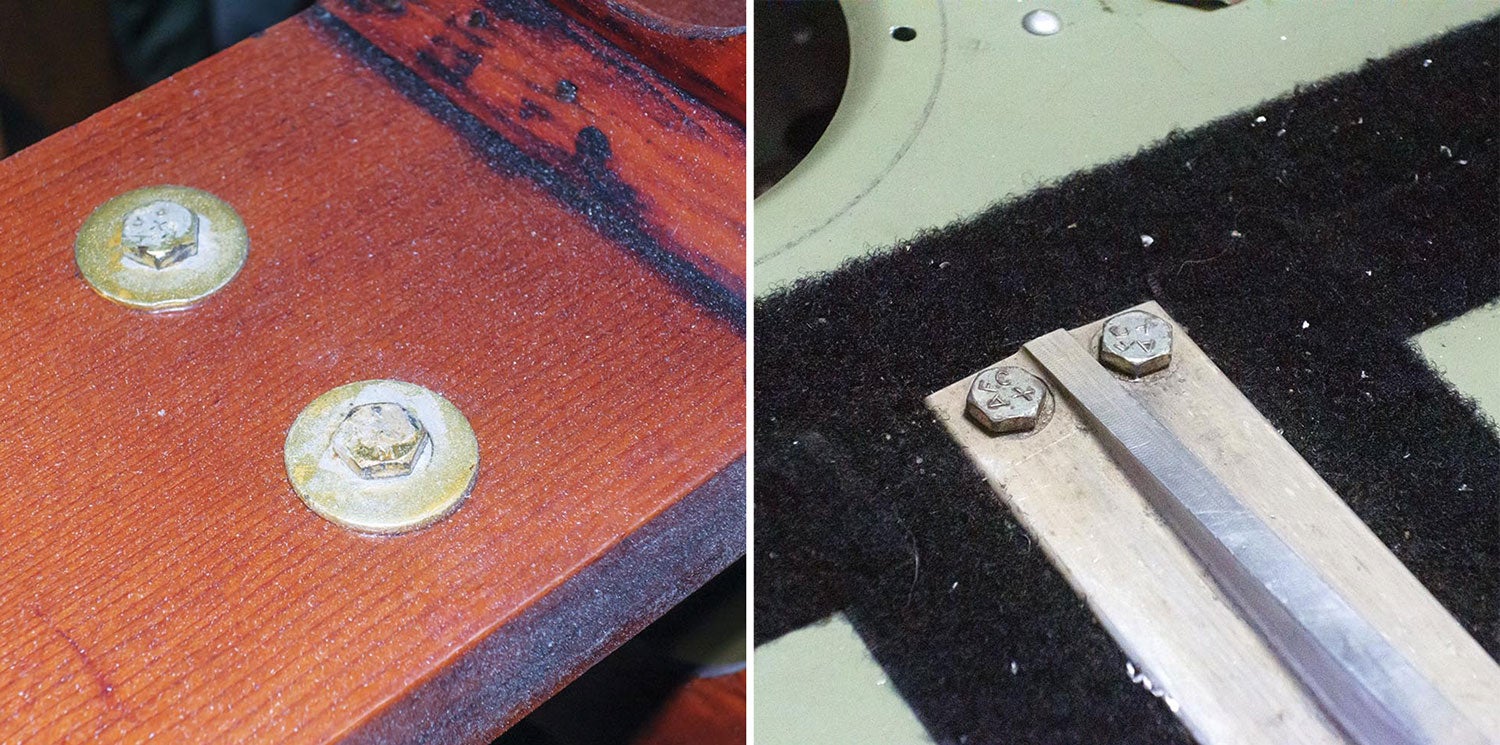
Other Considerations
Installing unnecessary washers impacts an airframe’s empty weight and cost. If you adopt the personal policy of placing a washer under every bolt head a percentage of bolts will need to be lengthened to have the correct grip length, further compounding weight gain. That may not impact a tube and fabric or wood airframe so much, but it can add up on aluminum airframes, which have more bolted joints.
Installing unneeded washers also encourages embedding loss. Embedding loss, something no one hashtags (#embedding_loss) on the socials, is a seldom referenced player in the washer debate. I’m hesitant to mention it because it sounds intimidating, but it isn’t. Embedding loss, simply put, is surface erosion. Grab a handful of change and you’ll see graphic evidence of surface erosion where the Lincoln Memorial has been rubbing against Monticello in pockets, cash register drawers and vending machines. Similarly, the high spots of freshly minted washers rest on the high spots of the neighboring washer. Over time they erode (as do the mating surfaces of the fastened parts), creating space where there was no space. The more washers employed, the greater the potential for loss. Embedding loss can cause a bolt to loosen even though the nut is exactly where it was when it was tightened.
The focus of this article is on the use of AN960 washers with structural fasteners in non-rotating assemblies; when securing Part A to Part B, AN960 washers don’t contribute strength to the joint, they facilitate the correct nut installation, which, I suppose, does contribute strength to the joint. There are applications where AN960 washers are used for other purposes, such as on rotating assemblies in control linkages or to space parts and assemblies. Follow the designer’s guidance and AC 43.13-1B for those applications.
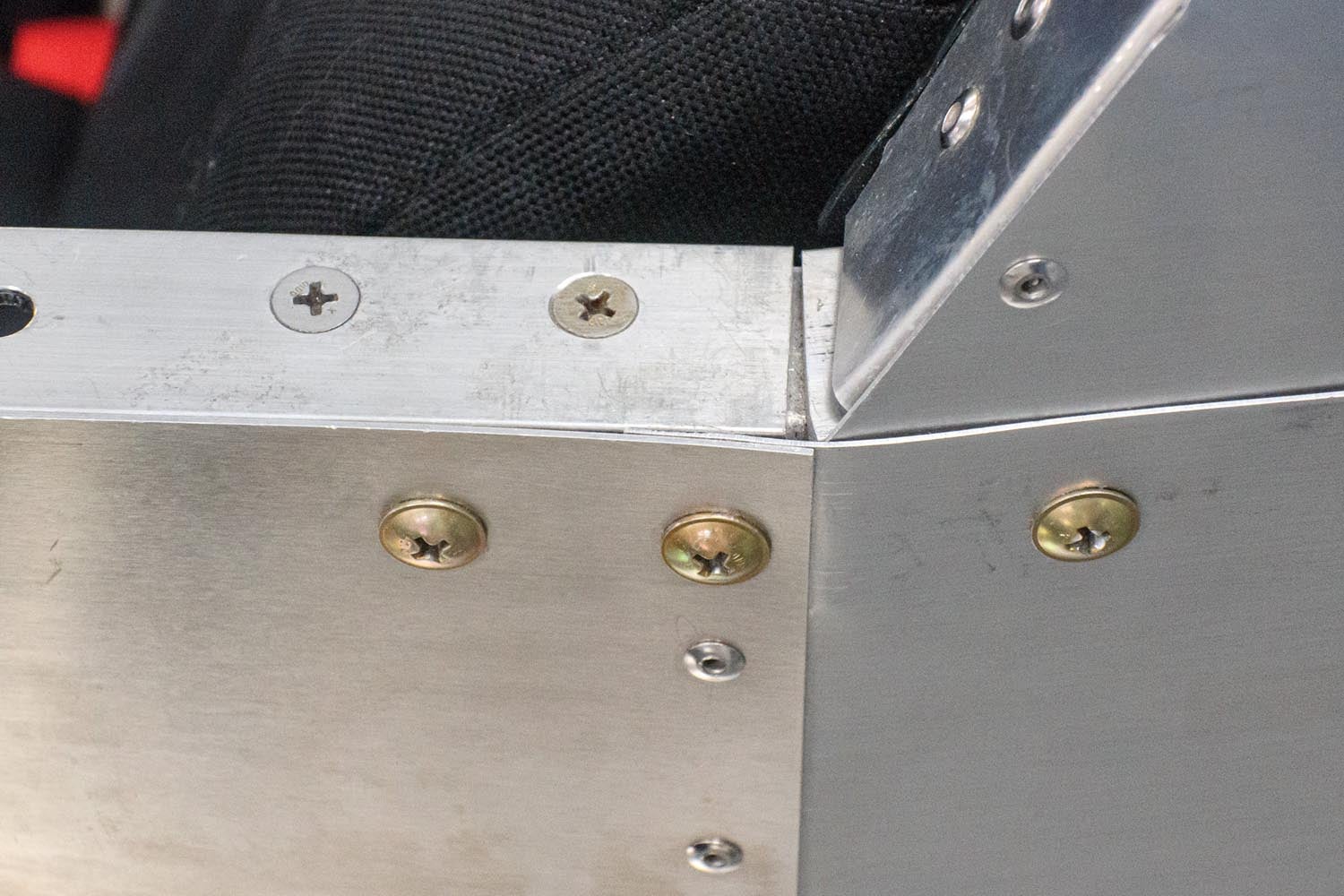
If You Were To Ask Me
Washer usage begins by choosing a fastener with the proper grip length. Best practices dictate the unthreaded shank of a fastener must extend fully (if only barely) through the parts being fastened. Therefore, at least one washer will be needed under the nut to keep it from bottoming out on the shank of the fastener. If a nut can be installed without a washer and without bottoming out, the fastener’s grip length is likely too short. With that in mind:
A. To keep weight down, choose the shortest fastener possible with no washer under the fastener’s head.
B. When possible, I use an AN960L thin washer instead of an AN960 washer under the nut. Thin washers are half the thickness and half the weight of the standard washer.
C. If the fastener’s grip length requires two washers, I place the second washer (a thin washer if possible, resulting in one standard washer and one thin washer) under the nut.
D. If a third washer is needed (a thin washer if possible, resulting in two standard washers and one thin washer) I first make sure I indeed used the correct length fastener. Depending on my mood I may place the third washer under the head of a bolt. Or not.
E. A fourth washer will never be needed. Instead, I reach for a shorter fastener.
Washer usage is something each builder should be able to determine for themselves, regardless of what is shown in a kit’s construction documentation. It was my middle school math teacher who said, “If you know the why, you know the how.” But he also said “the sezz-mezz,” a slurring of the phrase “the set whose members are,” which threw me off track for an entire math unit. Maybe I should quote Andrew Carnegie, instead, who said, “Take care of the pennies and the pounds will take care of themselves.” That applies to AN960 washers as well.
* I disagree with the statement “Plain washers are widely used with hex nuts to…act as a shim to obtain the proper grip length.” Proper grip length is determined by the thickness of the parts being fastened. Washers act as shims to prevent the nut from bottoming out on the shank of the fastener.
In your article “AN960 Washers, the Penny and My Thoughts”, you mentioned:
““The plain washer, AN960, is used under hex nuts,” and goes on to repeat, almost verbatim, the text from AC 43.13-1B. But two pages later it contradicts itself with the statement: “Be sure that washers are used under heads of bolts and nuts unless their omission is specified.” It doesn’t say why a washer should be placed under the bolt head, leaving us to argue amongst ourselves.”
Yes, it doesn’t say why to place a washer under the head of the washer. But since when does the FAA need to explain itself clearly or at all?
As you rightly mentioned, a washer under a bolt head will provide a greater bearing area than just the underside of the bolt head alone. That is certainly one point of consideration in and of itself.
What is completely omitted from consideration in the discussion so far has been the following. Per the bolt specification document, AN, MS, and NAS bolts will always have a radius under the bolt head adjacent to the shank. The purpose of this radius is critical to reducing the stress concentrations in the fillet under a bolt’s head and is a critical issue for the fatigue life of the component.
If you’re installing a close tolerance NAS bolt or even an AN bolt into a reamed or drilled hole which has been deburred… unless that hole is oversized, or has been countersunk, you will get interference between the under-head radius and the edge of the hole. This interference between the surface of the bolt head underside radius and the edge of the hole results in a stress concentration which can lead to metal fatigue.
This is why, in many applications, it is considered good practice to place a washer under the head of a bolt. Even though a reason isn’t stated in AC 43.13-1B, perhaps this is part of the reasoning behind it.
Hi all:
Having removed a bunch of bolts in my A & P career, I’ve seen a lot of part surfaces marred by bolts turning. For that reason, and to avoid having the bolt head’s radius contact the ID of the hole, I always install a AN-960L washer under the bolt head.
The clearance issue is worse with MS/NAS bolts with large under-head radii – the special washers needed for them must be installed with the raised side towards the bolt head.
I’ve seen washers up-side down, making big stress-risers on the bolt’s radius.
Yes, I know about weight gain – I have titanium thin washers surplused from the F-22 project for those applications. They float down if you drop them…
Keeping threads out of bearing seems to drive my bolt length increases.
Regards,
James
spell correct!
“…the special washers needed for them must be installed with the radiused side towards the bolt head.”
huh, I learned way more from this article than my ignorance led me to believe I would.
“radial scratches”. or circumferential scratches?
Agree completely with Glenn.
That fillet relief washer can even be the AN960LT in many cases. Looking at the AN960 spec will show the design range fillet radius. The fillet relief washer needs to be at least as thick as the largest radius plus tolerance.
Should have been AN960DL washer in my comment