I’ve ridden the early adopter bus before—found the seats uncomfortable, the ride jarring and the destination available only after many inconvenient stops. So it should not surprise anyone that I’m just now switching over to electronic ignition in my GlaStar (nicknamed Charlie after the original builder).
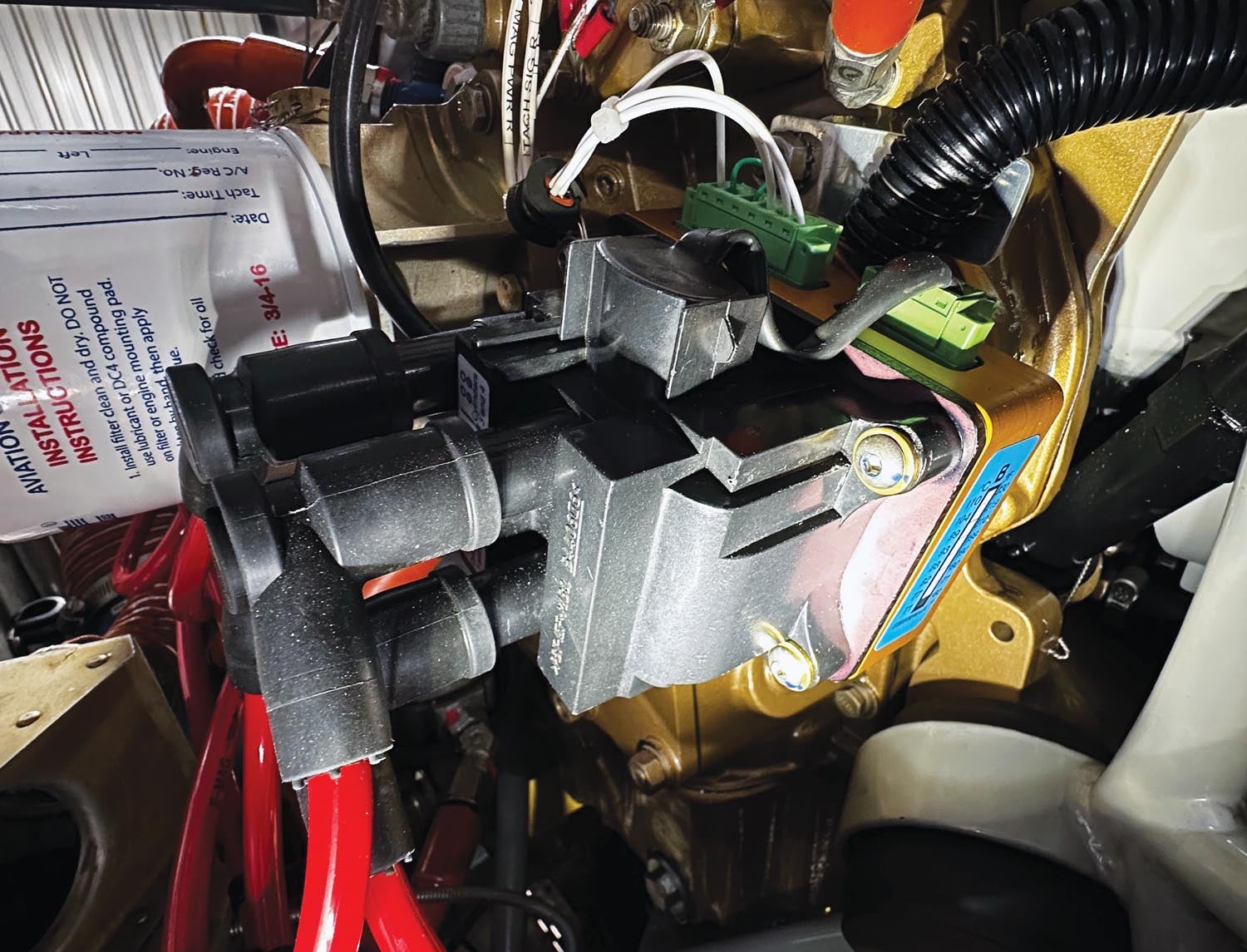
My choice for new ignition was to install a pair of E-MAG Electronic Ignition 114 Series P-MAG units. These units, which have been around for more than a decade, are designed to be as simple as possible to install. Each takes the physical space of a magneto—slightly less, actually. There are, of course, a few more wires to run through the firewall, plus you’ll have to route new spark-plug wires, make a connection to a manifold-pressure source and install new automotive plugs and the associated adapters. (See Paul Dye’s story for some tools and techniques around those adapters.) I also used some corrugated plastic tube for cooling the units, which is considered mandatory by E-MAG. I would say the retrofit was involved but not difficult. The documentation is extensive.
As with many aspects of my airplane, I’m installing over existing systems. So I kept the keyed ignition switch—first removing the jumper whose normal function is to keep the non-impulse-coupled mag from firing while starting—though I also advocate using one because it’s like so many certified airplanes, which makes it easier for other pilots to transition into.
A note about power for the P-MAGs. They need ship’s power only to start and in the event of the internal supply’s failure; in fact, during normal operation they’re not even using main-bus power. This is how I justify not having a truly redundant electrical system. In fact, I have considerable avionics redundancy because many pieces either have their own backup batteries or are powered through a TCW Technologies IBBS.
The P-MAGs’ internal power can be relied upon as low as 850 rpm. Below that, the internal generator can’t keep up and the system falls back on external power. Some builders wire momentary switches to test this function periodically but I used pullable breakers located right next to the ignition switch to do the same thing. (And partly so I wouldn’t have to run power all the way from the other side of the panel.) The procedure for landing with a total aircraft electrical failure is to maintain 850 rpm or greater until the runway is made, a small change from the SOP.
Advance and Performance
P-MAGs have two internal advance curves, chosen by a jumper; I used the less aggressive one. I also attempted to set the baseline timing to coincide with my engine’s spec, which is 20° before top dead center (BTDC). The P-MAGs are designed with an internal 25° BTDC timing, the most common, and are set with TDC as a reference. By setting mine 5° after TDC, the system fires at the correct timing for my engine.
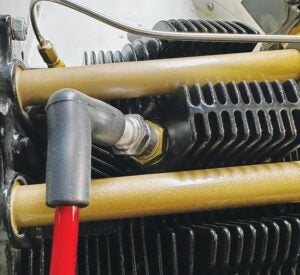
The two main functional advantages of electronic ignition include variable timing and a stronger spark on all plugs during start. Agreed on the strong start. My engine has never been easier to light off, hot or cold, first thing in the morning or right after a quick refueling—that aspect has been a solid win.
The variable timing comes into play at altitude and, especially, when running lean-of-peak mixture settings, which I almost always do in cruise. A lean mixture takes longer to burn, so advancing the timing helps move the peak of the power pulse back to where it does more good.
Once flying, I compared before-and-after engine data and was surprised to see higher EGTs with the P-MAGs. Retarded spark usually raises EGTs—it’s why a mag check sees the EGTs rise on one ignition source—so I was surprised when the P-MAGs seemed to be running late. I double-checked the timing and it was right where I wanted it. But the advance curves follow both engine speed and manifold pressure. With my fixed-pitch prop, I’m way down on the rpm-based advance curve for takeoff and the initial climb compared to an engine with a constant-speed prop that can turn 2700 rpm for takeoff.
After a lot of head scratching, I began incrementally advancing the installed timing to get the real-world spark near where it would be with magnetos. The engine remained happy with nearly all the offset removed. This is another reason to watch your data and try to interpret what it’s telling you. In addition, my experience speaks to the value of really understanding how systems work.
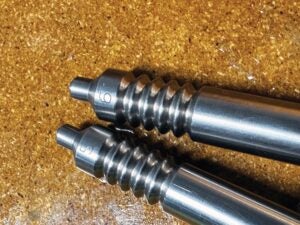
After tweaking the overall timing, I tried a prop adjustment. Because, well, everything is interconnected. By reducing prop pitch by “one number” in the Sensenich ground-adjustable, I was able to get static rpm up above 2200 and climb in the 2350–2400 rpm range, which made the airplane a bit more sprightly off the runway and during the climb to cruise—though I did lose 2–3 knots in cruise at any given engine speed.
More Testing…
I thought I was done. But one nice spring day I decided to take Charlie up to altitude to fill out missing fields in my cruise data. It revealed a couple of things. First, the timing advance really begins to show by about 5000 feet in the climb. At first you think the engine’s too rich because the EGTs are falling, but it’s really just the advance moving the combustion event ahead. I’ll have to recalibrate my sense of absolute EGTs to fuel flow during the climb phase. That’s not a bug, just a matter of learning the system. I do see higher cylinder-head temps later in the climb as the manifold-pressure-based ignition advance starts to take hold, but it’s been manageable so far.
In cruise flight, two characteristics stand out. First is that the engine will run much deeper lean-of-peak EGT prior to roughness. In fact, most of the time, as you lean, the engine just quietly stops making power. No fuss at all. The other change is that the engine is definitely making more power at altitude—not orders of magnitude but enough to show up as greater engine speed on any given prop setting. I’m now thinking I should have moved to electronic ignition sooner—but I also know exactly why I didn’t.
E-Mags have “shower of sparks” as a starting feature. In observing spark operation prior to first engine start, I saw (and heard) a “zzzzzt.” at the normal firing angle. At OSH, a few months later, the E-Mag rep told me that below a certain RPM there are 5 consecutive sparks for each firing. My Superior IO-360 with three-blade Whirl Wind typically starts on the second blade.