Most of us fly airplanes for fun. I would even venture to say that all KITPLANES® readers understand the fun side of aviation, especially the sharing side. Right? Yep, at times we all wonder why everyone doesn’t fly (although there are exceptions!). One of the real dampers can be when we are trying to share that fun factor and Murphy shows up. I’m sure it’s happened to many, if not all, at one time or another.
One day when I was working at the Base Leg Aviation hangar, I noticed my good friend and former hangar partner, George Shemo, was at his hangar with some people that I assumed were family. George is a really accomplished pilot, a former military and Delta captain. He has built an RV-7A and is currently finishing an RV-10. His hangar is 90° to mine, so it was easy to see all the activity while I was still inside my hangar. I saw him pull the RV-7A out and load a little boy into it who it turns out was his grandson, Kyle.
I really wasn’t paying much attention, but after a while it dawned on me that I hadn’t heard an engine start. After a while longer, I looked again and noticed the boy was back outside the aircraft, sitting on the ramp with his mom. I didn’t think much about it, with George having built the airplane. Initially, I assumed there may have been a delay in getting the fuel truck to come over.
A little while later I noticed that George had made multiple trips to the hangar and was now somewhat upside down in the cockpit. My interest was now piqued, so I went over and asked if he was having any problems and if I could be of any help.
Well, there was a reason for the lack of an engine start; the fuel pump wasn’t working and George was troubleshooting the issue. I asked what he had done so far, and he was checking the wires to the pump. George is pretty thorough, and he told me that he had measured 12 volts on the positive wire to the pump, so he was thinking that the pump was bad. Sometimes, banging on a fuel pump will cause it to start working, although I wouldn’t recommend it as a standard procedure. Since fuel pumps are quite expensive for injected engines, we wanted to eliminate any other potential causes first. Plus, there was Kyle waiting for an airplane ride!
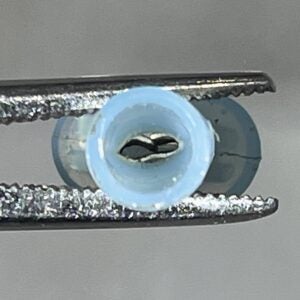
For grins I think we remeasured the voltage and, sure enough, it had 12 volts on the positive lead. I noticed George was taking the measurement from the positive wire to ground. I asked if he had measured between the positive lead and the pump ground wire. He had not. Guess what? That measurement showed less than 10 volts. When George went to change the connector on the end of the ground wire, it almost fell off.
I looked closely at the terminal and really didn’t like what I saw. The crimp was not exactly a strong double crimp. George agreed and replaced the crimp. Guess what? It still didn’t work. Hmm. That left one other connection—the ground wire. It had the same type of terminal on it. When George went to replace it, it almost fell off in his hands. There wasn’t much wire left to work with, but a quick temporary fix was to add a length of wire and make a new ground connection. It all worked and the day was saved.
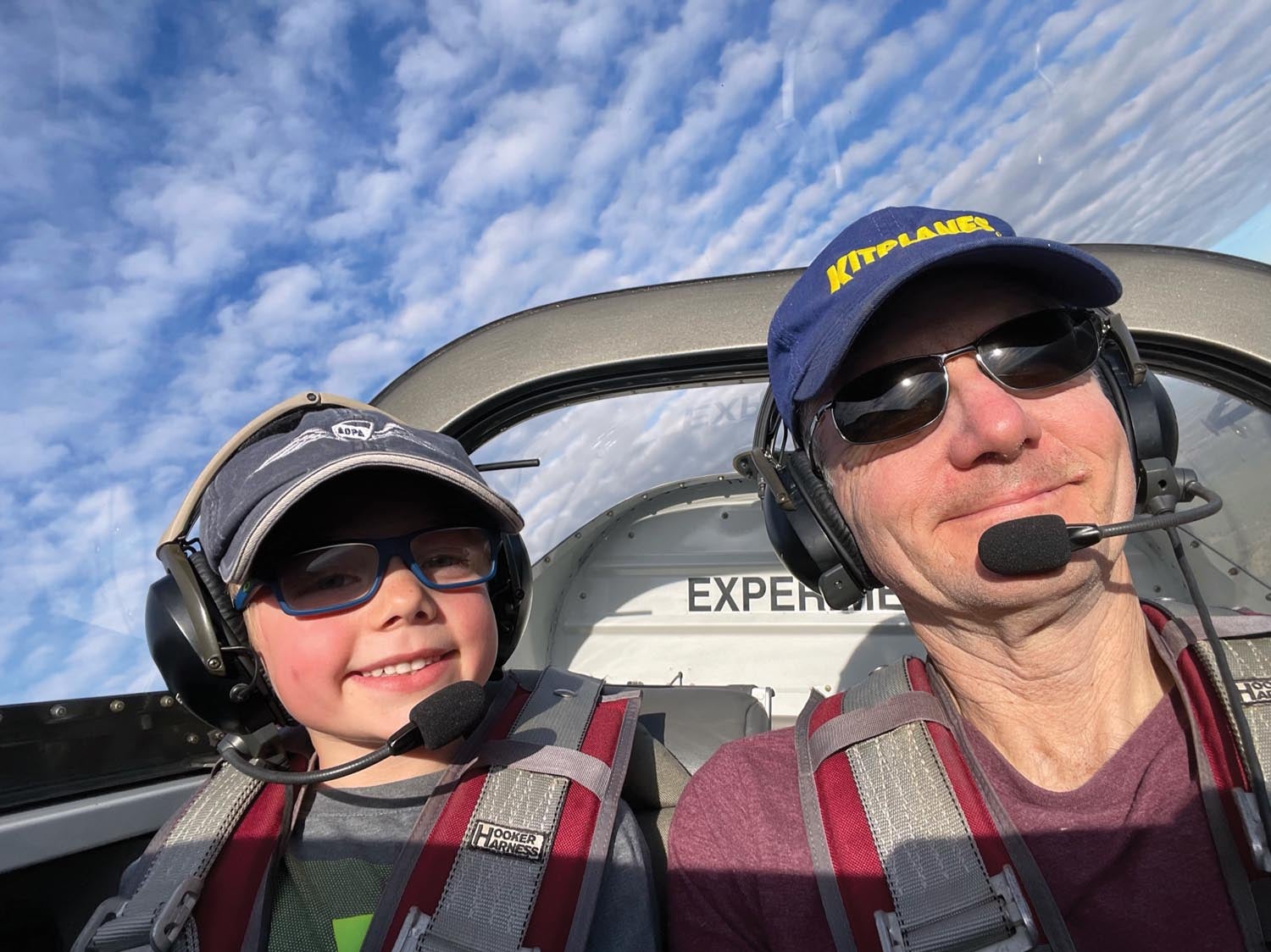
This isn’t the first time I have seen this type of problem. As the fleet is aging, crimps on terminals that were not quite made properly 10–20 years ago are beginning to cause problems. Heads up for those of you who might have aircraft of this vintage. It usually starts intermittently and then progressively gets worse, until Murphy raises his head and says, “I’m here to mess with your fun factor today!”
Wire crimps should be done with a proper crimper tool, inexpensive, and most will handle a number of terminal and wire sizes.
It will crimp the wire and do an insulation crimp to relieve the strain on the wire crimp.
Most also have a wire stripper, so no nicking of wire strands.
Finally, a strain relief of the wire should be made to a solid structure , [ adel clamp ], within 2 inches of the terminal, to keep vibration from fatigue failing the wire .
Properly crimped and strain relieved wires should last more than 20 years.!
IF he had two bad crimps there are more, he needs to check everything and get them up to spec.
The trick to making a tight crimp with the common crimp tool is to not use the part designated for insulated terminals. It makes a flat crimp and does not hold well. Instead use the non-insulated terminal part. It makes a V crimp deeper into the wire and holds much better. You can even double crimp if you wish. I have been using this method in marine work for 40 years with no problems.